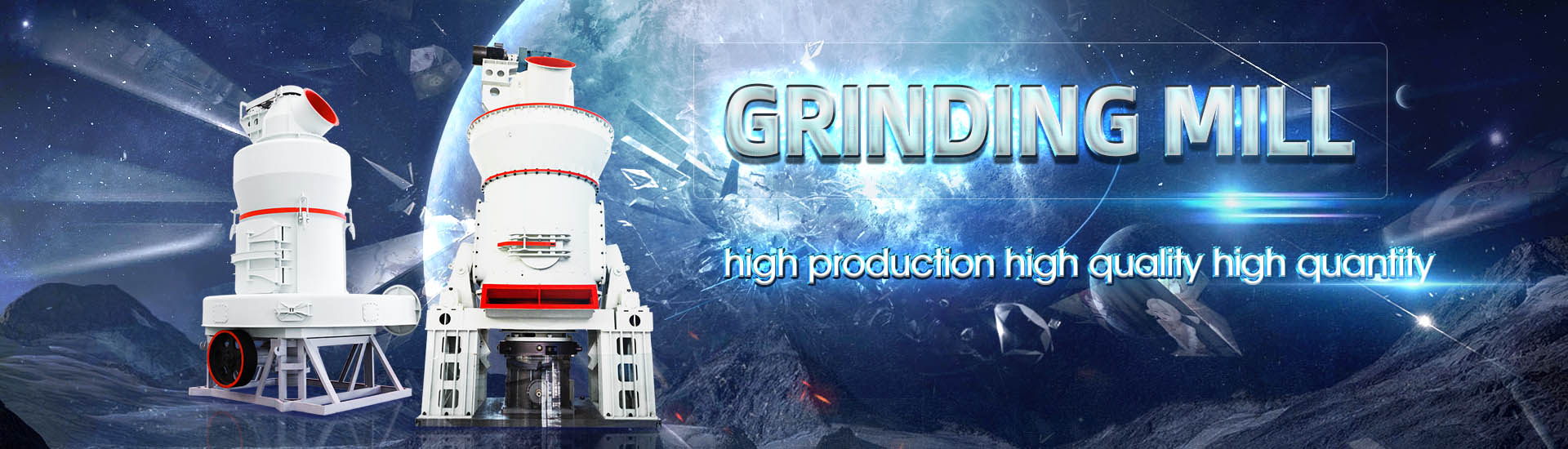
PD ore mill PD mine Stone mill PD ore mill
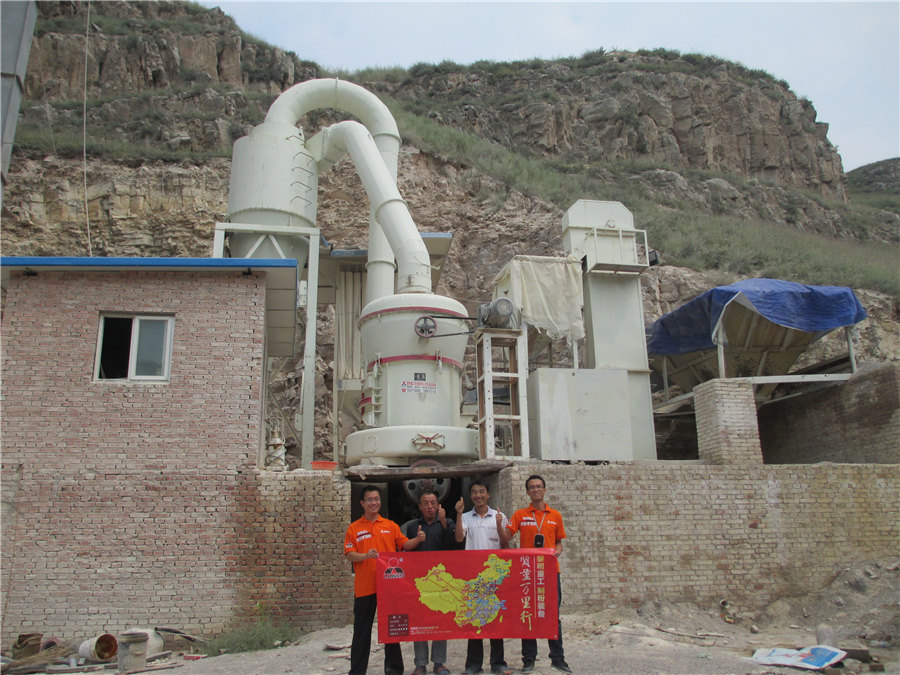
(PDF) Feasibility and necessity of mine to mill ResearchGate
2021年4月19日 Regarding this background, this article describes the feasibility of mine to mill optimization from three aspects: (1) different energy efficiencies between drillingblasting andRegarding this background, this article describes the feasibility of mine to mill 登录Mine to Mill, which links aspects of mining and mineral processing in order to optimise the combined mining and processing stages, has been under development and use for the last 20 UNDErsTaNDINg MINE TO MILL 911 Metallurgist2018年11月21日 Effort and insights from mineralogical and processing characterisation (eg ore hardness) of subore body domains allows sequencing for processing to ensure consistency Dynamic concepts for mine to mill operation and optimisation
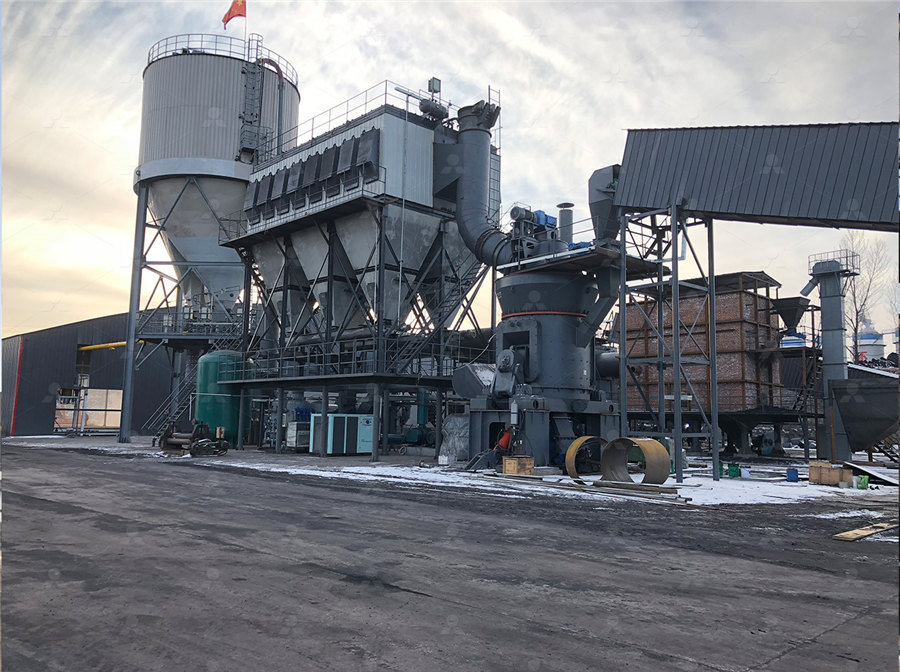
Stillwater Mining Companyapos;s PtPd Flotation Mill
The ratio of pd to Pt in the Stillwater ore and concentrates is about 35 The Stillwater ptpd mine and flotation mill are located about 130 km (80 miles) southwest of Billings in Stillwater county, The use of primary mills in mineral processing plants has expanded very significantly in the last twenty years, and they have been successfully applied to the treatment of a wide variety of Primary Grinding Mills: Selection, Sizing And Current Practices2017年9月1日 The objective of this work is to assess the influence of fine grinding in ball mills and stirred mills on valuable mineral liberation and particle shape characteristics of UG2 ore, a Fine grinding: How mill type affects particle shape characteristics MRC has developed and applied tools to explore ways of improving overall mine to mill process performance One such way is to modify blasting so that a more favourable size distribution isModelling and Simulation Techniques Applied for Optimisation of
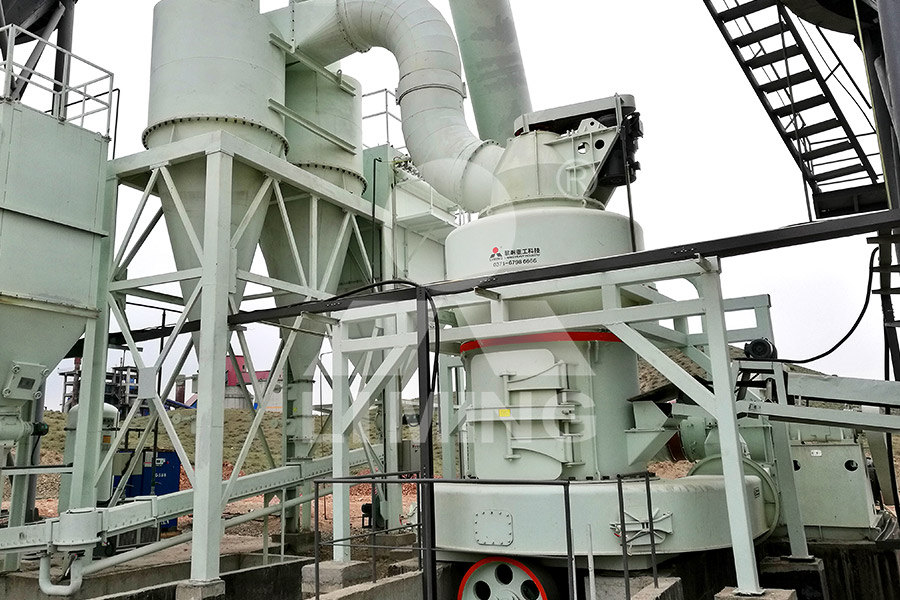
[PDF] Analysis and validation of a runofmine ore grinding mill
2013年4月1日 This brief investigates the feasibility of applying a robust nonlinear model predictive controller to a runofmine ore milling circuit, and the conditions under which such a 2023年6月7日 Semiautogenous mill has flexible loop, is highly adaptable to ore, and can process soft, hard, wet, viscous, dense, or loose ore Compared with conventional grinding Autogenous Mill SpringerLinkThis paper looks at the past, present and not too distant future of grinding mill reliningSince the adoption of autogenous grinding (AG) mills and semiautogenous grinding (SAG) mills as the 14th AusIMM Mill Operators' Conference 2018A Strategy to Minimise Ore Grade Reconciliation Problems Between the Mine and the Mill A Strategy to Minimise Ore Grade Reconciliation Problems Between the Mine and the Mill PDF Normal price $2200 Member price from $000 Add to cart Fees above are GST inclusive PD Hours Approved activity Published: 1997; PDF Size: Mine to Mill Conference, Brisbane, Qld, October 1998
.jpg)
MINE TO MILL OPTMISATION AT PADDINGTON GOLD
MINE TO MILL OPTMISATION AT PADDINGTON GOLD OPERATIONS *SS Kanchibotla1, TG Vizcarra1, SAR Musunuri1, S Tello1, A Hayes2 and T Moylan2 1JKTech Pty Ltd 40 Isles Road At the mill, separation of ore and waste takes place in different stages depending on the2014年10月20日 It is important to note here that the ore that feeds the Vertical Mill has a higher WI than the ore that feeds the ball mill and 10 4 kWh/t for the same P80 fro m the ore of Sequeirinho mineRegrind of metallic ores with vertical mills: An Mine to Mill (MTM) optimisation, a total systems approach to the reduction of energy and cost in mining and mineral processing operations, is wellestablished technology However, successful applications of MTM optimisation have been largely confined to gold, copper and lead/zinc semi autogenous grinding (SAG) operations, where the goals of tweaking the blast design to Can Mine to Mill Optimisation Succeed Under Complex Constraints?2019年9月22日 The scope of the project included insitu ore body characterization, drill and The minetomill studies have shown that 10mm size generated by blasting can be considered a key performance DRILLTOMILL PLANT OPTIMIZATION AT ALTYNALMAS PUSTYNNOYE GOLD MINE
.jpg)
14th AusIMM Mill Operators' Conference 2018
These technologies remove people from the hazardous environment inside the mill and will allow techniques used in modern advanced manufacturing to provide a nearfuture step change in mill relining safety and performanceCITATION:Rubie, P and Russell, J, 2018 21st century relining the path to greater mine site profitability, in Proceedings 14th AusIMM Mill Operators' The Ban Houayxai mine (BHX) is a relatively lowgrade, lowcost, open pit goldsilver deposit in Laos operated by Phu Bia Mining, a subsidiary of PanAust The ore production rate at BHX is 45 Mt/a, with direct tipping to a semiautogenous grinding/ball mill circuit with a carboninleach process plant Approximately 100 000 oz of gold is produced per annumThe operation is Predicting Mill Ore Feed Variability Using Integrated Geotechnical 2006年9月30日 MinetoMill optimization is a total systems approach to the reduction of energy and cost in mining and processing Developed at the Julius Krutschnitt Mineral Research Center in Queensland, Australia, the MinetoMill approach attempts to minimize energy consumption through optimization of all steps in the size reduction process The approach involves MinetoMill Optimization of Aggregate ProductionThe rod mill is another type of grinding mill used in the copper ore mining process This machine uses steel rods as the grinding media instead of balls, which are commonly used in ball mills The rods grind the ore by tumbling within the mill, similar to the action of a rotating drumUnderstanding the SAG Mill in Copper Ore Mining Process
.jpg)
Steadystate and dynamic simulation of a grinding mill using
where the centrifugal acceleration of a particle at the mill shell equals the gravitational acceleration The power draw (P mill) (kW) of the motor turning the mill is an indicator of the kinetic and potential energy imparted to the charge The ground ore in the mill mixes with water to create a slurry The density of the slurry is given by ˆ 10% in minetomill activities • Reduces greenhouse emissions by reducing use of explosives Applications in Our Nation’s Industry The aggregates industry, representing the largest segment of the US mining industry, will benefit the most from minetomill technology, focusing on particle size control rather than particle size reductionITP Mining: MinetoMill Optimization EnergygovBan Houayxai is a goldsilver mine operated by Phu Bia Mining Limited in Laos since 2012 The first two years of operation processed predominately soft oxidised ore but subsequent years were expected to process more fresh hard ore Fragmentation of the fresh primary ores was also expected to be much coarser than for the soft oxide ores This coarser and harder ore is Optimisation of Drill and Blast for Mill Throughput AusIMMThe Porgera Joint Venture and Dyno Nobel have commissioned a joint project to optimise the drill and blast operations to increase the overall profitability of the mine One of the aims of this project is to increase the throughput of semi autogenous (SAG) mills by optimising the blast fragmentation A number of test blasts were conducted during the period May 2000 to January Implementation of Mine to Mill Blast Optimisation at Porgera
.jpg)
Palladium (Pd) Ore Geology, Mineral, Occurrence, Deposits
2023年4月23日 Palladium (Pd) is a chemical element with the atomic number 46 and the symbol Pd on the periodic table It is a rare and lustrous silverywhite transition metal that belongs to the platinum group metals (PGMs), which also includes platinum (Pt), rhodium (Rh), ruthenium (Ru), iridium (Ir), and osmium (Os) Palladium was discovered in 1803 by William Hyde Wollaston, There are numerous examples in the literature, some of which are quantifying the effect of Mine to Mill Grundstrom et al, 2001;Hart et al, 2001; Scott et al, 2002; Burger et al, 2006;Jankovic et Tracking and Quantifying Value from ‘Mine to Mill’ Improvement3 Comminution Characterisation Rock breakage characteristics are determined by using a dropweight device This is used to break rocks in a range of sizes under a range ofModelling and Simulation Techniques Applied for Optimisation of Mine Find your ore mill easily amongst the 42 products from the leading brands (Fritsch GmbH, Retsch, Eriez, ) on DirectIndustry, the industry specialist for your professional purchases horizontal for limestone stone ball grinding mill Ф2200×7500 Final grain size: 74 µm 400 µmOre mill, Ore grinding mill All industrial manufacturers
.jpg)
CavetoMill: A MinetoMill approach for block cave mines
2015年3月1日 For example, concepts such as "minetomill" and the more recent "cavetomill" have highlighted the importance of optimizing Net Present Value (NPV) from ore extraction through to the processing 2015年6月19日 The basic parameters used in ball mill design (power calculations), rod mill or any tumbling mill sizing are; material to be ground, characteristics, Bond Work Index, bulk density, specific density, desired mill tonnage capacity DTPH, operating % solids or pulp density, feed size as F80 and maximum ‘chunk size’, product size as P80 and maximum and finally the type of Ball Mill Design/Power Calculation 911Metallurgist2005年9月19日 In 2003 the Sishen Iron Ore Mine in South Africa management systems into one centralised system that can be used to compare and reconcile the tonnes and grades from the mine through to the millIron Ore Mine Reconciliation—A Case Study From Sishen Iron Ore Mine 2017年7月26日 Soft ore Work Index 13 = 100,000/90,000 = 11 kwh/t Hard ore Work Index 16 = 100,000/65,000 = 154 kwh/t For the purposes of this example, we will hypothesize that the the crushing index of the hard ore with the increased energy input of 154 kw/t reduces the ball mill feed size to 6,500 micrometersHow Ball Mill Ore Feed Size Affects Tonnage Capacity
.jpg)
(PDF) Data mining for minemill ore grade reconciliation at
Data mining for minemill ore grade reconciliation at Erdenet Mining Corporation Narmandakh Sarantsatsral 2016 See full PDF download Download PDF Related papers Application of data mining in Iran's Artisanal and SmallScale mines challenges analysis Ali Nouri Qarahasanlou Resources Policy, 20212022年6月17日 Next, 4 00 g of ore and 2 0 0 m L of wa ter were p u t into a Φ 20 0 mm × 24 0 mm bal l mill in the l a bora t o ry The spe e d of the ba ll mill w a s 1 1 0 r/min and the volume w a s 7 5 LDifferences in Properties between Pebbles and Raw This paper discusses the progress of the Deep Mill Level Zone (DMLZ) mine from the prefeasibility study completed in 2005, through commencement of development access in 2008, completion of the feasibility in 2010 and cave initiation in late 2015 This fourth lift of caving in the East Ertsberg Skarn System (EESS) is located 500 m below the currently producing Deep Ore Deep Mill Level Zone from Feasibility to Production AusIMMThe capacity is about 100 tons of ore a day The quartz mill at the Vulture is a modern twenty stamp mill, each stamp weighing over a ton At this time, the stamps are the heaviest in use in the country The ore is taken from the mine and crushed to a suitable size in an AllisChalmers gyratory crusher, carried to the storage bin in an ore carWinning the Metal: Ore Mills of the West Western Mining History
.jpg)
Ø Effect of SAG Mill Feed Size Distribution and Ore Variability
CADIA HILL SAG MILL CIRCUIT S Hart (1), W Valery (2), B Clements (1), M Reed (1), M Song (3) and R Dunne (4) (1) Newcrest Mining Ltd Cadia Hill Gold Mine (2) Julius Kruttchnitt Mineral Research Centre (3) Ø Effect of SAG Mill Feed Size Distribution and Ore Variability Ø Mill liner design modifications, and2015年8月24日 The Anglo American phosphate mine is located in the Brazilian state of Goi#225;s and possesses one of Brazil’s most important phosphate rock deposits, with the site being the country’s second largest producer of phosphate rock concentrate Despite the site having been in operation since 1979, the mining team only started using explosives in 2004 OneMine Fragmentation Optimisation – Adopting Mine to Mill Gold ore chain mill, complete with a sluice box and 12 Volt water pump Processes 30mm size nuggets or gravel at 120kg per hour + d Ore Chain Mill Full Package Alluvial Pumps2001年1月1日 Mine monitoring and reconciliation must take a multidisciplinary approach across geology, mining engineering, operations, survey and metallurgy to deliver benefits throughout the mining value A strategy to minimise ore grade reconciliation problems between the
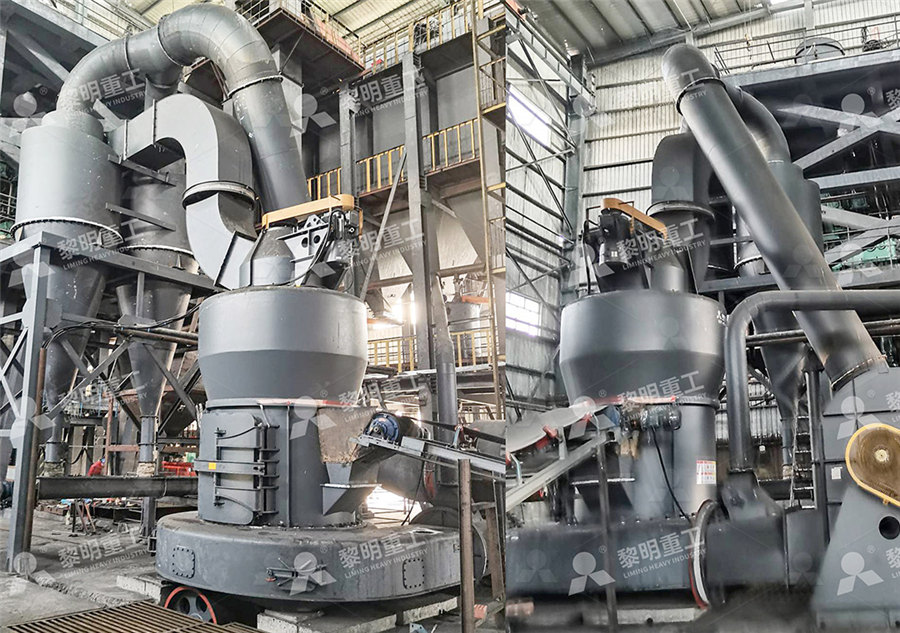
Analysis and validation of a runofmine ore grinding mill circuit
2013年4月1日 Two types of mills commonly found in the minerals processing industry are ball and semiautogenous (SAG) mills, which use both ore and steel balls as grinding media (Wei and Craig, 2009b)In the case of a ball mill the ore is crushed before it enters the mill, whereas a SAG mill receives runofmine (ROM) ore directly (Stanley, 1987)A SAG mill in a singlestage 2022年5月23日 Modeling and application of stirred mill for the coarse grinding of PGE bearing chromite ore May 2022; Separation Science and Technology 58(1) 07 ppm Pd, 015 ppm Ru, 012 (PDF) Modeling and application of stirred mill for the coarse The Mine to Mill Conference organised by The AusIMM in October 1998 documented a number of case studies where run of mine ore was not presented to the mill in the best possible form for subsequent stages of comminution and processing PD Hours Approved activity Published: 1999; PDF Size: 0318 Mb Unique ID: P; Share:Ore Characterisation for Mine to Mill Fragmentation AusIMMGuidelines and practical applications for continuous improvement in mine to mill reconciliation, in Proceedings 11th AusIMM Mill Operators' Conference, pp 309316 (The Australasian Institute of Mining and Metallurgy: Melbourne)11th AusIMM Mill Operators' Conference 2012
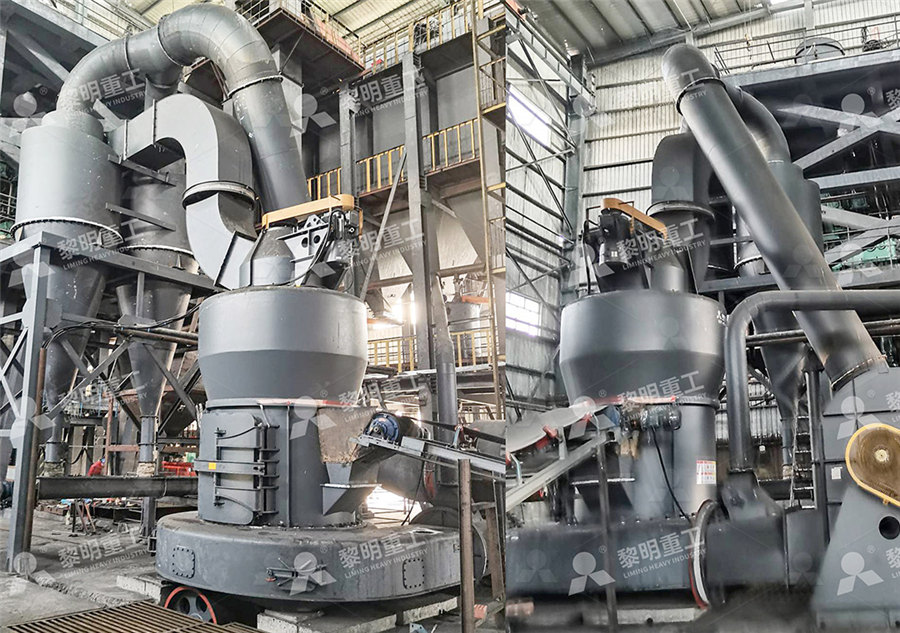
Rod Mill SpringerLink
2023年5月3日 Center Periphery Discharging Rod Mill The center periphery discharging rod mill feeds the material through the journals at both ends of the mill, and discharges the grinding products through the circular orifice in the middle of the cylinder (Fig 3)Ore pulp is characterized by short stroke, steep slope, and it can be coarsely ground with fewer fine particles and low quantify and manage the ‘value’provided by ‘Mine to Mill’improvement generated by the intense blasting of ore INTRODUCTION Cost versus value from blasting In everyday language, ‘value’ is a very personal assessment of the worth of something In business it is a description of monetary or material worth The value of ore in the Tracking and Quantifying Value from ‘Mine to Mill’Improvementpenti nized ore are presented Best results in the pilot mill were obtained with a sodium isobutyl xanthatenormal dodecyl mercaptan col lector combination at a natural pH of 82 A rougher concentrate con taining 17 oz/ton Pt and 47 oz/ton Pd was prepared Recoveries ofPilot Mill Flotation of Serpentinized PlatinumPalladium Ore Mine to Mill Conference, Brisbane, Qld, October 1998 Home; PD Hours Approved activity Published: 1998; PDF Size: Mine reconciliation is the practice of comparing the tonnage and grade of material processed by the mill with the tonnage and grade of The Myth of Mine Reconciliation AusIMM
.jpg)
[PDF] Analysis and validation of a runofmine ore grinding mill
2013年4月1日 DOI: 101016/JMINENG201210009 Corpus ID: ; Analysis and validation of a runofmine ore grinding mill circuit model for process control @article{Roux2013AnalysisAV, title={Analysis and validation of a runofmine ore grinding mill circuit model for process control}, author={Johan D le Roux and Ian Keith Craig and D G function is that it is independent of ore type and fails to capture ore property Discharge rate 7KH GLVFKDUJH UDWH IXQFWLRQ HVVHQWLDOO\ describes the transport of material out of the mill For grate discharge mills, this function is expressed in terms of a clasVL¿FDWLRQ IXQFWLRQ OXPSHG WRJHWKHU ZLWK D PD[LPXP GLVFKDUJH rate constantDynamic modeling and simulation of a SAG mill for mill charge As shown in this paper, reliable ore tracking systems will allow much more effective minemill reconciliations as well as the ability to model process holdups with regard to size by residence time distributionsx000D This should, in turn, allow metallurgists to have a better understanding of the size and grade of material that will report to the plant at different process holdup (eg TracerBased MineMill Ore Tracking Via Process Holdups at