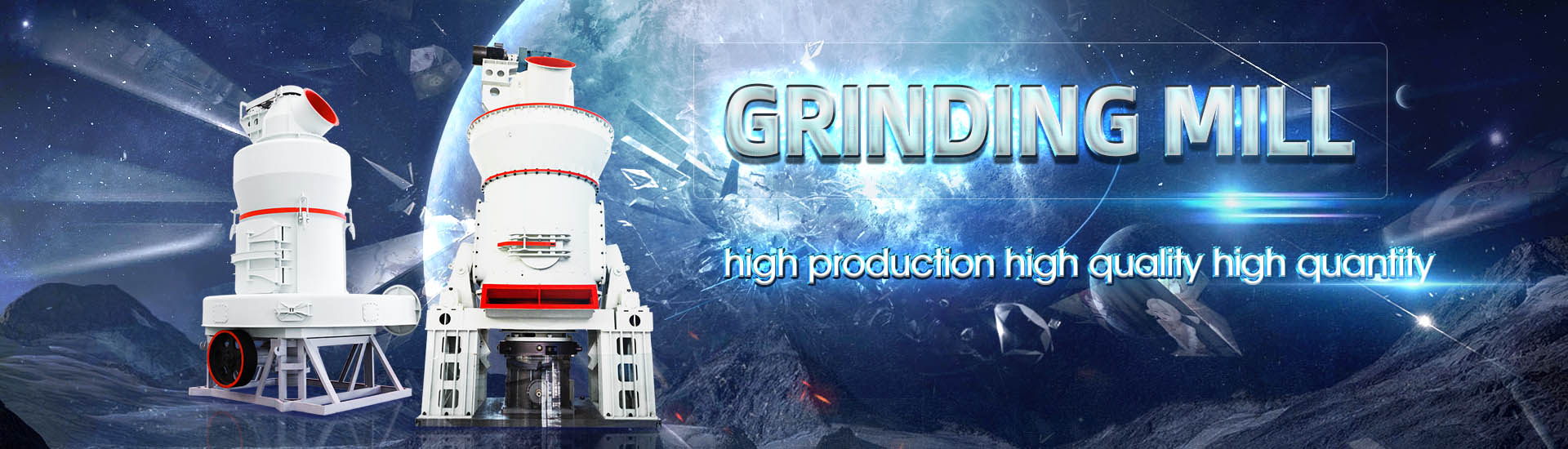
Efficiency lime mill
.jpg)
Mill study on improving lime kiln efficiency
2015年2月1日 This paper examines the effects that nonprocess elements (NPEs) can have on Kraft mill efficiency These include increased lime kiln To increase the energy efficiency of the lime kiln, all auxiliary unit operations must function properly It is also imperative that the lime and liquor in the system is of acceptableMill study on improving lime kiln efficiency ResearchGateIn this project, a control strategy was developed for the lime kilns in a Brazilian pulp mill in order to reduce the variability on calcination process and decrease the consumption of fuelOptimization of lime kilns based on strategies of advanced process All of the above areas can affect Kraft mill efficiency and operating costs This paper looks in more detail at the following topics: 1 Evidence for NPE aluminosilicate compounds in lime mud 2 Effect of NonProcess Elements on Kraft Mill Efficiency
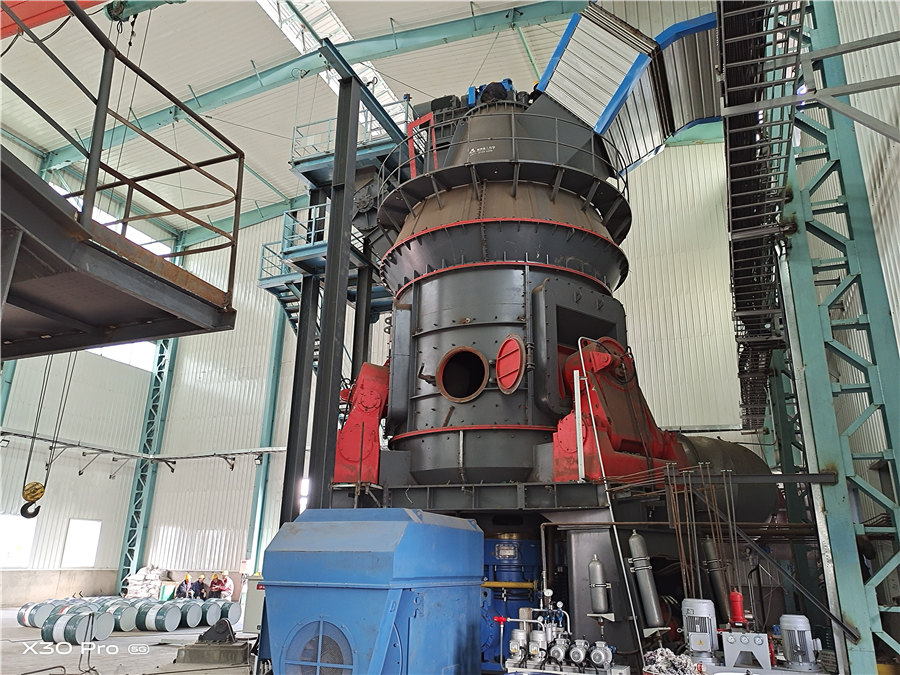
Global survey on lime kiln operation, energy consumption, and
A global survey was conducted to gather information on lime kiln operation and energy usage, and on the current status of alternative fuel use in kraft pulp mill lime kilns Questionnaires regulations in recent years, many kraft pulp mills have made it a priority to reduce their energy consumption Many mills have done this by improving their lime kiln thermal efficiency and by Global survey on lime kiln operation, energy consumption, and efficiency of a PFR lime kiln, operating according to this process, is as high as ≈85% as long as the calorific value of the fuel is not too low As many steel plants produce the required New PFR lime kiln process with blast furnace gas and oxygenAbstract: Due to a 50% increase in pulp production at DMI PRPD, purchased quick lime was used to supplement the mill’s lime requirements Excessive dust recycle in the kiln hindered kiln Upgrading a Lime Kiln Chain Section to Reduce Dust Loading and
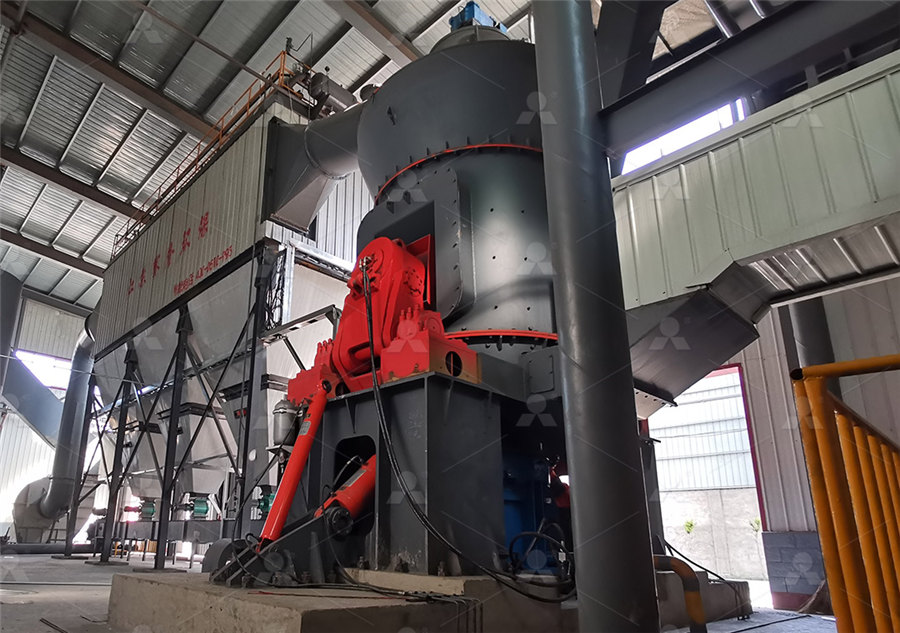
Mill study on improving lime kiln efficiency Semantic Scholar
2015年3月1日 This report describes the construction of a model that calculates mass and energy balances over the lime kiln in a kraft pulp mill The model was implemented in In the lime kiln process, Profit Suite improves lime quality (residual carbonate), reduces energy usage and maximizes lime kiln efficiency, while integrating the entire lime kiln process to drive millwide optimization Profit Suite for the Lime Kiln optimizes the following areas: Fuel flow control (primary, secondary, etc)Profit Suite for Lime KilnOptimization of the lime kiln requires an examination of the entire lime cycle In order to increase the energy efficiency of the lime kiln, it is important for all auxiliary unit operations to function correctly It is also imperative that the lime and liquor in the system to be of an acceptable qualityImproving Lime Kiln Efficiency: A Mill Study, 2014 PEERS For high gypsum board line speed and thus high production capacity utilization the use of high concentrations of gypsumbased ball mill accelerator (BMA) are common practice Very low concentration of retarder, such as amino acid Multifunctional polymers for increased gypsum board
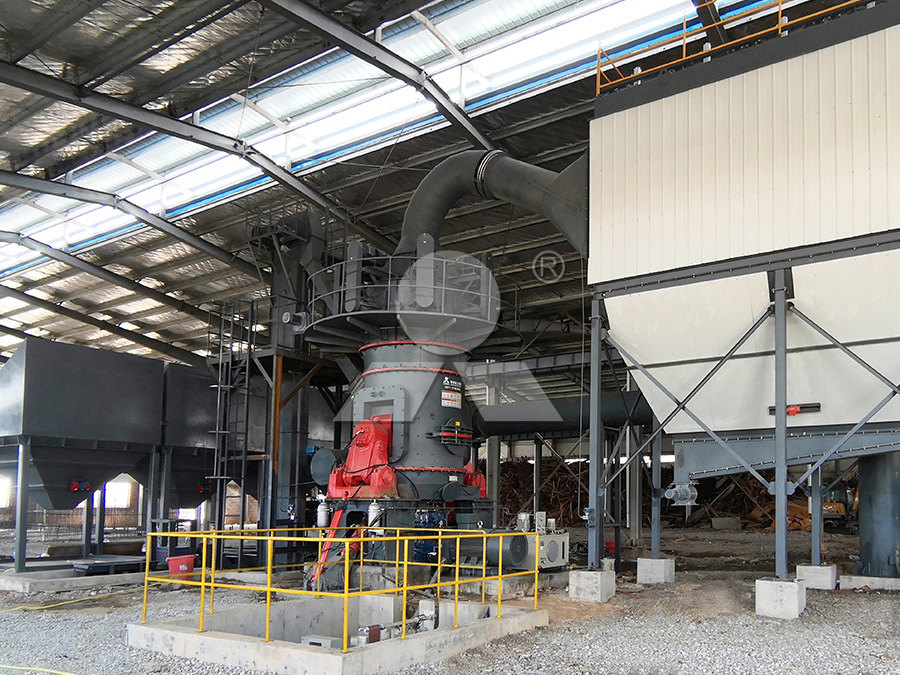
Limestone Grinding Mill Solution Adjustable Powder Fineness
The different finenesses of lime grinding powder are suitable for different industriesAGICO’s raymond limestone grinding mill and limestone ball mill can grind powder with fineness of 80400 mesh, if you want even finer powder, you can choose the vertical If you want finer powder, you can choose the vertical limestone grinding mill, which can grind the powder fineness above The energy efficiency of a lime kiln may be described by the heat rate The heat rate is the amount of energy that is consumed to create a certain amount of reburned lime For an efficient lime kiln, the heat rate is about 15 Gcal/ton of CaO Optimization of lime kilns based on strategies of advanced process LIME KILN HEAT RATE The energy efficiency of lime kilns is expressed as the Heat Rate Heat Rate is the reciprocal of energy efficiency, and is usually expressed as MM Btu/ton of CaO, or as GJ/tonne of CaO Lower values of Heat Rate indicate more efficient operation as indicated in 22 Lime Kiln Principles And Operations TAPPI8 Slide 15 Lime Kiln Heat Rate • Heat rate is a measure of energy efficiency – Units are MM Btu/ton CaO or GJ/tonne CaO – Often stated as MM Btu/ton “product” • Typical range – 5 to 9 MM Btu/ton CaO – 58 to 105 GJ/tonne CaO – Lower is better Slide 16 Lime Kiln Energy Balance Components • Drying • Calcining : CaCO3 + heat ÄCaO + CO2 • Losses – Heat loss through 22 Lime Kiln Principles and Operations TAPPI

Effect of ball mill grinding parameters of hydrated lime fine
2013年5月1日 The influence of several grinding parameters such as charged material volume, ball filling ratio, and mill rotation speed on energy efficiency of fine grinding of hydrated lime and the product Filtered lime mud at the Elk Falls mill had low solids content and was dark green Along with high NPE dead load, this caused additional kiln fuel costs of nearly $300,000/year An NPE mass balance was obtained, using composite samples from fifteen different process streams Kiln fuel oil was a significant source of phosphorus, iron and zinc NPE specifications for lime rock, fuel Nonprocess element mass balance improves recaust and lime 2021年2月26日 Milling is among the most energyconsuming technological stages of copper ore processing It is performed in mills, which are machines of high rotational masses The start of a mill filled to capacity requires appropriate solutions that mitigate the overloading One method for increasing the energy efficiency of ball mills is to optimize their drive systemsEnergy Efficiency Analysis of Copper Ore Ball Mill Drive Lime Kiln Efficiency at Elk Falls Mill", Pulp Paper Canada, 108(3), T4955 (2007) 2006 John S Bates Award for Best Branch Paper TAYLOR, K, and MCGUFFIE, B, "Investigation of NonProcess Element Chemistry at Elk Falls Mill Green Liquor Clarifier and Lime Cycle", Pulp Paper Canada, 108(2), T24– 29EFFECTS OF NONPROCESS ELEMENTS ON MILL EFFICIENCY
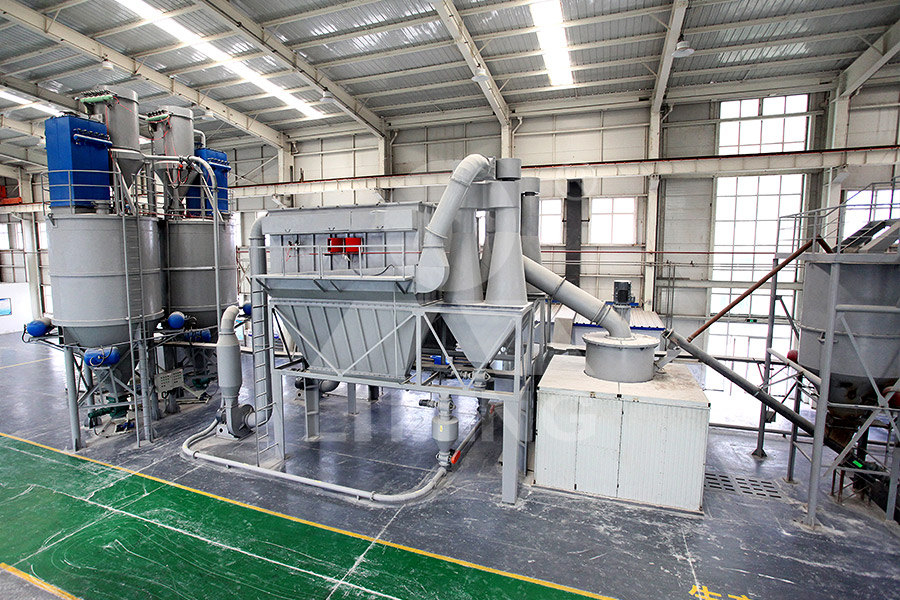
21 Recausticizing Principles and Practice TAPPI
causticizing efficiency above which the free lime becomes a major operating problem, especially with pressure filter systems Figure 33 was developed from mill data and illustrates the effect of trying to achieve a higher causticity This problem will be discussed later in Trouble Shooting2021年9月21日 Running a mill at its maximum efficiency means optimizing dozens of factors, most of which interact with other factors, so it isn’t necessarily easy to optimize a mill’s operations Sage words from former The Tube Pipe Tips for maximizing tube, pipe mill efficiency (Part I)2002年11月1日 Unfortunately, the energy efficiency is extremely low in mining operations For instance, the energy efficiency is about 10% in percussive rock drilling (Carrol 1985), 35% in rock crushing The energy efficiency of ball milling in comminutionDownload scientific diagram Lime Mud Solids Content, 10 Day Average from publication: Effect Of NonProcess Elements On Kraft Mill Efficiency This paper examines the effects that nonprocess Lime Mud Solids Content, 10 Day Average ResearchGate
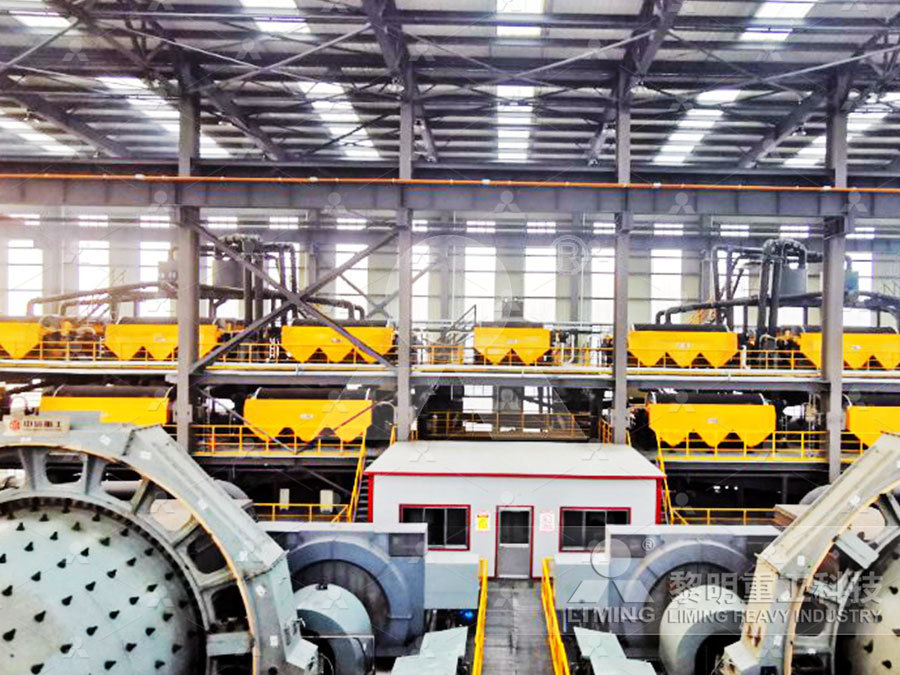
The Kraft Recovery Process TAPPI
black liquor vary from mill to mill depending on many factors, including mill location (inland or coastal), digester 112 Many problems can also occur in lime kilns including: low thermal efficiency, high fuel consumption, ringing, balling, dusting, refractory and chain damage, poor lime quality and air emissions2007年3月1日 Filtered lime mud at the Elk Falls mill had low solids content and was dark green Along with high NPE dead load, this caused additional kiln fuel costs of nearly $300,000/yearNonprocess element mass balance improves recaust and lime Abstract: Due to a 50% increase in pulp production at DMI PRPD, purchased quick lime was used to supplement the mill’s lime requirements Excessive dust recycle in the kiln hindered kiln production and was the main cause for poor kiln thermal efficiency The inefficient, high maintenance kiln chain systemUpgrading a Lime Kiln Chain Section to Reduce Dust Loading and 2006年3月1日 The effects of NPEs on Kraft mill operation have been extensively reviewed [113] and include increased lime kiln fuel use, reduced filtration efficiency, reduced lime mud settling and increased Investigation of green lime mud at Harmac mill ResearchGate
.jpg)
Lime Slaking Equipment 911Metallurgist
2015年9月4日 Lime Slaking If lime slaking efficiency is removed from the economic analysis, For the detention slaker, the proportion was 94% pebble lime, and for the Vertimill slaker, the proportion was 88% A single system for pH control will simplify the concentrator layoutIMPROVES RECAUST AND LIME KILN EFFICIENCY AT ELK FALLS MILL BEN MCGUFFIE Catalyst Paper, Elk Falls Division, Campbell River, BC KEVIN TAYLOR Taylor Industrial Research Inc, Victoria, BC, Canada Phone: 2504185705 : PAPTAC Parksville Conference April 2122, 2006 (Best NonProcess Element Mass Balance Improves Recaust and Lime 2024年2月28日 The company says this multiyear investment will deliver returns through improved efficiency and reduced costs The new Fline is part of DS Smith’s organic investment program According to the company, Kemsley is DS Smith boosts paper mill efficiency with new fibre There are mainly four factors that related to the grinding efficiency of Raymond mill which should be considered while using the mill Factor 1: The hardness of raw material The higher the hardness, the lower the output, the material with higher hardness will reduce the mill capacity, at the same time it will increase the wear of Raymond grinding partsFour factors Affecting the Grinding Efficiency of Raymond Mill
.jpg)
Vertical Shaft Kilns in Optimizing Lime Calcination
Verticle Shaft Kiln Introduction In factory of lime calcination, where precision and efficiency are paramount, vertical shaft kilns (VSKs) stand as stalwart contributors to the chemical transformation of limestone into quicklime As an engineer navigating the intricacies of industrial processes, understanding the design, components, and operational aspects of VSKs becomes It’s intended to monitor the efficiency of machines working in a series as part of continuous line manufacturing, unlike OEE which is aimed at tracking individual machines Sometimes, OLE includes employee efficiency as well as equipment efficiency, since workers are also part of the production processWhat is Overall Line Efficiency (OLE) in manufacturing? Precognizeefficiency on the different unit operations in the pulp mill The value of maximizing both total alkali and causticizing efficiency, as well as a method of optimizing both key performance variables, is described PEERREVIEWED 154 TAPPI JOURNAL MARCH 2024 VOL 23 NO 3 T he primary function of the kraft mill causticizingEffects of varying total titratable alkali and causticizing efficiency 2023年10月26日 Metsä Group's Äänekoski bioproduct mill, located in Central Finland It produces 13 million tonnes of softwood and birch pulp annually Valmet's Lime Kiln Optimizer has been implemented in 2022, resulting in significant process optimization and increased energy efficiency at the millOptimize process and increase energy efficiency with Valmet’s Lime
.jpg)
Ways to increase efficiency in feed mills
2022年7月3日 Stating that increasing efficiency in feed mills starts with determining the current situation and comparing it with both short and longterm goals, Nils Lastein, Application Manager at ANDRITZ Feed Biofuel, says, “ANDRITZ recommends hiring a qualified thirdparty consultant with a global perspective to inspect, analyze, interview and report on the state of the plant”2009年10月11日 Due to a 50% increase in pulp production at DMI PRPD, purchased quick lime was used to supplement the mill's lime requirements Excessive dust recycle in the kiln hindered kiln production and was (PDF) Upgrading a Lime Kiln chain section to reduce dust loading A mill is a device, often a structure, machine or kitchen appliance, that breaks solid materials into smaller pieces by grinding, crushing, or cutting Such comminution is an important unit operation in many processesThere are many different types of mills and many types of materials processed in them Historically mills were powered by hand or by animals (eg, via a hand crank), Mill (grinding) WikipediaChapter 3: Pellet Mill Design Pellet mill design BY MR RON TURNER, FEED PELLETING CONSULTANT REVIEWED AND EDITED BY ADAM FAHRENHOLZ, CASSANDRA JONES, AND CHARLES STARK W hen considering at pellet mill design, there are some important aspects to study to achieve maximum efficiency of the machine MaximumPellet mill design Feed Strategy
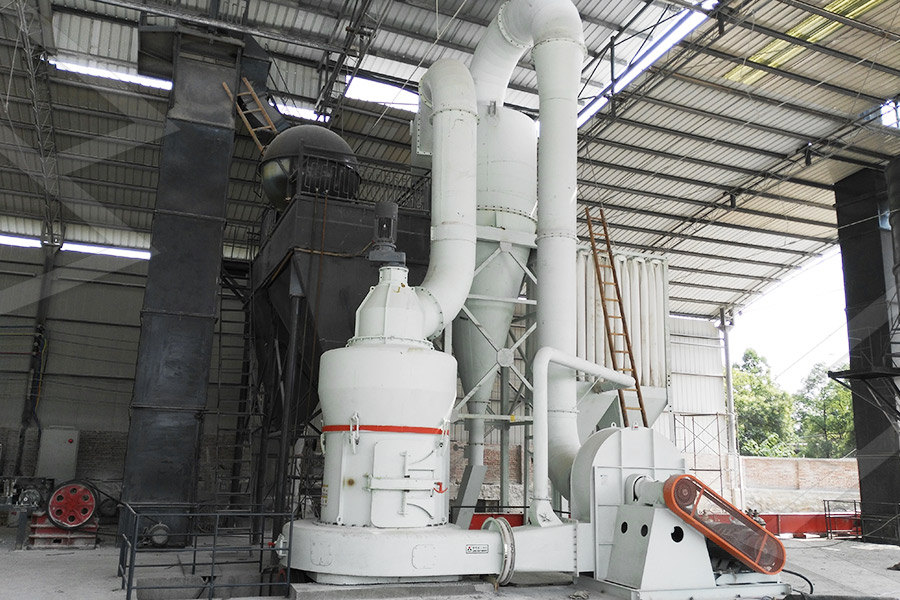
The energy efficiency of ball milling in comminution
2002年11月1日 In terms of this concept, the energy efficiency of the tumbling mill is as low as 1%, or less For example, Lowrison (1974) reported that for a ball mill, the theoretical energy for size reduction (the free energy of the new surface produced during grinding) is 06% of the total energy supplied to the mill setupInvestigation of green lime mud at Harmac mill @inproceedings{Taylok2006InvestigationOG, title={Investigation of green lime mud at Harmac mill}, author= (NPEs) can have on Kraft mill efficiency Investigation of green lime mud at Harmac mill2024年6月17日 “The mill will produce 25 times the electrical power we need for our own operations, and we will sell power to the national grid Heat generated by the mill will be used by Metsä Board’s paperboard machine at the Kemi integrated mill and for heating in the City of Kemi,” says Pekka Kittilä, VP, Mill Manager of Kemi bioproduct millFossilfree pulp production at Kemi bioproduct mill Metsä FibreMPS vertical mill from Pfeiffer is the ideal allrounder Grinding of coal, petcoke, clay, limestone, quicklime, KLV lime hydrator; The grinding principle and the high efficiency classifier ensure the reduction of electric energy consumption by up Coal mill, gypsum mill, clay mill, etc Pfeiffer MPS mills
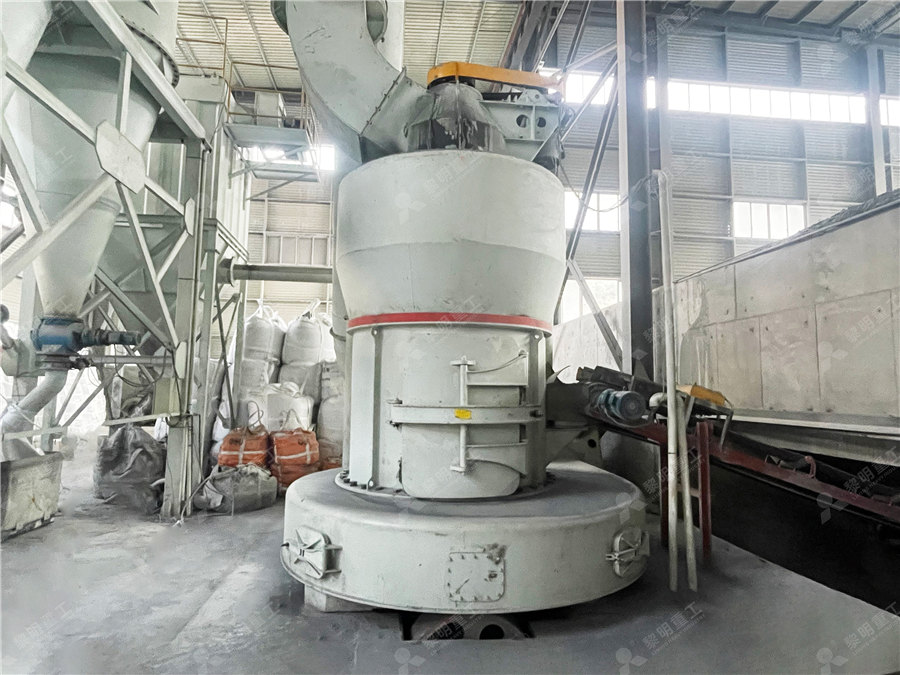
Study Case: Optimization of recausticizing plants in a Brazilian pulp mill
Figure 2: Causticizing Efficiency x Total Titratable Alkali Source: Olsson 1995 In order to get a good quality of white liquor, there are some actions that can be taken with the aim of improving the2016年6月6日 High singleline capacities (leading to capital efficiency) The ability to mill a broad range of ore types in various circuit configurations, Though some trepidation concerning AG or SAG circuits accompanied design studies for some lime, such circuits are now well understood, SAG Mill Grinding Circuit Design 911Metallurgist2019年4月11日 In a modern pulp mill, the lime kiln is the only major consumer of fossil fuel – usually natural gas or fuel oil During the oil crisis in the 1970s and 1980s, In addition to safety, moisture content and particle size is optimized for energy efficiency and kiln operationPulp mill lime kilns go fossil free ValmetThe vertical roller mill is used to grind the material by using the principle of material reduce energy consumption, increase operating rate, and continuously improve economic efficiency are central issues in the management and operation of Below is a brief analysis from 3 parts: lime raw materials, fuel options, and How to Improve Grinding Efficiency of Vertical Roller Mill
.jpg)
STICKIES REMOVAL IN A DEINKING LINE OF A NEWSPRINT MILL: EFFICIENCY
The study evaluates stickies removal efficiency of the different process stages in a deinking line of a newsprint paper mill, using 100% recovered paper as raw material