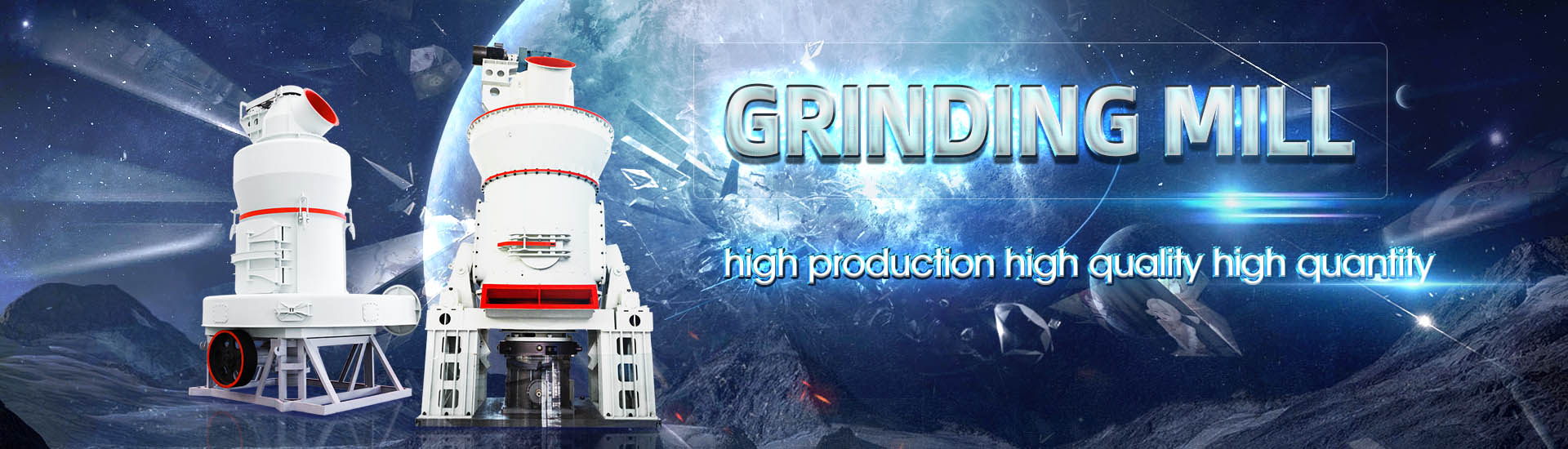
Energysaving evaluation report of 600,000 tons of cement grinding station per year
.jpg)
A comprehensive investigation of a grinding unit to reduce energy
2023年5月3日 The applications provide 18469 MJ reduction in specific energy consumption (SEC) per ton of cement produced and blocked 75,34337 tons of CO 2 emissions per year 2013年3月1日 In this paper, energy saving measures in the cement industry, such as energyefficiency measures for the preparation of raw materials, production of clinker, and the An overview of energy savings measures for cement industriesThe main results of the study are the benchmark curves, the energy saving potentials and the energy saving scenarios The following saving potentials were calculated: Frozen efficiency: Benchmarking Report for the Cement Sector UNIDO2020年3月1日 In this study, an integrated 3phase model is presented to address these shortcomings and assist the plant managers to select and invest in the most suitable projects A decision support tool for cement industry to select energy
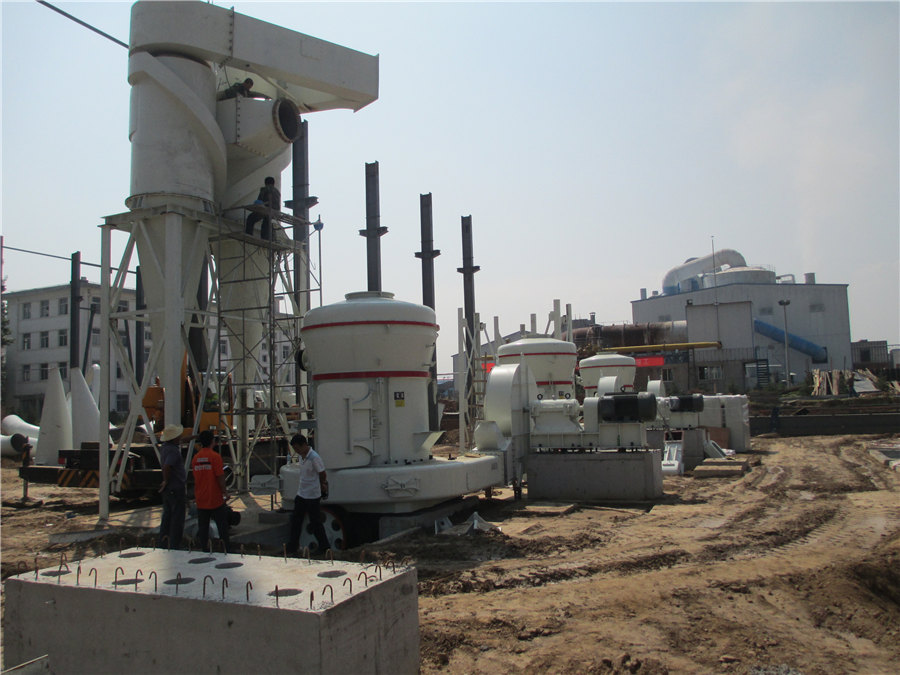
A critical review on energy use and savings in the cement industries
2011年5月1日 It has been identified that sizeable amount of energy can be saved and emission can be reduced in raw materials preparation, clinker production, finish grinding, general areas, 2016年10月5日 In this chapter an introduction of widely applied energyefficient grinding technologies in cement grinding and description of the operating principles of the related EnergyEfficient Technologies in Cement Grinding IntechOpenimproving its carbon footprint (emissions per unit of output) by improving energy efficiency, increasing the use of alternative fuels, and deploying renewable energy sources With a IMPROVING THERMAL AND ELECTRIC ENERGY EFFICIENCY AT In this paper, the specific energy consumption (SEC) and related emissions of a real scale cement factory currently running in Türkiye have been decreased by investigating the efects of A comprehensive investigation of a grinding unit to reduce energy
.jpg)
Benchmarking of Energy Consumption and CO2 Emissions in
Key energy and emissions parameters, including thermal and electrical energy intensity, recovered energy and CO2 intensity, are computed per tonne of cement produced along with This report reflects an indepth analysis of the cement industry, and identifies energy savings and carbon dioxide emissions reduction potentials In this analysis, the cementEnergy Efficiency Improvement and Cost Saving Opportunities for 2020年8月30日 Presently, the installed capacity is around 390 metric tons per annum, and the annual production is 270 metric tons per annum in 2014–2015 (Asia–pacific Partnership 2010) According to a government report, 178 large cement plants produce 97% of its total installed capacity Percapita intake of cement is 190 kg only (world’s average 396 kg)Estimation of waste heat and its recovery potential from energy 2013年3月1日 The current global consumption of cement industry is about 15 billion tons per annum and is rising at almost 1% per annum Cement production requires approximately 110 kW h/t of electrical energy, with 40% directed to clinker grinding [26]Using real auditing, Avami and Sattari [17] investigated technological methods that would reduce the energy consumption, An overview of energy savings measures for cement industries
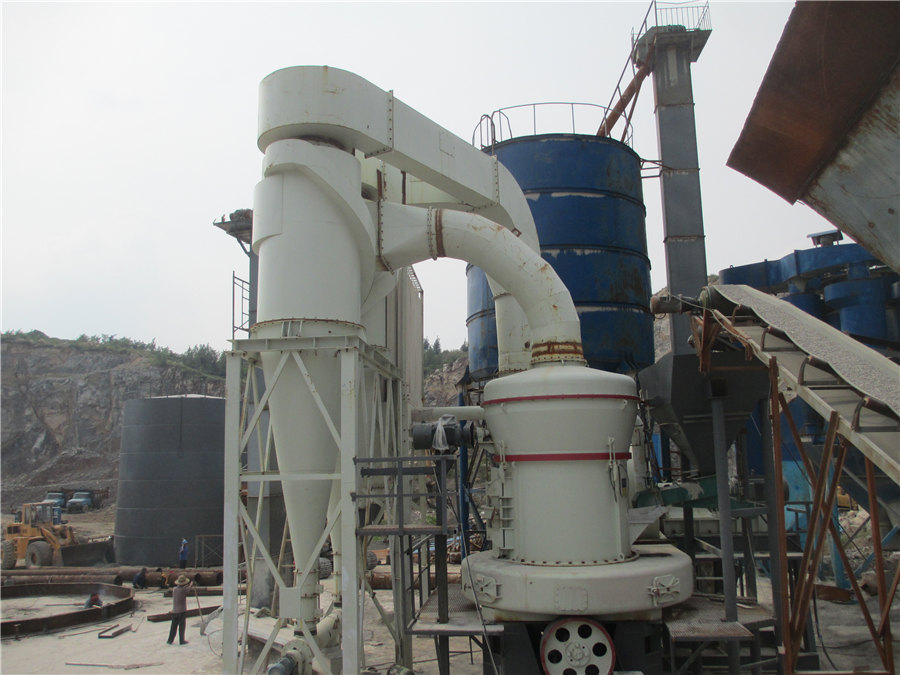
Evaluation of energy saving potential in China's cement industry
2015年2月1日 The cement industry, as a pillar of Chinese economic development, has grown rapidly alongside the national economy Cement production has increased dramatically from 6524 million tons in 1978 to 2099 million tons in 2011, with an average annual growth rate of 1108% (NBSC, 2013)Up to 2011, China has been the largest cementproducer in the world 2024年2月2日 The research utilises industrial data from a 2850 tonne per day capacity dry process cement plant Key energy and emissions parameters, including thermal and electrical energy intensity, recovered energy and CO 2 intensity, are computed per tonne of cement produced along with capacity utilisation across major process stages including raw Benchmarking of Energy Consumption and CO2 Emissions in Cement 2022年5月26日 Recycled cement production The RC production process analyzed in this research corresponds to the patented method developed at IST (Bogas et al 2020) described in Sousa and Bogas ()The method is based on the magnetic separation of the cement paste from the aggregates and, resuming briefly, it comprises three stages as depicted in Fig 1: (i) Industrial production of recycled cement: energy consumption 5 天之前 Cement Introduction Cement plays vital role in building economic development of any country Indian cement industry is the largest cement producing country in the world, next only to China The first cement company became operational in Porbandar, Gujarat with a capacity of 10,000 tons in 1914 The Industry recorded an exponential growth with the introduction of Cement BUREAU OF ENERGY EFFICIENCY, Government of India,
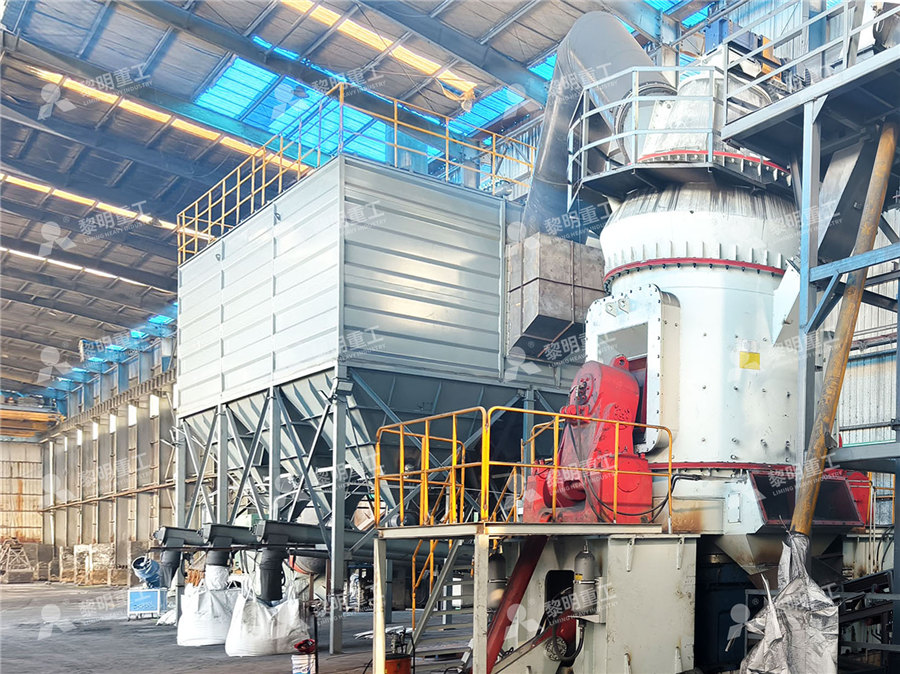
Energy efficiency of stateoftheart grinding processes
2018年1月1日 In times of unstable market development due to the energy system transformation and legislative measures concerning the reduction of CO 2 emissions, the manufacturing industry is increasingly aware of the ecological and economical importance of the factor energy A considerable share of industrial energy and resource consumption can be attributed to 2017年4月9日 Whereas the CCE of the three aforementioned options are the least, some other options were found to result in greater energy savings, albeit at a greater cost of conserved energy, for example, the implementation of an energy management and process control system to obtain energy savings of 71,20511 GJ per annum and conversion to dry multistage preheater Benchmarking energy utilization in cement manufacturing sharp decline in cement production over the last 15 years, from a peak of 262Mt in 2007 to 168Mt in 2017, equivalent to a reduction in cement per capita from 05 to 03 tonnes per person (3) The CO 2 intensity of cement production over that period has improved by about 7% (06t of CO 2 emitted per tonne of cement in 2017) (2)Deep decarbonisation of industry: The cement sector Europathe potential energy savings opportunity The costs associated with realizing these energy savings was not in the scope of this study The purpose of this data analysis is to provide macroscale estimates of energy savings opportunities for cement manufacturing subprocesses and sectorwide This is a step toward understanding the processes thatBandwidth Study on Energy Use and Potential Energy Saving
.jpg)
Energy and cement quality optimization of a cement grinding circuit
2018年7月1日 Many of the studies focussed on energy assessments of the cement industry to evaluate and then determine the possible energy savings These reports proved that savings varied between 20% and 50% was attainable by considering the optimization of the existing circuits, evaluation of the possible investments and the changes in the control 2022年12月1日 In the cement industry, the total energy consumption accounts for 50–60% of the overall manufacturing cost, while thermal energy accounts for 20–25% (Wang et al, 2009; Singhi and Bhargava, 2010)The modern cement industry requires 110–120 kWh of electrical power to produce one ton of cement (Mejeoumov, 2007)Thermal energy is used mainly during Review on energy conservation and emission reduction 2011年4月1日 Assuming these savings represent about 85% of the total savings from all 14 subsectors, net savings are about 106 Mtce (31 EJ) final energy and 129 Mtce (38 EJ) primary energy 31 When compared to the overall program goal of 118 Mtce (35 EJ) net energy savings in final energy, it appears that the program has saved an estimated 76% of the total goal in the Assessment of China's energysaving and emissionreduction about 49 PJ per year Per company this means annual savings of about 224 TJ In order to reach the saving of 1459 GJ in 2050 the sector would need to implement energy saving measures of about 38 PJ per year Per company this means annual savings of about 174 TJ In Chapter 48, the sectorspecific energy saving opportunities and measures are Benchmarking Report for the Cement Sector UNIDO
.jpg)
Best energy consumption International Cement Review
2015年2月16日 Grinding energy was approximately 50 per cent of the ball mill and the drying capabilities allowed direct processing of materials of up to 20 per cent moisture content The main energy issue was the high power consumption of mill fans, with pressure drops of 100mbar not uncommon with high nozzle ring velocities (>70m/s) and internal mill circulating loads of >1000 Audit report Energy performance improvement period Continuous improvement Energy performance (%) over an improvement period 5% Total energy cost saving over improvement 30 lakh USD Cost to implement EnMS Rs 6,40,000 per year The payback period of EnMS implementation year 034 years Total energy saving over an improvement period (GJ) 40,303 A Case Study on Evaluation of Energy Management System by Energy Efficiency Potential for China’s Cement Industry: A BottomUp TechnologyLevel Analysis 93 Table 1: Energy Savings and Costs for EnergyEfficient Technologies and Measures Applied to the Cement Industry No Technology/Measure Clinker Production Capacity in base year to which the measure is applied (Mt/year) Typical Fuel Savings (GJ/tcl)Energy Efficiency Potential for China’s Cement Industry: A2016年6月3日 7Ways to achieve energy saving in Cement grinding station power consumption can be reduced per unit of product 2, energy consumption between the three cement grinding energy saving, 7Ways to achieve energy saving in Cement grinding station
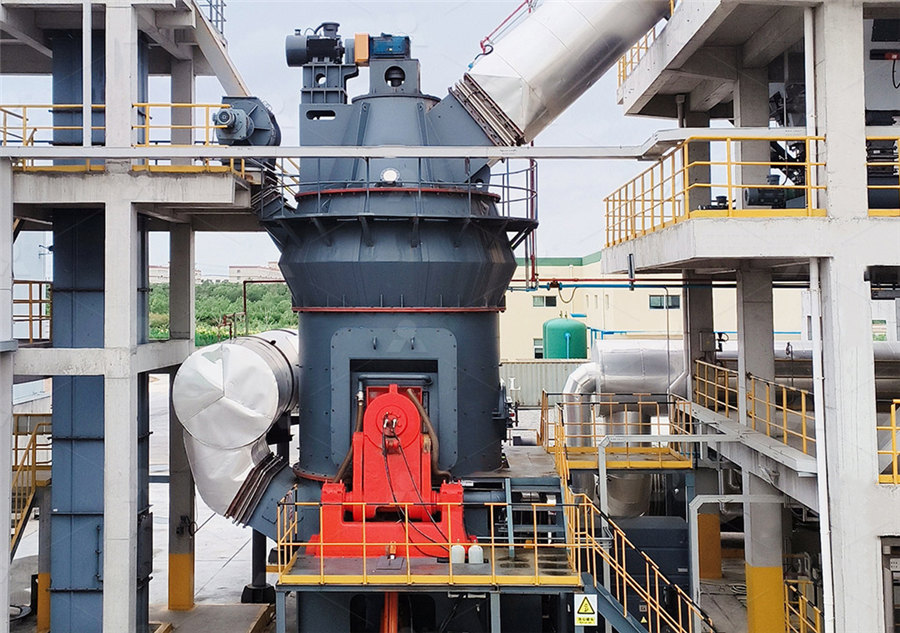
A comprehensive investigation of a grinding unit to reduce energy
consumption (SEC) per ton of cement produced and blocked 75,34337 tons of CO 2 emissions per year and reduced the cement production cost to 4047 $/ ton corresponding to a saving of $206 M per year It has been demonstrated that it is very important to keep the moisture content of raw materials used in the cement industry as low as possible 2020年3月1日 Manufacturing cement requires energy intensive processes; and consumes almost 15% of the total demand for energy in industry [3]On average, to produce one ton of cement, 34 GJ of thermal energy (in dry process) and 110 kWh of electrical energy are needed [4, 5]Furthermore, manufacturing a ton of cement releases 073–099 tons of CO2 [6] which A decision support tool for cement industry to select energy Figure 5 Final energy consumption in US cement production by fuel, 1970 to 2010 12 Figure 6 Primary energy intensity of US cement and clinker production, 1970 to 2010 13 Figure 7 Specific fuel and electricity consumption per ton of cement produced 14 Figure 8Energy Efficiency Improvement and Cost Saving Opportunities for Cement the potential energy savings opportunity The costs associated with realizing these energy savings was not in the scope of this study The purpose of this data analysis is to provide macroscale estimates of energy savings opportunities for cement manufacturing subprocesses and sectorwide This is a step toward understanding the processes thatBandwidth Study on Energy Use and Potential Energy Saving
.jpg)
Evaluation and mitigation of cement CO2 emissions:
2018年6月24日 The objective of this article is to describe China’s achievements in reducing cementrelated CO 2 emissions, mainly via energy efficiency improvements with respect to both fossil fuels and electricity consumption 2023年7月1日 The cement industry is one of the most energy and emissionintensive sectors, accounting for approximately 7% of totalindustrial energy use and 7% of global CO 2 emissions This study investigates the potential energy savings and CO 2 abatement in the cement plants of Ethiopia A Benchmarking and Energy Saving Tool for Cement is used to compare the energy Investigating energy saving and climate mitigation potentials in cement Cement Additives Division 1 Improvement of cement performances through the use of grinding aids in vertical roller mill PD’Arcangelo, MMagistri – Mapei SpA, Milan, Italy Abstract Due to the stringent requirement of energy saving, the use of vertical Improvement of cement performances through the use of grinding 2022年11月17日 Moreover, the electricity per ton of cement by country in 2018, which was directly collected from the International Energy Agency 79, was used to further compare the energy consumption and Modernizing cement manufacturing in China leads to substantial
.jpg)
An overview of energy savings measures for cement industries
2013年3月1日 The current global consumption of cement industry is about 15 billion tons per annum and is rising at almost 1% per annum Cement production requires approximately 110 kW h/t of electrical energy, with 40% directed to clinker grinding [26]Using real auditing, Avami and Sattari [17] investigated technological methods that would reduce the energy consumption, 2015年2月11日 As one of the most energy, emission and pollutionintensive industries, the production of ammonia is responsible for significant emissions of greenhouse gases (GHGs) and local air pollutants Although many energy efficiency measures have been proposed by Chinese government to mitigate GHG emissions and improve air quality, a less than full understanding Assessment of energysaving and emission reduction potentials in China nec = not elsewhere counted CIS = Commonwealth of Independent States BAT = energy intensity covers the process up to the liquid steel stage, ie it does not include energy used in casting and rolling, or energy used by captive thermal utilities (which are included in reported energy intensity)Electricity use per tonne of cement in selected countries and 2020年10月13日 The Global Cement Report 15th Edition Energy saving with separate fine grinding 13 October 2020 Advertisement Vietnam’s cement industry accounts for 17 per cent of the country’s fossil fuelderived CO 2 em Energy saving with separate fine grinding International Cement

Energy Efficiency Improvement and Cost Saving Opportunities for Cement
energy efficient technologies and measures and estimated energy savings, carbon dioxide savings, to make finished cement, or clinkergrinding plants that intergrind clinker obtained elsewhere, with between 05 and 31 million metric tons (Mt) per year Total production of US cement plants in 1997 was nearly 86 Mt, 2022年5月9日 Cement production is one of the most energyintensive manufacturing industries, and the milling circuit of cement plants consumes around 4% of a year's global electrical energy production It is Modeling of energy consumption factors for an industrial cement 2023年11月6日 The mode of action of GAs in improving the properties of cement is not fully understood []However, the proposed mechanisms are mostly pinned on two principles: first, the impact on particle distribution and material flow qualities; and second the chemical–physical influence on individual particles, for instance, surface energy reduction [21, 22]Review of the Effect of Grinding Aids and Admixtures on the 2022年11月27日 Once you have completed energy and exergy balance, identified the energysaving and carbon mitigation potential, proposed the solutions of energysaving and carbon mitigation, it is needed to have a technical and economic evaluation of energysaving projects, this chapter introduces the time value of capital, as well as the static evaluation method and Technical and Economic Evaluation of EnergySaving Measures
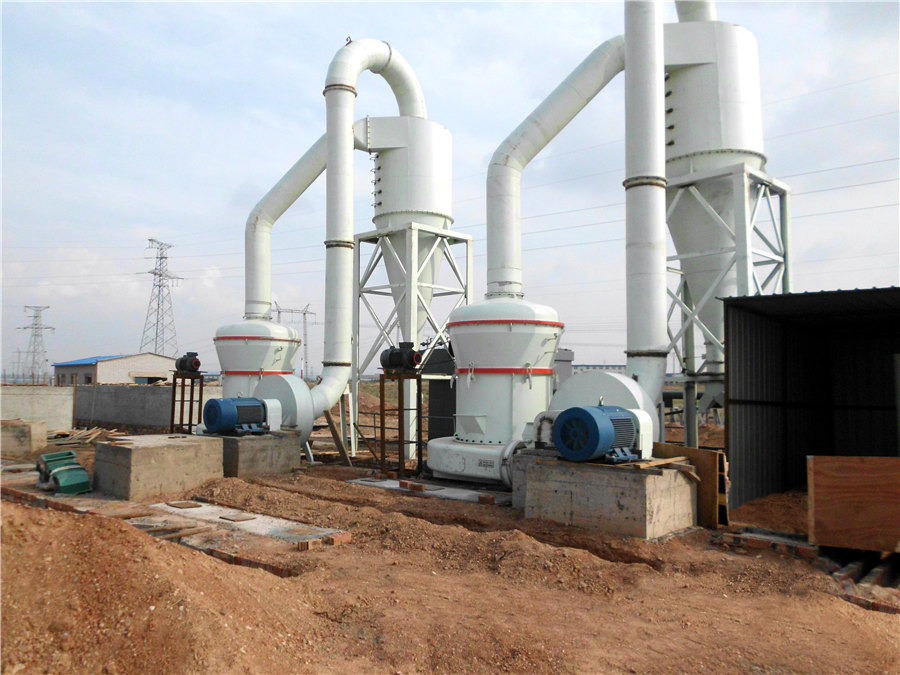
Potential energy savings and CO2 emissions reduction of China's cement
2012年6月1日 Cement production is highly energy intensive and the cement industry is one of the largest industrial energy consumers in China (CCA (China Cement Association), 2010, CCA (China Cement Association), 2011, NBS (National Bureau of Statistics), 2010a, Worrell et al, 2001)Because of the huge amount of cement output, China's cement industry accounts for 2020年2月15日 The plant current production capacity is about 770 tons of cement per day, and it has been growing dramatically during recent years as a result of the growing demand for cement in the country The cement production in the MCC plant is based on the dry process technology, and according to the preliminary energy audit, the thermal energy consumption in MCC is Parametric Studies of Cement Production Processes John 2020 MIDLAND, Mich, Oct 6, 2021 /PRNewswire/ Dow (NYSE: DOW) announced today that it has signed eight new renewable power purchase agreements (RPAs) spanning Europe and the AmericasThe power supplied by the new agreements is expected to reduce Dow's scope 2 emissions by more than 600,000 metric tons of CO2e per yearDow adds eight new renewable power agreements, reducing 2015年2月1日 The cement industry, as a pillar of Chinese economic development, has grown rapidly alongside the national economy Cement production has increased dramatically from 6524 million tons in 1978 to 2099 million tons in 2011, with an average annual growth rate of 1108% (NBSC, 2013)Up to 2011, China has been the largest cementproducer in the world Evaluation of energy saving potential in China's cement industry
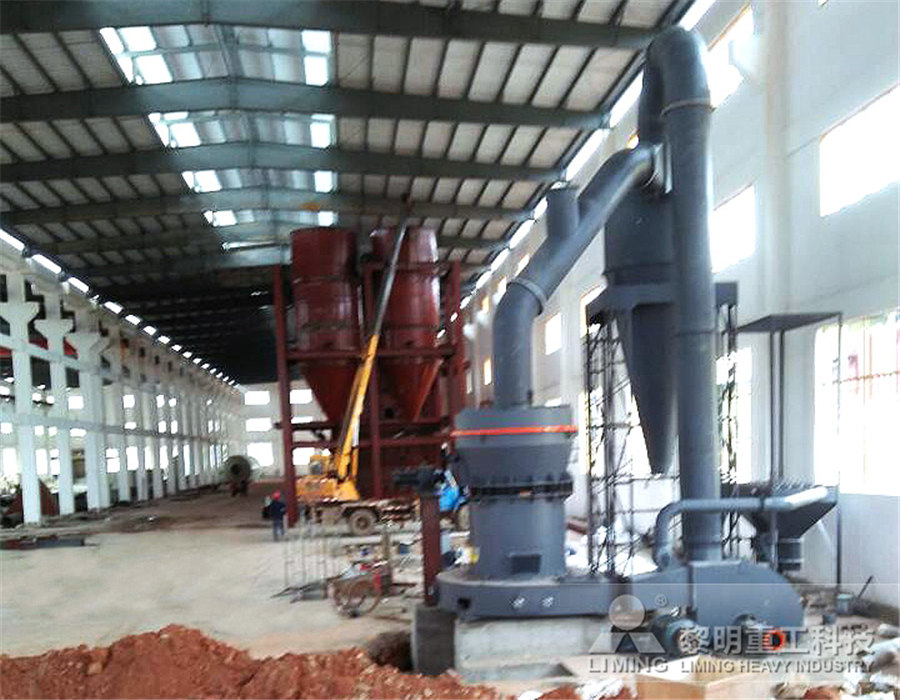
Conceptual design and lifecycle environmental and economic
2024年9月15日 The cement production process generally includes ore mining, raw material pretreatment and grinding, raw meal firing to clinker, clinker grinding, cement product storage and transport Among these steps, raw meal firing to clinker is a process that presents coupling, hysteresis, and strong nonlinearity, making modeling a great challenge ( Mungyeko Bisulandu 2009年10月1日 Plant energy use was compared to both domestic (Chinese) and international best practice using the Benchmarking and Energy Saving Tool for Cement (BESTCement) This benchmarking exercise indicated an average technical potential primary energy savings of 12% would be possible if the surveyed plants operated at domestic best practice levels in terms of Analysis of EnergyEfficiency Opportunities for the Cement