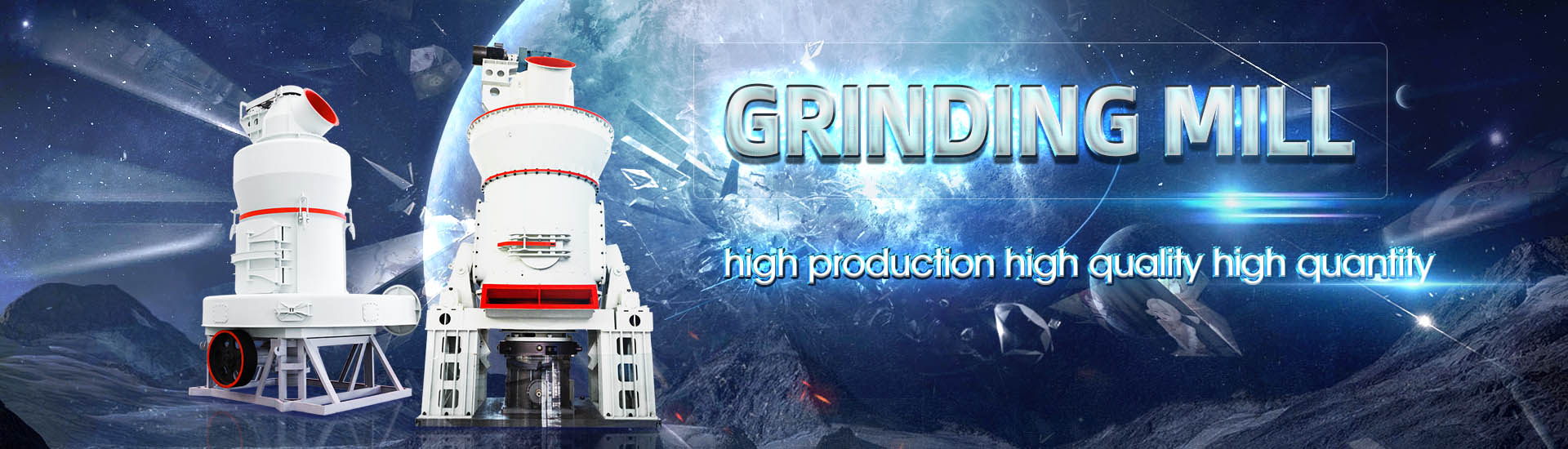
Reasons for coarseness of cement mill
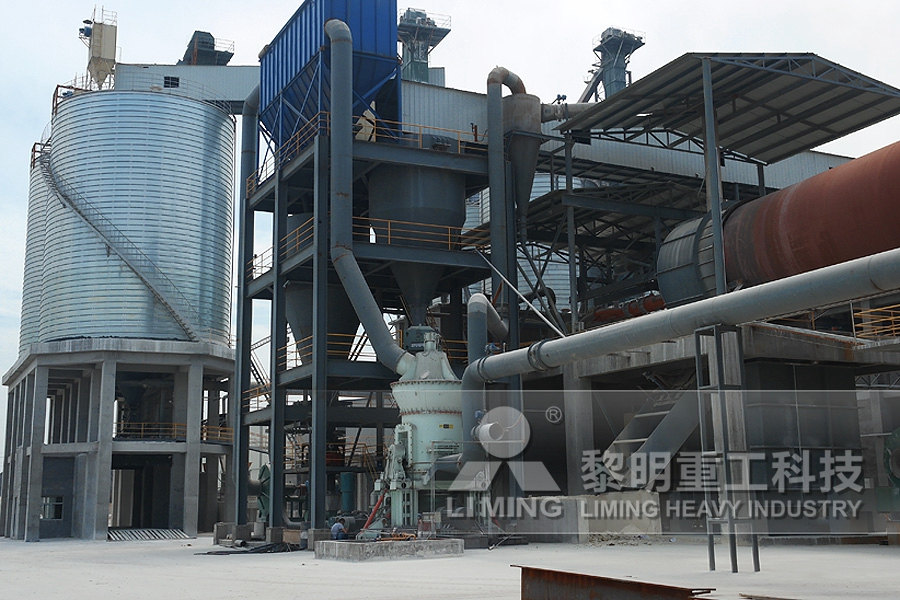
Optimization of Cement Grinding Operation in Ball
Optimization addresses the grinding process, maintenance and product quality The objective is to achieve a more efficient operation and increase the production rate as well as improve the run factor Consistent quality and maximum output Thomas Holzinger, Holzinger Consulting, discusses cement grinding system optimisation Introduction The cement industry uses a wide range of different systems in raw material, coal, Thomas Holzinger, Holzinger Consulting, grinding system Operation and Elements of a ClosedCircuit Ball Mill System Cement ball mills typically have two grinding chambers The first chamber is filled with larger diameter grinding media andlined OPTIMIZATION OF CEMENT GRINDING OPERATION IN BALL MILLSCement milling is usually carried out using ball mills with two or more separate chambers containing different sizes of grinding media (steel balls) Grinding clinker requires a lot of Cement Milling
.jpg)
Coarse Return Prediction in a Cement Industry’s Closed Grinding
2021年2月3日 A combined event modeling for feature extraction and the fully connected deep neural network model to predict the coarseness of cement particles is proposed2021年1月1日 High productivity and low power costs can be achieved by increasing output, lowering breakdowns and optimizing the energy consuming grinding process The objective of Review on vertical roller mill in cement industry its performance 2017年9月11日 The study revealed the causes of the destruction of the details of the roller mill: with the simultaneous impact of the workload and the displacement of the sectors resulting (PDF) Performance Evaluation of Vertical Roller Mill in Cement 2017年6月19日 The cement mill case study will showcase the active redundancy concept resulting from the innovative multi drive design These new features considerably reduce Grinding process optimization IEEE Xplore
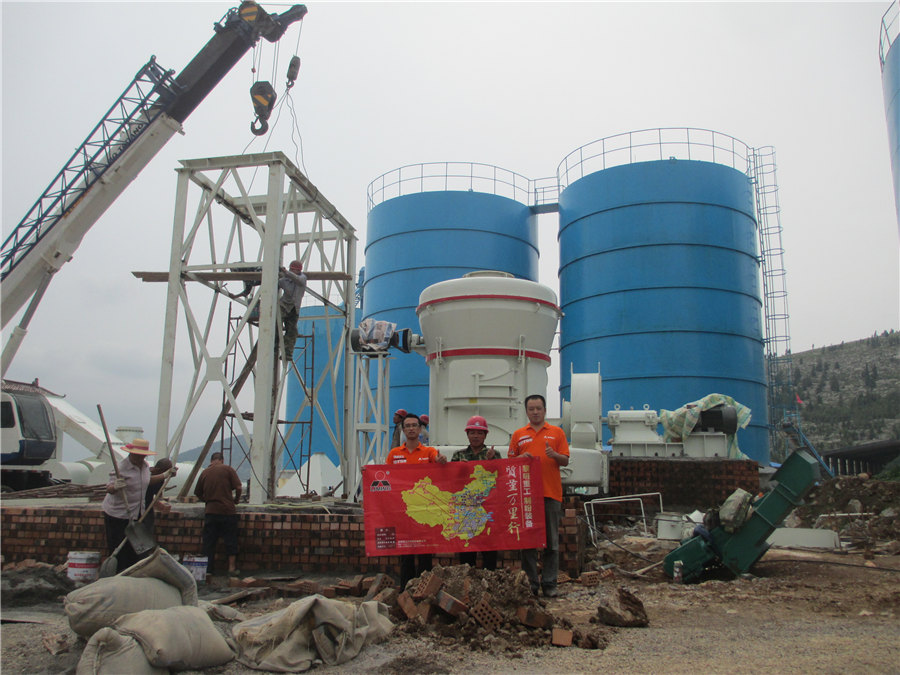
BALL MILLS Ball mill optimisation Holzinger Consulting
As grinding accounts for a sizeable share in a cement plant’s power consumption, optimisation of grinding equipment such as ball mills can provide significant cost and CO 2Reasons for use – benefits to the customer Benefits • Attainment of optimum throughput • Optimisation of specific power input • Simultaneous increase in efficiency, quality, safety and PROCESS OPTIMISATION FOR LOESCHE GRINDING PLANTS2021年11月27日 This document provides guidance on designing and optimizing bag filter systems used for dedusting applications It discusses key components of a dedusting system and factors to consider in the design such as Bag filter optimization in Cement Industry PPT2022年5月9日 By initiating a CL for an industrial cement vertical roller mill For these reasons, the total feed amount must be adjusted so that the ΔP is within the correct range 6,76Modeling of energy consumption factors for an industrial cement
.jpg)
INTERNATIONAL JOURNAL OF CIVIL AND STRUCTURAL
Minimum paste will mean less quantity of cement, less quantity of water, which will further mean increased economy, higher strength, lowershrinkage and greaterdu rability (Shetty, 2002)2018年7月1日 Energy and exergy analyses for a cement ball mill of a new generation cement plant and optimizing grinding process: A case A combined event modeling for feature extraction and the fully connected deep neural network model to predict the coarseness of cement particles is proposed and has improved efficiency resource use, the Energy and cement quality optimization of a cement grinding Stage of Cement Manufacture There are six main stages of the cement manufacturing process Stage 1: Raw Material Extraction/Quarry The raw cement ingredients needed for cement production are limestone (calcium), sand and clay (silicon, aluminum, iron), shale, fly ash, mill scale, and bauxite The ore rocks are quarried and crushed into smaller pieces of about 6 inchesHow Cement is Made Cement Manufacturing Process3 Factors affecting ball mill performance 4 Ball mill improvements case examples 5 Conclusions question time Introduction Cement manufacture is energy intensive o Cement manufacture consumes typically 3,100 – 3,400 MJ of fuel/t clinker 90 130 kWh / t cement in a modern plant, more for older or less efficient plants;Improvements in New Existing Cement Grinding Mills by Tim
.jpg)
Accretions in Cement Silos – Reasons for lump formation and
2019年12月31日 The formation of lumps and accretions in cement silos are of frequent occurrence in cement plantsSome of the common influencing factors for these lump formation are the fineness of cements, storage time in the silo, cement mill temperatures , the K 2 O contents in cement clinker , use of aged clinker in cement grinding or due to lack of periodic maintenance 2023年2月15日 What should we do to solve those problems? 1 First of all, it is necessary to do analyses including changes of nature of the ore, whether the amount of ore, water, sand and overflow size are normal Then do the measures to deal with them 2 Reduce the amount of feed to the mill until the working state of the ball mill returns to normal; 3 Appropriately reduce the 17 Signs of Problems with Ball Mills: Quickly Remove Hidden TroublesBefore the mill group is started the material removal group, the gas route group and the gear oil supply group have to be started For safety reasons and for the success of the start several checks are necessary before the mill is startedPROCESS TRAINING for operators of Vertical RAW MillsThe use of a ball mill is common in the cement production process, as it is efficient, costeffective, and able to This process step is very energy intensive and is one of the main reasons why cement production is representing a large share of global greenhouse gas emissions The objective of using a kiln in the Cement Production Demystified: StepbyStep Process and
.jpg)
PROCESS OPTIMISATION FOR LOESCHE GRINDING PLANTS
• Mill motor speed • Mill air flow/mill differential pressure • Temperature after the mill • Pressure before the mill • Grinding stock feed • Classifier speed • Mill fan speed • Water spraying • Hot gas • Fresh air Manipulated variables Disturbance variable Process measured value RelauchLMmaster 6 250814 11:47The roller grinding mill technology, patented in 1928 and continuously developed since then, has become synonymous with Loesche‘s pioneering engineering knowhow CEMENT BLAST FURNACE SLAG CEMENT RAW MATERIALCement Industry LoescheCEMENTS GROUND IN THE VERTICAL ROLLER MILL FULFIL THE QUALITY REQUIREMENTS OF THE MARKET DiplIng Th Fahrland, DrIng KH Zysk, Loesche GmbH, Duesseldorf, GermanyCEMENTS GROUND IN THE VERTICAL ROLLER MILL FULFIL THE 2020年11月22日 The grinding media play an important role in cement industry, and these balls suffered from severe wear during the grinding process of clinker inside horizontal millWear Resistance Improvement for Grinding Balls of Horizontal Cement
.jpg)
Raw mill Cement Plant
Raw mill is generally called cement raw mill, raw mill in cement plant, it refers to a common type of cement equipment in the cement plantIn the cement manufacturing process, raw mill in cement plant grind cement raw materials into the raw mix, and the raw mix is sent to the cement kiln to make cement clinker, next, clinker and other admixtures will be ground into finished cement by Ball mill liners are essential components in the operation of a ball mill They play a critical role in the following ways: Protecting the Mill: Ball mill liners protect the mill from wear and tear, reducing the need for repairs and prolonging the lifespan of the mill Improving Grinding Efficiency: By reducing the amount of friction between the grinding media and the material being processed Ball Mill Liner: What is it and How it Works AGICO Cement Plant1 cement mill ppt Free download as Powerpoint Presentation (ppt / pptx), PDF File (pdf), Text File (txt) or view presentation slides online The document discusses cement grinding systems It describes open circuit mills which have multiple compartments for coarse and fine grinding Closed circuit mills typically have two compartments and a separator to return oversized 1 Cement Mill2013年6月25日 Even if the cement is not lowalkali cement (below 060%), the amount is important for three reasons: Airentraining agents generally produce more air as the alkali content goes up Where the alkali occurs in the cement can affect this, but to get a first approximation, we need to track the equivalent alkali contentHow to Read a Cement Mill Certificate: Part 1
.jpg)
(PDF) Measurements of Vibration and Noise Level at Different Cement
2020年6月1日 The aim of this article is to compare Vibration and Noise measurements caused by different types of Machines at cement factories with the standard evaluation criteria of Vibration ISO 26314 EVS 2020年6月14日 What are the causes for an increase of Cement Mill trunnion Bearing temperature and what are the possible solutions Cement mill trunion bearing temperature may increase due to following reasons: 1 HP pump pressure is low 2 Cutoff time of HP pump after mill start up; 3 Mixing of contamination with oil; 4 LP pump oil flow is less; 5Improving Mill Shoe Bearing Reliability and Productivityincreases production of cement mill To seal air leakage in SKS Separator with uniform air gap increases output of cement mill Proper distribution of grinding media with appropriate sizes also enhanced productivity of cement mill Target To increase the TPH from 190 to 220 TPH (PPC) with maintaining quality parameter ie 8% residue on +45 micronINCREASING OUTPUT OF CEMENT GRINDING IN BALL MILLThe vertical cement mill is largescale cement grinding machine With advantages of energyefficient and stable quality, vertical roller mill is widely applied to many industries, such as cement, power, metallurgy, chemical and nonmetallic Vertical Cement Mill
.jpg)
BALL MILLS Ball mill optimisation Holzinger Consulting
and cement Roller presses are used mainly in combination with a ball mill for cement grinding applications and as finished product grinding units, as well as raw ingredient grinding equipment in mineral applications This paper will focus on the ball mill grinding process, its tools and optimisation possibilities (see Figure 1) The ball mill2017年9月11日 In this study, an extensive sampling study was carried out at vertical roller mill of ESCH Cement Plant in Luxemburg Samples were collected from mill inside and around the circuit to evaluate the (PDF) Performance Evaluation of Vertical Roller Mill in Cement 2020年9月10日 Mixture 3A2S design analysis including gradation, coarseness factor, and workability is shown in Fig 26 The cement provided a high resistance to the sulfates, present in the local soils Typical Type II/Type V cement mill test report results are presented in Table 219 Table 219 Cement mill test results Full size tableConcrete Mixture Design SpringerLinkProcess Training Ball Mill To Download this post + all manuals and books and Excel sheets and all notes I collected over my 23 years of experience in Cement industry click here now INTRODUCTION Comminution is a major unit operation in a cement plant, accounting for about 50 75 % of the total plant energy consumptionProcess Training Ball Mill INFINITY FOR CEMENT EQUIPMENT
.jpg)
Coal Mill Safety In Cement Production Industries
While this is not standard practice in cement production, cement plants in countries like India are often located far away from energy sources, so they rely on their own sources Power generation typically involves direct firing systems There is an air swept mill with direct pneumatic conveying through to the burnersThe ground material, known as mill feed, is discharged from the mill and sent to the next stage of the cement production process Importance of Cement Ball Mill Cement ball mills are essential in the cement production process for several reasons: 1 Grinding of Raw Materials: Cement ball mills are used to grind raw materials into fine powdersCement ball mill: A key component in cement productionMECHANICAL ELEMENTS OF TUBE MILLS this is a part of ASEC Academy training Courses SUMMARY the mechanical elements of a tube mill could be separated into elements which have a direct function with the grinding process (ie grinding media, liners, diaphragms) and into elements which can be considered as individual units which are connected to each other to a MECHANICAL ELEMENTS INFINITY FOR CEMENT EQUIPMENTThe finer the cement particles, the greater the surface area, and the higher the reactivity of the cement Here are some of the reasons why fineness is important for cement Early strength development: Finer cement particles hydrate more quickly and contribute to the early strength development of the concreteFineness of Cement: Definition, Importance, and How to Test It
.jpg)
(PDF) Dust Emission Monitoring in Cement Plant
2021年8月28日 This paper presents aspects of monitoring material dust emissions from stationary emission sources (monthly dust measurements performed on cement mill stacks—mill outlet and separator outlet)The vertical roller mill (VRM) is a type of grinding machine for raw material processing and cement grinding in the cement manufacturing processIn recent years, the VRM cement mill has been equipped in more and more cement Vertical Roller Mill Operation in Cement Plant2018年4月4日 We first discuss cement production and special nomenclature used by cement industrialists in expressing the composition of their cement products We reveal different types of cement products Cement Types, Composition, Uses and Advantages 2021年2月3日 The process can be optimized if the interaction effects of mill and separator factors on coarse return are understood However, the grinding process is complex and unstable, with nonlinear Coarse Return Prediction in a Cement Industry’s Closed Grinding
.jpg)
2 µm 5 µm Loesche
was used for the first time in an LM 462+2 for cement grinding in the Pu Shin mill works of Lucky Cement, Taiwan 1995 An LM 352+2 went into production in Fos sur Mer, Ciments Lafarge, France, as the first mill for grinding granulated blast furnace slag 1999 The first LM 562+2 was installed at Cementos Pacasmayo in Peru2023年11月1日 The design of the raw material grinding system should focus on the energysaving, vertical mill grinding system because of its powersaving, simple process to become a large cement plant, the use of a ball mill grinding system is no more than two reasons: first, the raw material is difficult to grind, such as high quartz sandstone content, the second is the 8 Tips For Cement Plant Design2017年4月1日 Productivity increase of the vertical roller mill for cement grinding Cement Industry Technical Conference, Conference Record, vol 39, IEEE (1997), pp 177194 View in Scopus Google Scholar Jorgensen, 2005 SW Jorgensen Cement grindinga comparison between vertical roller mill and ball millOperational parameters affecting the vertical roller mill A cement mill grinds the hard, nodular clinker from the cement kiln into the fine grey powder that is cement It is the last core equipment in the cement making process This paper demonstrates the use of Infinite Uptime’s autodiagnostics features to help detect faults for complex gear train assembly used to drive the cement millfault diagnosis for cement mill Infinite Uptime
.jpg)
Energy and exergy analyses for a cement ball mill of a new
2020年5月1日 Cement industry consumes a huge amount of electrical energy that is about 100 kWh/t (kWh per ton (10 3 kg) of cement) [16]In a cement plant, about twothirds of the total electrical energy is used for particle size reduction of raw materials and clinker [17]There is a diverse range of options to decrease the production expenses as well as CO 2 emissions that 2021年6月29日 Nowadays, ball mills are widely used in cement plants to grind clinker and gypsum to produce cement The research focuses on the mill speed as well as air classifier speed effect on the two Effects of Mill Speed and Air Classifier Speed on Performance of