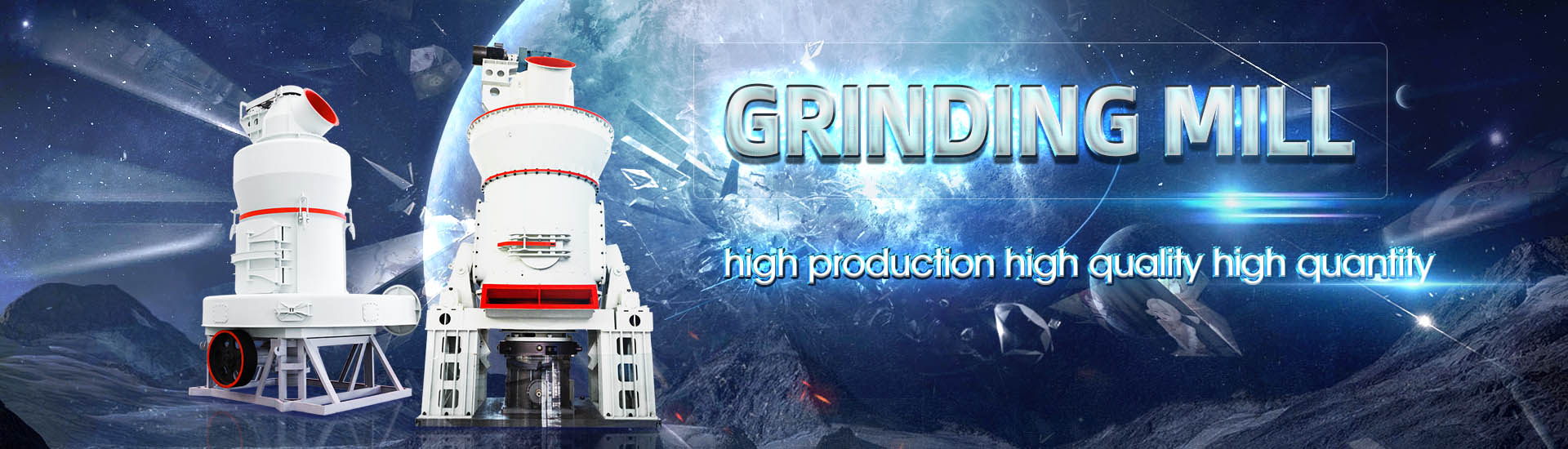
Blast furnace coal injection process flow chart
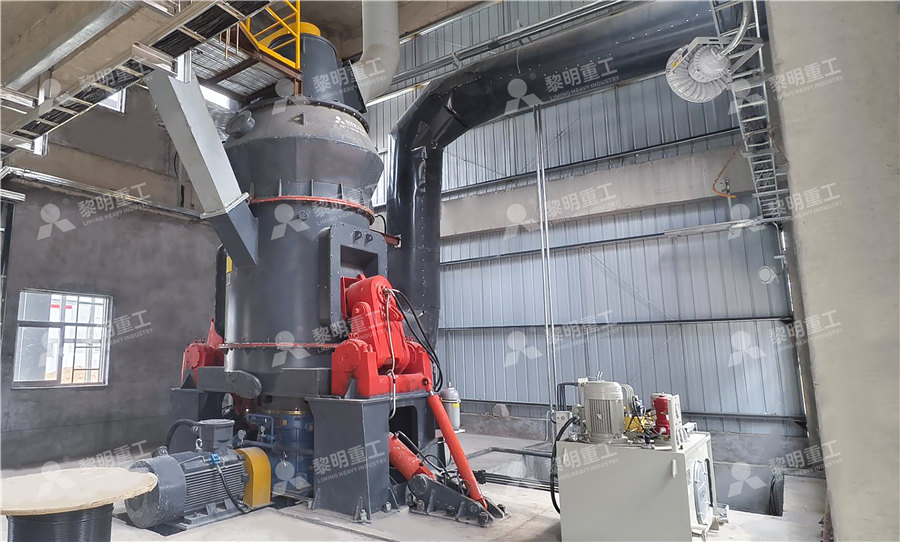
3A2 Pulverized Coal Injection for Blast Furnaces (PCI)
Pulverized coal injection technology has the potential to spur innovations to blast furnaces: recycled materials, such as waste plastics and biomass, as well as recycled ores can be injectedThe blast furnace process with pulverized coal injection (PCI) rate of up to 250 kg/THM and reduction of the coke rate from 500 down to 250 kg/THM has been realized The reduced coke Blast Furnace Process an overview ScienceDirect TopicsThe model simultaneously estimate the blast furnace process parameters like bosh gas volume and its composition, tuyere velocity and raceway adiabatic flame temperature (RAFT) for the definedBlast furnace process overview Download Scientific This paper assesses the injection of different syngas in airblown blast furnaces, oxygen blast furnaces, and advanced oxygen blast furnacesProcess flow diagram of a blast furnace in Aspen Plus
.jpg)
Schematic presentation of the blast furnace process
The present chapter will discuss the influence of various materials injection on the blast furnace operation The injection limit and changing of the blast furnace operating conditions,2018年10月21日 Pulverized coal injection (PCI) is a wellestablished technology for hot metal (HM) production in a blast furnace (BF) It is practiced in most of the BFs and all the new BFs Understanding Pulverized Coal Injection in Blast Furnace2020年7月15日 The blast furnace process with pulverized coal injection (PCI) rate of up to 250 kg/THM and reduction of the coke rate from 500 down to 250 kg/THM has been realized The Blast Furnace Ironmaking an overview ScienceDirect Topics2023年6月15日 The characteristics of pulverized coal injection of blast furnace ironmaking include basic performance (ash, sulfur, and fixed carbon) and process performance (ignition Pulverized Coal Injection of Blast Furnace Ironmaking
.jpg)
Optimizing Blast Furnace Operation to Increase Efficiency and
Optimize the burden and gas distribution for maximizing gas utilization with proper furnace permeability for given burden materials, productivities, coal injection rate, and BFs2018年10月21日 Fig 1 Pulverized coal combustion and gas composition in raceway The extent of combustion (combustion efficiency), and hence the amount of unburnt material transported out of the raceway, depends on several parameters which include (i) properties of the coal, such as the VM content, particle size and density, and (ii) operating conditions, for example, blast gas Understanding Pulverized Coal Injection in Blast FurnaceControl Blast Furnace Pulverized Coal Injection to Increase PCI Rates Roland Weiser, Ingo Braune, Peter Matthes AMEPA GmbH Jülicher Str 320 D52070 Aachen Germany Tel: +49241168040 Fax: +492411680444 Email: info@amepa Key words: Pulverized coal injection, Coal flow meter, Controlled injection, Equal distribution, Increase of PCIControl Blast Furnace Pulverized Coal Injection to Increase PCI 2016年4月8日 Blast furnaces are countercurrent chemical reactors, widely utilized in the ironmaking industry Hot reduction gases injected from lower regions of the furnace ascend, reacting with the descending burden Through Comprehensive Numerical Modeling of the Blast
.jpg)
Blast Furnace Process Springer
Blast Furnace Process 2 The objective of the blast furnace (BF) is to produce hot metal The blast furnace is a tall, vertical shaft furnace which uses coke to reduce iron ores The product, a hot metal (which is impure iron), is suitable as feed material for steelmaking There are different charging systems for BF discussed in detail2023年8月1日 At present, the blast furnace ironmaking process mainly includes sintering process, coking process, pelletizing process and pulverized coal injection process To study the environmental impact of biomass hydrochar injection on the blast furnace ironmaking process, the environmental impact before and after the application of biomass hydrochar was evaluatedLife cycle assessment of blast furnace ironmaking processes: A 2024年1月1日 The blast furnace injection process system is mainly composed of raw coal storage and transportation system, dry gas preparation system, pulverized coal preparation system, pulverized coal conveying system, pulverized coal injection system, and gas supply system (Fig 1)There is also a computer control center to control the entire pulverized coal Pulverized Coal Injection of Blast Furnace Ironmaking2021年11月3日 Abstract This article discusses the improvement methods of blast furnace energy efficiency by combined injection of preheated pulverized coal fuel and iron oxides (concentrates of advanced beneficiation, flue dust, and others) into its tuyeres The reasonability of the aforementioned measures is substantiated Based on the overall energy balance, their Improvement of Blast Furnace Energy Efficiency by Injection of
.jpg)
Influence of Reducing Gas Injection Methods on Pulverized Coal
2021年8月18日 Medium oxygenenriched blast furnaces that utilize reducing gas injections are a feasible new ironmaking process that can significantly reduce the coke ratio and carbon dioxide emissions To better inject the reducing gas into the blast furnace, two injection methods were designed in this study, and the effects of the reducing gas on the combustion of pulverized 2018年6月21日 These hot gases rise up in the blast furnace and cool down From a maximum of 2000 °C at the level of the hotblast nozzles (tuyere), the temperature decreases to around 200 °C up to the throat At this temperature, the filled charge are first dried and preheated This zone of the blast furnace is therefore called the preheating zoneBlast furnace process tecscience2020年7月15日 The blast furnace process with pulverized coal injection (PCI) rate of up to 250 The oxygen blast furnace process flow chart is shown in Fig 19 (Zhang, HJ et al, 2015) The current problem of oxygen blast furnace is the uneven distribution of recycled gas, which affects the utilization of recycled gasBlast Furnace Ironmaking an overview ScienceDirect Topics2022年2月18日 The injection of hydrogen reducing gas into the blast furnace has become a topic of interest in recent years; however, the stability of blast furnace operation is directly impacted by lowcarbon fuel injection, with limitations due to the quenching effects of the promoted chemical reactions Computational fluid dynamics modeling has been employed to Blast Furnace Hydrogen Injection: Investigating Impacts and
.jpg)
Optimizing Blast Furnace Operation to Increase Efficiency and
Blast Furnaces The blast furnace (BF) is the most widely used ironmaking process in the US A major advance in BF ironmaking has been the use of pulverized coal which partially replaces metallurgical coke This results in substantial improvement in furnace efficiency and thus the reductions of energy consumption and greenhouse gas emissionssubstantially on blast furnace (BF) process which produces about 70% of total world steel production [1] The goal of this process is to reduce the iron oxides into iron by the use of carbon and hydrogen related reducing agents ie coke, coal, oil, natural gas and hot reducing gases, etc [2] The carbon in these fossilbased energiesPROCESS SIMULATION OF BLAST FURNACE OPERATION WITH 2021年11月10日 The effect of hydrogen injection on blast furnace operation and carbon dioxide emissions was simulated using a 1D steadystate zonal model The maximum hydrogen injection rate was evaluated on the Replacement of Pulverised Coal Injection (PCI) with hydrogen and 2021年4月25日 Coal injection into a blast furnace is a very wellestablished technique used as a means to improve the efficiency of the ironmaking process and to reduce the amount of coke charged to the Blast Furnace Injection for Minimizing the Coke Rate and
.jpg)
Feasibility Analysis of Biomass Hydrochar Blended Coal Injection
2022年8月31日 It is critical for the iron and steel industry to achieve green transformation and development by effectively utilizing abundant biomass resources in blast furnace ironmaking In this paper, four types of typical biomass were carbonized and upgraded using the hydrothermal carbonization (HTC) method, and the metallurgical performance of the prepared hydrochar for Download scientific diagram Process flow diagram of a blast furnace in Aspen Plus (Online version in color) from publication: Extending the Operating Line Methodology to Consider Shaft and Process flow diagram of a blast furnace in Aspen Plus2016年1月29日 Fig 1 Schematics of typical air blast system The main components of an air blast system of a blast furnace consist of (i) air blower, (ii) cold blast main, (iii) hot blast stove along with its combustion system, (iv) hot blast main, (v) bustle pipe, (vi) blow pipes and tuyeres known as tuyere stocks, (vii) set of valves, and (viii) control instrumentsAir Blast System for Blast Furnace IspatGuruDownload scientific diagram Schematic presentation of the blast furnace process from publication: Bioreducer use in blast furnace ironmaking in Finland: technoeconomic assessment and CO2 Schematic presentation of the blast furnace process
.jpg)
Maximum Rates of Pulverized Coal Injection in Ironmaking Blast Furnaces
2011年7月15日 The tuyère injection is one of the key tools to exhaust the blast furnace potential and to minimize its CO2 emissions The review argues theoretical basis and operation strategies for ensuring 2022年5月1日 Comparative study on the combustion performance of coals on a pilotscale test rig simulating blast furnace pulverized coal injection and a labscale droptube furnace Development of Particle Flow Simulator in Charging Process of Blast Furnace by Discrete Element Method Miner Eng, 33 (6) (2012), pp 2733 View in Scopus Google Optimization of pulverized coal injection (PCI) rate in an 2021年9月17日 A Comparison of Laboratory Coal Testing with the Blast Furnace Process and Coal Injection September 2021; Metals 11(9):1476; DOI:103390 then switching to a CO 2 flow rate of 100 mL/min until A Comparison of Laboratory Coal Testing with the PDF On Jan 1, 2021, Lingling Liu and others published Optimization of Pulverized Coal Injection (PCI) Rate in an Ironmaking Blast Furnace By an Integrated Process Model Find, read and cite all (PDF) Optimization of Pulverized Coal Injection (PCI)
.jpg)
Mathematical Modeling of the Blast Furnace Process
Dmitriev, A N Mathematical Modeling of the Blast Furnace Process Ekaterinburg: IMET UB RAS, 2019 On the basis of modern concepts, the results of many years of research on the mathematical modeling of the blast furnace process are presented A complex of mathematical models is described, including twoA blast furnace is a block that smelts ores, raw metals and metal armor and tools twice as quickly as a furnace but cannot smelt anything else It also serves as an armorer's job site block A blast furnace can be picked up using any pickaxe If mined without a pickaxe, it does not drop Blast furnaces drop their contents when broken Blast furnaces can generate in any armorer house; Blast Furnace – Minecraft Wiki2021年10月15日 ULCOSpilot testing of the lowCO2 blast furnace process at the experimental BF in Lulea Rev Metall Model studies of liquid flow in the blast furnace lower zone ISIJ Int, 36 (1) (1996), pp 3239 Crossref Industrial practice of Bipci process of pulverized coal injection for blast furnace ironmaking at SSAB Steel Res Modeling of hydrogen shaft injection in ironmaking blast furnaces2023年5月26日 PDF Intensifying hydrogen use in the blast furnace is a key technology for significant coke and CO 2 emissions reductions BF process with injection of hydrogenous gases at shaftImpact of Hydrogenous Gas Injection on the Blast Furnace Process
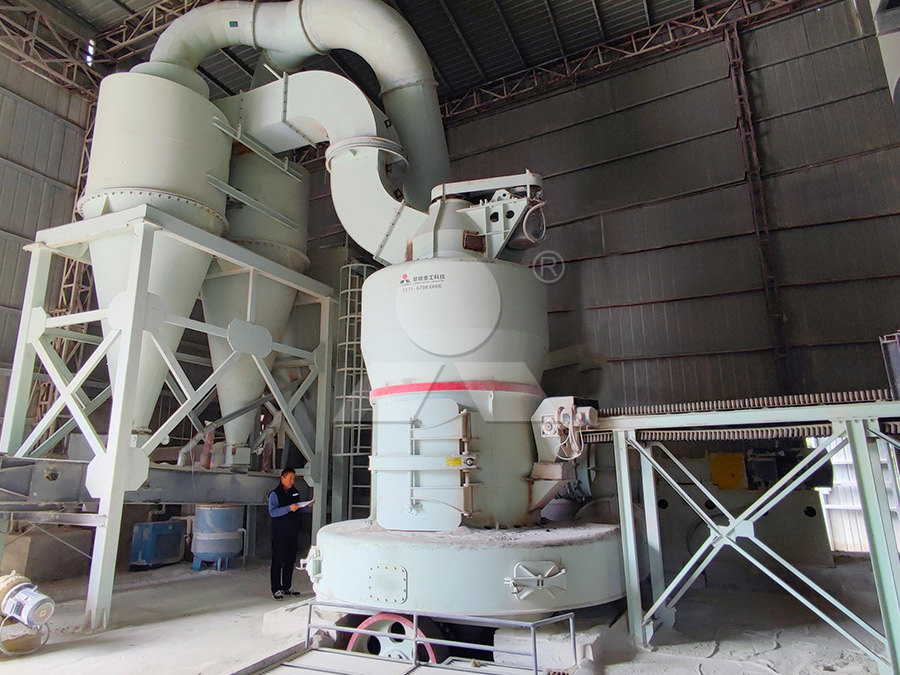
Energy Conservation for Granular Coal Injection into a Blast Furnace
2012年7月31日 Due to the lack of knowledge regarding the combustion of granular coal injected into a blast furnace, injection characteristics of granular coal were first studied through proximate analysis, element analysis, and research of explosivity, ignition point, meltability of ash, grindability, calorific value, etc Using a sampling device in the raceway combined with WASTE PLASTICS INJECTION: REACTION KINETICS AND EFFECT ON THE BLAST FURNACE PROCESS1 Marco Knepper2 Alexander Babich2 Dieter Senk2 Thomas Buergler3 Christoph Feilmayr3 Nina Kieberger3 AbstractWASTE PLASTICS INJECTION: REACTION KINETICS AND EFFECT ON THE BLAST Today in Asia, coal injection equipment is installed on all BFs in Japan, Korea and Taiwan and nearly all of the full sized furnaces in China A goal was set for an injection rate of 150 kg/thm to be achieved in all of China’s large and medium BFs in 2005, and an average 100 kg/thm in the smaller ones (Pei, 2003) Coal injection is installed Use of PCI in blast furnaces ICSCThe blast furnace still dominates the production and supply of metallic units for steelmaking Coke and coal used in the blast furnace contribute substantially to CO2 emissions from the steel sectorBlast furnace process overview Download Scientific
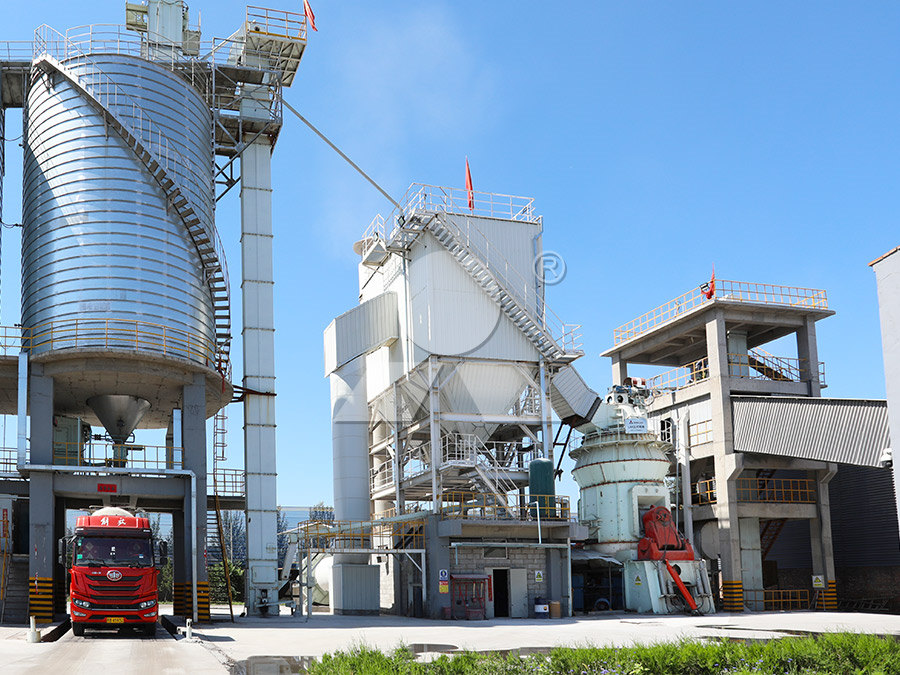
Blast Furnace Granular Coal Injection System Demonstration
Blast Furnace Granular Coal Injection (BFGCI) Process at Bethlehem Steel’s Burns Harbor Plant in Burns Harbor, Indiana The technology is installed on Blast Furnaces C and D, each of these units having a production capacity of 7,000 net tons of hot metal per day In the BFGCI process, granular coal is injected into the blast furnace as a fuelBlast furnaceShanWen Du a, WeiHsin Chen, dec 2005 [3] Numerical analysis for the multiphase flow of pulverized coal injection inside blast Furnace tuyereChingWen Chen, JAN 2005, vol 29, no9, pp 871884 [4]Threedimensional simulation of the pulverized coal combustion inside blast furnaceComputational Analysis of Blast Furnace Pulverized Coal Injection For CO 2 injection into blast furnace tuyeres is a new technology to utilize CO 2 , aiming at expanding the way of CO 2 selfabsorption in the metallurgical industry The decisive factor of whether CO 2 can be mixed into a blastfurnace hot blast and the proper mixing ratio is the effect of CO 2 injection on pulverized coal burnout To investigate the effect of CO 2 injection into tuyeres on Effect of CO2 injection into blast furnace tuyeres on the pulverized Pulverized Coal Injection (PCI) using the denseflow method The Küttner developed and perfected denseflow method offers several advantages over a lowerdensity system Higher injection rates are achieved with simultaneously lower coke rates, which can optimize the fuel costs of the blast furnacePulverized coal injection (PCI) Iron Steel Kuettner Group
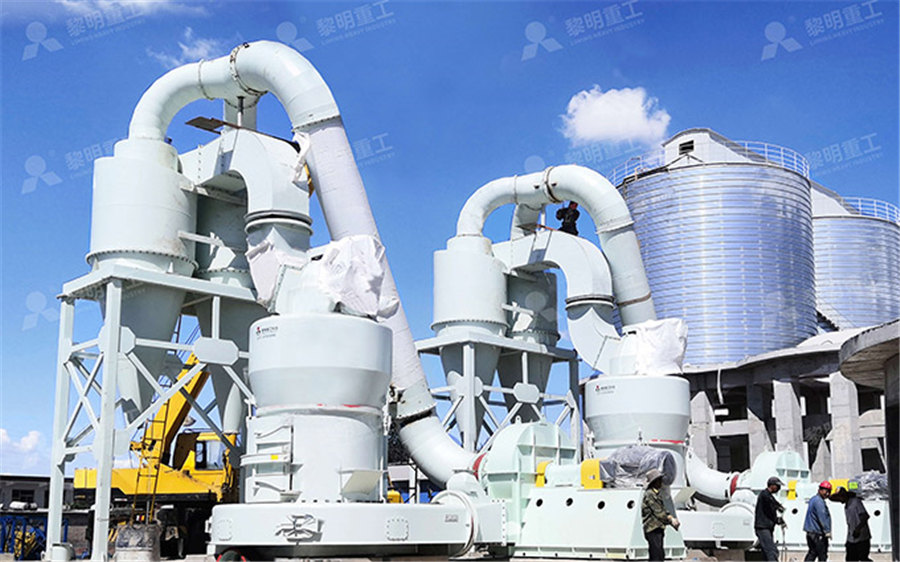
Pulverized coal injection PPT Free Download SlideShare
2018年2月21日 4 WHATIS PCI ? Pulverized Coal Injection (PCI) is a process that involves injecting large volumes of fine coal particles into the raceway of a blast furnace (BF) What it does in BF : Reduces the need of metallurgical coke for reactions in the blast furnace Supplemental source of carbon Speeds up the production of liquid ironthe relationship between raceway characteristic indices, blast furnace process variables, blast furnace production indices, blast furnace energy utilization and COG injection volume, which provide the theory basis for deeply researching the injection of COG into blast furnace, and provide the references for the comprehensive evaluation NUMERICAL ANALYSIS ON BLAST FURNACE LOW CO2 EMISSION enhancement of blast furnace functions, summarizes our blast furnace operations historically and technologically, and provides a view towards future blast furnace operation 1 Milestones of our blast furnace operation technologies Tamura categorized our history of pigiron making into the following three periods, in an articleThe Principle of Blast Furnace Operational Technology and Internally the blast furnace is considered to consist of five discrete zones, see Fig 172, through which all furnace gases and/or liquids must passThe location, shape and extent of each zone is influenced by the properties of the material layers (relative thickness, etc) and by the properties of the materials themselves These factors interact to determine the flow and distribution of Blast Furnace Operation an overview ScienceDirect Topics
.jpg)
Calculation flow chart of blast furnace operation window
Download scientific diagram Calculation flow chart of blast furnace operation window from publication: Use of Hydrogen−Rich Gas in Blast Furnace Ironmaking of V−bearing Titanomagnetite