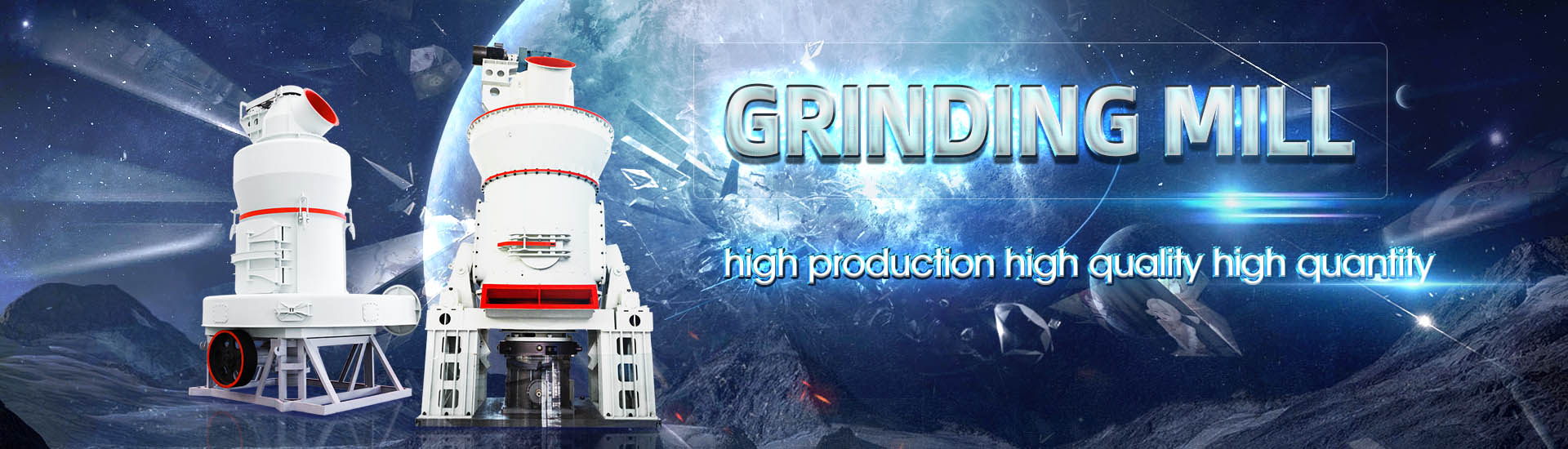
Desulfurization process Mixed limestone
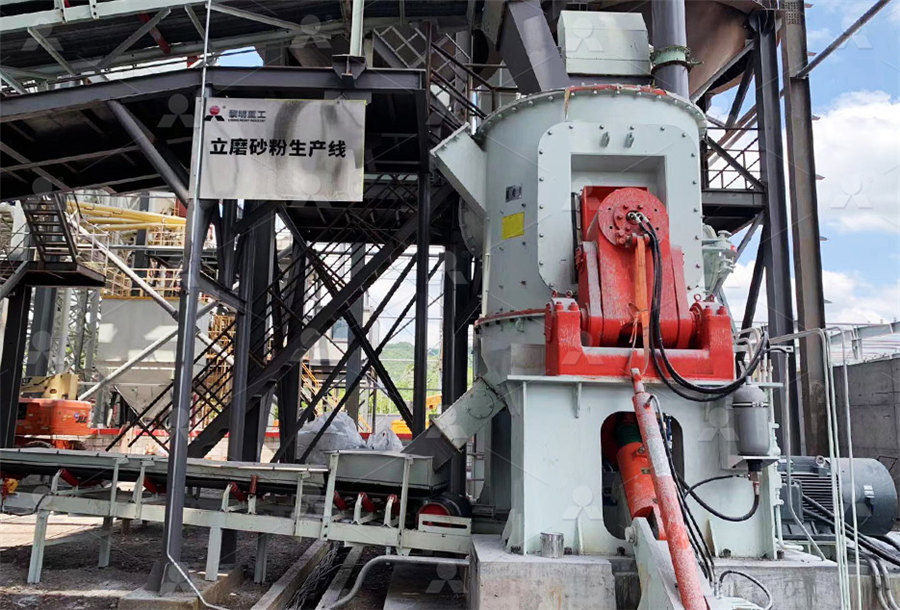
Desulfurization characteristics of limestone slurry with added
2023年3月15日 A desulfurization reaction was performed in bubbling reactor to investigate the effect of six different organic acid additives on improving desulfurization in the limestone slurry The newly developed dry desulfurization processes including source/end control technologies and the various dry desulfurization materials including Calcium/Magnesium/Sodium/Carbonbased Recent advances in process and materials for dry desulfurization of The most common commercial process for SO 2 removal from flue gas is wet limestone flue gas desulfurization, in which sulfite oxidation represents an important limiting phenomenon A LimestoneGypsum Flue Gas Desulfurization Process: Modeling of 2024年8月13日 Limestone Preparation: Limestone (CaCO 3) can be delivered to site by truck or rail The limestone is then typically crushed and/or milled, mixed with water to form a limestone Flue Gas Desulfurization: Detailed Process Overview
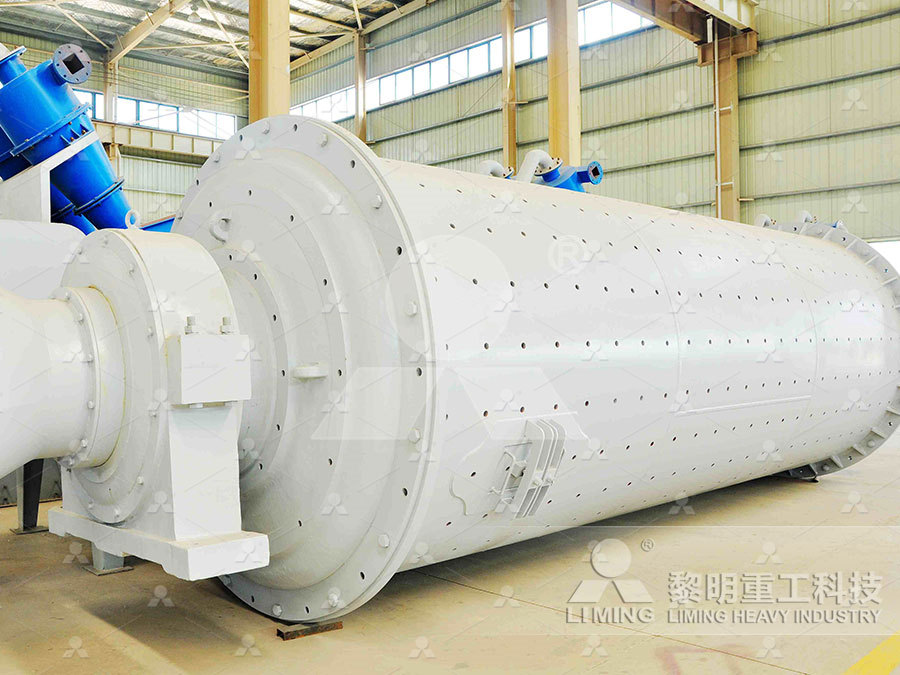
Lime / Limestone Wet Scrubbing System for Flue Gas Desulfurization
Wet scrubbers are used in utilities, paper mills, and chemical plants to remove sulfur dioxide (SO 2) and other pollutants from gas streams Undesirable pollutants are removed by contacting 2020年11月24日 In the present study, the limestone dissolution operated within the Wet Flue Gas Desulfurization (WFGD) process conditions is contrasted successfully against experimental dissolution assays For this technology, Modeling of Limestone Dissolution for Flue Gas 2005年12月7日 This work presents a practical result of experimental investigation of the limestone particle size effect on deSO x from a circulating fluidized bed combustion (CFBC) Desulfurization with a Modified Limestone Formulation in an 2001年5月19日 A detailed process model of the wet limestone flue gas desulfurization system has been presented This model can be used to calculate indispensable parameters for Model of the Wet Limestone Flue Gas Desulfurization Process for
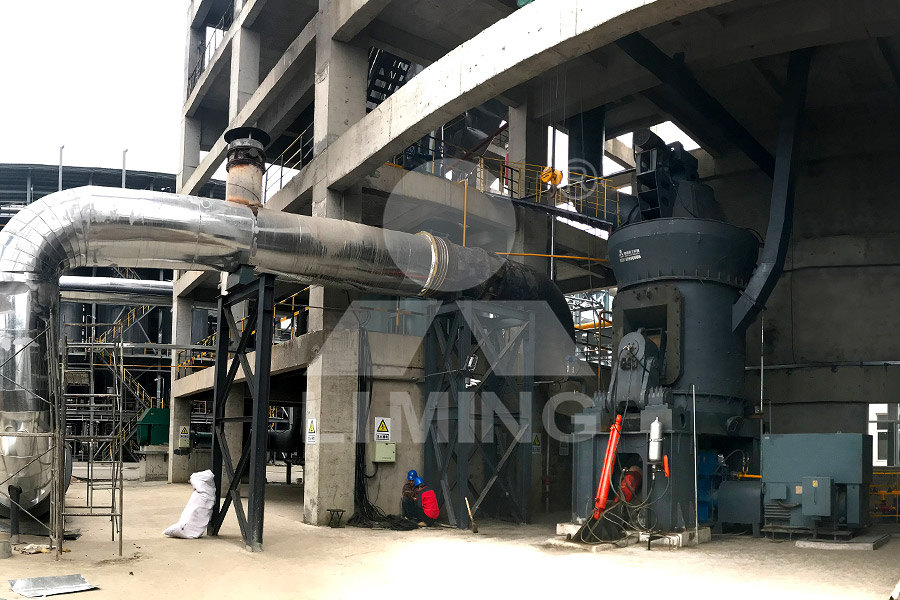
Applications of Ultrafine Limestone Sorbents for the
2019年10月29日 Therefore, in this paper, the application of natural ultrafine limestone, with a Sauter mean diameter of less than 20 μm, was tested by conducting benchscale, pilotscale, and commercialscale experiments to 2021年11月1日 Flue gas desulfurized gypsum mainly comes from thermal power plants, smelters, and largeenterprise boilers, and contains industrial byproducts produced through a wet desulfurization combustion process, where SO 2 gas and lime slurry react under strong oxidation conditions The main component of this gypsum is calcium sulfate dihydrate, which also Production and resource utilization of flue gas desulfurized 2021年10月1日 With the increasingly stringent emission standards of flue gas, a demonstration project of desulfurizing by “red mudlimestone process” was established to make the flue gas meet the Emission Standards of Pollutants for Aluminum IndustryAs shown by the detection results, the emission concentration of Sulfur dioxide (SO 2) was less than 50 mg/m 3, and the Research on red mudlimestone modified desulfurization mechanism and 2024年1月10日 Flue gas desulfurization (FGD) is a critical process for reducing such as limestone (calcium A Modeling and optimization of CO 2 capture into mixed MEAPZ amine solutions using machine Modeling based on machine learning to investigate flue gas
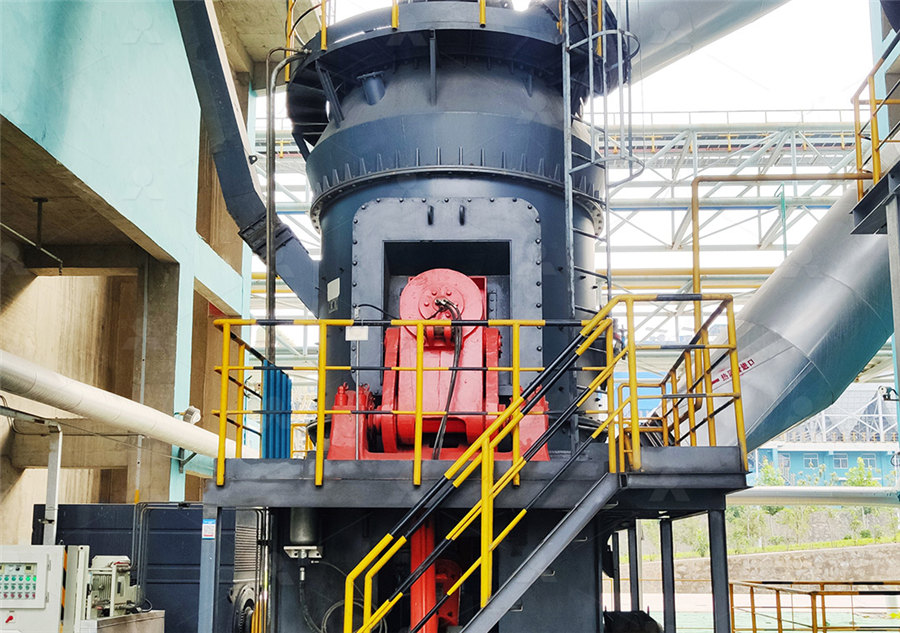
Fluegas desulfurization Wikipedia
Before flue gas desulfurization was installed, the emissions from the Four Corners Generating Station in New Mexico contained a significant amount of sulfur dioxide The G G Allen Steam Station scrubber (North Carolina) Fluegas desulfurization (FGD) is a set of technologies used to remove sulfur dioxide (SO 2) from exhaust flue gases of fossilfuel power plants, and from the 2017年2月13日 In this paper, waste gypsum from wet flue gas desulfurization (WFGD) mixed with NH3H2O was applied for CO2 absorption in the solidliquidgas phase system The effects of operation temperature, CO2 flow rates, and ammoniatogypsum ratio on carbonation process were discussed Meanwhile, a model for CO2 absorption in the suspension of WFGD gypsum Carbonation of gypsum from wet flue gas desulfurization process Dry desulfurization can be mainly divided into source control technology and end treatment technology from the process segment Compared to the traditional wet/semidry desulfurization process, dry desulfurization has the characteristics of simple operation and low equipment investment, which has recently been widely used in industryRecent advances in process and materials for dry desulfurization 2020年11月24日 Examples are illustrated here in relation to limestone dissolution taking place within the Wet Flue Gas Desulfurization process, where calcium carbonate is dissolving in an acidic environment The method is the most common used technology to abate SO2 released by fuel combustion Limestone dissolution plays a major role in the processModeling of Limestone Dissolution for Flue Gas Desulfurization
.jpg)
Recent advances in flue gas desulfurization gypsum processes
Flue gas desulfurization gypsum (FGDG) is an industrial byproduct generated during the flue gas desulfurization process in coalfired power plants Due to its abundance, chemical and physical properties, FGDG has been used in several beneficial 2019年10月29日 Request PDF Applications of Ultrafine Limestone Sorbents for the Desulfurization Process in CFB Boilers With the stringent emission regulation taking effect, it is difficult for the Applications of Ultrafine Limestone Sorbents for the Desulfurization 2024年3月20日 Desulfurization wastewater is industrial wastewater with a high salt content, high metal ions, and high hardness produced by flue gas desulfurization of the limestonegypsum method in coalfired power plants This paper summarizes the source of desulfurization wastewater, water quality characteristics, water quality impacts, and other factors, combined Current Status of Zero Liquid Discharge Technology for Desulfurization 2020年5月16日 Numerous mitigation techniques have been incorporated to capture or remove SO2 with flue gas desulfurization (FGD) being the most common method Regenerative FGD method is advantageous over other methods due to high desulfurization efficiency, sorbent regenerability, and reduction in waste handling The capital costs of regenerative methods are Sulfur dioxide removal: An overview of regenerative flue gas
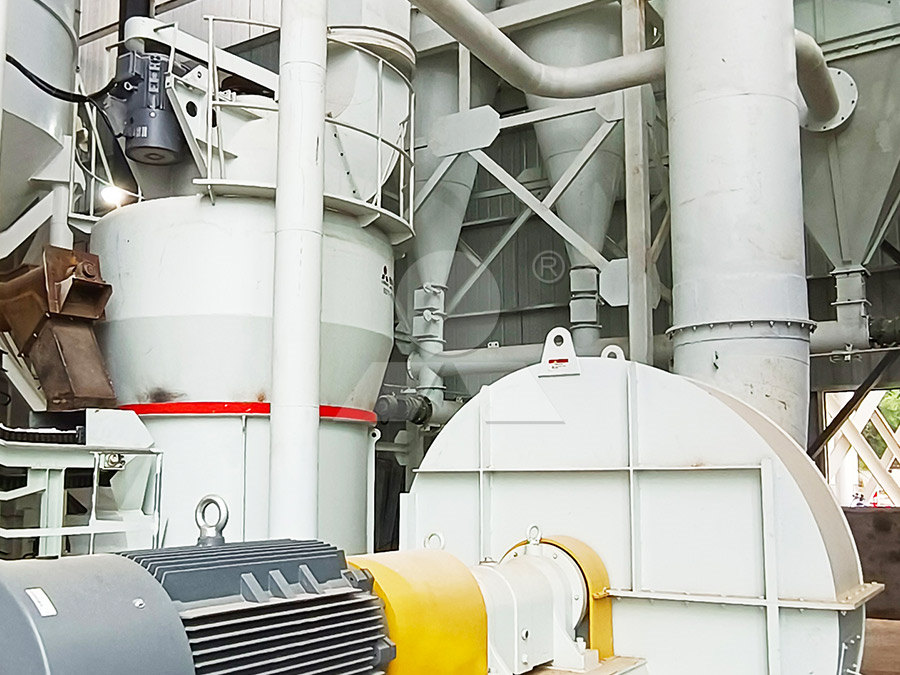
Condensable Particulate Matter Removal and Its Mechanism by
2024年11月18日 Limestonegypsum wet flue gas desulfurization (WFGD) played a key role in SOx removal and clean emissions However, it would also affect the condensable particulate matter (CPM) removal and compositions The effects of the WFGD system on the removal of CPM and the contents of soluble ions in CPM were investigated in a spray desulfurization LimestoneGypsum Flue Gas Desulfurization Process: Modeling of Catalyzed Bisulfite Oxidation Giuseppe Mazziotti di Celso*a, Despina Karatzab, Amedeo Lanciac, Dino Musmarrab, Marina Prisciandarod aDipartimento di Scienze degli Alimenti, Università degli Studi di Teramo, Via Carlo R Lerici, 64023 Mosciano S Angelo (TE), ItalyLimestoneGypsum Flue Gas Desulfurization Process: Modeling 2012年1月1日 This paper attempts to explore the effect of red mud (two kinds of Bayer process red mud and one kind of sintering process red mud) from alumina plant on desulfurization performance and microstructure of limestone, in order to explore the factors to affect modified limestone’s desulfurization activity and get an optimal approach to improve desulfurization Experimental Study and Mechanism Analysis of Modified Limestone 2001年5月19日 A detailed process model of the wet limestone flue gas desulfurization system has been presented This model can be used to calculate indispensable parameters for estimating costs and next to minimize capital and operating costs The process model describes most important stage of SO2 removal running in an absorber and a holding tank It includes Model of the Wet Limestone Flue Gas Desulfurization Process
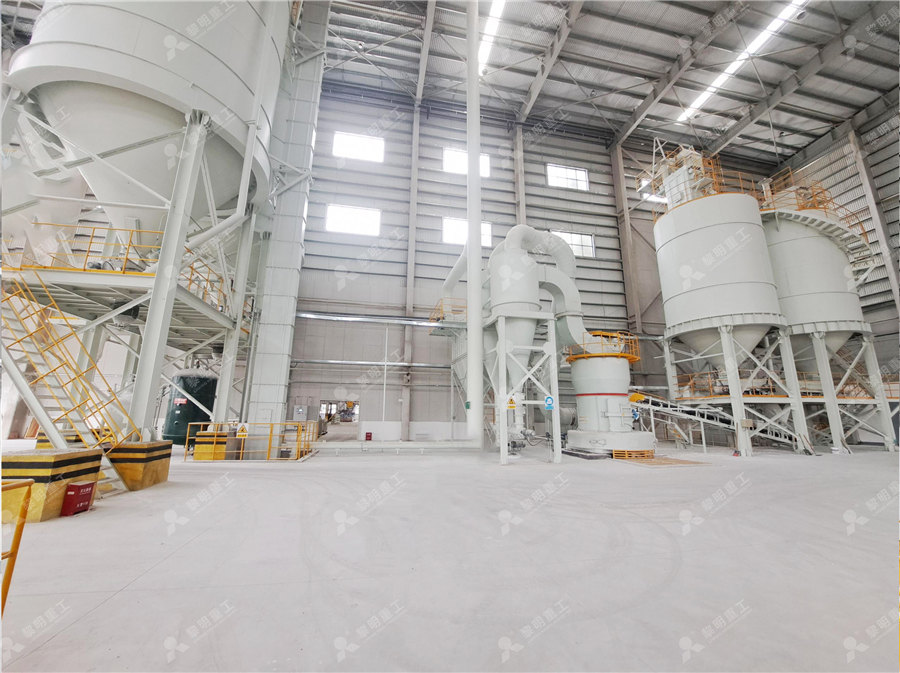
Enhancing the recovery of gypsum in limestonebased wet flue
2017年7月1日 Among the reasons for the success of the wet FGD system, there is the possibility of recovering a new product to be allocated on the market namely gypsum (He and Lee, 2014)In fact, the synthetic gypsum suitable for several applications such as wallboard manufacturing is the byproduct of the SO 2 scrubbing process for scrubbers using lime or 2015年7月27日 3 Flue Gas Desulfurization Technologies Flue gas desulfurization is an efficient method for the reduction of the sulfur dioxide emissions Citation 2 Many processes are available in the market, such as (a) wet scrubbers, (b) spray dry scrubbers, (c) sorbent injection, (d) regenerable processes, and (e) combined SO 2 /NO X removal processes The different flue Review of Design, Operating, and Financial Considerations in Schematic PFD of a limestonebased wet FGD process Specific issues include the degree of desulfurization that the process can offer as well as its flexibility 2019) for untreated and treated (fluegas desulfurisation) BR, mixed with 50 wt% Class C or Class FFA (cured at 20 °C) Read more View articleFlueGas Desulphurization an overview ScienceDirect Topics2019年12月1日 According to the US Energy Information Administration's statistics, in the 2006–2016 period, approximately 42% of the electricity consumed in the USA was produced by coal combustion (US Energy Information Administration, 2018)The coal combustion process generates various types of residues such as fly ash, bottom ash, boiler slag, flue bed Recent advances in flue gas desulfurization gypsum processes
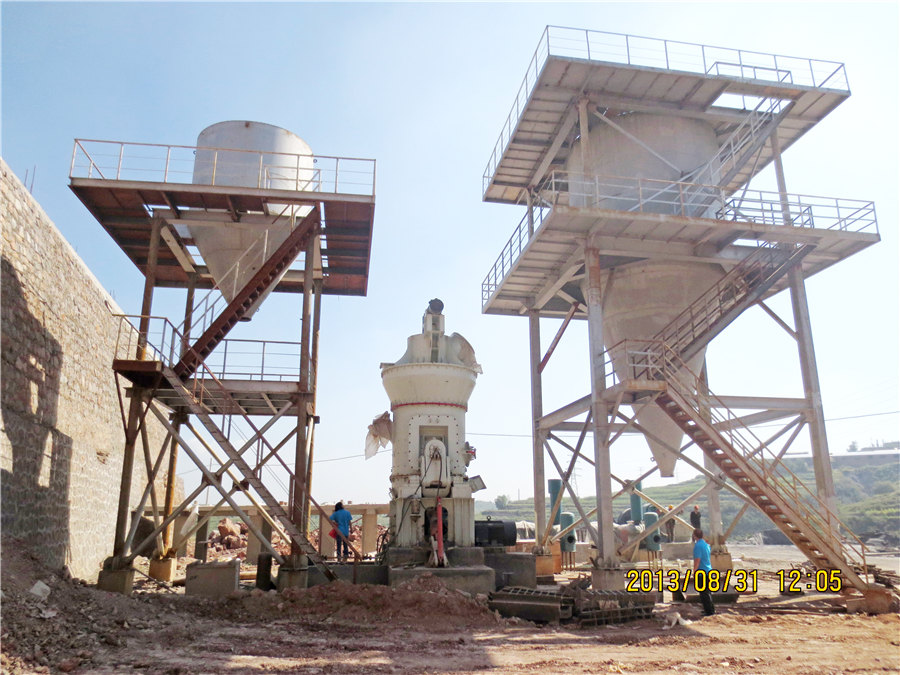
Schematics of limestoneforced oxidation process (LSFO)
Download scientific diagram Schematics of limestoneforced oxidation process (LSFO) from publication: PLEASE SCROLL DOWN FOR ARTICLE Flue Gas Desulfurization: Physicochemical and 2015年3月15日 The acidified absorber effluent is mixed with additional seawater to ensure that the pH is at optimal level for the oxidation process Model of the wet limestone flue gas desulfurization process for cost optimization Ind Eng Chem Res, 40 (2001), pp 25972605 View in Scopus Google Scholar [41]Status of Flue Gas Desulphurisation (FGD) systems from coal 2024年4月19日 Limestone gypsum wet flue gas desulfurization process 2 Magnesium oxide desulfurization process The basic principle of magnesium oxide desulfurization is similar to that of limestone (lime) method, that is, the SO2 in 4 Flue Gas Desulfurization Process You Should Never 2019年10月29日 With the stringent emission regulation taking effect, it is difficult for the conventional desulfurization technology in circulating fluidized bed (CFB) boilers to meet the requirements of ultralow SO2 emission Therefore, in this Applications of Ultrafine Limestone Sorbents for the
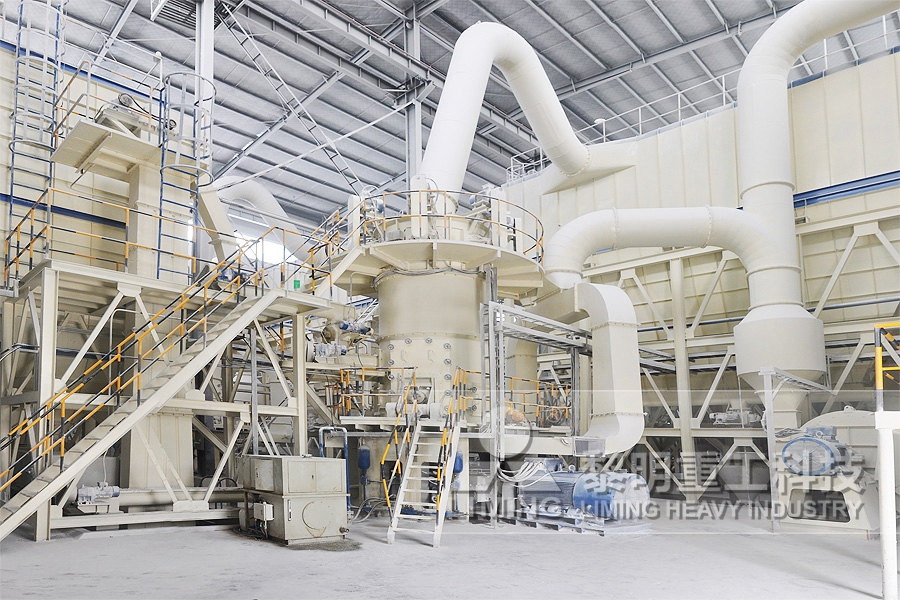
Experiment and Mechanism Analysis of Desulfurization with a
2020年11月16日 To reduce the cost of the current commercial desulfurization and eliminate effluents, the MgObased desulfurizer fixed bed desulfurization tests were carried out in a dry environment By means of Xray diffraction, scanning electron microscopy, and Xray photoelectron spectroscopy, the absorption effects of the MgObased desulfurizer on SO2 2002年4月1日 In this article the method of cost optimization of the “Wet Limestone Flue Gas Desulfurization System” is presented The optimization calculations include process and cost modelsOptimum Values of Process Parameters of the “Wet Limestone 2021年7月1日 The process model was developed for predicting the optimal blending ratio of waste oyster shells to limestone with constraints of desulfurization efficiency and purity of desulfurized gypsumOptimization of wet flue gas desulfurization system using 2013年1月1日 This paper presents an experimental study of calcium bisulfite oxidation, a key step in the wet limestonegypsum flue gas desulfurization (FGD) process, in the presence of catalysts (eg, cobalt LimestoneGypsum Flue Gas Desulfurization Process: Modeling
.jpg)
Full article: Modeling and optimization of wet flue gas desulfurization
2019年3月13日 The control system has also been improved to guarantee stability of the desulfurization process (Villanueva Perales et al Citation 2010, Citation 2009; Wu, Warych, J, and M Szymanowski 2001 Model of the wet limestone flue gas desulfurization process for cost optimization Ind Eng Chem Res 40 (open in a new window) 2021年12月1日 Typically, the adsorption of SO 2 in alkali slurry is a gasliquid adsorption process where gas adsorption rate can be greatly affected by the dissolution rate of solid desulfurizer However, in our previous work [24], it was elucidated that the existence of CaMg(CO 3) 2 in LGL can significantly inhibit the dissolution of CaCO 3 in acid environment, thereby Insights into the desulfurization mechanism of lowgrade limestone Also known as calcium desulphurization limestone gypsum flue gas desulfurization, lime writing broken ground into powder mixed with water and stir into the absorption slurry, in the absorption tower, absorption slurry mixed with flue gas contact, sulfur dioxide in flue gas withResearch progress of flue gas desulfurization and SJISR2) and limestone (CaCO 3) Rosemount Analytical pH equipment is used to control the feed rate of these chemicals PROCESS After fly ash removal, the flue gas (seen in Figure 1) is bubbled through the scrubber, and the slurry is added from aboveThe lime or limestone reacts with the SO 2 in the flue gas to create insoluble calcium sulfite (CaSO Lime / Limestone Wet Scrubbing System for Flue Gas Desulfurization
.jpg)
Desulfurization characteristics of limestone slurry with
2022年12月1日 For process optimization, the following constraints were set: 93 wt% gypsum purity, 94% desulfurization efficiency, and 3,710 kg/h total limestone usage, which maximized the mass flow of lowgrade Seawater desulfurization process, pure use of natural seawater washing flue gas, In the wet FGD process, the limestone slurry should be prepared initially in two continuous steps tank for later use In LSD FGD system (Fig 7), the flue gas is introduced through an inlet pipe of absorber and mixed with the lime slurry droplets, Desulphurisation an overview ScienceDirect Topics2002年6月1日 A new wet limestone−gypsum process for flue gas desulfurization (FGD) has been developed The main difference compared to a conventional wet FGD process is the ability of the new process to New Wet FGD Process Using Granular Limestone ResearchGate2000年7月31日 Emissions Control Strategies for Power Plants Bruce G Miller, in Coal Energy Systems, 2005 Dry Flue Gas Desulfurization Technology Dry FGD technology includes lime or limestone spray drying; dry sorbent injection, including furnace, economizer, duct, and hybrid methods; and circulating fluidizedbed scrubbersDry Flue Gas Desulfurisation Technology ScienceDirect
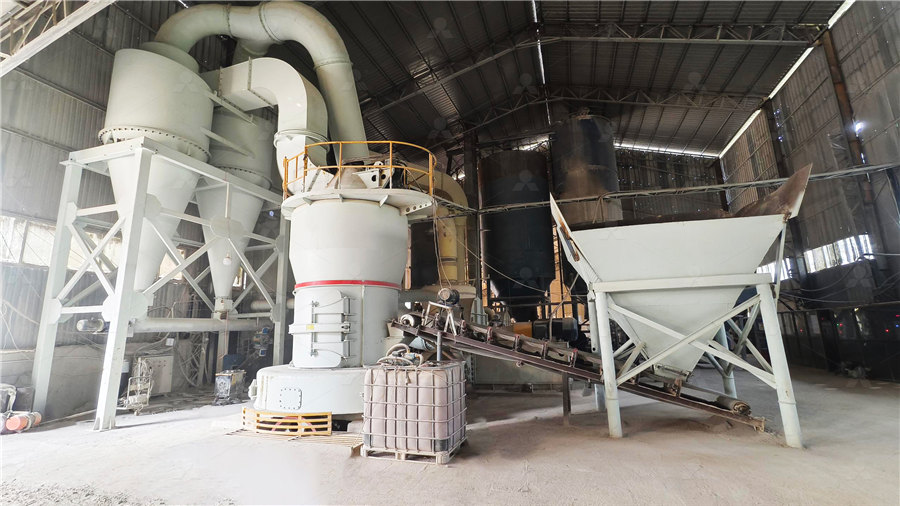
Desulphurization mechanism and engineering practice of carbide
2022年7月14日 In order to give full play to the alkaline neutralization value of carbide slag and reduce the environmental hazards of carbide slag, it is of great practical significance to study the resource utilization of carbide slag The adsorption of sulfur compounds on carbide slag was studied in the laboratory, and the process parameters of carbide slag desulfurization were 2022年1月15日 Wet desulfurization technology includes limestonegypsum desulfurization, dualalkali desulfurization, magnesium oxide desulfurization, zinc oxide Prospects Based on the study of dry desulfurization, semidry desulfurization, and wet desulfurization, the research progress of various desulfurization processes, mass transfer mechanisms and process parameters are Summary of research progress on industrial flue gas desulfurization The limestone is mixed with the coal prior to injection into the reactor, directly in the combustion chamber, 2009 Bragança, S R, Castellan, J L, FBC desulfurization process using coal with low sulfur content, high oxidizing conditions and metamorphic limestones Brazilian Journal of Chemical Engineering, 26(02), p 375383 (2009)EVALUATION OF LIMESTONE IMPURITIES IN THE DESULFURIZATION PROCESS The limestone dissolution rate for limestonecontaining slurries used in wet flue gas desulfurization (WFGD) systems is enhanced by the addition of ammonium ions The ammonium ions may be obtained by incorporating into the limestonecontaining slurry gaseous or aqueous ammonia and/or a watersoluble ammonium salt, such as ammonium sulfate, ammonium Limestonebased wet flue gas desulfurization process
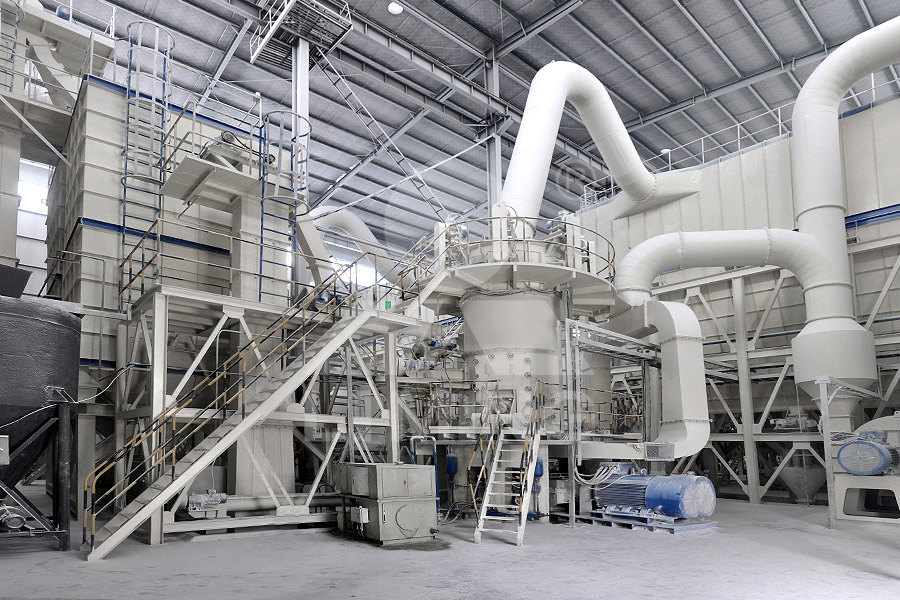
Limestonegypsum flue gas desulfurization process
A flue gas desulfurization process capable of producing a high purity gypsum and also making equipment employed as minimum as possible is provided, which process comprises the steps of cooling and dedusting flue gas containing SO x ; contacting the cooled gas with a slurry containing limestone to remove SO x by absorption and also form CaSO 3 ; controlling the pH