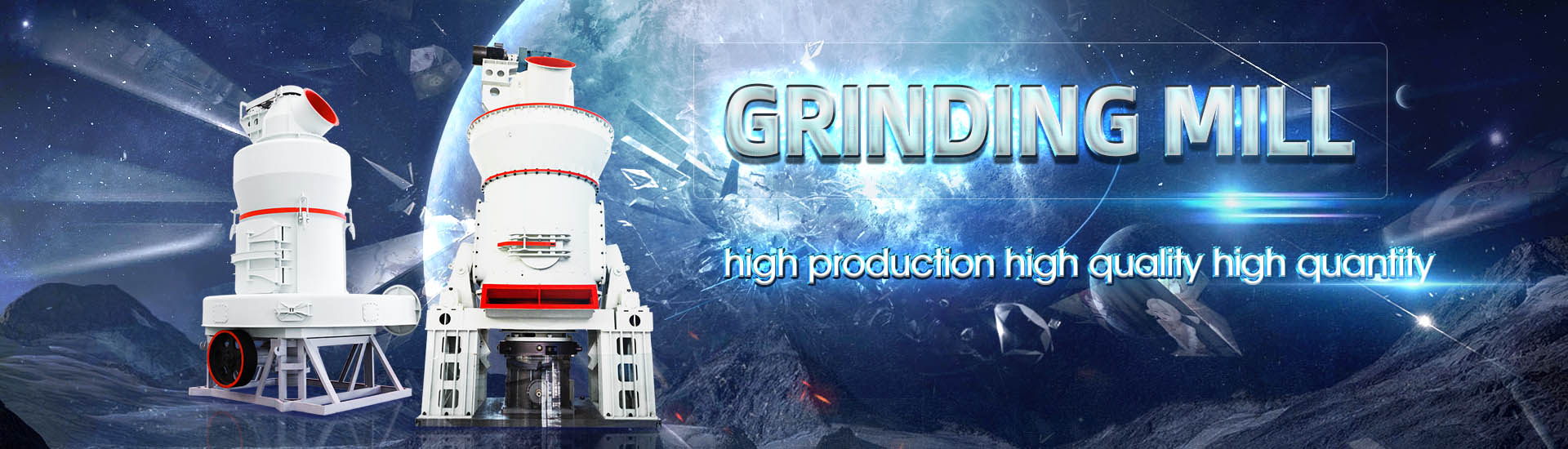
Highenergy ball mill model
.jpg)
Modelling of the HighEnergy Ball Milling Process
2021年1月1日 In this paper, the milling parameters of high energy ball mill (Fritsch Pulverisette 7) like vial geometry, number and size of balls and speed of the mill were modelled and discussedHigh energy ball milling (HEBM) is known as an economic, simple and yet powerful method for the production of nanostructured and Optimization of the high energy ballmilling: Modeling and 2017年7月5日 Our simulation reveals that the ball milling velocity, ball volume fraction inside the canister, ball size, and impeller shaft design all have impacts on the degree of powder Modeling and Analysis of HighEnergy Ball Milling Through Attritors2016年4月1日 High energy ball milling (HEBM, the suitable milling time was 2 h) can reduce the particle size and make it uniform, also can improve the color properties of pigments The Optimization of the high energy ballmilling: Modeling and
.jpg)
DEM Modeling and Optimization of the High Energy Ball Milling
This present work focuses on DEM simulations of a scale laboratory planetary ball mill through DEM Altair 20212 software to optimize and modulate the milling parameters The simulation show a good agreement with the experiments The numerical model is shown to be a promising tool for the knowledge of dry milling in a planetary ball mill KeyWords: Highenergy ball milling, Simulation, Optimization, Parameters, Modeling Received: June 5, 2021 Revised: March 11, 2022 Accepted: April 13, 2022 Published: June 29, 2022DEM Modeling and Optimization of the High Energy Ball MillingThe BM400 Mixer/Mill (part #8000M), is a highenergy ball mill that grinds up to 02 10 grams of dry, brittle samples (115V) or 875 cycles/minute (230V) Alternate pulley supplied with 230V model for 1060 cpm operation BM400 Mixer/Mill ® (part # 8000M) HighEnergy High Energy Planetary Ball Mill High Energy Planetary Ball Mill Model List Model: FP 2000: FP 4000: Working Principle: impact force: friction force: Feed material: hard / mediumhard / brittle / moist / fibrous: Applications: nano High Energy Planetary Ball Mill 엘엠테크
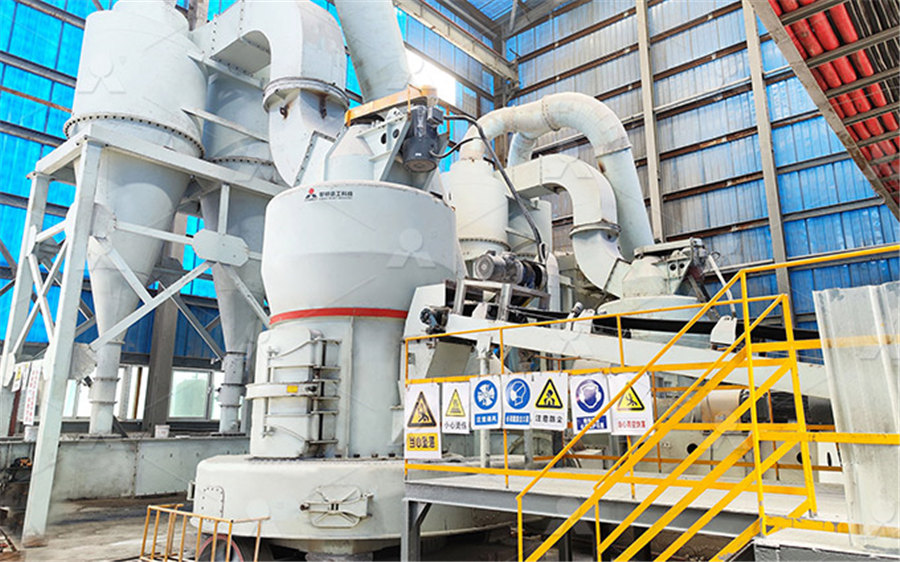
High Energy Ball Mills Milling RETSCH
The High Energy Ball Mill Emax, the most powerful in the RETSCH portfolio, achieves the highest energy input with speeds up to 2000 rpm, resulting in an acceleration of 76 g this model is highly suitable for research applications in mechanochemistry The PM 400 with four grinding stations is available with speed ratios 1:25 and 1:3, M Mhadhbi DOI: 104236/ampc2021 33 Advances in Materials Physics and Chemistry Figure 1 Photograph of the highenergy planetary ball millModelling of the HighEnergy Ball Milling Process ResearchGateHighenergy ball milling is a ball milling process in which a powder mixture placed in a ball mill is subjected to highenergy collisions from the balls Highenergy ball milling, also called mechanical alloying, can successfully produce fine, uniform dispersions of oxide particles in nickelbase super alloys that cannot be made by conventional powder metallurgy methodsHighEnergy Ball Milling an overview ScienceDirect TopicsOnce the application requirements are clear, a suitable mill can be selected To facilitate this process, Retsch displays the strength and efficiency of each ball mill model in a spidernet diagram, see Figure 3 A planetary ball mill, for example, offers a big jar volume compared to a mixer mill and shows a high value on this diagonalBall Mills Suitable for every application Retsch
.jpg)
Modeling and Analysis of HighEnergy Ball Milling Through Attritors
2017年7月5日 Models to understand the fundamental process during highenergy ball milling have focused on the description of powder deformation, fracture, cold welding, microstructure, and property evolution in response to ball milling conditions[21,22,23,24,25,26,27,28,29,30] The most basic “event” during highenergy ball milling is elastic/plastic deformation and can be The High Energy Ball Mill Emax combines highfrequency impact, intensive friction, and controlled circular jar movements to a unique and highly effective size reduction mechanism The grinding jars have an oval shape and are mounted on two discs respectively which move the jars on a circular course without changing their orientationEmax High Energy Ball Mill Retsch2023年5月1日 The equipment for obtaining ZnO nanoparticles is a highenergy ball mill (see Fig 1), Netzch brand (model LMZ10), connected by piping to a tank that includes a high Xray diffraction was used to determine the ZnO phases (XRD; PANalytical Empyrean model), cobalt was used as the target metal (radiation Kα = 178901 Largescale production of ZnO nanoparticles by high energy ball high energy ball mill Figure 1 illustrates the high energy ball mill (Mitui Miike Attritor, model MA1DX) developed especially for the synthesis of amorphous powders by mechanical alloying This ball mill has a large motor which makes it possible to raise the arm rotating speed R Development of an Extremely High Energy Ball Mill for Solid
.jpg)
Characterization of Stressing Conditions in a High
2022年4月1日 On a laboratory scale, the Emax high energy ball mill accounts for high stresses and power densities, as well as for temperature control, Tavares, LM Predicting the effect of operating and design variables on 2022年6月17日 Highenergy ball milling (HEBM) of powders is a complex process involving mixing, morphology changes, generation and evolution of defects of the crystalline lattice, and formation of new phases This review is Materials Development Using HighEnergy Ball The High Energy Ball Mill Emax, the most powerful in the RETSCH portfolio, achieves the highest energy input with speeds up to 2000 rpm, resulting in an acceleration of 76 g this model is highly suitable for research applications in mechanochemistry The PM 400 with four grinding stations is available with speed ratios 1:25 and 1:3, Retsch : 产品 : 粉碎设备 : High Energy Ball Mills2013年10月19日 Specially designed ball mills with a higher milling energy are used for HEBM purposes Different types of milling equipment are available for nanoparticle formation, including the vibrating mill, planetary ball mill, highenergy rotating mill, and attritors (Fig 72)HighEnergy Milling SpringerLink
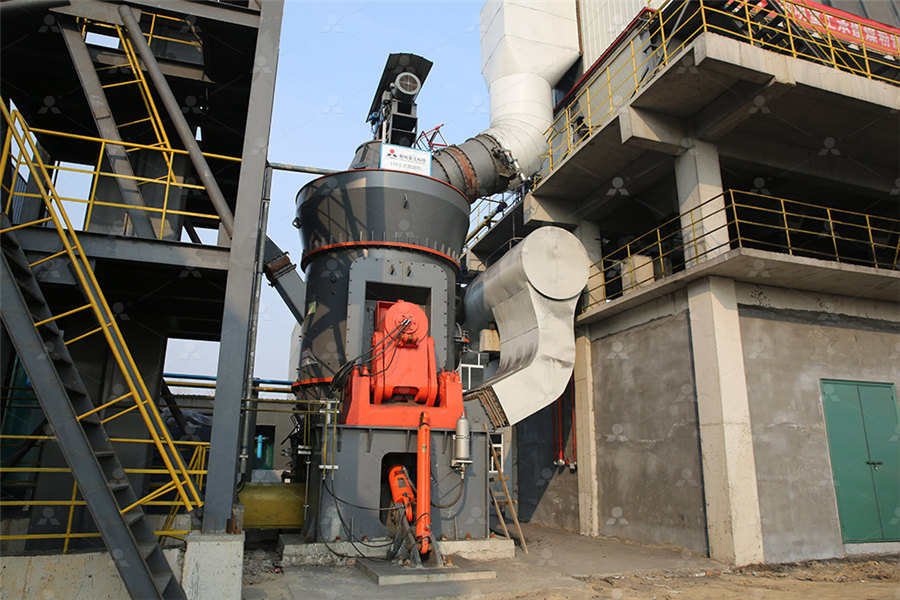
Navigating Ball Mill Specifications for TheorytoPractice
2024年8月15日 By using mechanical energy, 1 modern highenergy ball mills have revolutionized the domain of mechanochemistry, paving the way for academia and the fine chemical industry to unseen efficiencies, improved sustainability, and novel reaction paradigms 25 While studying the solidstate chemistry within the ball mill remains a challenging task, Planetary Ball Mill PM 400 for size reduction with the highest degree of fineness powerful short grinding times The extremely high centrifugal forces of Planetary Ball Mills result in very high pulverization energy and therefore short Floor model, storable SOPs and cycle programs, 5 different jar materials for Planetary Ball Mill PM 400 RETSCH powerful and quick grindingExperience fast and effective sample processing with the FP2000 highenergy planetary ball mill This versatile equipment offers precise control and excellent grinding capabilities Perfect for laboratories, it features multiple grinding bowls for simultaneous testing and high output Achieve optimal results with its ergonomic design, compact structure, and advanced featuresHigh Energy Planetary Ball Mill Kintek SolutionLABINDIA's High Energy Ball Mill MM1600 is a multifunctional benchtop ball mill specially designed for fast preparation of ultrafine sample with high sample throughput capable of handling 6384 samples simultaneously in modern laboratory applications, specially for Dry, Wet and Cryogenic grinding can process multiple small sample volumesGrinds, Mixes, Homogenizes HIGH ENERGY BALL MILL Labindia Analytical
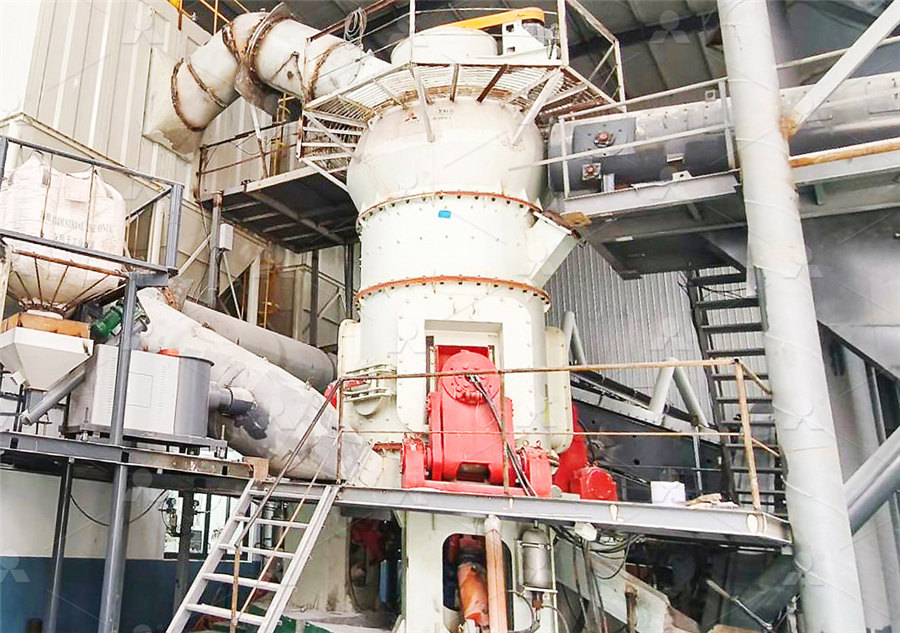
Particle aggregation and the grinding limit in high energy ball mill
2024年10月16日 Here, we will analyze mechanochemical treatment of brown coal with sodium percarbonate in an AGO2 planetary ball mill The term “mechanochemical treatment” is usually understood and used here as carrying out chemical reactions under mechanical action [7, 8]Sodium percarbonate was chosen as a convenient solid oxidizer, since it contained the Model 1 Introduction High energy ball milling (HEBM) is known as an economic, simple Fig 1 A schematic diagram of the planetary ball mill and the vial Fig 2 Sudden increase in the vial temperature after ignition in TiO 2,Al,B 2O 3 system Fig 3 XRD patterns of TiOOptimization of the high energy ballmilling: Modeling and Model Numbers and Specifications, Please Contact Us for Quotations For planetary jars comparable with horizontal ball mill, please also contact us Model Number Total Volume (L) Maximum Rotation Speed (RPM) Power (KW) MSE PRO Horizontal High Energy Planetary Ball Mills2020年10月13日 Simulations and in situ monitoring 27,29,30,31,32,33,34,35,36 of media interactions in highenergy ball mills have shown agreement with the underlying assumptions and estimated impact energies Mechanochemical conversion kinetics of red to black
.jpg)
Optimization of the high energy ballmilling: Modeling and parametric
2015年12月1日 Request PDF Optimization of the high energy ballmilling: After determining the model parameters, the mill was simulated in mill fillings of 15, 20, 25, 30, 2015年3月23日 HighEnergy Ball Milling as a General Tool for Nanomaterials Synthesis and Processing Marzia Pentimalli, Marzia Pentimalli ENEA – Italian National Agency for New Technologies, Energy and Sustainable Economic Development, Technical Unit of Materials – Materials Chemistry and Technology Lab, High‐Energy Ball Milling as a General Tool for Nanomaterials 2017年8月24日 The minimum achievable grain size and extent of alloying depend on a number of parameters ie, type of highenergy ball mill, milling container, balltopowder weight ratio, milling speed, grinding medium, extent of filling of the vial, milling atmosphere, process controlling agents, milling temperature, type of material being milled etc Synthesis of nanocrystalline HighEnergy Ball Milling Parameters in Production of 2016年4月1日 A mathematical model is also introduced to analyze the effect of milling parameters on the milling energy and the obtained results are compared with the experimental ones Mechanochemical destruction of DDTs with FeZn bimetal in a highenergy planetary ball mill Journal of Hazardous Materials, Volume 342, 2018, pp 201209Optimization of the high energy ballmilling: Modeling and
.jpg)
(PDF) High Energy Ball Mill Processing ResearchGate
2003年2月15日 The highenergy ball mill processing can be divided in three main groups according to the mechanisms involved and/or the purpose envisaged: There are other models describing mechanical alloying2020年4月1日 Let us consider in brief a model of mechanical powder milling to a smaller particle size [34–39] and its applicability to estimating the powder particle size as a function of the milling energy E mill, mass M of the initial powder and particle size D in of the initial powderThe particle volume and surface area in an initial powder are equal to and , respectively, where f v and f s Highenergy ball milling of nonstoichiometric compoundsAs regards ball milling of powders and its final result, ie the particle size, the studies of this kind are still performed at the empirical level, since models relating the size of particles in prepared nanocrystalline powders to the milling energy are unavailable In this paper we propose a model of ball milling ofProduction of nanocrystalline powders by highenergy ball 2022年4月1日 Characterization of Stressing Conditions in a High Energy Ball Mill by Discrete Element Simulations April 2022; Processes 10(4):692; which only models the energy dissipation insideCharacterization of Stressing Conditions in a High Energy Ball Mill
.jpg)
Modelling of the HighEnergy Ball Milling Process
In this paper, the milling parameters of high energy ball mill (Fritsch Pulverisette 7) like vial geometry, number and size of balls and speed of the mill were modelled and discussed Simulations through discrete element method (DEM) provide correlation between the milling parameters A mathematical model is used to improve and develop this process2022年6月29日 The Discrete Element Method (DEM) is a numerical method for simulating the dynamics of particles processes This present work focuses on DEM simulations of a scale laboratory planetary ball mill DEM Modeling and Optimization of the High Energy Ball Milling2023年7月6日 In the present work, nanocrystalline binary Fe60Al40 (wt%) powders have been synthesized by a highenergy planetary ball mill under an inert argon atmosphere The evolution of structural, morphological, and magnetic properties of ballmilled powders was studied as a function of milling time using xray diffraction (XRD), scanning electron microscopy with energy Effect of HighEnergy Ball Milling on the Structural and Magnetic FRITSCH Planetary Ball Mills – highperformance allrounder in routine laboratory work The Planetary Mill PULVERISETTE 5 premium line with 2 grinding stations is the ideal mill for fast wet and dry grinding of hard, mediumhard, soft, brittle and moist samples as well as for mechanical alloying, mixing and homogenising of larger sample quantities with reliable results down into Planetary Mill PULVERISETTE 5 premium line / Description
.jpg)
High Energy Vibratory Ball Mill Kintek Solution
The highenergy vibrating ball mill is a highenergy oscillating and impacting multifunctional laboratory ball mill The tabletop type is easy to operate, small in size, High energy vibratory ball mill multiplatform: Model: KTBM500: KTBM500L: KTBM500P: Recommended maximum injection size: 10 mm: Sample particle size range ~01um:VBCC's HIGH ENERGY PLANETARY MILL Description: Planetary ball mills indeed sound like marvels of engineering! By leveraging the dynamic interplay of centrifugal and Coriolis forces, they achieve impressive feats of pulverization In VBCC's high energy planetary mill, the stationary jar filled with grinding balls becomes the center of attentionHigh Energy Planetary Mill VB Ceramics2008年7月2日 A model of highenergy ball milling of powders has been proposed It is demonstrated that part of the energy is consumed for initiation of microstrains ε during milling and, hence, the process of Production of nanocrystalline powders by highenergy ball VQN ball mills may be referred to as shaker mills, mixer mills or highenergy ball millsThey can be used for both wet and dry grinding as well as to mix a variety of solids, suspended liquids and pastes This unit is ideal for preparing small batches of your sample efficientlyAcross International VQN High Energy Ball Mills
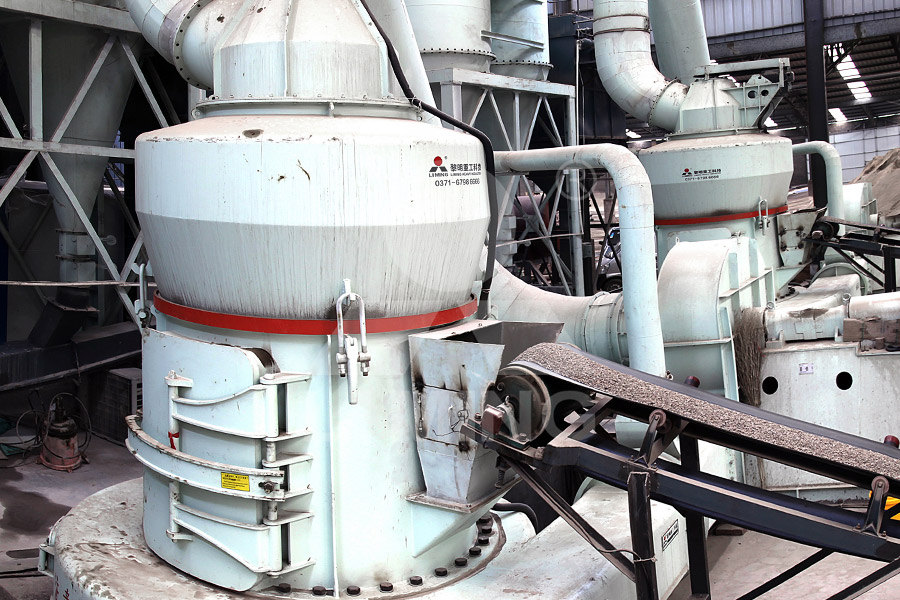
Planetary Mills – fritsch
PULVERISETTE 1 Model Iclassic line; PULVERISETTE 1 Model IIclassic line; Disk mills Planetary Ball Mills HighPerformance allrounders in routine laboratory work MENU The comminution of the material to be ground takes place primarily through the highenergy impact of grinding balls in rotating grinding bowls The grinding