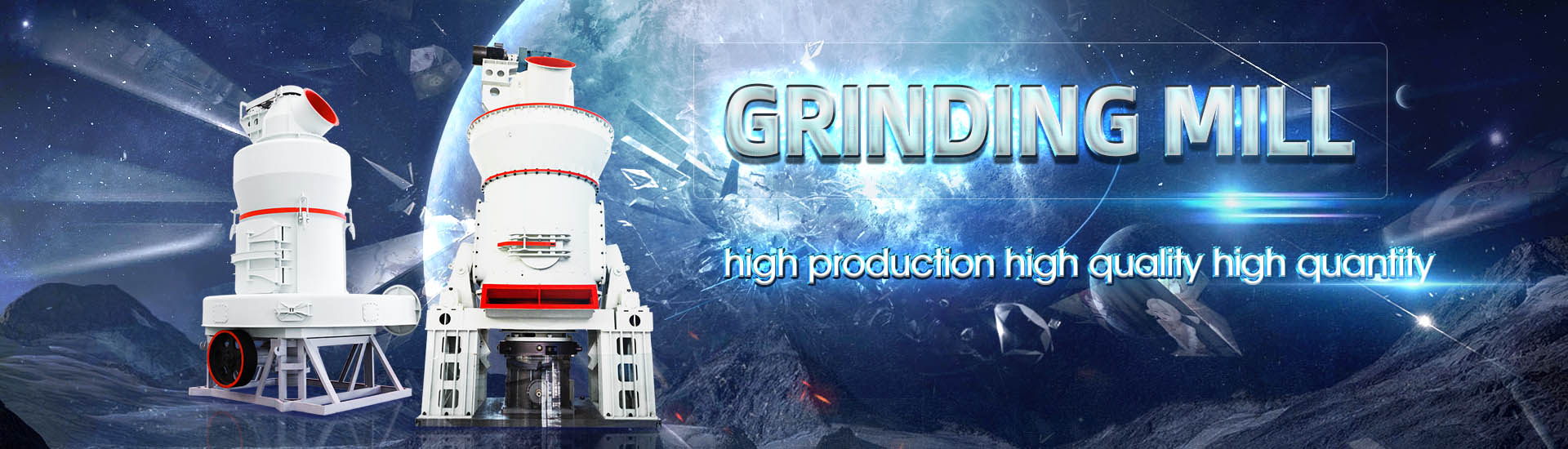
Bulk density of sintered composite insulation bricks
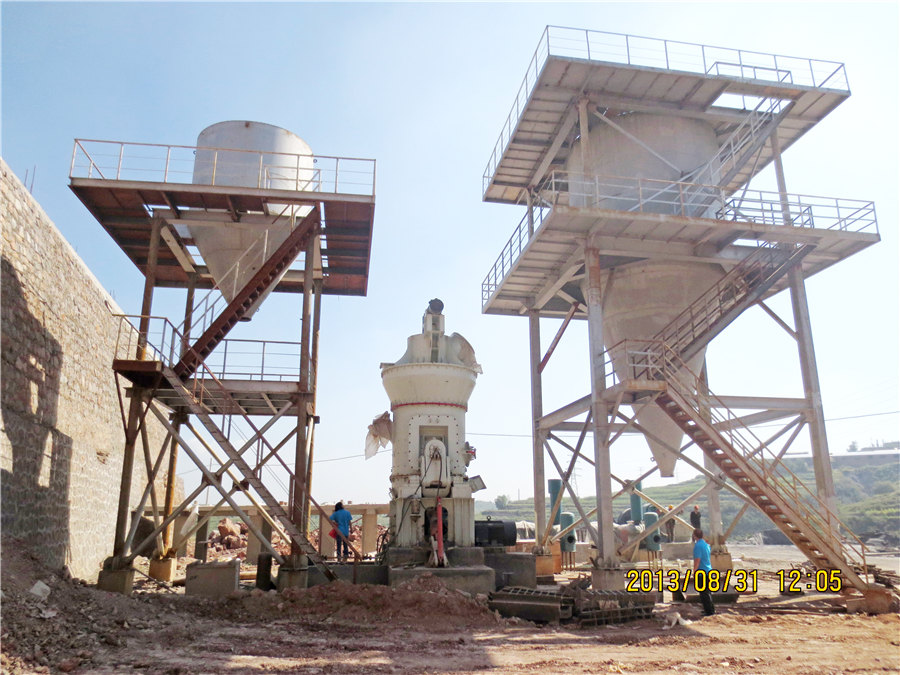
Effect of sintering temperature and composition on the
In this research, kaolin, ball clay, sawdust and rice husk were used to produce insulation bricks through the solid state synthesis method Two temperatures, 1100oC and 1200oC were used to2023年11月16日 Luo et al produced composite sintered bricks using iron waste and coal gangue powder and found that when temperatures increased from 950 °C to 1150 °C, the bulk density of bricks increased from 162 g cm −3 to 165 Newly Generated CaFeldspar during Sintering 2022年1月1日 Integrating up to 20% ESP into the composite bricks minimizes the bulk density of the sintered samples leading to lightweight ceramic bricks This can lower the expenses Preparation of innovative ecoefficient composite bricks based on 2024年9月1日 In order to determine the physical properties of sintered bricks, such as bulk density (BD) and apparent porosity (AP), established test protocols are utilized, including the Preparation and characterization of highstrength insulating
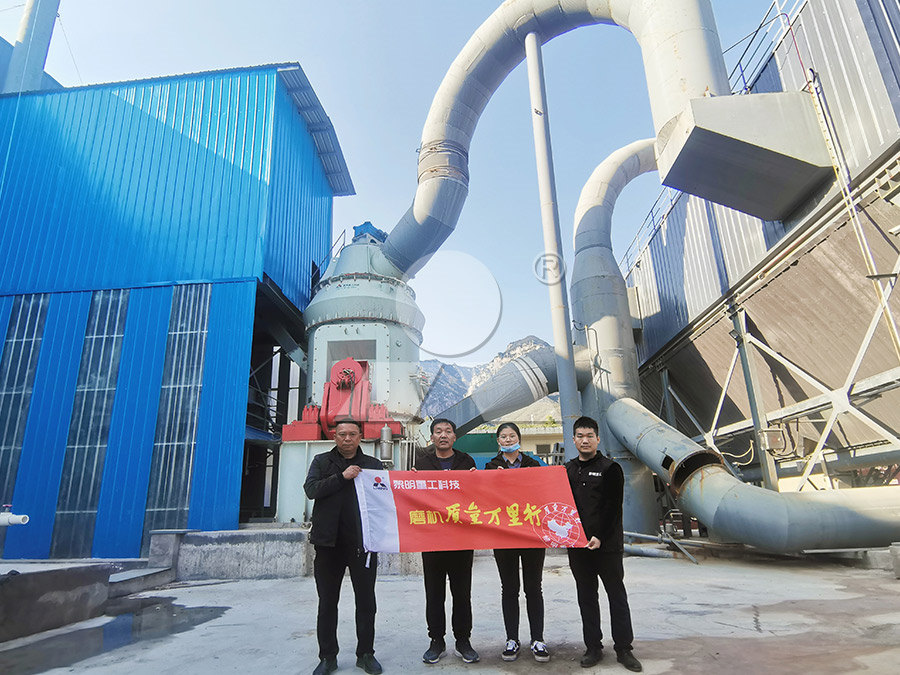
(PDF) The Effects of Sintering Temperature and Agro Wastes on
As the amounts of kaolin used in preparing the samples decrease, the bulk density, modulus of rupture and cold crushing strength of the bricks decreases while the water absorption capacity, 2019年12月31日 The bulk density, sintering shrinkage, water absorption and compressive strength of the composite sintered bricks were tested to determine the optimum preparation Preparation, characteristics and mechanisms of the composite The findings revealed that the inclusion of 20% eggshell to the samples sintered at 950 °C generated composite bricks with the lowest density (14 g/cm³) and thermal conductivity of 027Preparation of innovative ecoefficient composite Results of test indicate that when the sintering temperature of the brick is 1050 ℃, the minimum amount of waste mixture can be used to produce regenerated sintered shale bricks with Effect of Sintering Temperature on Properties of Regenerated
.jpg)
Reducing the carbon footprint of buildings using biocharbased
2023年11月4日 This review discusses the potential benefits of incorporating biocharbased bricks and insulation materials, focusing on their preparation methods, material properties, 2019年2月20日 Here, we report dense bulk hBN with 976% theoretical density achieved at a lower preparation temperature (1700 °C) via a selfdensifying mechanism without sintering additivesLow temperature selfdensification of high strength 2015年10月1日 Based on the finite volume method (FVM) and finite element method (FEM), the threedimensional heat transfer and mechanical properties of the inorganic composite sintered shale hollow brick were Analysis on the performance improvement of inorganic composite sintered 2020年1月30日 We found that the qualified composite sintered bricks with 1638 g/cm 3 of bulk density (BD), 83% of sintering shrinkage (SS), 1747% of water absorption (WA) and 1424 MPa of compressive strength (CS) could be obtained by the optimal conditions: 54:30:10:6 mass ratio of iron ore tailings: coal gangue powder: shale: sewage sludge, 20 MPa of molding pressure, Preparation, characteristics and mechanisms of the composite sintered
.jpg)
Using waterbased drilling cuttings from shale gas development to
2021年2月8日 The sintered bricks were sintered at 800 °C and maintained 1 h, and Fig 4 shows the influence of waste glass as an amorphous binder on the physicalmechanical performance of sintered bricks As the percentage of waste glass was increased from 0 to 30%, the weight loss on ignition decreased from 1452 to 816% and bulk density increased from 1785 to 1924 g 2021年10月1日 The present study introduces the preparation of thermal insulation geopolymer bricks using ferrosilicon slag and alumina waste Compressive strength, bulk density, cold and boiling water (PDF) Fabrication of Thermal Insulation Geopolymer Bricks Using 2018年11月10日 This study investigated the thermophysical and mechanical properties of biowasteadded fired clay bricks, which were sintered at two different temperatures in the framework of energy conservation Tea waste, sawdust and wheat straw were mixed with clay and fired to obtain fired clay bricks at sintering temperatures of 500 °C and 980 °C Physical Effect of sintering temperature on mechanical and thermophysical 2018年11月10日 Fig 8 Relationship between thermal conductivity, porosity (%) and density of brick samples sintered at 500 °C and 980 °C with the addition of a tea waste, b sawdust, c wheat stra w Journal of Effect of sintering temperature on mechanical and thermophysical
.jpg)
(PDF) Ceramic bricks with enhanced thermal insulation produced
2021年11月9日 The findings revealed that the inclusion of 20% eggshell to the samples sintered at 950 °C generated composite bricks with the lowest density (14 g/cm³) and thermal conductivity of 027 W/mk 2013年2月1日 Luo et al [32] produced composite sintered bricks using iron waste and coal gangue powder and found that when temperatures increased from 950 °C to 1150 °C, the bulk density of bricks increased The Preparation of Pavement Brick and the Research on Samples pressed from FA and FA+MW mixtures were sintered at low The varied characteristics of fired bricks are bulk density (160–1 the MDcontaining composites exhibited a three Relationship between porosity and bulk density of bricksIt can be observed from Fig 10 that the values of bulk density of burnt clay bricks incorporating SF additive varied from 1452 to 1570 kg/m 3 which is 743 to 1439% lower than the virgin burnt Thermal conductivity of fired clay bricks at 1000 o C
.jpg)
(PDF) The Effects of Sintering Temperature and Agro
2020年7月22日 In this research, kaolin, ball clay, sawdust and rice husk were used to produce insulation bricks through the solid state synthesis method Two temperatures, 1100oC and 1200oC were used to sinter 2024年9月28日 In the current work, aluminum dross from the aluminum industry and firedclay brick waste (Homra) were combined with alkaline activators (Na2SiO3/NaOH) with varying molarities of NaOH to create insulating Performance of Geopolymer Insulation Bricks 2020年4月1日 On the other hand, bricks containing 20 % aluminum dross and sintered at the same temperature exhibited the highest compressive strength (58 MPa), a bulk density of 19 g/cm3, and a water The effect of expanded perlite on fired clay bricks ResearchGateRS Refractory Bricks Factory recommends low thermal conductivity multilayer composite mullite bricks for the the service life The performance indicators of the working layer are Al2O3≥67%, apparent porosity≤20%, and bulk density 270 g To purchase refractory bricks, refractory castables, thermal insulation bricks, thermal Properties and Application of Low Thermal Conductivity Multilayer
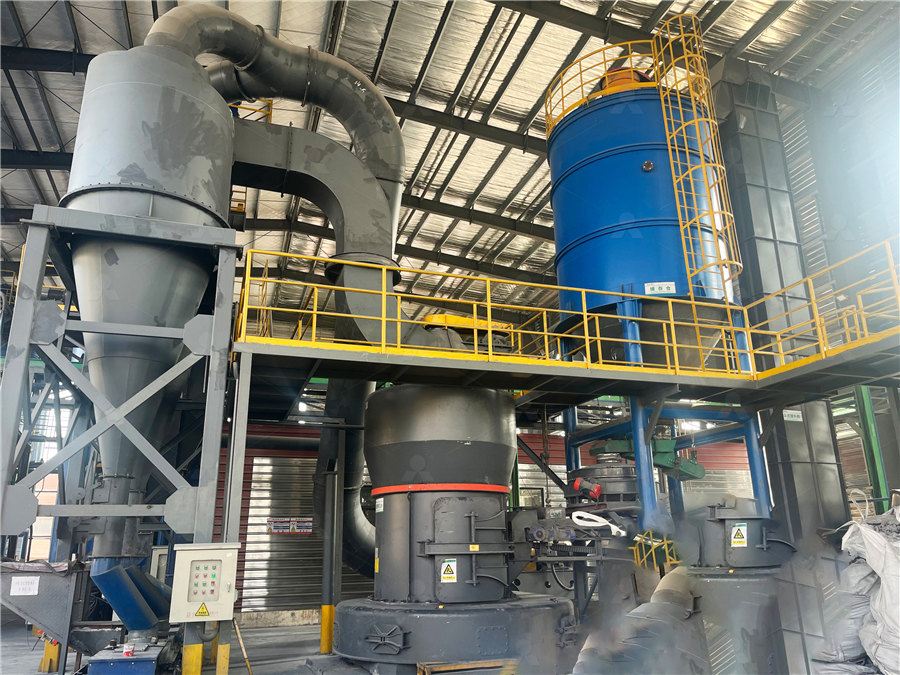
Enhancing the Thermal and Energy Performance of Clay Bricks
2024年3月8日 The bulk density of the bricks fired at 900 °C consistently decreased with increasing percentages of P florida waste, Z Thermal behavior of mesoporous Aramid fiber reinforced silica aerogel composite for thermal insulation applications: Microscale modeling J Appl Comput Mech 2024, 10, 140–151 [Google Scholar]2023年12月4日 The Relationship Between Porosity and Bulk Density in Refractory Bricks Porosity is the percentage of the pore volume contained in refractory bricks to the total volume of the product That is to say, the higher the bulk density, the smaller the porosity The apparent porosity of heavy refractory bricks is generally between 10% and 28%Relationship between Porosity and Bulk Density in Refractory BricksThe composite of construction waste brick powder and other building powder materials the volume density of regenerated sintered shale brick typically increases with the increase in temperature between 900 ℃ and 1100 ℃ when the but a high sintering temperature will cause the brick’s bulk density to drop and cause the over Effect of Sintering Temperature on Properties of Regenerated Sintered 25 Properties of Insulation Bricks Insulation bricks should have low bulk density, high porosity as a result the strength of the brick is low These brick also showed very low thermal conductivity and low heat capacity Typical property requirements of insulation bricks is provided in Table –I TableI Properties of insulation bricks 2 ServiceDevelopment of Low Bulk Density Fireclay Insulation Brick
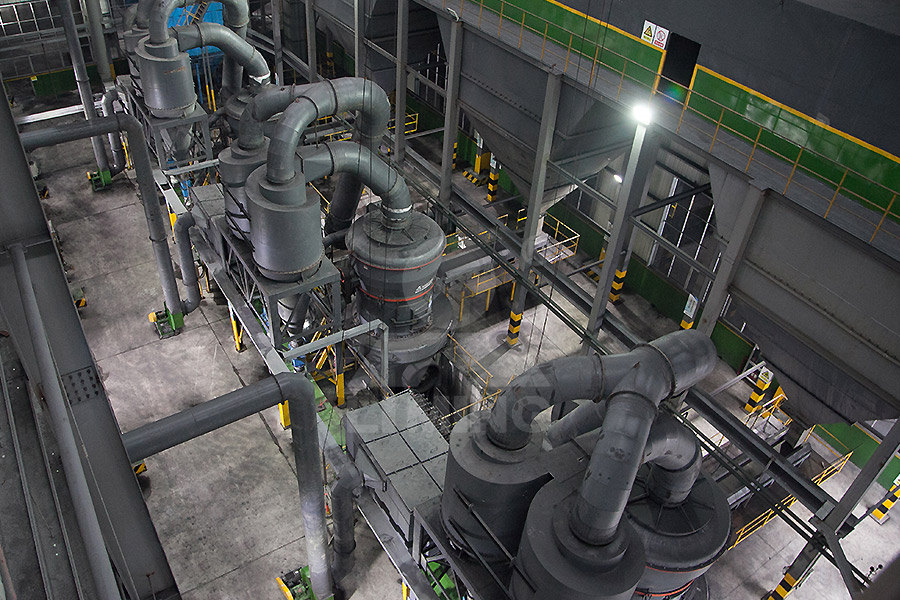
Characterization and performance evaluation of lightweight
2024年5月17日 Therefore, with the increase of EP and WA dosage under the same water–to–cement ratio, the dry density decreases linearly, of which the dry density decreased by 1149% on average when the EP dosage increased from 20 to 50%, and the dry density decreased by 1738% on average when the WA dosage increases from 20 to 40%, as shown 2022年1月4日 This study examined the production of porous and light clay bricks, which have low thermal conductivity and are made of a mixture of 10 wt%, 20 wt%, 30 wt%, 40 wt% pumice, 5 % expanded vermiculite, and clay Pumice and vermiculite were added to the raw material of the soil brick as additives to create pores and provide thermal insulation in the buildings via the Thermophysical and Mechanical Properties of Clay Bricks2018年2月1日 Effect of the insulation materials filling on the thermal performance of sintered hollow bricks under the airconditioning intermittent operation February 2018 Case Studies in Construction Materials 8(PDF) Effect of the insulation materials filling on the 2013年5月1日 The first refractory material on a base of 80% magnesia and 20% zirconium silicate was introduced in 1986 The intention was to solve problems in the condensation zone of checkersMagnesiazircon brick: Evolution of microstructure, properties
.jpg)
Preparation of tungstenparticlereinforced Zrbased bulk metallic
2024年1月17日 A new twostep spark plasma sintering (TSS) process with lowtemperature presintering and hightemperature final sintering has been successfully applied to prepare the tungstenparticle (Wp)reinforced bulk metallic glass composites (Wp/BMGCs) Compared to normal spark plasma sintering (NS), the densification rate and relative density of Wp/BMGCs 2013年1月1日 In addition, bulk density measurements showed that prepared brick samples can be classified as lightweight structures, as their bulk density is lower than 175 g/cm3Porosity–density relations in stone and brick materialsThe bulk density, sintering shrinkage, water absorption and compressive strength of the composite sintered bricks were tested to determine the optimum preparation conditions, including sludge content, molding pressure, sintering temperature and holding timePreparation, characteristics and mechanisms of the composite sintered 2020年10月2日 The pressed samples were left to dry at ambient temperature and later sintered in an electric muffle furnace at 1000 o C Properties such as bulk density, porosity, thermal conductivity and (PDF) Influence of Pore Nature on the Thermal Conductivity of
.jpg)
Preparation, characteristics and mechanisms of the composite sintered
2020年1月30日 The density of the fired brick slightly reduced with the RAS addition The thermal conductivity results suggest that RAS has better insulation properties compared to earth material The RAS sludge can be used in combination with earth material to fabricate fired bricks, which can meet the requirements of many Standards all over the World2022年1月7日 Bricks sintered at 1000°C met the IS:2042 standards for insulation bricks (IS2042, 2006) These results also show that the apparent porosity of sintered bricks is inversely proportional to the sintering temperature and increases with the addition of sawdust RM provides additional iron content, porosity decreases and density increasesApplications of Red Mud as a Masonry Material: A Review2018年5月15日 Densified silicon carbide (SiC) is prepared through dry pressing of SiC powder followed by pressureless sintering in the presence of boron carbide and carbon as the additives Sintering of SiC parts shows the increase in density with the increase in temperature (19502180 °C) by resulting in higher than 98% relative density (RD) at 2150 °C and above for 1 h Effect of Sintering Temperature on Density and Mechanical From the measurement, it is observed that the shrinkage value increases gradually with the increment of sintering temperature 34 Density Measurement Density in gm/cc 225 22 22 215 21 205 205 2 195 19 19 185 950 1000 1050 1100 Sintering Temperature 1150 in 0C 1200 Fig 4: Density of ceramic based brick composites sintered at Development and Evaluation of Various Properties of Ceramic Based Brick
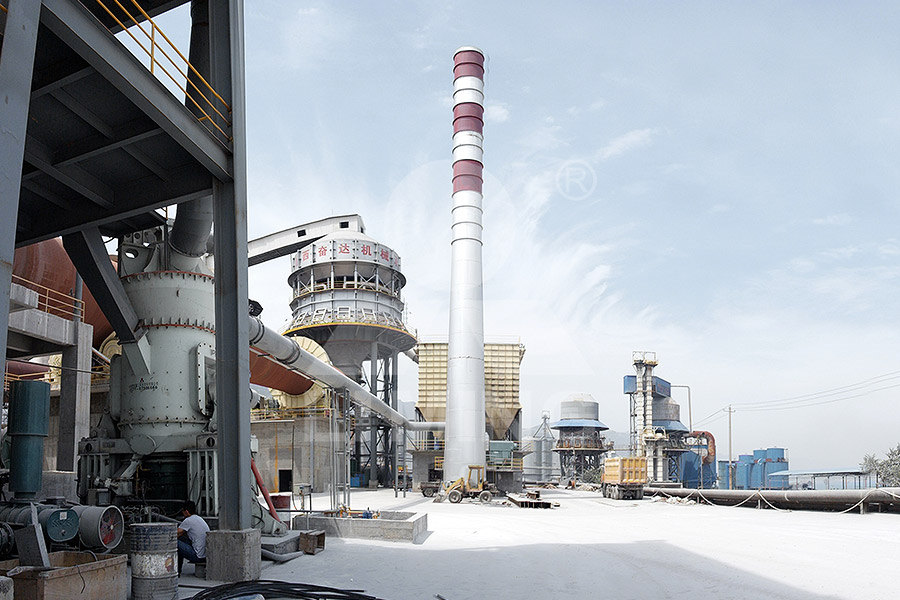
Hardened brick density of bricks Download
The findings revealed that the inclusion of 20% eggshell to the samples sintered at 950 °C generated composite bricks with the lowest density (14 g/cm³) and thermal conductivity of 027 W/mk 2019年7月3日 The impact value and 10% fines value are according to the methods specified in IS: 5640—1970 , and the properties of bricks such as compressive strength, water absorption and bulk density are determined by according to IS: 4139—1989 The brick, blocks and concrete were prepared by following methods and procedureRelevance and Assessment of Fly AshBased Sintered Aggregate The present study deals with the development of low bulk density 054 to 088 g/cc, high cold crushing strength 895 to 7997 kg/cm2 insulation brick using low cost raw materials In the present study river silt is used as low cost raw materials in the insulation brick formulation Effect of plastic clay to silt ratio on the proportion of insulation brick has been studied, and attempt Development of Low Bulk Density Fireclay Insulation BrickThe bulk density, sintering shrinkage, water absorption and compressive strength of the composite sintered bricks were tested to determine the optimum preparation conditions, including sludge content, molding pressure, sintering temperature and holding timePreparation, characteristics and mechanisms of the composite sintered
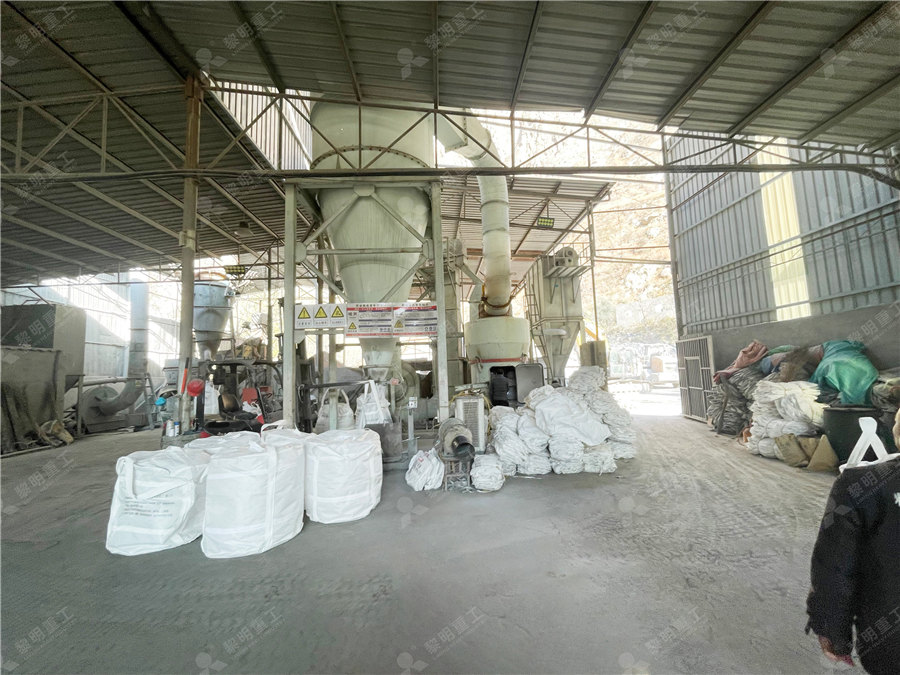
A comprehensive study of building materials and bricks for
2024年4月26日 The study found that CLC blocks have significantly lower bulk density than traditional clay bricks, Various mixtures of these materials were sintered at different temperatures A novel vermiculite/ vegetable polyurethane resincomposite for thermal insulation ecobrick production Compos B Eng, 221 (2021), 4) Bulk Density: The bulk density is generally considered in conjunction with apparent porosity It is a measure of the weight of a given volume of the refractory For many refractories, the bulk density provides a general indication of the product quality; it is considered that the refractory with higher bulk density (low porosity) will be Overview of Refractory Materials PDHonline2012年2月15日 The bulk density, sintering shrinkage, water absorption and compressive strength of the composite sintered bricks were tested to determine the optimum preparation conditions, including sludge content, molding pressure, sintering temperature and holding timePreparation and mechanism of the sintered bricks produced from Samples sintered at 1100oC had slightly higher bulk density and lower linear shrinkage compared to those sintered at a temperature of 1200 oC As the amount of kaolin present in the bricks decreased (increasing rice husk), the density of the samples decreased while the linear shrinkage values increased(PDF) The Effects of Sintering Temperature and Agro Wastes on

Insulating Firebricks Hard Firebricks Straights Custom Shapes
Insulating Firebricks, also known as fire brick, refractory brick, or IFB, are used in high temperature applications ranging from 2,000°F (1,093°C) to 3,000°F (1,649°C) Refractory bricks are manufactured from high purity refractory clays and other ceramic raw materials according to international standards, and are suitable to operate in various temperatures and atmospheres