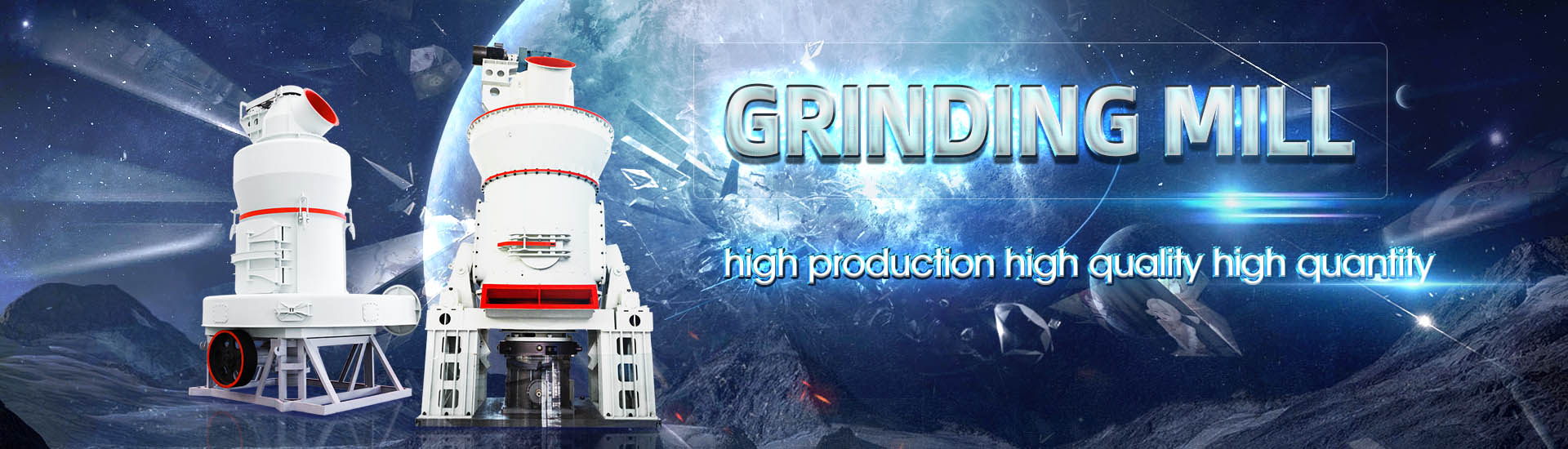
Can oxide ore be used to make sponge iron
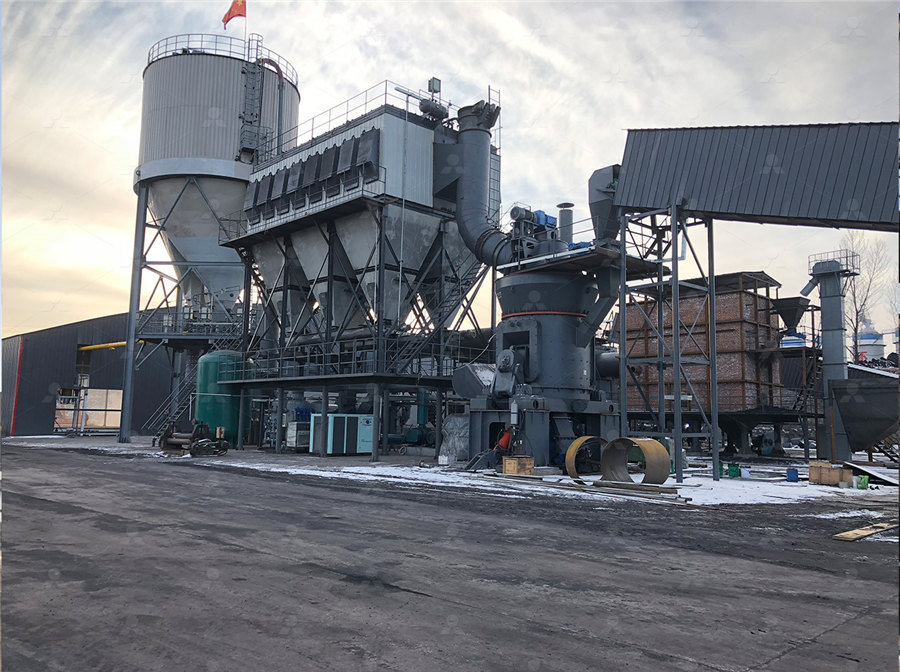
Direct reduced iron Wikipedia
Sponge iron is not useful by itself, but can be processed to create wrought iron or steel The sponge is removed from the furnace, called a bloomery, and repeatedly beaten with heavy hammers and folded over to remove the slag, oxidize any carbon or carbide, and weld the iron together This treatment usually creates 展开2017年10月17日 However, the reduced "sponge iron" from a DRI process is porous and will oxidize or rust if shipped or stored in the porous form Sponge From Ore to Iron with Smelting and Direct Iron 2016年3月30日 During the last four decades, a new route of ironmaking has rapidly developed for direct reduction (DR) of iron ore to metallic iron by using noncoking coal/natural gas This product is known(PDF) i) Direct Reduced Iron: Production ResearchGateDRI, also known as sponge iron, is the product of reducing iron oxide in the form of iron ore and steel plant wastes into metallic iron, below the melting point of iron and typically in the range of Sponge Iron an overview ScienceDirect Topics
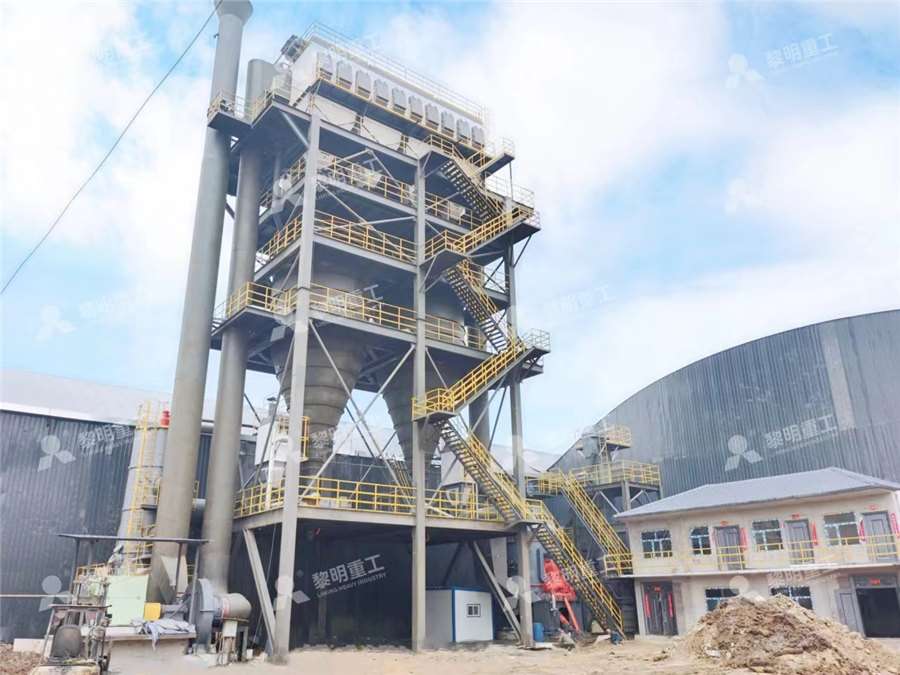
Direct Reduction of Ferrous Oxides to form an Iron
2015年12月1日 Sponge iron is the metallic form of iron produced from reduction of iron oxide below the fusion temperature of iron ore by utilizing hydrocarbon gases or carbonaceous fuels as coal The reduced product having high Common forms of ore are hematite (Fe20a) and magnetite (Fea04)' For the ore to be made into iron the oxygen atoms must be separated from the iron atoms by the process known as The Direct Reduction of Iron Ore2023年10月9日 It is the noncoke ironmaking process in which a gaseous, liquid, or solid reductant is used to reduce the iron ore into metallic iron in a temperature less than the ore Direct Reduction Ironmaking SpringerLink2020年3月3日 Melting of sponge iron/DRI in EAF is greatly influenced by factors like carbon content and degree of metallization of DRI Carbon in sponge iron/DRI reacts with unreduced Sponge Iron SpringerLink
.jpg)
LECTURE NOTES ON Sponge Iron Ferro Alloys KIIT Polytechnic
2O3) is directly reduced by the reductant The percentage of oxygen associated with iron ore as oxide removed from the particle is known as percentage reduction whereas the percent of iron Part 3A: Iron Sponge Basics November 2017 One of the oldest technologies for the removal of hydrogen sulfide (H 2 S) from gas is the use of “Iron Sponge” A chemicalphysical process, originally developed to remove H 2 S from natural and coal gas streams, iron sponge has been in use for over 140 years and more recently to remove H 2HYDROGEN SULFIDE REMOVAL FROM BIOGAS Part 3A: Iron Sponge ‘The reduction involves removing the oxygen from the iron ore, which is a prerequisite for steel productionThe sponge iron will be compressed to form socalled HBI (Hot Briquetted Iron)In a traditional process, this is done using Hydrogen reduced sponge iron to cut carbon 41 Direct Reduction of Iron Production Using Solid Coal 39 42 Direct Reduction of Iron Production Using Coal Gasification 43 43 Direct Reduction of Iron Production Using Gas Route 49 44 Hydrogen Use in Indian Iron and Steel Sector 54 50 Conclusion 57 Technology Vendors – Energyefficient Equipment and Systems 60 References 65ENERGYEFFICIENT TECHNOLOGY OPTIONS FOR DIRECT REDUCTION OF IRON
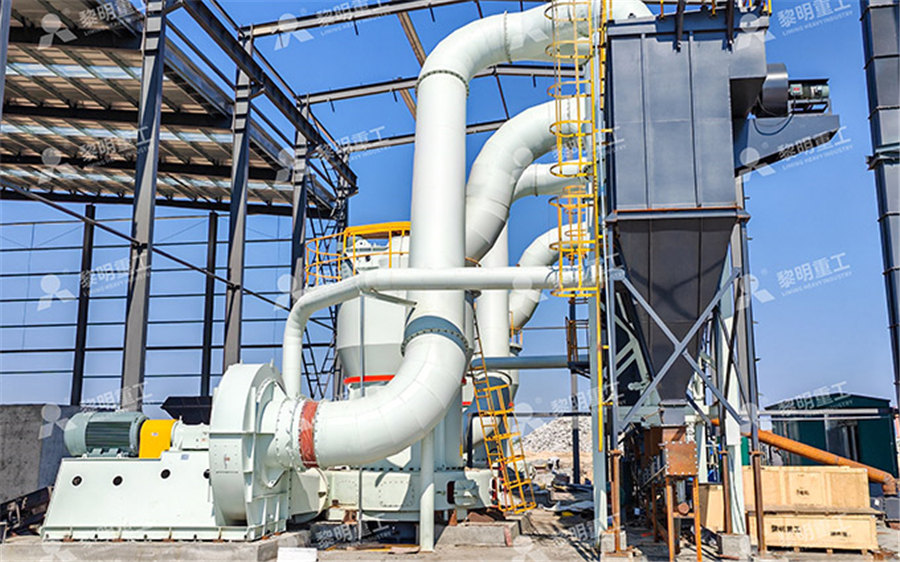
Direct Reduced Iron and its Production Processes – IspatGuru
2013年3月16日 Iron ore is used mostly in pellet and/or lumpy form Oxygen (O2) is removed from the iron ore by chemical reactions based on H2 and CO for the production of highly metalized DRI In the direct reduction process, the solid metallic iron (Fe) is obtained directly from solid iron ore without subjecting the ore or the metal to fusion2024年7月29日 What is sponge iron Sponge iron, also known as DRI (direct reduced iron or direct reduction iron), bulk density 1619g/cm3, apparent density 3436g/cm3, typical size 420mm, is a kind of material produced by the reduction of iron ore with reducing gases such as H2 or CO gas generated from various carbon or hydrocarbon resourcesDRI briquetting, sponge iron briquette making – why and how2023年11月5日 Introduction To Oxides And Stains In Pottery Pottery and ceramics have been a source of artistic expression and practical use for centuries One key element in creating unique and visually appealing pottery is the use of oxides and stains These substances serve various purposes, including fluxing, glass formation, and coloringUnderstanding how to utilize oxides How to Use Oxides in Pottery: Techniques and Effects2017年10月10日 Iron ores with lower iron content such as taconite are first processed to concentrate the iron level and drive off volatile impurities The iron ore is dressed or crushed into 051 in chunks, which increases surface area for reactions Magnetic separation is used to remove some of the undesirable minerals or gangue in the crushed oreIronmaking 101 – From Ore to Iron with Blast Furnaces
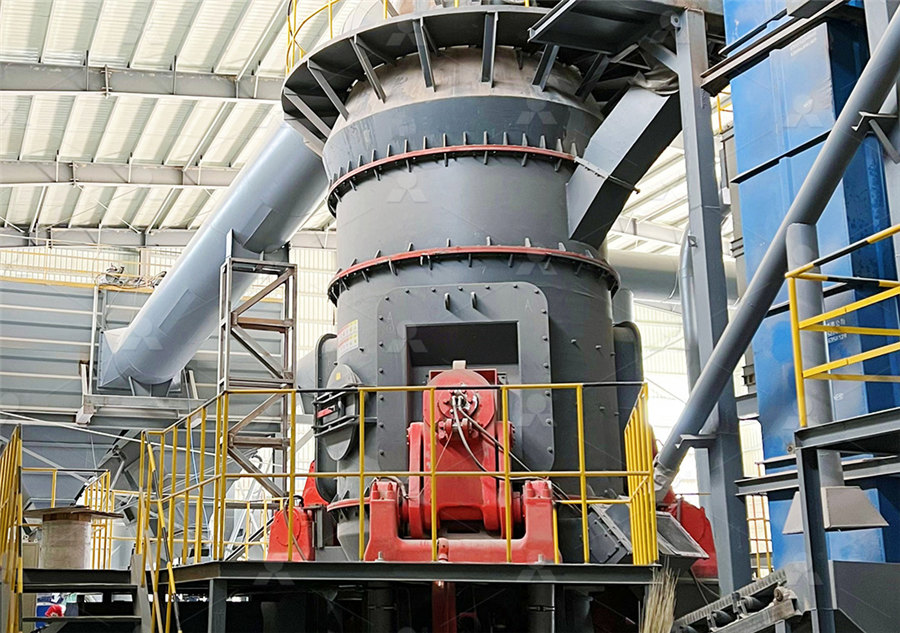
Reducing Iron Oxide with Ammonia: A Sustainable Path to Green
2023年3月30日 Iron making is the biggest single cause of global warming The reduction of iron ores with carbon generates about 7% of the global carbon dioxide emissions to produce ≈185 billion tons of steel 2013年12月14日 These standards are (i) ISO 4701:2019 Iron ores and direct reduced iron – Determination of size distribution by sieving, ISO 9686:2006 Direct reduced iron – Determination of carbon and/or sulphur – High frequency combustion method with infrared measurement, (iii) ISO 10835:2007 Direct reduced iron and hot briquetted iron – Sampling and sample Direct Reduced Iron IspatGuru2019年7月19日 The ITmk3 process uses lowgrade iron ore and coal (other feedstocks can be used as supplements) to produce iron nuggets whose quality is superior to that of DRI (97% iron content) but is similar to that of pig iron The mixing, agglomeration, and feeding steps are the same as in the production of DRI or BFs, but the RHF is operated differentlyDirect Reduced Iron: Most Efficient Technologies for Greenhouse 2023年4月5日 The blast furnace and direct reduction processes have been the major iron production routes for various iron ores (ie goethite, hematite, magnetite, maghemite, siderite, etc) in the past few decades, but the Recent Trends in the Technologies of the Direct
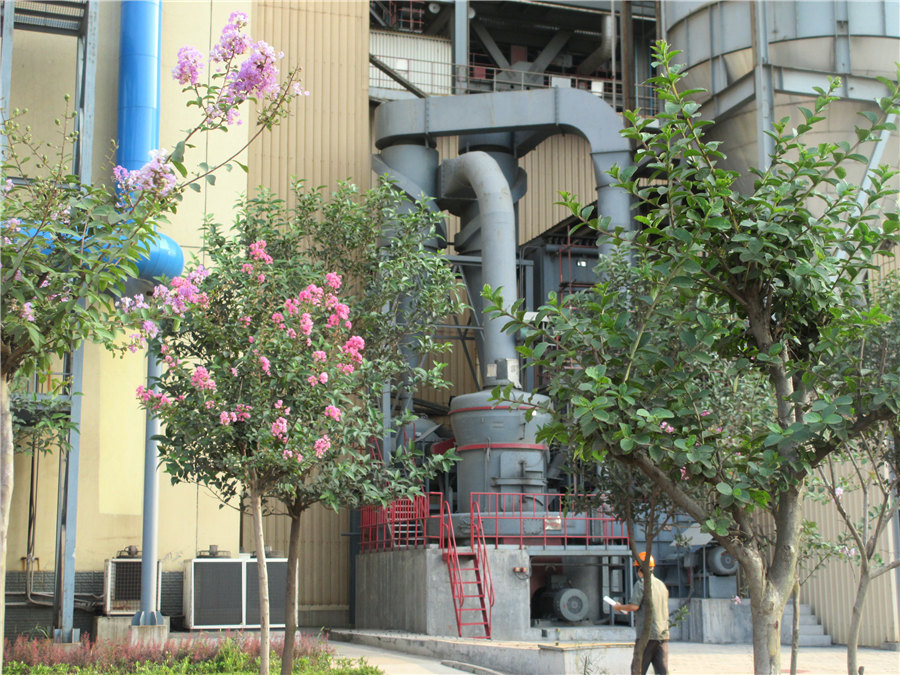
4 Ways to Make Iron Oxide wikiHow
2023年2月19日 To make iron oxide, start by getting an iron source with as much exposed surface area as possible, like steel wool Then, choose an oxidizing agent, such as hydrogen peroxide, bleach, or salt water Next, submerge the 2023年10月9日 The iron product has 6% carbon content The product is stable and free from spontaneous combustion In addition to the advantages of direct reduction iron, the product has high carbon content, and the smelting combustion releases heat that is used in the steelmaking process, which reduces electricity consumption during steelmakingDirect Reduction Ironmaking SpringerLink2020年6月3日 A new route for making steel from iron ore based on the use of hydrogen to reduce iron oxides is presented, detailed and analyzed The main advantage of this steelmaking route is the dramatic reduction (90% off) in CO2 emissions compared to those of the current standard blastfurnace route The first process of the route is the production of hydrogen by Hydrogen Ironmaking: How It Works MDPIFerrous Oxide (FeO), Iron Oxide (Spent) or Iron Sponge Ferrous Oxide (FeO) may be formed in Oxygenlimited atmospheres, in flue gas, and from coal gas purification Iron Oxide (Spent) or Iron Sponge is produced when Iron Ore is heated below the melting point of Iron With further processing, they become Wrought Iron REASON FOR CITATIONIRON OXIDE HAZARD SUMMARY Iron Oxide The Official Web
.jpg)
LowCarbon Production of Iron Steel: Technology Options,
2021年3月8日 These processes operate with different feedstocks The BFBOF pathway converts raw iron ore to pig iron and then to steel HM – while EAF converts both steel scrap and sponge iron to steel HM DRI converts raw iron ore to sponge iron, a porous, permeable, and highly reactive product that requires treatment with EAF before selling to market2023年12月11日 In that case, you're starting from iron ore (eg, taconite) which is almost always some form of iron oxide So, the main impurity you need to remove from iron ore to get iron is oxygen In a traditional blast furnace, you use carbon not only as something to burn to get heat, but also as a chemical reactantCan electric furnaces be used for steel production from ore?2015年12月1日 In this study, production of sponge iron by direct reduction of oxides and the effect of reductant on metallization were investigated In the first stage of the study, scale formed during hot rolling of slabs was reduced in a rotating furnace using solid and gas reductants Coal was used as solid reductant and hydrogen released from the combustion reaction of LNG was Direct Reduction of Ferrous Oxides to form an IronRich Iron ore is the raw material used to make pig iron, which is one of the main raw materials to make steel—98% of the mined iron ore is used to make steel [2] In 2011 the Financial Times quoted Christopher LaFemina, mining analyst at Barclays Capital, saying that iron ore is "more integral to the global economy than any other commodity, except perhaps oil "Iron ore Wikiwand
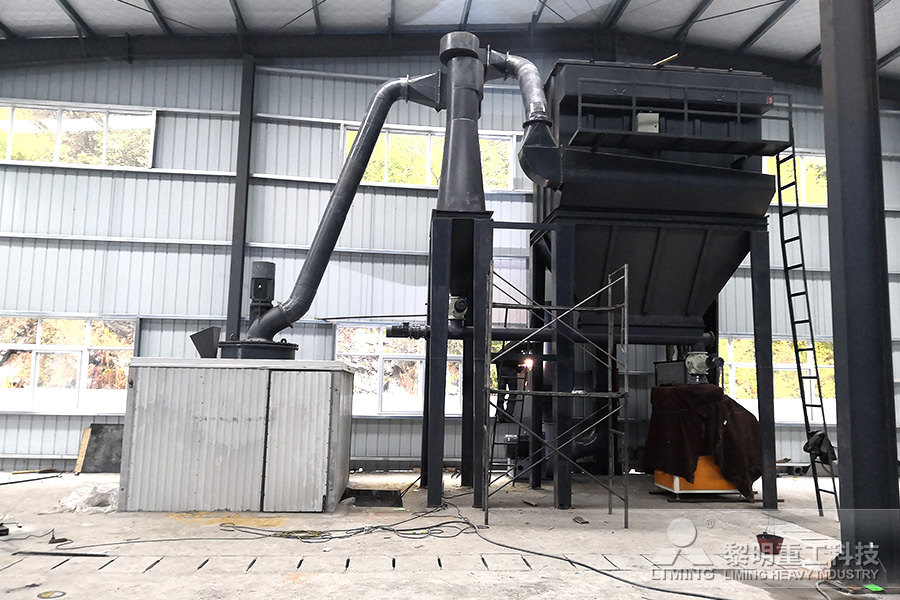
Reducing Iron Oxide with Ammonia: A Sustainable Path to Green
2023年3月30日 1 Introduction Iron and steel are pillars of global civilization and industrialization, with currently 185 billion tons produced per year [] This staggering amount is forecast to grow up to 25–30 billion tons by the year 2050 [] As the primary synthesis of iron uses fossil reductants (from coal, coke, and methane) to reduce oxidic ores, the steel industry is currently the largest To determine how long the reactor can go between media changeouts the following equation can be used P𝑐=314 𝑥 10−8 𝐹 2 𝐻 𝑔 𝑀𝐹 Where: t c: Change out time, days Fe: Iron sponge content lbs Fe 2 O 3 per bushel of media e: reaction efficiency, 06 to 08 Typically iron sponge contains 15 lbs Fe 2 O 3 per bushelDairy Environmental Systems Program HYDROGEN SULFIDE During reduction of a porous iron ore particle, the following process steps occur: 19, 2224 mass transfer of the gaseous species (reducing gases H 2 and CO) from the gas stream through the laminar layer of the oxide to the interface; Reduction of Iron Oxides with Hydrogen—A Review2023年12月1日 How Are Iron Ore Pellets Made? Here’s a quick introduction for you on how Pellets are made Usually, Iron Ore is manufactured and converted into Pellets These are oval lumps of iron ore that are hardened using fuel This process of converting iron ore into pellets is known as Pelletization Iron Ore Pellets are then used in the production of Applications of Iron Ore Pellets Sree Metaliks
.jpg)
Iron ore uses – types of iron ores and the specific application
2024年4月7日 What is iron ore Iron ore is a mineral aggregate that contains iron element or iron compound and can be used economically It can be used for refining elemental pig iron, steelmaking and many other purposes About 98% of iron ore is used to produce iron, it is one of the important sources used to refine steel In steel mills, natural ore (iron ore) undergoes The term direct reduction of iron ore originates from the fact that the iron oxide(Fe 2 O 3) is directly reduced by the reductant The percentage of oxygen associated with iron ore as oxide removed from the particle is known as percentage reduction whereas the percent of iron as part of whole iron existing as metallic iron is called as degree Chapter 1 Review of Sponge Iron Making Process Historical The red iron oxide or ferric oxide glaze is one of those prevalent glazes that act as a much more common colorant for the glazing mixture With its easy availability, it offers a beautiful color to the glazing when fired inside the kiln Moreover, the potters use iron oxide wholeheartedly because during pottery glazing, the iron changes quite quickly in reduction firingEverything You Wanted to Know About Iron Oxide GlazeIron ores consist predominantly of the iron oxide minerals hematite (Fe 2 O 3) and magnetite (Fe 3 O 4)The primary intermixed noniron oxides are SiO 2, Al 2 O 3, MnO, and MgO, and are referred to as gangueBoth pellets and sinter can be produced from a mixture of hematite and magnetite; essentially all the input magnetite is oxidized to hematite when pellets are Overview of the Steel Production Process Springer
.jpg)
TOP 10 WAYS TO DECORATE WITH OXIDES BigCeramicStore
2019年11月5日 Make some slip and add some oxides to create colors To get more TOP 10 WAYS TO DECORATE WITH OXIDES You’ve probably heard of oxides, but you're probably Or use a piece of Styrofoam or a sponge to pick up the oxide and transfer it to your piece Keep the pattern as it lands, or smear it around In this case if you’re once applications which surface area is the required feature In regard to purity, sponge iron is reduced from iron ore and even after the reduction process can still contain significant levels of unreduced iron oxide and impurities such as SiO 2 and V 2 O 5 Most iron powders that are produced by atomization utilize water as the atomizing medium PROPERTIES AND APPLICATIONS FOR IRON POWDER MADE BY 2017 integrated steel producers smelted iron ore to make liquid iron in blast furnaces and used basic oxygen furnaces (BoFs) to refine the liquid iron, with some steel scrap, to produce raw liquid steel The BoF process was used to make 277 Mt of steel in the United States, a 7% increase from 258 Mt in 20172018 Minerals Yearbook USGS Publications Warehouse2 Materials Used to make Steel 21 Iron Ore Composition Iron very rarely occurs in the earth's surface as a metal It is widely distributed, combined with oxygen as iron oxides In fact it is believed that iron makes up about 5% by weight of the earth's crust Geologists recognise various types of iron ore, classified chiefly according to iron (Fe)The Making of Iron Steel SEAISI
.jpg)
Iron ore Wikipedia
Hematite, the main iron ore found in Brazilian mines Stockpiles of iron ore pellets like this one are used in steel production An illustration of iron ore being unloaded at docks in Toledo, Ohio Iron ores [1] are rocks and minerals from 2023年10月31日 Turkey’s iron ores may be used to manufacture sponge iron, and the country’s coal resources, which are plentiful despite being of poor quality, can be used as a reducing agentOptimization of sponge iron (direct reduced iron) 2017年2月14日 The metallic iron in this process is produced by the reduction of iron oxide below the fusion temperature of iron ore (1535 deg C) by utilizing carbonaceous material present in the noncoking coal As the iron ore is in direct contact with the reducing agent throughout the reduction process, it is often termed as direct reduced iron (DRI)Coal based Direct Reduction Rotary Kiln Process – IspatGuru2017年2月16日 Sintering is a thermal agglomeration process that is applied to a mixture of iron ore fines, recycled ironmaking products, fluxes, Iron oxide can simultaneously be reduced by carbon monoxide (PDF) Iron Ore Sintering: Process ResearchGate
.jpg)
How to Manufacture Pig Iron: How Pig Iron is made?
(3) Sponge Iron Process: As the name implies, the spongy iron is obtained by the reduction of lumpy iron ore or iron ore pellets from the oxide form into the metallic state The iron content of the product so obtained varies from 90% to 94% and the balance represents the traces of gangue and residual iron oxide2020年8月19日 Even when the process is similar, the technology is completely different due to the knowledge available about the physical–chemical changes that are produced in the iron ore when the temperature is changed in a reductant environment However, as opposed to previous times, the sponge iron is not used to obtain bars or steel ingots by forgeProduction of Iron in the Blast Furnace SpringerLink2024年7月18日 Australia’s iron ore makes a significant contribution to our economy, with a gross added value of over $100 billion each yearHowever the process of turning the world’s iron ore into steel currently contributes around seven per cent of global greenhouse gas emissionsThere are a number of ways of reducing the carbon footprint of the iron making industry, one of the How hydrogen can help to decarbonise iron making CSIRO2016年5月5日 Composite briquettes are solid mixtures of iron ore and carbon often with a binder and flux additive When heated, the iron oxides are reduced through a series of gas–solid reactions The resulting sponge or direct reduced iron (DRI) can be used as a supplementary iron source to a blast furnace or as a feed material to an electric arc furnace The Strength and Density of Green and Reduced Briquettes Made with Iron
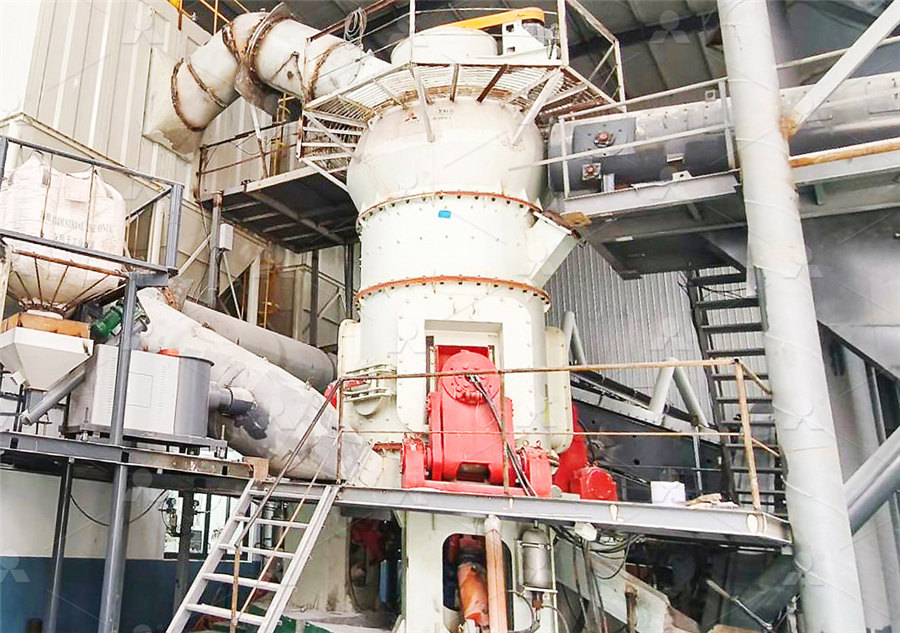
Iron Ore Pelletizing Process: An Overview IntechOpen
44 Iron Ores and Iron Oxide Materials To avoid such effects, binders are added to the material to be pelletized, aiming to: increase the strength of pellets before heating (green strength); prevent the collapse of pellets during the initial stages of heating, when a large volume of