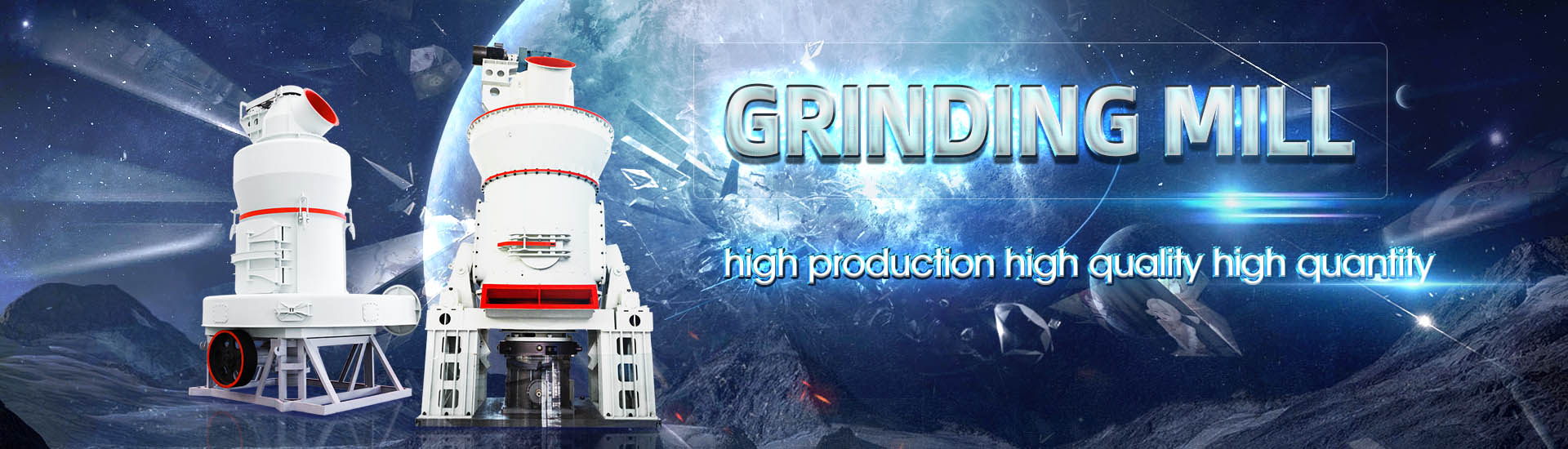
Chemical raw material mill model and technical parameters
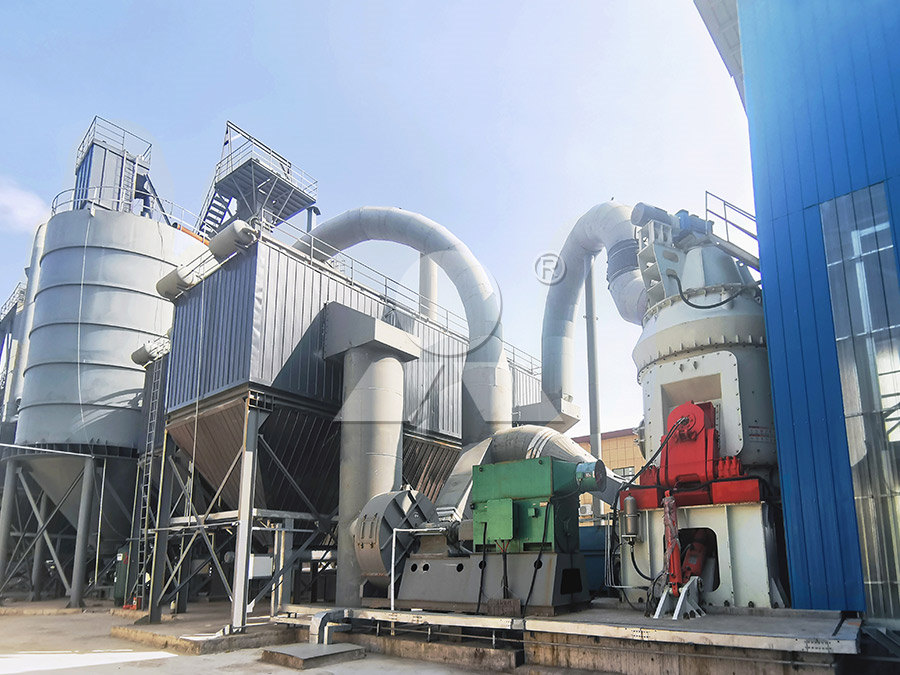
Modeling of Raw Material Mixing Process in Raw Meal Grinding
Abstract: The objective of the present study is to build a reliable model of the dynamics among the chemical modules in the outlet of raw meal grinding systems and the proportion of the raw 2019年8月1日 Introduction of mill, material and formulation parameters to stress model Prediction of optimum operation conditions, grinding times or specific energies Model is Mill, material, and process parameters – A mechanistic model for 2010年10月1日 The objective of the present study is to build a reliable model of the dynamics among the chemical modules in the outlet of raw meal grinding systems and the proportion of the raw(PDF) Modeling of Raw Material Mixing Process in Raw 2012年6月1日 The paper presents an overview of the current methodology and practice in modeling and control of the grinding process in industrial ball mills Basic kinetic and energy Grinding in Ball Mills: Modeling and Process Control ResearchGate
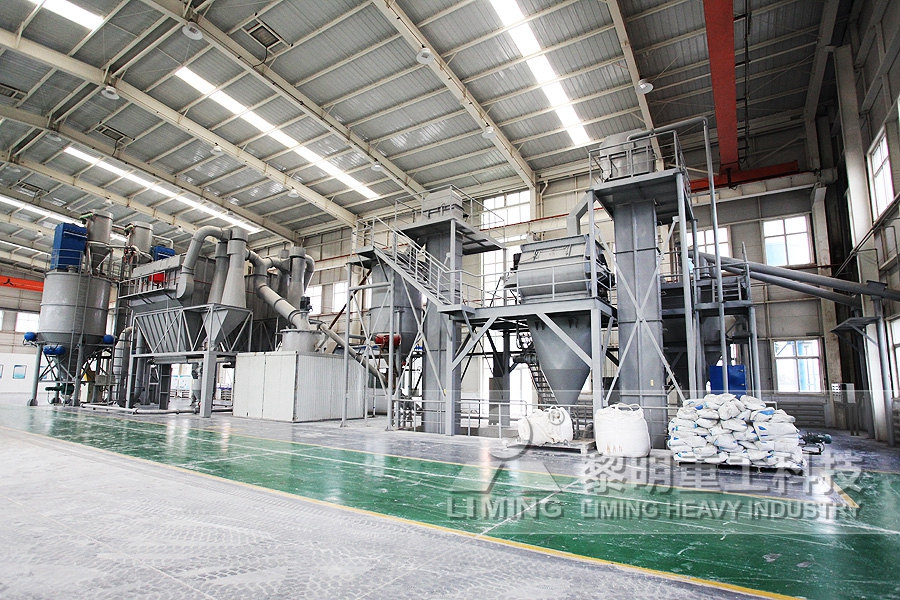
Mill, material, and process parameters – A mechanistic model for
2019年8月1日 Introduction of mill, material and formulation parameters to stress model Prediction of optimum operation conditions, grinding times or specific energies Model is 2010年7月1日 The objective of the present study is to build a reliable model of the dynamics between the chemical modules in the outlet of raw meal grinding systems and the proportion of the rawModeling of Raw Materials Blending in Raw Meal Grinding in ball mills is an important technological process applied to reduce the size of particles which may have different nature and a wide diversity of physical, mechanical and chemical Grinding in Ball Mills: Modeling and Process Control Sciendo2010年10月1日 The objective of the present study is to build a reliable model of the dynamics among the chemical modules in the outlet of raw meal grinding systems and the proportion of [PDF] Modeling of raw material mixing process in raw meal
.jpg)
A novel chemical composition estimation model for cement raw
Abstract: Raw material blending process is an essential part of the cement production process The main purpose of the process is to guarantee a certain oxide composition for the raw meal Abstract: The objective of the present study is to build a reliable model of the dynamics between the chemical modules in the outlet of raw meal grinding systems and the proportion of the raw Modeling of Raw Materials Blending in Raw Meal Grinding Systems2012年6月1日 As the cylinder starts to rotate, the grinding balls inside the cylinder crush and grind the feed material, generating mechanical energy that aids in breaking bonds, activating the catalyst, and Grinding in Ball Mills: Modeling and Process Control2010年10月1日 The objective of the present study is to build a reliable model of the dynamics among the chemical modules in the outlet of raw meal grinding systems and the proportion of the raw materials(PDF) Modeling of Raw Material Mixing Process in
.jpg)
Effect of Ball Mill Parameters’ Variation on the Particles of a
2021年10月21日 The economic and technical values of the hydrometallurgical or leaching processing are a function of its reaction rates and these reaction rates are enhanced by mechanical activation (MA) in hydrometallurgical processing This study presents a novel derived theoretical model for MAassisted leaching in investigating the effects of ball mill parameters 2020年11月22日 materials, end pr oduct, high concentration of chemicals such as sodium carbonate, sodium sulphide, bisulfi t es elemental chlorine dioxide, calcium oxide, hydrochloric acid, etc [29](PDF) Characteristics and Treatment of Pulp and Paper Mill 2014年11月1日 A series of multivariable models composed from linear differential equations, integrals, and delays has been developed to describe the dynamics of mixing of the raw materials during the cement raw Modelling and simulation of raw material blending process in cement raw 2022年4月12日 Through correlation analysis, the chemical composition of the sintered raw material was determined as the input parameter and the physical and metallurgical properties of the sintered ore were (PDF) A Model Study on Raw Material Chemical Composition to
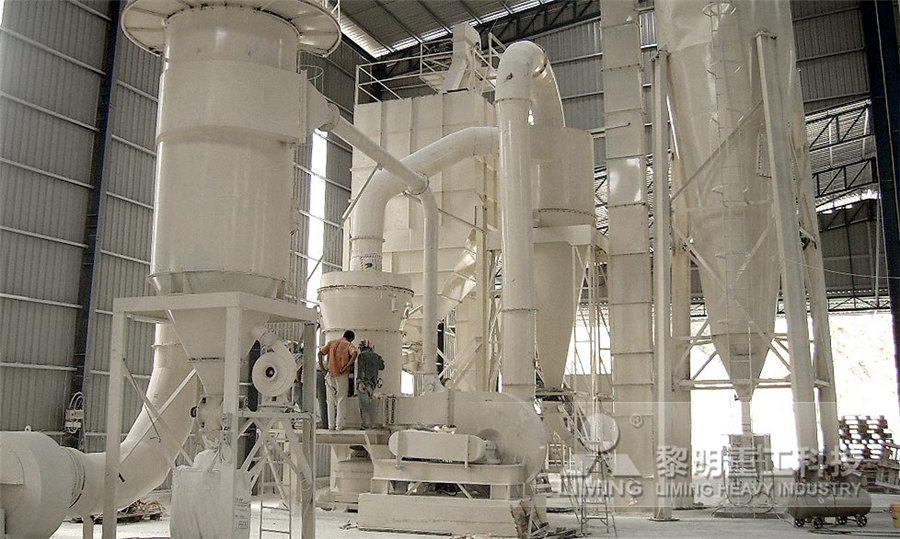
Toxicity Removal of Pulp and Paper Mill Effluent by Employing Chemicals
Feb 2017 62 IRAInternational Journal of Applied Sciences ISSN 24554499; Vol06, Issue 02 (2017) Institute of Research Advances Pg no 6269Raw mill has features of various materials application, continuous running, secondary grinding is unnecessary for largescale and medium vertical mill 4 Stable chemical composition and even particle size products 5 ZKRM Specification and technical parameter of raw meal vertical mill: Model: Capacity (t/h) Geometric diameter of Henan Zhengzhou Mining MachinerySince raw material performance data beyond their sheer number are coming from a number of value chain functions, eg procurement, raw mate rial experts, production, product management, sales and finance, it is clear that raw material portfolio management, too, has to be a crossdiscipline approach, often orchestrated by raw material experts A Raw Material Excellence in the chemical industry, a game 2020年2月24日 Raw Material Particle Size and Surface Characteristics Liquid Phase Estimating Liquid Phase Values Heat of Chemical Reaction Insoluble Binders Liquid phase control Acid/ammonia neutralization methods in the granulator Direct neutralization in granulator Preparing the Production Formula A discussion of the key physical and chemical parameters Physical and chemical parameters for the granulation of
.jpg)
Modeling and Simulation study on Cement Raw Mill Process
In this control system, the chemical composition in the raw mill is measured in realtime and analyzed comprehensively Process Model Process parameters that indicate the quality of raw meal consist of LSF, SR, and AR M = Total mass in Raw Mill x = Raw material fraction rate (%) S = SiO 2 (%) A = Al 2 O 3 (%) F = Fe 2 O 3 (%)study, the second production line was surveyed The cement raw materials (lime, silica and iron ore) enter the circuit through two apron feeders The raw materials are crushed in a hammer crusher to D 95 of 80mm The raw materials are mixed in a certain proportion and fed into a vertical roller mill (LOESCHE mill)Modeling and simulation of vertical roller mill using population 2017年3月29日 A kraft pulp mill can be divided into four main parts: (1) raw material handling; (2) pulping line with an almost closed chemical and energy recovery system; (3) bleaching with an openPulp Mill Wastewater: Characteristics and 2019年8月1日 In this study, the stress model developed by Kwade was improved by introducing parameters corresponding to the mill and the material in addition to the process parameters Using this model, the optimum operating conditions for stirred media milling processes can be determined with a reduced amount of experimental work, even for geometrically unequal millsMill, material, and process parameters – A mechanistic model
.jpg)
Raw mix composition (% by weight) and chemical parameters
The raw materials were homogenized in a QUIMIS horizontal rotary mill (Model Q298) For the clinker production process, the methodology proposed by the Brazilian Portland Cement Association (ABCP The dynamics between the main oxides and chemical modules of raw mix in mill outlet and the materials proportions in mill entrance is investigated The distributions of model parameters (gains, time constants, delays (LSF) Thus, the effect of the raw materials compositions and their uncertainty on LSF dynamics is studied The Modelling and simulation of raw material blending process in cement raw Request PDF On Sep 1, 2016, Deniz Altun and others published Operational parameters affecting the vertical roller mill performance Find, read and cite all the research you need on ResearchGateOperational parameters affecting the vertical roller mill 2024年3月15日 In this study, factors influencing the smelting parameters of electrical arc furnace were studied by using a material balance and energy balance model The smelResearch on technical parameters of electrical arc furnace

A Survey and Analysis on Electricity Consumption of Raw Material Mill
2021年1月22日 Based on the statistics of the electricity consumption of the raw material mill system of 1005 production lines in China between 2014 and 2019, it is found that the average electricity consumption 2015年4月17日 Vertical Mill for raw grinding is a type of industrial equipment used to crush or grind materials into small particles Vertical roller mills are widely used in the concrete and mining fields, and are also used to process gypsum These units can process both raw and recycled materials, while helping to reduce waste and preserve virgin supplies of these materialsGreatWall Vertical Mill for raw grindingKey words: Raw material blending process, Chemical component estimation, Modulus prediction, System identification 摘要: Raw material blending process is an essential part of the cement production processThe main purpose of the process is to guarantee a certain oxide composition for the raw meal at the outlet of the mill by regulating the four raw materialsA novel chemical composition estimation model for cement raw material Vertical raw mill is one kind of raw mill, generally used to grind bulk, granular, and powder raw materials into required cement raw meal in the cement manufacturing plantVertical raw mill is an ideal grinding mill that crushing, drying, grinding, Vertical raw mill Cement Plant
.jpg)
A novel chemical composition estimation model for cement raw material
2019年11月1日 Raw material blending process is an essential part of the cement production process The main purpose of the process is to guarantee a certain oxide composition for the raw meal at the outlet of the mill by regulating the four raw materials But the chemical compositions of raw materials vary from time to time, resulting in difficulties to control the oxide compositions to The raw material mill consists of feeding part, discharging part, refractory material plants, chemical industry, electric power, etc Model: Φ15×57 m Capacity: 45–6 t/h Power: 130 kW Model: Φ3×9 m Capacity: 55–60 t/h Power: 1000 kW Parameter Product specification (m) Milling form: Transmission form: Gear box: Motor powerRaw Material Mill with Excellent Performance Fote Machinery2020年9月3日 For economic reasons, increasing the use of various fibrous pulps with high lignin contentsie, chemothermomechanical pulp (BCTMP and CTMP), thermomechanical pulp (TMP), and semichemical pulpis Analysis of Cellulose Pulp Characteristics and Processing Parameters 2022年4月12日 When constructing the model, it is constructed based on the principle of conservation of materials, and the content of the chemical composition of the raw material of the finished sinter can be determined according to the raw material parameters and the batching parameters, as shown in the following formula:A Model Study on Raw Material Chemical Composition to
.jpg)
Palm oil mill effluent: A waste or a raw material? ResearchGate
2012年1月1日 Palm oil mill effluent (POME) is a good source of raw material for bioconversion through biotechnological processes given it high concentration of carbohydrate, protein, nitrogenous compounds 关键词: Raw material blending process, Chemical component estimation, Modulus prediction, System identification Abstract: Raw material blending process is an essential part of the cement production processThe main purpose of the process is to guarantee a certain oxide composition for the raw meal at the outlet of the mill by regulating the four raw materialsA novel chemical composition estimation model for cement raw material 2016年8月12日 This paper focuses on modelling and solving the ingredient ratio optimization problem in cement raw material blending process A general nonlinear timevarying (GNLTV) model is established for (PDF) Mathematical modeling of a cement rawmaterialAt the same time, the plant has a strict quality limitation interval when selecting raw materials, and the quality of raw materials does change in actual production, but the fluctuation is small; moreover, since the quality of some raw materials can not be accurately accessed in real time, it is proposed to determine the selection of 4 raw material parameters, 13 state parameters and Collaborative Optimization Model of Blast Furnace Raw Materials
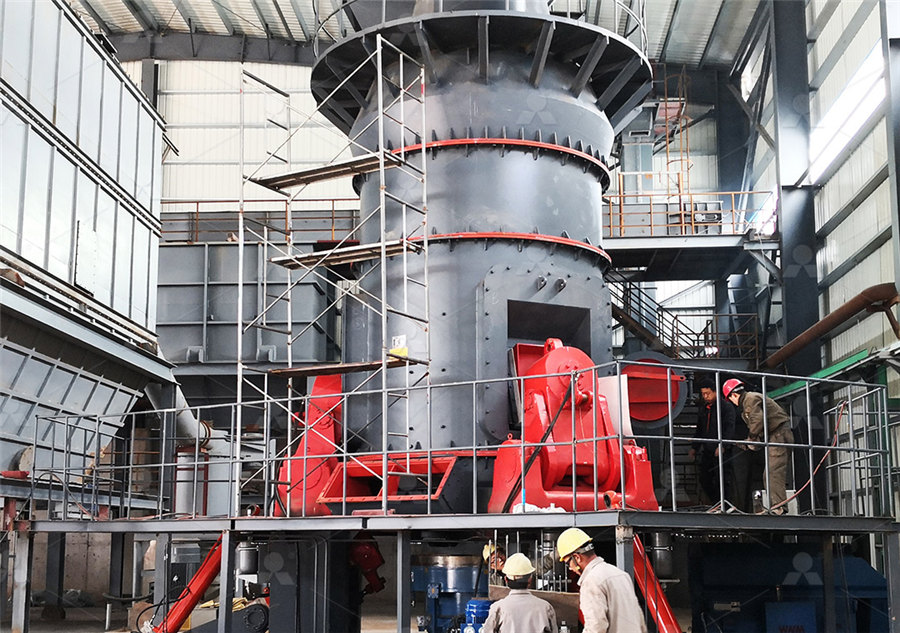
PFD of physicochemical treatment of paper mill effluent (raw material
Download scientific diagram PFD of physicochemical treatment of paper mill effluent (raw material: imported pulp/recycled paper) from publication: Wastewater treatment options for paper mills Raw materials will be ground via the force of cutting, impact, innumerable high speed vortex and high frequency vibratory Technical parameters of horizontal Turbo Mill MODEL 300 500 750 1000 1250 ;Turbo Mill EPIC Powder MachineryA twostage submerged anaerobic membrane bioreactor (2sAnMBR) was operated to demonstrate the technology concept and to accelerate anaerobic biodegradation of Palm Oil Mill Effluent (POME)Chemical composition of palm oil mill effluent (POME)The Tunisian clinkers investigated as part of this study contain four main phases: alite (C3S), belite (C2S), tricalcium, aluminate (C3A) and ferrite (C4AF)(PDF) Influence of raw material's parameters on the clinker's
.jpg)
Modeling and Parameter Identification of Coal Mill
2009年9月20日 A control oriented model was then developed by Fan (1994) and Fan and Rees (1994) In 2009, coal flow and outlet temperature of mill were modelled using mass and heat balance equations for startup 2023年12月29日 Ball mill is a commonly used grinding equipment, widely used in mining, metallurgy, building materials, chemical industry and other industries 3245 ball mill is a common model of ball mill, and Technical parameters of 3245 ball mill LinkedIn2018年9月10日 The simulator was used for the thermodynamic performance of a raw mill (RM) and raw materials preparation unit in a cement plant in Nigeria using actual operating data The raw mill has a capacity (PDF) Thermodynamic Analysis of Raw Mill in Cement2006年12月1日 The raw materials are ground and mixed together in controlled proportions to form a homogeneous blend, termed as a raw meal or rawmix, with the required chemical compositionEnergy and exergy analyses of a raw mill in a cement production
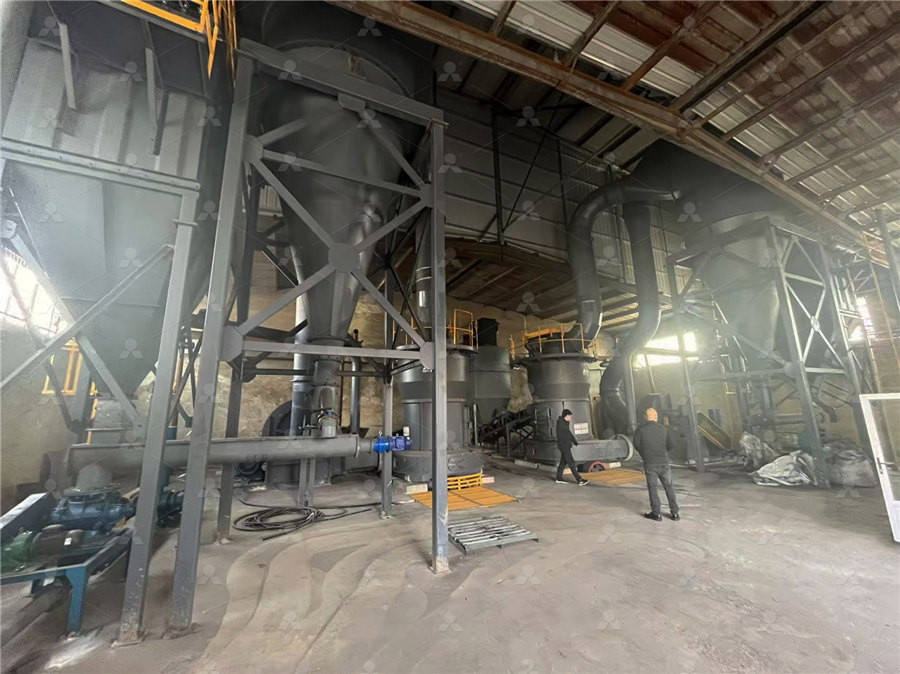
Raw material identification and verification simplified Chemical
Raw material identification and verification (RMID) is a complicated process for a very important reason: it confirms the quality of the raw materials used in the manufacture of products that you put on and in your body The complexity of RMID spans the spectrum from analytical techniques and instruments to the testing process, then to []2023年6月1日 Pulp and paper mills produce approximately 50 to 70 million tonnes (MT) of lignin every year, and this number is expected to grow by 225 million tonnes by 2030, according to the Environmental Protection Agency (EPA) (Bajwa et al, 2019)For decades, scientists and researchers have tried to remove lignin from wood to extract an enriched cellulose fraction, Transforming lignin into renewable fuels, chemicals, and materials