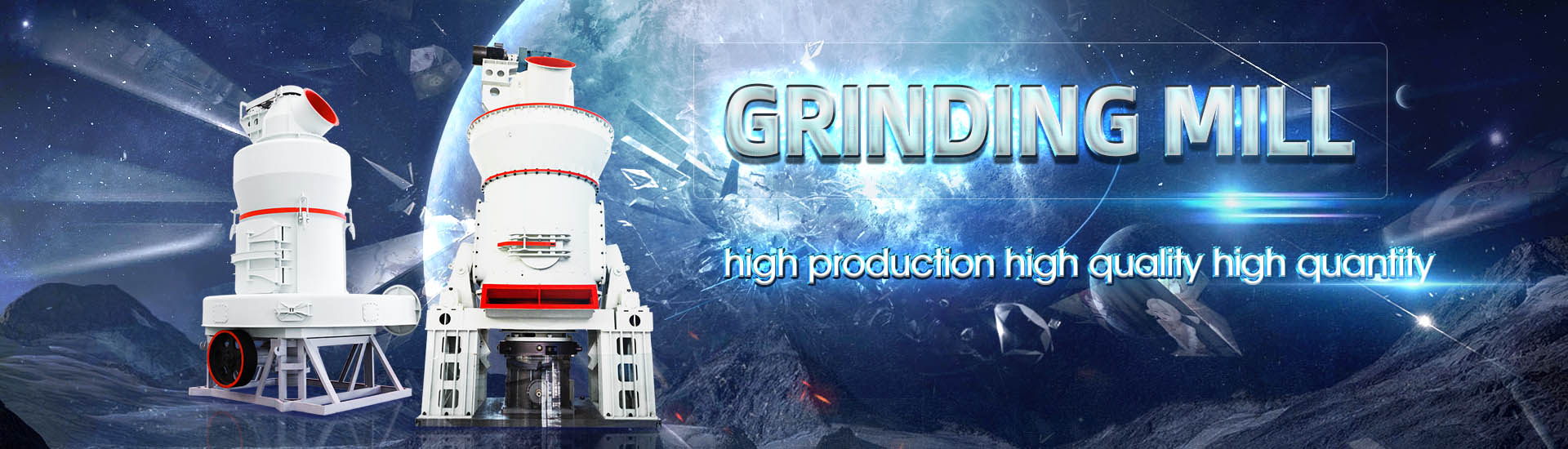
Coal mill inlet blockage
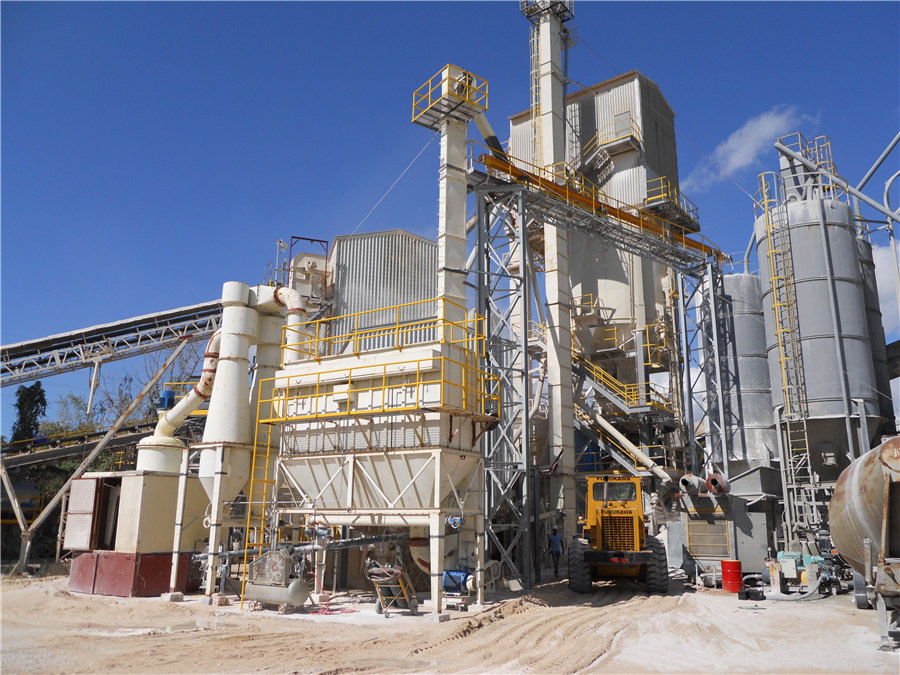
Research on fault diagnosis of coal mill system based on the
2020年9月1日 Coal interruption of the coal mill system is usually caused by the blockage of coal dropping pipe or the fault of coal feeder, which directly lead to the reduction or even 2018年5月2日 Coal mill malfunctions are some of the most common causes of failing to keep the power plant crucial operating parameters or even unplanned power plant shutdowns Therefore, an algorithm has been developed that Detection of Malfunctions and Abnormal Working Thus, more coal falls into the scrapper space than the coal that goes to the classifier, inlet pressure increases, and a plugging mill occurs Monitoring, optimization control, and diagnosis Decision Support System for Coal Mill Fault Diagnosis in Coal 2022年1月1日 The experimental results show that it can effectively detect the coal blocking and coal breaking faults of the coal feeder and the coal mill, effectively reduce the system false alarmResearch and Application of Coal Blockage Early
.jpg)
Detection of Malfunctions and Abnormal Working Conditions of a
2018年5月2日 Coal mills produce the air and pulverized fuel mixture, which is burned in the boiler; hence, abnormal operating conditions can decrease boiler efficiency and increase CO2 2020年1月1日 Taking advantage of unsupervised learning methods and historical process data from distributed control systems (DCS), a stacked denoising autoencoder (SDAE) networkbased approach for monitoringEarly Warning of Critical Blockage in Coal Mills Based 2023年5月23日 Fault 1 is the insufficient coal feed caused by coal inlet tube blockage, and fault 2 is the fault induced by low grinding oil pressure Before faults occur, the HI value is approximately between 85 and 90, and it gradually Health indicator construction and application of coal For a complex equipment with seventeen inputs and six outputs, a power plant coal mill is used as a target to study and model using two methods: least squares linear regression and multilayer Modeling of complex equipment coal mill in power plant ICJE
.jpg)
A Fault Early Warning Method for Coal Mills Based on Causality
2024年9月4日 Li et al proposed a deep learning network based on stacked denoising autoencoder (SDAE) for realizing early blockage warnings for coal mills in coalfired power 2020年6月15日 The blockage of pulverized fuel (PF) conveying pipes on a coalfired power plant is a hazard accident An indepth understanding of the factors that cause PF pipe blockage provides operators with prior knowledge to avoid such accidents Two representative primary air pipe blockage events are observed on two commercial boilers, respectivelyInvestigations into the blockage of pulverized fuel pipes on coal 2018年5月2日 The coal is fed to the coal mill through the central inlet pipe, where it is pulverized by a series of large balls separated by two types of rings The pulverized material is carried out in the millDetection of Malfunctions and Abnormal Working Conditions of a Coal MillThe coal mill system is an important part of the dry process cement manufacturing to do is make sure that they are always in a flow dynamic state to avoid spontaneous combustion and explosion caused by blockage and long Coal Mill – Coal Mill In Cement Plant AGICO Cement
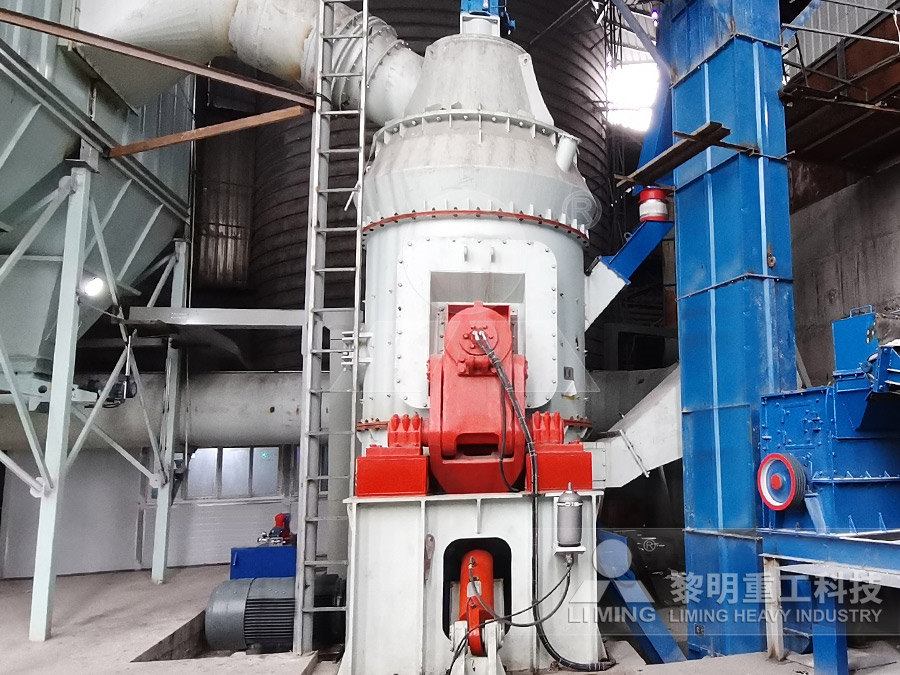
Coal Mill an overview ScienceDirect Topics
The work presented in this paper, is based on a Babcock MPS 212 coal mill used at Elsam’s Nordjyllandsværktet Unit 3 However, the methods proposed in the paper are so generic hence they can be applied to other coal mill types The coal mill is illustrated in principle in Fig 1 The coal is fed to the coal mill through the central inlet pipe2022年1月1日 of the inlet and outlet differential pressur e, and S Guo Cause analysis of boiler MFT accident caused by coal pipe blockage of coal mill[J] Zhejiang Electric Power, no 4, pp: 6668, 2005Research and Application of Coal Blockage Early Warning duty watercooled bearings Pressurized air seals between the rotating mill and inlet/outlet boxes prevent leakage of coal dust or air from the mill Each mill is completely enclosed in an insulated soundattenuating housing with panels that provide easy access to the mill The mill is driven by a directcoupled ac motor throughA Comparison of Three Types of Coal Pulverizers Babcock Powerreferring to fig 1, the online monitoring and early warning system for the operation safety of the medium speed coal mill comprises a pebble coal level sensor 3, a coal mill base vibration sensor 4, a coal mill inlet wind pressure sensor 5, a coal mill inlet wind temperature sensor 6, a coal mill body vibration sensor 13, a coal mill outlet wind pressure sensor 10, a coal mill outlet CNA Mediumspeed coal mill operation safety on
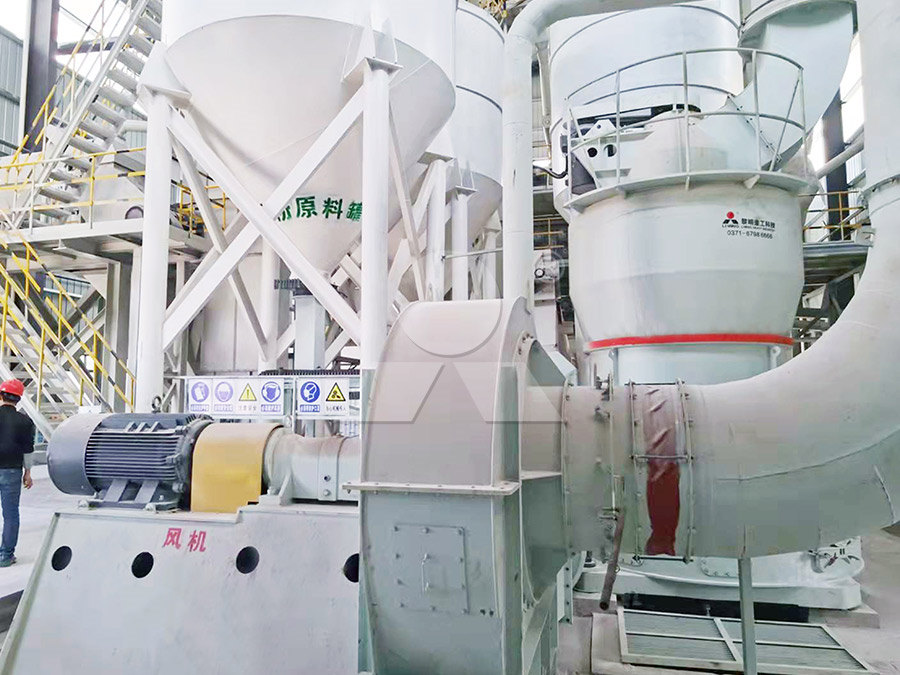
Decision Support System for Coal Mill Fault Diagnosis in Coal
The common reasons are blockage of the coal falling pipe, malfunctions of the coal feeder, etc Such faults are the decrease of differential pressure between the inlet and the coal mill outlet, the reduction of the mill current, and the increased outlet temperature [5]Very hot mill inlet temperatures are required to: Dry coal Achieve mill outlet temperatures Heat required is determined by coal moisture Heat supplied is product of the temperature and quantity of airflow at mill inletMill Inerting and Pulverizer/Mill Explosion Mitigationthe coal pulveriz ing system, the coal feeder and the coal mill run at a continuous high load for a long time will lead to various failures in the coal pulverizing system, and a large number ofResearch and Application of Coal Blockage Early Warning 2019年11月7日 Comprehensive treatment,we should have a test on the 300 MV unit steel ball coal mill pulverizing systemAt the same time,analyze the main operating parameters before modificationTransform the Optimization and transformation of 300MV units steel ball coal mill
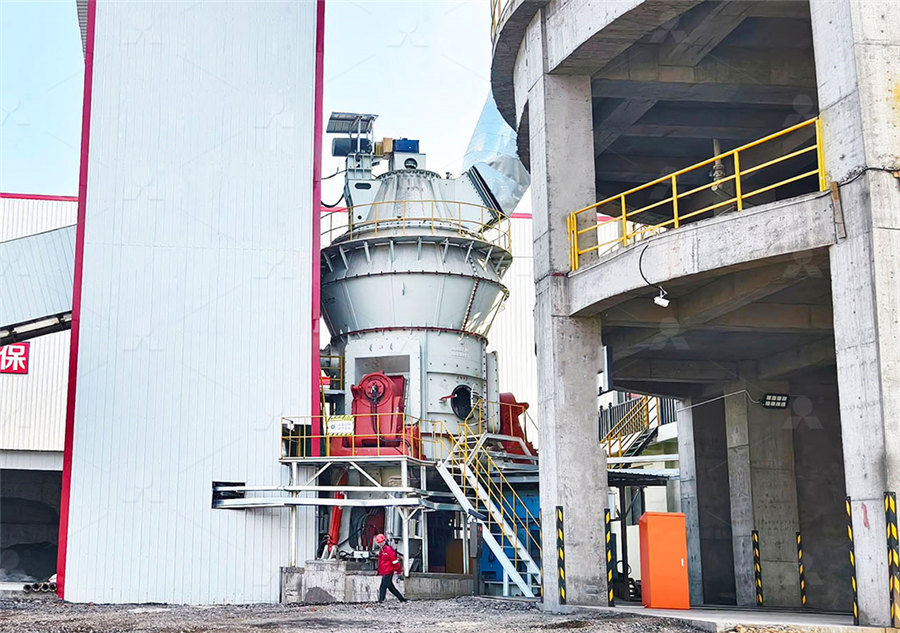
An investigation of performance characteristics and
2020年8月12日 This study shows the performance of a currently running vertical roller coal mill (VRM) in an existing coalfired power plant In a power plant, the coal mill is the critical equipment, whose The invention discloses a method and a system for preventing the coal blockage of a raw 1, increased feeder operation burden; 2, receive the restriction of coal mill temperature out, reduced exerting oneself of coal mill; 3, increased all are connected on the coolant inlet pipe (3) 4 water film type run coal bin according to Method and system for preventing coal blockage of raw coal The ball mill is a traditional coal pulverizer machine, which has been widely used since it was invented In the cement plant, the new dry process cement manufacturing requires the moisture content of coal powder to be 05% ~ 15%, while that of raw coal is 15% ~ 40%Coal Mill in Cement Plant2024年10月15日 Fine coal residue: 12% residue on 90 µm Mill inlet shutoff damper 100% open Mill vent fan outlet damper 100% open Pulverized coal drying: Raw coal is grinded in the vertical coal mill and dried by hot air (usually below 300°) into the vertical roller coal mill, which meets the drying standard of finished pulverized coalCashew Nutshell and Raw Coal Cogrinding for Sustainability
.jpg)
Impact of PCI Coal Quality on Blast Furnace Operations
2003年1月1日 Pulverized coal injection has assisted the steel industry to lower operating costs, extend coke oven life and lower greenhouse emissions As the understanding of the impact of quality of the B coal feed, T / h; m the quality of a fixed length of raw coal on the scraper, kg; V coal feeder measured scraper speed, M / h; L the length of raw coal on the scraper, M Table1Optimization and transformation of 300MV units steel ball coal mill Coal mill is a kind of ball mill, then hot air at about 300℃ blows into the cylinder through the inlet pipe In the drying bin, special lifting plates are arranged to lift up the raw coal, which can effectively prevent the material blockage phenomenon at the entrance of the coal mill; Coal Mill with Industrial Solutions Fote Machinery(FTM)2020年9月1日 There are many reasons for coal blockage, such as a low primary air flow, excessive coal feed flow, low grinding capacity, As a result, the inlet primary air flow of the coal mill is gradually reduced to zero Based on the above analysis, the simulation results are consistent with the fault characteristics of coal blockageResearch on fault diagnosis of coal mill system based on the
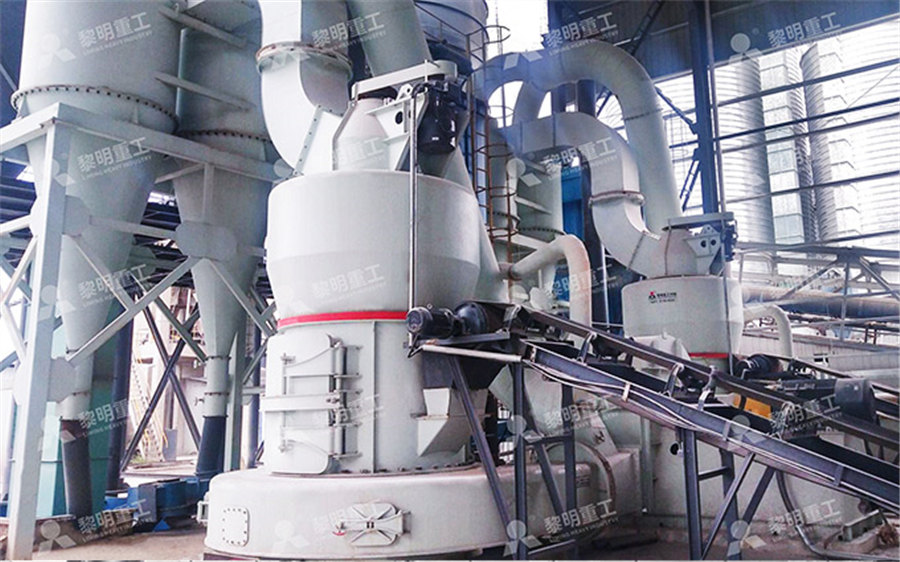
Bowl Mill Coal Pulverizer COAL HANDLING PLANTS
2 The hot air is used for transportation of the recirculating coal within the mill and also for transporting the coal from the pulverizer to the furnace As the coal is continuously reduced in size, the smaller/lighter particles are swept from the bowl by the hot air Hot air (and cool tempering air) is provided by the primary air fans2016年4月1日 This study analyzes the dynamic characteristics of duplex inlet and outlet ball mill direct firing pulverizing system A mass and energy balancebased model is built by thermodynamic analysisModeling and control of ball mill system considering coal moisture2003年1月1日 Wei et al [11] proposed a multisegment coal mill model that covers six milling processes (startup, standard milling, shutdown, idle and transit periods) with parameters identified in each processCoal mill modeling by machine learning based on onsite measurements 2020年8月12日 Ultimately, the energetic efficiency of coal mill has been investigated and performance value has been found to be a maximum value of 962% KEYWORDS: Vertical roller coal mill; energetic performance; coalfired power plant; Coal inlet Co =: Coal outlet M =: Motor CLS =: Classifier Log in via your institution Access through An investigation of performance characteristics and energetic
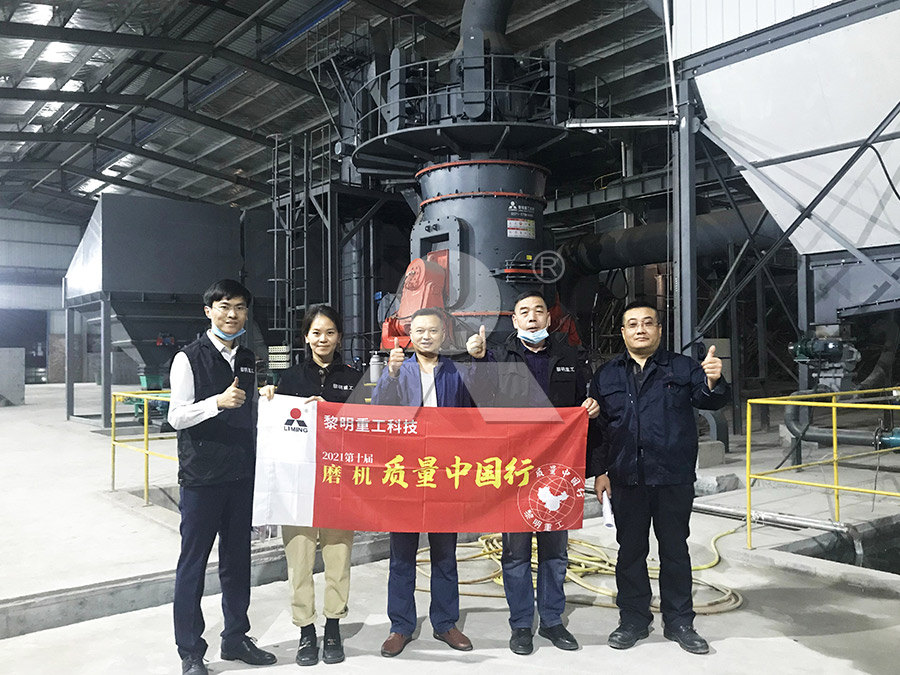
(PDF) MPS mills for coal grinding ResearchGate
2014年1月1日 Two mill systems are employed for most coal grinding applications in the cement industry These are, on the one hand, vertical roller mills (VRM) that have achieved a share of almost 90% and, on Key words: Coal mill classifier, Cut size, Nonswirling inlet, Particle image velocimetry, Impeller rotational speed 摘要: The classification performance of model coal mill classifiers with different bottom incoming flow inlets was experimentally and numerically studiedThe flow field adjacent to two neighboring impeller blades was measured using the particle image velocimetry techniqueClassification performance of model coal mill classifiers with cip2013年3月1日 In this work, two typical faults, mechanical failure and coal blockage, are employed to further demonstrate the superiority of RPPFA over PPFA 15 variables are selected for modeling based on Nonlinear coal mill modeling and its application to model predictive Certainly inadequate drying of coal in a ball mill Installation will reduce output and may lead to blockage of the mill However, Coal drying is ensured by controlling the coal mill inlet temperature, to give a target mill exit temperature, usually between 70 and 900C Drying capability varies according to mill circuit design, COAL PREPARATION AND FIRING INFINITY FOR CEMENT EQUIPMENT
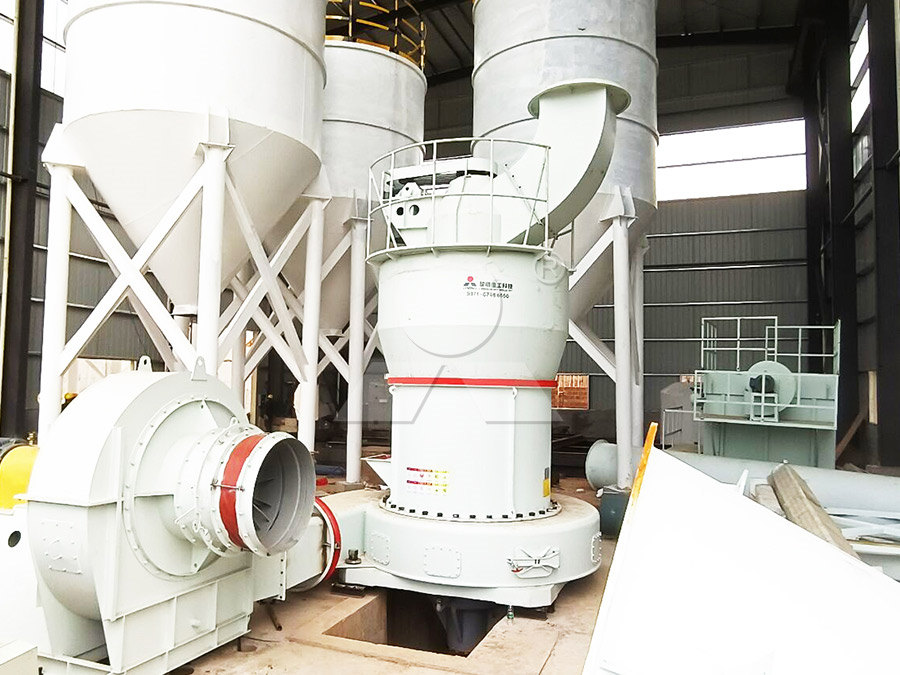
Early Warning of Critical Blockage in Coal Mills Based on Stacked
2020年9月25日 Coal mills have a significant influence on the reliability, efficiency, and safe operation of a coalfired power plant Coal blockage is one of the main reasons for coal mill malfunction It is highly essential to accurately detect the critical blockage in coal mills to ensure a safe and stable operation of the unit Taking advantage of unsupervised learning methods and Previous Post Next Post Contents1 7 Most Common Problem in PyroProcessing for Kiln and Cooler11 Main Reasons for Cycolne Blockage 12 Main Reasons for Kiln Inlet Blockage 13 Main Reasons for big size clinker ball formation 14 Main Reason for heavy coating formation in kiln15 Main Reason for Feed rushes and dust kiln16 SNOWMAN FORMATION IN COOLER17 7 Most Common Problem in PyroProcessing for Kiln and Cooler2020年4月2日 the mill at classifier inlet The mill journa l hydraulic system is design t o control the Coal mill motor power (kW) 0 4171 4548 4390 4586 4562 4410 Mill motor currentAnalysis of the Coal Milling Operations to the Boiler Parameters2021年8月1日 A root cause failure analysis of coal mill vertical shaft used in thermal power plant has been carried out The failed parts of the shaft showed the signature of fatigue failures(PDF) Fault analysis and optimization technology of HP
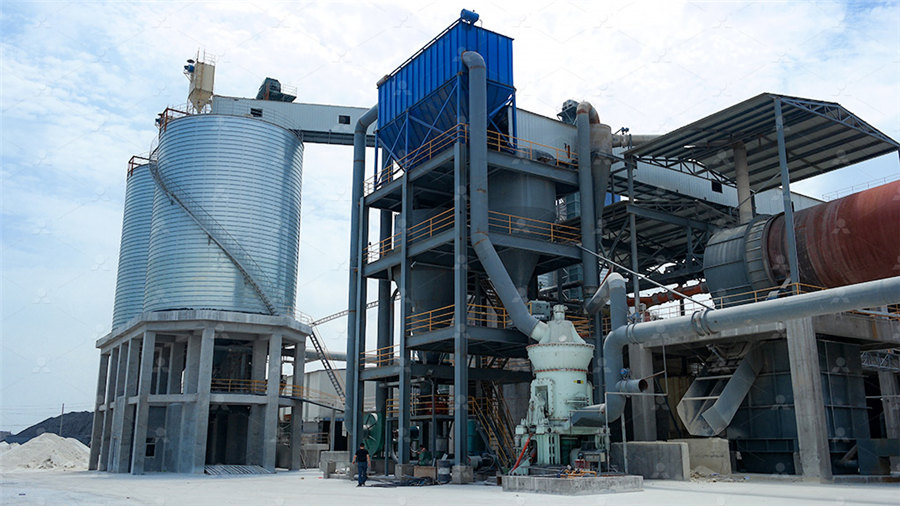
Coal Mills SolidsWiki
Coal Mills are used to pulverize and dry to coal before it is blown into the power plant furnace Operation The coal is feed into the coal mill through a central inlet pipe where gravity is used to lead the coal to the bottom of the mill, where the grinding table and some heavy rollers pulverizes the coal to particlescoal mills may suffer from blockage, fire, shutdown, and enters the coal mill through the inlet pipe, and finally falls onto a constant speed rotating grinding tableA novel multimode Bayesian method for the process monitoring 2021年1月28日 coal mills may suffer from blockage, fire, shut down, and enters the coal mill through the inlet pipe, and finally falls onto a constant speed rotating grinding tableA Novel MultiMode Bayesian Method for the Process2015年5月7日 Coal blockage is one of the main reasons for coal mill malfunction It is highly essential to accurately detect the critical blockage in coal mills to ensure a safe and stable operation of the unitReview of Control and Fault Diagnosis Methods Applied to Coal
.jpg)
Air Swept Coal Mill AGICO Ball Grinding Mill ball mill machines
The air swept ball mill is an ideal grinding machine that merges pulverizing and drying into a single It has the characteristics of high efficiency, energy saving, and environmental protection It is often used as the main equipment in the coal preparation system, which is capable to grind coal of various hardness (the fineness of pulverized coal can reach 85% and the moisture content Cold Air Locking at Mill Inlet: This is very important for coal mill, as ambient air throttling the drying capacity of mill as well as increases the oxygen content of kiln gases making it riskier Oxygen percentage of more than 1214% is considered catalyst for fire/explosion riskCoal Grinding Cement Plant Optimization2015年2月1日 Considering the effect of coal moisture on the energy balance of the coal mill, Zeng [5] et al established a dynamic model of a coal mill and designed an optimized control scheme for the coal Modelling and control of pulverizing system considering coal moistureperancangan slidegate pada inlet booster fan (613fa13) di coal mill laporan tugas akhir oleh dara mutia nim program studi d3 teknik mesin konsentrasi rekayasa industri program eve kerjasama pnj – pt solusi bangun andalas jurusan teknik mesin agustus, 2023 iiPERANCANGAN SLIDEGATE PADA INLET BOOSTER FAN (613FA13) DI COAL MILL