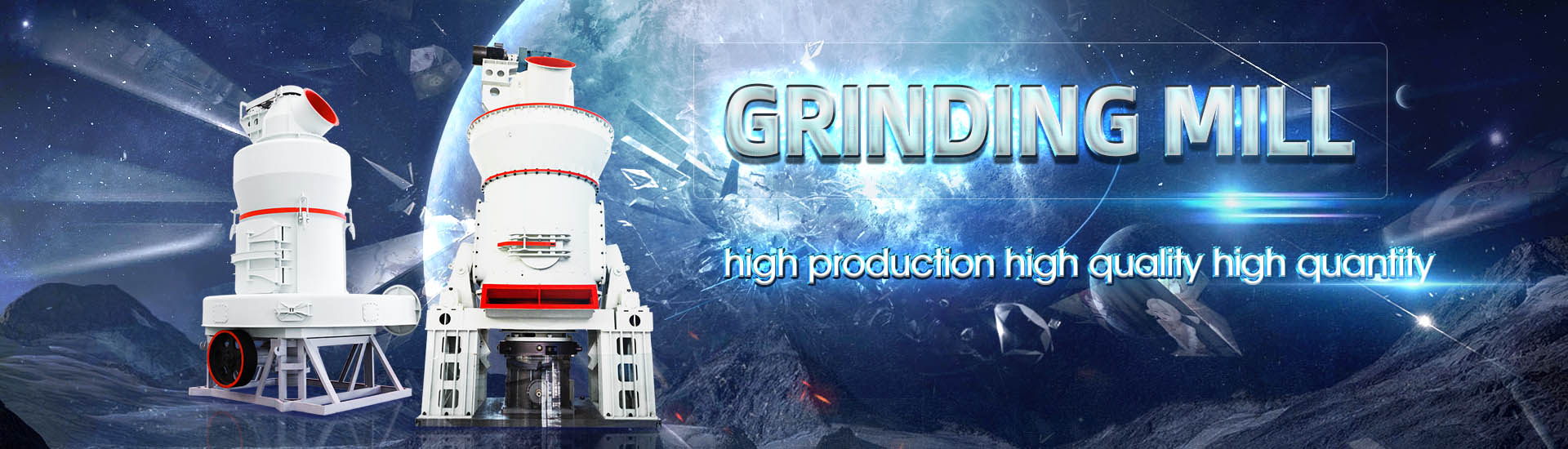
White clay slag refining equipment
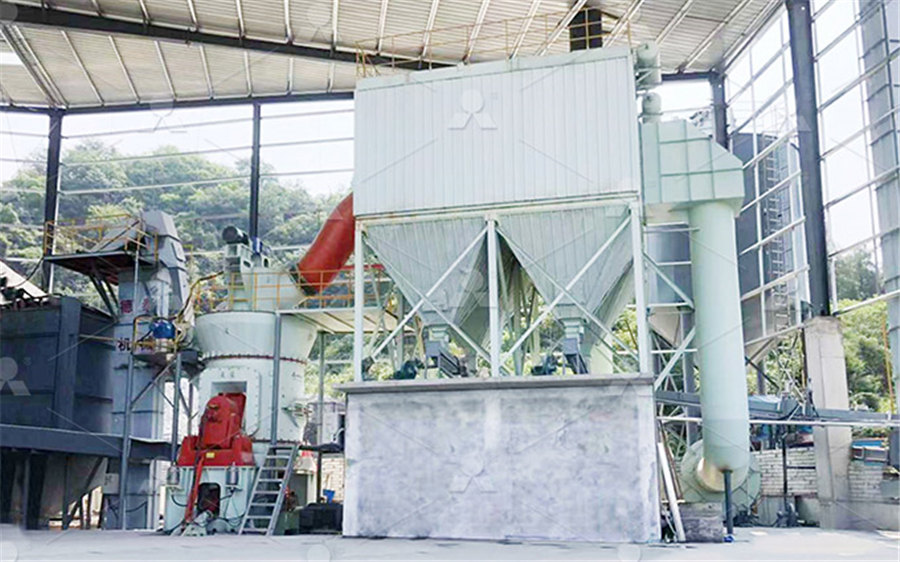
Ladle Steel Slag in Activated Systems for Construction Use MDPI
2020年6月18日 The current research aims to study the possibility of obtaining a binder by alkaline activation from ladle furnace slag (white slag) and to evaluate its application to Bontrue New Materials Co, Ltd is China’s leading supplier of tabular alumina, blast furnace slag, refining slag, taphole clay, well block, tapping hole block, and nozzle brickBontrue New Materials Bontrue New Materials2021年7月12日 The ladle furnace (LF) slag, which is also known as basic slag, reducing slag, white slag, or secondary refining slag, is a byproduct of the final stages of steelmaking, when Steel slags in cementbased composites: An ultimate review on 2023年11月23日 The steel slag produced during the ladle refining stage consists of calcium oxide (CaO) and magnesium oxide (MgO), contributing to 60 % of its weight All the other added alloys and the chemicals used to protect Ladle Furnace Slag: Synthesis, Properties, and
.jpg)
Ladle Furnace Process SpringerLink
2024年1月1日 The white slag of LF furnace is mainly comprised of calcium oxide–calcium fluoride The slag quality is usually 2–4% of liquid steel The slag can adsorb and dissolve the oxides in liquid steel, thus realizing deoxidation2024年11月26日 Ladle furnace slag (LFS), a byproduct of steel refining, shows a promising reuse pathway as an alternative additive or substitute for Portland cement due to its high Potential Reuse of Ladle Furnace Slag as Cementitious Material: A As a result of growing environmental awareness, steel slag is now highly regarded as a recycled material that can reduce environmental impact due to its resourceconservation and energysaving properties MEKA is designing and Slag Recycling and Metal Recovery MEKA2018年11月7日 Slag in ironmaking and steelmaking processes has several metallurgical functions such as preventing contamination by atmosphere, providing thermal insulation, and removing impurities in the liquid metal Slag Treatments and Recycling of Metallurgical Slags
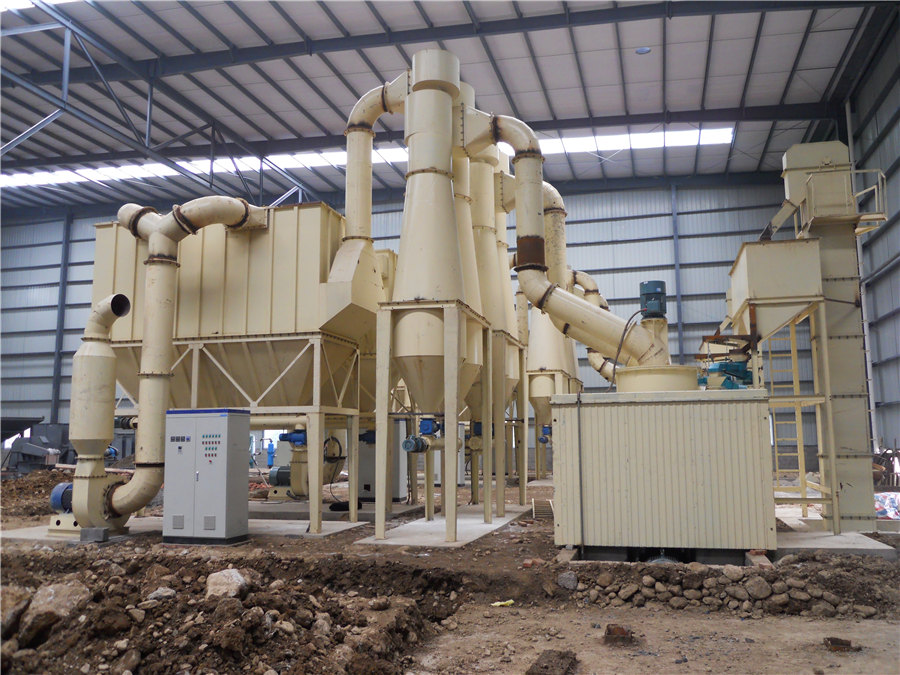
Ladle Steel Slag in Activated Systems for Construction Use
2020年7月31日 In terms of refining steel slag (ladle or white slag), it is estimated that for each ton of steel, between 20 and 30 kg of slag is produced; that is, in 2016, more than 700,000 2019年5月23日 Steel slag is the waste generated in the steelmaking process and includes ferric oxide and the impurities of some infusible matters It is the byproduct when slagforming Comprehensive Utilization Technology of Steel Slag2023年9月19日 Understanding Refining Refining is the process of purifying gold to remove any impurities that may be present This is done to ensure that the gold is of the highest quality and purity, making it more valuable The refining Understanding the Gold Melting and Assaying Process: 2023年9月1日 In the present work, “slag–steel” equilibrium experiments were carried out at 1873 K to determine the effects of C/A ratio (CaO/Al 2 O 3) and the binary basicity (CaO/SiO 2) in Al 2 O 3 –CaO–SiO 2 –MgO(–CaF 2) refining slags on the characteristics of the inclusions and sulfur (S) content in 316L stainless steelsThermodynamic investigations were performed to Influence of refining slag on transformation and separation of
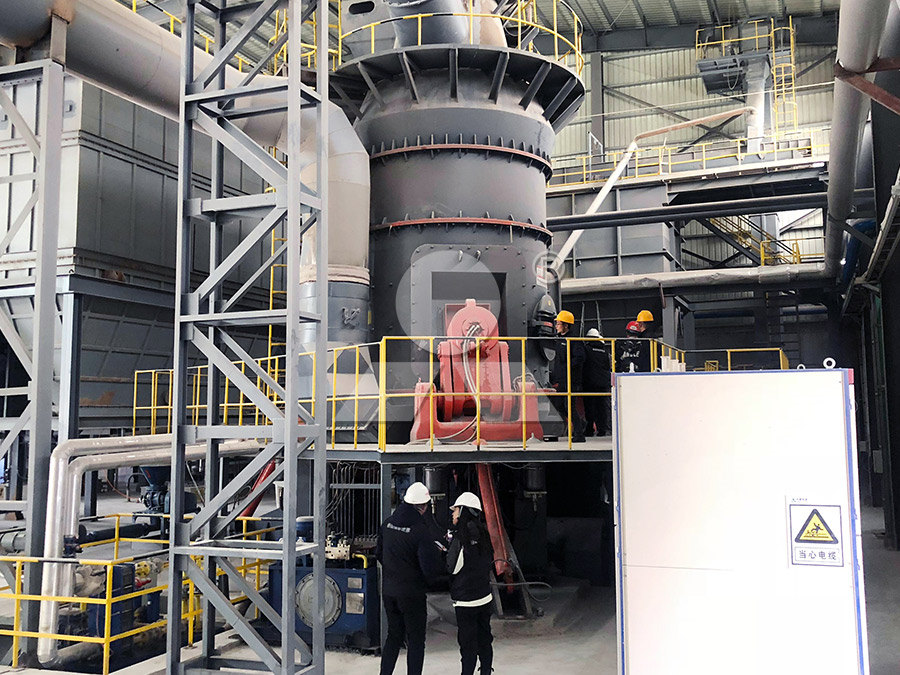
Metallurgical Mechanism Guided Machine Learning to Predict Slag
2024年4月1日 This study analyzed the impact of gas flow rate, oil layer thickness, and purging plug position on oil eye area and oil entrapment depth during ladle refining To this end, a singleplug stirred water model system was used to experimentally investigate the dynamics of slag entrapment, which plays a vital role in purifying molten steel Highdefinition cameras captured Calcium aluminate is an inorganic salt with the chemical formula 3CaOAl2O3 It is a white cubic crystal Relative density 3038, decomposes when heated to 1535°C Insoluble in water, soluble in acid It is commonly found as hexahydrate with a molecular weight of 37796 and is a spherical colorless or white crystalline powderCalcium Aluminate/Refining Slag Manufacturers, Calcium 2020年11月19日 Slag refining of silicon has been modified in recent years by combining the process with solvent refining, in which an alloy of silicon is first treated by slag and then solidified under controlled conditions to yield highpurity silicon crystals This paper discusses the effect of alloying elements on the efficiency of slag treatment A set of criteria are established and A Review of Slag Refining of Silicon Alloys JOMThe process of LF Refining is introduced in this paperThe LF method is a ladle without vacuum equipment can arc refining methodBecause the LF ladle furnace has the advantages of simple equipment, low investment cost, flexible operation and excellent refined effect, are widely used and developed in many countriesThe argon is blown from the bottom of the ladle, and molten The Introduction of the LF Refining Function and Process
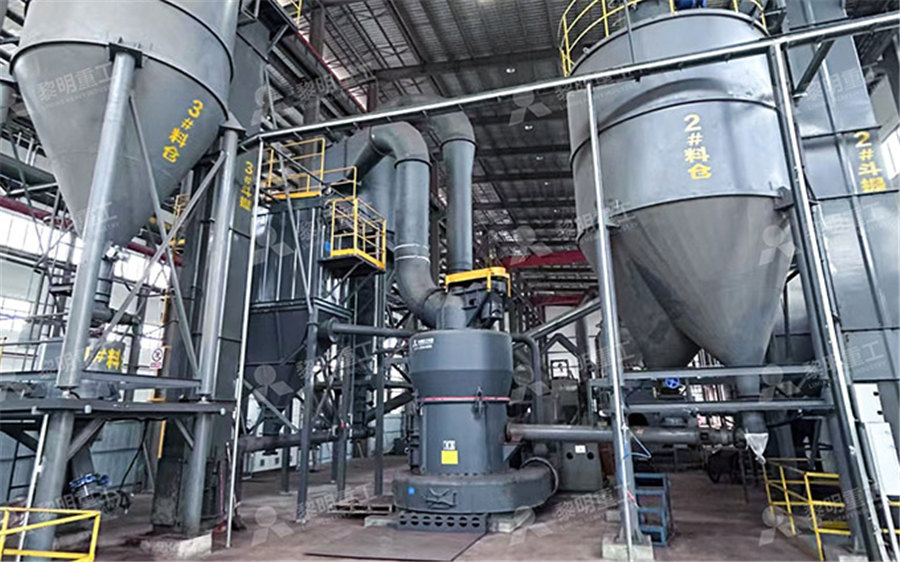
Bontrue New Materials Bontrue New Materials
Possessing sophisticated production lines and inspection equipment, Product Information White Fused Alumina( also known as white corundum or costeffective products, solutions and services The main products are tabular alumina, blast furnace slag, refining slag, taphole clay, well block, tapping hole block and nozzle brick Companykaolin clay refining) and various additives K Okada, T Toya, Y Kameshima A Nakajima Department of Metallurgy and Ceramics Science, Tokyo Institute of Technology, Japan Abstract Five different glassceramics were prepared from Kira (waste byproducts from processing of silica sand and kaolin clay) with various additives Mixtures ofProperties of glassceramics prepared from Kira (waste by 2024年1月1日 The carbon monoxide generated will enhance the reducing property of the atmosphere in LF furnace (4) White slag refining The white slag of LF furnace is mainly comprised of calcium oxide–calcium fluoride The slag quality is usually 2–4% of liquid steel The slag can adsorb and dissolve the oxides in liquid steel, thus realizing deoxidationLadle Furnace Process SpringerLink2014年2月1日 Numerous approaches have been reported on using slags to refine silicon melts, such as the removal of Al, Ca, and B by slag refining Related slag systems, such as CaOSiO 2 , CaOSiO 2 CaF 2 (PDF) Mass Transfer in Slag Refining of Silicon with Mechanical
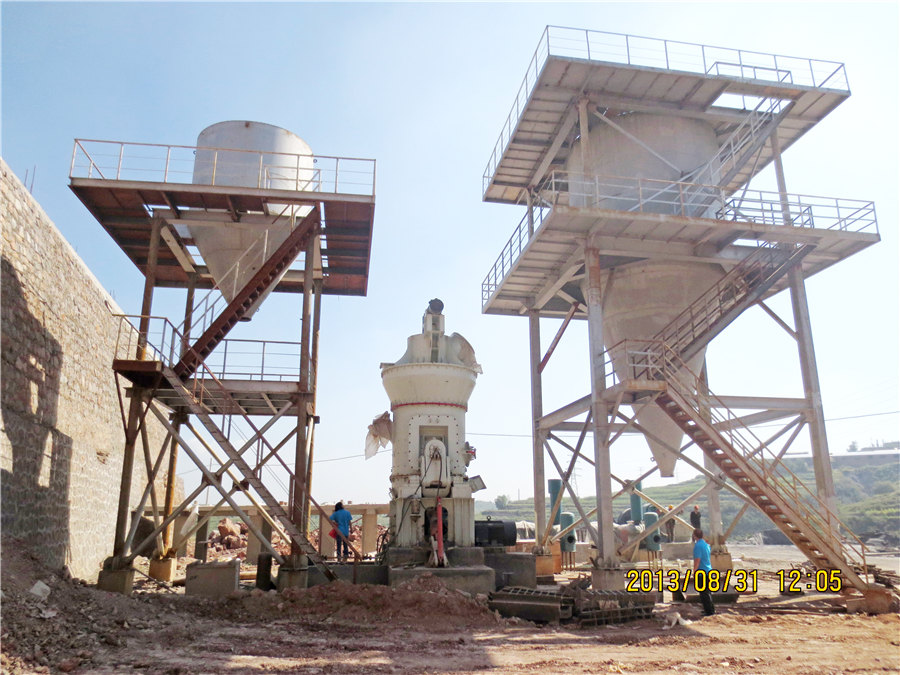
Mass Transfer in Slag Refining of Silicon with Mechanical Stirring
2013年12月7日 Experiments have been carried out to study the rates of mass transfer between liquid silicon and CaOSiO2 slag with impeller stirring at 1823 K (1550 °C) The occurrence of transient interfacial phenomena related to the mass transfer of calcium has been observed; the evidence suggests that the reduction of calcium oxide at the interface leads to a rapid, 2023年11月15日 With the increasing demand for energy conservation and emission reduction, more attentions have been paid to the intelligentization, greenization and low carbonization during the transformation and upgrading of steelmaking plants Ladle furnace (LF) refining is one of the key procedures in steelmaking process and has been widely used in steelmaking plants for its Modeling of LF refining process: a review Journal of Iron and 2023年11月23日 With increased slag usage, the ladle refining process of steelmaking can be turned into a more carbonneutral process 1 Introduction and some may result in lowquality products depending on the mineral and Ladle Furnace Slag: Synthesis, Properties, and 2020年11月23日 It was found that removal of B and P through slag refining alone is not practical on an industrial scale as it would require a large volume of slag, White et al 8 used a CO(g) and(PDF) A Review of Slag Refining of Crude Silicon ResearchGate
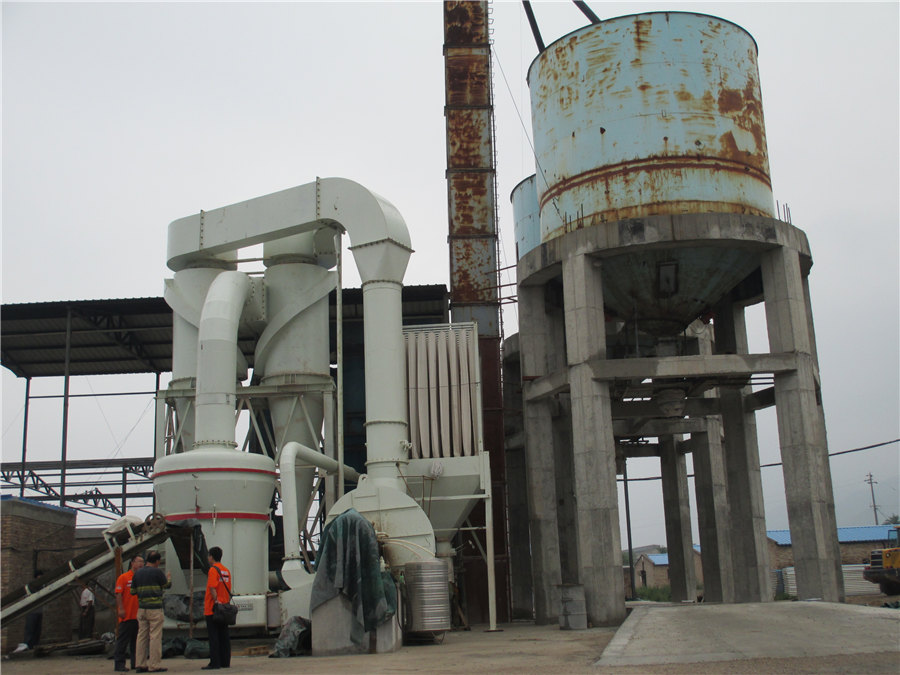
Mass Transfer in Slag Refining of Silicon with Mechanical Stirring
2014年9月11日 Mechanical stirring was demonstrated to be a potent means to increase the mass transfer rates of B and Ca in slag refining of silicon, and optimal stirring conditions were attained with only a modest kinetic energy input into the melt Experiments were undertaken to measure mass transfer rates between liquid silicon and CaOSiO2 slags at 1823 K (1550 °C) 2016年8月31日 Current total productions of steel slag in India, are around 12 million tonnes per annum (Indian Minerals Yearbook, May 2016), which is far behind the developed countriesSteel Slag Utilization — Overview in Indian Perspective2016年5月4日 Produces Slag as a byproduct for lower tier refining products (crushed, chunks, crystals) GFX by Arch666AngelFiltration Unit: Filters dissoluted slag, needs a constant supply of filters to do that Filter are made disposeable from coal or multi use from ceramic (alumina)Angel's Refining Factorio ForumsFLS offers a comprehensive range of equipment and processes for the recovery of precious metals, including complete carbon ADR and Merri ll Crowe systems, cyanide leach, precious metals electrowinning and refining equipment, carbon regeneration kilns, mercury retort and abatement systems, and gravity concentration and intensive cyanidation systemsEnhance precious metals recovery with FLS
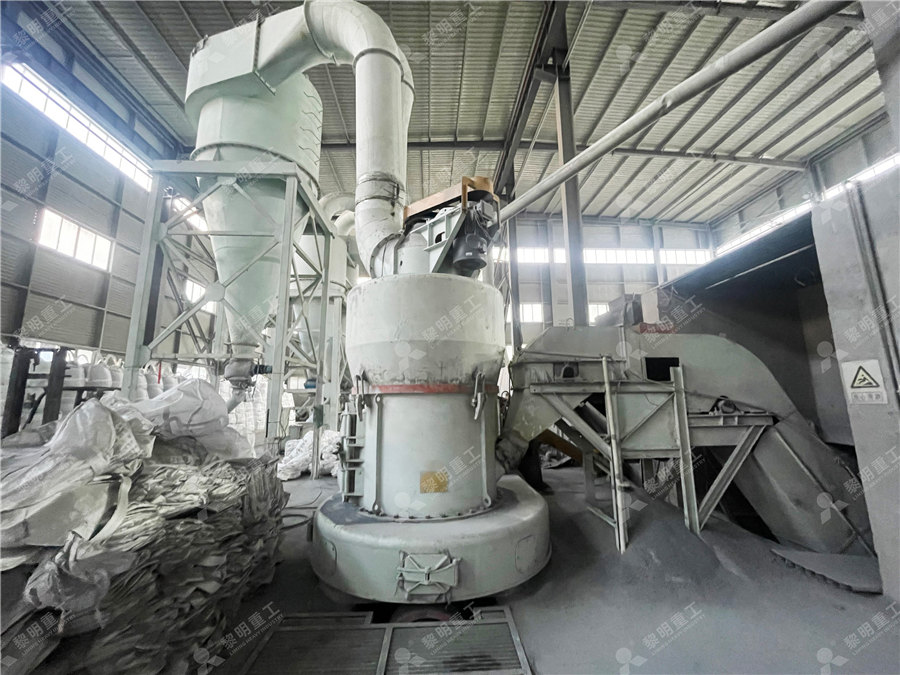
Study on recycling Si from silicon diamondwire saw cutting waste
2023年4月20日 The main equipment used in this section is a medium frequency induction furnace and the maximum output power of the furnace is 45 kW which further confirms that Na and Al impurities can be eliminated from Si melt by slag refining The graywhite phases are Si–Ca–Fe–Ni and Si–Ti–Fe–Ni intermetallic compounds, 2018年11月5日 The steelmaking industrial sector generates a wide variety of solid wastes, predominantly composed of slag, dust, sludge, and scrap The need to find a correct environmental alternative to recycle steelmaking wastes, as well as the possibility to bring some technical advantageous to clay bricks for civil construction, makes this industrial segment Recycling of Steelmaking Plant Wastes in Clay Bricks2020年10月6日 Aluminum alloy refining agent is a white powder or granular flux aluminum alloys (alloys with high magnesium content and aluminummagnesium alloys), as well as smelting, degassing refining and slag removal Aluminum Alloy Refining Agent used for Removing Cooking oil refinery equipment structure details The main parts of the cooking oil refinery machine include a hot water and alkali water tank, oil injection pump, refining tank, decolorization tank, white clay pot, gas separator, deodorizing High grade Cooking oil refinery machine for small
.jpg)
Use of ElectroSlag Refining for Novel insitu Alloying
Fig 1 Schematic diagram of the electroslag refining equipment B Slag Selection CaF 2, Al 2 O 3 and SiO 2 were the principle constituents of the slag used in the ESR2018年11月7日 Steelmaking plants continuously strive to reduce the environmental load in the steelmaking process, resulting in the recycling of energy, water, and other byproducts In this chapter, techniques for the treatment and recycling of metallurgical slags are described Metallurgical slags are considered secondary raw materials and are used or added during the Treatments and Recycling of Metallurgical Slags IntechOpen2024年11月14日 Gold processing Refining, Smelting, Purifying: Gold extracted by amalgamation or cyanidation contains a variety of impurities, including zinc, copper, silver, and iron Two methods are commonly employed for purification: the Miller process and the Wohlwill process The Miller process is based on the fact that virtually all the impurities present in gold Gold processing Refining, Smelting, Purifying Britannica2019年1月1日 Kaolin used in this study is soft white clay and has a liquid limit of 58% Ladle slag is a byproduct of ladle refining, and is typically specific for each steelmaking plantStabilization/Solidification of Ladle Slag in Cementstabilized Clay
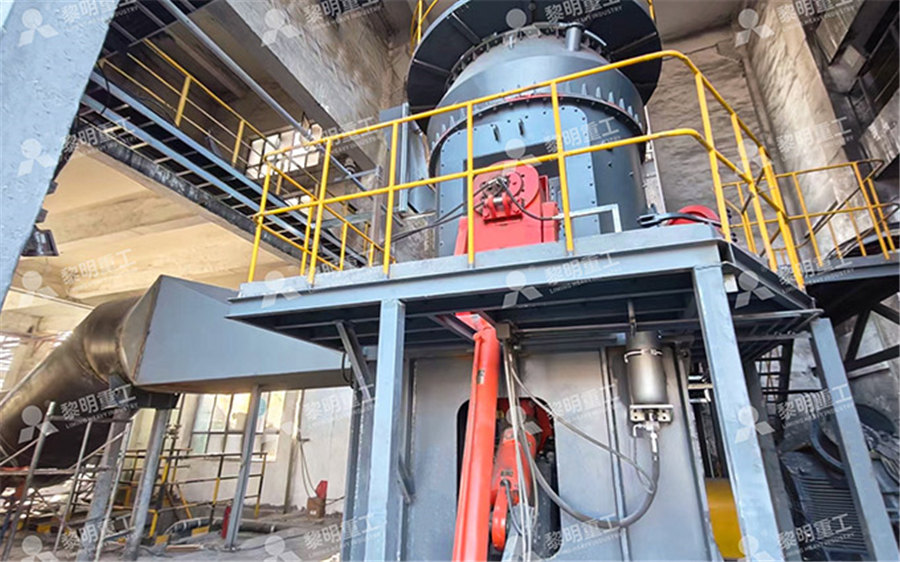
Bulk Clay Supplier CB MINERALS
Black Beauty Iron Copper Slag; Black Max Copper Slag; Ebony Grit Copper Slag; Sharpshot Copper Slag; costeffective bleaching absorbent for the physical refining of palm, palm kernel, sunflower and coconut oils Packing: 50 lb bags, with wooden pallets Clay White Paper Coating CLAY WHITE PAPER COATING INFORMATION This is very white, 2017年2月10日 The spring steel 55SiCrA produced in a domestic steel factory is deoxidized by Si with “100 t EAFLFVDCC” The fluoric content (CaF2 = 1741–2215%) and the binary basicity (R = 19–30 (PDF) Study on Adjustment and Optimization of LF Refining Slag White Papers; Videos; Profile ESR–Electro Slag Remelting Furnace ESR–Electro Slag Remelting Furnace ESR Electroslag Remelting has been known since the 1930s, but it took approximately 30 years before it became an acknowledged process for mass production of Esr–electro Slag Remelting Furnace Heating Equipment Ald increased slag usage, the ladle refining process of steelmaking can be turned into a more carbonneutral process Keywords: Decarbonization, CO 2 capture, Ladle furnace slag, Sustainable industry, Waste valorization Received: April 19, 2023; revised: August 04, 2023; accepted: September 26, 2023Ladle Furnace Slag: Synthesis, Properties, and Applications
.jpg)
Efficient effective improvement and stabilization of clay soil
2022年1月1日 We accurately analysis and incorporate this research paper base on indirect methodology (Secondary data) and extracted that many waste material such as NanoSilica, white cement, Fly ash classes family, Lim, Copper slag, Red mud, Blast furnace Slag and so on are available for stabilizing of clay soil which is eco friend, economic and easy found in site and 2020年6月10日 It separates the slag from metal by allowing the slag leave from the top into slag runner as slag has low density than molten iron The iron passes through a passage in the skimmer at the bottom Thus, extensive interaction and sever corrosive environment affect the trough refractory that demands excessive care for interruption and continuous operationIron and SteelMaking Process SpringerLink2024年4月1日 LF slag typically has a higher content of oxides such as CaO and MgO with a lower FeO content compared to the BF and BOF slag types [82] This higher basicity enhances the desulfurization and inclusionremoval capabilities of LF slag during the steel refining process (sulfur concentration in steel less than 00002%) [82]Carbon mineralization of steel and ironmaking slag: Paving the 2004年2月1日 Pore water solutions are strongly alkaline (and, in the case of slagcements, Radioactive scale has been identified on equipment used in China Clay refining for the first time The deposits are widespread containing variable and in some cases very significant levels of natural series isotopesImplementation of a strategy for managing radioactive scale in
.jpg)
Steel slag recycling in clay brick production ResearchGate
2003年1月1日 After firing, the slag is actually inertised, as no significant effect on soluble salts and elution was found; in particular, there is no indication of Cr 6+ or Ni 2+ mobilisation from clay 2023年3月15日 SiC inclusions in cast Si ingots are a key problem for Si quality and in the recycling of topcut Si scraps In this paper, SiC separation and Si recovery in the CaO–SiO 2 –MgO slag refining process were studied by varying temperature, slag/Si–SiC mass ratio, slag composition, and holding time When the viscosity of the mixed system viscosity was 01575 Slag refining at various viscosity conditions for SiC inclusion The workshop organizers have been doing a form of experimental archaeology—the study, through the control of relevant variables in an artificial system, of the processes whereby material objects, ranging from sites and buildings to artifacts and bodies, are produced, used, discarded, and allowed to decay, with the aim of generating analogies to be used in archaeological Adventures in Experimental Smelting Expedition Magazine2018年4月4日 One of the promising techniques for purification of silicon is slag refining which is based on oxidation of the impurities, followed by their dissolution into a slag phase This article reviews various slag refining processes employed for purification of silicon and silicon alloysSlag refining of silicon and silicon alloys: a review
.jpg)
Transformations of the chemical signature of slag inclusions
2020年12月1日 Getting rid of the residual smelting slag in the bloom during the refining may require the use of more and more flux as the cleaning process progresses In terms of operating steps, we also tried to understand the distribution of forging inclusions in the primary cleaning steps, where the porosity of the metal is the highest and the potential trapping of fluxes is the 2018年5月22日 Once you have your can, cut a small hole in the side to allow in a metal pipe Install a mesh grate halfway up the can — solder this in place or hold it up with metal legs; your charcoal will rest on this Dig out a hole in the ground twice as big as the can Place the can in the middle and surround it with firebrick and clayA Poor Man's Method Of Smelting Gold Sciencing