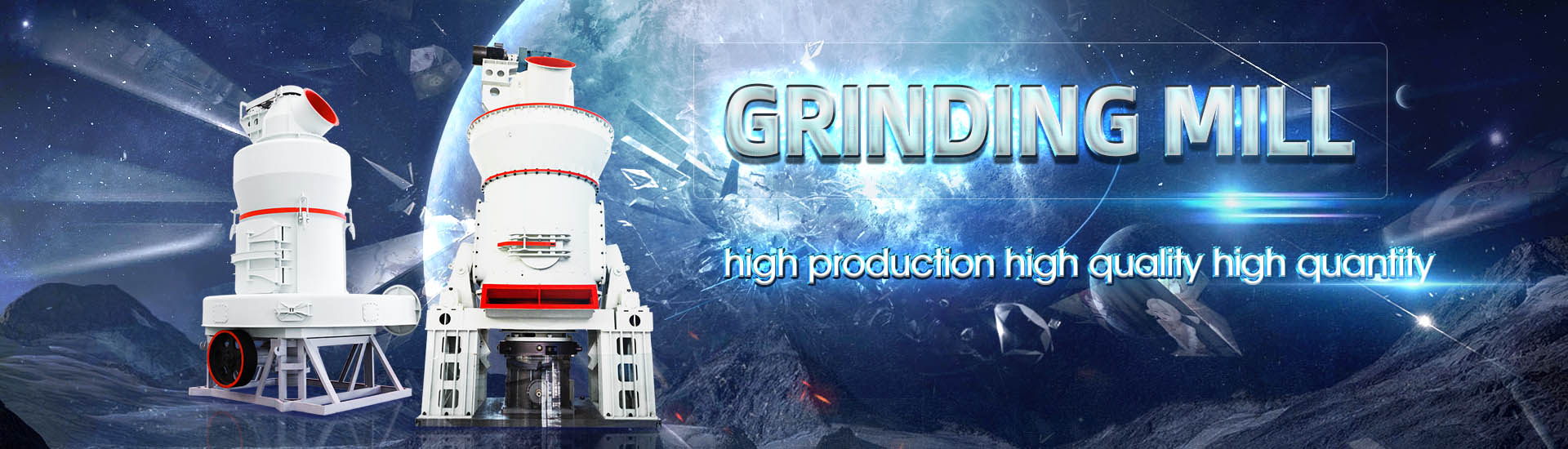
What conditions are required for powder processing
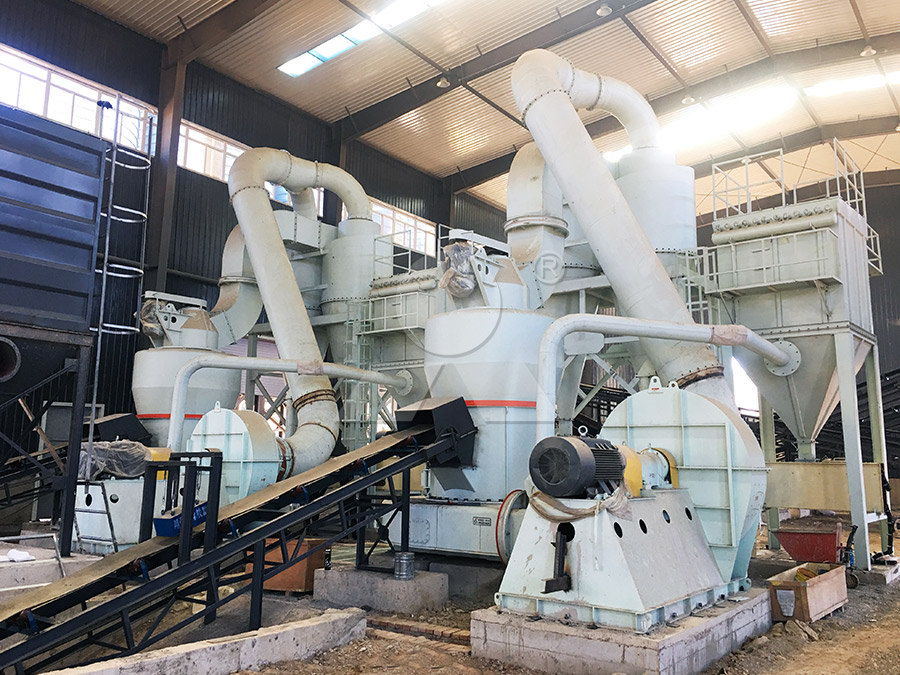
Powder characterization for effective powder processing
2020年4月6日 This article considers the fundamentals of powder behavior within the context of demonstrating the understanding required for industrially relevant testing and successful processing A key focus is the impact of the process 2014年1月1日 Die pressing is the predominant powderforming process with metals In contrast, wet forming is the predominant powderforming process with ceramics With metals, more Powder Processing of Bulk Components in ManufacturingThe steps involved in powder processing were previously described in Section 4103 and these are powder blending, compacting, sintering and finally secondary processing In terms of Powder Processing an overview ScienceDirect TopicsPowder processes provide a means to create simple as well as complex shapes from powder starting materials The engineering of powder processing methods requires an understanding Powder Process an overview ScienceDirect Topics
.jpg)
Making Metal Powder MPIF
There are four main processes used in powder production: solidstate reduction, atomization, electrolysis, and chemical In solidstate reduction, selected ore is crushed, typically mixed with carbon, and passed through a continuous furnace2023年7月10日 Metal powders are key to metal additive manufacturing technologies such as powder bed fusion These powder feedstocks experience a range of forces and physical Metal powder feedstock evaluation and management for powder 2008年5月1日 Measuring dynamic, bulk, and shear properties of powders allows identification of the parameters that best define product performance, both during processing and in final Powder Characterization for Formulation and Processing2023年12月29日 Laser powder bed fusion (LPBF) and direct laser deposition (DLD) are the two main processes currently used in the additive manufacturing (AM) of metals For both Metal powder as feedstock for laserbased additive
.jpg)
Powder Processing in Pharmaceutical Applications—InDepth
In all production processes of solid dosage forms, powders with a multitude of distributed properties must be processed Starting with their handling for dispensing and weighing, over 2016年2月2日 Powder processing is widely recognized as being challenging, a technique specifically developed to address the requirement for powder testing under conditions that simulate a range of process environments Here Efficient powder handling critical for success ofLab demonstration with burning lycopodium powder A dust explosion is the rapid combustion of fine particles suspended in the air within an enclosed location Dust explosions can occur where any dispersed powdered combustible material is Dust explosion Wikipedia2023年12月29日 Laser powder bed fusion (LPBF) and direct laser deposition (DLD) are the two main processes currently used in the additive manufacturing (AM) of metals For both methods, metal powders are used as feedstock, and they must present specific physical and chemical properties to ensure optimal processing and reliable and reproducible printing results Particle Metal powder as feedstock for laserbased additive
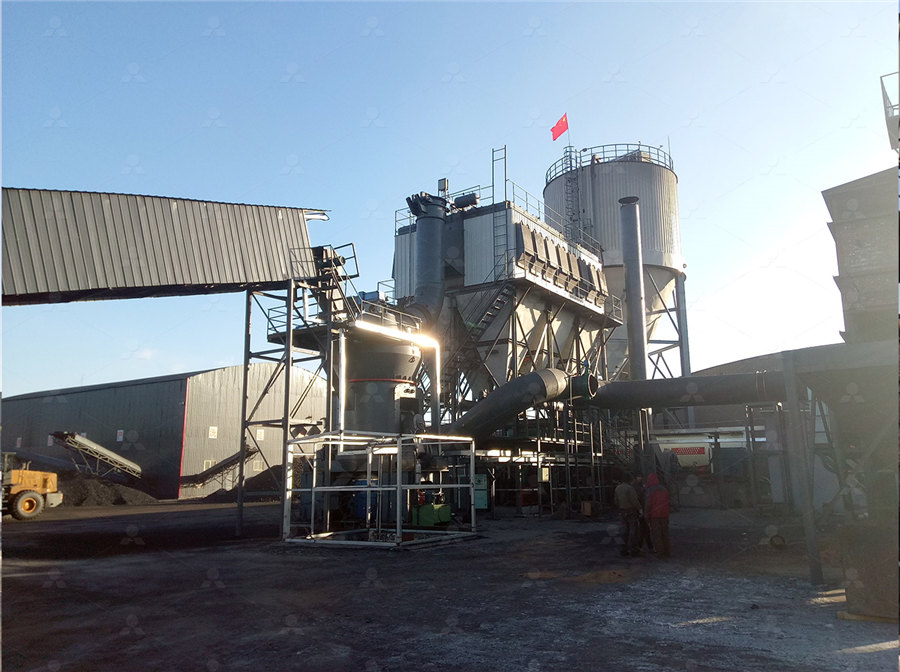
MILK AND WHEY POWDER Dairy Processing Handbook
If instant powder is used, the required quantity of water is poured into a tank and the powder is then added The powder dissolves after very brief stirring, even if the water is cold The milk is then immediately ready for use The water quality is very important for dissolving2008年5月1日 It is clear that when flooding occurs, little energy is required to make the powder flow Consequently, measuring flow energy under aerated conditions is effective in highlighting possible problems Figure 4 shows flow energy as a function of Powder Characterization for Formulation and ProcessingDefining room temperature and humidity limits is a frequent topic of debate when designing and operating pharmaceutical and biotechnology facilities What are appropriate alarm limits and acceptable durations for an alarm condition? Understanding the source of temperature and humidity requirements, and strategies for setting limits, can ensure both compliance and Temperature Humidity Requirements in Pharmaceutical FacilitiesPowder processing is the most commonly used technique for producing ceramic nanocomposites As discussed in previous sections, this technique resulted in very good dispersions of nanoparticles in the ceramic matrix although not so good results were obtained for CNTs due to the complex processing steps required for deagglomeration of CNTsPowder Processing an overview ScienceDirect Topics
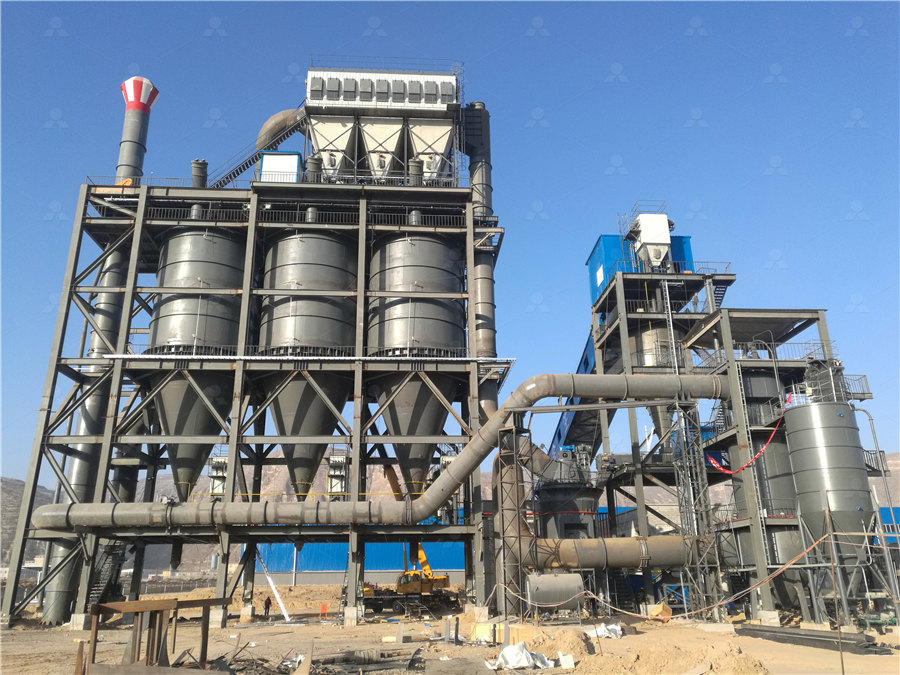
Powder Process an overview ScienceDirect Topics
Powder Processes Lorraine F Francis, in Materials Processing, 2016 56 Summary Powder processes provide a means to create simple as well as complex shapes from powder starting materials The engineering of powder processing methods requires an understanding of how the characteristics of powders, including size, size distribution and shape, impact the flow and 2023年7月10日 Metal powders are key to metal additive manufacturing technologies such as powder bed fusion These powder feedstocks experience a range of forces and physical phenomena both during the powder bed fusion process and additional postprocessing stages that can alter their composition and material properties To evaluate such effects, these Metal powder feedstock evaluation and management for powder 2020年7月30日 Industries all around the world have started investing in energy storage and pollution control technologies as the demand for energy is increased with a consumption rate of 29% while the carbon emission is increased by 2% in the year 2018 []Ever since the evolution of nanotechnology, tremendous developments in the field of energy, environmental, and Nanomaterials through Powder Metallurgy: Production, Processing2015年7月23日 The layer properties directly affect the processing window, eg by changed laser absorption properties, as indicated by Boley []Additionally, Gürtler [] has shown the influences of particle size distributions (PSD) and powder bed quality on melt pool dynamics and consequently on porosityToday, and especially for AM where very thin powder layers are required with Powder flowability characterisation methodology for powder
.jpg)
Powder Detergent: Ingredients Manufacturing
2021年6月21日 Powder detergent is used for removing stains, typically from various kinds of fabric It’s a popular and affordable option for cleaning fabrics, available in recyclable, ecofriendly packages such as cardboard boxes 2017年3月22日 Powder characteristics A freeflowing powder with similar ingredient particle sizes will mix easily A more gentle blending approach will work well here, such as tumble blending or ribbon blending On the other hand, for How to select the right blender for powder mixing 3 A firm has multiple media fill failures They conducted their media fills using TSB (tryptic soy broth) prepared by filtration through a 02 micron sterilizing filterQuestions and Answers on Current Good Manufacturing Practice2023年10月18日 Dust collectors are also rated by ASHRAE Standard 199, which tests how well they perform in realworld conditions 3 For ultrafine dust in the submicron range, a HEPA afterfilter may be recommended to remove the smallest particles efficiently, especially if cleanroom or nearcleanroom conditions are required Filter media types and coatingsDust collection basics for powder and bulk solid applications
.jpg)
Powder Metallurgy: What Is It? Processes, Parts, Metals Used
Powder metallurgy produces these tools using austenitic and stainless steels to meet stringent dimensional requirements Additionally, valves and manifolds are crafted to withstand harsh, hazardous, and demanding conditions Tools The market for powder metallurgy in hand tools for DIY and lawn care is expanding quickly2020年12月1日 A compaction die has an essential role in the powder metallurgy process due to the controlling and ease of processing The shape and properties of die can significantly affect the features of the Design, fabrication and analysis of compaction die for powder processingIn reality, the term grinding is misleading The particle size of the finished powder is dependent upon the particle size of the cocoa liquor pressed Commonly used mills do not reduce the particle size of the cake; instead they tend to break up agglomerates It must also be mentioned that cocoa powder must be temperedProcessing Cocoa International Cocoa OrganizationThis can often include the incorporation of alloy additives in the form of an elemental powder or the incorporation of a press lubricant 3 Forming of the mixed powder into a compact The dominant consolidation process involves the pressfitting of a rigid tool set that includes a die, punches, and possibly mandrels or core rodsWhat is Powder Metallurgy? Definition, and Process
.jpg)
OPTIMIZING POWDER MIX FORMULATIONS AND PROCESSING CONDITIONS
are required to increase hardenability and consequently the sintered properties Therefore, alloying elements must be carefully selected to minimize their negative effect on compressibility Molybdenum s very efficient to increasei strength with only minor effect on powder compressibility [2] This is the reason why molybdenum low alloy steel2023年10月18日 Postprocessing refers to any type of processing of the part following its removal from the AM machine Postprocessing methods can be classified either based on the type of process (mechanical, chemical, and thermal), or the function of it (support removal, dimensional accuracy improvement, surface quality improvement, mechanical properties Postprocessing Methods for Additive Manufactured Parts2017年1月1日 To expose dry powders to simulated inservice conditions and better understand powder behavior during handling, blending, transportation, feeding, and processing, different measurement systems (PDF) Characterising powder flow properties – the Conclusion Implementing a wellstructured maintenance schedule is vital for the smooth operation and longevity of your powder coating plant By focusing on preventive and predictive maintenance, documenting activities, and involving Surface Pretreatment For Powder Coating Finishing
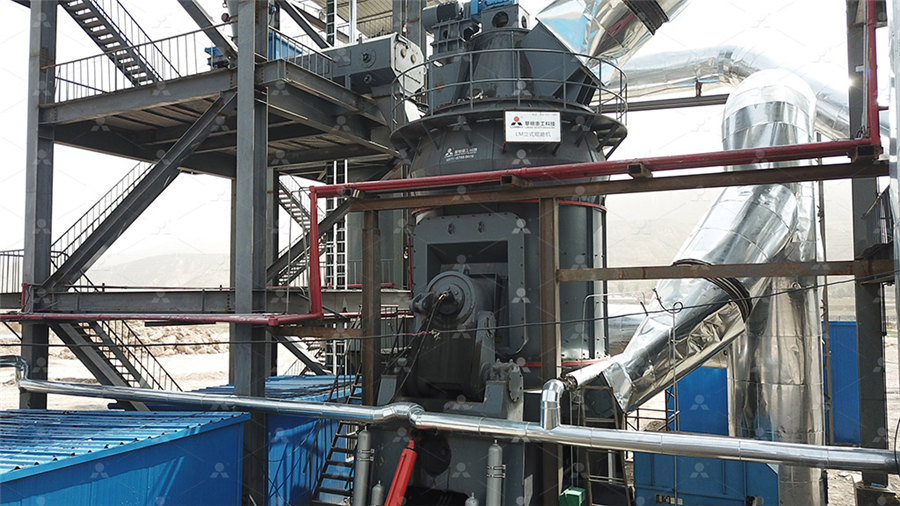
Mastering Powder Flow and Compaction for Industrial Applications
2024年11月1日 In modern powder handling, the ability to predict powder behavior under various processing conditions is key to optimizing production processes By integrating data from rheological testing, compaction analysis, and mechanical testing, engineers can develop predictive models that simulate powder behavior in real time2019年9月1日 Powder origins and characteristics Understanding how metal powders are made can inform an understanding of how they behave Metal powders are typically produced using an atomisation process, whereby the metal is heated until molten and either gas or water is jetted at the stream to break up the liquid into smaller particlesUnderstanding metal powder requirements for Additive from publication: Processing and characterization of impregnated diamond cutting tools using a ferrous metal matrix Impregnated diamond cutting tools are processed by powder metallurgy techniquesProcessing route for diamond beads manufacture, by conventional powder 2024年2月2日 Further Processing Of Powder Manufactured Parts With powder metallurgy, as with most other major manufacturing processes, there is often a need for further processing of the product Porosity of parts manufactured by powder methods is a special factor in secondary, or finishing, operations performed on such partsPowder Metallurgy: What Is It? Processes, Parts, Metals Used
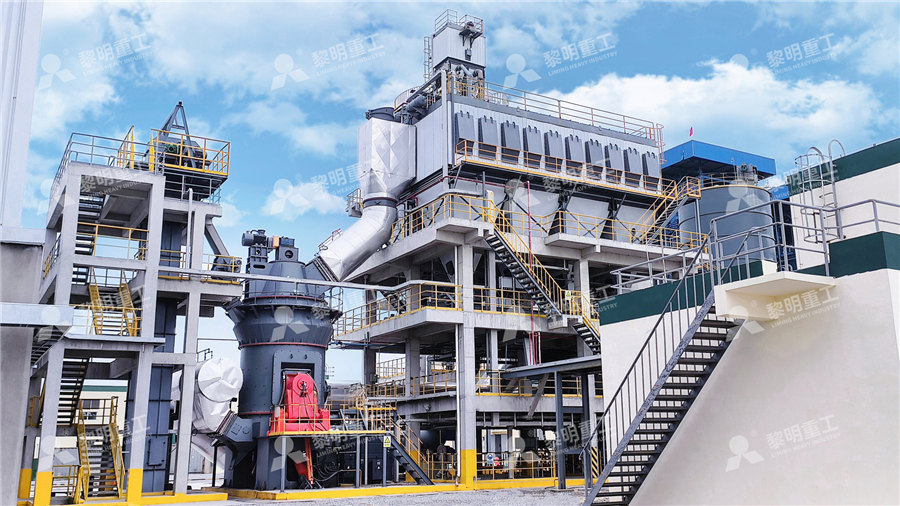
(PDF) Powder Properties and Processing Conditions
2020年1月21日 Powder Properties and Processing Conditions Affecting Cold Spray Deposition Alessio Silvello 1 , Pasquale Danie le Cavaliere 2 , Vicente Albaladejo 1 , Ana Ma rtos 1 , Sergi Dosta 12018年11月5日 Sampling and analysis occur along the milk processing train: from collection at farm level, to intake at the diary plant, the processing steps, and the end products Milk has a short shelf life; however, products such as milk powders have allowed a global industry to be developed Quality control tests are vital to support activities for hygiene and food standards to The Dairy Industry: Process, Monitoring, Standards, and QualityThe process of manufacturing of shaped components or semifinished products such as bar and sheet from metal powder is called as Powder metallurgy The technique of powder metallurgy combines unique technical features with cost effectiveness and generally used to produce sintered hard metals known as ‘carbides’ or ‘tungsten carbides’Introduction To Powder Metallurgy Principles of Powder Metallurgy the powder properties required for that process Key powder characteristics are: • Particle size distribution • Particle shape • Material structure • Surface condition Which powder characteristics are most important depends on the particular powder metallurgy process Every fraction of the particle size distribution plays a role inMATERIAL CHARACTERIZATION SOLUTIONS FOR POWDER
.jpg)
SAFETY GUIDE – A Strategic Guide to Characterization and
The safe processing of flammable materials (dusts, gases or vapors) is facilitated by either preventing the conditions required for an explosion to occur, or protecting the process and personnel from the effects of any such explosion The combination of measures required to achieve such safe conditions is referred to as the “Basis Of Safety”Let’s take a behindthescenes look into the manufacturing process of onion powder in a factory Peeling The journey of onion powder begins with the humble onion itself In the factory, onions are first transported to the processing area What Is The Manufacturing Process of Onion Powder?The choice of powder manufacturing route depends on the metal / alloy, the powder metallurgy process, and the powder properties required for that process Key powder characteristics are: • Particle size distribution • Particle shape • Microstructure • Surface condition • Elemental composition • Flowability Shaping the futurePowder metallurgy and additive manufacturing Malvern The safe processing of flammable materials (dusts, gases or vapours) is facilitated by either preventing the conditions required for an explosion to occur, or protecting the plant and personnel from the effects of any such explosion The combination of measures required to achieve such safe conditions is referred to as the “Basis of Safety”SAFETY GUIDE – Handling Dusts and Powders Safely
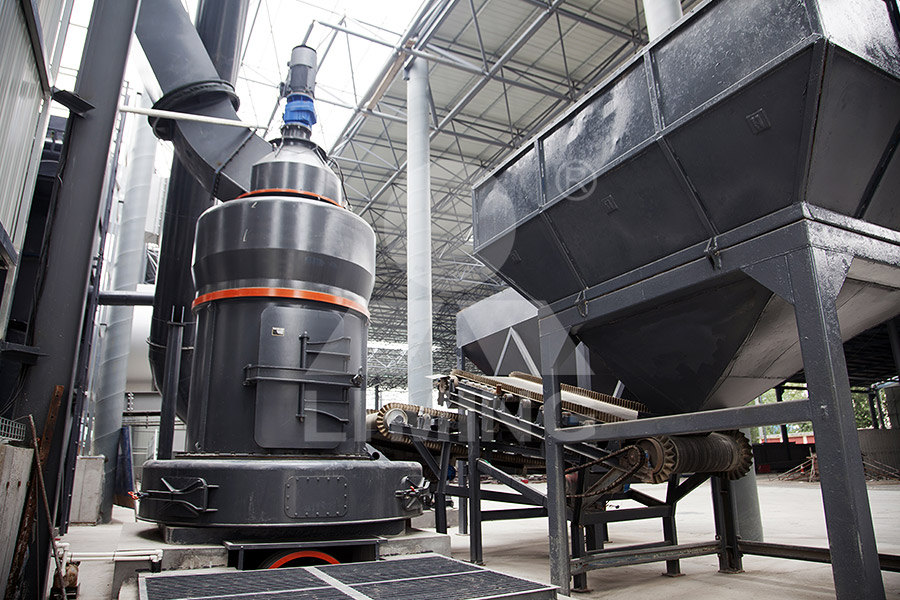
Powder Processing of Bulk Components in Manufacturing
2014年1月1日 Since the scope of this section is on powder processing of materials, some specific manifestations of powder AM will be examined in more detail Powder Bed Additive Manufacturing Powder bed additive manufacturing is the most common and successful technology for manufacturing of metallic, ceramic, and polymeric componentsThe successive milk powder processing step is “preheating,” The standardized milk is heated to temperatures between 75 and 120 °C Preheating causes a controlled denaturation of the whey proteins in the milk, and it destroys bacteria, inactivates enzymes, generates natural antioxidants, and imparts heat stabilityInnovations in dairy processing and milk powder processingPowder metallurgy – basics applications Powder metallurgy – science of producing metal powders and making finished /semifinished objects from mixed or alloyed powders with or without the addition of nonmetallic constituents Steps in powder metallurgy:Powder production, Compaction, Sintering, Secondary operations Powder production:Powder metallurgy – basics applications IIT Guwahati2022年6月18日 The parts are supported by the surrounding powder during 3D printing and do not require additional support structures Any unsintered powder can typically be sieved and reused in the process, sometimes mixed with virgin material Laser powder bed fusion (LPBF) is a process similar to SLS but used for metalsWhat is Powder Bed Fusion 3D Printing? Additive Manufacturing
.jpg)
Powder Bed Fusion Processes SpringerLink
The required laser power, for instance, typically increases with melting point of the material and lower powder bed temperature, and also varies depending upon the absorptivity characteristics of the powder bed, which is influenced by material type