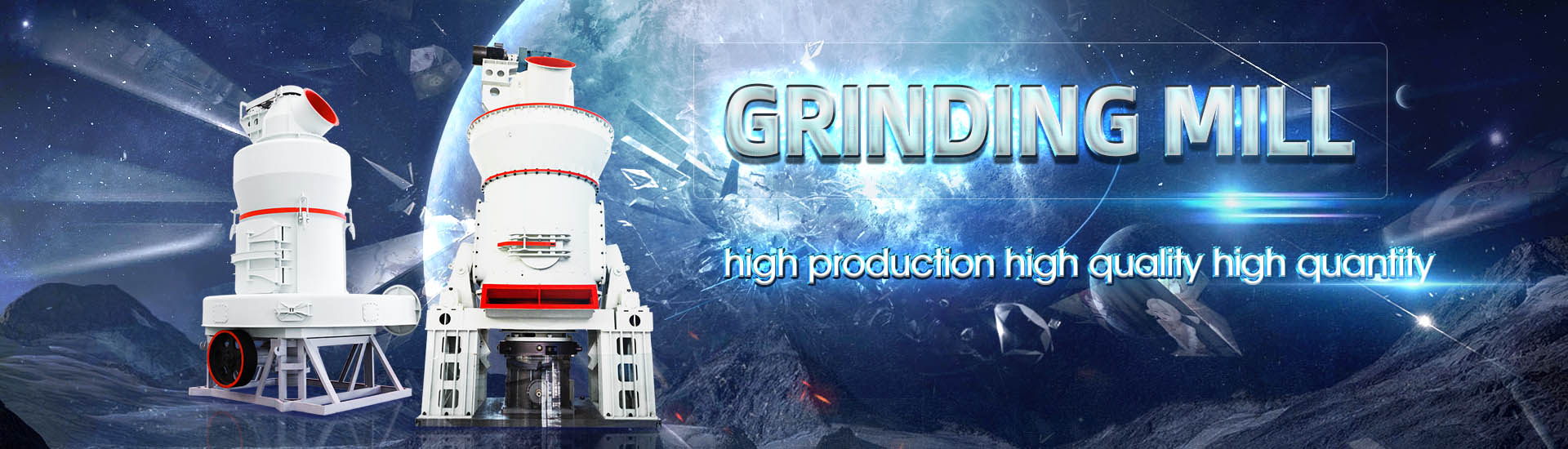
Northeast roasted spodumene mill ball mill
.jpg)
Aspects of Spodumene Lithium Extraction Techniques
2024年9月30日 In the study, the spodumene concentration (Australia) was crushed in a jaw crusher, processed in a ball mill, and screened to 200 mesh (less than 0074 mm) Known amounts of spodumene concentrate and NaOH spodumene may be milled using our ball mills and then transported to storage The beta spodumene is then dosed from storage to a mixer where concentrated sulfuric acid is mixed Lithium processing technology Complete solutions that FLSmidth2022年10月31日 Considering that the ball mill had a lowball mill loading (10%) in contrast to standard ball milling (50%), the ball mill was used to simulate a semiautogenous grinding millLithium deportment by size of a calcined spodumene ore2024年2月3日 Mechanochemical approaches are one of the most promising alternative lithium extraction processes Milling αspodumene in a planetarystyle mill for only 30 min drastically Mechanochemical Extraction of Lithium from αSpodumene at
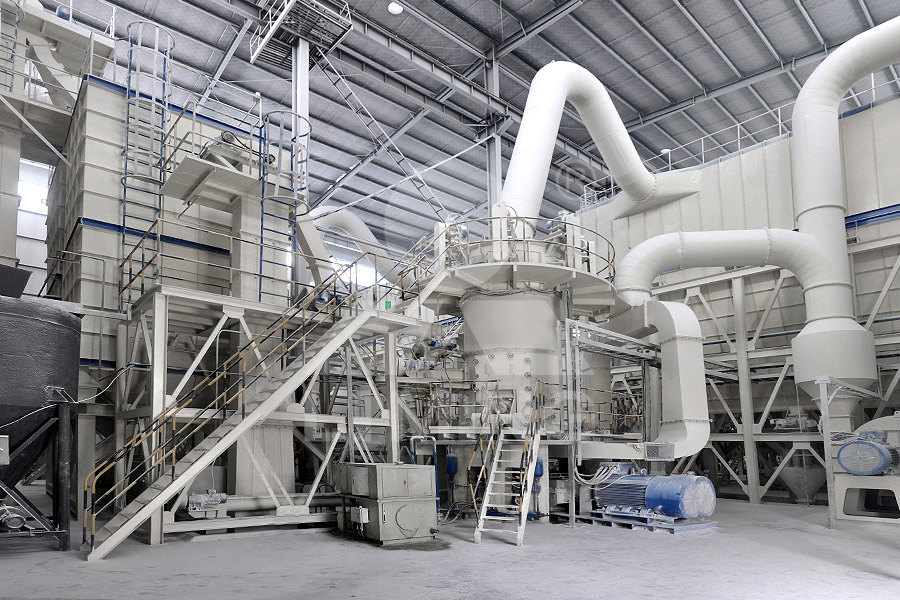
Direct Lithium Extraction from αSpodumene through
2024年7月9日 In this work, we report an alternative method to extract Li directly from αspodumene, which is performed at lower temperatures and avoids the use of acids It is shown that Li 2 CO 3 is formed with >90% yield at 750 °C by 2023年4月7日 To produce lithium carbonate with spodumene as raw material, the mature technology is the sulfuric acid production process in the industry 1 The spodumene concentrates obtained from ore dressing are first roasted in a Green Battery Minerals How to Get Lithium from spodumene concentrates after roasting and acid roasting operations A concentrate with at least 6% Li2O (approximately 75% spodumene) is suitable for roasting Roasting is performed at Hard Rock Lithium Processing SGSCalcination of spodumene is used to convert αspodumene to more reactive βspodumene, has been shown to greatly impact the physical characteristics of some of the components in the Lithium deportment by size of a calcined spodumene ore Nature
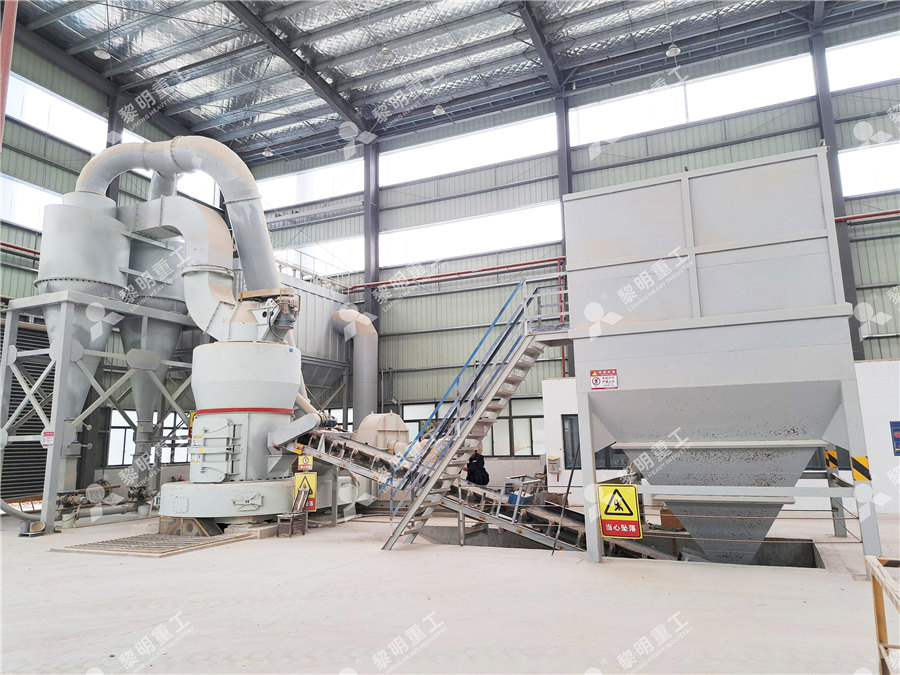
(PDF) Literature Review and Thermodynamic Modelling
2020年9月30日 The focus is on the pyrometallurgical pretreatment of spodumene Information on the phase transformation from α to β, the heat treatment methods as well as the behavior of various compounds in2015年4月24日 2 Ball mill consist of a hollow cylindrical shell rotating about its axis Axis of the shell horizontal or at small angle to the horizontal It is partially filled with balls made up of Steel,Stainless steel or rubber Inner surface of the Ball mill PPT Free Download SlideShareCalcined spodumene ( βSpodumene) is sent to the raw material warehouse by the conveying equipment after being cooled and crushed by the grate cooler, and the calcined materials are sent to the ball mill through the lower rod valve of News Which Spodumene Ginding Mill Is Selected 2024年11月21日 Spodumene (Kunzite) is a highquality mineral source for the industrial extraction of lithium But the beautifully colored and crystalclear Kunzite (emerald spodumene, purple spodumene) is used as a gemstone material Progress of Five Spodumene Beneficiation Methods
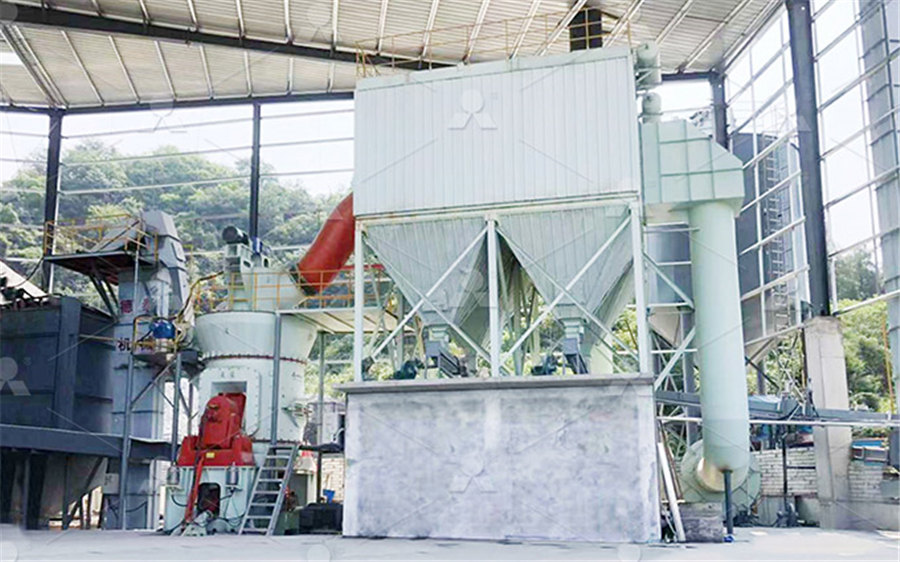
Ball Mills Glen Mills, Inc
The extremely high centrifugal forces of planetary ball mills result in very high pulverization energy and therefore short grinding times The PM 400 is a robust floor model with 4 grinding stations You may also be interested in the High Energy Ball Mill Emax, an entirely new type of mill forCubic Boron Nitride Ball End Mills for Tool Steel and Hardened Steel Make finishing cuts in tool steel and hardened steel with these cubic boron nitride (CBN) end mills Harder than carbide end mills, they’re better for making small, precise cuts and last more than five times as longBall End Mills McMasterCarr2015年6月19日 The basic parameters used in ball mill design (power calculations), rod mill or any tumbling mill sizing are; material to be ground, characteristics, Bond Work Index, bulk density, specific density, desired mill tonnage capacity DTPH, operating % solids or pulp density, feed size as F80 and maximum ‘chunk size’, product size as P80 and maximum and finally the type of Ball Mill Design/Power Calculation 911Metallurgist2013年8月3日 In Grinding, selecting (calculate) the correct or optimum ball size that allows for the best and optimum/ideal or target grind size to be achieved by your ball mill is an important thing for a Mineral Processing Engineer AKA Metallurgist to do Often, the ball used in ball mills is oversize “just in case” Well, this safety factor can cost you much in recovery and/or mill liner Calculate and Select Ball Mill Ball Size for Optimum Grinding
.jpg)
(PDF) Grinding Media in Ball MillsA Review ResearchGate
2023年4月23日 One of the most used tumbling mills is the ball mill [60] using ball and rod media, the flotation data indicated that the rodmilled spodumene has a This design uses heavy duty support rollers to drive the rotation of the mill shell directly Depending on the, the drive and support rollers can be polyurethane lined rollers or a series of rubber tyres Bulk Handling Techonolgies can design and supply roller mounted ball mills with capacities ranging from 500 kg/hr up to 25 TPH in a single millBall Mills and Ball Charging Bulk Handling Technologies2022年10月31日 Calcination of spodumene is used to convert αspodumene to more reactive βspodumene, The ball mill had 12 grinding balls (each grinding ball had 273 mm in diameter) Lithium deportment by size of a calcined spodumene ore2017年7月3日 How do you decide between using a ball mill or a rod mill? Many investigators have attributed the selective grinding of rods to line contact Other things should be considered In the two pairs of tests shown in table 12 the Ball Mills vs Rod Mills 911Metallurgist
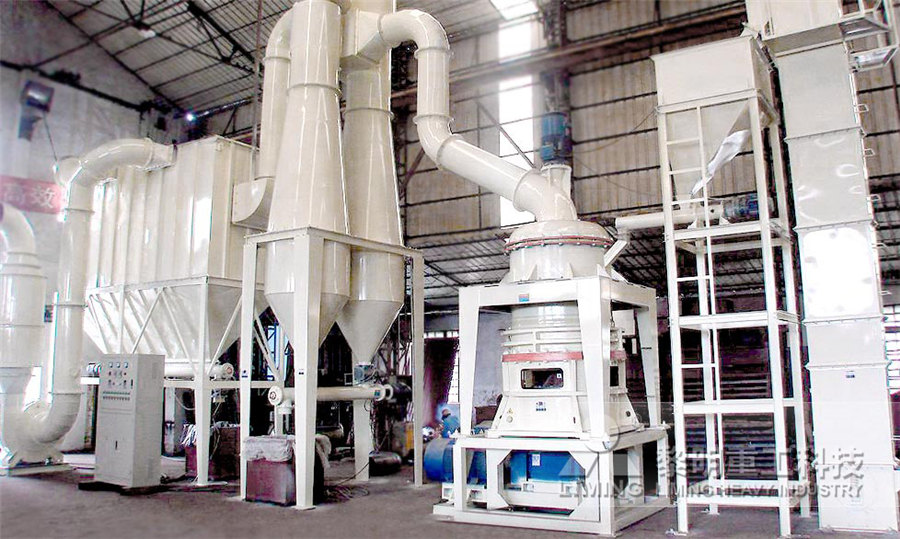
Grinding equipment for spodumene and spodumene
There are many different types of grinding mills, each with its own properties and uses In this article, we will discuss the properties of three common types of grinding mills: spodumene lepidolite mills, sandpaper grit mills, and ball milling Spodumene lepidolite mills are used to grind materials such as spodumene and lepidolite2016年10月20日 Am sure your Ball Mill is considered the finest possible grinding mill available As such you will find it is designed and constructed according to heavy duty 911 Metallurgist is a trusted resource for practical Ball Mill Maintenance Installation Procedure2023年11月7日 Crushing equipment includes jaw crushers, cone crushers, and impact crushers Grinding equipment such as ball mills, Raymond mills, or ultrafine mills is used to further reduce the particle size Beneficiation Equipment: Beneficiation equipment is used to separate spodumene from other minerals and impurities in the oreSpodumene Processing And Production EquipmentGrate discharge ball mills use a grating at the discharge end to control the flow of material out of the mill Batch ball mills are used for smallscale grinding operations C Advantages and Disadvantages Ball mills offer several advantages, including high capacity, low maintenance, and the ability to grind a wide range of materialsWhat is the Difference Between Tumbling Mill and Ball Mill?
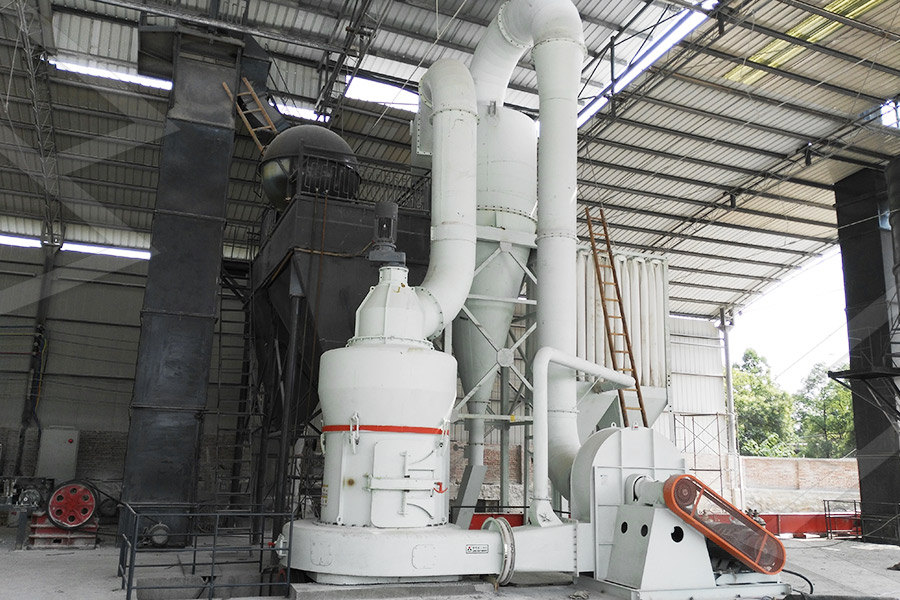
A comparison of wear rates of ball mill grinding media
2016年1月1日 The Ball Mill Abrasion (BMA) test was developed by the University of Queensland Materials Performance group to simulate the high stress abrasion conditions experienced in production ball millsBall mills are used in grinding various kinds of materials They use impact to break the material into smaller pieces The ball mill is a type of grinder that uses balls to do this It has an inlet where the material is put in and a outlet where the balls come out Calculating the Grinding Efficiency of a Grinding efficiency of ball mill calculating equationBall mills are horizontal rotating cylindrical or conical steel chambers, approximately one third to half full of steel, alloy steel or iron balls, like that shown in Fig 410 A–C, or flint stones The size reduction is accomplished by the impact of these balls on the material as they fall back after being lifted by the rotating chamberBall Mill an overview ScienceDirect TopicsBall Mill, Working Principle, Types, Parts, Applications and Advantages Ball Mill Grinding Machines: Exploring the Working Principle, Types, Parts, Applications, Advantages, and Recent Developments Ball mill grinding machines are widely used in various industries for the comminution of materials into fine powdersBall Mill Grinding Machines: Working Principle, Types, Parts
.jpg)
Ball Mills 911Metallurgist
2017年2月13日 The apparent difference in capacities between grinding mills (listed as being the same size) is due to the fact that there is no uniform method of designating the size of a mill, for example: a 5′ x 5′ Ball Mill has a working diameter of 5′ inside the liners and has 20 per cent more capacity than all other ball mills designated as 5′ x 5′ where the shell is 5′ inside diameter and 2023年9月18日 This index is determined on a laboratoryscale using a Bond ballmill and by simulating dry grinding in a closed circuit until the 250% circulating load has been obtainedBond´s work index estimation using nonstandard ball millsBM400 Mixer/Mill® (part # 8000M) HighEnergy Ball Mill Highenergy ball mill that grinds up to 10 grams of sample Wide selection of grinding and mixing vials available including hardened steel, stainless steel, tungsten carbide, alumina ceramic, zirconia ceramic, silicon nitride, agate, polystyrene, methacrylate, polystyrene, and polycarbonateMixer/Mill – highenergy ball mills, mechanical alloying, mixing 2013年8月19日 The present review focuses on the insight into several parameters like properties of grinding balls, the filling ratio or revolution speed, and some general guidelines to follow for modelling processes in planetary ball mills in terms of refinement, synthesis' yield and contamination from wear Planetary ball mills are well known and used for particle size Process engineering with planetary ball mills Semantic Scholar
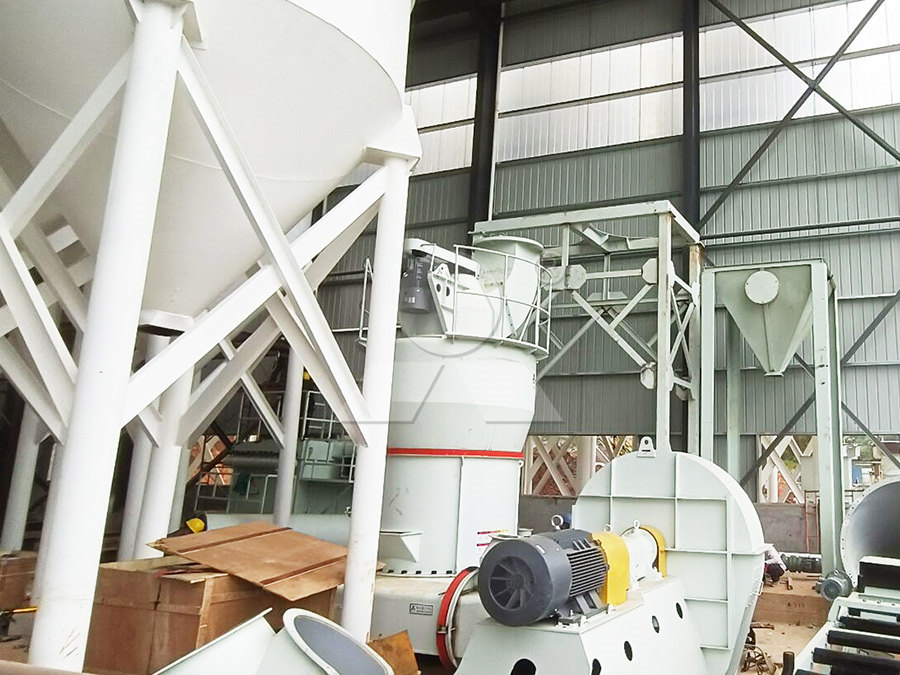
Ball Mills Orbis Machinery
Ball Mills Steel Ball Mill Lined Ball Mill Since the late 1800s, the ball mill has revolutionized industrial grinding processes, establishing itself as the gold standard in particle size reduction The basic construction of a ball mill is a cylindrical container with journals at its axis Inside this cylinder, grinding media – composed of ceramic, metallic balls, or rods – fills the spacespodumene refining operation – from advanced equipment, to islands, to total process flow solutions Spodumene conversion flowsheet Partnership provided ALPHA SPODUMENE CONCENTRATION FLSMIDTH® ROTARY KILN FLSMIDTH ROTARY DRYER LITHIUM CARBONATE FULLERTRAYLOR® BALL MILL ACID ROASTER LITHIUM SULFATE Lithium processing technology Complete solutions that FLSmidth2015年7月28日 Ball Mill TRUNNION BEARINGS Swivel type leadbronze bushed trunnion bearings are generally furnished on large diameter ball Mills The bearing swivels are of Meehanite metal spherically turned outside and bored and faced inside to receive the removable bushing The bushing is bored and scraped to fit the mill trunnionTrunnion Bearing Assembly Ball Mill Rod Mill 911Metallurgist2019年6月30日 According to the properties of spodumene, Fote Machinery develops an advanced ball mill with obvious strengths Unique Strengths of Spodumene Ball Mill Made of super wearresistant material in its bearing, steel ball and wheel gear, there is more than 3 times improvement on abrasive resistance of the spodumene ball millSpodumene Ball Mill Fote Machinery(FTM)

Effects of Mill Speed and Air Classifier Speed on Performance of
2021年6月29日 Nowadays, ball mills are widely used in cement plants to grind clinker and gypsum to produce cement The research focuses on the mill speed as well as air classifier speed effect on the two 2022年2月28日 Some investigations demonstrate that stirred mills (compared to ball mills) have better performance when grinding occurs on a micronscale This improvement is because the mechanism of supplying energy during stirred milling is different from what happens in ball mills In ball mills, the abrasive and impact stress lead to particle breakageGrinding SpringerLink2019年8月14日 Ball mill is a common grinding equipment in concentrator Common Types of Ball mill back to top The common industrial ball mills mainly include cement ball mill, tubular ball mill, ultrafine laminating mill, cone ball mill, ceramic ball mill, intermittent ball mill, overflow ball mill, grid ball mill, wind discharge ball mill, double bin ball mill, energy saving ball millThe Ultimate Guide to Ball Mills MiningpediaIf a ball mill uses little or no water during grinding, it is a ‘dry’ mill If a ball mill uses water during grinding, it is a ‘wet’ mill A typical ball mill will have a drum length that is 1 or 15 times the drum diameter Ball mills with a drum length to Ball Mill (Ball Mills Explained) saVRee saVRee
.jpg)
What ball mill should I buy? Pyrotechnics APC Forum
2023年6月19日 If you are new to this and are just starting out, then you are in the same boat I was in not that many years ago I was looking for the cheapest solution I could find (realizing that itay take me longer to achieve the same result as others with homemade or more expensive ball mills), and I just wanted something that would work (not be the best at it)Ball mills are ideal for achieving uniform particle sizes and are essential in material processing applications FAQ What factors should I consider when purchasing a used ball mill? Consider the mill's age, condition, capacity, and previous usage Check for any signs of wear, damage, or necessary repairsUsed Ball Mills for sale in USA Machinio2023年2月15日 What should we do to solve those problems? 1 First of all, it is necessary to do analyses including changes of nature of the ore, whether the amount of ore, water, sand and overflow size are normal Then do the measures to deal with them 2 Reduce the amount of feed to the mill until the working state of the ball mill returns to normal; 3 Appropriately reduce the 17 Signs of Problems with Ball Mills: Quickly Remove Hidden Troubles2022年3月15日 These mills consume enormous amounts of electrical energy (5060%); consequently, comminution costs roughly 60% of the overall investment in a beneficiation plant [2,3](PDF) Power consumption management and simulation of
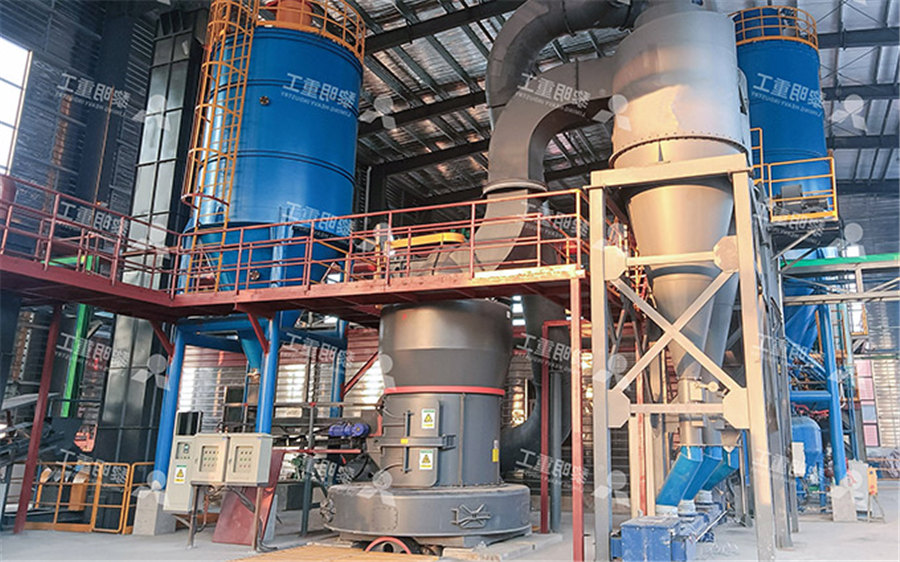
A Review of the Grinding Media in Ball Mills for Mineral
2023年10月27日 The ball mill is a rotating cylindrical vessel with grinding media inside, which is responsible for breaking the ore particles Grinding media play an important role in the comminution of mineral ores in these mills This work reviews the application of balls in mineral processing as a function of the materials used to manufacture them and the mass loss, as Table 1 Chemical composition of typical grinding media (% wt) Adapted from [24] 211 Cast Iron Cast iron can be grey cast iron or white cast iron, but white cast irons are commonly used in Grinding Media in Ball MillsA Review ResearchGate32 OK Mill™ The OK Mill™ was initially developed for the cement industry and is an ideal candidate for lower throughput mining applications, especially in scenarios where the ROM ore has less than 3% moisture The OK Mill™ is designed to produce material suitable for flotation without water addition When compared to a ball mill,Lithium Shakeup: An alternative crushing and grinding circuit for 2013年7月24日 Let’s compare! Rubber Liners are better for abrasion grinding ie: cascade action but not for cataract mills The graph below shows the increased operating cost of rubber and steel liners as the grinding ball size increases Larger mill, larger ball increases the cost benefit of using steel only mill pare the Benefits of Steel VS Rubber/PolyMet Mill Liners
.jpg)
(PDF) Energy Efficient Ball Mill Circuit – Equipment Sizing
2013年7月15日 PDF The ball mill in closed circuit with hydrocyclones is an industry standard, and well known methodologies exist for equipment sizing, selection and