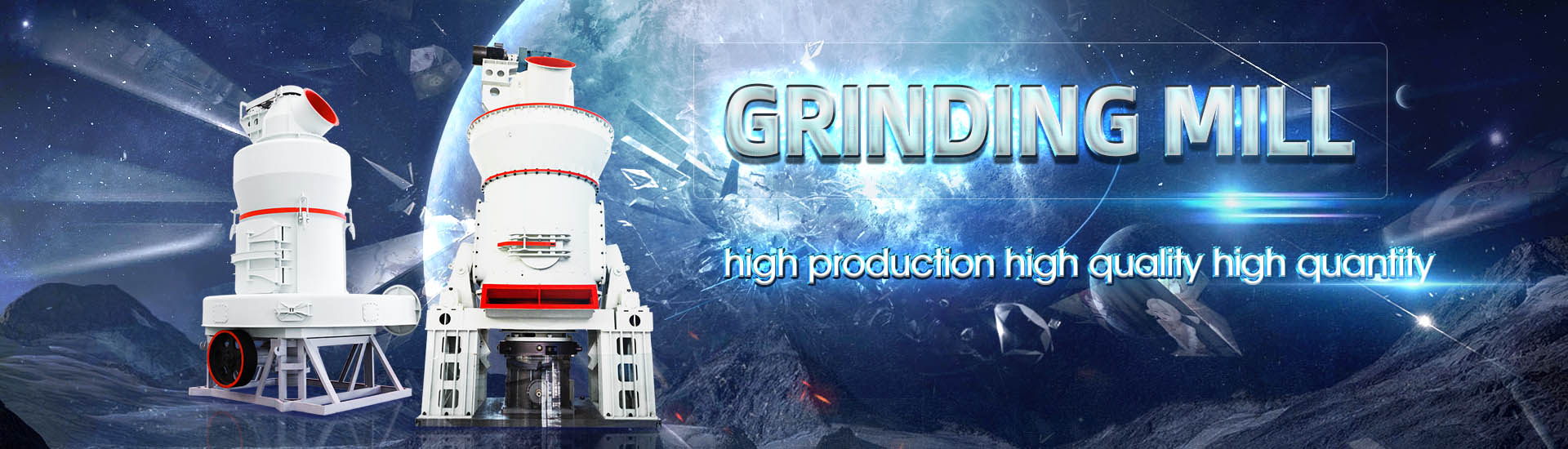
HOME→Aircoal ratio of coal mill in thermal power plant Aircoal ratio of coal mill in thermal power plant Aircoal ratio of coal mill in thermal power plant
Aircoal ratio of coal mill in thermal power plant Aircoal ratio of coal mill in thermal power plant Aircoal ratio of coal mill in thermal power plant
.jpg)
A Control Strategy of the Air Flow Rate of CoalFired
2020年11月25日 We use the proposed control strategies of the air flow rate and conduct an experiment in a 300 MWe coalfired power generation plant The Summary of air/fuel ratio in cases of different air and particle flow rate Complete combustion of coal fuel in thermal power plant is often achieved, by ensuring output of fineTable 5 Summary of air/fuel ratio in cases of different 2020年8月12日 This study shows the performance of a currently running vertical roller coal mill (VRM) in an existing coalfired power plant In a power plant, the coal mill is the criticalAn investigation of performance characteristics and Abstract: In a pulverized coalfired (PCF) thermal power plant (TPP), mixture of coal, air and gas is supplied into the furnace volume via the mill duct system and coal/airNUMERICAL AND EXPERIMENTAL INVESTIGATION OF A
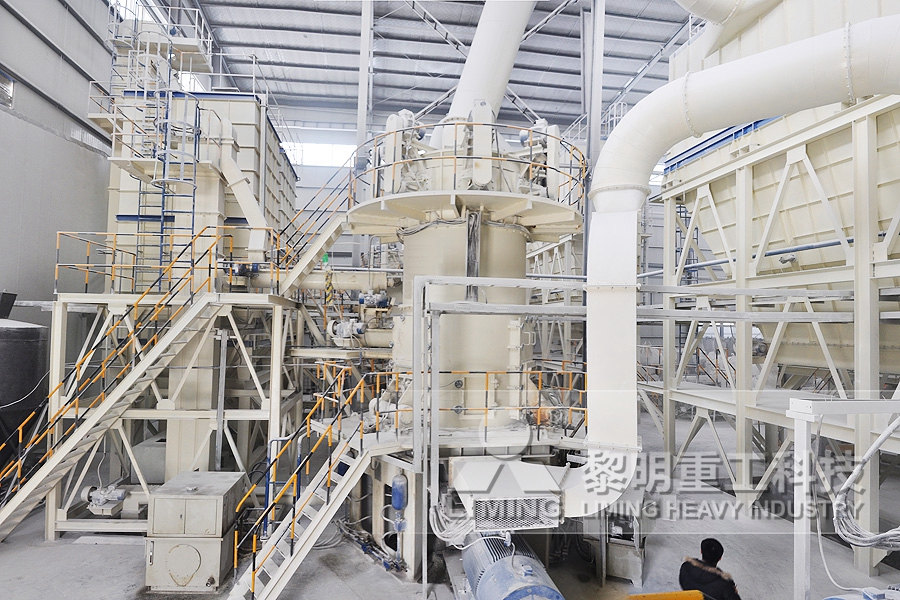
Thermal efficiency of coalfired power plants: From theoretical to
2015年11月15日 The study starts by calculating the maximum thermal efficiency for a specific coal feed in an ideal (reversible) power plant This efficiency will decrease when realistic For a reference power plant, the exergy of the coal feed is calculated to be 108 times the lower heating value The actual thermal efficiency is 455% The irreversibilities are caused by the combustion reaction, heat transfer between Thermal efficiency of coalfired power plants: From 2022年5月1日 A smart control layout for controlling energy generation at NTPL Thermal Power plant by effectively controlling the flow rate of coal, air and feedwater is made operational here Improvement in efficiency of thermal power plant using 2018年3月1日 Two advanced tools are combined for airfuel ratios monitoring per burner in large boilers They were tested in a 660 MW e coalfired power plant The measured ranges are Burner airfuel ratio monitoring in large pulverisedfuel boilers
.jpg)
Pulverised Coal Flow measurement in Thermal Power Plant
In coal fired power plants, pulverised coal (PF) flow from coal mills is to be measured accurately for maximising combustion efficiency and improved dynamic response to load2016年7月31日 In this research, a new method for determine the limit range or accurate value of PAR is suggested by making use of thermogravimetric analysis (TGA) and differential A Quantitative Method for Determining the Primary Air Ratio in Abstract: In a pulverized coalfired (PCF) thermal power plant (TPP), mixture of coal, air and gas is supplied into the furnace volume via the mill duct system and coal/air distribution should NUMERICAL AND EXPERIMENTAL INVESTIGATION OF A PULVERIZED COAL MILL Coal Mill in Thermal Power Plant Free download as Word Doc (doc / docx), PDF File (pdf), Text File (txt) or read online for free This document discusses coal pulverizers/mills which are critical components that convert the stored Coal Mill in Thermal Power Plant
.jpg)
Coal Mill in Thermal Power Plant: Enhancing Efficiency and
Understanding Coal Mills in Thermal Power Plants: Coal mills are largescale industrial equipment designed to pulverize coal into fine particles suitable for combustion in boilers These mills are typically used in thermal power plants to grind coal to the desired fineness, facilitating efficient combustion and maximizing the generation of They found optimum bleed steam temperature ratio and pressure ratio as 04 and 02–025 (irrespective of the number of heaters) Sengupta et al [154] presented exergy analysis of a coalbased thermal power plant using the design data from a 210 MW thermal power plant under operation in IndiaCoalFired Thermal Power Plant ScienceDirect TopicsPulveriser mill are one of the critical equipment of coal fired thermal power plant They are required to feed pulverized coal in required quality and quantity to meet boiler Optimized mill air to fuel ratio 4 Minimum fineness level: greater than or equal 75 percent passing 200 mesh and less than or equal 01 percent Pulveriser Mill Performance Analysis Optimisation in Superestimate the pulverised coal flow using real time onsite plant data 2 COAL MILL MODELLING In thermal power plant, pulverization of coal is carried out by coal mill Raw coal is moved from the storage to the mill by conveyor mechanism The type of coal mill envisaged for our model is bowl mill which is shown in Fig1Pulverised Coal Flow measurement in Thermal Power Plant
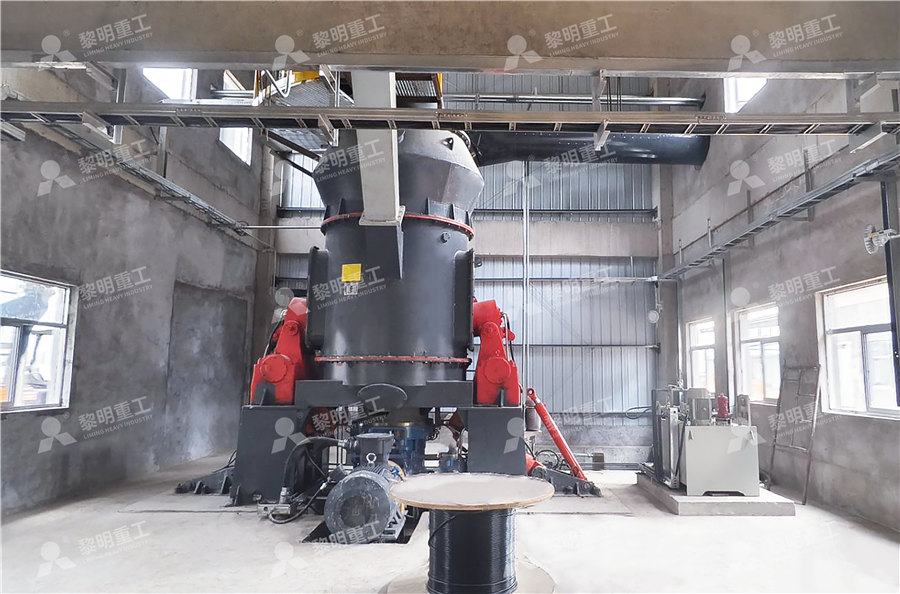
Understanding coalfired power plant cycles ICSC
6 IEACLEAN COAL CENTRE 2 Types of power generation cycles ratio raises efficiency up to a maximum, before it falls off as the compressor power requirement rises faster than the power developed by the turbine The optimum point lies at higher pressures as the turbine inlet temperature is increased As most gas turbines exit to atmosphere 1834 by increasing steam pressure to145 psig [9] Presently the efficiency of a coal based power plant is of the order of 40% Process description of a coalfired power plant In a coalfired power coal is burnt to produce electricity In a coalfired plant, pulverisers are used to mill the coal to a fine powder for burning in the combustion Auxiliary Power Analysis of a Coalbased Thermal Power Plant2021年11月15日 This work discusses the supercritical technology that has been instrumental in reducing pollution levels and quick load response from the thermal plant Various operating parameters such as main steam pressure and temperature; reheat steam pressure and temperature; excess air ratio for a given fuel, feedwater heater bleed steam pressure and Optimization and Analysis of Design Parameters, Excess Air Ratio, Section of coal bowl mill Table 1 Guaranteed coal conditions for mill performance evaluation Coal Moisture % 20 Coal HGI 55 Mill Outlet Temperarure °C 80 Mill Air Flow T/hr 102 Coal Fineness (% passing trough 200 mesh) 70% passing through 200 mesh and 90% passing through 50 mesh Differental Pressure 300 mmwc Coal Output from Mill 609 t/hrA Study on 500 MW Coal Fired Boiler Unit’s Bowl Mill
.jpg)
ENERGY AUDIT OF AUXILIARY POWER IN A COAL
2010年11月1日 efficiency of the coal fired thermal power plants are in the range of 1923 % (30 MW plant) and 3069 % (500 MW plant) T he auxiliary power consumption is varying between 7 % (500 MW plant) and 12 %A thermal power plant uses thermal energy from fuel to produce electric power Coal and air are burned in the furnace The overall efficiency of the steam power plant is defined as the ratio of heat equivalent of electrical output to the What is Thermal Power Plant? Basic, Definition, 2020年3月2日 Instead of dividing the total reference amount of coal into four equal parts and forwarding the information to the algorithm to determine the optimal distribution within each pair, first 1/7 of the total quantity was allocated to the mill coupled with the inactive mill (eg if mill M3 is inactive, mill M7 gets 1/7 of the total load), while the remainder of the total demand was One approach to temperature distribution control in thermal power plant In this paper, GA is applied to develop the coal mill model and to estimate the pulverised coal flow using real time onsite plant data 2 COAL MILL MODELLING In thermal power plant, pulverization of coal is carried out by coal mill Raw coal is moved from the storage to the mill by conveyor mechanism The type of coal mill envisaged for ourPulverised Coal Flow measurement in Thermal Power Plant
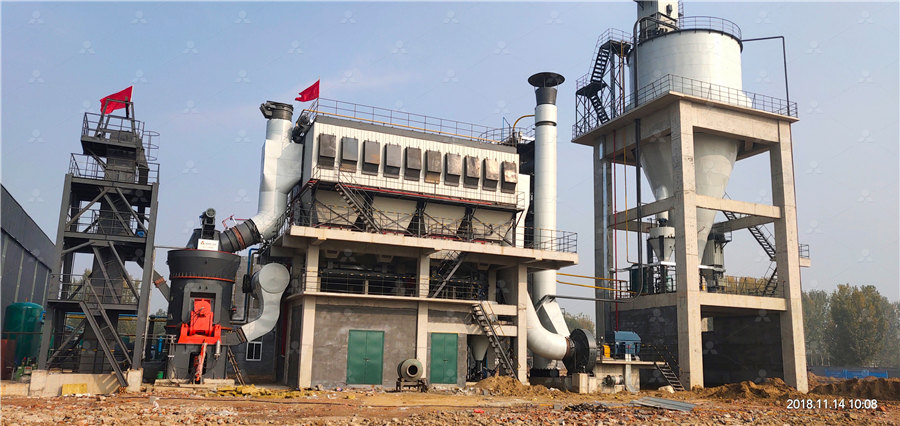
Flow Diagram of a Steam Thermal Power Plant Electrical4U
2012年2月24日 Key learnings: Thermal Power Plant Definition: A thermal power plant uses coal, air, and water to generate electricity based on the Rankine Cycle; Coal Circuit: The coal circuit involves transporting, cleaning, pulverizing coal into dust, burning it, and handling the resulting ash; Air Circuit: The air circuit preheats air, supplies oxygen for coal combustion, and carries 2022年5月1日 The durability of impact plates in the ventilation mill in the coal grinding facility was enhanced in the Serbian power plant Kostolac B, demonstrating an interesting technique to boosting the energy efficiency of coalfueled thermal power plants Improvement in efficiency of thermal power plant using 2015年10月1日 The ball tube mill requires less mass flow rate of primary air and raw coal per MW of power produced than the bowl mill It contains larger mass of raw and pulverized coal but less grinding heat (PDF) Control for pulverized fuel coal mill ResearchGate2016年7月31日 In a longterm time, the primary air ratio (PAR) is determined based on the empirical data in coalfired power plants and lack of theory With the TGDSC experiment of three different rank coals, a new method is proposed for quantitatively determining the PAR in coalfired power plant in terms of the theory of intensive ignition at the initial stage of coal combustion, at A Quantitative Method for Determining the Primary Air Ratio in Coal
.jpg)
Burner airfuel ratio monitoring in large pulverisedfuel boilers
2018年3月1日 In 2014, the share of electricity produced in the world from coal combustion was 408 % [1]While this share will need to be drastically reduced in the coming decades to reach the current CO 2 emission targets, it is nonetheless important to keep on increasing the efficiency of the existing assets worldwide in order to limit their global environmental impactWet flue gas loss loss due to moisture in fuel due to moisture formed by combustion of H 2 in fuel 6 Radiation Unaccounted losses (Dr VK Sethi,2011) III MAJOR ENERGY SAVING POTENTIAL AREAS IN THERMAL POWER PLANT Thermal power plant is designated sector as per EC act 2001 Most thermal power plant uses 3040% of energy value of primary To Improve Thermal Efficiency of 27mw Coal Fired Power Plant 2018年11月2日 SO 2 contribution to the ambient air is highest from coalbased power plant emissions as it depends on the sulfur content of coal used in these power plants However, Indian coal’s sulfur content (06%) is low compared to United States (10–18%) and Chinese coals (05–10%) (Guttikunda and Jawahar 2014 ; Reddy and Venkataraman 2002 )Atmospheric Emissions from Thermal (CoalFired) Power Plants 2011年1月1日 Compared with actual situation of the current thermal power plant, this paper studies operation process of coal handling system in thermal power plant Keywords: Thermal Power Plant; Coal Handling System; Belt Conveyor Corresponding author Tel: +0086432; fax: Operation and Maintenance of Coal Handling System in Thermal Power Plant
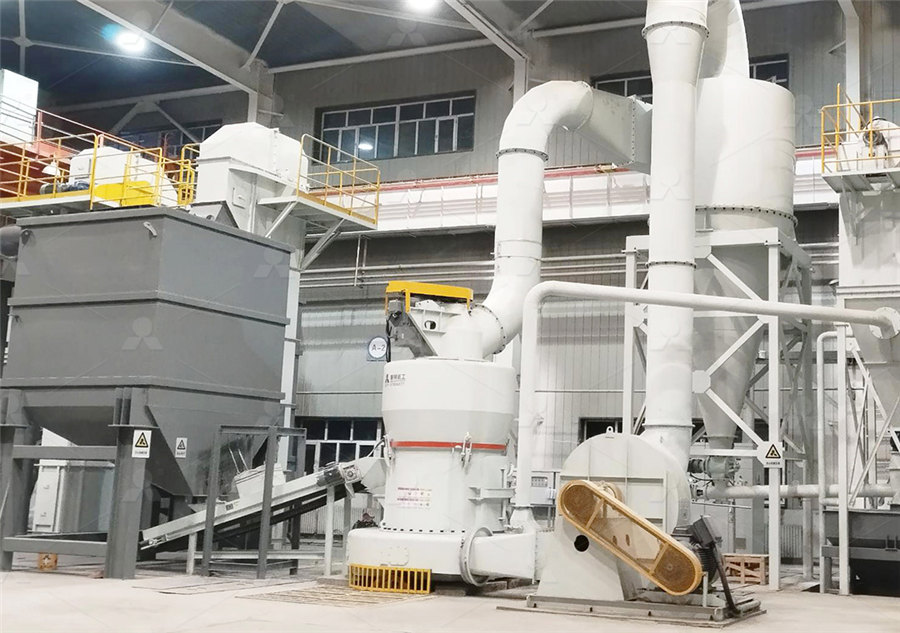
Thermal Power Plant Components, Working and
Sometimes, the thermal power plant is also known as a stealturbine power plant or coal power plant Related Post: Hydropower Plant – Types, Components, Turbines and Working; Working of Thermal Power Plant The thermal power PDF On Dec 1, 2015, M Siddhartha Bhatt published Effect of moisture in coal on station heat rate and fuel cost of Indian thermal power plants Find, read and cite all the research you need on (PDF) Effect of moisture in coal on station heat rate and fuel cost 2020年5月13日 Thermal Power Plant: Layout, Working, Elements, Advantages and More; Power Plant: Types, Factors, Choices and Terminology Used in Power Plant; What is Power Plant Economics? It’s Cost of Power Generation and Calculation; Various Stages in Coal Handling The various stages in coal handling are : 1 Coal DeliveryCoal Handling Plant [Layout] in Thermal Power GenerationIn this video you will get a live overview of ball and tube type coal mill used in thermal power plantLive Working of Ball and Tube Coal Mill in Thermal Power Plant/ Coal
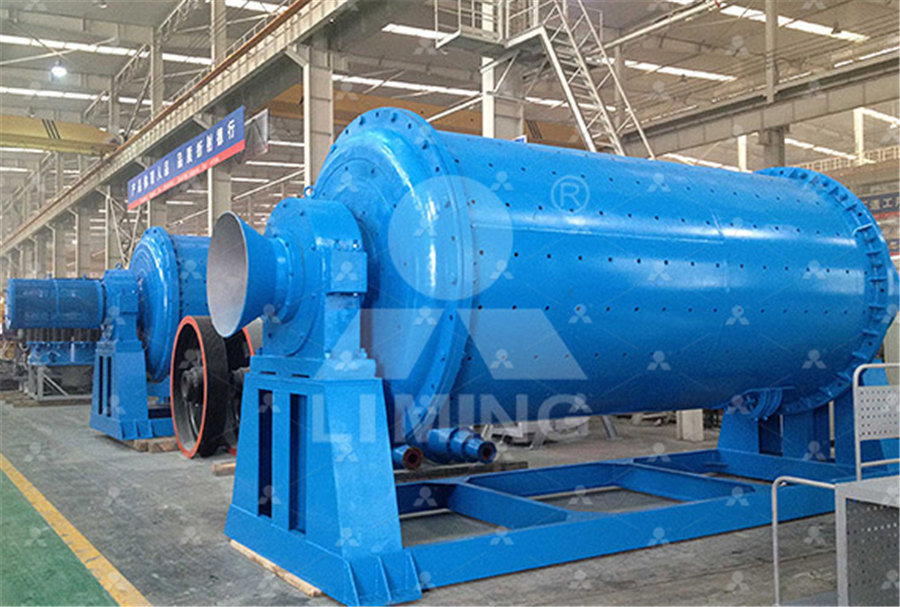
Coal Mills In Thermal Power Plant Documents and Ebooks
PRIMARY AIR FLOW Primary air provides the means to dry, classify, and transport the coal from the grinding zone of the mill through the classifier PF pipes to the furnace Two constraints for the PA flow are: • Ability to maintain the minimum air velocity (15–16 m/sec) to transport the coal • To maintain the correct air fuel ratio This paper reports the results of energy analysis of two 210 MW coalfired thermal power stations located a good distance apart A new and simple method for evaluation of thermal efficiency has been presented Measures for improvement in plantEnergy conservation in 210 MW coal‐fired thermal power plantsFig 1: Typical arrangement of a vertical bowl mill Primary air is admitted through the mill, which carries the finest coal particles to mill outlet The air and coal mixture passes through a classifier, located at the upper part of the mill, where an additional particle separation takes placeAnalysis of the Coal Milling Operations to the Boiler Parameters2018年5月2日 Coal mill malfunctions are some of the most common causes of failing to keep the power plant crucial operating parameters or even unplanned power plant shutdowns Therefore, an algorithm has been developed that enable online detection of abnormal conditions and malfunctions of an operating mill Based on calculated diagnostic signals and defined Detection of Malfunctions and Abnormal Working Conditions of a Coal Mill
.jpg)
Exergy analysis of a coal‐based 210 MW thermal power plant
2007年1月1日 Suresh et al (2010) carried out energy, exergy and environmental analyses of coalbased thermal power plant based on three configurations: subcritical, supercritical and ultrasupercritical cycle 2019年3月12日 It can be used for the sootblowing optimization in most coalfired power plant boiler with air preheaters Boiler main operation values Parameters of the functions in Figure 6(PDF) An Optimization Study on SootBlowing of Air 2020年12月8日 For instance, Liu et al (2020) have used the air to carbon, not air to coal ratio, and the total (primary + secondary) air flows might be considered instead of only the primary air as in our case (PDF) A Control Strategy of the Air Flow Rate of Coal 2016年10月1日 In a pulverized coalfired (PCF) thermal power plant (TPP), mixture of coal, air and gas is supplied into the furnace volume via the mill duct system and coal/air distribution should ideally be NUMERICAL AND EXPERIMENTAL INVESTIGATION OF A PULVERIZED COAL MILL
.jpg)
CFD Applications for Coal/Air Balancing in Power Plants
2006年9月1日 In a pulverized coalfired (PCF) thermal power plant (TPP), mixture of coal, air and gas is supplied into the furnace volume via the mill duct system and coal/air distribution should ideally be 2016年6月5日 1 Introduction Coal based thermal power generation accounts for more than sixty percent of the total power generated in India [1]With large reserves available, coal will be the predominant source of fossil energy, with thermal power stations continuing to be the largest consumer, utilizing about three fourth of the total coal produced in the country [2]Characterization of coal blends for effective utilization in thermal By pulverizing to a fine powder and being piped into different burners placed in the furnace of the boiler Large capacity power plant boilers use this method By circulating fluidized bed where large coal particles spread on to the bottom of the furnace and the air pressure from the bottom keeps it floating to give good combustion; Smaller units use grate firing where the coal is spread on a Coal Burners in Large Thermal Power Plants Bright Hub 2011年12月31日 Compared with actual situation of the current thermal power plant, this paper studies operation process of coal handling system in thermal power plantOperation and Maintenance of Coal Handling System in Thermal Power Plant
.jpg)
COMBINED IMPACT OF PRIMARYSECONDARY RATIO AND EXCESS AIR ON COAL
COMBINED IMPACT OF PRIMARYSECONDARY RATIO AND EXCESS AIR ON COALFIRED POWER PLANT PERFORMANCE Djarot B Darmadi 1 *, Nurdin Hasananto Teguh 1, Lilis Yuliati 1, Eko Siswanto 1, Marco Talice 2 1 Mechanical Engineering Department,Faculty of Engineering ,Brawijaya University Malang, Indonesia 2 PMSQUARED Engineering Srls, 2019年10月19日 In the thermal power plant where chemical energy of the coal is converted into electricity It is most demanding industry now days because of high energy demand Boiler is the most important part Performance analysis of boiler in thermal power plant