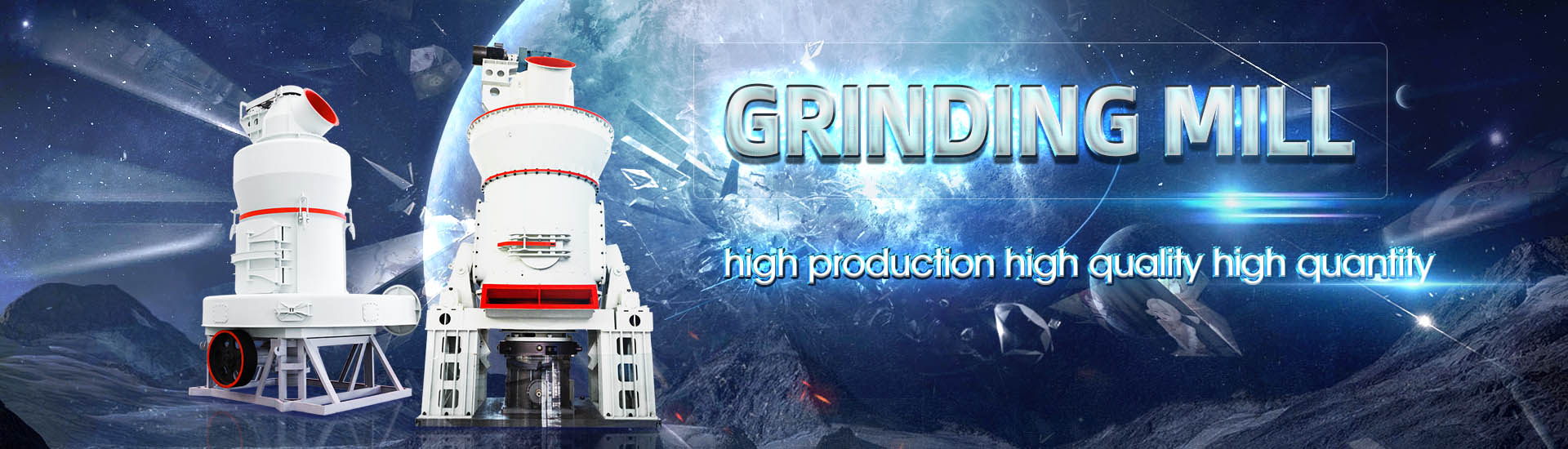
Electricity consumption for concrete production
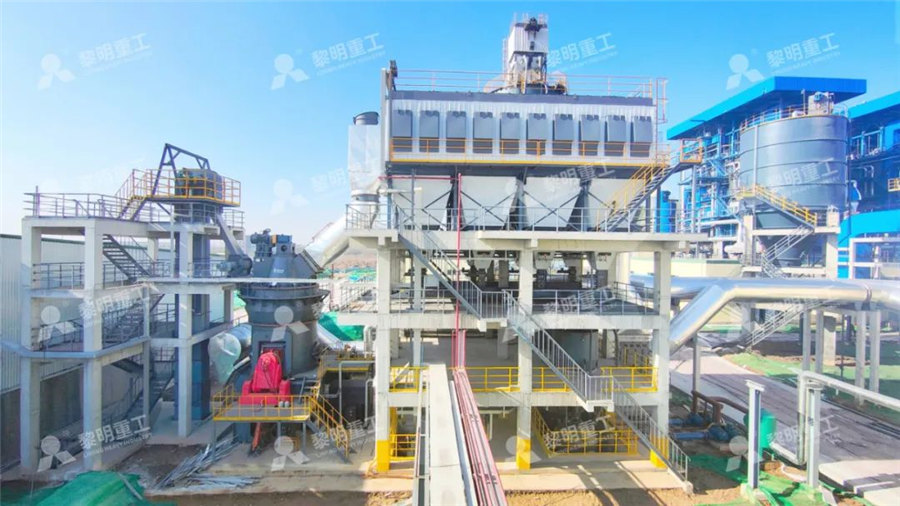
Electricity use per tonne of cement in selected countries and
BAT = energy intensity covers the process up to the liquid steel stage, ie it does not include energy used in casting and rolling, or energy used by captive thermal utilities (which are included in reported energy intensity)What is the role of cement in clean energy transitions? Key strategies to cut carbon Cement IEA International What is the role of cement in clean energy transitions? Key strategies to cut carbon emissions in cement production include improving energy efficiency, switching to lowercarbon fuels, promoting material efficiency (to reduce the Cement IEA International Energy Agency2011年5月1日 The electrical energy consumed in cement production is approximately 110 kWh/tonne There is potential to optimize conventional cement clinker grinding circuits The A critical review on energy use and savings in the cement industries
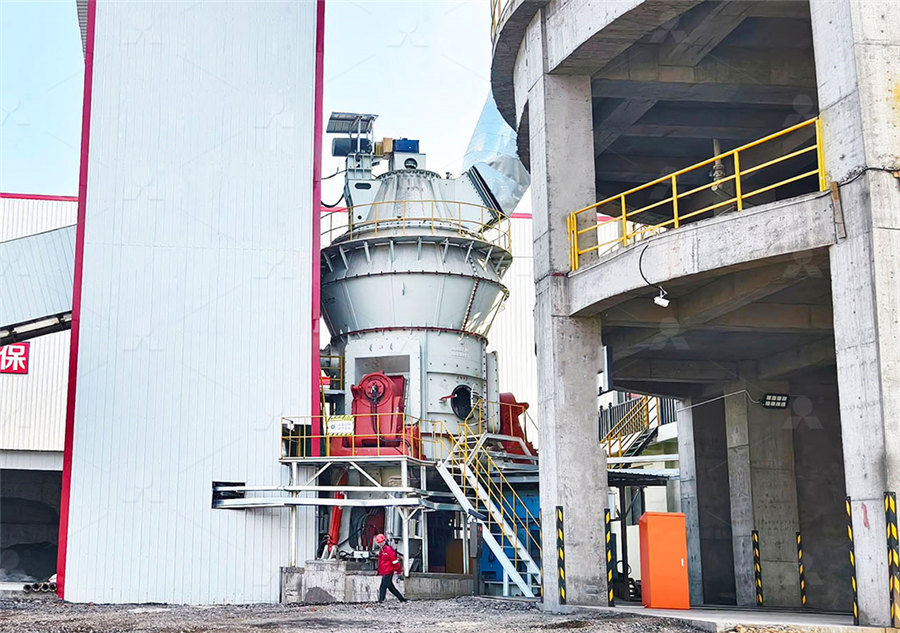
A decision support tool for cement industry to select energy
2020年3月1日 Cement accounts for 83% of total energy use in the production of nonmetallic minerals and 94% of CO2 emissions Both financial and technical aspects need to be taken 2020年10月1日 The impact of improving the electrical energy efficiency of cement production is offset by the increased electricity demand arising from the use of carbon capture and other The impact of future power generation on cement demand: An 2022年5月9日 As one of the most energyintensive industries, cement plants consume around 100 kWh of electrical energy for each ton of their production This can be counted yearly as Modeling of energy consumption factors for an industrial cement 2023年9月26日 Cutting emissions from cement production is difficult due to the present reliance on carboncontaining raw materials and hightemperature heating requirements Energy and Cement – Analysis IEA International Energy Agency
.jpg)
Global database of cement production assets and upstream
2023年10月13日 According to the World Cement Association, global cement production is expected to reach 82 billion tonnes by 2030 6, 7, 8, 9 Thus, in Western Europe 9, 10, the Key energy and emissions parameters, including thermal and electrical energy intensity, recovered energy and CO2 intensity, are computed per tonne of cement produced along with Benchmarking of Energy Consumption and CO2 Emissions in 2018年5月25日 An important energy consumption index in cement production is electricity consumption whose accurate prediction provides basis for scientific production scheduling and Prediction of electricity consumption in cement production: a time Download scientific diagram Specific fuel and electricity consumption per ton of cement produced can also be utilized as a geopolymer to totally replace cement in concrete productionSpecific fuel and electricity consumption per ton of
.jpg)
Energy Efficiency Improvement and Cost Saving Opportunities for
Final energy consumption in US cement production by fuel, 1970 6 Primary energy intensity of US cement and clinker production, 1970 to 2010 13 Figure 7 Specific fuel and electricity consumption per ton of cement concrete, which is a combination of cement, mineral aggregates and water Concrete is a key building 2023年11月1日 The total electricity consumption in the ehCHS case is completed with the This study is supported by the Innovandi Global Cement and Concrete Research Network, as part of its Core Project 12: Metaanalysis on the use of electric energy for clinker production The authors want to acknowledge the industrial mentors of Decarbonization of cement production by electrification2013年7月1日 The industrial sector, which encompasses manufacturing, mining, agriculture, and construction, accounted for almost a third of total US energy use in 2012Energyintensive manufacturing accounted for a little more than half of total industrial energy use Although the cement industry used only onequarter of one percent of total US energy, it is the most The cement industry is the most energy intensive of all 2023年5月1日 The concrete industry has made a firm commitment to reduce its excessive carbon footprint, essentially related to clinker production Recycled cement (RC) from the thermoactivation of hardened cement waste at low temperature is a very promising approach, tackling the reduction of the clinker factor, the reuse of construction and demolition waste and Recycled cement production energy consumption optimization
.jpg)
Energy Production and Consumption Our World in Data
Primary energy consumption Total energy consumption How much energy do countries across the world consume? This interactive chart shows primary energy consumption countrybycountry It is the sum of total energy consumption, including electricity, transport, and heating We look at electricity consumption individually later in this article2017年8月28日 The production of 1 m³ of concrete requires 2,775 MJ of energy This energy comes mostly from oil burning, which generates CO2 2775 MJ of energy is produced by 037 barrels of oil Saving concrete, eg by adopting appropriate building solutions, means therefore not only reducing fossil fuels consumption, but also pollutant emissionsEnergy consumption in production of concrete2024年5月7日 Annual data and statistics for US energy production and consumption Skip to subnavigation US Energy Information Administration EIA Independent Statistics and Analysis Menu Sources Uses; Nuclear electric power: 8%: Total primary energy consumption 9359 quadrillion Btu; By fuel/energy source: share of total US energy facts data and statistics US Energy Information 2024年2月2日 The cement industry ranks as the thirdlargest consumer of industrial energy worldwide, responsible for approximately 7% of global industrial energy consumption and ~ 7% of global CO 2 emissions, faces particular challenges in achieving sustainability due to its inherent energy and emissionsintensive production processes [10, 11]Benchmarking of Energy Consumption and CO2 Emissions in
.jpg)
The Environmental Profile of Clinker, Cement, and Concrete: A Life
2022年3月6日 Concrete is the mostused material in the construction industry, and the second mostused after water Cement is the main component of concrete A total of 8% of global CO2 emissions correspond to the cement industry; CO2 is the main greenhouse gas contributing to global warming To mitigate climate change, it is necessary to design buildings with a lower 2013年3月13日 In this paper, we review the energy requirements to make materials on a global scale by focusing on the five construction materials that dominate energy used in material production: steel, cement, paper, plastics The energy required to produce materials: constraints 2020年1月1日 On the one hand, regarding the material of concrete consumption, the EBCS, DOE, and ACI methods were castoff in an excess amount (522 kg/m³, 40 kg/m³, and 20 kg/m3) of cement, respectively (PDF) Assessment on Cement Production Practice 2011年5月1日 Specific energy consumption in cement production varies from technology to technology The dry process uses more electrical but much less thermal energy than the wet process In industrialized countries, primary energy consumption in a typical cement plant is up to 75% fossil fuel and up to 25% electrical energy using a dry processA critical review on energy use and savings in the cement industries
.jpg)
Comparison of energy and environmental performance between
2024年3月8日 The electricity consumption relative to the mixing of 1 ton of HMA and WMA is calculated as a portion of the electricity spent in a mixing cycle for an average mass of 245 tons of asphalt concrete The electricity spent in a mixing cycle is estimated as follows: (12) E C e = P × d e × 1 3600 where: E C e = electricity consumption [kWh 2022年5月9日 Cement production is one of the most energyintensive manufacturing industries, and the milling circuit of cement plants consumes around 4% of a year's global electrical energy production It is Modeling of energy consumption factors for an industrial cement 2018年5月25日 An important energy consumption index in cement production process is electricity consumption whose accurate prediction is of great significance to optimize production However, it is difficult to establish an accurate electricity consumption forecasting model in cement production, for some problems such as the time delay, uncertainty and nonlinearity existing in Prediction of electricity consumption in cement production: a 2022年11月17日 Looking at the global electricity consumption of cement production (Fig 4b), Canada and the US appeared as the top two countries, with more than 130 kWh t −1 of cement in 2018 due to the Modernizing cement manufacturing in China leads to substantial
.jpg)
Decarbonising cement and concrete production: Strategies,
2024年6月1日 Decarbonising cement and concrete production: Strategies, The power island generates electricity and in natural gas cases, The traditional linear model of production, consumption and disposal is being replaced by a circular approach that aims to close the resource loop and minimise waste generationWith more and more strict Energy conservation and environmental protection policy published, excess production capacity, and severe market competition, energy conservation in cement grinding plant is the key for Cement Manufacturing Plant to achieve the purpose of reducing power consumption Fuel and electricity costs are the single largest Power Consumption of Cement Manufacturing Plant2024年6月28日 The United Kingdom's electricity consumption for iron and steel production has mostly declined over the years Basic Statistic Daily electricity consumption in France 20192024;UK: electricity use for iron and steel production 2023 Statista2023年1月1日 The addition of SCMs in cement makes it economically cheaper and also environmentally friendly SCMs reduce energy consumption in cement production, hence reduce CO 2 emissions associated with the production of concrete with the added benefit that the industrial waste streams are recycled and turned into valueadded streamsProduction of cement and its environmental impact ScienceDirect
.jpg)
OpenConcrete: a tool for estimating the environmental impacts
2022年10月4日 As such, a robust and methodological means of calculating the environmental impacts of concrete production which provides for specific conditions (eg, kiln efficiencies, electricity mixes) will assist in understanding and monitoring the burdens of concrete production, allowing for regionspecific decision making toward concrete with improved environmental 2011年7月15日 Some other facts about aluminium: the least efficient smelters may use as much as 20kWh/kg Al – relying on very cheap coal fired power in China, which dominates world smelting capacity, and although China does Electricity consumption in the production of 2021年7月15日 However, comparing this additional energy consumption in processing the concrete waste with the energy required to process the raw material for Portland cement production, it should be significantly lower due to: i) the higher porosity of the concrete waste, being easier to mill than the natural raw material used in the clinker production; and ii) the raw Comparison of energy consumption and carbon emissions from 2020年3月23日 Concrete is the world’s most widely used manmade material, with consumption growing exponentially as populations and incomes rise 1,2,3Concrete’s popularity, which stems from its low cost Climate and health damages from global concrete production
.jpg)
Electric Cement Production: The Technologies
2024年6月17日 Cambridge Electric Cement Cambridge Electric Cement is a novel approach to the electrification of cement that integrates cement production with the production of steel in an electric arc furnace (EAF) The process is premised on the fact that spent cement powder from concrete waste has a similar composition to the slag used in the EAF processvi Improving Thermal and Electric Energy Efficiency at Cement Plants: International Best Practice Cement is paramount for economic development and poverty reduction in emerging markets Along with aggregates and water, cement is the key ingredient in the production of concrete, and, as such, is an essential construction materialIMPROVING THERMAL AND ELECTRIC ENERGY EFFICIENCY AT In contrast, concrete production is far more decentralised (Fig 5), with production typically at the local level of batching plants (or prefabrication factories), with onsite production widespread for the informal sector in developing countriesThis difference in the supply chain distribution makes changes easier to enact for a given site, but less easy to cascade horizontally along the Concrete Production an overview ScienceDirect Topics2022年1月1日 There are different types of permanent magnets (PMs) used in wind turbines, such as the samariumcobalt and the neodymiumironboron (NdFeB) (Venås, 2015)The most common PM in wind turbines is NdFeB because it is 25 stronger than the samariumcobalt magnet (Venås, 2015)The NdFeB was developed in the 80s by General Motors and its Material consumption and environmental impact of wind turbines
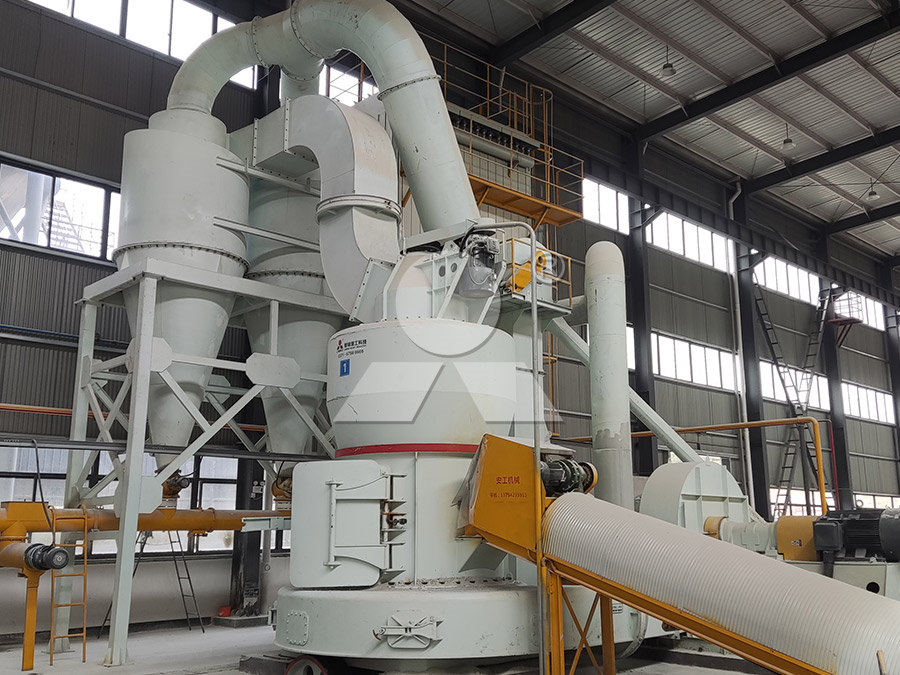
Impacts of booming concrete production on water resources worldwide
2018年1月8日 Concrete is the mostused construction material worldwide Previous studies on the environmental impacts of concrete production have mainly focused on the materials involved and energy consumption 2019年3月8日 and water, cement is the key ingredient in the production of concrete, and, as such, In addition, electricity consumption can be reduced by up to 1 kWh per ton of clinker 18IMPROVING THERMAL AND ELECTRIC ENERGY 2023年10月29日 The cement industry is a major contributor to carbon emissions, responsible for 5–8% of global emissions This industry is expanding, particularly in emerging economies, and it is expected that CO2 emissions will Evaluation of Carbon Emission Factors in the Cement The Australian Energy Statistics is the authoritative and official source of energy statistics for Australia and forms the basis of Australia’s international reporting obligations It is updated annually and consists of historical energy Australian Energy Statistics energygovau
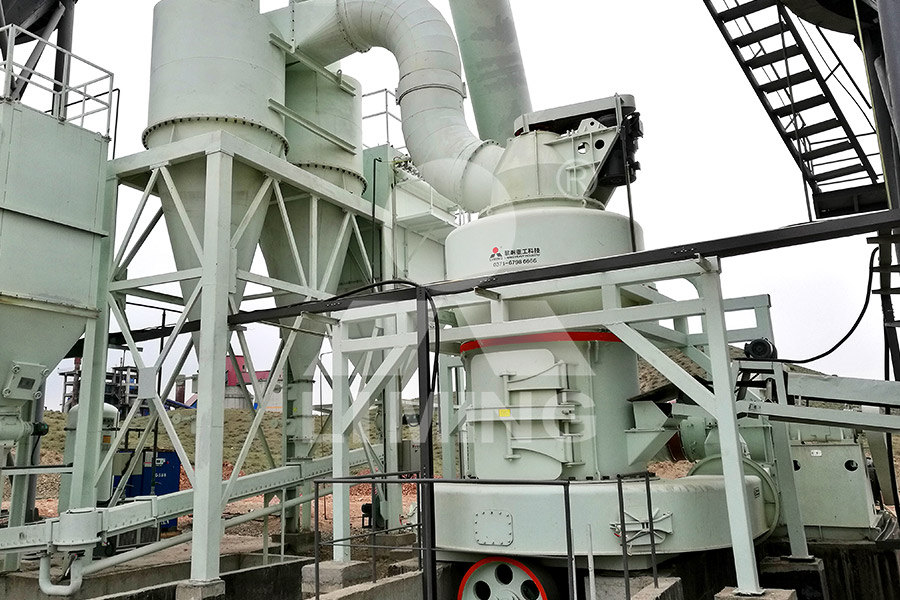
OPPORTUNITIES FOR REDUCING WATER CONSUMPTION IN CONCRETE PRODUCTION
Eproceedings of the 38th IAHR World Congress September 16, 2019, Panama City, Panama 4665 Table 3 Water figures for energy production used in different concrete constituents or activities Component Electricity Fuels l/kg l/kg Coarse aggregates 0 2261 00052 00178 Fine aggregates 0 0622 00053 00089 Cement 0 19659 00005 10237 In this study, the water 2024年2月19日 Comparison of energy and environmental performance between warm and hot mix asphalt concrete production: A case study The electricity consumption relative to the mixing of 1 ton of HMA Comparison of energy and environmental performance between 2024年11月19日 The electricity consumption of a concrete plant depends on various factors, including its size, type, production capacity, and level of automation For a precise calculation, you’d need to measure the plant’s actual energy usage based on production data and the specific equipment in useHow much electricity does a concrete plant use?2021年7月28日 Energy efficiency in a cement plant is measured as a combination of two factors, viz, Thermal Energy Consumption and (2) Electrical Energy Consumption The former specifically measures the kiln performance while the latter measures the overall performance of the plant Thermal Energy Consumption (measured as MJ/t clinker)Indian Cement Sector CMA
.jpg)
Recycled Aggregates for Concrete Production: StateoftheArt
2016年10月2日 Only the chipping of concrete according to type 1 and type 2 (as defined in the above standard) can be used for concrete production Type 1 RA can be associated to a RCA: it contains at least 90 % of concrete and natural aggregates, not more than 10 % of clinker, nonpored bricks, sandlime bricks, less than 2 % of other mineral materials and less than 1 % of 2017年8月28日 The production of 1 m³ of concrete requires 2,775 MJ of energy This energy comes mostly from oil burning, which generates CO2 2775 MJ of energy is produced by 037 barrels of oil Saving concrete, eg by adopting appropriate building solutions, means therefore not only reducing fossil fuels consumption, but also pollutant emissionsEnergy Consumption In Production Of Concrete2022年10月4日 As the increasing global consumption of concrete drives notable environmental burdens from its production, particularly greenhouse gas (GHG) emissions, interest in mitigation efforts is increasingOpenConcrete: a tool for estimating the environmental impacts