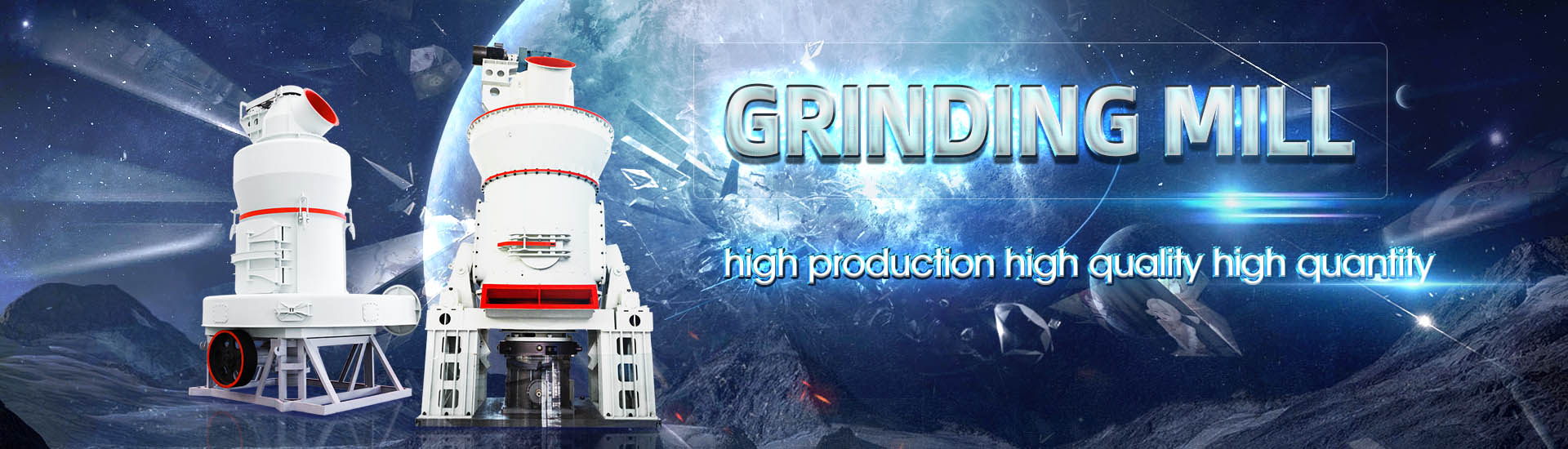
Standard ball loading of xmq24090 conical ball mill
.jpg)
试验室XMQ240×90型锥形球(棒)磨机技术参数
Technical Parameters of Laboratory Cone Ball (Rod) Mill XMQ 系列锥形球磨机,是一种实验室磨矿设备。 可供实验室湿法磨细矿石之用(其中 150 × 50 锥形球磨机亦可用于干磨),适用于 XMQ series cone ball mill is a laboratory grinding equipment for wet grinding of ore (150*50 cone ball mill can also be used for dry grinding) It is suitable for mineral feasibility study of GTEK Laboratory Ball/Rod MillXMQ series cone ball mill is a laboratory grinding equipment for wet grinding of ore (150×50 cone ball mill can also be used for dry grinding) It is suitable for mineral feasibility study of Ball mill introduction Mining, Lab2018年2月9日 XMQ cone ball mill is a laboratory grinding equipment for ore wet grinding It is a key equipment that is crushed after the material is broken It can wet and dry grinding (150 × Cone Ball Mill Super Fine Grinding Mill JXSC Machine
.jpg)
XMQ Laboratory conical ball mill Lab Ball Mill Jiangxi Victor
XMQ Series Cone Ball Mill is the necessary ore fine grinding equipment for fine grinding of ore It is applied in labs for processing and fine grinding of artificial placer materials and ores in 2015年6月19日 Use this online calculators for Motor Sizing and Mill sizing as well as mill capacity determinators In extracting from Nordberg Process Machinery Reference Manual I Ball Mill Design/Power Calculation 911MetallurgistThis document provides guidance on ball mill grinding processes It covers topics such as ball mill design including length to diameter ratios, percent loading, critical speed, and internals Ball Mill Grinding Process HandbookXmq240*90 Conical Ball Mill, Laboratory Mineral Processing Grinder, High Manganese Steel Stone Grinding Equipment, Find Details and Price about Planetary Ball Mill Mining Machine Xmq240*90 Conical Ball Mill, Laboratory Mineral Processing
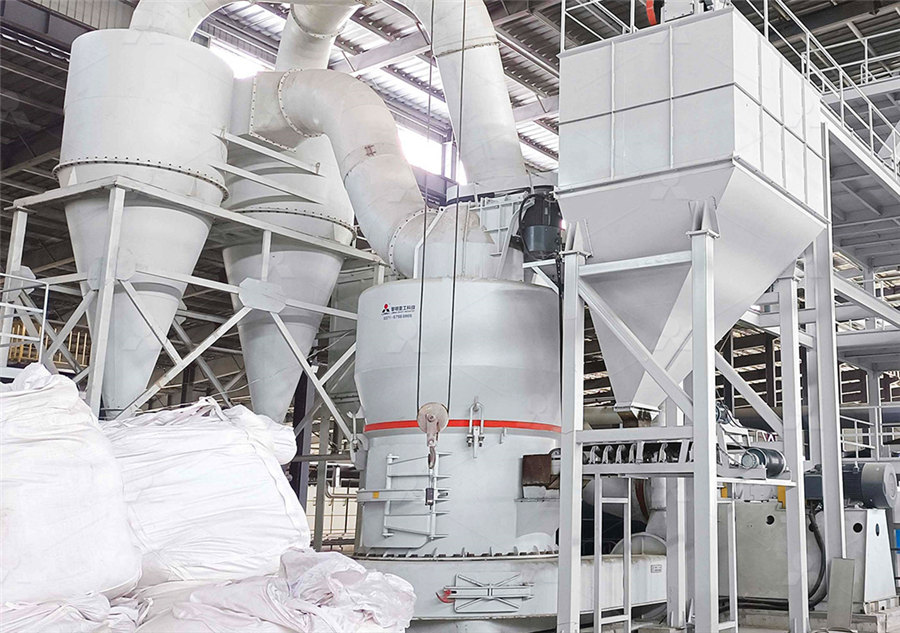
Conical Ball Mill Xmq Series 240*90 Grinding Mill Mining Iron Ore
Conical Ball Mill Xmq Series 240*90 Grinding Mill Mining Iron Ore Grinding Mill, Find Details and Price about Planetary Ball Mill Mining Machine from Conical Ball Mill Xmq Series 240*90 Xmq240*90 Lab Scale Conical Mineral Ball Mill For Mine Using , Find Complete Details about Xmq240*90 Lab Scale Conical Mineral Ball Mill For Mine Using,Ball Mill For Mine Using,Lab XMQ240*90 Lab Scale Conical Mineral Ball Mill for Mine Using2023年12月12日 Mining, metallurgical, enrichment and processing enterprises require a large amount of electricity consumption Among them, hydrometallurgical and enrichment enterprises currently consume 5060% (PDF) Control of ball mill operation depending on ball 2012年6月1日 As the cylinder starts to rotate, the grinding balls inside the cylinder crush and grind the feed material, generating mechanical energy that aids in breaking bonds, activating the catalyst, and Grinding in Ball Mills: Modeling and Process Control
.jpg)
(PDF) Energy Efficient Ball Mill Circuit – Equipment
2013年7月15日 For a standard ball mill circuit the circulating load is usually 250%, as established by Bond (1962) The classification efficiency depends directly on circulating load (Hukki and Eklund, 1965 2015年6月19日 The basic parameters used in ball mill design (power calculations), rod mill or any tumbling mill sizing are; material to be ground, characteristics, Bond Work Index, bulk density, specific density, desired mill tonnage capacity DTPH, operating % solids or pulp density, feed size as F80 and maximum ‘chunk size’, product size as P80 and maximum and finally the type of Ball Mill Design/Power Calculation 911Metallurgist2021年7月12日 standard Bond ball mill in time intervals of 05 min, 1 min, 2 min, and 4 min After each grinding run, the mass of the sample is measured, and the PSD is determinedA Review of Alternative Procedures to the Bond Ball Mill Standard Energy saving ball mill, overflow conical ball mill, ceramic conical ball mill for sale with best price Skip to content Home; Product Center; Ball Mill Parts Menu Toggle Ball Mill Shell; Ball Mill End Cover; Ball Mill Pinion; Ball Mill Bearing; Grinding Media Load: 0639t; Applications: It can be used to grind various ores and other Conical Ball Mill for Sale Wet Dry Conical Ball Mill Energy
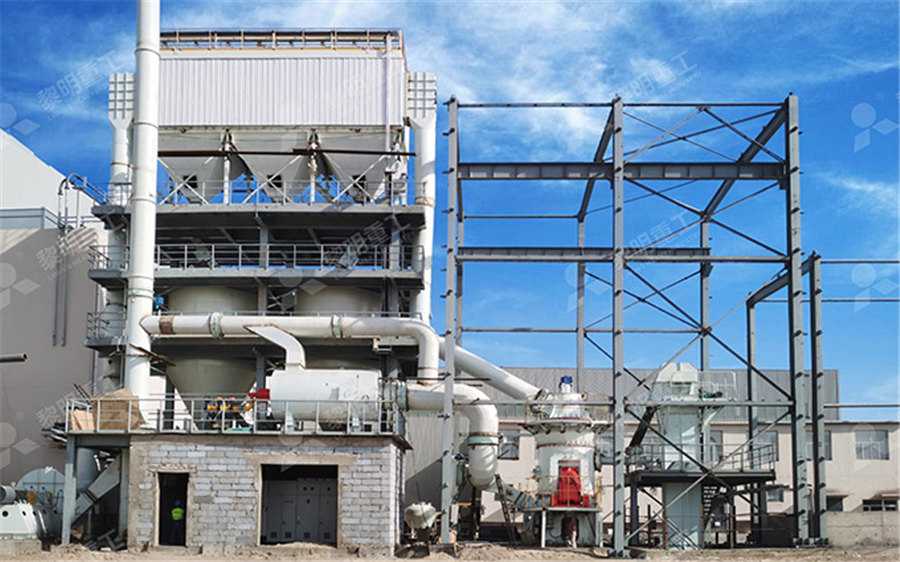
Conical Mill Grinding Tests 911Metallurgist
2016年3月4日 The plan of the work was to start with some given set of conditions for instance, a 16in cylindrical section, 4,006lb load of mixed balls, a trap rock feed of a given size, no moisture, mill level (Test 202); and keeping these conditions constant, vary one other condition, (Tests 203 and 204 in this case the feed rate, and determine the effect of this variation on the key factors affecting mill throughput and grinding efficiency: mill speed, ball loading, and liner lifter face angle (angle between the lifter face in contact with a grinding ball and the lifter base)A POWER BASED APPROACH FOR THE SELECTION AND COMPARISON OF BALL MILL 2022年3月15日 These mills consume enormous amounts of electrical energy (5060%); consequently, comminution costs roughly 60% of the overall investment in a beneficiation plant [2,3](PDF) Power consumption management and simulation of 2015年6月20日 A Ball Mill Critical Speed (actually ball, rod, AG or SAG) is the speed at which the centrifugal forces equal gravitational forces at the mill shell’s inside surface and no balls will fall from its position onto the shell The imagery below helps explain what goes on inside a mill as speed varies Use our online formula The mill speed is typically defined as the percent of the Ball Mill Critical Speed 911Metallurgist
.jpg)
AMIT 135: Lesson 7 Ball Mills Circuits – Mining
Mill Type Overview Three types of mill design are common The Overflow Discharge mill is best suited for fine grinding to 75 – 106 microns; The Diaphram or Grate Discharge mill keeps coarse particles within the mill for additional 2013年8月3日 In Grinding, selecting (calculate) the correct or optimum ball size that allows for the best and optimum/ideal or target grind size to be achieved by your ball mill is an important thing for a Mineral Processing Engineer AKA Calculate and Select Ball Mill Ball Size for Optimum This design uses heavy duty support rollers to drive the rotation of the mill shell directly Depending on the, the drive and support rollers can be polyurethane lined rollers or a series of rubber tyres Bulk Handling Techonolgies can Ball Mills and Ball Charging Bulk Handling Kolev et al (2021) –In press Improving the energy efficiency in tumbling mills with the use of Relo grinding media (MDPI) • Lab trials conducted using a standard Bond ball mill (@ Wardell Armstrong) • Standard Bond ball mill procedures were followed –only the RELO media PSD and mass of charge adjusted to match spherical mediaRethinking Grinding Efficiency in Ball Mills
.jpg)
Ball Mill Loading Dry Milling Paul O Abbe
Ball Mill Loading (dry milling) When charging a ball mill, ceramic lined mill, pebble mill, jar mill or laboratory jar use on a jar rolling mill it is important to have the correct amount of media and correct amount of product Charging a Dry Mill The general operation of a grinding mill is to have the product impacted between the balls as Conical Ball Mill The Conical Ball Mill is most ef cient when compare with cylindrical mill Classi cation and circulation within the mill is the principle of operation for the conical mill In a cylindrical mill most of the work is accomplished in only a portion of the mill cylinder length and the end corners are in effectiveBall Mill Catalogue2022年11月30日 Several types of ball mills exist They differ to an extent in their operating principle They also differ in their maximum capacity of the milling vessel, ranging from 0010 liters for planetary ball mills, mixer mills, or vibration ball Ball Mill: Operating principles, components, Uses, Advantages andThe document discusses grinding technology for limestone using ball mills It covers: 1 The properties and applications of limestone powder 2 Wet and dry grinding processes 3 Different types of grinding circuits including classical ball mill, airswept mill, birotator, and compound mill circuits 4 Details of mill internals such as ball charges and linings for compound and double Grinding Technology of Limestone With Ball Mills
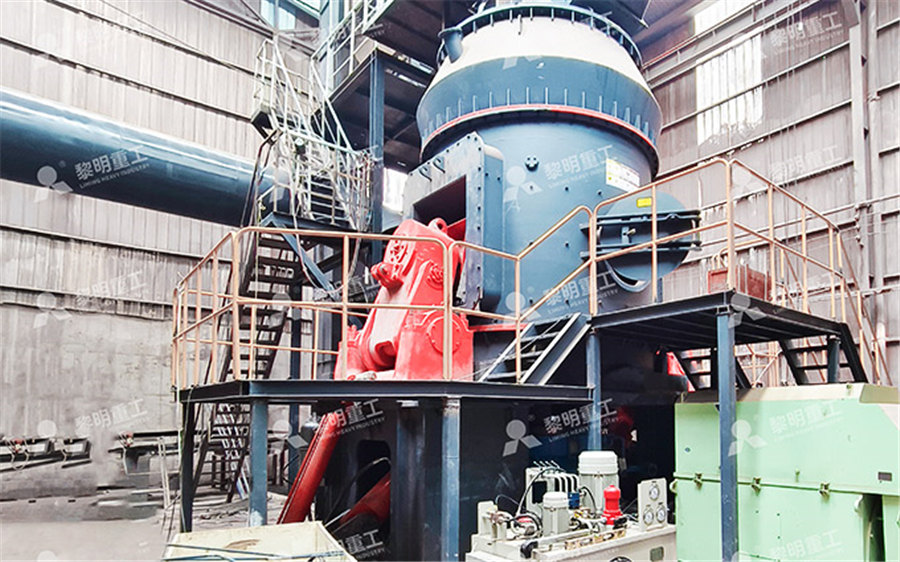
(PDF) Effects of Ball Size Distribution and Mill Speed and Their
2020年7月2日 A comprehensive investigation was conducted to delineate the effect of ball size distribution, mill speed, and their interactions on power draw, charge motion, and balls segregation in a 2018年2月1日 In another study to investigate ball size distribution on ball mill efficiency by Hlabangana et al [50] using the attainable region technique on a silica ore by dry milling, a threeball mix of Effect of ball and feed particle size distribution on the milling 2022年10月1日 Based on the standard procedure defined by Bond, the ball mill work index is determined by simulating a closed cycle dry grinding in a laboratory Bond ball mill until a stable circulating load of 250% is established (Bond, 1949, Bond, 1952, Bond, 1961) The ball mill work index is determined by Eq (10)A new methodology to obtain a corrected Bond ball mill work 2022年4月21日 Generally speaking, the ball mill load refers to the instantaneous load inside the mill, including the load of ore feeding, the circulating load, load of grinding medium, etc The accuracy of the detected load is a crucial condition for ensuring the quality of the ground products and the safety, continuity and operational stability of mineral processing productionSoft measurement of ball mill load under variable working
.jpg)
05 TO 15 TPH SMALL SCALE MINER’S BALL MILL
Standard mills are furnished with liners to avoid replacement of the shell; however, the mill can be obtained less liners This ball mill is often driven by belts placed around the center, although gear drive units with cast gears can be nonstandard mills BM1 to BM3, all ball mills without lifters) Bond standard ball mill (Fig 2(a); BBM) has a total volume of 22284 cm 3 , is fed with 700 cm of ore and 1638 cm of steel ballsBond´s work index estimation using nonstandard ball mills2017年2月13日 Conical Ball Mills The only conical ball mills on the market are those made by the Metso Fig 12 shows the construction of this type of mill It consists essentially of a short cylindrical section with conical feed and discharge ends The shell is made up of steel plates riveted or welded togetherBall Mills 911Metallurgist2013年4月1日 For a closed circuit ball mill flowsheet as represented in Figure 2, a simplified relationship (Equation 1) for relative capacity at different circulating load and classification efficiencies was Closed circuit ball mill – Basics revisited Request PDF
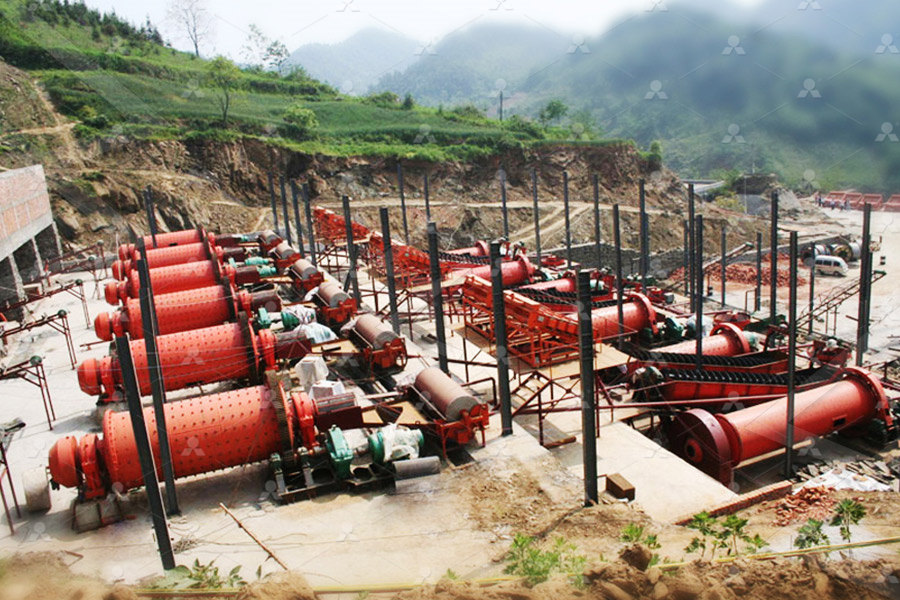
Monitoring the fill level of a ball mill using vibration sensing and
2019年10月19日 Ball mills are extensively used in the size reduction process of different ores and minerals The fill level inside a ball mill is a crucial parameter which needs to be monitored regularly for optimal operation of the ball mill In this paper, a vibration monitoringbased method is proposed and tested for estimating the fill level inside a laboratoryscale ball mill A vibration 2015年10月15日 A) Total Apparent Volumetric Charge Filling – including balls and excess slurry on top of the ball charge, plus the interstitial voids in between the balls – expressed as a percentage of the net internal mill volume (inside liners) B) Overflow Discharge Mills operating at low ball fillings – slurry may accumulate on top of the ball charge; causing, the Total Charge Calculate Ball Mill Grinding Capacity 911Metallurgist2023年10月1日 The Bond ball mill work index is an expression of the material’s resistance to ground and a measure of the grinding efficiency The test is a standardized methodology that ends when a circulating load of 250% is obtained In this paper, a new method based on the Population Balance Model (PBM) is proposed and validated to estimate the results Estimation methodology for Bond ball mill work index experiment Motor Power: The motor power of a ball mill is an important factor in determining its grinding capacity Ball mills can be equipped with motors ranging from 10 kW to 500 kW or more, depending on the size and desired output of the mill Speed: Ball mills are usually operated at speeds between 60% and 70% of the critical speedTechnical specifications and selection guide for ball mills
.jpg)
(PDF) Performance optimization of an industrial ball
2017年1月1日 An increase of over 10% in mill throughput was achieved by removing the ball scats from a single stage SAG mill These scats are non spherical ball fragments resulting from uneven wear of balls 2011年1月1日 A Panalytical (Epsilon1; 50 kV; Ag anode Xray tube) XRF spectrometer was used to analyze the elemental composition of pulverized rock samples at Sepro Mineral Systems (Langley, BC)Measurement of electrical energy consumption in a 2009年1月31日 The Bond ball mill grindability test is run in a laboratory until a circulating load of 250% is developed It provides the Bond Ball Mill Work Index which expresses the resistance of material to Procedure for determination of ball Bond work index in the 2019年8月1日 By comparison, the point load on the particles in ball mills is conducive to the attrition process (Bu et al, 2019b;Bu et al, 2020a) Abrasion and attrition result in rounder (more spherical Differences in dry and wet grinding with a high solid
.jpg)
Ball Mill an overview ScienceDirect Topics
The characteristic tumbling motion of these mills has given them the name ‘tumbling mills’, which include the ball mill, tube mill and rod mill Ball mills are horizontal rotating cylindrical or conical steel chambers, approximately one third to half full of steel, alloy steel or iron balls, like that shown in Fig 410 A–C , or flint stonesFactors such as ball size, rotation speed, and loading capacity also influence the overall grinding performance Types of Ball Mill which increase the efficiency of grinding Conical ball mills are suitable for both coarse and fine grinding Planetary Ball Mills: These mills consist of a rotating sun wheel and one or more grinding jars, Ball Mill Grinding Machines: Working Principle, Types, Parts 2017年7月1日 Increasing the ball loading from 30% did not further increase the product fineness but also increased the energy input, hence 30% was the optimum ball fillingThe effect of ball size distribution on power draw, charge motion 2019年11月1日 Grinding was performed using a XMQΦ240 × 90 laboratoryscale conical ball mill (Wuhan Exploring Machinery Factory, Wuhan, China) The diameter and length of the intermediate cylinder part of mill were 240 and 90 mm, respectively (Fig 2) The operational speed was kept at 96 rpm (68% critical speed) according to the literature [13]Differences in dry and wet grinding with a high solid
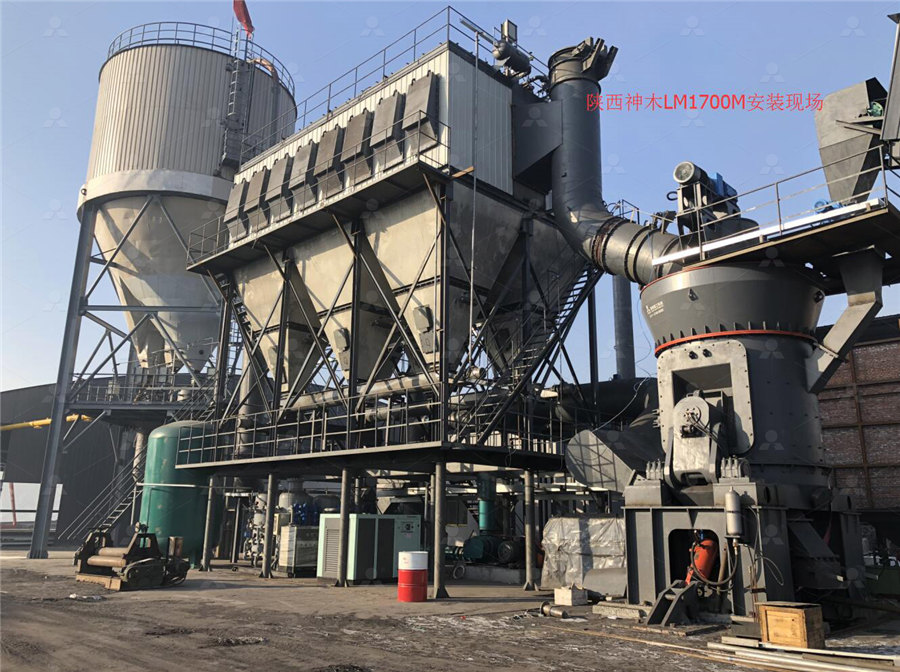
Conical Ball Mill And Design Manufacturer Tongli Machinery
Mill Shell: The foundation of the conical ball mill, the mill shell, is a cylindrical structure made of premiumgrade steel Tongli heavy machinery is equipped with a large annealing furnace of 65x65x20m and a 65x65x20m large sandblasting room, which can conduct overall heat treatment and sandblasting on the ball mill to ensure the service life and appearance of the 2013年12月1日 Percent passing of milled Al 2 O 3 powder as a function of particle size for varying ball diameter Rotation speeds are (a) 50 rpm, 100 rpm, and (c) 153 rpmEffect of ball size and powder loading on the milling efficiency