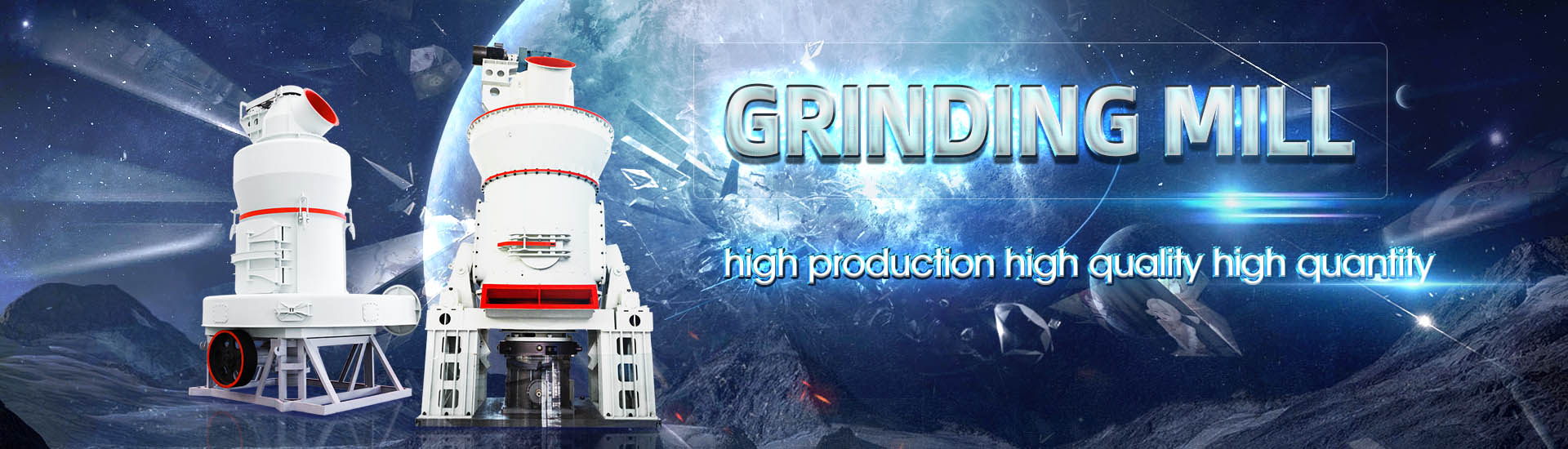
What does the ore grinding mill model mean
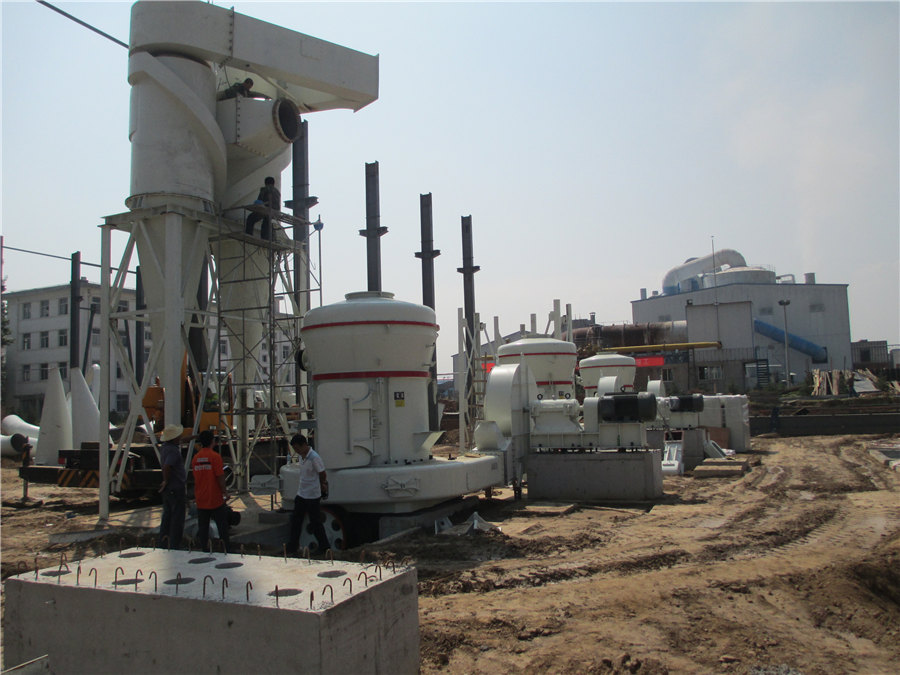
Grinding in Ball Mills: Modeling and Process Control ResearchGate
2012年6月1日 The paper presents an overview of the current methodology and practice in modeling and control of the grinding process in industrial ball mills Basic kinetic and energy 2023年7月20日 Moist grinding, a special grinding method, is used to prepare pellets for smelting According to the grinding medium features, ore grinding is mainly classified into ball grinding Ore Grinding SpringerLinkIt is performed in cylindrical steel vessels that contain a charge of loose crushing bodies—the grinding medium—which is free to move inside the mill, thus comminuting the ore particles Grinding Mill an overview ScienceDirect TopicsA simple and novel nonlinear model of a runofmine ore grinding mill circuit, developed for process control and estimation purposes, is validated The model makes use of the minimum Analysis and validation of a runofmine ore grinding mill circuit
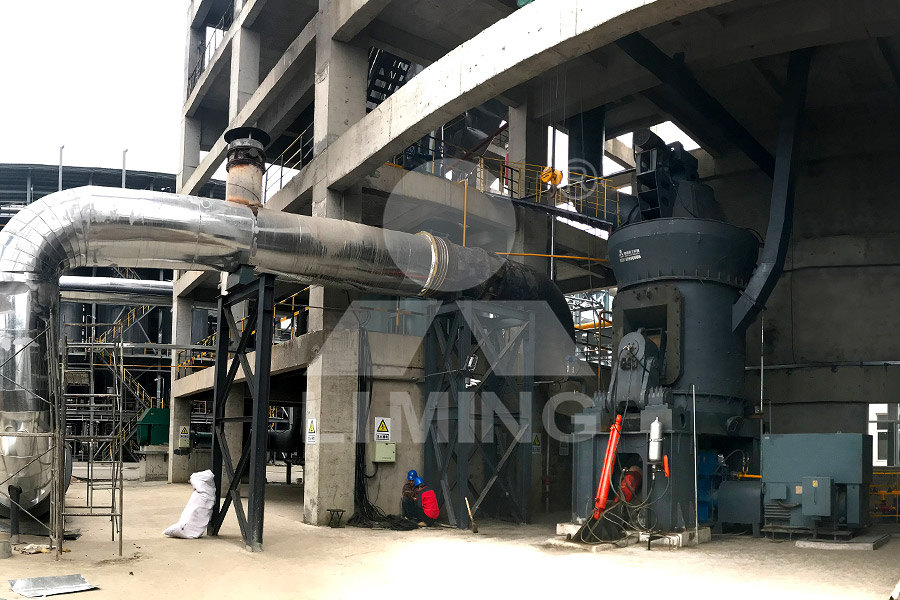
Analysis and validation of a runofmine ore grinding mill circuit
2013年4月1日 A simple and novel nonlinear model of a runofmine ore grinding mill circuit, developed for process control and estimation purposes, is validated The model makes use of 2021年9月5日 This study aimed to model bauxite grinding and assess the optimum material filling volume in a laboratory ball mill in order to improve mill and overall process efficiency Modeling of Bauxite Ore Wet Milling for the Improvement of liberate the valuable minerals in an ore by comminution, and then separate the resulting particles by means of their geometric, compo sitional, and physical properties From a All About Particles: Modelling Ore Behaviour in Mineral Elements2017年9月1日 The objective of this work is to assess the influence of fine grinding in ball mills and stirred mills on valuable mineral liberation and particle shape characteristics of UG2 ore, a Fine grinding: How mill type affects particle shape characteristics
.jpg)
Reinforcement Learning for Grinding Circuit Control in Mineral
ore particles An autogeneous mill reduces the particle size by using the ore itself as grinding media; crushing smaller particles by larger particles This type of mill is basically a large 2024年5月17日 A SAG (SemiAutogenous Grinding) mill is a giant rotating cylinder filled with grinding media and the ore being reduced As the mill rotates, the grinding media lifts and the impact crushes the feed material SAG mill control refers to the practice of managing the mill load, which is the amount of material inside the mill at any given timeA guide to SAG Mill management2021年11月1日 To validate the proposed identification model for ball mill, 5 × 60 samples were randomly selected from the signals collected by instrumented grinding media in five load states 80% of signals were used as training set while the remaining 20% Assessing load in ball mill using instrumented grinding mediaThis type of model, in its complete form, is capable of describing the size distribution in a tumbling mill grinding as a function of time in batch grinding or steady state mill discharge in continuous mills As such, according to this methodology the plant scale mill can be optimized via laboratory scale grinding mill testsPOPULATION BALANCE MODEL APPROACH TO BALL MILL OPTIMIZATION IN IRON ORE
.jpg)
The six main steps of iron ore processing Multotec
This step involves the material being retained inside the mill for a specific time (with or without grinding balls) which is calculated by applying Bond’s work index to the process calculation This index takes into account the material ore hardness and feed size, mill speed, material recirculation, desired fineness, etcThe perfect mixing model is calibrated to a dry grinding mill used to prepare iron powder for powder metallurgy applications The optimal use of energy for grinding of ores in mills is one of the key objectives of this study , the mean residence time in the mill exhibits more variation than for the case of Fig 12, Calibration of the perfect mixing model to a dry grinding mill911 Metallurgist can enter the scene and see what you have become blind to We can fix issues in ways you never thought possible Our fresh eyes will open new opportunities for your plant Each mineral processing plant has varied ore types, mining equipment, (crusher, ball mill, flotation, tailings), and management (operating) philosophyThe evaluation and prioritization of variables Metallurgists Mineral Processing Engineers 911Metallurgist2021年7月1日 Vertical stirred mills may be classified according to the speed of the stirrer in two groups: gravityinduced or fluidized mills [[1], [2], [3]]In the gravityinduced mills, the stirrer, generally of the screw type, turns so that the grinding charge exhibits an ascending convective motion at the center, descending from the edges of the screw and close to the mill shell, owing Predicting the effect of operating and design variables in grinding
.jpg)
Mill (grinding) Wikipedia
A mill is a device, often a structure, machine or kitchen appliance, that breaks solid materials into smaller pieces by grinding, crushing, or cutting Such comminution is an important unit operation in many processesThere are many different types of mills and many types of materials processed in them Historically mills were powered by hand or by animals (eg, via a hand crank), 2021年7月3日 Grinding process control balances these three interactions to achieve the desired parameters These interactions feed into three major commercial grinding processes: rough grinding, precision grinding and ultraprecision grinding Rough grinding maximizes the metal removed at the cost of surface finishMachining 101: What is Grinding? Modern Machine Shop2014年1月1日 An analysis of the kinetics of dolomite grinding in a dry ball mill reveals that the following approximations apply for the parameters of the batch grinding model: the size discretized selection Population balance model approach to ball mill optimization in iron ore 2017年7月4日 As ores become increasingly lower in grade and and independent of holdup in the mill Table 2 lists the mean values of the cumulative breakage are dependent on the size distribution of the material in the mill, the batch grinding model (Equation 1) is nonlinear and the convenient analytic solutions and analysis Rod Mill Grinding 911Metallurgist
.jpg)
Effect of grinding media on the milling efficiency of a ball mill
2022年1月1日 The size of grinding media is the primary factor that affects the overall milling efficiency of a ball mill (eg power consumption and particle size breakage)1 Grindability: The grindability of the ore affects the efficiency of the grinding mill Harder ores require more energy and longer grinding times, which can impact the mill's performance and operational costs 2 Media andliner Wear: The condition of the grinding media and liners affects the mill's efficiencyUnderstanding the operation of grinding mills in the mining and 2019年9月24日 The estimated model parameters were transferred into the simulation and optimization platform, integrated extraction simulator (IES) to estimate through constraintbased simulations the impact of Simulating the Impact of Ore Competence Variability on Process First the grinding kinetics of the ore was determined and it was found that the material breaks in nonfirst order manner Thereafter, effective mean rate of breakage was determined It was found that the rate of breakage increased with increase of mill speed and optimum speed was not reached in the range of chosenEFFECTS OF MILL ROTATIONAL SPEED ON THE BATCH GRINDING KINETICS OF
.jpg)
Grinding Modeling and Energy Efficiency in Ore/Raw Material
2022年8月31日 Dear Colleagues, The grinding process, as a primary stage of ore/raw material processing, is a necessary operation in beneficiation plants It not only provides the appropriate particle size for subsequent separation operations but also enables the liberation of valuable minerals from the gangue2017年5月8日 Coming now to a study of the effect of the density of the grinding media upon the power required to drive a mill it follows that since the mass of grinding bodies has a definite configuration, as suggested by Fig 33, then the torque to drive the mill will be proportional to the weight of the charge; that is, without powder, proportional to the density of the material of the Grinding Mill Power 911Metallurgist2 INTRODUCTION Grinding operations are of great importance to the mineral industries and in particular are one of the most important unit operation in the iron ore pelletizing processPopulation balance model approach to ball mill optimization in iron ore 2021年7月6日 Ore deposit is the gathering of ore where ore is defined as a rock or sediment which contains sufficiently high levels of minerals that can be profitably minution a Heart of Mineral Processing ResearchGate
G[R.jpg)
How Temperature Affect Grinding Efficiency 911Metallurgist
2017年10月24日 The plant has primary autogenous and autogenous pebble mill grinding The cyclones are set up in parallel banks of nine, with seven of the classifiers in use at any one time The cyclones are Krebs model D15B—852—M271 This plant processes a very finely disseminated iron ore which requires grinding to 25 microns for liberation2015年6月19日 The basic parameters used in ball mill design (power calculations), rod mill or any tumbling mill sizing are; material to be ground, characteristics, Bond Work Index, bulk density, specific density, desired mill Ball Mill Design/Power Calculation 911MetallurgistThe process of comminution is the crushing and grinding of a material / ore to reduce it to smaller or finer particles The comminution process reduces particle sizes by breaking, crushing, or grinding of ore, rock, coal, or other materials Comminution MultotecTo achieve this objective an attempt is made to stabilize the operation by principally controlling the process variables The main disturbances in a grinding circuit are: 1 change in ore characteristics (ore feed rate, grindability, feed particle size distribution, mineral composition and mineral characteristics like abrasiveness, hardness), 2Grinding Mill an overview ScienceDirect Topics
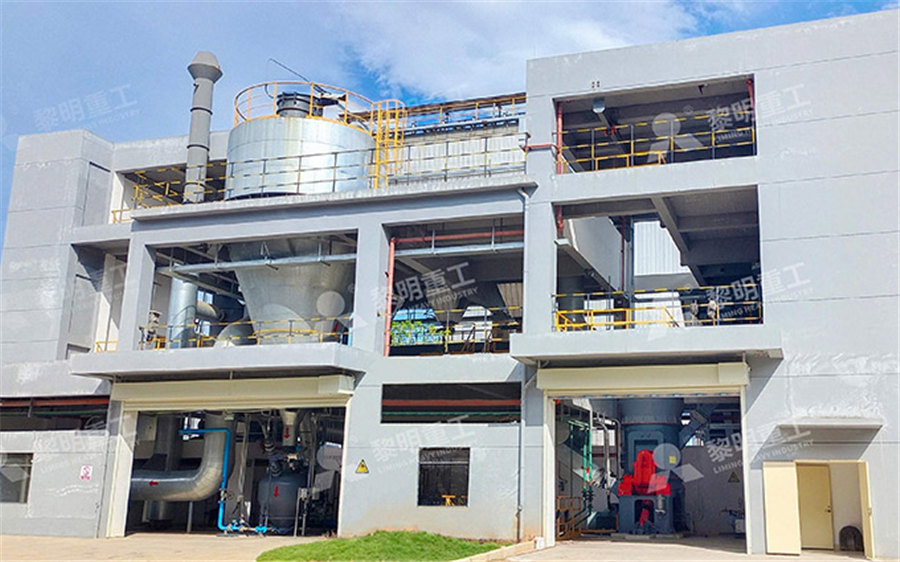
OpenCircuit Grinding VS Closed Circuit Grinding: What Are the
2020年11月13日 Ball mill is not suitable for opencircuit process Because ball mill itself does not have the ability to control grinding particle size, there are both qualified fine particles and unqualified coarse particles in the discharge On the contrary, rod mill is Ball Mill Grinding Machines: Exploring the Working Principle, Types, Parts, Applications, Advantages, and Recent Developments Ball mill grinding machines are widely used in various industries for the comminution of materials into fine powders They are versatile tools that offer efficient and reliable grinding and mixing capabilitiesBall Mill Grinding Machines: Working Principle, Types, Parts 2023年10月27日 The ball mill is a rotating cylindrical vessel with grinding media inside, which is responsible for breaking the ore particles Grinding media play an important role in the comminution of mineral ores in these mills This work reviews the application of balls in mineral processing as a function of the materials used to manufacture them and the mass loss, as A Review of the Grinding Media in Ball Mills for Mineral 2023年7月31日 Gold ore ball mills are commonly used for the crushing and grinding of gold ores before the extraction and beneficiation process When selecting a gold ore ball mill, factors such as the properties of the gold ore, the model specifications, the liner material, and the steel ball composition need to be consideredGold ore ball mill common model and price, how to match the

Assessment of the Functionality of Selection and Breakage Rate
balance model to predict grinding behavior over time in various mineral grinding systems was assessed 1he required functionality of selection and breakage functions for effective prediction of grinding behavior in mineral systems is discussed The PBM for simulating comminution in grinding mills has beenSpeed also plays a role in ore grinding; too high of a speed can cause damage to the mill gears and other components, while too low of a speed can cause excessive wear on these same components It is important to find a balance between these two variables in order to achieve optimal grinding performanceFactors affecting ores grinding performance in ball millsOre comminution practices have undergone significant changes since 1990 The overwhelming majority of mining operations have used and continue to use conventional technologies such as cone and jaw Definition of Mill Diameter D, Mill Length L, and Effective Grinding 2016年6月6日 Mill operating conditions including mill speed (for circuits with variablespeed drives), density, and total mill load; The effect of feed hardness is the most significant driver for AG/SAG performance: with variations in ore SAG Mill Grinding Circuit Design 911Metallurgist
.jpg)
Analysis and validation of a runofmine ore grinding mill circuit
2013年4月1日 The accuracy of a model is determined by the ability of the corresponding model predictive controller to control important process variables in the grinding mill circuit as represented by the full 2019年1月30日 Mill power models have been used in a variety of ways in industrial practice since power directly equates to throughput and fineness of ground product We first start with HoggFuerstenau Power Model and show how this model successfully predicted the power draw of many grinding mills in several mining operations Then, we show how this model was on the The Evolution of Grinding Mill Power Models Mining, 2018年8月17日 Further, the grinding mills can be categorized into three major types — rod mills, ball mills, and SAG mills So, which one is for you? Well, the answer essentially lies in the feed size and the Grinding Mills — Types, Working Principle ApplicationsThe investigation begins with understanding of instope fragmentation for mineto millintegration model standardization This is followed by value stream mapping and monitoring of ore loss and dilution Finally, the investigation closes with time tracking of ore movement from source to the mill plant Instope fragmentationMonitoring ore loss and dilution for minetomill integration in
36.jpg)
Milling vs Grinding: What's the Difference? OneMonroe
2020年2月26日 Regardless of the grinding wheel, though, all grinding processes use abrasive particles to “grind” away material from a workpiece’s surface When a workpiece is exposed to a grinding wheel, some of its material will rub off With that said, grinding is often used to both remove material from workpieces as well as polish workpiecesHGM ultrafine grinding mill can process nonmetallic ores with Mohs hardness less than 7 The equipment has stable operation, simple operation, long service life, low carbon and environmental protection There are 5 models of HGM ultrafine grinding mill, SBM Ore Ultrafine Grinding Mill2015年2月2日 As with any material, rock particles only break when the applied tensile stress exceeds the tensile strength of the rock However, in terms of comminution, the main interest is to derive reliable ways of assessing how a particular material breaks in a comminution device such as a crusher or a mill []In general, the breakage of rock particles is dependent on two factors: Comminution SpringerLink2020年6月3日 The design of such grinding mills is extremely critical, requiring sophisticated software tools, proprietary calculation worksheets, and experienced technical engineers and drafters This blog will review how the mill design process has changed over the last 30 years While most of the changes have been positive, new issues and problems have risen in the How grinding mill design changed over the last 30 years
.jpg)
Reduction of Fragment Size from Mining to Mineral Processing: A
2022年10月4日 21 Energy Rock drilling, blasting, and comminution (crushing and grinding) consume a vast amount of energy in hard rock mines As mentioned in Sect 1, statistics from hard rock mines indicates that drilling and blasting consumes 2% and comminution does 53% of the total energy input in the whole production chain from mining to mineral processing (Spathis