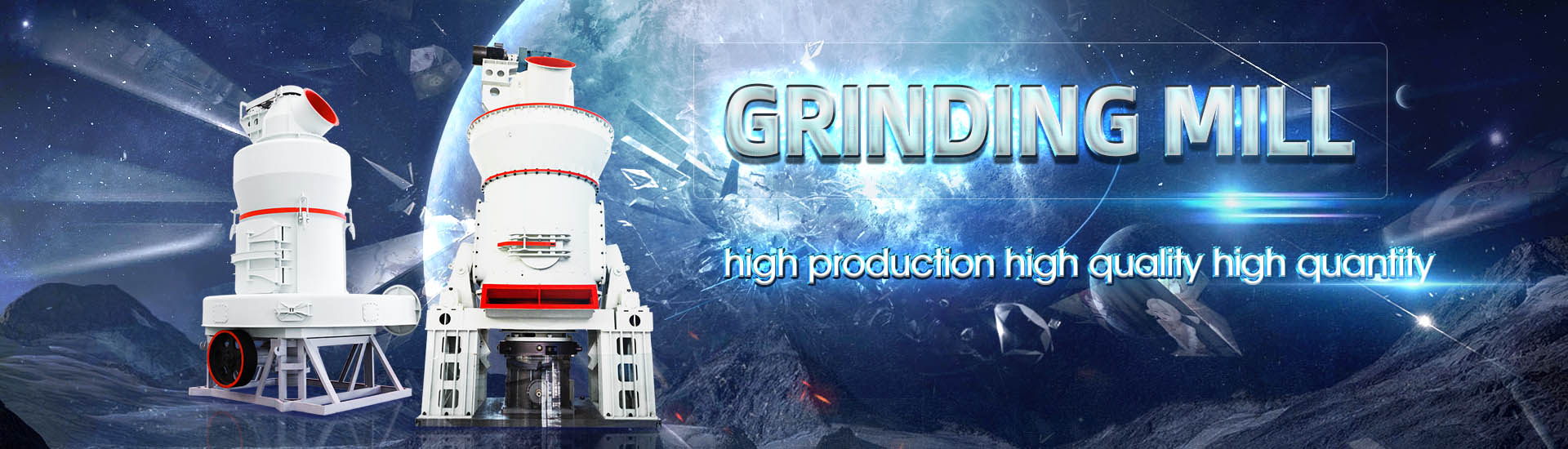
Coal mill insulation Coal mill insulation Coal mill insulation
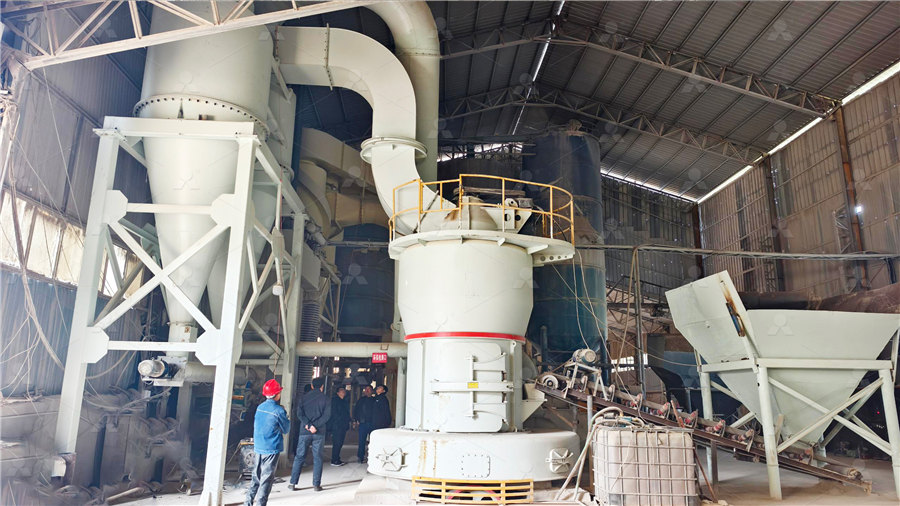
CHALLENGE Parker Hannifin Corporation
the cyclical operation of the coal mill circuit promote the formation of sulfuric acid which then corrodes exposed metal inside the dust collector and ductwork Keeping the metal and filtered 2020年4月5日 Among them, the superior performance and wide application of the heat insulation materials have attracted the attention of the coal mining Foundation Research on Physicochemical Properties of The invention also discloses a method for using the sound insulation device for sound insulation The sound insulation device has the advantages of good sound insulation and sound Sound insulation device suitable for coal mill and methodA sound insulation device suitable for a coal mill includes a steel structure sound insulation skeleton, a sound insulation cover is fixedly arranged on the steel structure sound insulationCNA Sound insulation device suitable for coal mill and
.jpg)
Preparation and characterization of highstrength insulating
2024年9月1日 Coal Mine Waste (MW) and Red Mud (RM) is used to develop IS:2042 standard insulation brick Rice husk (RH) is used as fugitive material for tailoring the porosity Effect of Coal mills or pulverizers play a very essential part in the coalfired power production system Coal mills grind the coal into fine powder, and the primary air entering the mill dries and drives the Coal Mill an overview ScienceDirect Topics2017年3月13日 A new cable insulation online monitoring based on pattern recognition is proposed, in case singlephase grounding fault in coal mine Firstly, using the pattern Highvoltage cable insulation online monitoring in coal mine A technology for coal mills and sound insulation, which is applied in the direction of soundgenerating equipment, layered products, and grain processing It can solve problems such as Sound insulation device suitable for coal mill and method
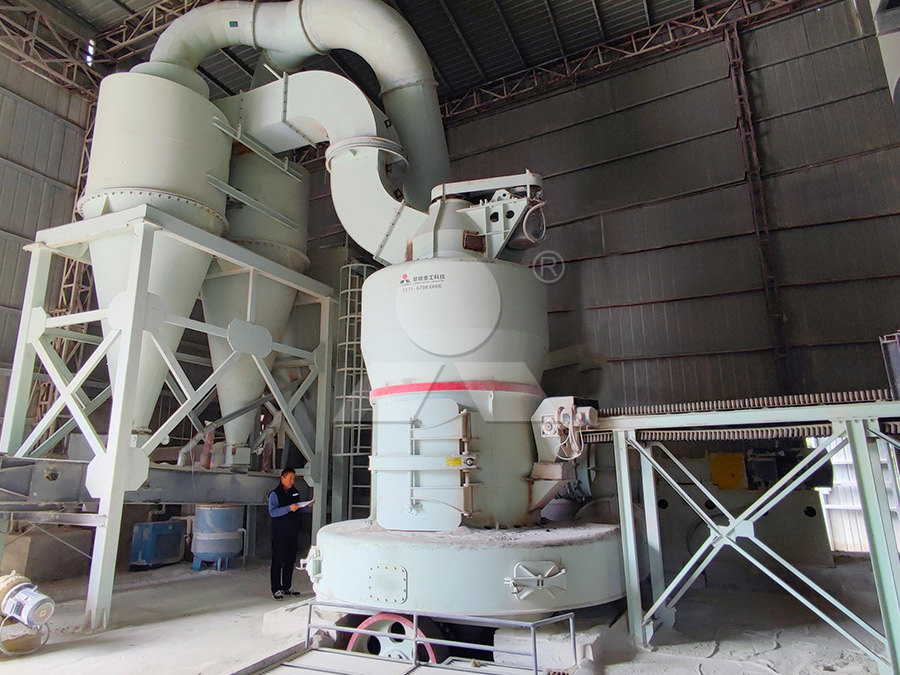
Coal mill, gypsum mill, clay mill, etc Pfeiffer MPS mills
MPS vertical mill from Pfeiffer is the ideal allrounder Grinding of coal, petcoke, clay, limestone, quicklime, gypsum, and many other materialsration of coal mills in different stages (crushing of coal – CC or mixing of coal with biomass – MCB) – Fig 1 Considering the case of a power plant where a significant increase in the Analysis of the effectiveness of solutions to reduce coal mill coal mill Free download as Powerpoint Presentation (ppt), PDF File (pdf), Text File (txt) or view presentation slides online This document discusses maintenance of coal mills and coal feeders Key points include: Maintenance Coal Mill PDF Mill (Grinding) TroubleshootingCoal and mill Free download as PDF File (pdf), Text File (txt) or view presentation slides online The document discusses pulverized coal mills used in power plants It describes different types of mills including tube mills, ball mills, Coal and Mill PDF Mill (Grinding) Mechanical
.jpg)
In discussion Vincent Grosskopf, Coal Mill Safety Global
2019年2月1日 Vincent Grosskopf has more than 45 years of experience in bulk material handling, particularly regarding the safety of coal grinding systems As the founder of Coal Mill Safety, he acts as a consultant to those seeking to design and build safe greenfield coal grinding systems or improve existing installations2020年8月12日 In a power plant, the coal mill is the critical equipment, whose effectiveness impacts the overall power plant efficiency Uniform coal feeding mass flow rate and required particle size and temperature at the outlet channel throughout with better classifier performance are crucial indicators that characterize the coal mill performanceAn investigation of performance characteristics and energetic 2020年4月7日 Monitoring and diagnosis of coal mill systems are critical to the security operation of power plants The traditional datadriven fault diagnosis methods often result in low fault recognition rate or even misjudgment due to the imbalance between fault data samples and normal data samples In order to obtain massive fault sample data effectively, based on the Modeling of Coal Mill System Used for Fault Simulation MDPICan GE service my boiler mills? YES Our boiler mills and coal pulverizers span the globe and are built in a variety of sizes and capacitiesWe provide customized maintenance solutions, and offer a full spectrum of highquality solutions for each—in addition to our thousands of standard boiler mill parts and boiler service solutionsThis is the Power of YesBoiler Mill and Coal Pulverizer Performance GE Steam Power
.jpg)
(PDF) MPS mills for coal grinding ResearchGate
2014年1月1日 The emission factors of kiln end, kiln head, coal mill, crushing and cement mill was 0156 clinker g/t, 3914 clinker g/t, 1538 coal g/t, 0016 stone g/t and 0056 cement g/t respectively, the 2015年11月1日 As presented by Andersen et al (2009) and Odgaard, Stoustrup, and Mataji (2007), coal moisture imposes limit on the maximum load at which a coal mill can be operated and the load gradient (how fast the mill may change its operating point), if it is desired that the pulverized coal entering the furnace has moisture content less than or equal to a certain value A unified thermomechanical model for coal mill operation2009年1月1日 This newlydeveloped coal mill model provides a valuable tool that can be used to improve the pulverizer design and optimize unit operation For example, reject coal rate, CFD Modeling of MPS Coal Mill for Improved Performance and SafetyHP coal mill adopts a new type of spiral bevel gear and planetary gear twostage reduction vertical transmission at which is convenient for maintenance, heat insulation and sealing 132 HP coal mill adopts mature roller surfacing technology and large diameter tapered roller For general coal, the design life of grinding roller is HP Bowl type millspower plant equipment

Coal Mill PDF Combustion Chemistry
Coal Mill PPT Free download as Powerpoint Presentation (ppt / pptx), PDF File (pdf), Text File (txt) or view presentation slides online The document provides an overview of coal mill operation, protections, and interlocks It discusses 2021年8月1日 Yukio et al [7] proposed a model consisting of blending, grinding and classifying processes for pulverizer control Agarawal et al [8] differentiated coal powder into ten size groups, divided the bowl mill into four zones, and developed a unified model Palizban et al [9] derived nonlinear differential mass equations of raw coal, recirculation coal and suspension coal in Coal mill model considering heat transfer effect on mass A Study on 500 MW Coal Fired Boiler Unit’s Bowl Mill Performance through Coal Sampling and Characterization: CPRI’s Experience M G Anandakumar* and M Venkateswara Rao Training Division, Central Power Research Institute, Bengaluru , Karnataka, India; mgananda@cpri ISSN (Print) : 09730338 Vol 18(2)/165170, December 2022A Study on 500 MW Coal Fired Boiler Unit’s Bowl Mill Figure 1NUMERICAL AND EXPERIMENTAL INVESTIGATION OF A PULVERIZED COAL MILL
.jpg)
Preparation and characterization of foamed ceramics from coal
2023年3月1日 from coal bottom ash for construction insulation materials Mingkai Zhou 1 and Xuexiang Ge 1,2, ³ 1 School of Materials Science and Engineering, Wuhan Univ ersity of Technology , Wuhan , China2020年4月2日 represent the temperature distribution in the boiler while PCs pipes at level 1 are not in service In the meanwhile, the others PC still in service and produced 700MWnettAnalysis of the Coal Milling Operations to the Boiler ParametersSafe operation of coal grinding systems: Raw coal silo protection against fire and explosions Safe operation of coal grinding systems: Raw coal yard management The purchasing process for coal grinding systems needs changes Talk at a virtual seminar, November 2023 Accept the probability that the fire and explosion safety of your coal grinding system is nothing more than a mirageOptimisation of coal mill systems, with fire and explosion and energetic efficiency of vertical roller coal mill Mehmet Tontu To cite this article: Mehmet Tontu (2020): An investigation of performance characteristics andAn investigation of performance characteristics and energetic
.jpg)
Coal Mill PDF Mill (Grinding) Industries
Coal Mill Free download as PDF File (pdf), Text File (txt) or view presentation slides online This dissertation examines technologies to enhance the maintenance performance of coal pulverizers through new technologies It presents the results of testing modifications to rotating throat assemblies, spider and guide wear plates, ball loading cylinders, classifier cones, and MILL Bag filter yang ada di unit coal mill memiliki komponen – komponen utama sebagai berikut : Inlet outlet duct, top box lid, Inlet outlet damper, hoist, w eather enclosure, purge tube dan venturi compressed air manifold, filter casing, hopper, distribution screen, insulation, crew conveyor, kantongANALISIS EFISIENSI TEORETIS KONDISI FABRIC FILTER DI UNIT COAL MILL Coal mills, essential components in power generation and various industrial processes, pose significant safety risks if not properly managed These mills, used to grind coal into a fine powder for combustion, present potential hazards such as fire, explosion, and mechanical failures This article outlines best practices and precautions to ensure thBest Practices and Precautions Coal Mill Safety, Explosion and Mill output at raw coal moisture and at Coal HGI 100110 31 Fineness Requirement 32 Duocast Roll Roller Setting 34 Throat Velocity 35 36 Mill Gear Box 37 Mechanical face Seal 38 • Insulation survey • Furnace temperature survey • Boiler Efficiency TestsPulverizer Plant OM Aspects
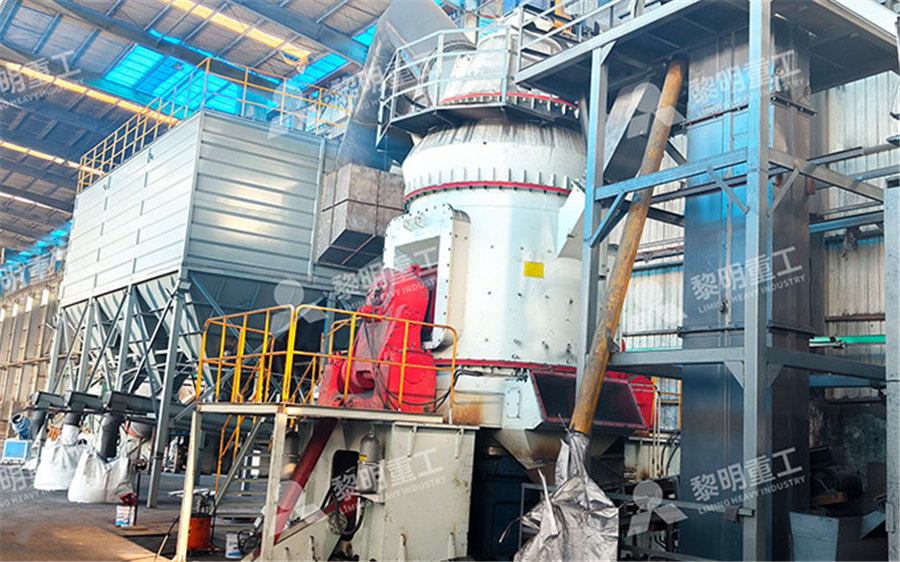
Development of Millburner System for Lowrank Coal with Super
Coal Very highmoisture coal Very highmoisture coal Mill Total moisture in raw coal 55% 45, 50, 55% Inlet gas temperature 450°C up to 450°C Outlet gas temperature 75°C 67 to 75°C Outlet relative humidity 85% 47 to 94% Figure 3 shows the relationship between relative humidity and the drying ratio fraction of pulverized coal2009年9月20日 A control oriented model was then developed by Fan (1994) and Fan and Rees (1994) In 2009, coal flow and outlet temperature of mill were modelled using mass and heat balance equations for startup Modeling and Parameter Identification of Coal Mill2013年6月9日 3 insulation 4 piping ( critical and internal) 5 LOS ( Lub oil supply unit) 6 Motorised valves and dampers 7 ( connection between Raw Coal Feeder and Mill) After coal reaches Mill bowl grinding started and hot air also been given to make the pulverised fuel dried enough to classifierMILLS IN A THERMAL POWER STATION PART I2007年8月20日 This paper presents a multisegment coal mill model that covers the whole milling process from mill startup to shutdown This multisegment mathematical model is derived through analysis of energy transferring, heat exchange, and mass flow balances The work presented in the paper focuses on modeling Etype vertical spindle coal mills that are widely used in coal Development of a Multisegment Coal Mill Model Using an
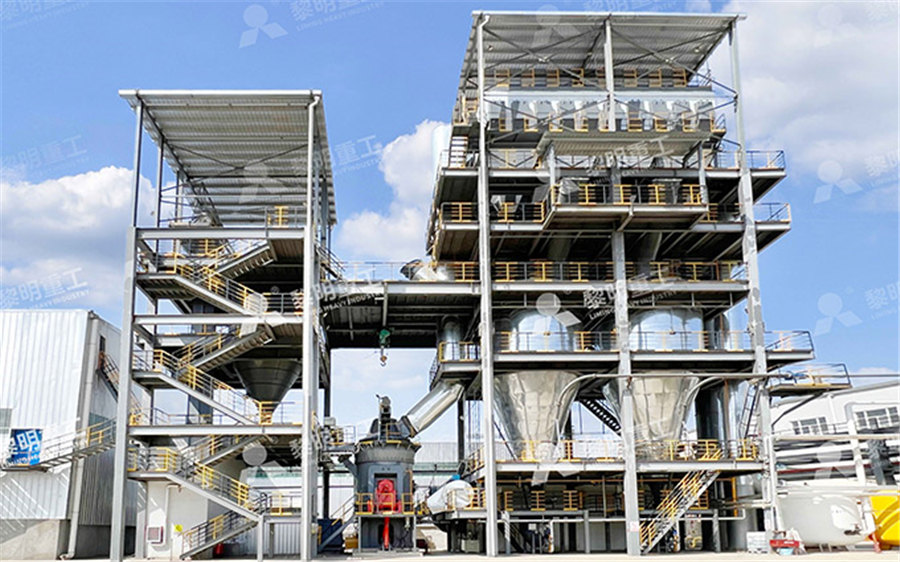
AirSwept Coal Mill of High Quality Fote Machinery
Coal Mill is the main equipment of the rotary kiln cement clinker production system and at the same time, The original insulation layer of the hot air duct from the outlet of the hightemperature fan to the inlet of the coal mill is thin and mostly Coal Mills Free download as Powerpoint Presentation (ppt), PDF File (pdf), Text File (txt) or view presentation slides online This document discusses performance tests conducted at a coal power plant to optimize operations It describes tests done on coal mills and other equipment to analyze performance and efficiency These include air flow tests, efficiency tests, and tests to Coal Mills PDF Thermal Insulation Mechanical Engineering2010年5月1日 Mill performance not only influences its own internal operation and but also affects the combustion performance of the furnace Indicators of combustion performance, NO x, CO, unburned carbon, slagging, fouling, flame stability and boiler capacity are directly altered by mill outputBurners and other allied combustion equipments are designed with the assumption CFD modeling of MPS coal mill with moisture evaporationFrom the coal yard, the coal is transfer to the mill bunkers through conveyor belt The bunkers are sized for an effective capacity of twelve (12) hours at BMCR with design coal Each mill bunker has one hopper, connected to the feeders Mills operate when the bunker coal gate valves are opened, coal is allowed to flow to the gravimetric feedersAnalysis of the Coal Milling Operations to the Boiler Parameters
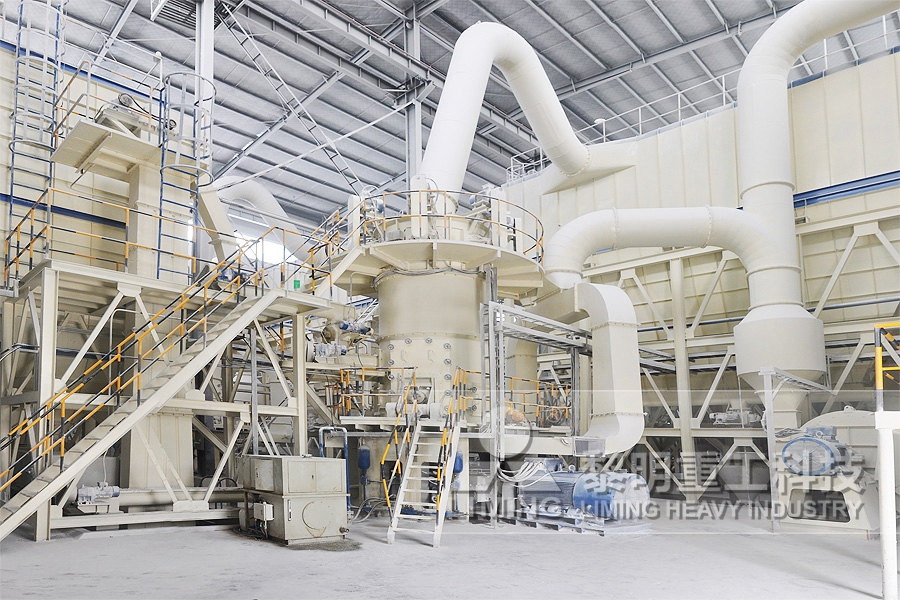
Coal pulverizer mill system modeling for failure simulation
2023年5月8日 In this study, a coal pulverizer mill simulation was carried out with dynamic modeling to analyze mass flow rate, heat transfer, and energy balance to overcome these problems Dynamic modeling simulations are carried out using Matlab software by Bowl Mill, Coal Pulverizer Mill, Raymond Mill, Bowl, Bowl Hub, Vertical Shaft, Worm Shaft, Mill Base Plate, Insulation Cover plate Hub, Grinding Rolls, Tyre Roller for Power Plant, Raw Coal Pulverizer Spare parts, Dynamic Classifer, Vertical Mills Ring Roller Coal Pulverizer DuoCast Coal Very highmoisture coal Very highmoisture coal Mill Total moisture in raw coal 55% 45, 50, 55% Inlet gas temperature 450°C up to 450°C Outlet gas temperature 75°C 67 to 75°C Outlet relative humidity 85% 47 to 94% Figure 3 shows the relationship between relative humidity and the drying ratio fraction of pulverized coalDevelopment of Millburner System for Lowrank Coal with Super MILL Bag filter yang ada di unit coal mill memiliki komponen – komponen utama sebagai berikut : Inlet outlet duct, top box lid, Inlet outlet damper, hoist, w eather enclosure, purge tube dan venturi compressed air manifold, filter casing, hopper, distribution screen, insulation, crew conveyor, kantongANALISIS EFISIENSI TEORETIS KONDISI FABRIC FILTER DI UNIT COAL MILL
.jpg)
TPS Coal Mills and Fan Performance PPT SlideShare
2019年5月8日 7 Maintenance Strategy Maintenance Significant Item Inspection / Execution Task Coal Measure HGI (hard grove index), moisture content, abrasiveness and size of coal fed to mill Pulverised fuel (PF) Measure particle size distribution, PF velocity and temperature Grinding media (Balls and Rings) Measure ball diameter, ring depth profile and material Coal grinding mills are essential components of power plants, responsible for converting raw coal into fine coal powder that is essential for efficient combustion in power plant boilers Coal grinding mills can also be used to grind biomass and other alternative fuels, providing a more sustainable and renewable energy source for power generationWhat is a Coal Grinding MillA control oriented model was then developed by Fan (1994) and Fan and Rees (1994) In 2009, coal flow and outlet temperature of mill were modelled using mass and heat balance equations for startup Sectional view of MBF coal mill Download Scientific Diagram2023年2月1日 Additives provide substantial improvement in the properties of composites Although biobased composites are preferred over synthetic polymer and metalbased composites, they do not have the requisite properties to meet specific needs Hence, organic, inorganic and metallic additives are included to improve the properties of biobased Natural subbituminous coal as filler enhances mechanical, insulation
.jpg)
010Method Statement of Coal Mill Instattalation PDF Scribd
010Method Statement of Coal Mill Instattalation Free download as Word Doc (doc), PDF File (pdf), Text File (txt) or read online for free This document provides a method statement for installing a coal mill at a project site It outlines the general components and purpose of the coal mill It then describes the responsibilities of personnel overseeing the installationMill no 4 coal flow measured was 80,21 t/h; infiltration of air into the mill and the coal feeder of the mill have values up to 0,892; regarding the smoothness of grinding: rest on sieve 009, with an average value of 61,32%, exceeds the limit imposed STUDY ON THE ENERGY BALANCE OF COAL MILLS FOR ENERGY