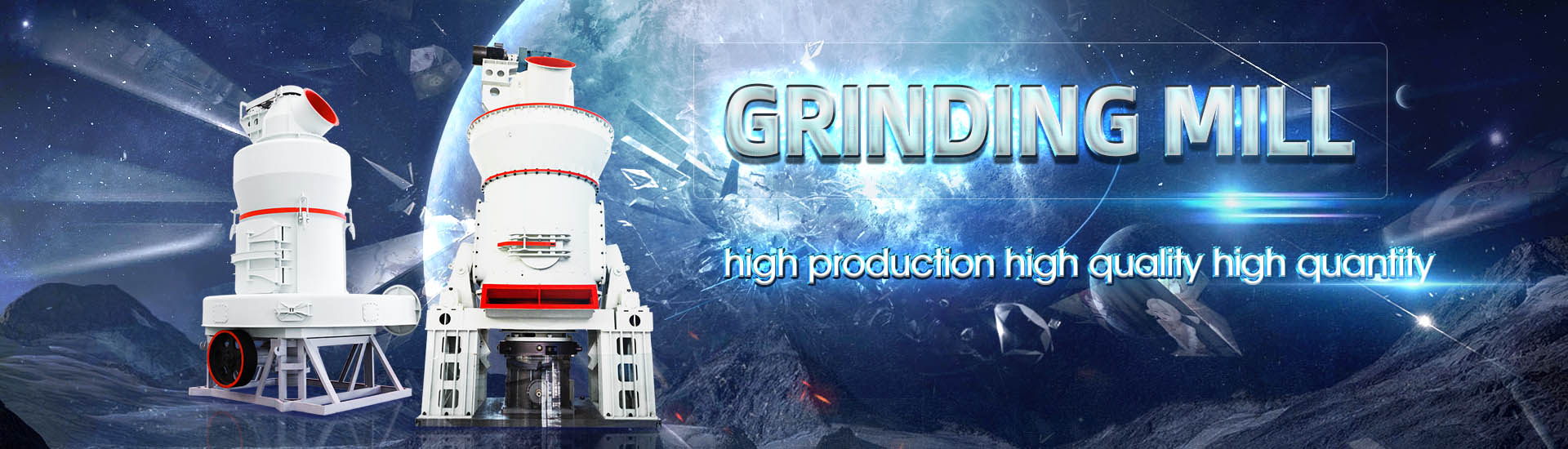
Crystalline silicon ore grinding machine
.jpg)
Abwood Machine Tools Silicon Block Grinding Machines for the
The Abwood TS5 has revolutionised the grinding process for monocrystalline silicon ingots Following on from the existing range of twin spindle surface grinders for multicrystalline monocrystalline silicon work pieces in the format of 125 x 125 mm and 156 x 156 mm, with three grinding aggregates (2x pre, 1x fi ne grinding) and one addi onal grinding aggregate for OD Silizium Arnold GruppeGrinder (LTGMS950) is an integrated machine for polishing monocrystalline silicon square rods of different sizes in both arc and surface after square cutting, with the functions of rough Grinder LTGMS950 Linton Crystal TechnologiesFind out all of the information about the JSG product: surface grinding machine RGM8C1000ZJS Contact a supplier or the parent company directly to get a quote or to find out a price or your Surface grinding machine RGM8C1000ZJS DirectIndustry
.jpg)
Silicon Crystal Ingot Processing Silfex
Our bestinclass grinding and slicing techniques result in minimal edge damage, low kerf loss and reduce waste of materials Our postprocess testing ensures the highest quality silicon 2023年11月28日 This chapter introduces 15 kinds of main silicon wafer manufacturing equipment, including Single Crystal Growth Furnace, Float Zone Crystal Growth Furnace, Manufacturing Equipment for Silicon Wafer SpringerLinkThe monocrystalline silicon ingots from which silicon wafers are created are manufactured by a technique called the CZ (Czochralski) crystal growth process Polysilicon purified until the Monocrystalline pulling process SUMCO CORPORATIONCustomized grinding mill parts including heads, shells, trunnions and liners, main bearings, gears and pinions, and more! Metallic, PolyMet™, Megaliner™, Rubber and Orebed™ mill liners for Grinding Metso

Processing Methods of Silicon to its Ingot: a Review Silicon
2018年9月21日 Any metal must be processed from its ore before employing it in various industrial applications; this is the similar case with Silicon (Si) as well Occurring in the form of 2024年10月1日 The estimated average lifespan of crystalline silicon solar panels is about 25 years Still, premature waste through damage to equipment during transportation, installation, natural disasters (hails, hurricanes, storms, landslides) and fire accidents [16] is generated in significant quantities By 2050, it is projected that up to 78 million metric tons of solar panel A technical review of crystalline silicon photovoltaic module 2017年10月19日 3 Types of grinding Machine Grinding machines according to quality of surface finish, may be classified as 1 Rough /Nonprecision grinding 2 Precision grinding Rough/Nonprecision grinding To remove more stock than Grinding machine PPT SlideShare2021年8月27日 If the difference between the middle size and the two ends of the silicon ingot is too large, such as more than 02 mm, it will cause much machining allowance in the next grinding process, which affects the The machining accuracy and surface roughness of
.jpg)
(PDF) Residual Stress Distribution in Silicon Wafers Machined
2017年3月6日 Subsurface damage (SSD) and grinding damageinduced stress (GDIS) are a focus of attention in the study of grinding mechanisms Our previous study proposed a load identification method and The wafer infeed grinding process includes rough and ne grinding processes A typical wafer grinding machine (for either rough or ne grinding) is displayed in Fig 1 The grinding wheel in Fig 1a is a diamond cup wheel installed on a spindle Figure 1b shows the wafer is held on the chuck table by a vacuum3D grinding mark simulation and its applications for silicon wafer grinding2023年11月28日 This chapter introduces 15 kinds of main silicon wafer manufacturing equipment, including Single Crystal Growth Furnace, Float Zone Crystal Growth Furnace, Ingot Grinding Machines, Slicing Machines, Silicon Wafer Annealing Furnaces, Edge Rounding Machines, Lapping Machines, Wafer Etching Machines, Polishers, DoubleSide Grinders, Manufacturing Equipment for Silicon Wafer SpringerLinkSilicon Carbide is one of the hardest of ceramics retains hardness at elevated temperatures, which translates into the best wear resistance Skip to content About; it is nevertheless a relatively brittle material and can only be machined using diamond grinding techniquesMachining of Silicon Carbide Process, Applications and Types
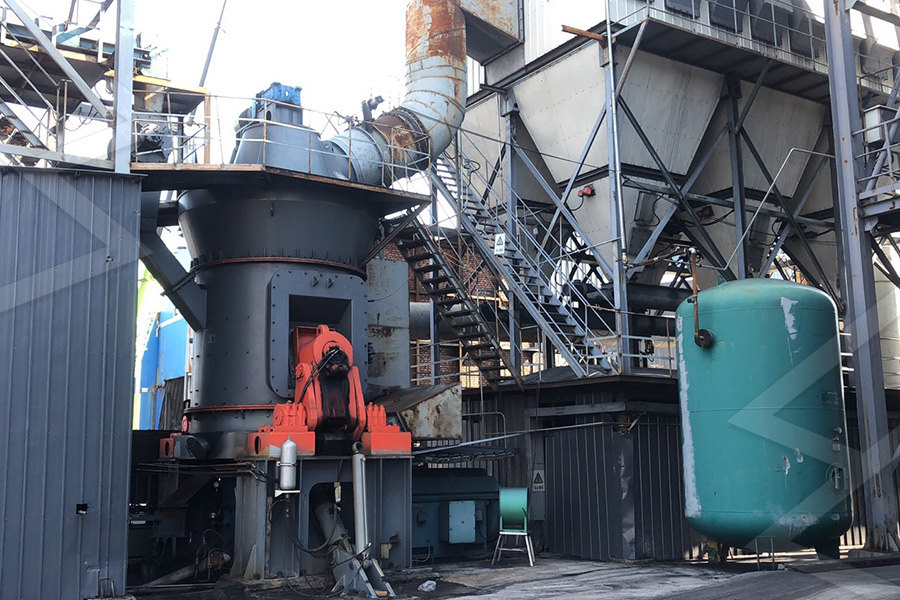
Surface evolution and stability transition of silicon wafer subjected
2017年3月31日 Comparing silicon after grinding to before grinding, we obtain that the elastic modulus and hardness of silicon after grinding are also smaller than before grinding The changed properties of silicon before and after grinding, combined with the SEM images in Fig1c and 1d, indicate that amorphous silicon grows on single crystalline silicon waferstudy the effect of grinding along crystallographic directions on the surface finish of singlecrystal silicon are reported with promising results 20 LITERATURE REVIEW Typical processes in the manufacturing of siliconbased devices are as follows A seed crystal of silicon is placed on the end of a rod and dipped into a vat of molten siliconGrinding of SingleCrystal Silicon Along Crystallographic Directions2018年10月17日 In practice, grinding is the most widely used process for machining of silicon wafers Pei et al studied grindinginduced SSCs in silicon wafers and found their configurations to be complex, ie, to exhibit “umbrella”, “chevron”, and “median crack” configurations 6 The distribution of SSCs has appeared to be stochastic and Formation of subsurface cracks in silicon wafers by grinding2023年12月20日 This review addresses the growing need for the efficient recycling of crystalline silicon photovoltaic modules (PVMs), in the context of global solar energy adoption and the impending surge in endoflife (EoL) Comprehensive Review of Crystalline Silicon Solar
.jpg)
Grinding Machine PPT PPT SlideShare
2020年4月24日 6 6 • The grinding machine consists of a bed with a fixture to guide and hold the work piece, and a powerdriven grinding wheel spinning at the required speed The speed is determined by the wheel’s diameter and 2024年1月16日 The wafer infeed grinding process includes rough and fine grinding processes A typical wafer grinding machine (for either rough or fine grinding) is displayed in Fig 1The grinding wheel in Fig 1a is a diamond cup wheel installed on a spindle Figure 1b shows the wafer is held on the chuck table by a vacuum Figure 2 presents the top and front views of the relative 3D grinding mark simulation and its applications for silicon wafer 2020年10月1日 Grinding as a pretreatment method for HFHNO 3H 2 O solution etching of diamond wire sawn (DWS) multicrystalline (multiSi) silicon wafers was proposed and researched Significant improvement in morphological uniformity and decrease in light reflectivity of the wet acid etched surface textures were achieved with the pretreatmentSurface modification of diamond wire sawn multicrystalline silicon The monocrystalline silicon ingots from which silicon wafers are created are manufactured by a technique called the CZ (Czochralski) crystal growth process Polysilicon purified until the metal impurities are no more than a few parts per billion (ppb) is put into a quartz crucible along with boron (B) and phosphorous (P), and melted at a temperature of around 1420℃Monocrystalline pulling process SUMCO CORPORATION
.jpg)
Selective grinding of glass to remove resin for siliconbased
2021年2月1日 Secondary grinding was investigated as a mean of liberating glass from locked particles of glass and resin obtained by the primary shredding from the siliconbased PV panelsWafer manufacturing includes a series of processes, beginning with crystal growth and ending with prime wafers, as illustrated in Fig 521, in which a process flow of wafer manufacturing with various categories of operations is shown []Slicing is the first major postgrowth waferforming process, and is primarily accomplished using various technologies, discussed in Sect 522Wafer Manufacturing and Slicing Using Wiresaw SpringerLink2024年9月1日 What is crystalline silica? Silica is silicon dioxide, a naturally occurring and widely abundant mineral that forms the major component of most rocks and soils There are noncrystalline and crystalline forms of silicon dioxide The most common type of crystalline silica is quartz (CAS 1) Crystalline silica and silicosis Safe Work Australia2006年6月1日 Highperformance grinding of unconventional materials such as highalloy chromium, titanium steels, very hard tungsten carbides, advanced ceramics, silicon nitride, superalloys and metal–matrix composites, requires suitable grinding tools to ensure their costefficient machining, as well as attain their greater dimensional accuracy and groundsurface quality Highperformance grinding—A review ScienceDirect
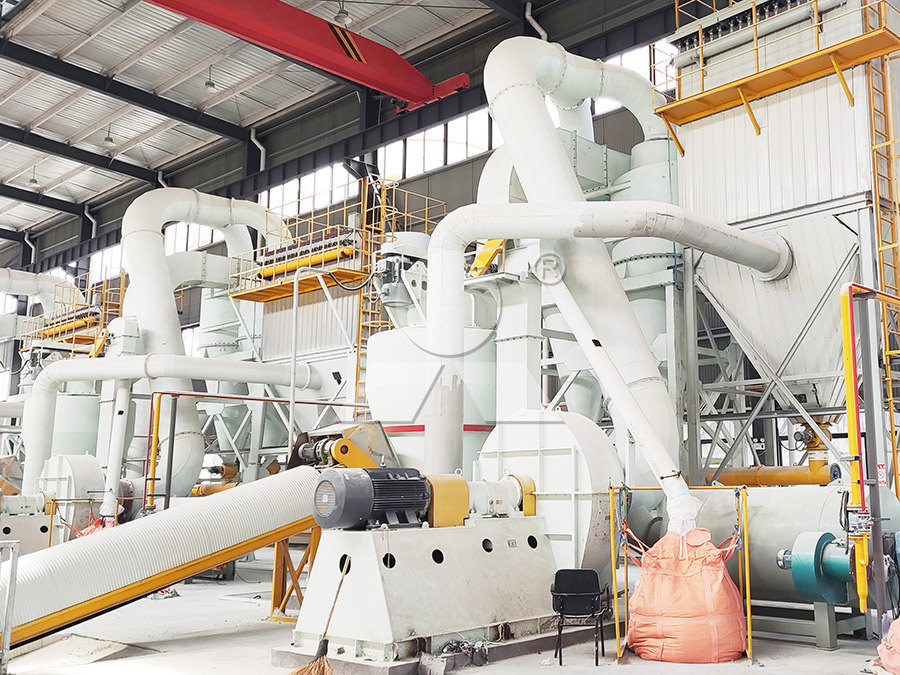
The Influence of Crystal Orientation on Subsurface Damage of
2021年3月28日 The silicon samples were spotted at three random positions along the radial direction with a commercial MRF machine (QED Technologies, Q22400X, Rochester, NY, USA) and In order to reveal the effects of the grinding parameters on the subsurface damage of monocrystalline silicon grinding to guide processing for improving the 2010年1月1日 Fig 6 shows exemplary scratch tracks made in singlecrystalline {1 1 1}silicon Whereas the scratch under ambient pressure shows only brittle material behaviour, On a very stiff grinding machine Namba demonstrated that glass can be ground in ductile mode at depth of cuts larger than 10 Ultraprecision grinding ScienceDirect2022年12月1日 It is important to summarise the limitations and possible improvements for emerging new processes This paper aims to provide a comprehensive overview of the progress in silicon PV module recycling processes, at both the lab scale and pilot scale over the last decade, focusing on the mechanism, recycling yield, advantages and disadvantages, and Recent progress in silicon photovoltaic module recycling processes2021年3月4日 In this paper, we first report the laser grinding method for a singlecrystal silicon wafer machined by diamond sawing 3D laser scanning confocal microscope (LSCM), Xray diffraction (XRD (PDF) Laser Grinding of SingleCrystal Silicon Wafer
.jpg)
Status and perspectives of crystalline silicon photovoltaics in
2022年3月7日 With a typical wafer thickness of 170 µm, in 2020, the selling price of highquality wafers on the spot market was in the range US$013–018 per wafer for multicrystalline silicon and US$030 2023年7月1日 The laser was installed on a CNC ultraprecision surface grinding machine (SL800A/1HZ, Zhejiang Hangzhou Machine Tool Group CO, A laser texturing study on multicrystalline silicon solar cells Sol Energy Mater Sol Cells, 214 (2020), Article View PDF View article View in Scopus Google Scholar 21A hybrid chemical modification strategy for monocrystalline silicon Comparing polycrystalline (left) to monocrystalline (right) solar cells In singlecrystal silicon, also known as monocrystalline silicon, the crystalline framework is homogeneous, which can be recognized by an even external colouring [4] The entire sample is one single, continuous and unbroken crystal as its structure contains no grain boundariesPolycrystalline silicon WikipediaFind out all of the information about the JSG product: surface grinding machine RGM8C1000ZJS (Vnotch) of semiconductor monocrystalline silicon ingot The equipment integrates the function of two different processing equipments which completes grinding outer cylinder and orientation edge(Vnotch), respectivelySurface grinding machine RGM8C1000ZJS JSG
.jpg)
Grinding of SingleCrystal Silicon Along Crystallographic Directions
study the effect of grinding along crystallographic directions on the surface finish of singlecrystal silicon are reported with promising results 20 LITERATURE REVIEW Typical processes in the manufacturing of siliconbased devices are as follows A seed crystal of silicon is placed on the end of a rod and dipped into a vat of molten siliconPage 1 of 26 1 Introduction Monocrystalline silicon is a predominant type of semiconductor materials, and is considered as the building block of many electronic devices [1, 2], such as largescaleAnalytical modeling of grindinginduced subsurface damage in 2017年9月15日 Similar silicon grinding trials was also performed by Liu et al [13], where the results indicated the change regulation of the grindinginduced SSD was the same as the change tendencies of the grinding force and surface roughness, ie SSD depths were reduced by using a high wheel speed or a grinding wheel with a large abrasive size [14]Analytical modeling of grindinginduced subsurface damage in 2021年3月28日 DOI: 103390/mi Corpus ID: ; The Influence of Crystal Orientation on Subsurface Damage of MonoCrystalline Silicon by BoundAbrasive Grinding @article{Yang2021TheIO, title={The Influence of Crystal Orientation on Subsurface Damage of MonoCrystalline Silicon by BoundAbrasive Grinding}, author={Wei Yang and Yaguo Li}, The Influence of Crystal Orientation on Subsurface Damage of

Robust combined modeling of crystalline and amorphous silicon
2022年10月25日 npj Computational Materials Robust combined modeling of crystalline and amorphous silicon grain boundary conductance by machine learning Skip to main content Thank you for visiting nature2008年4月25日 All the tests were performed on the (1 0 0) surface of monocrystalline silicon (Si) fabricated by nanogrinding using different grinding conditions and CMGBoth nanogrinding and CMG were performed on 8in silicon wafers commercially available using a UPG300H grinding machine [5]The face grinding method was employed for nanogrinding and CMG [5], [6]Characteristics of silicon substrates fabricated using nanogrinding and 2019年5月1日 Subsurface damage (SSD) induced by silicon wafer grinding process is an unavoidable problem in semiconductor manufacturing Although experimental attempts have been made on investigation of the influential factors on the SSD depth, however, few theoretical studies have been conducted to obtain SSD depth through grinding parametersAnalytical prediction for depth of subsurface damage in silicon wafer 2022年3月1日 Nevertheless, the knowledge of a crack on silicon (Si) is limited to microscale, and the origin and evolution of a crack in a single crystal Si have not been reported(PDF) Origin and evolution of a crack in silicon induced by a single
.jpg)
A study on the diamond grinding of ultrathin silicon wafers
2012年1月1日 In this work, diamond grinding for thinning silicon wafers was carried out on an ultraprecision grinding machine The thinning performance and the minimum wafer thickness were investigated under 2022年2月9日 Diamond wire cutting is a process in which a large number of diamond grains interact with the workpiece surface []The mechanism of diamond sawing is a fixed grinding, which is considered to be a twobody grinding process consisting of workpiece and abrasive grains fixed on the core wire [2, 3]The cutting process depends on the contact between the abrasives and Evaluation method for the machining accuracy of diamond wire 2012年5月1日 Silicon substrates form the foundation of modern microelectronics Whereas the first 50 years of silicon wafer technology were primarily driven by the microelectronics industry, applications in Silicon Crystal Growth and Wafer Technologies ResearchGate2009年9月1日 s Xray Photoelectron Spectroscopy (XPS) wide spectrum of silicon wafer surface ground by soft abrasive wheel The spectrum shows that there are not only Si but also Ce, Ca, C, O on the surface(PDF) Study on Grinding Performance of Soft Abrasive Wheel for Silicon
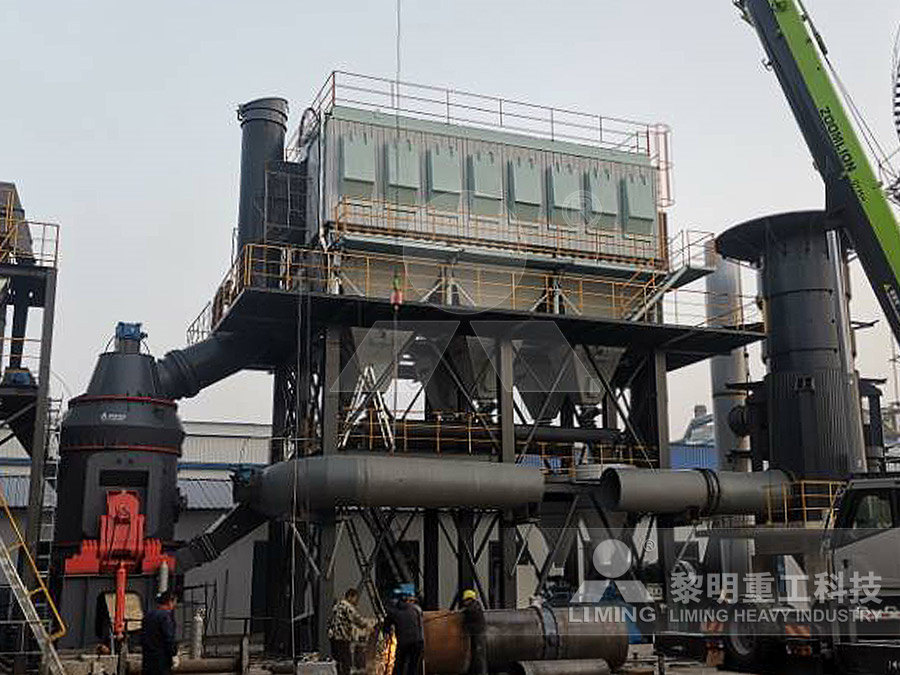
Chapter 16: Grinding Wheels and Operations American Machinist
2020年6月29日 The manufactured abrasives most commonly used in grinding wheels are aluminum oxide, silicon carbide, cubic boron nitride, and diamond Aluminum oxide Refining bauxite ore in an electric furnace makes aluminum oxide