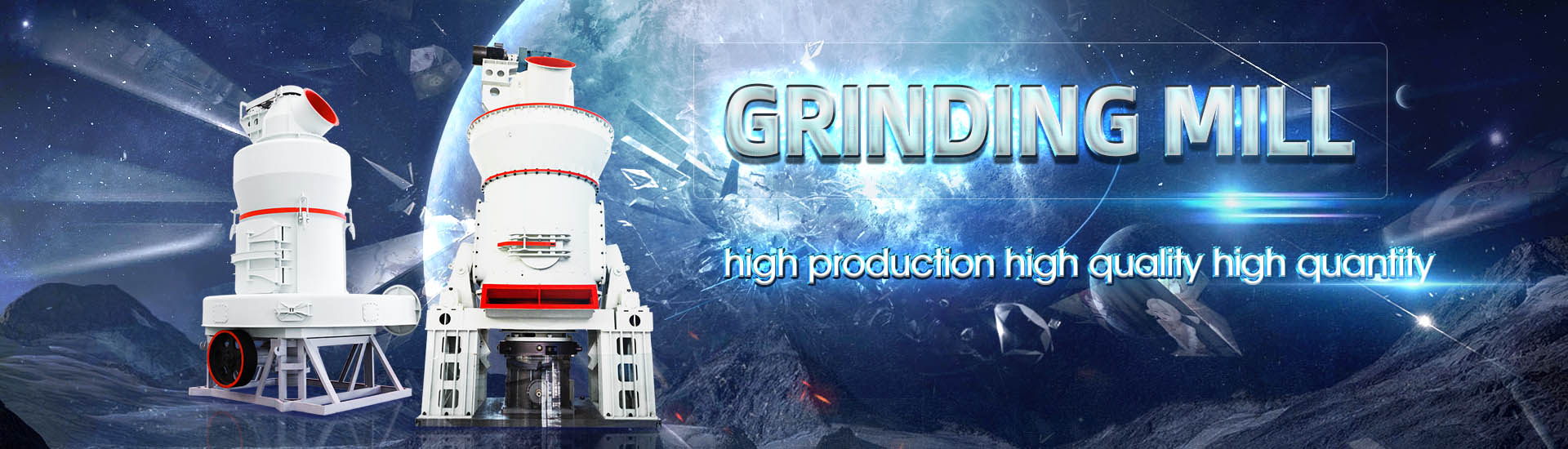
Minimum considerations for transfer of ore powder mill
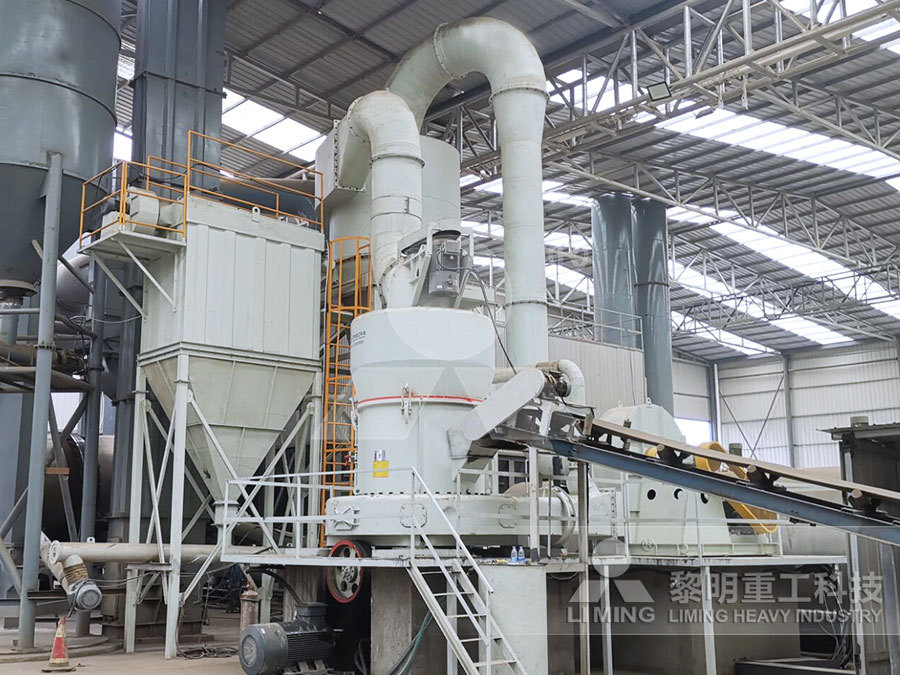
Towards waterless operations from mine to mill ScienceDirect
2022年9月1日 A conceptual diagram with considerations for selecting minetomill ore beneficiation technologies with lowwateruse or waterless focusAlkali activation of mine tailing can represent one of these low cost View Article2021年4月19日 Regarding this background, this article describes the feasibility of mine to mill optimization from three aspects: (1) different energy efficiencies between drillingblasting and(PDF) Feasibility and necessity of mine to mill ResearchGate2022年9月1日 To respond to the increased demand for commodities, increased volumes of primary ores need to be mined This could lead to major challenges with water and tailings (PDF) Towards waterless operations from mine to mill
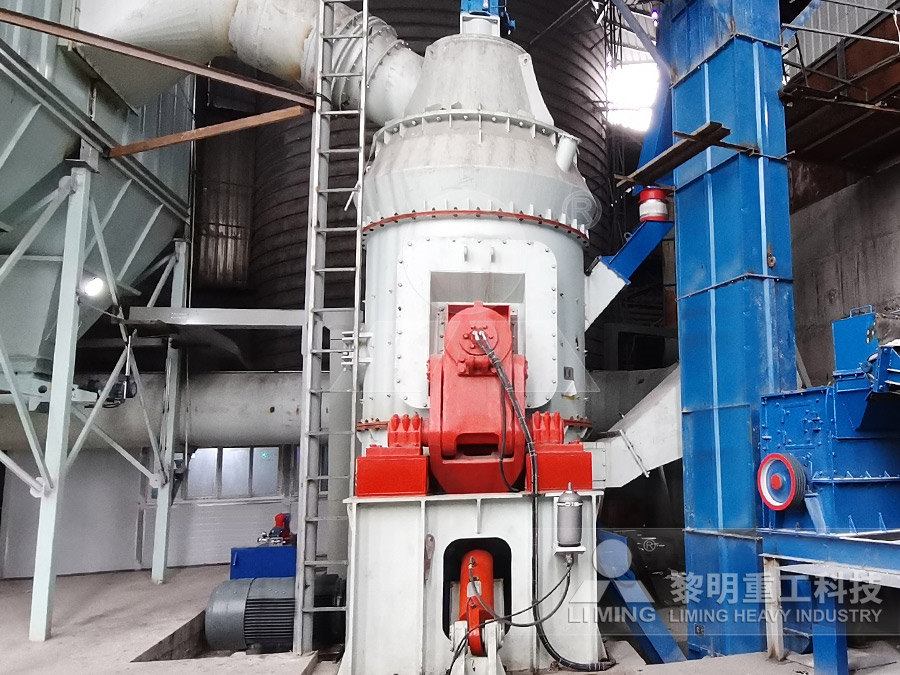
A CRITICAL REVIEW OF GRINDING DESIGN PROCEDURES FOR THE
2021年1月8日 For peak performance and balancing the power available in the SAG mill and ball mill, the transfer size must be measured and controlled The transfer size will be 500 microns Ore powder production involves the conversion of mined ore into fine particles through a series of crushing, grinding, and classifying processes The equipment used in this process must be Advancements in ore powder production process equipment: Mine to Mill is a site activity and each operation must determine which of the many Mine to Mill variants fits its needs and has the greatest potential to deliver benefits The old adage that UNDErsTaNDINg MINE TO MILL 911 Metallurgist2010年4月1日 Apart from the ore comminution, milling is also used for preparing materials for many industrial applications, such as milling of quartz to fine powder (under 70 μm in Powder Milling an overview ScienceDirect Topics
.jpg)
Fine grinding: How mill type affects particle shape characteristics
2017年9月1日 The findings of this work suggest that at the plant scale, UG2 ore particle shape characteristics within any particular size class are not significantly affected by grinding in an CRC ORE and Mine to Mill expert Don McKee released a publication entitled Understanding Mine to Mill The publication documents the history of Mine to Mill, explaining the concept in simple Understanding Mine to Mill CEEC (Coalition for Eco Efficient 2013年12月1日 Percent passing of milled Al 2 O 3 powder as a function of particle size for varying ball diameter Rotation speeds are (a) 50 rpm, 100 rpm, and (c) 153 rpmEffect of ball size and powder loading on the milling 2011年3月10日 Section snippets Materials used An antimonial refractory gold/silver ore sample obtained from Akoluk (OrduTurkey) was used in this work The ore sample was crushed down to − 4 mm using jaw and rolls crushers, and riffled to obtain 1 kg representative subsamplesThese were then ground in laboratory rod mill at 50% pulp density for 40 min (80% passing size, d 80 Optimization of some parameters of stirred mill for ultrafine
CFB石灰石脱硫剂制备——磨机公众号12.8 推送案例(8)53.jpg)
Development of design criteria for reducing wear in iron ore transfer
2019年9月15日 In Australia, the inclination of transfer chute walls when handling iron ore is typically at minimum angles of 65–70° to the horizontal An important reason for this categorical value widely accepted by industry is to prevent buildup and minimise the propensity for chute blockage and downtime during handling highly cohesive and adhesive ores2009年8月1日 Mill scale is an iron oxide waste generated during steelmaking, casting and rolling Total generation of mill scale at JSWSL is around 150 t/day and contains 60–70%FeO and 30–35%Fe2O3Recycling of steel plant mill scale via iron ore ResearchGate2015年7月1日 Hightemperature quench method, scanning electron microscopeenergy dispersive spectroscopy (SEMEDS), and thermodynamic analysis were adopted to study the effects of Fe2O3 on reduction process of Thermal Analysis Study on the Carbothermic Reduction of Chromite Ore 2004年1月1日 The iron ore sintering was characterized as a relatively uniform process of solid material, coke combustion, various modes of heat transfer, and the complicated physical changes of solid particlesModeling of Combustion and Heat Transfer in an Iron Ore
.jpg)
Powder grinding mills: Revolutionizing the manufacturing industry
Considerations for Optimization: 1 Mill Size: The size of the powder grinding mill should be selected based on the required production capacity and particle size Larger mills can handle higher throughputs, but they may require more energy and have higher capital costs 22007年1月1日 Animal feed is a major production cost of raising livestock and accounts for about 65 68 % of the total production cost, mainly ingredients and processing costsDesign Considerations for the Construction and Operation of METALLURGICAL CONSIDERATIONS ThermoMechanical Processing • Often referred to as ‘thermomechanical processing’ because metallurgical REVERSING ROUGHING MILL A Transfer Bar headed to the Coil Box (1125 in thick) 31 32 11/2/2020 17 Making, Shaping and Treating of Steel: 101Principles of Hot Rolling AIST1 Principles of milling bulk solids Milling is the action of reducing the size of particles thanks to a mechanical action The mechanical action is submitting the particles to a stress, under the stress, some cracks will appear and subsequently the particle will be broken in different partsSolids and powder milling Size reduction
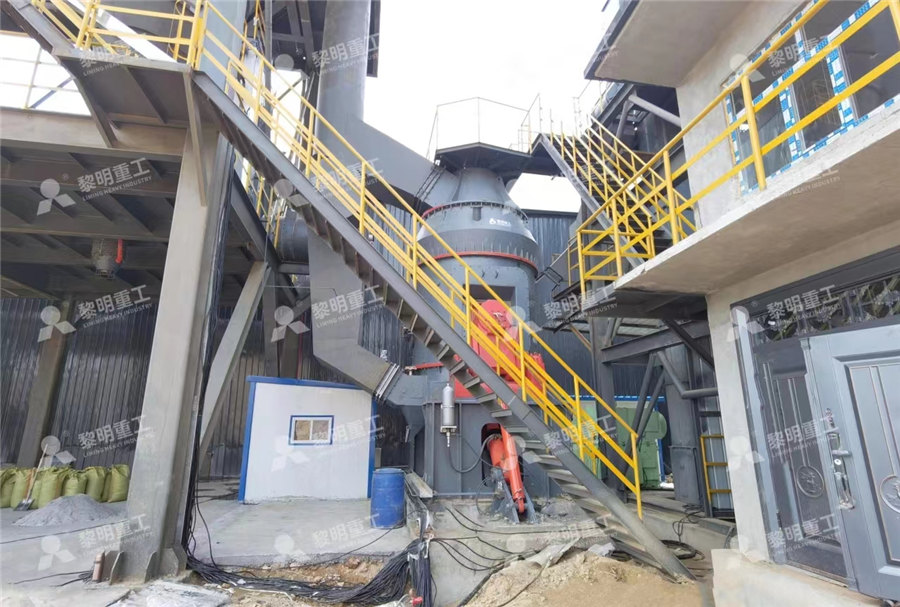
(PDF) Material handling and flowsheet selection
PDF On Nov 15, 2019, B Foggiatto and others published Material handling and flowsheet selection considerations for particlebased ore sorting Find, read and cite all the research you need on INTRODUCTION Amir R Khoei, in Computational Plasticity in Powder Forming Processes, 2005 15 Powder metallurgy technology Powder metallurgy considers the methods of producing commercial products from metallic powders by pressure Powder compaction forming is a material processing technique utilized to achieve a coherent neartonet shape industrial component Mixing of Powder an overview ScienceDirect Topics2014年5月8日 Historically, each town had their own mill, and the miller would operate for a portion of the finished flour This was the hub of each community, and remained that way for centuries The development of the roller mill in the Design Considerations for the Construction and 2019年1月1日 A grain size reduction hammer mill for crushing corn (Zea mays L) was designed depending on variety characteristics and by using computer aided design “ANSYS” softwareDesign and Evaluation of Crushing Hammer mill ResearchGate
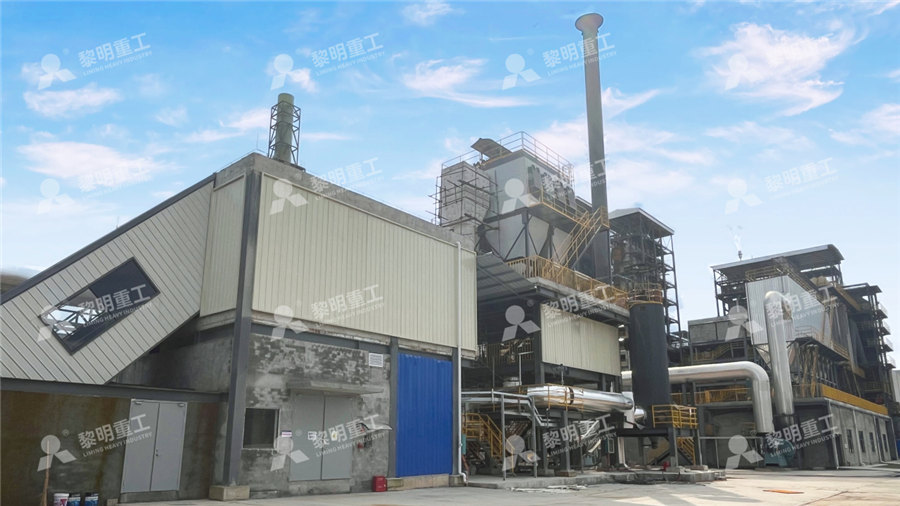
A CRITICAL REVIEW OF GRINDING DESIGN PROCEDURES FOR THE
2021年1月8日 • The transfer size will be 500 microns using a 12mm opening trommel This can be true under special conditions of operation when treating fine ore at high mill density, but in general the transfer size for such a trommel will lie in the range of 2 to 6 mm • Fine grinding in a SAG mill is less efficient than in a ball millFurthermore, in transfer and storage operations, dusts may experience pressures different from 1 atm Transfer of dusts may be performed through the powder transfer system (PTS), which is based on Different methods of powder transfer into a reactor2024年4月26日 The extracted ore is transported to the surface for further processing It's important to note that the choice between openpit and underground mining depends on various factors, including the depth of the deposit, the ore quality, environmental considerations, and economic feasibilityIron Ore Processing: From Extraction to Manufacturing2023年10月17日 Ultrafine powder mill (threering / fourring mediumspeed micropowder mill) feed particle size ≤25 mm, production capacity 0545 t/h, production fineness 1503500 mesh,it is a highefficiency and lowconsumption ultrafine powder processing equipment that successfully replaces the traditional jet mill and complex process ball mill grinding and powder selection, How to choose a suitable ore powder grinding mill?
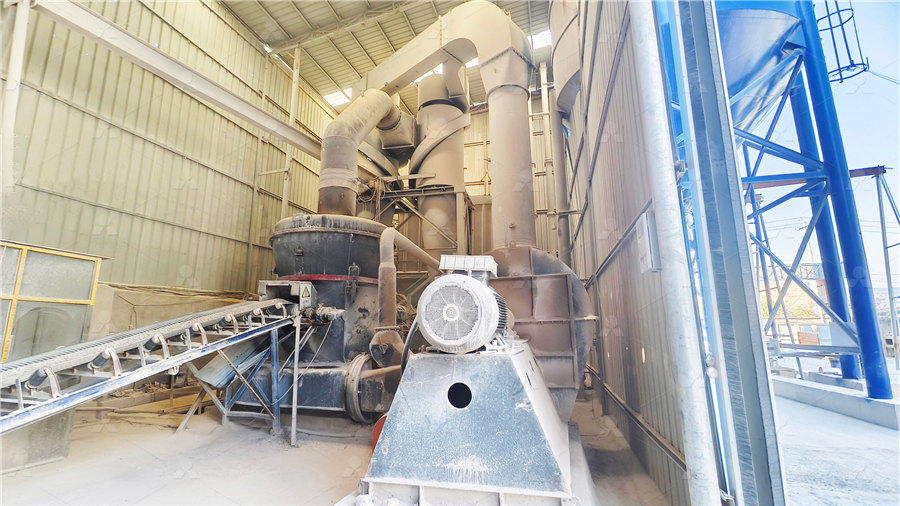
Grinding Mills and Their Types – IspatGuru
2015年4月9日 Typically, this type of mill can produce a product with a fineness of less than 01 mm Testing of materials is needed beforehand for determining the suitability of the ore for processing in an autogenous mill This type of mill has a distinct advantage of accepting coarse input material and supplying a relatively fine ground product2019年8月1日 The wet grinding processes were carried out in circuit operation mode The following mill geometries were used: an annular gap mill with pins (Advantis V 15, Bühler AG), a disc mill (PML1, Bühler AG), a pin mill (Labstar LS 1, Netzsch Feinmahltechnik), and an accelerator mill (NPM, WAB AG) These geometries are depicted in detail elsewhere [47]Mill, material, and process parameters ScienceDirect2013年4月1日 However, a lot of academic applications have been developed using Matlab/Simulink R le Roux et al (2013) proposed and validated a novel and simple nonlinear model, Sbárbaro (2010), Liu and Analysis and validation of a runofmine ore grinding mill circuit 2017年1月1日 An increase of over 10% in mill throughput was achieved by removing the ball scats from a single stage SAG mill These scats are non spherical ball fragments resulting from uneven wear of balls (PDF) Performance optimization of an industrial ball
.jpg)
Advancements in ore powder production process equipment:
Here, we delve into the key components and technologies that make up the modern ore powder production process Key Components of Ore Powder Production Equipment: 1 Crushers The initial step in ore powder production is the reduction of ore size, which is accomplished by crushers Jaw crushers, cone crushers, and impact crushers are commonly 2013年7月15日 The ball mill in closed circuit with hydrocyclones is an industry standard, and well known methodologies exist for equipment sizing, selection and designEnergy Efficient Ball Mill Circuit – Equipment Sizing Considerations2018年2月1日 In another study to investigate ball size distribution on ball mill efficiency by Hlabangana et al [50] using the attainable region technique on a silica ore by dry milling, a threeball mix of Effect of ball and feed particle size distribution on the milling it entered the mill (approximately 24 hour delay) Figure 8 shows how the crusher product % medium values match up with the mill feed 24 hours later Understandably, as the amount of critical size fed to the mill rose, the tonnage of one of the semiautogenous mills fell from 2000 tph to 1800 tph 10 15 20 25 30 35 40 45 50 Weight % Medium 1600 The Importance of Primary Crushing in Mill Feed Size Optimization
.jpg)
(PDF) Analysis of the Usability of Iron Ore UltraFines for
2022年4月6日 The essential theoretical considerations and processrelevant issues are provided for the usability of iron ore ultrafines for hydrogenbased fluidized bed direct reduction2015年11月26日 In the FeOSiO 2 diagram phase, the Fe 2 SiO 4 phase melts congruently at 1205°C, and it also forms under the eutectic reaction L → FeO + Fe 2 SiO 4 at the eutectic composition of 23 molar (PDF) Coproduction of DRI Powder and Semicoke from Siderite Ore 2017年2月1日 Three possible combinations of heat transfer coefficients were analyzed, from (1) Kapakyulu and Moys, (2) Duda and (3) the heat transfer laboratory of Universitat Politecnica de CatalunyaHeat generation model in the ballmilling process of a tantalum ore2020年5月14日 The concentration of lowgrade iron ores is vital to the continued availability of iron and steel in our everyday lives (Eisele and Kawatra, 2003;Kawatra and Claremboux, 2021a;Zhang et al, 2021)THE GROWING IMPORTANCE OF PELLETIZING FOR IRON ORE
.jpg)
Solids Choose the Right Grinding Mill Chemical
1 Ensure material is properly dispersed before adding to the mill This will help to prevent agglomeration and clogging of the discharge screen 2 Don't choke the mill by starting with solids content that's higher than the mill can process A 2012年9月27日 Eight optimization steps – pass schedule generation, work roll determination, backup roll diameter, mill type selection, mill window layout, mill housing dimension, roll profile calculation, and On the Optimization Procedure of Rolling Mill 2017年6月19日 2 C O N F I D E N T I A L OMTEC 2017 June 1315, 2017 Presented by: Ray DeFrain, Regional Metallurgist Midwest US /Canada Claudia Mumau, External Collaborations Manager Considerations for Metal Additive Manufacturing: Considerations for Powder 2023年10月27日 The ball mill is a rotating cylindrical vessel with grinding media inside, which is responsible for breaking the ore particles Grinding media play an important role in the comminution of mineral A Review of the Grinding Media in Ball Mills for Mineral Processing
.jpg)
Understanding metal powder requirements for Additive
2019年9月1日 Powder origins and characteristics Understanding how metal powders are made can inform an understanding of how they behave Metal powders are typically produced using an atomisation process, whereby the metal is heated until molten and either gas or water is jetted at the stream to break up the liquid into smaller particles2016年3月21日 where R represents the ratio: % Pb in crude ore/% Cu in crude ore Formula (32) is very convenient for milling calculations on ores of this type Example: An ore contains 5% lead and 1% copper The ratio of perfect concentration for a concentrate of maximum grade and 100% recoveries of lead and copper would be:Common Basic Formulas for Mineral Processing Calculations2013年9月27日 Roasting of refractory gold ores has been a commercial process for many years Improvements in design of fluidised bed roasting technologies and low capital and operating costs compared with other (PDF) Conditions and Design Considerations for ResearchGate2021年3月1日 MnZn ferrite and iron powder addition can effectively improve the dissipation of electric energy and magnetic energy, and reduce the “superior” thickness range (STR) of the composites 3% iron powder addition can decrease the STR from over 173 mm to 94–163 mm Taking the thickness of 115 mm as an example, the minimum RL and the mean RL of the Innovative methodology for cotreatment of mill scale scrap and
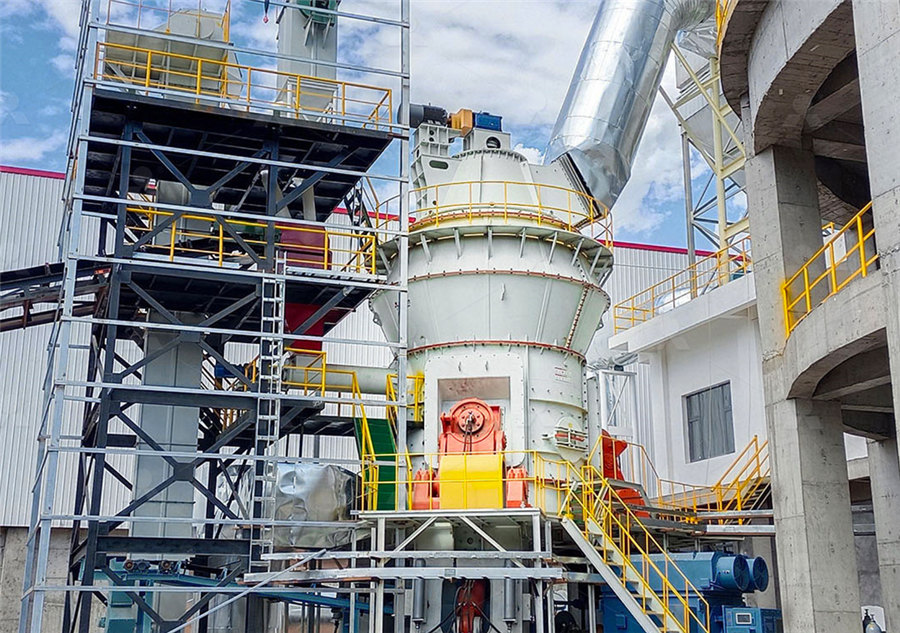
Sintering Properties and Regression Analysis of Imported Iron Ore Powder
2022年11月24日 In order to reduce the sintering allocation scheme and lower the cost of allocation, two semilignite ores with similar properties and large price differences were selected for blending to achieve the purpose of complementary advantages The sintered ore specimens were studied by using FactSage71, an infrared sintering furnace, and regression analysis Figure 1 Historical Face Powder First made popular in the 1930s, until recently, it's arguably lacked the finesse of modern makeup (like foundation) which, over the last decade, has been finetuned, finely milled and given a twentyfirst century makeoverAn Extensive Review of Face Powder Formulation Considerations