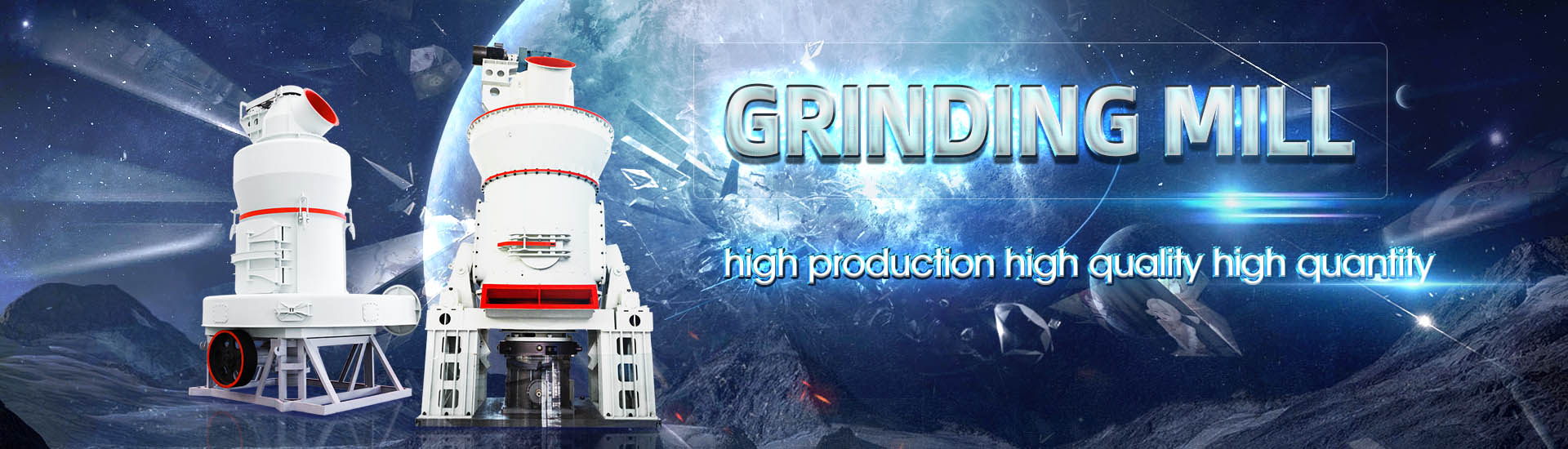
Steel slag crushing and grinding system magnetic separation production line
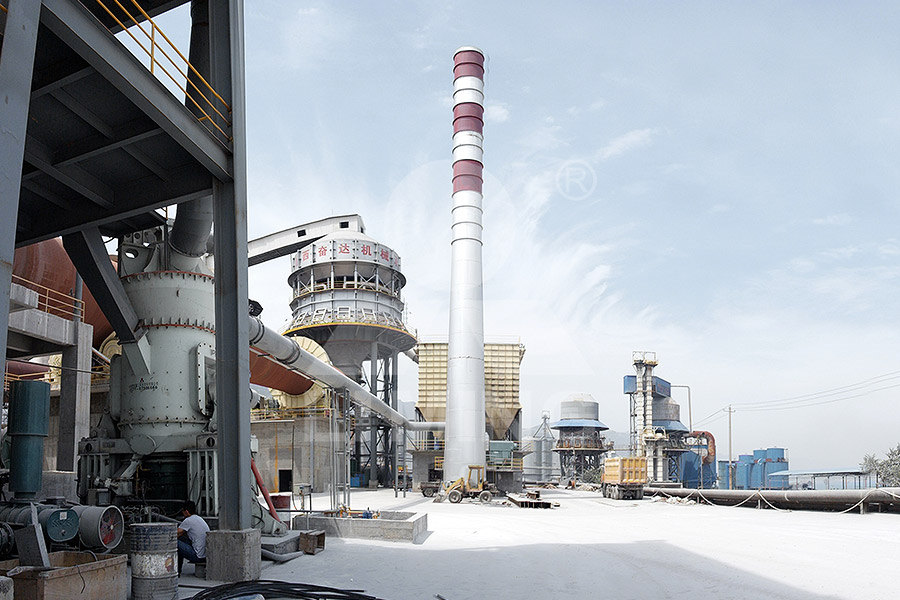
Steel slag recycling crushing and grinding production line
To achieve effective separation of slag and iron, keep the activity of steel slag as much as possible, and reduce the instability of steel slag Our advantage: The magnetic steel slag magnetic separation treatment of the slag to recover the metal iron, ③ crushing and classification of the slag for grain size adjustment to manufacture the slag product, and ④ aging treatment Processing and Reusing Technologies for Steelmaking SlagProject Introduction: The project is 10000 t/y steel slag treatment and recycling production line The waste residue is turned into treasure after crushing, magnetic separation, grinding, and T/Y Steel Slag Treatment and Recycling Production LineIn universities and research institutes, the technique used for efficient recycling of iron mainly include dry magnetic separation of bulk slag, wet stage grinding and magnetic separation, wet DRY MAGNETIC SEPARATION TECHNOLOGY FOR THE RECOVERY
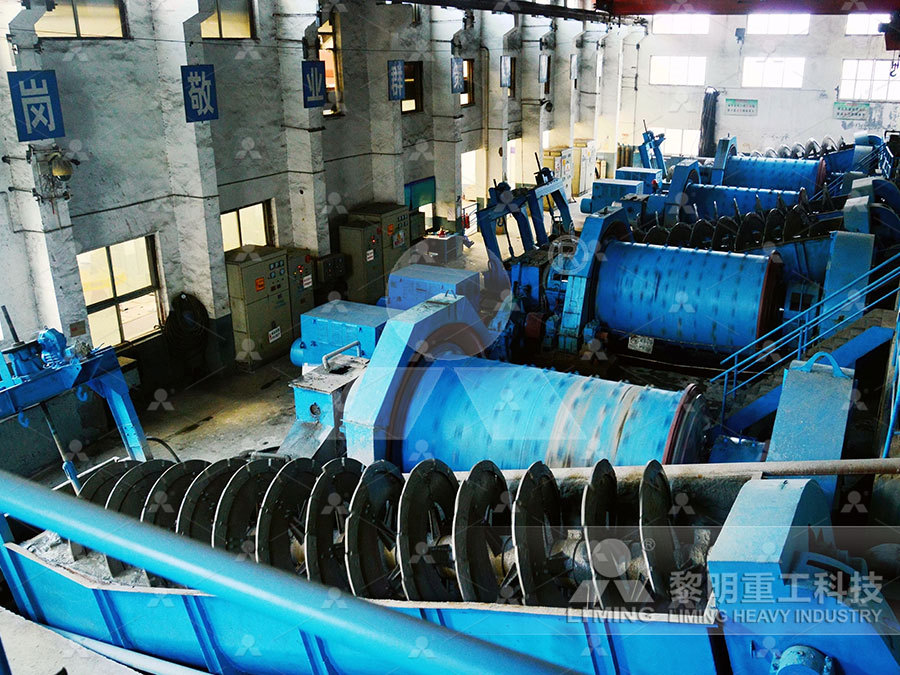
Steel Slag Grinding Plant CHAENG
The steel slag after pretreatment is screened by a vibrating feed screen to remove large slag steel, and then enters the crushing magnetic separation system, where the steel slag is 2024年3月1日 Primary magnetic separation tests on a steel slag fine powder material demonstrate that the air fluidized dry magnetic separator effectively separates inert minerals (PDF) An airfluidized magnetic separator and its separation 2023年8月22日 It is found that the removal rate of hardtogrind minerals in steel slag is the highest when steel slag enters magnetic separation particle size of 1 mm and magnetic field The Effect of Removing HardtoGrind Minerals from Steel Slag on In order to allow fast, highly precise analysis with a high sample throughput rate, thyssenkrupp has developed an automated slag sample preparation line from crushing through to Highprecision automated slag sample preparation for XRF and
.jpg)
Highprecision automated slag sample preparation for XRF and
of slag sample to the readyforanalysis pressed tablet Sample preparation takes about 400 seconds, depending on grinding parameters The innovative sample preparation method consists of an automated crusher with an inline magnetic separator, a handling unit, a gravimetric dosing unit, a grinding unit, a second magnetic separator and a2024年3月1日 Primary magnetic separation tests on a steel slag fine powder material demonstrate that the air fluidized dry magnetic separator effectively separates inert minerals from active minerals in the (PDF) An airfluidized magnetic separator and its separation chemical/mineralogical composition Mostly , steel slag magnetic separation process includes crushing/ grinding, screening and magnetic separation':", In order to liberate metallic iro n and other ferrous min erals fr om steel slag, size reduction pretreatment Received 10 May 2016 ; Received in revised for m 2 August 2016 ; Accepted 1 August Optimization of magnetic separation process for iron recovery 2024年7月29日 The mineral dry separation method is a technique for the comprehensive utilization of steel slag In this process, two products, ie, steel slag powder with high activity (reaches 75% of the cementitious activity of pure cement) and inert mineral material, are obtained by crushing and separating steel slag 12,13 If wet magnetic separation is adopted, the active Magnetic separation characteristics of steel slag powder in a
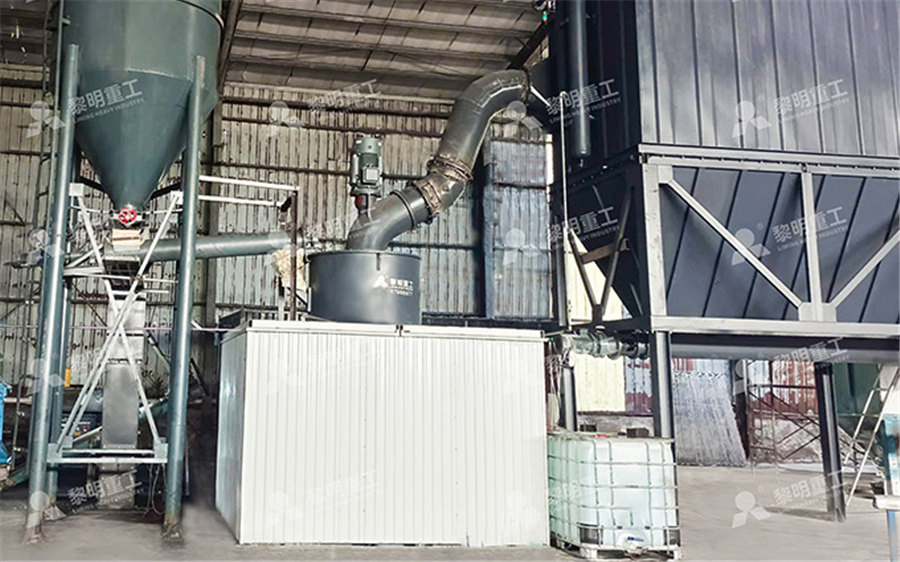
Loesche Mills for Metal Recovery and Filler Production from Steel Slag
Stainless steel slag with metal inclusions Reflected light microscopy with typical phases of a stainless steel slag Heavy product (metal) light product after dry density separation ( 2 mm) Loesche GmbH Sales Ores Slags Hansaallee 243 40549 Düsseldorf Tel +49 211 53 53 777 Fax +49 211 53 53 500 Email: ores@loesche www 2024年11月12日 Ferronickel, produced from the thermal upgrading of nickeliferous ores, is one of the feed materials for stainless steel production However, traditional hightemperature smelting processes for producing ferronickel are facing increasing pressure due to environmental concerns and decreasing ore grades The pyrometallurgical processing of lowgrade laterites, aimed at A Review of Direct Reduction–Magnetic Separation Process for May 26 28, 2021, Brno, Czech Republic, EU SEPARATION OF THE MAGNETIC FRACTION FROM THE SLAGS ORIGINATED DURING STEEL PRODUCTION 1Kryštof FONIOK, 1Vlastimil MATĚJKA, 2Petra MAIEROVÁ, 3Petra MATĚJKOVÁ, 2Jozef VLČEK 1VŠB Technical University of Ostrava, Faculty of Materials Science and Technology, Department of Chemistry, Ostrava, SEPARATION OF THE MAGNETIC FRACTION FROM THE SLAGS Steel slag is a solid waste of the steel industry, produced during steel production Three types of slag, namely electric arc furnace (EAF), basic oxygen furnace (BOF), and LinzDonawitz processed slag (LDslag) are the steel industry byproducts That slag comprises precious elements including zinc (Zn), chromium (Cr), iron (Fe), nickel (Ni), silicon (Si) , aluminum (Al), An Overview of Precious Metal Recovery from Steel Industry Slag
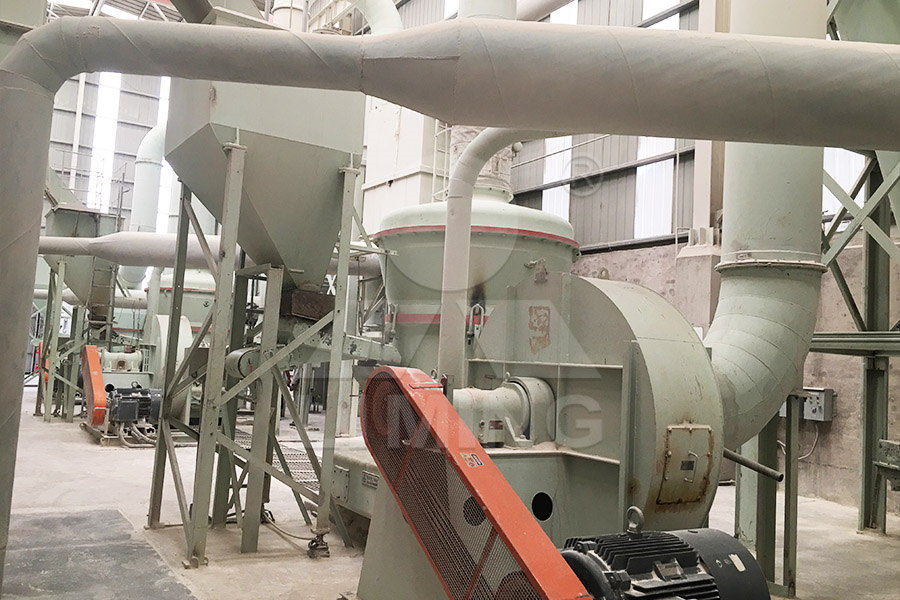
Steel Slag Magnetic Separation Line FTM Mac
Its waste material serves for paving the way, land reclamation, agricultural fertilizer and cement production Main Equipment of Steel Slag Magnetic Separation Plant There are two stages of the steel slag magnetic separation line; respectively they are grinding and screening With the main equipment of ball mill and magnetic separator, the 2023年12月27日 The magnetic separation of steel slag includes drymagnetic separation and wetmagnetic separation Prev Previous Feldspar Powder Crushing Grinding Production Line Equipment Next Limestone Crushing And SandMaking Plant Next Contact Us Now Your Name Your Phone/WhatsApp Project Location Steel Slag Processing Plant Equipment SelectionOur plants utilize stateoftheart magnetic separation equipment to maximize the recovery of metallics from the raw slagThe processing plants include the latest technology in crushing and screening plant design to cleanly separate the slag Slag Recycling and Metal Recovery MEKA2017年2月1日 To improve the efficiency of iron recovery from steel slag and reduce the wearandtear on facilities, a new method was proposed by adding a secondary screen sizer to the magnetic separation Optimization of magnetic separation process for iron recovery
.jpg)
WET MAGNETIC SEPARATION OF IRON FROM FINEGRAINED
Generally, the steel slag (steel furnace and ladle furnace slags) contains an appreciable amount of magnetic substances such as metallic iron and magnetic iron oxide, and thus, they can be recycled by wet magnetic separation This work presented here investigates the effect of fine grinding for maximum recovery of iron from the steel furnace slags2021年9月24日 During steel production, the impurities in the hot metal react with the fluxes forming the steel slag Chemical constituents of this steel slag (SS) are relevant to iron/steelmaking or blended cement manufacture Harmful impurities present in it, however, limit its recycling to these applications Japan, Europe, and the US consume a significant amount of BOF Steel Slag: Critical Assessment and Integrated Approach for The slag grinding production line is a production system specially used to process slag and make slag powder Slag, as a byproduct in the industrial production process, can be converted into valuable resources through grinding processing and used in cement mixtures, highperformance concrete admixtures, etcSlag Grinding Production Line TAYMACHINERY2016年10月28日 The converter steel slag cannot be widely used in building materials for its poor grindability In this paper, the grinding characteristics of untreated and pretreated (ie, magnetic separation (PDF) Comparison of Grinding Characteristics of Converter Steel Slag
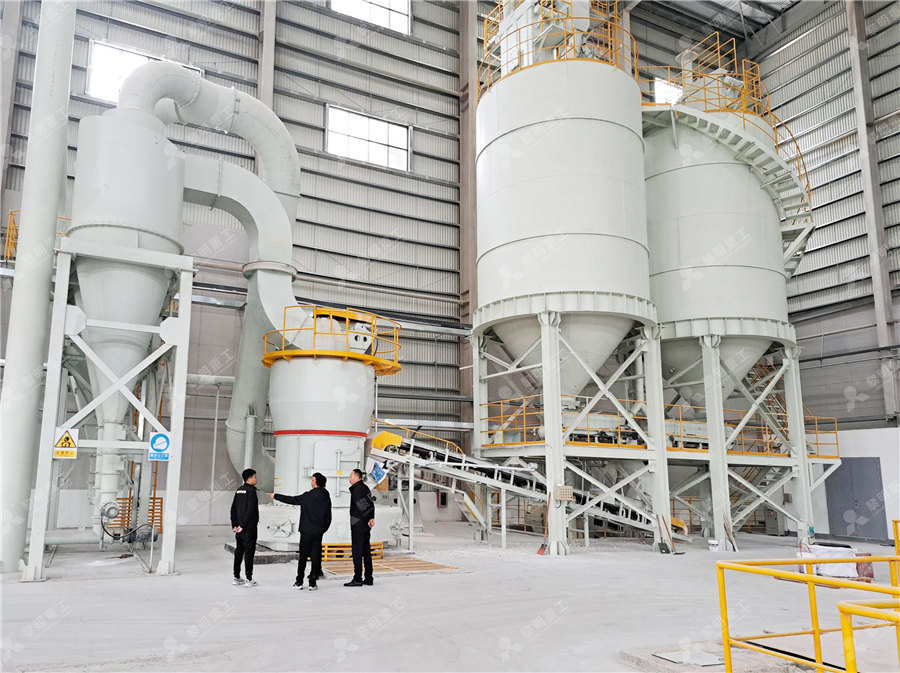
Steelmaking Slag Beneficiation by Magnetic Separator and
2014年1月1日 After BOF slag was oxidized at 1300 ℃ for 240 min and cooled in the furnace (1 ℃/min), the grade of magnetic slag obtained by magnetic separation had a grade of 4026%, a recovery of 7095% 2023年11月7日 Magnetic separation has wideranging applications in both mineral processing and recycling industries Nevertheless, its conventional utilization often overlooks the interplay between mineral and particle characteristics and their impact on operational conditions, ultimately influencing the efficacy of the separation process This work describes a methodology able to Characterization of Magnetic and Mineralogical Properties of Slag 2014年2月19日 The recovery ratio was less than 151 % The waste sensible heat of the molten BF slag at 1,500 °C and that of the molten steel slag at 1,550 °C reached respectively 185 and 51 kg CE per tonne of steel production Furthermore, the recovery ratio of sensible heat for the molten BF slags was only 216 % and that for steel slag was zeroCurrent Development of Slag Valorisation in Chinadry magnetic separation of bulk slag, wet stage grinding and magnetic separation, wet magnetic separation for full grain level, finegrained level flotation, and gravity separation [79] The wet separation and electromagnetic separation technologies suffer from high power and water consumption, whereas by contrast, dry permanentDRY MAGNETIC SEPARATION TECHNOLOGY FOR THE
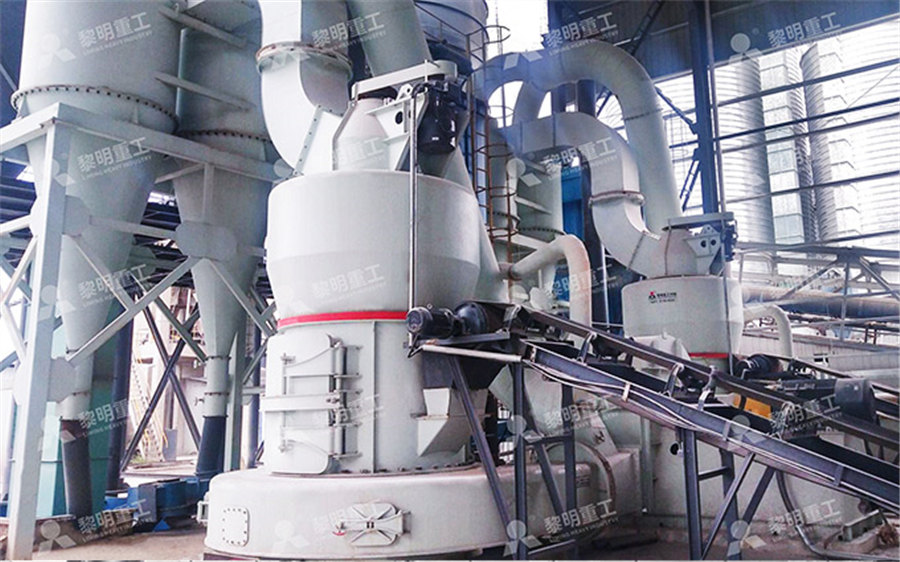
Application of Magnetic Separation to Steelmaking Slags for
In 2006, 1015 million metric tons of steel slag were generated in the US Out of the total steel slag produced in the US every year, about 5070% is used as aggregate for road and pavement The iron/steel slag processing flow is schematically shown in Fig 2 Steelmaking slag is subjected to the following four processes: ① solidify and cooling of the hot molten slag, ② crushing and magnetic separation treatment of the slag to recover the metal iron, ③ crushing and classification of the slag for grain size adjustmentProcessing and Reusing Technologies for Steelmaking Slag2021年8月30日 Chromium slag is the waste residue generated by the industrial process of extracting chromium (Cr) from chromite ore Due to different needs for chromite quality in the target product, the extraction processes for chromium Enrichment Characteristics of Cr in Chromium Slag A company from Guangdong, after the process of hot stew, crushing and screening, magnetic separation, coarse grinding, all kinds of broken steel slag into the annual output 600,000 tons of steel slag comprehensive utilization of resources and environmental protection engineering production line slag heap storage shed,Then by screening, magnetic separation, prepink Steel Slag Grinding Plant
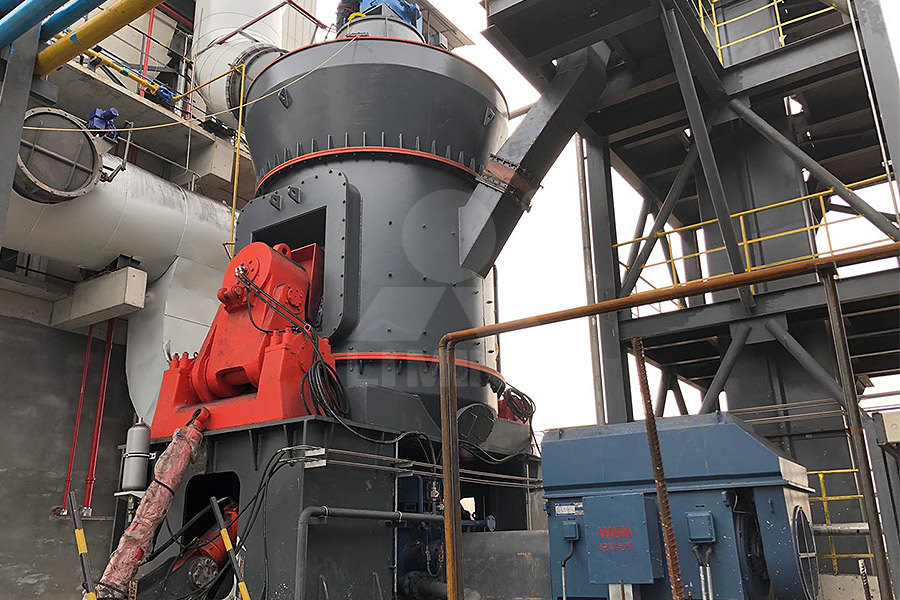
Steel Slag Ball Mill Quality Ball Bill Supplier Provide Best Price
Steel slag ball mill is the key equipment of steel slag processing production line The steel slag ball mill is different from other ball mills For the treatment of steel slag, enterprises usually adopt crushing, grinding, screening, magnetic separation and other processes to recover part of the metal in steel slag2024年2月27日 Tire waste is a challenging waste and its handling requires efficient technology and equipment The tirecrushing production line with steel separation is an advanced technical system that can effectively break down waste tires into reusable materials and achieve the separation and recycling of steel at the same time Tire crushing technology: aTyre shredding line with separation of steel SUNY GROUP2020年9月24日 With the rapid development of China’s steel industry, rising rates of steel production have led to the increase of steel slag emissions Steel slag is a kind of industrial solid waste produced in the process of iron and steel smelting, and its emission is about 15 wt%–20 wt% of crude steel output []According to the data released by the World Iron and Steel Sustainable Utilization of Steel Slag from Traditional Industry and dry magnetic separation of bulk slag, wet stage grinding and magnetic separation, wet magnetic separation for full grain level, finegrained level flotation, and gravity separation [79] The wet separation and electromagnetic separation technologies suffer from high power and water consumption, whereas by contrast, dry permanentDRY MAGNETIC SEPARATION TECHNOLOGY FOR THE
.jpg)
Activation technology of steel slag for concrete exposed to
Steel slag is a byproduct generated during the steelmaking process As the largest steel producer in the world, China produces over 100 million tons of steel slag annually, accounting for approximately 15–20% of crude steel production (Rui et al 2022, Shi et al 2022)After steelmaking, the slag is placed in a slag heap and subjected to magnetic separation to recover Keywords Gasquenched steel slag abrasive Thermal property Magnetic property Compressive strength Surface roughness Micromorphology 1 Introduction Steel slag is the main solid waste during steel production [1 ] This slag is formed by the oxidation of impurities, such as metals, fluxes, and furnace linings, in the raw materialsStructure characterization and grinding performance of gas Introduce Steel Slag Processing, Iran Steel slag generally contains 7% to 10% iron, and more than 90% of the iron and some magnetic oxides can be recovered through crushing, screening, magnetic separation and other techniquesSteel Slag Processing Line Henan Forui Machinery Integrated mechanical separation for municipal solid waste Zhou Tao, Eugene Atta Nyankson, in Resource Recovery Technology for Municipal and Rural Solid Waste, 2023 633 Magnetic separation The magnetic separation of solid waste is a method of separating ferromagnetic substances using the magnetic field generated by the magnetic separation equipmentMagnetic Separation an overview ScienceDirect Topics
.jpg)
Comparison of Grinding Characteristics of
2016年10月28日 The converter steel slag cannot be widely used in building materials for its poor grindability In this paper, the grinding characteristics of untreated and pretreated (ie, magnetic separation) steel slag were 2023年2月1日 The multistage wet weak magnetic separation method is suitable for steel slag, with a best magnetic separation intensity of 100 mT in the laboratory range and a single magnetic separation time of Efficient separation of iron elements from steel slag based on magnetic The final products of steel slag crushing production line are mainly slag steel and magnetic separation powder The former can be reused in steelmaking and the latter can be reused in sintering The tailings can also be further processed, such as producing steel slag powderSteel slag grinding plant2024年3月1日 China is the world's largest carbon emitter and steel producer In 2022, China's CO 2 emissions reached 121 Gt, accounting for 33% of the global total (IEA, 2023)Additionally, China's crude steel production reached 1018 billion tonnes, 539% of the global share (WSA, 2023a)The steel industry is one of the vital foundational sectors of the national economy, Towards the cobenefits of carbon capture, utilization and
.jpg)
(PDF) Mineralogical characterisation and magnetic separation of
2018年9月10日 Grinding, sieving and magnetic separation were combined to recover metallic iron from the converter slag, and yielded approximately 415% of iron in which the iron content was as high as 85%, and 2023年11月20日 In 2017, Japan claimed ~ 14 million tonnes of steel slag production, while China reported 100 million tonnes of steel slag in the year 2016 [2, 3], which is in line with the available data of 10 to 15% or pyrometallurgical methods The mechanical methods are based on crushinggrindingmagnetic separation unit operations A A Review on Environmental Concerns and Technological Springer2018年8月1日 In recent years, common applications of steel slag have been road construction, concrete aggregate, cement production, and landfill materials [2, 3,5,6] 80,000 tons of steel slag was used in the Steel slag in China: Treatment, recycling, and management2021年8月5日 To solve the problem of difficult utilization of steel slag, the liquid steel slag was modified and the airquenching granulation process was carried out to make steel slag into a valueadded end product: airquenching granulated steel slag The granulated slag was tested to analyze the variation rule of slag properties under different modification conditions Based on Hightemperature modification and airquenching granulation of steel slag