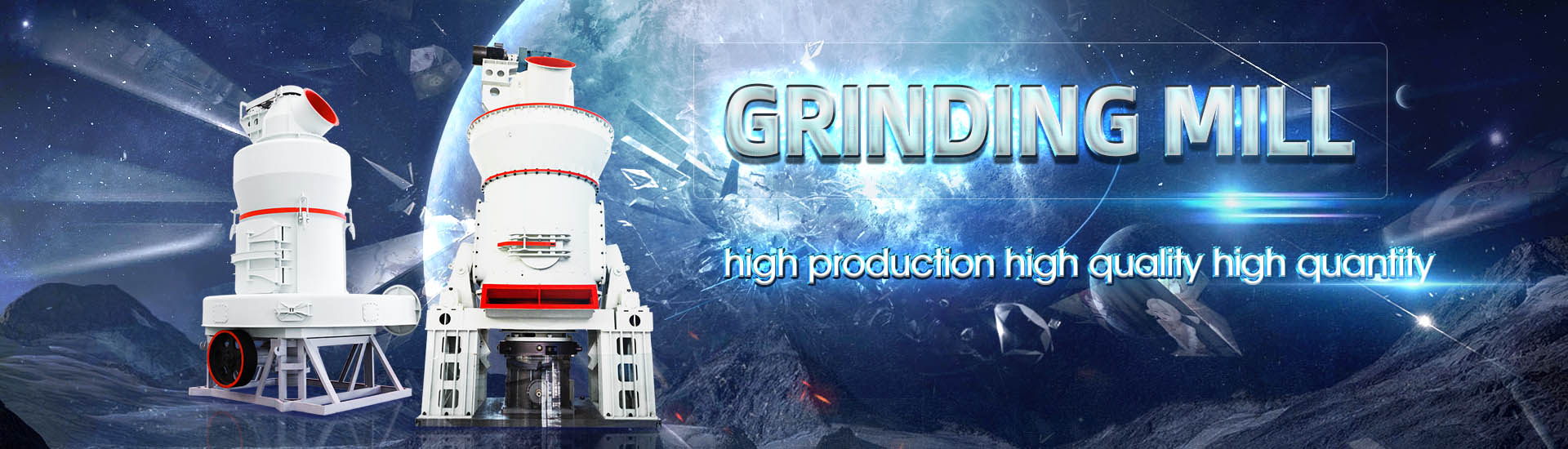
Reduce the fineness of raw coal and increase coal mill output
.jpg)
Improved Coal Fineness Improves Performance, Reduces Emissions
Since that time, pulverizer capacity has increased to meet the corresponding growth in unit sizes with incremental improvements in grinding efficiencies The pulverizer 展开2015年11月1日 Coal mills are one of the critical power plant components that influence the efficiency and reliability of a coal fired power plant The coal mill grinds the raw coal into fine A unified thermomechanical model for coal mill operationCoal Pulveriser Mill Function and Operation details Pulverizer as shown in fig1 is used in power plant to reduce the size of the incoming raw coal to a fineness thatPulveriser Mill Performance Analysis Optimisation in Supermajor components of a coalfired thermal power station These are used for grinding the raw coal so that the pul are four major mechanisms that happen during the coal crushing in the mills A Study on 500 MW Coal Fired Boiler Unit’s Bowl Mill Performance
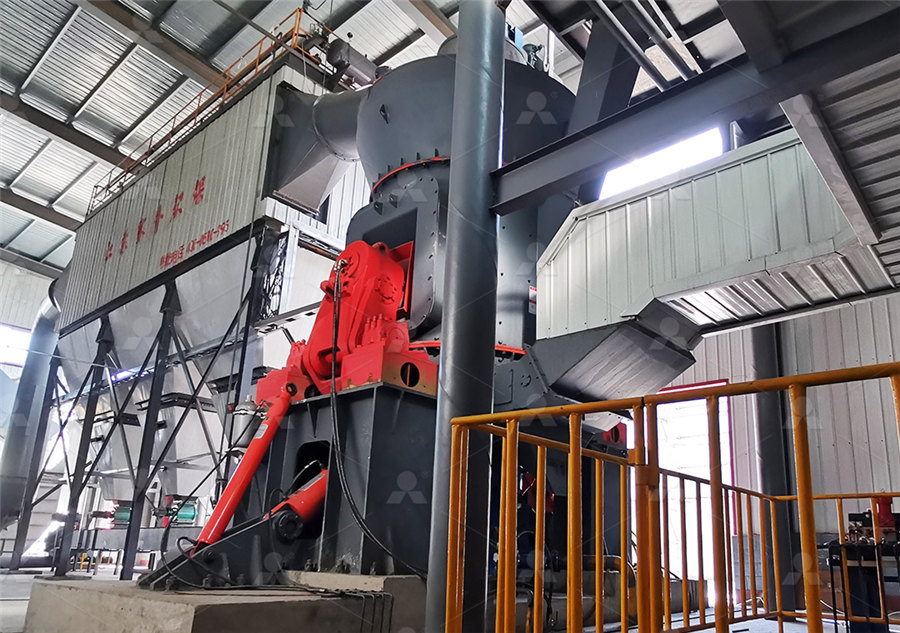
Effect of particle properties on the energysize reduction of coal in
2018年6月15日 Quantitative analyses of energysize data indicate that grinding energy efficiency could be improved if raw coal in low ash content is chosen Except for energy saving, less 2017年11月15日 A method for choosing the optimum fineness of coal in pulverisedfuel boilers is presented This method is based on economic criteria and takes into account variations of Optimisation of coal fineness in pulverisedfuel boilersspindle coal pulverising mill’s performance to facilitate optimal plant performance Plant design and mill’s acceptance test data was analysed to understand the design and subsequent Performance optimisation of vertical spindle coal pulverisersAs many are technologies constantly striving performance for pulverised available to to improve overall plant performance power plant operators, or biomass flow balancing can achieve is Optimising fuel flow in pulverised coal and biomassfired boilers
.jpg)
Coal Pulverizer Design Upgrades to Meet the Demands of Low
INTRODUCTION As part of the continuing effort to improve combustion performance commensurate with reduced emissions in coalfired power plants, Riley Power Inc (RPI), a ABSTRACT: The paper describes the beneficial application of online coal flow measurement and control and online coal fineness measurement for optimization of the combustion process CPRI Online Coal Flow Balancing and Fineness Adjustment年11月17日 20 131Fineness Fineness is an indicator of the quality of the pulverizer action Specifically, fineness is a measurement of the percentage of a coal sample that passes through a set of test sieves usually designated at 50, Coal mill pulverizer in thermal power plants PPT2019年11月7日 pressure between inlet and outlet of coal mill, the treatment of coal mill has been improved obviously The speed of coal feeder is 320 350 r/min, the output of coal mill is 5155 t/h, and the Optimization and transformation of 300MV units steel ball coal mill
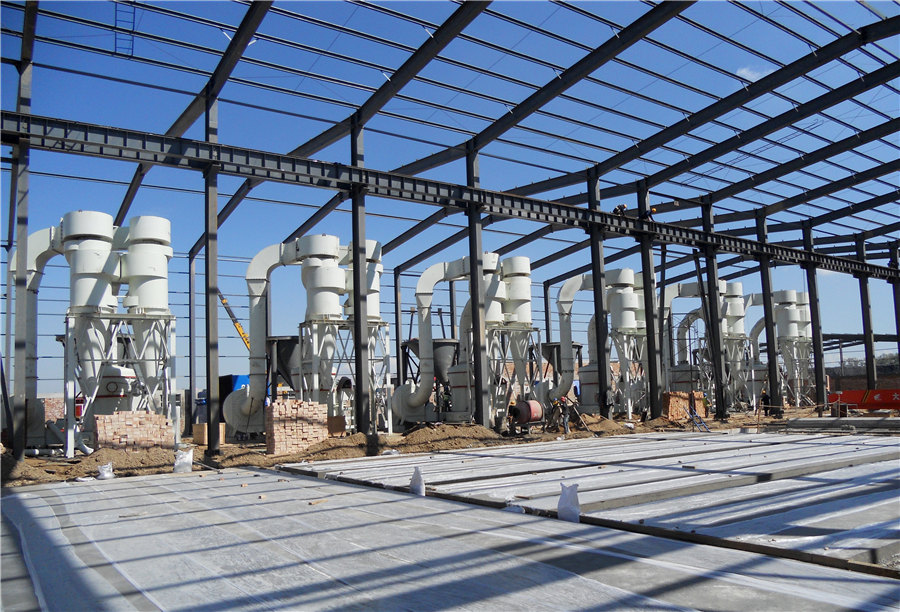
ATOX® Coal Mill FLSmidth Cement
Our ATOX® Coal Mill has large rollers with great grinding capability of virtually all types of raw coal The rollers work harmoniously with a highlyefficient separator and feed sluice to consistently and reliably deliver coal meal to your desired 2021年8月1日 pressure is not less than 28Mpa(5)Low quality coal causes insu fficient output of coal mill Fault treatment and improvement and Optimization: (1) check the operation status of primary fan,(PDF) Fault analysis and optimization technology of HPB coal feed, T / h; m the quality of a fixed length of raw coal on the scraper, kg; V coal feeder measured scraper speed, M / h; L the length of raw coal on the scraper, M Table1Optimization and transformation of 300MV units steel ball coal mill Effect of fineness Maximum Mill capacity vs PF fineness at 12 % Raw coal moisture and at Coal HGI 100110 3300 3400 3500 3600 3700 3800 3900 4000 4100 65 70 75 80 85 Mill output at raw coal moisture and at Coal HGI 100110 31Pulverizer Plant OM Aspects
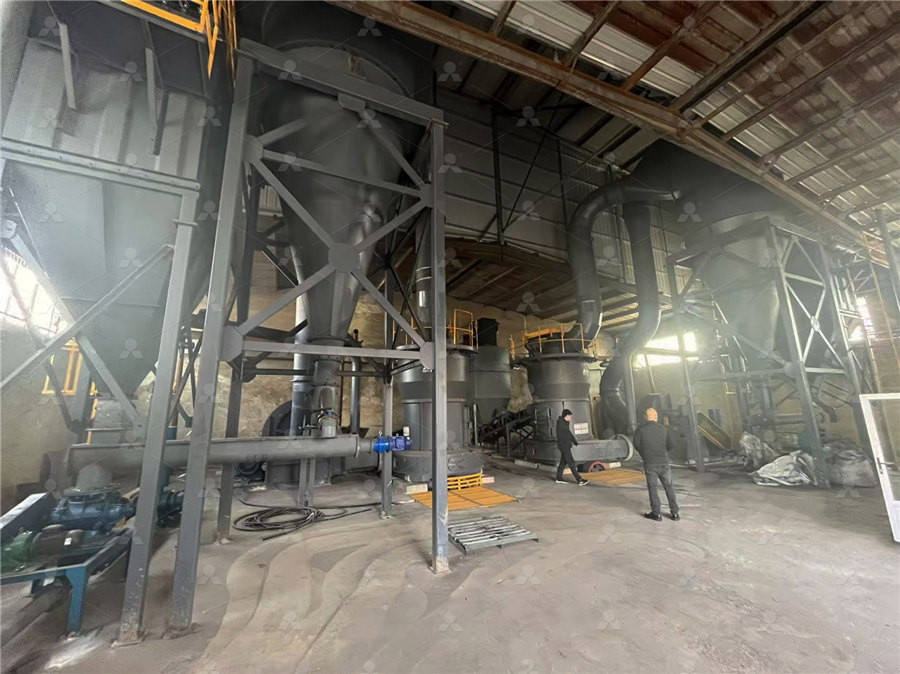
Effect of Coal Quality and Performance of Coal pulverisers / Mills
2021年3月31日 3 COAL QUALITY –IMPACT COMPLEX • Pulverizer capacity, fineness wear • Slagging fouling in boiler • Corrosion erosion in boiler • Ash characteristics affect efficient collection in ESP • Affects furnace convective pass heat absorption boiler availability • Quantification of impact is complex 31Mar2021 total output power solutions 32004年4月8日 There have been very few conversions of UK coal mills from static to dynamic classifiers But test experience with a dynamic classifier at Powergen's RatcliffeonSoar power station has demonstrated significant fineness gain, especially at the coarse end of the particle size distribution curve, and minimal effect on mill coal throughput and operability, with greatly Dynamic classifiers: a fine way to help achieve lower emissionsInstead of maximizing coal fineness improvements only, the dynamic classifiers can be used to increase mill capacity while improving the preretrofit fineness level somewhat or the capacity can be maximized by allowing the fineness to drop to lower levels The enhancedPulverizer Fineness and Capacity Enhancements at Danskammer 2017年8月1日 This paper presents a coal mill model that considers the effect of coal moisture on its accuracy This mathematical model is derived through the analysis of mass flow, heat exchange, and energy transferring balances in which all heat input into or output from the coal mill are calculated quantitatively to reduce the number of unknown parameters that need to be Modeling of a medium speed coal mill ScienceDirect

Pulverizer Capacity is not simply “tons throughput per hour!”
the fineness is reduced from about 75% passing 200 mesh to 45% passing 200 mesh, as much as 30% more coal throughput can be pushed through the pulverizers The previous example is often inadvertently done by increasing primary airflows or opening classifier blades up to increase the coal flow to the furnace by sacrificing coal fineness This PDF On Dec 1, 2015, M Siddhartha Bhatt published Effect of moisture in coal on station heat rate and fuel cost of Indian thermal power plants Find, read and cite all the research you need on (PDF) Effect of moisture in coal on station heat rate 2017年8月1日 This paper presents a coal mill model that considers the effect of coal moisture on its accuracy This mathematical model is derived through the analysis of mass flow, heat exchange, and energy transferring balances in which all heat input into or output from the coal mill are calculated quantitatively to reduce the number of unknown parameters that need to be Modeling of a medium speed coal mill ScienceDirect2011年10月1日 For most static classifier designs in use, there is the ability to increase coal fineness This generally involves one or more of the following three adjustments: Insertion or lengthening of the Improved Coal Fineness Improves Performance, Reduces Emissions
.jpg)
Pulveriser Mill Performance Analysis Optimisation in Super
Coal Pulveriser Mill Function and Operation details Pulverizer as shown in fig1 is used in power plant to reduce the size of the incoming raw coal to a fineness that will efficiently burn in a furnace [1] Fig 1 H P Pulveriser actual view and parts As in Introduction This article concerns itself with vertical grinding mills used for coal pulverization only (coal pulverizers), although vertical grinding mills can and are used for other purposes The 3D model in the saVRee database represents a vertical grinding bowl millOther grinding mill types include the ball tube mill, hammer mill, ball and race mill, and , roll and ring millVertical Grinding Mill (Coal Pulverizer) Explained saVRee21 Particle fineness measurements and control 14 211 Commercially available systems/equipment for online particle size measurement 14 22 Coal fineness optimisation 16 221 Ensuring the correct/optimal raw coal size and its supply to the mill 16 222 Maintenance of grinding elements and setting the correct grinding pressure 17Optimising fuel flow in pulverised coal and biomassfired boilersVertical Coal Mill, also known as coal mill, for superfine grinding of raw coal, soft coal specifically for cement, power plant, steel mill and other fields Its special design structure and production process creates the higher production efficiency with lower energy consumption, less dust, lower noise than ball mill, which meets national standard of energy saving industryVertical Coal Mill Great Wall
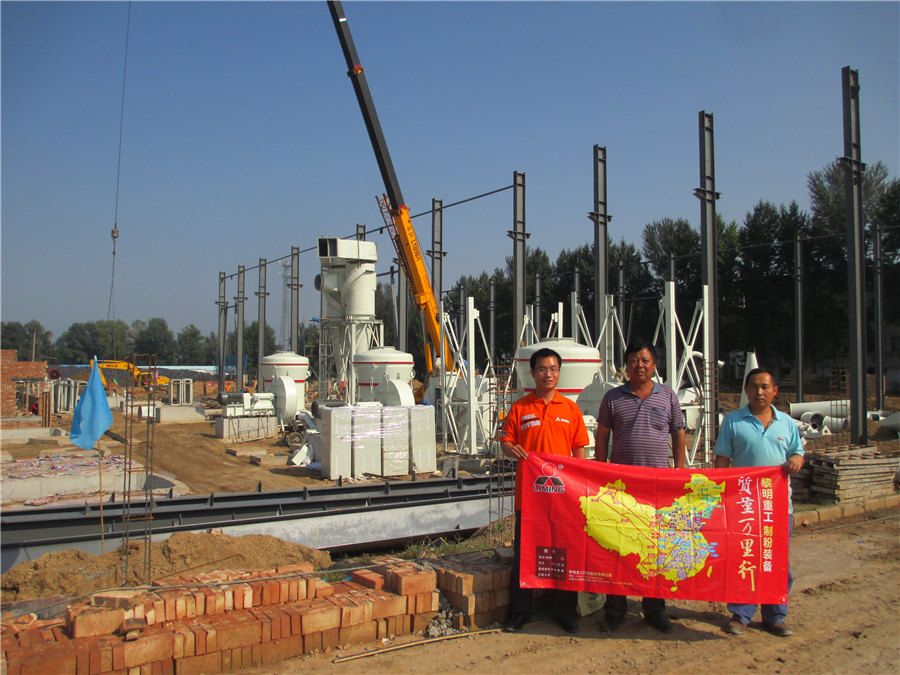
The Storm Approach to Coal Pulverizer Optimization
raw coal top size, 7% moisture and produces pulverized coal that is 70% passing 200 mesh fineness (red line) This is pretty standard Now, take that same pulverizer and provide fuel that is 40 HGI, still ¾” top size and still 7% moisture, but increase the fineness requirement to 80% passing a 200 mesh sieve1 High efficiency and large output GRMC series coal vertical grinding mill has higher working efficiency Compared with the same type of old vertical mill, the output increases by 2050%, and can greatly reduce the operation power consumption of the coal mill; 2 The fineness of finished product can reach 80μmR3%coal grinding machine CHAENG2021年8月1日 Yukio et al [7] proposed a model consisting of blending, grinding and classifying processes for pulverizer control Agarawal et al [8] differentiated coal powder into ten size groups, divided the bowl mill into four zones, and developed a unified model Palizban et al [9] derived nonlinear differential mass equations of raw coal, recirculation coal and suspension coal in Coal mill model considering heat transfer effect on mass 2015年8月1日 Mill power consumption/current increases Mill pulverized coal/air output reduces3: Wear (In rollers/balls, grinding table segments, cones and vanes of the classifier system, etc) [14], [16] Due to the mechanical action, this fault causes deformation or removal of material from the surface of different components Mill bowl differential goes Review of control and fault diagnosis methods applied to coal
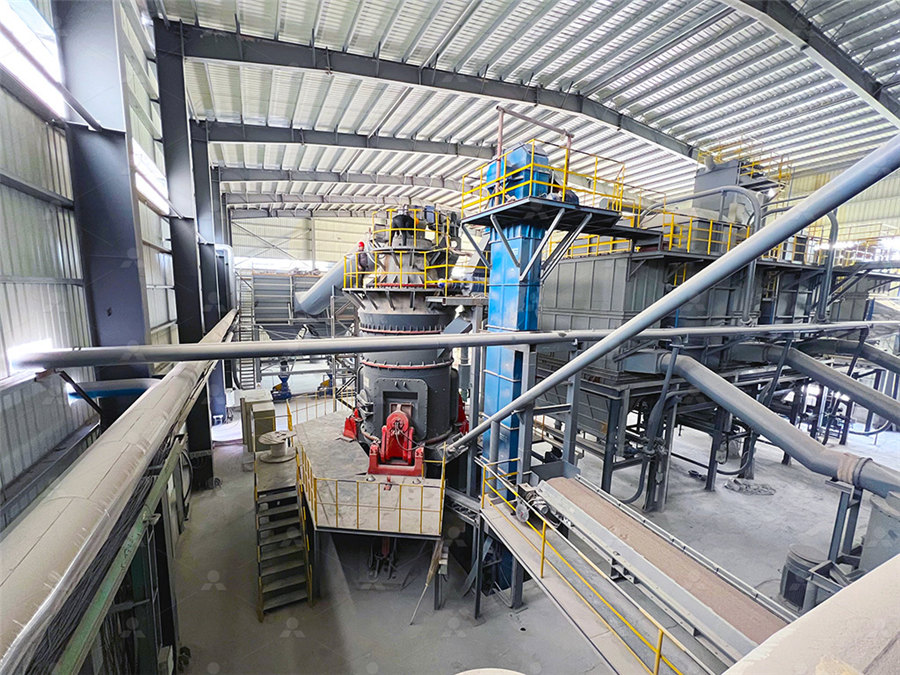
A Comparison of Three Types of Coal Pulverizers Babcock Power
The BTM is a lowspeed mill that primarily grinds coal by impact and attrition The VRM is a medium speed mill that grinds coal by compression and, because of the low coal inventory in the mill and flat grinding surfaces, develops shearing action as well For both mills a constant centrifugal force is maintained The speed2009年1月1日 below shows the particle tracks colored by the particle velocity magnitude for particles with a diameter size of 58 μm Fine particles of such a size are easily entrained in the flow and follow a CFD Modeling of MPS Coal Mill for Improved Performance and SafetyCollecting coal samples using an isokinetic probe provides the best data describing actual operating conditions inside the coal pipe Source: Storm Technologies Inc The isokinetic coal sampling method, although more difficult, is the best option for determining the true mill coal fineness produced and to calculate pulverizer performancePulverized Coal Pipe Testing and Balancing Storm Technologies, Energetic Efficiency An investigation of performance characteristics and energetic
.jpg)
COAL PREPARATION AND FIRING INFINITY FOR CEMENT EQUIPMENT
Certainly inadequate drying of coal in a ball mill Installation will reduce output and may lead to blockage of the mill However, it has been shown in many installations that if the exit gas temperature of the mill Is maintained at 70750C, satIsfactory For the cement industry the ball mill was really an epochmaking breakthrough as for almost 80 years it was the predominant mill for grinding of raw materials and coal, and still today is the most used mill for cement grinding Over the last three decades the vertical roller mill has become the preferred mill for grinding of raw materialsCement grinding Vertical roller mills VS ball mills2020年9月1日 For modelbased fault diagnosis method, it first needs to establish a mathematical model of the coal mill Odgaard et al [2] used a simplified energy balance equation to monitor and diagnose abnormal energy flow in the coal mill Andersen et al [3] designed a Kalman filter to estimate the moisture entering and leaving the coal mill, thereby identifying whether the Research on fault diagnosis of coal mill system based on the fineness desired, the coal’s Hargrove Grindablity Index (HGI), and the coal’s raw feed size and moisture content (see Figure 3 in “Finessing Fuel Fineness”) Plant operators can only improve throughput of a given mill with a particular coal (moisture and HGI are typically outside operator control) by sac“Blueprint” Your Pulverizer for Improved Performance
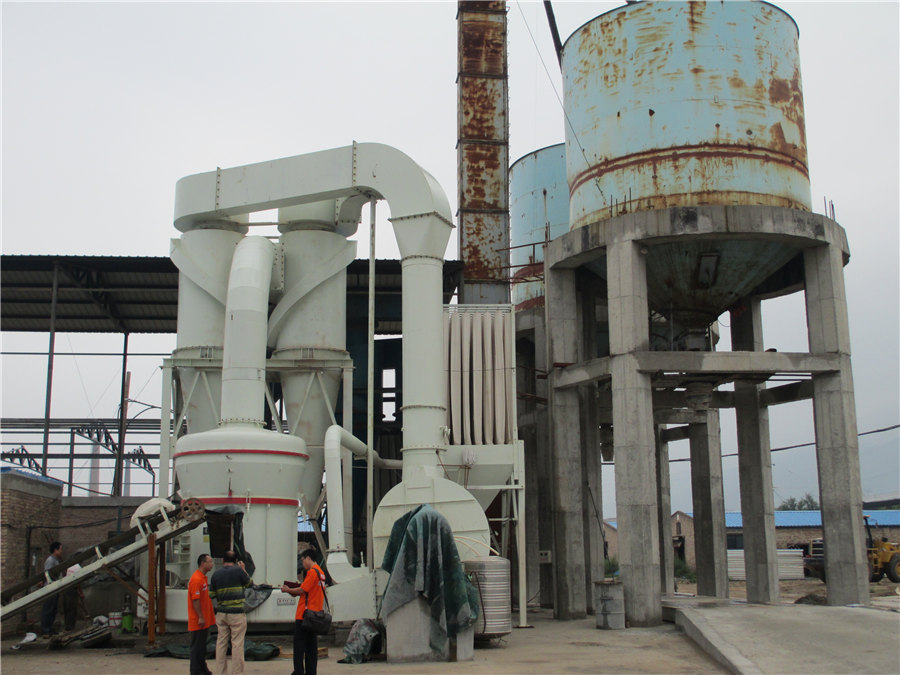
SHPHGLXP VSHHGFRDOPLOO ResearchGate
Journal of Physics: Conference Series PAPER OPEN ACCESS)DXOWDQDO\VLVDQGRSWLPL]DWLRQWHFKQRORJ\RI+3ERZOW\SHPHGLXP VSHHGFRDOPLOO To cite this article: Dou Jie 2021 J Phys: Conf Ser 2005 年8月1日 Pulverizers prepare raw fuel by grinding it to a desired fineness and mixing it with the just the right amount of air before sending the mixture to boiler burners for combustion In Part I of Pulverizers 101: Part I POWER MagazineCoal Fineness: It is understood Coal Crusher: Generally, require when ball mill is used for grinding and raw coal size is on higher side(>25mm) Conveying to Hoppers: This is very important for coal mill, as ambient air throttling the drying capacity of mill as well as increases the oxygen content of kiln gases making it riskierCoal Grinding Cement Plant Optimization2007年7月15日 Obviously, not all of the particles leaving the pulverizer are that size The fineness of coal is measured using a US standard sieve with a sleeve opening of 00030 inchesDynamic classifiers improve pulverizer performance and more
.jpg)
Mill Inerting and Pulverizer/Mill Explosion Mitigation
– Interruptions in raw coal feed – Lower feeder speeds – This occurs because a minimum airflow through the coal mill must be maintained to insure that burner line velocities are not too low to allow settling of coal in the fuel lines or burner components – Not uncommon to achieve air to fuel ratios of 3 to 5 pounds of air per pound While all these are regarding the mill performance, the coal fineness and mill out let temperature also affect the boiler performance The coal fineness has an effect on the combustion performance like the bottom ash percentage combustibles when the plus 50 mesh percentage goes up It has been very well established that in the case of tangential firing system, the Boiler Performance and Mill Outlet Temperature Bright Hub Compared with the same type of old vertical mill, the output increases by 2050%, and can greatly reduce the operation power consumption of the coal mill; 2 The fineness of finished product can reach 80μmR3% GRMC series coal mill uses the most advanced static and dynamic combined separator which has high classification efficiency and big room for controllingCOAL VERTICAL MILL Xinxiang Great Wall Machinery Co, Ltd2014年10月1日 Milanović, in his PhD dissertation, [4] investigates turbulent multiphase flow in the straight channels of noncircular section Živković et al in their paper [5] and S Atas et al in [6 Numerical and experimental analysis of pulverized coal mill
.jpg)
Air Swept Coal Mill Cement Plant Machinery
Advantages of air swept coal mill The feeding device of the airswept coal mill adopts a louvertype structure with oblique air intake, which enhances the heat exchange capacity of the mill and can effectively prevent material blocking at the entrance of the coal mill; optimize the support system, improve the lubrication structure, and reduce system resistance