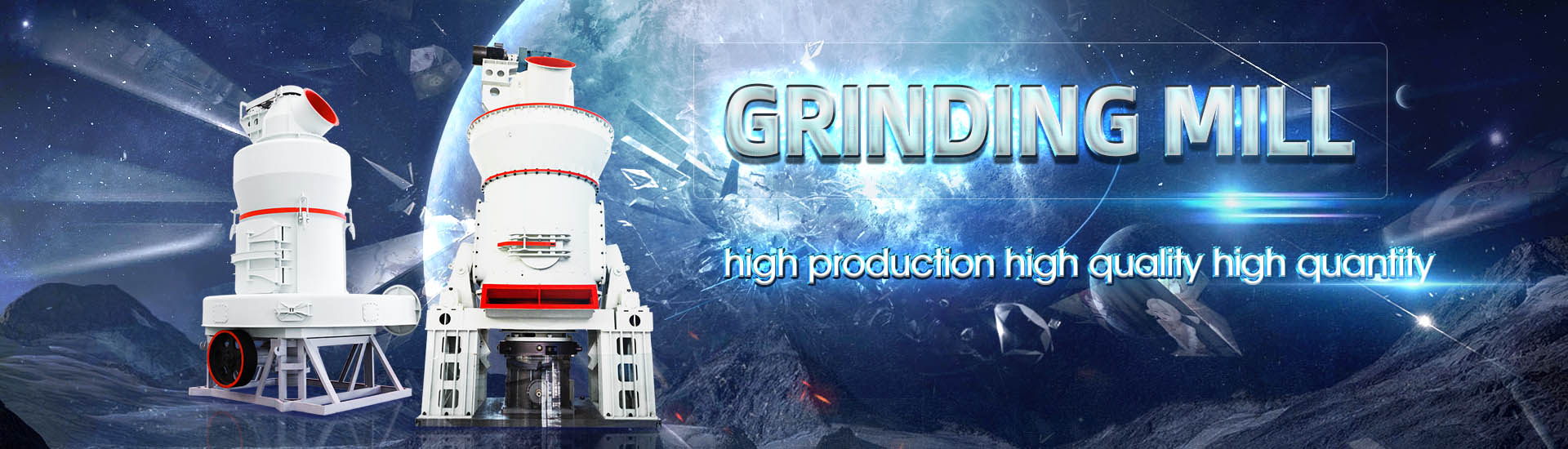
SIC micro powder overflow classification optimization process and
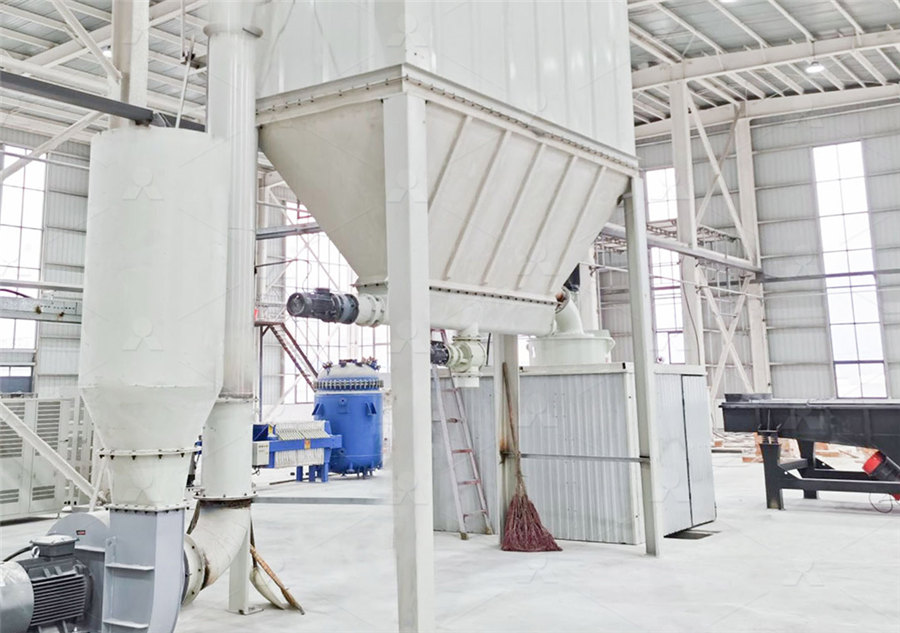
Full Length ArticleTipbased nanomanufacturing process of single
2020年1月15日 Tipbased nanomanufacturing (TBN) process has proven to be a promising technique for fabrication of nanostructures on single crystal SiC This study investigates the deformation and removal mechanism of SiC under different scratching directions in TBN SiC powder source material is sublimed at elevated temperatures above 2000 C and crystallizes at a slightly colder seed For a review on the SiC bulk growth process, refer to [1] The proper Optimization of the SiC Powder Source Material for Improved 2024年6月1日 A systematic and comprehensive investigation was conducted on the impact of process parameters on the surface roughness, macro texture, and micro morphology of single Mechanism analysis and process optimization of nanogrinding 2023年11月29日 This work explored the best combination of processing parameters for pressure sintering of microsilver joints between SiC and DBC that produces promising joints Pressure Sintering of MicroSilver Joints in SiC Power Devices
.jpg)
Microgrooves machining and optimizing on SiC/SiC composites
2024年1月1日 The effects of singlefactor parameters and multifactor interactions on groove width, groove depth, volume material removal rate, and surface roughness were analyzed 2019年10月1日 By adapting the size distribution of the SiC source material, the study of the influence of different SiC powder size distributions and the sublimation behavior during Optimization of the SiC Powder Source Material for Improved This study aims to utilize silicon carbide (SiC) powder and phenolformaldehyde resin (PF) as the primary raw materials to prepare phenolformaldehyde coated silicon carbide composite Study on process and parameter optimization of selective laser 2019年10月8日 We have studied the influence of different SiC powder size distributions and the sublimation behavior during physical vapor transport growth of SiC in a 75 mm and 100 mm Optimization of the SiC Powder Source Material for Improved
.jpg)
Advance understanding of the synthesis process, special
2024年3月1日 In this paper, we present a comprehensive summary of the synthesis technology, distinctive properties, and potential applications of SiC NWs and the composite constructed 2021年11月12日 In this study, we aim to find a simple and lowcost purification process, and provide a theoretical basis for the mass production of high purity powders βSiC powders Purification of β SiC powders by heat treatment in vacuum2023年3月4日 Kamble KS et al [21] studied EDM process parameters considering Inconel 925 material, he thus, concluded the output by the one of the most commonly used optimization techniques, Taguchi method He chose Inconel considering its wide variety of applications in aerospace engineering S Abulais [22] conducted a detailed review of the EDM process and A review of electrical discharge machining (EDM) and its optimization 2016年1月13日 Request PDF Multiobjective optimization of process parameters involved in microfinishing of Al/SiC MMCs by abrasive flow machining process It is hard to finish small slots in composite Multiobjective optimization of process parameters involved in micro

Tipbased nanomanufacturing process of single crystal SiC:
2020年1月15日 TBN processing technology can realize micronano structures of different dimensions on the surface of materials, such as microgrooves [9], [10], ripples [11], [12], surface grating structures [13], and threedimensional micronano structures [14]As the most common application field, surface microgroove processing has attracted much attention, including the 2016年9月18日 The present experimental study deals with the machining of AlSiC p metal matrix composite (MMC) (with 20 % SiC reinforcement) by using a brass tool electrode using electric discharge machining (EDM) process The aim of the research work is to analyze the effect of process parameters namely input current (I p), pulse on time (T on), duty cycle (DC) and Multiobjective Optimization of EDM Process Parameters Using 2020年6月3日 Abstract Powder injection molding (PIM) is a wellknown manufacturing technique for the production of complex, netshaped macroparts using a broad range of materials and alloys Eventually, the PIM method has been modified into micropowder injection molding (μPIM) because of the increasing demand of microparts in global market Nowadays PIM and μPIM Process Parameters Used in Macro/Micro Powder Injection Molding2024年3月19日 A silicon carbide/yttrium aluminum garnet (SiC/YAG) composite powder feedstock material developed and patented by NTNU (Norway) in 2012 has been used to produce industrial SiC thermal spray coatings since 2014 This powder is the first of its kind in the thermal spray industry The commercial powder is produced by the agglomerated and sintered route SiCYAG Coating Microstructure Optimization Through Powder
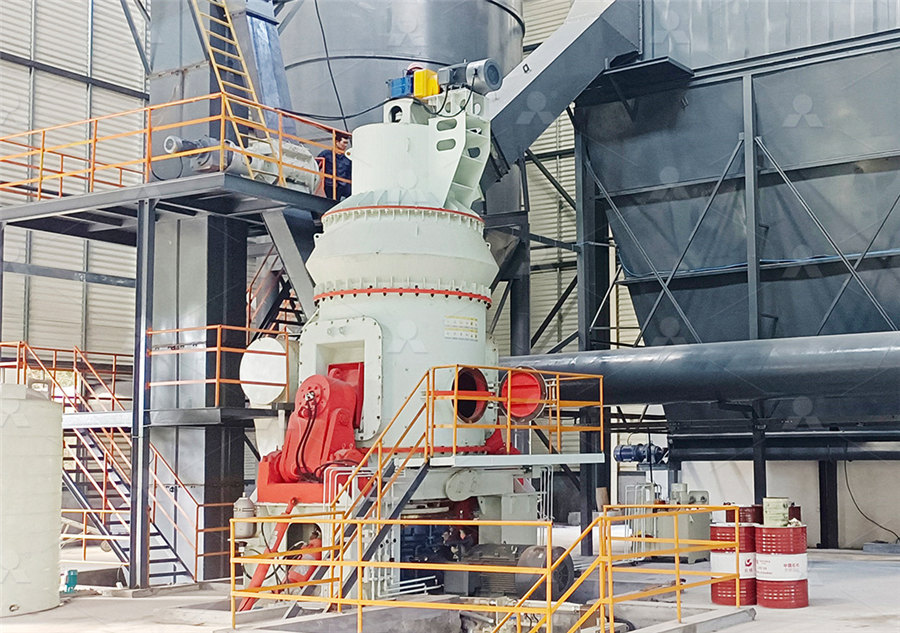
Process Optimization of SiCReinforced Aluminum Matrix MDPI
2024年3月4日 Process parameters and powder spreading quality are important factors for aluminum matrix composites (AMCs) prepared using laser powder bed fusion (LPBF) In this study, a Box–Behnken Design (BBD) was used to optimize the process parameters, and nearspherical βSiC was selected to improve the quality of powder spreading The rationality of 2023年7月1日 Due to the exceptional mechanical qualities of particles, including their high strength, high elastic modulus, and good electrical and thermal conductivity, they are one of the most promising reinforcements for MMCs [[1], [2], [3]]The related particulate matters are listed as carbon nanotubes (CNTs) [4], silicon carbide (SiC) [5], zirconium oxide (ZrO 2) [6], aluminium Systematic study of preparation technology, microstructure 2023年12月26日 Request PDF Thermal Modeling and Parametric Optimization for Machining of Aluminum (Al10%SiC micro SiC nano )Based Hybrid Composite Using Spark Erosion In this study, the authors divided Thermal Modeling and Parametric Optimization for2022年7月26日 In the present work, optimization of powder metallurgy process parameters, ie, compaction pressure, sintering time, and sintering temperature, for magnesium alloy AZ91 is done using Taguchi Optimization of powder metallurgy process parameters to
.jpg)
Modelling and Characterization of Basalt/Vinyl Ester/SiC Micro
2024年2月27日 Basalt fiber reinforcement in polymer matrix composites is becoming more and more popular because of its environmental friendliness and mechanical qualities that are comparable to those of synthetic fibers Basalt fiber strengthened vinyl ester matrix polymeric composite with filler addition of nano and microsized silicon carbide (SiC) element spanning DOI: 101080/2015 Corpus ID: ; Experimental Investigation and Optimization of Process Parameters of Al/SiC MMCs Finished by Abrasive Flow Machining @article{Sushil2015ExperimentalIA, title={Experimental Investigation and Optimization of Process Parameters of Al/SiC MMCs Finished by Abrasive Flow Machining}, author={Mittal Sushil and Experimental Investigation and Optimization of Process 2024年2月23日 (A) SiC crystal growth by PVT method, showing the sublimation and crystallization process of SiC from powder to crystal (B) The fundamental mechanism of the transmitted xray imaging The xrays are transmitted, Nondestructive and deep learningenhanced 2021年12月1日 Request PDF Optimization of Tribological Properties of Powder MetallurgyProcessed Aluminum7075/SiC Composites Using ANOVA and Artificial Neural Networks This paper investigates the mechanical Optimization of Tribological Properties of Powder Metallurgy
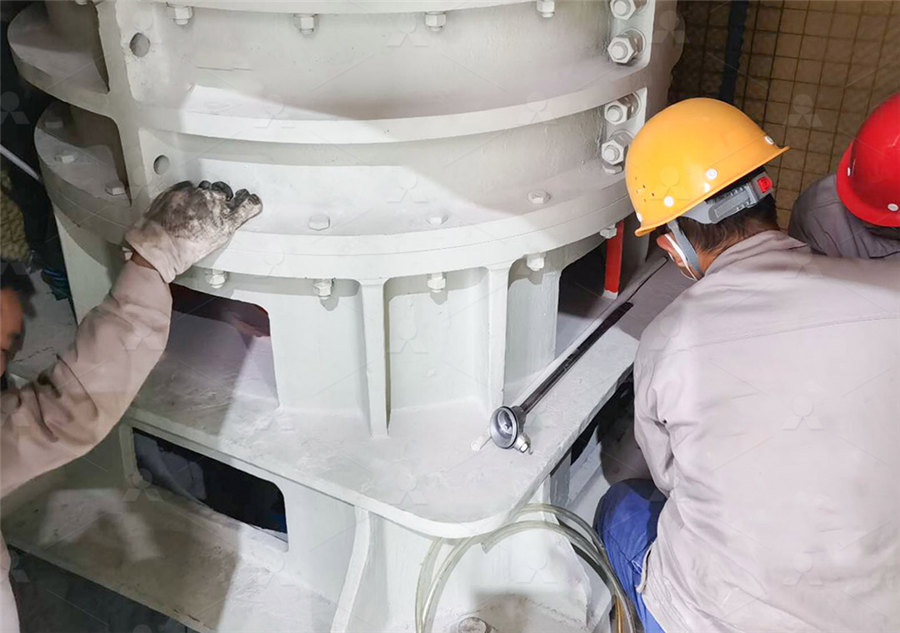
(PDF) SiCYAG Coating Microstructure Optimization Through Powder
2024年3月19日 A silicon carbide/yttrium aluminum garnet (SiC/YAG) composite powder feedstock material developed and patented by NTNU (Norway) in 2012 has been used to produce industrial SiC thermal spray 2024年8月1日 Subsequently, 10 % of the weight of aluminum (8 g) of SiC micro powder (size74 μm) and 3 % of the weight of aluminum (24 g) of SiC nano powder (size 50 nm) were carefully added The SiC micro and nano powders were mixed in a ball milling machine for 20 min at 700 rpm, with a balltopowder ratio of 4:1 by weightFinite element analysis of wire EDM process parameters on 2021年2月1日 The result of TOPSIS multiobjective optimization formulated to identify the optimal grouping of powder metallurgy process parameter It is established form the testing, the most influencing TOPSIS multiobjective optimization of powder metallurgy process 2023年6月20日 In this study, a novel friction material with biomassceramic (SiC) dual matrixes was fabricated using Chinese fir pyrocarbon via the liquidphase silicon infiltration and in situ growth method SiC can be grown in situ on the surface of a carbonized wood cell wall by mixing and calcination of wood and Si powder The samples were characterized using XRD, SEM, Fabrication and Process Optimization of Chinese FirDerived SiC
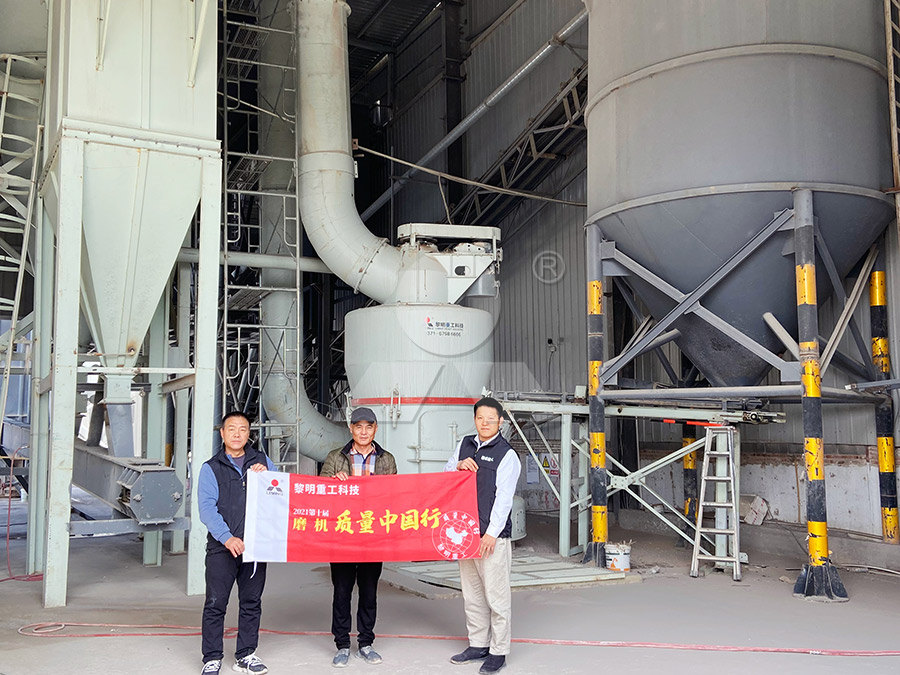
Analysis and multiobjective optimization of slag powder process
2020年7月1日 PDF Slag powder is a process with characters of multivariables, Analysis and multiobjective optimization of slag powder process Xiaoli Li, Shiqi Shen, Shengxiang Y ang, Kang W ang, Y ang 2024年8月25日 For nano/micro powder mixing into dielectric liquid, Characteristics optimization of powder mixed electric discharge machining using titanium powder for die steel materials Proc Hoang, XT, Vu, NP, Le, TQ (2024) Effect of SiC Powder in PMEDM Process on Electrode Wear When Machining CylindricalShaped Part by SKD11 Effect of SiC Powder in PMEDM Process on Electrode Wear When Download Table Jenike(1964)classification of powder flowability by flow index from publication: An Investigation of the Effect of Particle Size on the Flow Behavior of Pulverized Coal In this Jenike(1964)classification of powder flowability by 2019年9月26日 Taguchi methodology was implemented to optimize and evaluate the effect of process parameters such as the applied pressure and time of holding on the tribological properties of ultrahigh molecular weight polyethylene (UHMWPE) nanocomposite reinforced with different loadings of silicon carbide (SiC) nanoparticles An L9 orthogonal array was used to Optimization of SiC Concentration and Process Parameters for a
.jpg)
Optimization of PMEDM process parameters for B4C and B4C+SiC
2023年9月12日 Optimization of PMEDM process parameters for B 4 C and B 4 C+SiC reinforced AA7075 composites Author links open overlay panel Gözde Keskin a, Role of powder in the machining of Al10%SiC metal matrix composites by powder mixed dielectric discharge machining J Compos Mater, 45 (2) 2023年12月13日 Actually, additive manufacturing (AM) is considered as a set or a class of manufacturing processes that are designed to produce complex parts The classification of the AM processes is based on the materials that are used and the type of fed energy in the fabrication process Then, the mechanical and physical characteristics of the produced materials mainly Experimental investigation of the effects of processing parameters 2020年5月11日 A novel structureoptimized SiC fiber reinforced metalintermetalliclaminated composite (SiCfTi/Al3Ti) without intermetallic centerline defect has been fabricated by vacuum hot pressing using stacked fibers and foils as well as Ti barrier layer Through microstructure characterization by SEM and EBSD, the mechanisms of centerline formation and structural Optimization Mechanisms of Microstructure and Mechanical 2024年3月4日 Process Optimization of SiCReinforced Aluminum Matrix Composites Prepared Using Laser Powder Bed Fusion and the Effect of Particle Morphology on Performance March 2024 Materials 17(5):1187Process Optimization of SiCReinforced Aluminum Matrix
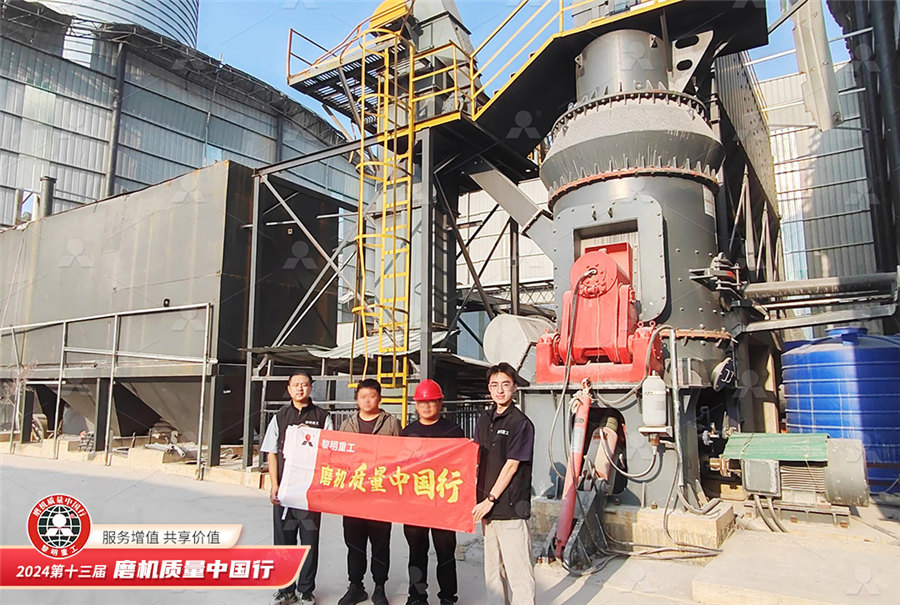
Design Optimization and Mechanical Properties of SiC Particle
2023年7月28日 Tibased bulk metallic glass (BMG) alloys have attracted widespread attention due to their strong glass forming ability, high specific strength, and good corrosion resistance However, the poor plasticity of BMGs limits their further application in the aerospace and aircraft fields, as well as others We optimized the composition of SiCreinforced, Tibased metallic 2019年10月8日 Due to the phase equilibrium in Si and C, the method is based on a physical vapor transportation (PVT) where the source (SiC) in the form of a powder is sublimed at ~ 23002500 °C in a closed Optimization of the SiC Powder Source Material for Improved Process 2019年10月8日 We have studied the influence of different SiC powder size distributions and the sublimation behavior during physical vapor transport growth of SiC in a 75 mm and 100 mm crystal processing configuration The evolution of the source material as well as of the crystal growth interface was carried out using in situ 3D Xray computed tomography (75 mm crystals) Optimization of the SiC Powder Source Material for Improved Process Download Citation On Jan 1, 2024, HoangTien Cao and others published Machined quality prediction and optimization for microEDM drilling of semiconductive SiC wafer Find, read and cite all Machined quality prediction and optimization for microEDM
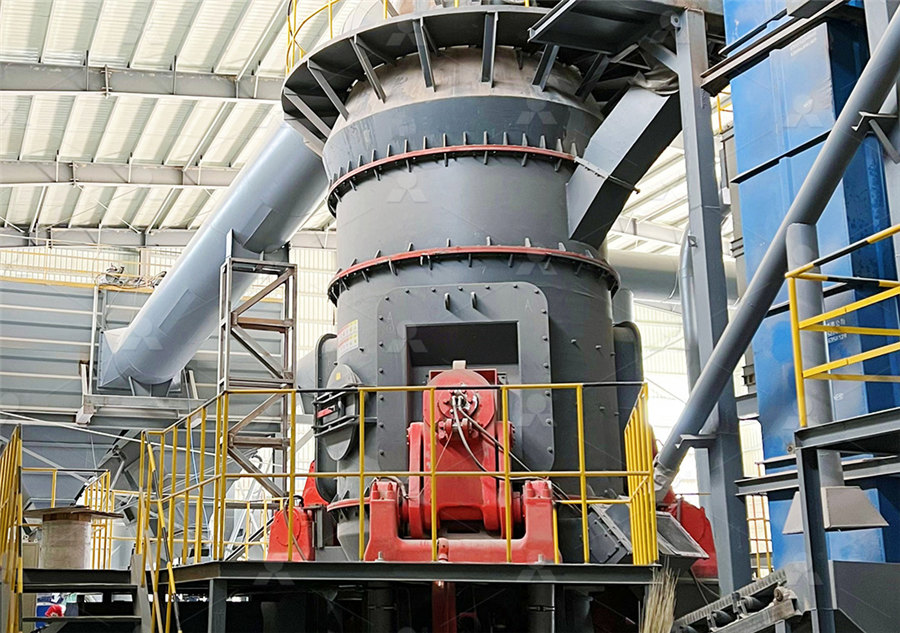
Analysis of surface quality and optimization of process
2022年7月27日 In comparison with mixed powders of Si3N4–SiC and Y2O3, the evaluated densification of Si3N4–SiC–Y2O3 composite powder can be carried out with a smaller amount of Y2O3, since Y2O3 was 2021年3月16日 Titanium coating was deposited on the diamond surface by the vacuum microvapor deposition method to improve the wettability and enhance the interfacial bonding between diamond and copper The Ticoated diamonds were used as the reinforcement particles to fabricate Ticoated diamond/copper composites by the spark plasma sintering, and the effects Optimization of process parameters, microstructure, and thermal 2021年10月20日 This paper investigates the mechanical and tribological characteristics of aluminum alloy 7075 (AA7075) composites reinforced with (2, 4 6) wt% of silicon carbide fabricated using powder metallurgy technique The microstructural examination confirms the even distribution of SiC particles in the AA7075 matrix An increase in hardness and density is Optimization of Tribological Properties of Powder Metallurgy 2023年7月3日 Ore resources in the mining process form a large number of unmanageable tailings, mostly inhalable fine mineral particles, into the environment will cause serious pollution, and recycling is a precious resource The cyclone classification provides the possibility for the recovery and exploitation of fine particles, but the recovery and utilization rate of conventional Enhancement of the classification and recovery process of fine
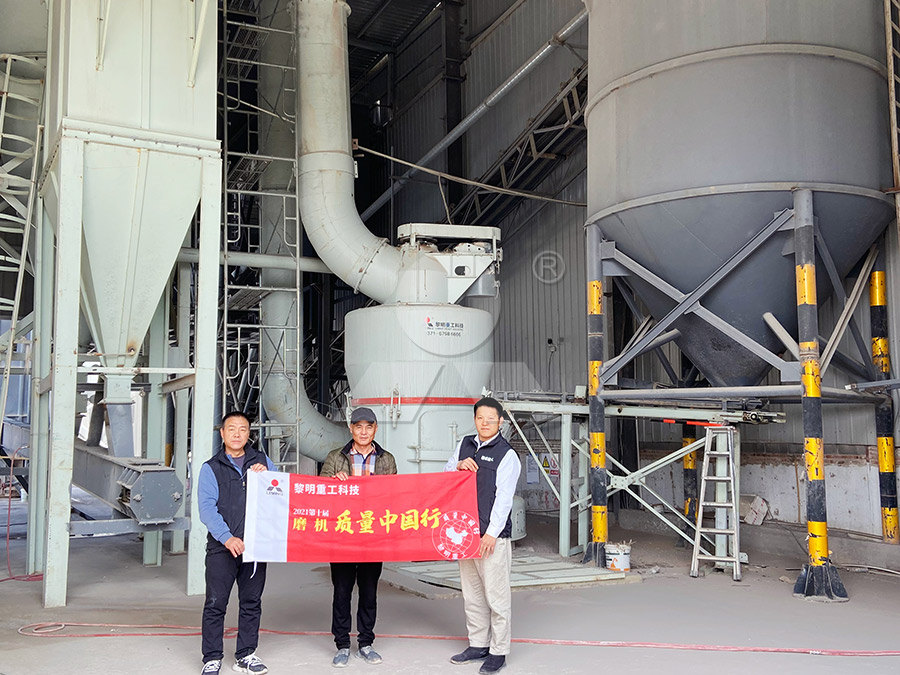
Synthesis, Optimization and Characterization of Silicon Carbide (SiC
2019年1月1日 Al2O3–SiC composite powder (ASCP) is successfully synthesized through a novel moltensaltassisted aluminum/carbothermal reduction (MSACTR) method using silica fume, aluminum powder, and carbon 2021年5月13日 1 INTRODUCTION Silicon carbide (SiC) metal oxide field effect transistors (MOSFETs) are gaining popularity in many applications due to their potential to achieve faster switching speed and attractive voltage ratings [13]However, with their fasterspeed switching, voltage and current overshoots during the switching transient are likely much worse than their Modelling and optimization of SiC MOSFET switching voltage 2012年5月1日 Optimization of process parameters for producing AA6061/SiC nanocomposites by friction stir processing May 2012 Transactions of Nonferrous Metals Society of China 22(5):1055–1063Optimization of process parameters for producing AA6061/SiC With better performances than the traditional SiC powder, the Nanosized SiC powder can meet the strict demands in the new high tech fields and has more extensive uses It summarized the preparation methods of Nanosizeded SiC powder developed in the new high tech fields in recent years and emphasized introducing some new preparation methodsSilicon Carbide (SiC) Micron and Nano Powder Nanografi
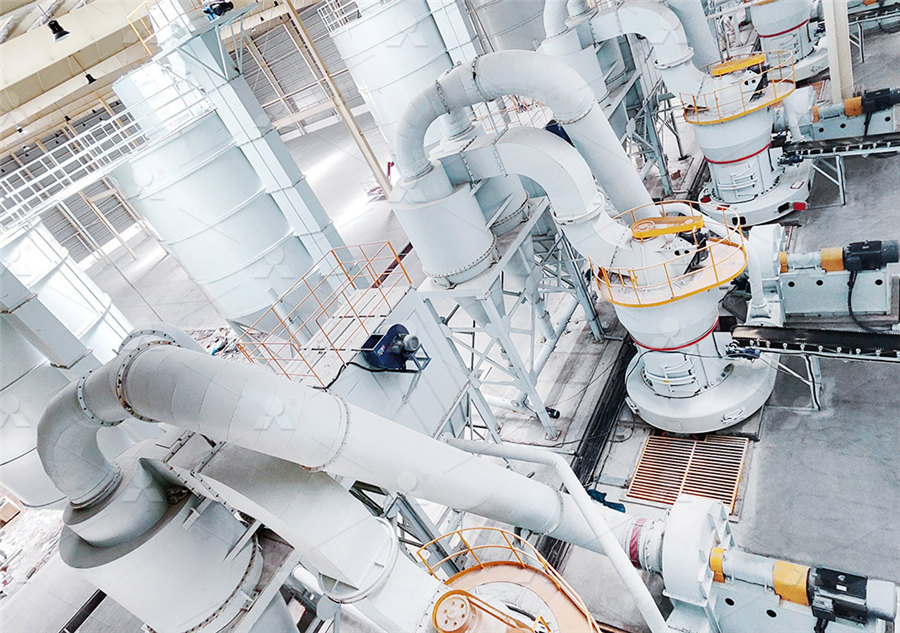
Optimization of Squeeze Casting Process Parameters to Investigate
2020年1月1日 Optimization of Squeeze Casting Process Parameters to Investigate the Mechanical Properties of AA6061/Al2O3/SiC Hybrid Metal Matrix Composites by Taguchi and Anova Approach January 2020 DOI: 10 2021年8月1日 In the BJ 3DP Table 9 Composite types, material compositions, and applications of DEM printed parts Fig 9 (a) Printing process in BJ method (Huang et al, 2019), (b) stepwise process in BJ SiCSi composite part fabrication via SiC powder binder jetting