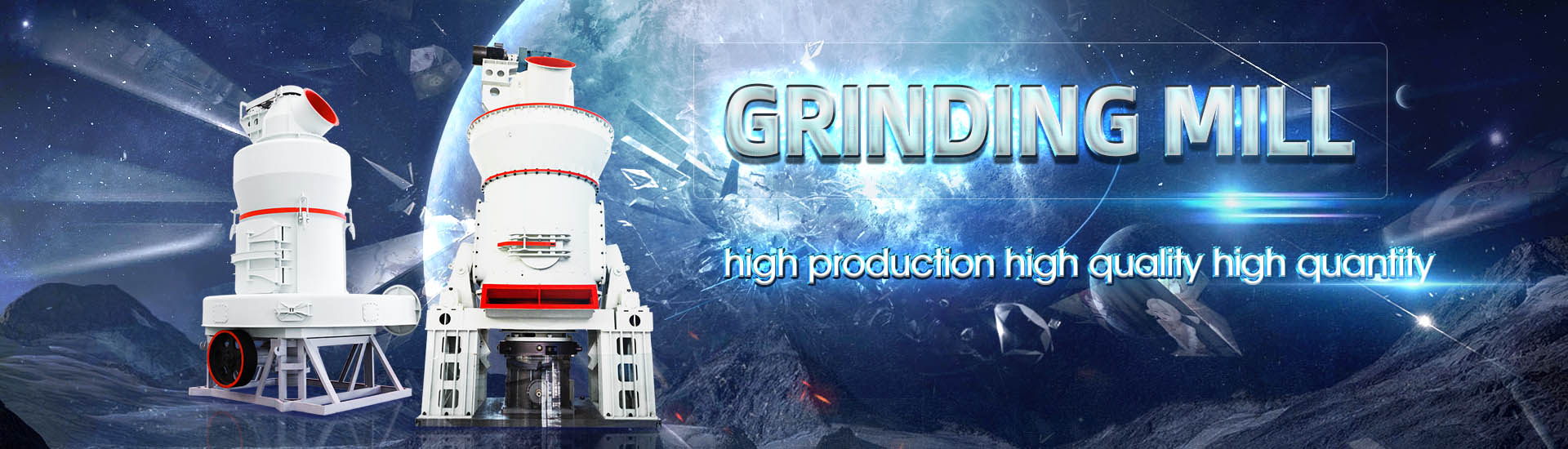
What is the power of the ore mill from China used in the ore powder processing plant
.jpg)
Iron Ore Processing: From Extraction to Manufacturing
2024年4月26日 Iron ore processing is a complex and vital process that transforms raw iron ore into usable steel From exploration and extraction to grinding, beneficiation, and ironmaking, each stage plays a crucial role in How to estimate the power required for a grinding mill ? What is the work index ? What is the power required to mill an ore ?Grinding power : step by step calculation PowderProcess2016年1月1日 This chapter considers comminution for gold ores, starting with breakage induced in the blasting process, continuing through primary crushing, primary milling, and secondary Comminution Circuits for Gold Ore Processing ScienceDirect2017年3月4日 Milling is one of the most important industrial processes The electric power consumption by this process run on ore mining and processing enterprises is variously estimated as a valueSIZE REDUCTION BY GRINDING METHODS
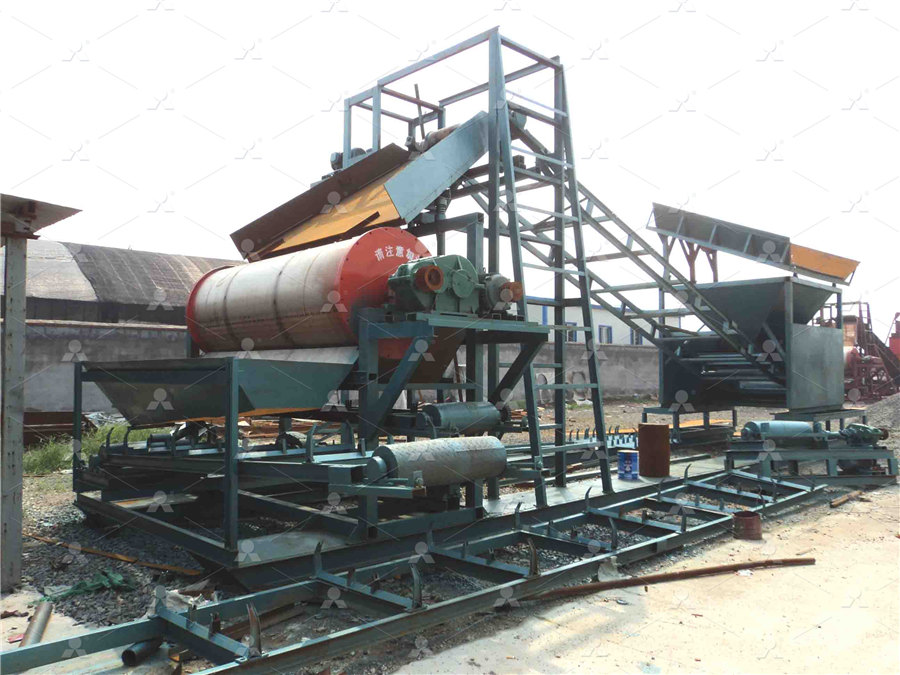
The Chinese Iron Ore Deposits and Ore Production
2018年7月11日 China’s imports of iron ore are mainly iron ore powder, massive iron ore (raw ore) and pellets, respectively, from more than 30 countries and regions, in which Australia, Brazil, India and South Africa are China’s most 2013年12月18日 Fine grinding, to P80 sizes as low as 7 μ m, is becoming increasingly important as mines treat ores with smaller liberation sizes This grinding is typically done using stirred mills such as the Isamill or Stirred Energy Use of Fine Grinding in Mineral Processing2014年10月15日 Dualenergy Xray transmission has been used to sort ore from different mines, and an analysis identifying the economic impact of these results is presented Significant Development of ore sorting and its impact on mineral processing 2022年10月20日 Making iron and steel from iron ore requires a long process of mining, crushing, separating, concentrating, mixing, agglomeration (sintering and pelletizing), and Iron Ore Processing, General SpringerLink
.jpg)
Ore Grinding SpringerLink
2023年7月20日 In the mineral processing industry, ore grinding is the particle size preparation before the separation of the crushed ore Except those that process some placers, almost all 2017年3月4日 The electric power consumption by this process run on ore mining and processing enterprises is variously estimated as a value from 5 to 20% of overall world electric powerSIZE REDUCTION BY CRUSHING METHODS2016年6月6日 Percent Solids – in the mill B Mill Power Mill Speed: Percent Critical/Peripheral; Direction of Rotation; Power Draft Design Drive Power C Total Feed Conditions, including total mill volumetric flow rate; recirculating SAG Mill Grinding Circuit Design 911Metallurgist2024年3月20日 The article provides an overview of the steel making process, detailing how raw materials like iron ore, coke, and limestone are transformed into versatile and durable steel through a complex series of steps depicted in a Understanding the Steel Making Process: A Flow
.jpg)
Ball Mill Design/Power Calculation 911Metallurgist
2015年6月19日 The basic parameters used in ball mill design (power calculations), rod mill or any tumbling mill sizing are; material to be ground, characteristics, Bond Work Index, bulk density, specific density, desired mill tonnage capacity DTPH, operating % solids or pulp density, feed size as F80 and maximum ‘chunk size’, product size as P80 and maximum and finally the type of A mill is a device, often a structure, machine or kitchen appliance, that breaks solid materials into smaller pieces by grinding, crushing, or cutting Such comminution is an important unit operation in many processesThere are many different types of mills and many types of materials processed in them Historically mills were powered by hand or by animals (eg, via a hand crank), Mill (grinding) WikipediaThis is known as dewatering and allows for the water used in ore separation processes to be recycled and reused It is subsequently sent to beneficiation plants for further processing Jump to: Ore separation methods; Ore processing steps after extraction; Equipment for ore processingOre Processing Multotec2023年9月18日 To know more about this process and iron ore mining, contact us and learn all about iron ore, polyurethane, and the associated processes of processing iron ore Stockpiling And Crushing Before being crushed, the iron ore must first be broken up to an F 80 grind sizeTop 6 Steps Of Iron Ore Processing Australian Mining Services
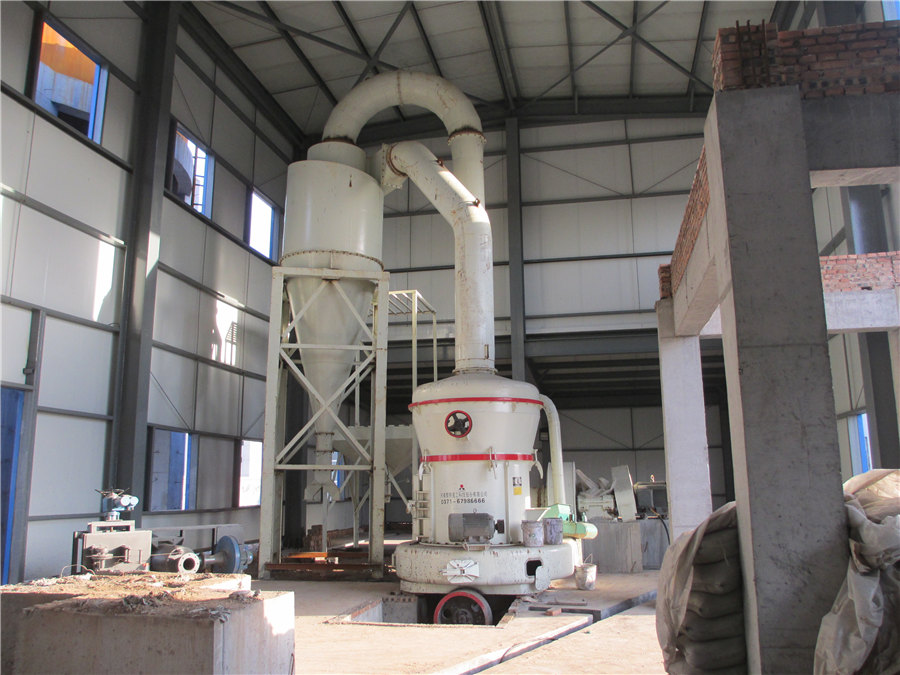
Simulating the Impact of Ore Competence Variability on Process
2019年9月24日 Although ore variability is frequently debated as a major source of uncertainty in process performance, most of the current ore testing methods do not capture this variability and plant designs 2019年8月14日 Ball mill is a common grinding equipment in concentrator Common Types of Ball mill back to top The common industrial ball mills mainly include cement ball mill, tubular ball mill, ultrafine laminating mill, cone ball mill, ceramic ball mill, intermittent ball mill, overflow ball mill, grid ball mill, wind discharge ball mill, double bin ball mill, energy saving ball millThe Ultimate Guide to Ball Mills Miningpedia2023年4月23日 It consumes most of the energy used in mineral processing plants with grinding using up to 50% of the provided energy Tumbling mills are an old technology that is still commonly used for grinding(PDF) Grinding Media in Ball MillsA Review ResearchGate2009年1月1日 Also, equipment like ball mill is used at the final stages of grinding Among the comminution and grinding equipment, HPGR is increasingly utilized as tertiary crusher or primary mill because of Processing of Magnetite Iron Ores–Comparing
.jpg)
(PDF) The Chinese Iron Ore Deposits and Ore Production
PDF On Jul 11, 2018, Guangrong Li published The Chinese Iron Ore Deposits and Ore China iron ore import country to increase a large number of mineral processing, power plants, water and 2018年11月19日 PDF The aim of mineral processing is to get the mineral from rock or Ore that has good economic value in the market Generally, the ability of Find, read and cite all the research you need (PDF) Comminution in mineral processing2016年2月29日 The processing of gold ores has traditionally made use of conventional crushing and grinding circuits In each case where gold is formed either as coarse native particles or in coarse grained sulphides, it is recovered by gravimetry concentration in the in the comminution circuit in addition to recovery of finer values by leachingGold Extraction Recovery Processes 911Metallurgistmineral processing, art of treating crude ores and mineral products in order to separate the valuable minerals from the waste rock, or gangue It is the first process that most ores undergo after mining in order to provide a more concentrated material for the procedures of extractive metallurgyThe primary operations are comminution and concentration, but there are other Mineral processing Metallurgy, Crushing Grinding Britannica
.jpg)
Essential Guide to Mineral Processing Equipment Flyability
Mineral processing is an important step in converting ore into a product that can be sold and used for everyday applications What Are the 4 Stages of Mineral Processing? Aside from profitability, the main objective of mineral processing is to break down ore from its heterogeneous properties and turn it into a homogeneous product to sell2013年12月18日 Fine grinding, to P80 sizes as low as 7 μm, is becoming increasingly important as mines treat ores with smaller liberation sizes This grinding is typically done using stirred mills such as the Isamill or Stirred Media Detritor While fine grinding consumes less energy than primary grinding, it can still account for a substantial part of a mill’s energy budget Overall Energy Use of Fine Grinding in Mineral Processing2023年10月27日 The ball mill is a rotating cylindrical vessel with grinding media inside, which is responsible for breaking the ore particles Grinding media play an important role in the comminution of mineral ores in these mills This work reviews the application of balls in mineral processing as a function of the materials used to manufacture them and the mass loss, as A Review of the Grinding Media in Ball Mills for Mineral Processing A sinter plant is used to agglomerate iron ore to produce sinter, a product that can be used in a blast furnace#91;1#93; According to the US Environmental Protection Agency, the sintering process converts finesized raw materials, including iron ore, coke breeze, limestone, mill scale, and flue dust, into an agglomerated product, sinter, of suitable size for charging into the blast Sinter plant Global Energy Monitor
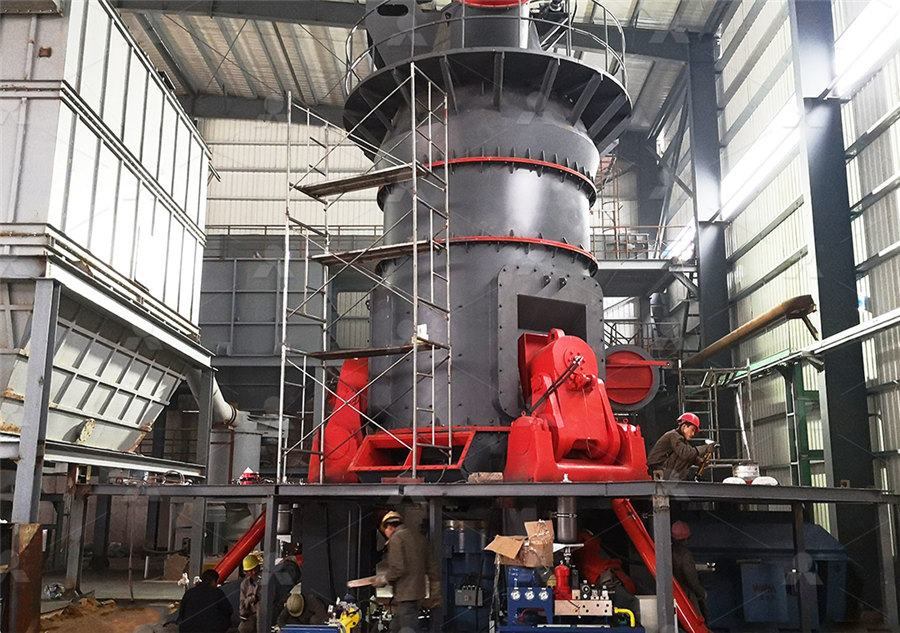
Overview of Mineral Processing Methods ResearchGate
2015年8月3日 The electric power consumption by this process run on ore mining and processing enterprises is variously estimated as a value from 5 to 20% of overall world electric powerThis article delves into the journey from ore to alloy, exploring the technologies, challenges, and innovations that shape modern ironmaking 1 Iron Ore: Source of Steel's Strength Iron ore, primarily hematite and magnetite, serves as the From Ore to Alloy: Navigating Ironmaking in Modern 2024年10月30日 Ore is a deposit in Earth’s crust of one or more valuable mineralsThe most valuable ore deposits contain metals crucial to industry and trade, like copper, gold, and iron Copper ore is mined for a variety of Ore National Geographic Society2017年7月26日 We will consider an ore with a ball mill work index varying between 16 and 13, feeding into a single stage ball mill operation with one million kilowatts per day consumed power For the particular mill configuration, a performance graph, Fig (21), has been constructed according to Bond’s methodsHow Ball Mill Ore Feed Size Affects Tonnage Capacity
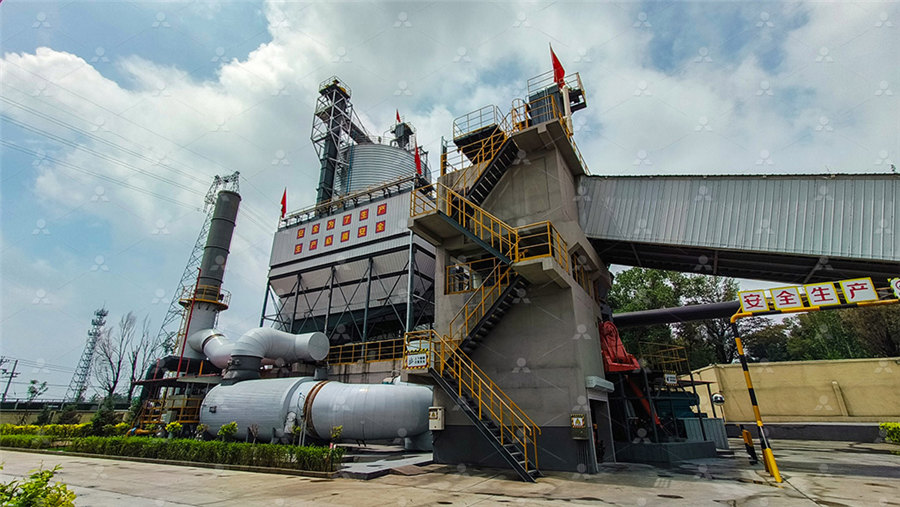
From Ore to Iron with Smelting and Direct Iron Reduction
2017年10月17日 Smelting Reduction Figure 2: The smelt reduction vessel (SRV) is the core technology component of the Hismelt process Source: RioTinto While years of ironmaking technology innovations have optimized blast furnace productivity, two alternative processes—smelting reduction and direct iron reduction— are growing in adoption The BLOOMS: A Semifinished product, usually in square (at times in rectangular) section of cross sectional size exceeding 5”x5” (125mm X 125mm) In some of the modern mills, the term bloom is used to cover such products of cross sectional size exceeding 8”x8” These are inputs for producing Heavy sections and Sheet piling section normally by hot rollingGlossary of Terms/ Definitions Commonly Used in Iron Steel 2017年2月13日 In general, therefore, the required mill power is calculated using the following equation where n is the number of efficiency factors, EFi, used and fo is the feed rate of new ore to the mill The power calculated from equation 2 can be looked up in published tables (Rowland and Kjos, 1978) and the correct mill size and type can be selectedBall Mills 911Metallurgist2023年10月25日 Iron ore is a crucial raw material for the global steel industry, and its supply chain is a complex network that involves multiple stakeholders and activities The iron ore supply chain begins with the mining of iron ore, which is then transported to processing plants for beneficiation and further refinement The refined iron ore is then transported to steel mills for Iron Ore Supply Chain: From Mining to Steel Production

Crushing in Mineral Processing 911Metallurgist
2015年12月26日 In mineral processing or metallurgy, the first stage of comminution is crushing Depending of the type of rock (geometallurgy) to be crushed, there are 2 largely different techniques at your disposition for crushing rocks In principle, compression crushing is used on hard and abrasive rocks by placing them between a high wearresistant plate/surface2023年7月20日 Therefore, the rod mill is mostly used for coarse grinding of the previous period of ball mill, or grinding of brittle materials and materials against overcrushing, such as tungsten and tin ore before gravity separation; and (3) autogenous mill – it refers to the materials which themselves are collided and ground mutually to be crushed when the grinding mill rotates, and Ore Grinding SpringerLinkGenerally, mineral processing begins when an ore is delivered from a mine, to a processing facility At this point, the ore is called runofmine material because there has been no treatment performed on it There are three primary types of runofmine materials: Runofmine consisting of useful materialsIntroduction to Mineral Processing or Beneficiationof oxygen from iron ore in its solid form The iron used in the steelmaking process is currently chemically reduced from iron ore through the use of fossil resources – natural gas or coal This process is known as Direct Reduced Ironmaking (DRI) Carbon combines with the oxygen in the iron ore, producingFact sheet Hydrogen (H2)based ironmaking
.jpg)
The effects of ore blending on comminution
2018年8月17日 The concept of ore blending is a very relevant notion in modern high tonnage production mines It is not only essential for the prolongation of the mine life of the concerned mine but as well as a 2022年10月4日 A notable fact is that the energy efficiency of conventional milling is only about 1%, as mentioned in Sect 1 An earlier experimental study indicated that about 80–90% of the energy input of a ball mill was used in heating the material (Schellinger 1951, 1952), and a recent study showed that over 75% of the electrical energy was used to heat the slurry (Bouchard et Reduction of Fragment Size from Mining to Mineral Processing: A 2023年11月30日 In a coalfired power plant, a mill or pulverizer plays a crucial role in the process of converting raw coal into a form that can be burned efficiently and used to generate electricityWhat is the role of a mill in a coalfired power plant?2024年8月23日 China accounts for 15% of global production, with the largest producers being Australia, Brazil, China and India Exports of iron ore from China increased by 2% in 2023 over 2022, with the highest share being exported to Japan China’s iron ore exports are expected to drop at a CAGR of 018% between 2023 and 2027Iron ore in China Mining Technology
.jpg)
Study on the Selection of Comminution Circuits for a Magnetite Ore
2016年4月26日 Based on the ore characteristic parameters derived from the standard drop weight and Bond work index tests as well as the size requirements for the final products, the SAG + ball mill process was simulated on the JKSimMet platform to determine the required sizes of the mills and the driving power, eg, Φ1006 m × 503 m for the SAG mill, Φ503 m × 823 m for 2016年1月8日 The first commercial production of phosphate rock began in England in 1847 A wide variety of techniques and equipment is used to mine and process phosphate rocks in order to beneficiate lowgrade ores and remove impurities The eighth chapter of this book deals with mining and beneficiation of phosphate ore The principle and operating conditions of important Mining and Beneficiation of Phosphate Ore IntechOpenThe capacity is about 100 tons of ore a day The quartz mill at the Vulture is a modern twenty stamp mill, each stamp weighing over a ton At this time, the stamps are the heaviest in use in the country The ore is taken from the mine and crushed to a suitable size in an AllisChalmers gyratory crusher, carried to the storage bin in an ore carWinning the Metal: Ore Mills of the West Western Mining History2019年1月15日 There are two economic sources of lithium; brines and hard rock ores The majority of the global lithium production, greater than 60%, is produced from brines while lithium ores accounted for the remaining production (Ebensperger et al, 2005)Table 1 summarises the world’s major lithium producers from ores and brines, and the total reservesThe beneficiation of lithium minerals from hard rock ores: A
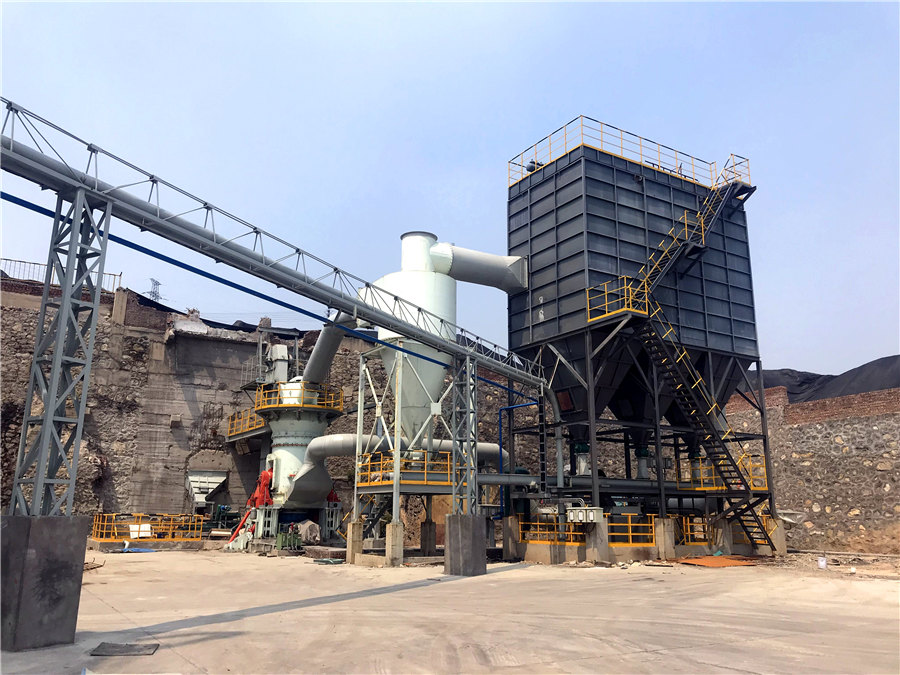
Mineral Processing SpringerLink
The mineral processing technologies in China should be focused on the following fields: intensified research into modern mineral processing theories; develop the green, ecofriendly, and fine mineral processing technologies that match the beneficiability of mineral resources; develop the large, highefficiency, and energysaving mineral processing equipment; develop the