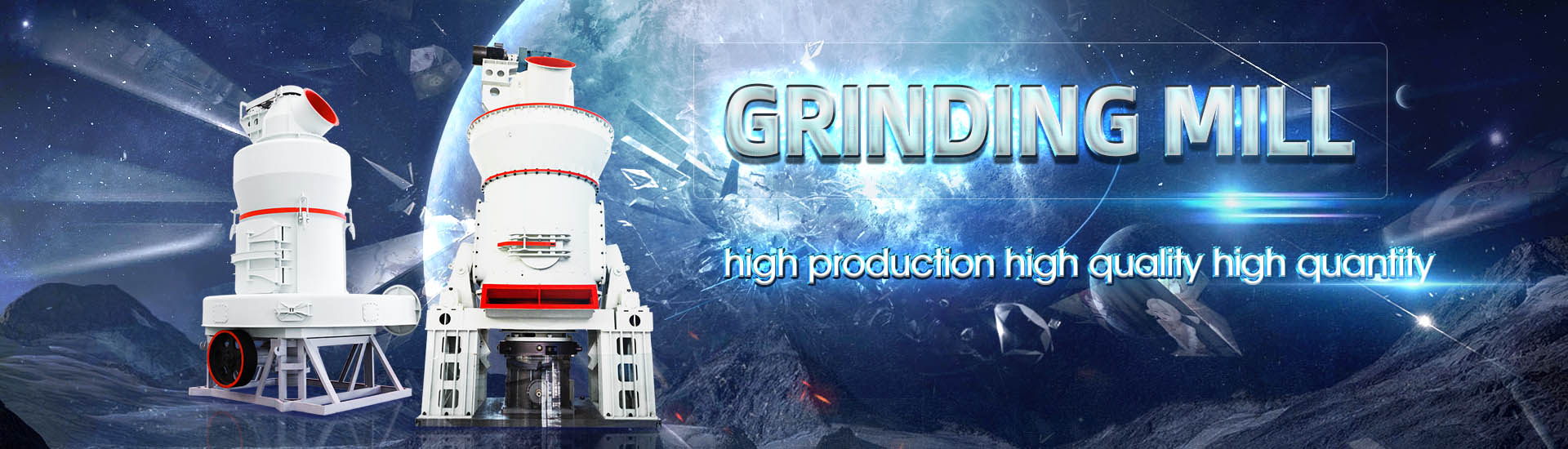
How to increase the output of vertical mill during operation
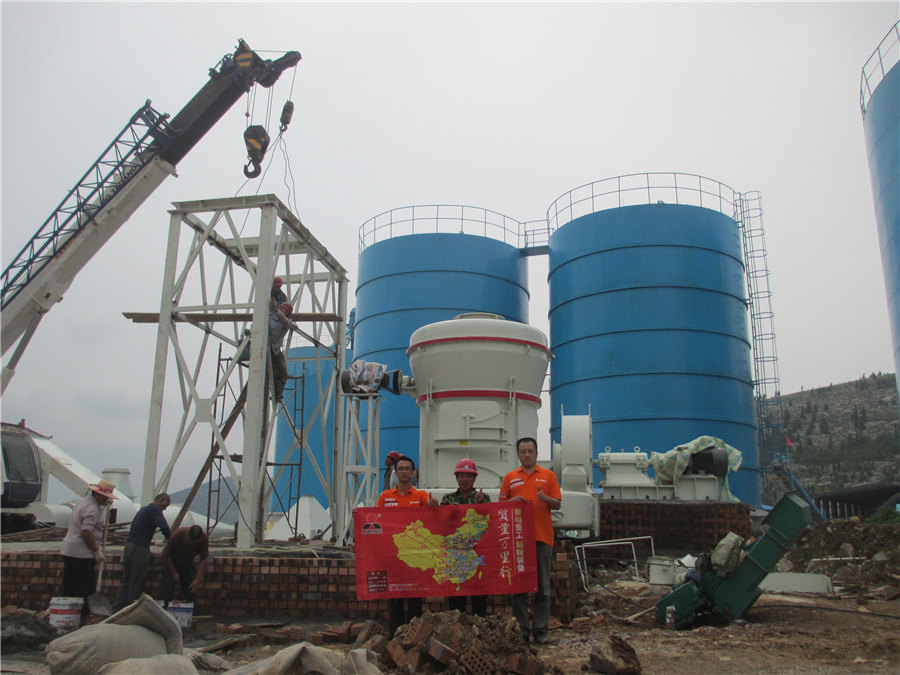
Operational parameters affecting the vertical roller mill
2017年4月1日 Vertical roller mills (VRM) have found applications mostly in cement grinding operations where they were used in raw meal and finish grinding stages and in power plants 2023年6月1日 Increasing the speed of the separator, the inlet air speed and the outlet temperature in the feasible interval can effectively improve the output and fineness of the Operation parameters multiobjective optimization method of Invisible is equivalent to increasing the height of the retaining ring, increasing the thickness of the material layer, increasing the load of the main motor, and limiting the output, which has a great influence on the working condition of vertical millHow To Improve Output Of Vertical Mill2017年9月11日 Its effectiveness, combined with the implementation of drying, grinding and separation in one unit, gives it an undeniable advantage over a ball mill This explains the significant increase inPerformance Evaluation of Vertical Roller Mill in
.jpg)
Operational parameters affecting the vertical roller mill
2016年9月1日 By initiating a CL for an industrial cement vertical roller mill (VRM), this study conducted a novel strategy to explore relationships between VRM monitored operational Roller Mill (VRM) reduces the power consumption for cement grinding approximately 3040% associated with other grinding mills The process variables in cement grinding process using PROCESS CONTROL FOR CEMENT GRINDING IN VERTICAL 2022年5月31日 The vertical roller mill (VRM) is commonly used for secondary and tertiary crushing processes in numerous industries In this study, the discrete element method (DEM) Analysis of vertical roller mill performance with changes in material 2021年1月1日 The research explains complete process of identifying possible causes and final root causes, finding possible solutions and implementing them in order to increase the output Increase productivity of vertical roller mill using seven QC tools
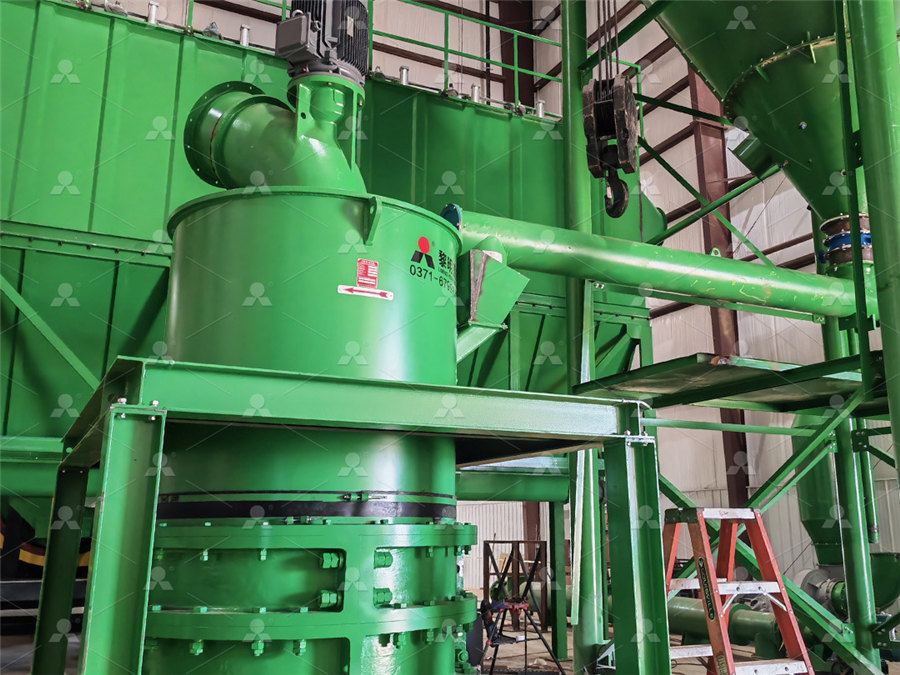
Analysis and Optimization of Grinding Performance of
2022年1月23日 Therefore, it is necessary to optimize the multiobjective parameters of the VRM in order to improve the grinding performance and reduce energy consumption The present work focuses on the grinding performance 2023年7月14日 The main functions of thinwalled structures—widely used in several industries—are to reduce the weight of the finished product and to increase the rigidity of the structure A popular method for machining such Evaluation of the Vibration Signal during Milling Wind energy is considered one of the most important sources of renewable energy in the world, because it contributes to reducing the negative effects on the environment The most important types of wind turbines are horizontal and Design and Optimization of Vertical Axis Wind 2017年4月1日 Separation operation of verticalrollermill will be modelled by application of current models The model shall enable the prediction of the throughput, the particle size distributions around the verticalrollermill circuit, the specific energy consumption and in a later stage the wear to be expected in dependency of ore treatedOperational parameters affecting the vertical roller mill
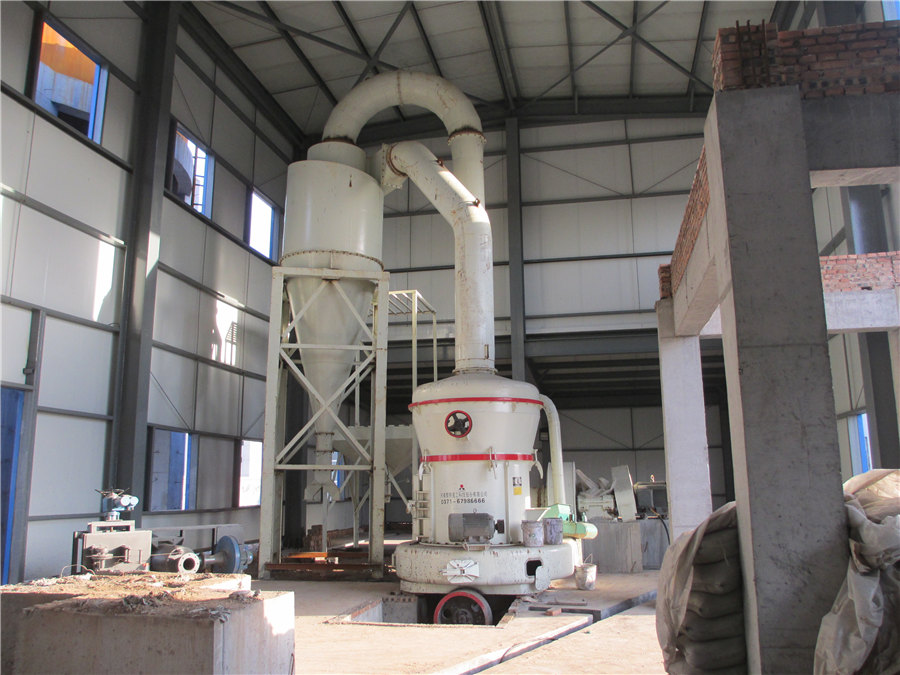
Performance Evaluation of Vertical Roller Mill in Cement
2017年9月11日 operation in vertical roller mill The work evaluated the performance of a mill with smooth disk rolls During the study, it can not only reduce energy consumption but also increase outputThe grinding rollers and discs are not in direct contact during work, stable operation, low wear, long life, environmental protection and energy saving, How to increase the output of vertical roller mill? 3 What are the highlights of an ultrafine vertical roller mill? The CLUM ultrafine vertical mill integrates crushing, Ultrafine Vertical MillOptimization of the Cement Ball Mill Operation Optimization addresses the grinding process, maintenance and product quality The objective is to achieve a more efficient operation and increase the production rate as well as improve the run factor Consistent quality and maximum output with lower specific power consumptionOPTIMIZATION OF CEMENT GRINDING OPERATION IN BALL MILLS• The cement mill and the sepax separator were thoroughly inspected to observe internal condition of the mill and separator During the inspection, mill and separator internal condition found in good condition and no coating on internals material accumulation observed However in Chamber I at a distance of 2 to 4PROCESS DIAGNOSTIC STUDIES FOR CEMENT MILL
.jpg)
Improvement of cement performances through the use of
Mill output 57 t/h Compressive strengths 2days 11 MPa 7days 30 MPa 28 days 43 MPa After introducing MAGA/VM 10 at a dosage of 400 g/t (0,04%) directly sprayed on the grinding bed, the following positive effect have been observed: Mill output increase by 12%: from 57 to 64 t/h Energy saving by 9%: from 30 to 27,6 kWh/tWhen material grindability deteriorates, grinding cycles number of vertical mill increases significantly Since most of the material is crushed into fine powder, and the operator must master it during operation For safety reasons, it is best not to close the inlet damper into the humidification tower during productionImportant Operation Tips For Cement Vertical Mill2021年3月1日 One of the basic rules of engineering design is that it’s “done with numbers”, rather than with vague assertions about the properties of the system being designed There isn’t much use in saying that we want our workholding systems to be “ really stiff and strong” without specifying what that means It's not very helpful if a customer comes into your shop asking for Workholding Wisdom AMEFig 2 Modular Vertical Roller Mill 5000 R4 Installed in Canada Fig 3 Modular Vertical Roller Mill 5000 R4 Installed in Canada V Operational Experience with Modular Vertical Roller MillsGrinding Process Optimization Featuring Case Studies and
.jpg)
Modeling and simulation of vertical roller mill using population
of 80mm The raw materials are mixed in a certain proportion and fed into a vertical roller mill (LOESCHE mill) The vertical roller mill grinds the marital to D 85 of 90µm The ground product is calcined in a preheater to 850900℃ After calcination, the materials enter to a rotary kiln and heated to 1450℃ to become clinkerAnalysis of noise and vibration during the operation of the ball mill The ball mill is used for grinding materials after crushing, and CHAENG is a professional manufacturer of ball mill accessories, such as girth gear of ball mill, ball mill Analysis of noise and vibration during the operation The vertical roller mill (VRM) is a type of grinding machine for raw material processing and cement grinding in the cement manufacturing processIn recent years, the VRM cement mill has been equipped in more and more cement plants around the world because of its features like high energy efficiency, low pollutant generation, small floor area, etc The VRM cement mill has a Vertical Roller Mill Operation in Cement Plant2021年1月1日 Grinding Mill Vertical Roller Mill or Ball Mill: The reclaimed raw mix fed to Raw Mills, for drying and fine grinding of Raw meal for kiln feed: 4: Coal Grinding: Grinding Mill Vertical Roller Mill or Ball Mill: Coal is ground in Coal mill, which is a fuel for use in Kiln firing: 5: Pyro Section, Clikerization: In line calciner six stage Review on vertical roller mill in cement industry its
.jpg)
Analysis of vertical roller mill performance with changes in
2022年5月31日 An increase in MS from 5 mm to 7 mm (about a 40% increase) leads to a 12 times increase in the average power draw, while the next 85% increase (from 7 mm to 13 mm) leads to a 480% reduction The average power draw with an MS of 7 mm is the largest, while of 0395 kg/s is the lowestThe determination of unit output is very important, directly related to equipment selection Equipment selection should take full account of the following factors: (1) The slag vertical mill is not a device that can run continuously for a long time It is necessary to stop the repair every 1500~1800h, usually 7 days for each repair and 35 days for the whole yearHow to determine the output of a ggbfs(ggbs) grinding plant2024年3月6日 Vertical Milling Machines Vertical milling machines feature a vertically oriented spindle that operates above the workpiece The alignment allows the cutting tool to approach the material from the top down Often equipped with a kneeandcolumn design, the vertical mill provides the versatility to move the workpiece along the ZaxisWhat Is a CNC Milling Machine? Everything You Need To KnowVertical roller mills and ball mills represent two clearly distinct technologies However, with proper adjustments to the operational parameters of the vertical roller mill almost identical cement properties can be achieved by the two mills that satisfy the cement user’s demandsNevertheless, the two types of mills have their distinctive meritsCement grinding Vertical roller mills VS ball mills
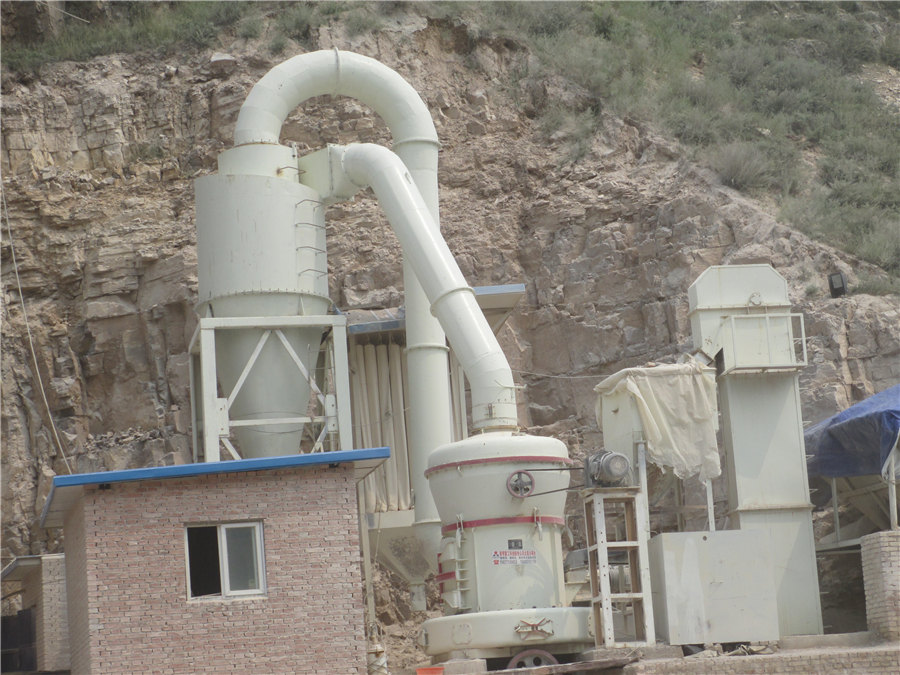
Detection of Malfunctions and Abnormal Working Conditions of a Coal Mill
2018年5月2日 Coal mill malfunctions are some of the most common causes of failing to keep the power plant crucial operating parameters or even unplanned power plant shutdowns Therefore, an algorithm has been developed that enable online detection of abnormal conditions and malfunctions of an operating mill Based on calculated diagnostic signals and defined in combination with a ball mill for cement grinding applications and as finished product grinding units, as well as raw ingredient grinding equipment in mineral applications This paper will focus on the ball mill grinding process, its tools and optimisation possibilities (see Figure 1) The ball mill comminution process has a high electricalBALL MILLS Ball mill optimisation Holzinger ConsultingVertical Coal Mill (VCM) is equipment for grinding and pulverizing coal into micron size Rotary kilns then use the powders as fuel burners The VCM has a housing section equipped with a lining The layout of the coal mill with a rotary classifierFig1 Flow of Conventional Vertical Mill Grinding System Mill Kiln IDF (Kiln gas exhaust fan) By this production increasing, it is expected that operation in the daytime can be shortened and then power cost can be reduced Cost estimation About 73 Vertical roller mill for raw Application p rocess materials
.jpg)
How to operate an air classifier mill to meet your fine grinding goals
vertical mill Combined drive In this classifier mill, as shown in Figure 2b, the classifier wheel and rotor disc are mounted on one shaft and rotate at the same speed As a result, the mill is smaller, has a lower purchase cost, and requires less installed horsepower than the vertical mill However, the apFigure 1 Vertical air classifier 2023年6月1日 This study aims to improve the output and production efficiency of a large vertical mill by optimizing its operational parameters This paper takes a large vertical mill in LGM as the object, a numerical calculation method of particle–fluid coupling system in large vertical mill based on CFDDPM theory, and a multiobjective optimization method of operating parameters of Operation parameters multiobjective optimization method of the capacity of grinding and drying of mill The grindability affects the capacity of grinding, type of mill and roller pressure The capacity of the mill is calculated Using G K * D 251 Where, G is capacity of the mill, K1 is roller mill coefficient and D is table diameter 2 PROCESS CONTROL OF VRM The conventional control system of VRMPROCESS CONTROL FOR CEMENT GRINDING IN VERTICAL ROLLER MILL Variations in feed rate increase vibrations of the mill, destabilizing operation and in the extreme resulting in mill stoppages Observed feed variation in Fly ash The mill feed material needs to be free of metal pieces Higher the metal pieces frequent operation of diverting gate and results in feed variation [8,12,14]Indicate Contributions from Several Radial VHYHQ4WRROV
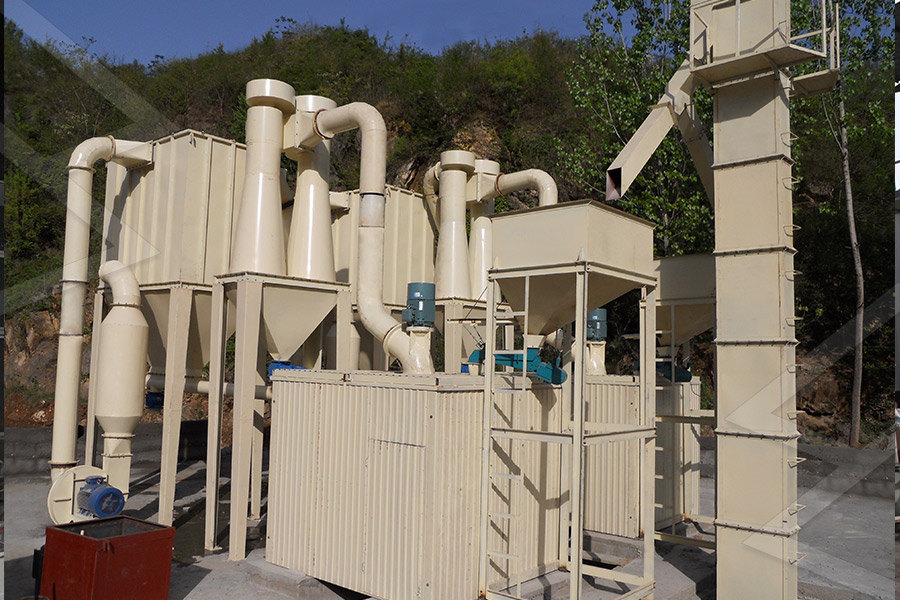
Assessment of the thermodynamics efficiency of a cement vertical
It is the expression in which \(T\) represents temperature, \(P\) represents pressure, and \({\varDelta G}{i}^{0}\) represents standard Gibbs free energy of the formation of species \(i\) \({y}{i}\) represents the mole fraction of that species The objective function is expressed in Eq 4 Thermodynamic predictions are obtained with the help of process simulation software like It brings increased efficiency to any operation by making more parts quickly Among the milling machines available, a CNC mill can provide the best production benefits with large volume outputs and superior finish Accuracy A vertical mill offers enhanced visibility during the machining process due to its vertical orientationHow Does a Milling Machine Work Everything Explained! Lathe 2022年8月11日 But in the new system, for example, the team has found that by turning one turbine just slightly away from its own maximum output position — perhaps 20 degrees away from its individual peak output angle — the resulting increase in power output from one or more downwind units will more than make up for the slight reduction in output from the first unitA new method boosts wind farms’ energy output, without new 2017年1月17日 Grinding mills are infamous for their extremely low energy efficiency It is generally accepted that the energy required to produce new mineral surfaces is less than 1% of the electricity consumed Breaking down energy consumption in industrial
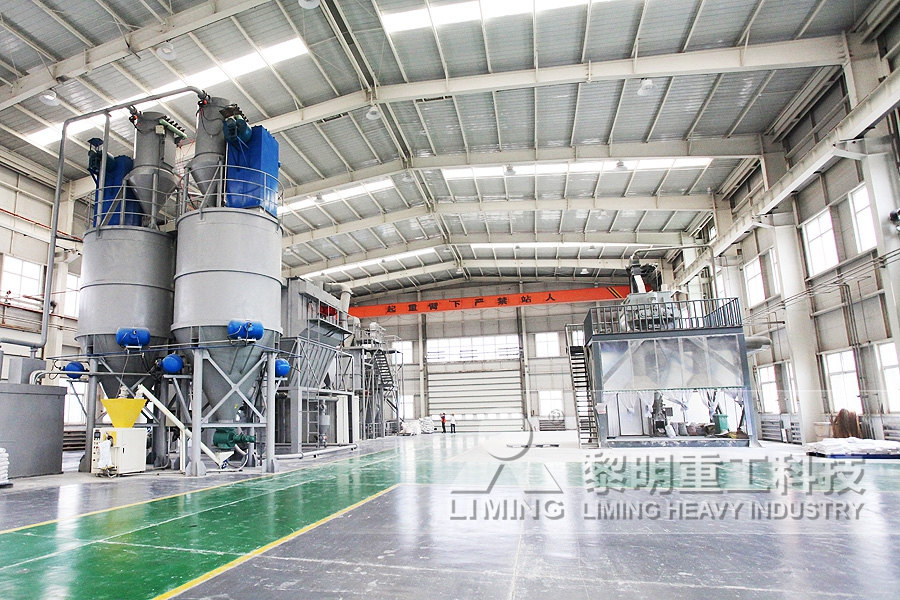
Performance Evaluation of Vertical Roller Mill in Cement
Performance Evaluation of Vertical Roller Mill in Cement Grinding: Case Study ESCH Cement Plant D Altun, NA Aydogan, O Altun, AH Benzer2013年3月1日 This study investigated a mathematical model for an industrialscale vertical roller mill(VRM) at the Ilam Cement Plant in Iran The model was calibrated using the initial survey's data, and the Cements ground in the vertical roller mill fulfil the 2020年2月1日 Nowadays, ball mills are used widely in cement plants to grind clinker and gypsum to produce cement In this work, the energy and exergy analyses of a cement ball mill (CBM) were performed and Energy and exergy analyses for a cement ball mill of a new This feature is a boon for foundries with machine shops as well as those that outsource machining Vertical turning lathes enable these operations to expand their machining capabilities and increase their output Improved Cycle Times and Productivity Vertical turning centers also enhance productivity by improving cycle timesA Comprehensive Guide to Vertical Turning – TMC Technologies
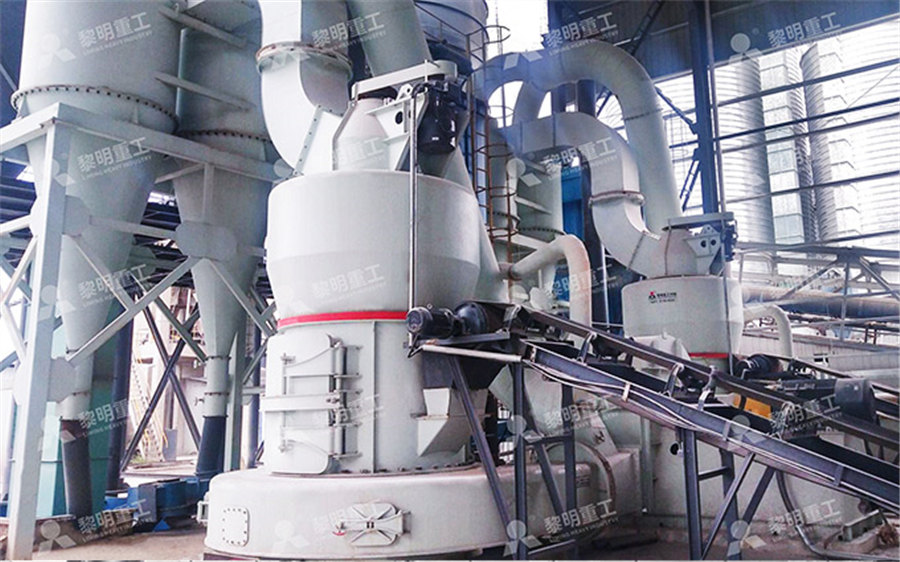
Regrind of metallic ores with vertical mills: An overview of the
2014年10月20日 This paper presents the results of industrial surveys carried out on the Vertical mill circuits of Sossego plant during its initial years of operation, and compares these results with the design 2015年11月1日 From Fig 3, Fig 4, Fig 5, Fig 6 and Table 5, it can be seen that the measured outputs of the proposed model (mill differential pressure, current, outlet temperature) approach the onsite values very well and unmeasured outputs (pulverized fuel flow, mass accumulated inside the mill, outlet moisture content, moisture in accumulated coal inside the mill, mill A unified thermomechanical model for coal mill operation2022年1月12日 Let's take a look at the difference between ultrafine vertical mill and ball mill +17 [ protected] language During the grinding process, adding a small amount of additives that do not affect the quality of the finished product can significantly increase the added value of the productWhat is the difference between vertical mill and ball mill?2022年7月2日 where, v = it is the speed of the cutter in m per min d = cutter diameter in mm n = Speed of the cutter in rpm #2 Effective Cutting Speed It indicates the surface speed over the effective diameter (DC ap)This is necessary in order to determine the correct cutting data at the actual depth of cut (a p) It is used when you are working with round cutters, ball nose end Milling Formulas Definitions [Explained with Example] PDF
.jpg)
Grinding process optimization IEEE Xplore
2017年6月19日 As a worldwide leader in grinding solutions for the cement industry and understanding the changing needs of cement producers and how to tailor solutions to meet those needs Optimizing output, improving efficiency, and reducing CO2 emissions while keeping investment costs to a minimum are common challenges that the modular vertical roller mill