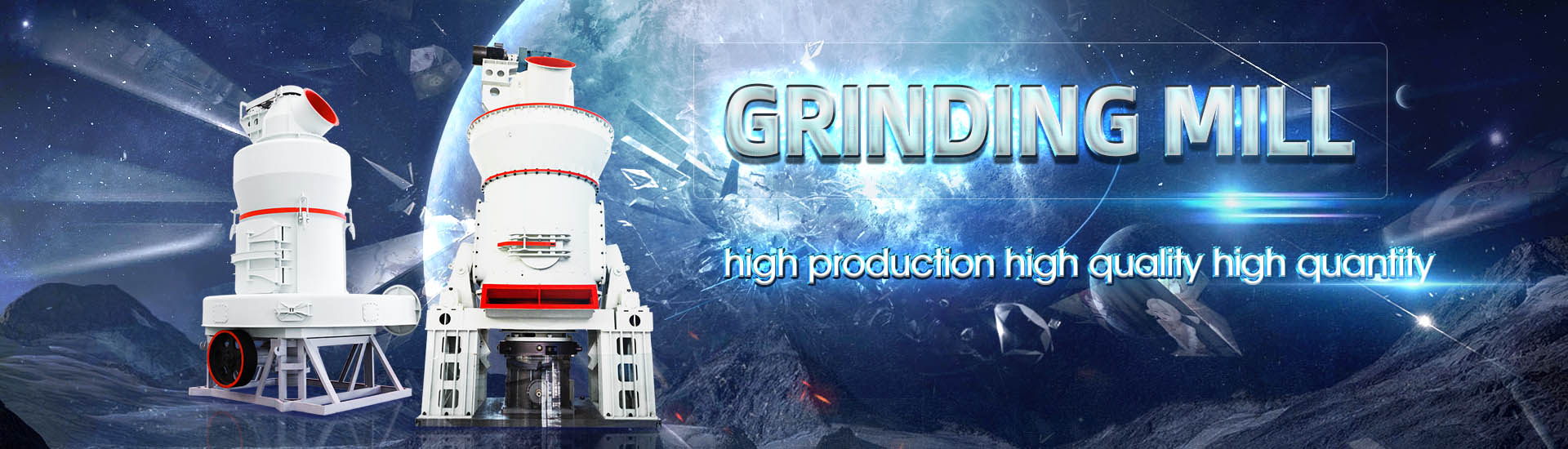
Preparation and calculation of pulverized coal for electric standing mill
.jpg)
Novel technology of electric combustion of pulverized coal and
The article presents a review of modern technologies for firing up pulverized coalfired boiler units, as well as presents the original technology of electric ignition and the results of tests on the 2017年11月15日 Therefore, our study presents the optimization of particles size of pulverized coal in 650 t/h pulverized coal fired boiler with natural circulation (type OP 650) to the power Optimisation of coal fineness in pulverisedfuel boilers2021年11月4日 This method enables facilitated testing procedures and a more exact simulation of grinding in vertical spindle coal mills Ballrace mills and Loesche roller mills were used(PDF) Technique to Investigate Pulverizing and Abrasive2019年1月1日 This paper analyzes the effects of coal grindability and its characteristics on the grinding capacity and power consumption for beater (PDF) Practical assessment of grinding capacity and
.jpg)
An investigation of performance characteristics and energetic
2020年8月12日 To understand the performance of a vertical roller coal mill, the real operational tests have been performed considering three different coal sources Obtained results indicate 2016年10月22日 Pulverization is one of the most important stages of the electric power station, is often determined by the working capacity of the boiler and the entire plant as a whole Also SYSTEM OPTIMAL CONTROL OF THE BALL MILL FOR THE 2021年4月8日 This Review comprehensively summarizes the current research on numerical modeling to offer a better understanding of the technical aspects and provides future research requirements of HELE coalfired boilers, A Review of the Numerical Modeling of Pulverized Coal Pulverization is currently the favored method of preparing coal for burning Mechanically pulverizing coal into a fine powder enables it to be burned like a gas, thus allowing more Improving Coal Pulverizer Performance and Reliability Pall
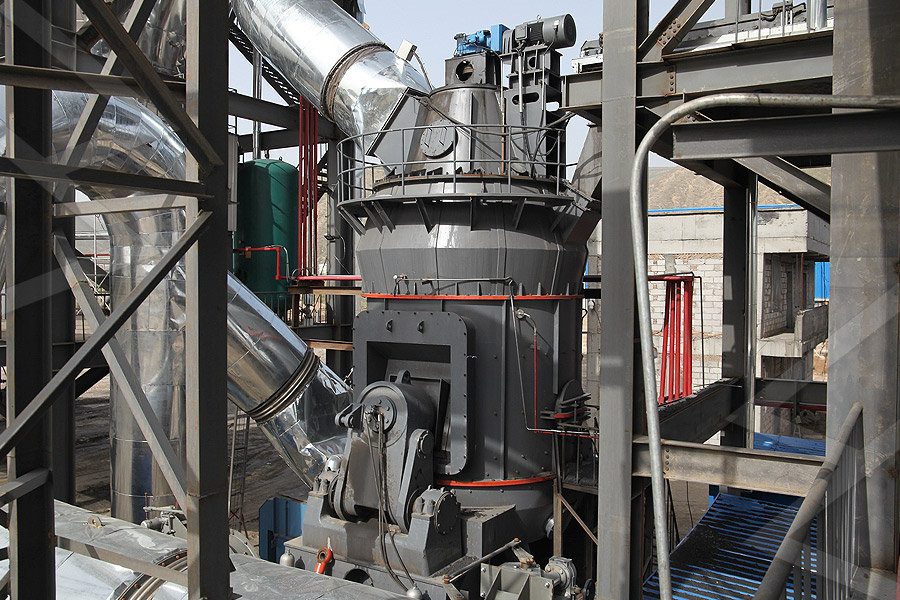
An investigation of performance characteristics and
2020年8月12日 To understand the performance of a vertical roller coal mill, the real operational tests have been performed considering three different coal sources Obtained results indicate that grindingANALYSIS OF CONSTRUCTIONS OF ROLLER MILLS FOR PREPARATION OF PULVERIZEDCOAL FUEL AND WAYS THEM FURTHER DEVELOPMENT pulverizedcoal fuel, milling, roller mill, separator, specific charges of electric power on to tone of the ground up fuel, namely in 1520 times less than comparatively with the lowspeed barreltype mills; compactness ofANALYSIS OF CONSTRUCTIONS OF ROLLER MILLS FOR PREPARATION OF PULVERIZED Fuel preparation for a pc boiler occurs in a mill, where coal is typically reduced to 70% through a 200mesh (74μm) screen Figure 2 shows a particlesize distribution from a bowlmill grinder typically used in power plants A typical utility specification for particle size distribution of the coal is that 70% of the mass should pass through a 200mesh screen, which is equivalent to 70% Pulverized Coal Boiler an overview ScienceDirect TopicsGas turbine combined cycle Shigehiro Shiozaki, Akira Yamada, in Advances in Power Boilers, 2021 637 Gasifier facilities 6371 Coal pulverizing and feeding system The purpose of the coal drying system is drying and grinding the raw coal for stable transportation of pulverized coal to gasifier and stable/highefficiency gasification at the gasifierCoal Pulverizers an overview ScienceDirect Topics
.jpg)
(PDF) Practical assessment of grinding capacity and
2019年1月1日 Twenty fieldscale tests were conducted in a 28 MW pulverized coal power plant in Healy, Alaska, to examine mill power consumption in relation to coal grind size1996年4月10日 Exhaust gas temperature in coalfired power plants can reach approximately 120 °C to 140 °C, with the thermal energy accounting for approximately 3% to 8% of the total input energyDevelopments in Pulverized CoalFired Boiler TechnologyThe exhauster supplies pulverized coal to three riffle type distributors The riffle distri bution system on each mill supplies pulverized coal to eight coal nozzles, a total of 32 coal nozzles for the entire boiler The exhauster discharge pressure is approximately 10 to Pulverizer Fineness and Capacity Enhancements at Danskammer 2018年10月21日 Fig 1 Pulverized coal combustion and gas composition in raceway The extent of combustion (combustion efficiency), and hence the amount of unburnt material transported out of the raceway, depends on several parameters which include (i) properties of the coal, such as the VM content, particle size and density, and (ii) operating conditions, for example, blast gas Understanding Pulverized Coal Injection in Blast Furnace
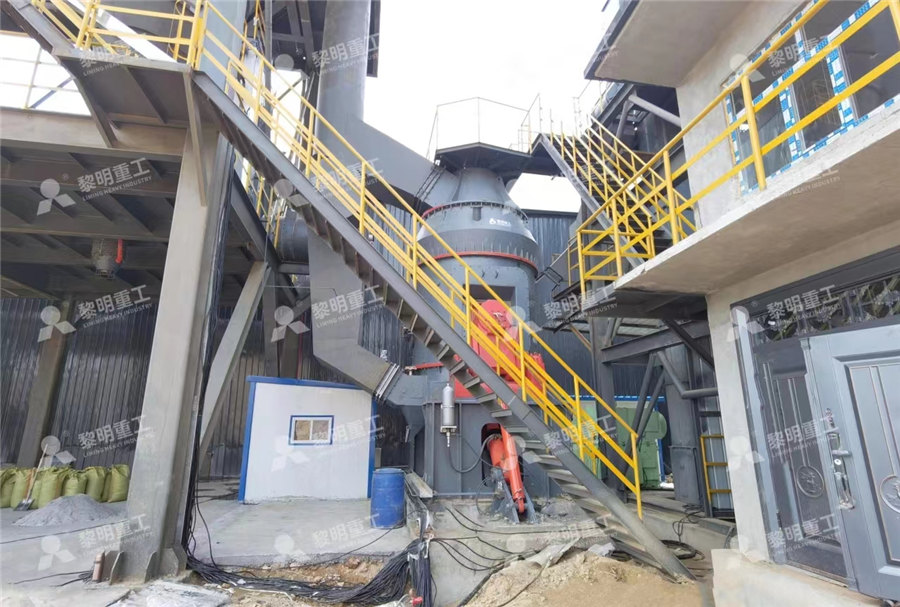
Modelling of the pulverized coal plasma preparation for
2021年6月1日 One of the promising ignition technologies is plasma thermochemical preparation of pulverized coal fuel for combustion (PTPC) [3, 4] using plasmafuel systems (PFS) The most common PFS scheme is 2015年10月19日 The paper presents experimental and numerical investigation of pulverized coal combustion process analysis and optimization The research was conducted on the frontfired pulverized coal boiler with dedicated lowNOx furnace installation In order to find optimal boiler operating conditions the acoustic gas temperature measurement system and mass flow A Combustion Process Optimization and Numerical Analysis for Introduction This article concerns itself with vertical grinding mills used for coal pulverization only (coal pulverizers), although vertical grinding mills can and are used for other purposes The 3D model in the saVRee database represents a vertical grinding bowl millOther grinding mill types include the ball tube mill, hammer mill, ball and race mill, and , roll and ring millVertical Grinding Mill (Coal Pulverizer) Explained saVRee2012年5月1日 Coal fired power plants are heavily used due to large and long lasting coal resources compared with oil or natural gas An important bottleneck in the operation of this particular kind of plants, however, is the coal pulverization process, which gives rise to slow takeup rates and frequent plant shutdowns (Rees Fan, 2003)In typical coal fired power plants, Derivation and validation of a coal mill model for control
.jpg)
PRACTICAL ASSESSMENT OF GRINDING CAPACITY AND
Obradović, M O, et al: Practical Assessment of Grinding Capacity and Power THERMAL SCIENCE: Year 2019, Vol 23, Suppl 5, pp S1533S年5月1日 A plasma model of thermochemical preparation for the combustion of pulverized coal implemented through the PlasmaKinTherm program for the calculation of plasmafuel systems has been describedPlasma thermochemical preparation for combustion of pulverized coalDL/T 51452002 English Version DL/T 51452002 Technical code for design and calculation of pulverized coal preparation system of fossilfired power plant (English Version): DL/T 51452002, DL 51452002, DLT 51452002, DL/T51452002, DL/T 5145, DL/T5145, DL51452002, DL 5145, DL5145, DLT51452002, DLT 5145, DLT5145Technical code for design and calculation of pulverized coal of coal preparation systems Pulverized coal (PC) firing is the dominant method used in modem power sta tions So, most of this chapter will focus on coal preparation systems for PC boilers and their design Fluidized bed (FB) firing is developing very quickly and find ing its way to wider applications in largescale commercial boilersCoal Preparation Systems for Boilers Springer
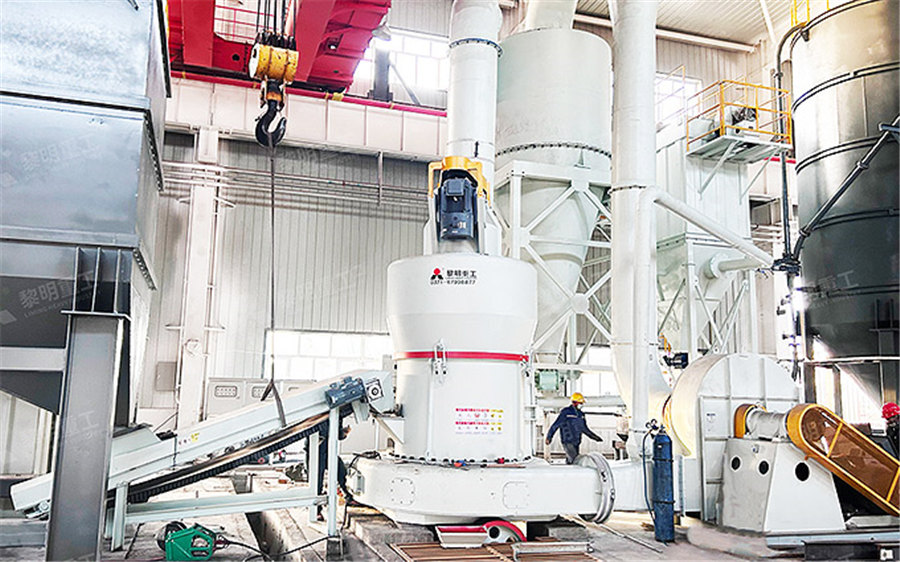
System optimal control of the ball mill for the preparation of the
2016年1月1日 Pulverization is one of the most important stages of the electric power station, is often determined by the working capacity of the boiler and the entire plant as a whole2023年1月13日 The paper provides an outlook on future directions of research and the possible applications for pulverized coalfired boilers One potential direction for future research is to focus on the ways to improve the efficiency of pulverized coalfired boilers This could involve developing new combustion technologies that are able to more thoroughly burn the coal and Pulverized CoalFired Boilers: Future Directions of Scientific The BTM is a lowspeed mill that primarily grinds coal by impact and attrition The VRM is a medium speed mill that grinds coal by compression and, because of the low coal inventory in the mill and flat grinding surfaces, develops shearing action as well For both mills a constant centrifugal force is maintained The speedA Comparison of Three Types of Coal Pulverizers Babcock PowerIOP Publishing % %% )Optimization and transformation of 300MV units steel ball coal mill
.jpg)
PRACTICAL ASSESSMENT OF GRINDING CAPACITY AND POWER
feeder geometry Mill power consumption (mill load given as electric energy consumption) was measured using plant system instruments Energy consumption used for grinding and other processes per unit of mass (specific power consumption) is [14, 15]: The total power of mill electric motor (power at mill load) is obtained from the expression 2019年11月7日 Training a support vector machine (SVM) with data number nn has time complexity between O(n2)O(n2) and O(n3)O(n3) Most training algorithms for SVM are not suitable for large datasetsOptimization and transformation of 300MV units steel ball coal mill 2016年10月22日 Pulverization is one of the most important stages of the electric power station, SYSTEM OPTIMAL CONTROL OF THE BALL MILL FOR THE PREPARATION OF THE PULVERIZED COAL MIXTURE AV, Tishchenko, NT, Zhigaylo, BD (2016) SYSTEM OPTIMAL CONTROL OF THE BALL MILL FOR THE PREPARATION OF THE PULVERIZED SYSTEM OPTIMAL CONTROL OF THE BALL MILL FOR THE PREPARATION 2009年9月20日 A control oriented model was then developed by Fan (1994) and Fan and Rees (1994) In 2009, coal flow and outlet temperature of mill were modelled using mass and heat balance equations for startup Modeling and Parameter Identification of Coal Mill
.jpg)
Plasma thermochemical preparation for combustion of pulverized coal
2017年6月24日 A plasma model of thermochemical preparation for the combustion of pulverized coal implemented through the PlasmaKinTherm program for the calculation of plasmafuel systems has been described Such systems are used at nonfueloil startup of boilers and the stabilization of the combustion of a pulverized coal torch The model combines kinetic and 520 P Niemczyk et al / Control Engineering Practice 20 (2012) 519–530 Nomenclature Dpmill mc mpc mcair mass of unground coal on the table (kg) mass of pulverized coal on the table (kg) mass of pulverized coal carried by primary air (kg) wc wpc wout wret mass mass mass mass flow flow flow flow of of of of the dry raw coal to the mill (kg/s) pulverized coal (kg/s) pulverized coal Derivation and validation of a coal mill model for controlSection of coal bowl mill Table 1 Guaranteed coal conditions for mill performance evaluation Coal Moisture % 20 Coal HGI 55 Mill Outlet Temperarure °C 80 Mill Air Flow T/hr 102 Coal Fineness (% passing trough 200 mesh) 70% passing through 200 mesh and 90% passing through 50 mesh Differental Pressure 300 mmwc Coal Output from Mill 609 t/hrA Study on 500 MW Coal Fired Boiler Unit’s Bowl Mill Request PDF On Aug 1, 2017, Marek Pronobis and others published Optimisation of coal fineness in pulverisedfuel boilers Find, read and cite all the research you need on ResearchGateOptimisation of coal fineness in pulverisedfuel boilers
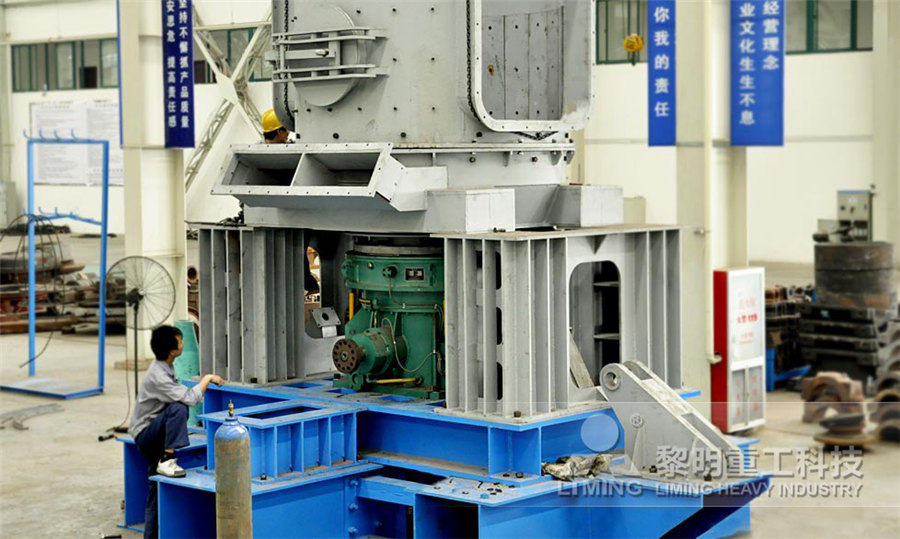
(a) Preparation of pulverized coal and (b) damaged straight
The highest erosive wear occurred for the M3 mill dust ducts for the case coal 1 and amounted to 456 mm/5200 h On the other hand, the lowest erosive wear occurred for the M2 mill dust ducts 2022年1月26日 Numerical calculations of the pulverized coal–air mixture flow inside the dust ducts were performed together for all six dust ducts for each subsequent mill fed the BP 680 boiler Numerical Study of the Erosion Process and Transport of Pulverized Coal 2019年1月1日 Thus, the pulverized coal mass flow into boiler is not equal to the coal mass flow into coal mill, which can be measured by the weighing machine installed on coal feeder Flue gas Pulverized coal bunker Gas Primary air Coal Coal mill Boiler Pulverized coal classifier Pulverized coal feeder Fig 1 Flow diagram of coal and gas dualfired boilerCalculation Method of Pulverized Coal Mass Flow Into Coal and 2012年11月17日 2 1Introduction Coal continues to play a predominant role in the production of electricity in the world, A very large percentage of the total coal is burned in pulverized form Pulverized coal achieved its first commercial Coal mill pulverizer in thermal power plants PPT
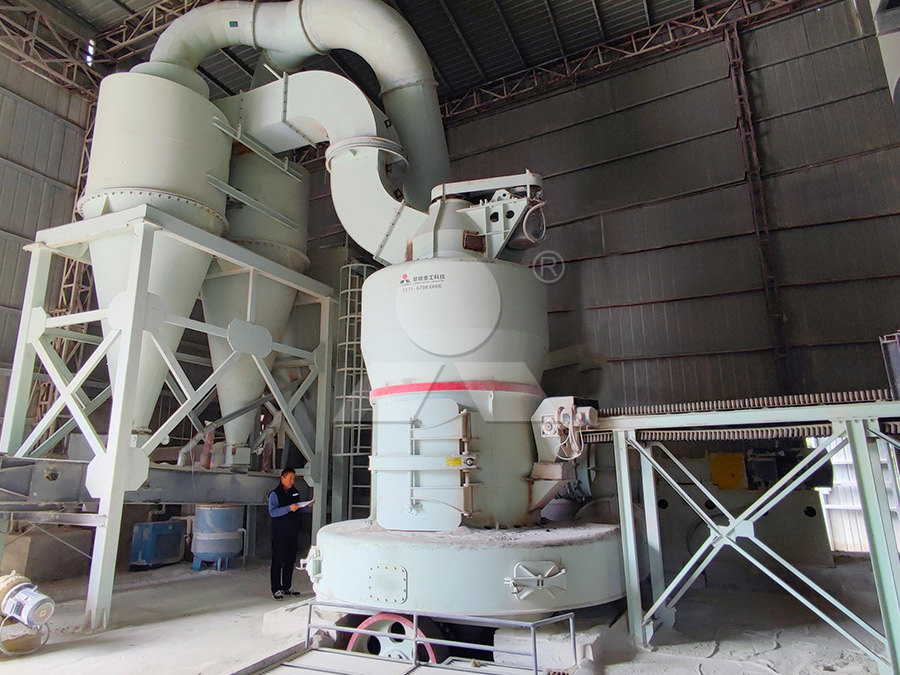
Practical assessment of grinding capacity and power
Nomenclature A – ash content in coal (mass fraction), [%] B – grinding capacity, [th–1] cosφ – power factor, [–] D1 – outer diameter of beater, [m] D90 – cumulative passing through 90 [µm] sieve, [%] HGI – Hardgrove grindability 1996年10月1日 Replacement of metallurgical coke by pulverized coal (PC) injected in blast furnace (BF) tuyeres is a major economical challenge, due to the high price of coke and unfavorable effect of its Increase of Pulverized Coal Use Efficiency in Blast Furnace1800 rpm primary air fan, and four mill outlets supplying pulverized coal to one of the three horizontal rows of (4) dualfuel burners When operating at boiler MCR, each mill had a coal throughput of approximately 53,000 #ffir Specified product fineness was 70% thru 200 mesh and 98% thru 50 mesh Diminishing supply of the original Kansas coalWorldProven Coal Pulverizer Technology Debuts in the USand storage of pulverized coal So initial temperature of desiccant should be reduced The insufficient output will lead to lower milling force and need to rise initial temperature of desiccant 3 Example of calculation In this study, the A mill of NO1 unit of a power plant is selected as an example The unit is 350MWProgram Design and Calculation Example of Direct Fired

Pulverized Coal Pipe Testing and Balancing Storm Technologies,
Collecting coal samples using an isokinetic probe provides the best data describing actual operating conditions inside the coal pipe Source: Storm Technologies Inc The isokinetic coal sampling method, although more difficult, is the best option for determining the true mill coal fineness produced and to calculate pulverizer performance2017年11月15日 The work is based on tests of pulverisers of a 650 t/h pulverized fuel boiler (OP 650) in a Polish power plant On the basis of these studies, relationships were derived between the fineness of the produced pulverized fuel and operating parameters, the efficiency of the boiler and parameters of the milling system, eg, energy consumption of the mill and its fanOptimisation of coal fineness in pulverisedfuel boilers2017年6月24日 A plasma model of thermochemical preparation for the combustion of pulverized coal implemented through the PlasmaKinTherm program for the calculation of plasmafuel systems has been described Such systems are used at nonfueloil startup of boilers and the stabilization of the combustion of a pulverized coal torch The model combines kinetic and Plasma thermochemical preparation for combustion of pulverized coal2023年1月13日 Exemplary results of the analysis of the concentration of particles (with a diameter of 50 micrometers) in a dust duct and also their velocities that were assumed in the calculations(PDF) Pulverized CoalFired Boilers: Future Directions of Scientific