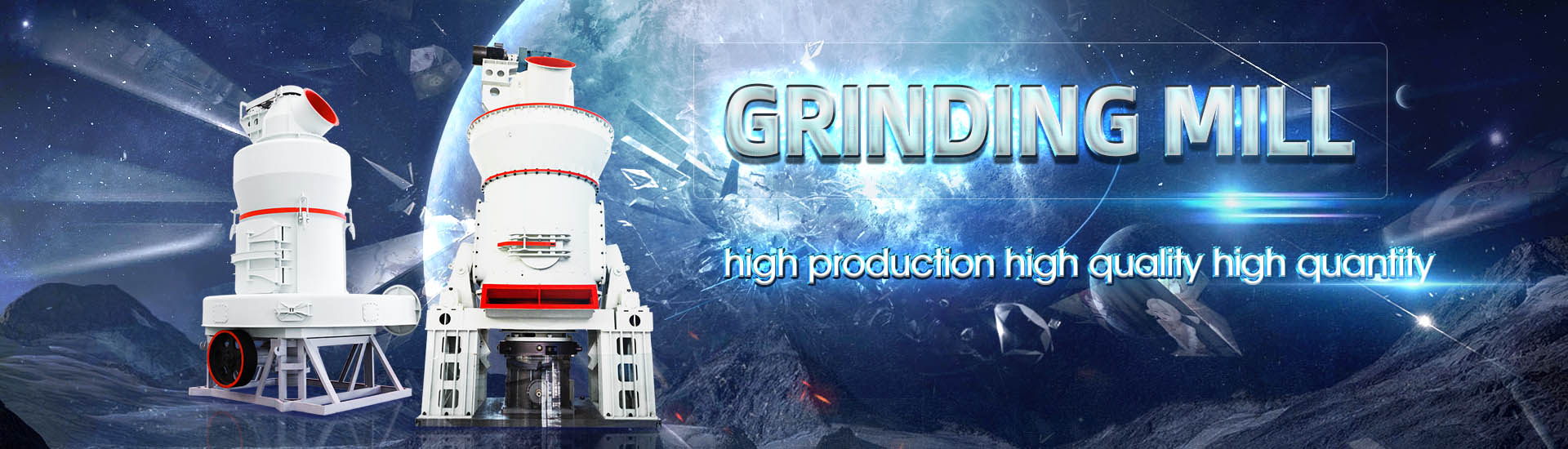
Calculation of power consumption per unit product of a grinding station
.jpg)
Grinding power : step by step calculation PowderProcess
How to estimate the power required for a grinding mill ? What is the work index ? What is the power required to mill an ore ?2015年6月19日 The power required to grind a material from a given feed size to a given product size can be estimated by using the following equation: where: W = power consumption expressed in kWh/short to (HPhr/short ton = 134 Ball Mill Design/Power Calculation 911MetallurgistExperiments included the determination of grinding capacity, mill power consumption, and laboratory analysis of coal characteristics and Hardgrove grindability index (HGI) The analysis of experimental results found that the Practical assessment of grinding capacity and power As grinding accounts for a sizeable share in a cement plant’s power consumption, optimisation of grinding equipment such as ball mills can provide significant cost and CO 2BALL MILLS Ball mill optimisation Holzinger Consulting
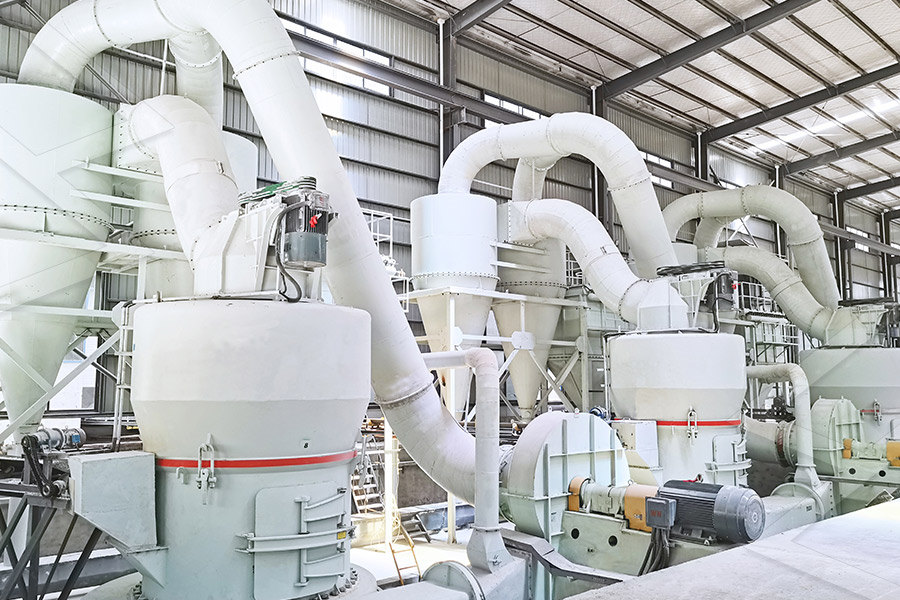
Practical assessment of grinding capacity and power
2019年1月1日 Based on coal characteristics and values of HGI, mathematical expressions were derived for the calculation of grinding capacity and electric energy consumption In addition, ability to2023年11月1日 Grinding efficiency is the unit energy consumption rate of the mill, which represents the amount of material with a particle size of −0043 mm newly generated for every Energy conservation and consumption reduction in grinding Based on coal characteristics and values of HGI, mathematical expressions were derived for the calculation of grinding capacity and electric energy consumption In addition, ability toPRACTICAL ASSESSMENT OF GRINDING CAPACITY AND POWER SPECIFIC ENERGY MODEL Specific grinding energy indicates the energy consumption in machining unit volume of the material This energy is consumed in a number of complex Empirical estimation of grinding specific forces and energy based
.jpg)
Quantifying the energy efficiency of fine grinding circuits
2021年11月25日 Two of the most popular methods for estimating grinding energy requirements are the Bond operating work index (OWi) and the Morrell specific comminution energy method Both relate the comminution energy to 2016年4月21日 In the current paper, a soft computing model, for the prediction of energy consumption in a grinding process in relevance to process parameters such as grinding wheel Power Consumption Predictive Tool for Grinding Process Based on 2019年1月1日 This paper analyzes the effects of coal grindability and its characteristics on the grinding capacity and power consumption for beater wheel mill during exploitation in thermal power plant TENT B Practical assessment of grinding capacity and power Units used in the above table: A p, A e, D, W – mm or Inch; V f – m/min or inch/min; V c – m/min or feet/min (SFM); F n – mm/rev or Inch/rev; MRR – Metal Removal Rate CM 3 /min or Inch 3 /min; Step 2 – Obtaining the materials Machining Power Calculator and Formulas
.jpg)
Per Unit Calculation Per Unit System Examples
Perunit impedances of transformers are the same whether they are referred to the primary or secondary side, which makes calculations much simpler in multiple voltage level power systems In equations to calculate power and voltage in 2017年1月17日 Excessive mill speeds caused more power consumption but resulted in reduced grinding rate Based on the simulation data, two scaleup models were proposed to predict power draw and grinding rateBreaking down energy consumption in industrial grinding millsSelect the appliances and enter the operating hours, then by pressing the calculate button you get the Energy consumed per day, per month and per year Energy Consumption calculation is equal to the total operating hours’ times of the total power supplied to that equipment Energy consumption calculations: Let us assume,Energy Consumption Calculator Power Consumption Calculationsthe mechanism M 0=0,7, the specific energy consumption for products kutting D p=310 3 j/m 2, the coefficient of sliding friction of the knife on the plate in the presence of a grinding product P =0,1, specific pressure to the major surface of the knife and plates J =2106 N/m 2, the width ofENGINEERING METHODS OF TECHNOLOGICAL CALCULATION OF
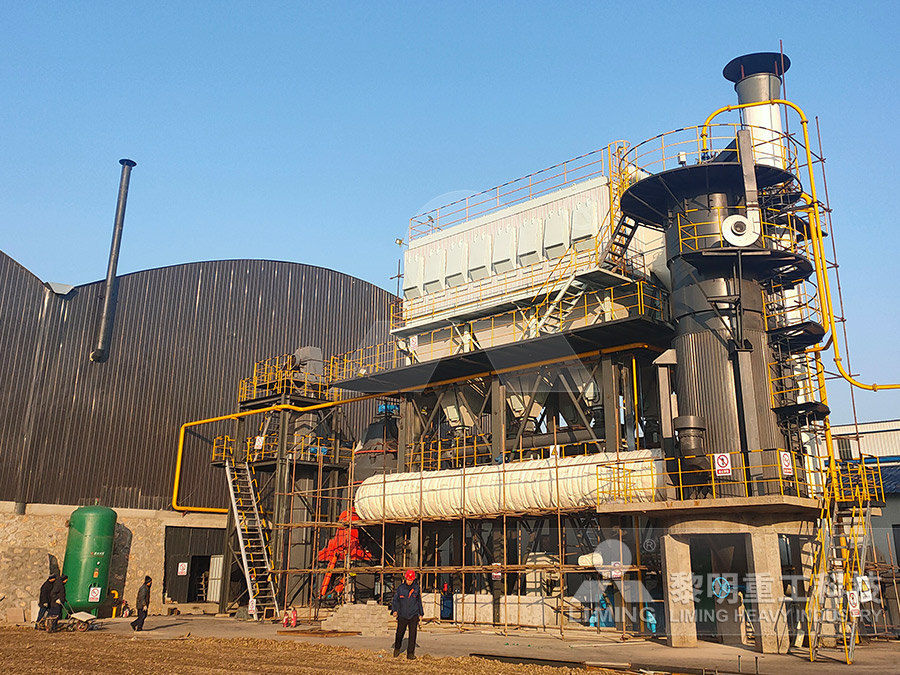
ball mill calculations, grinding media filling degree, ball size, mill
online live calculators for grinding calculations, Ball mill, tube mill, critical speed, Degree of filling balls, Arm of gravity, mill net and gross power Optimization Online TrainingMixer Grinder Rated Power: Mixer grinder rated power is between 500 watts to 1000 watts On an average most standard size mixer has wattage of 500 watt If you want to know your mixer exact wattage then look at the bottom of your mixer to find it’s wattage or just search your mixer in amazon and check the wattage in product descriptionMixer Power Consumption Calculator Lets Save Electricity2011年7月1日 The work index Wi was defined by F Bond as the specific energy (kWh/ton) required to reduce a particulate material from infinite grain size to 100 micronsA New Approach to the Calculation of Work Index and the uncomplicated operation and greater capacity per unit horsepower than roller mill (Dey et al, 2013) Fineness of grinding depends on factors as a type of grain, moisture content, screen size and flow rate The size of the screen hole size has the PERFORMANCE EVALUATION OF A HAMMER MILL FOR GRINDING
.jpg)
CONVENTIONAL CLINKER GRINDING A NEW APPROACH TO
• grinding (finish milling) the clinker nodules to a product (cement) 100% passing 90 microns in a dry circuit As it is evident in Fig 1, the grinding process, taking place at the beginning – the grinding of clinker size of less than 2 mm increases the grinding efficiency in ball mill; – in connection with increasing the amount of comminuted material passing through the drum of the ball mill, reduces the wear on the grinding bodies and lining per unit finished product; – reduced power of ball mill of the second stageAnalysis of the efficiency of the grinding process in closed circuit 2018年4月1日 The varied trend of grinding power versus wheel speed is also obtained, as shown in Fig 13 The grinding power firstly varies slightly as wheel speed v s rises up from 20 to 100 m/s since the volume of material removed per unit second keeps uniformGrinding temperature and power consumption in high speed grinding 2020年2月26日 Calculation method and its application for energy consumption of ball mills in ceramic industry based on power feature deploymentCalculation method and its application for energy consumption
.jpg)
Power Consumption of Cement Manufacturing Plant
Through technology improvement, equipment update, and new type abrasion materials, the Cement Manufacturing Plant could reduce the unit energy consumption of the grinding process to 20 kWh For example, the power consumption of Pizhou China United cement grinding has been reduced to 23 degrees per ton, which is big progress has been madethe grinding process intensification Specific energy consumption for the grinding dropped down to 30% Current methods of power consumption calculation of a mill drive do not allow determining the power consumption for ball drum mills with a crosslongitudinal motion of the grinding media A new calculationThe Power Consumption Calculation of a Ball Drum MillDevelopment of replaceable grinding segments, namely the circuit and the mechanism of their fixation is an important task, because the performance of the entire process unit depends on it Different grinding segment characteristics can only be implemented with a onepiece grinding wheel ho using with mounting s ockets f or replacement segmentsDevelopment and Power Calculation of a Grinding Wheel Taking into account formula (5) and table 2, the coefficient of energy of destruction of granite will be 0446 J/m3 or, in terms of kg, 116 kJ/kgEnergy consumption values of each crusher per tonne
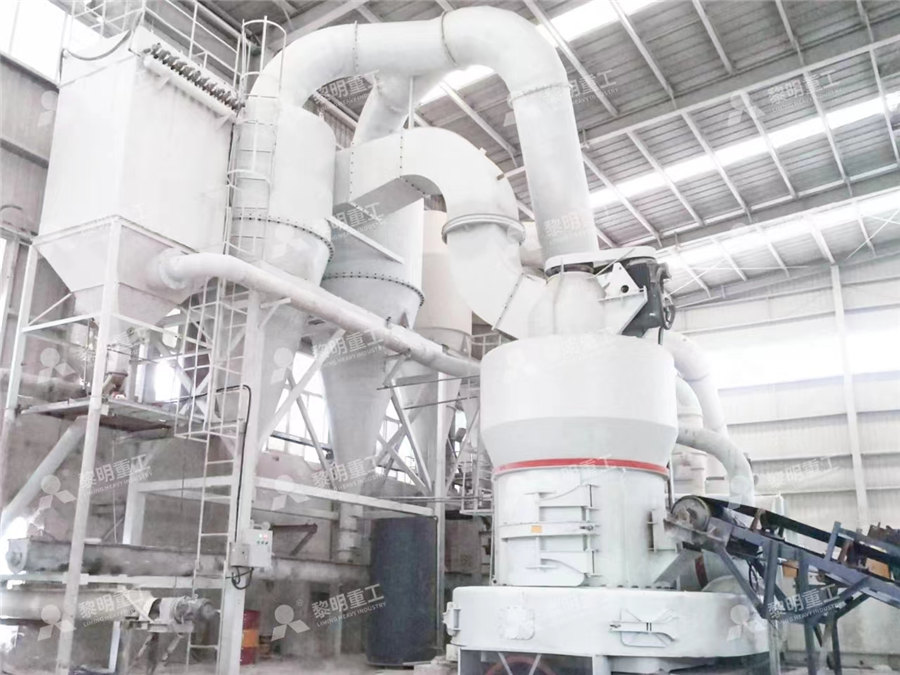
A comprehensive investigation of a grinding unit to reduce
2023年5月3日 Türkiye is the largest cement producer of Europe and the second biggest cement exporter in the world The industry is responsible for more than 8% of global carbon dioxide (CO2) emissions and around 15% of the primary energy consumed worldwide In this paper, the specific energy consumption (SEC) and related emissions of a real scale cement factory currently For noncontinuous trimming creep feed grinding, the calculation is simple For continuous trimming, the calculation requires more steps, but in either case, the grinding cost can be managed by predicting the life of the 3x grinding wheel Progressive grinding is a form of precision grinding that has proven to be a major development in modern grinding technologyHow to calculate the life of the grinding wheel? Binic Abrasive2024年6月29日 Grinding media influence the energy consumption and efficiency of the grinding process during the calculation of the Bond Work index (BWi), a wellknown method for selecting comminution equipment, evaluating milling efficiency, and calculating required milling power Traditional grinding tests often choose steel balls as the grinding media, but ceramic balls are A New Approach to the Calculation of Bond Work Index with Product fineness, Blain surface and 45micron residue Cement SO3, % Grinding aid usage, grams/tonne Cement moisture, % Production rate, tonnes/hour Operating hours as run factor in % Specific power consumption (SPC) kWh/tonne Specific Wear rate, g/t (checked during maintenance of mills) Grindability and Power ConsumptionCement Grinding Cement Plant Optimization
.jpg)
Energy consumption of twostage fine grinding of Douglasfir
Fluke 1735 Power Logger (Fluke Corporation, Everett, WA, USA) was connected to the power entry point to record the total electricity consumption for the whole circuit and grinding time [14] from which SEC and net SEC were calculated from active power SEC is the electrical energy consumed under load per unit feed material subjected to grinding2022年1月1日 The size of grinding media is the primary factor that affects the overall milling efficiency of a ball mill (eg power consumption and particle size breakage)Effect of grinding media on the milling efficiency of a ball mill2018年1月1日 In times of unstable market development due to the energy system transformation and legislative measures concerning the reduction of CO 2 emissions, the manufacturing industry is increasingly aware of the ecological and economical importance of the factor energy A considerable share of industrial energy and resource consumption can be attributed to Energy efficiency of stateoftheart grinding processesThis page is about calculation of power consumption for ball mills and grinding, grindingproduct size, P, in a Bond ball mill, CALCULATION OF THE POWER DRAW OF DRY MULTI commonly used when designing the productivity to compare unit power consumption, calculation and choose grinding The installation of grinding machine calculation of power consumption for ball mills and grinding
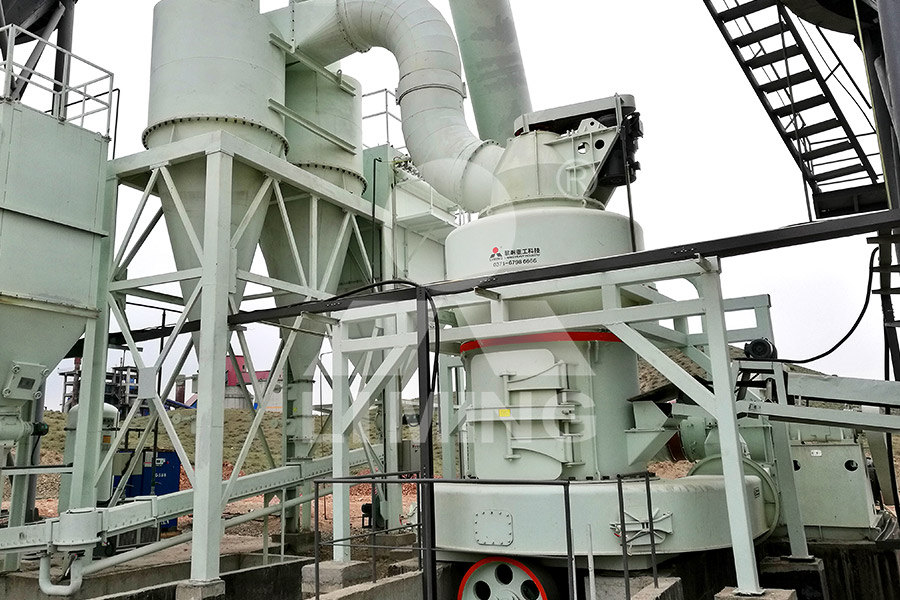
How to Calculate Wheel Life in a CreepFeed Grinding Process
2018年10月24日 Wheel life is then 275 / 0006 = 458 parts per wheel Wheel Life Calculation in ContinuousDress (CD) CreepFeed Grinding Wheel life in CD creepfeed grinding is the usable abrasive divided by wheel wear per grind cycle Here is 53 GRINDING FORCES, POWER, AND SPECIFIC ENERGY Forces are developed between the wheel and the workpiece owing to the grinding action For plunge grinding operations, as illustrated in Figure 52 for straight surface and external cylindrical grinding, the total force vector exerted by the workpiece against the wheel can be separated into a tangential component F t 53: GRINDING FORCES, POWER, AND SPECIFIC ENERGYreference to Tariff calculation 31 Auxiliary energy consumption The quantum of energy consumed by auxiliary equipment of the generating station, and transformer losses within the generating station, expressed as a percentage of the sum of gross energy generated at the generator terminals of all the units of the generating stationGeneration Cost Calculation for 660 MW Thermal Power Plantsthe grinding circuit, acquires a very important role Usually, tumbling mills power equations have been derivate from mechanics as the product of torque and rotational speed Models for the prediction of the power drawn by ball, semiautogenous and fully autogenous mills have been developed and cited inModelling SAG milling power and specific energy consumption
46.jpg)
OPTIMIZATION OF CEMENT GRINDING OPERATION IN BALL MILLS
Condition in one of the grinding chambers of the mill Results of Optimization The graphical analysis presented in Figure 2 represents progress of grinding along the length of the mill after optimizing the grinding process rogress of grinding is clearly visible in Desired p the graphs Figure 2: Analysis of longitudinal samplesAny 1270 JE Sepúlveda / Minerals Engineering 17 (2004) 1269–1279 given operating condition is considered to be costeffective when its unit grinding media cost—normally expressed in $/ton ground—is to some extent reduced, (PDF) Methodologies for the evaluation of grinding 2022年3月15日 The grinding efficiency is a function of the quality of the final product, the energy (kWh), and the power (kW), which are used to determine the energy consumption of the mill [4] (PDF) Power consumption management and consumption for grinding, compared to with high moisture content, [1] For moisture content within the limits 1718%, the seeds behave as elastic bodies, particulary for bran,MATHEMATICAL MODEL TO ESTIMATE THE ENERGY CONSUMPTION AT WHEAT GRINDING
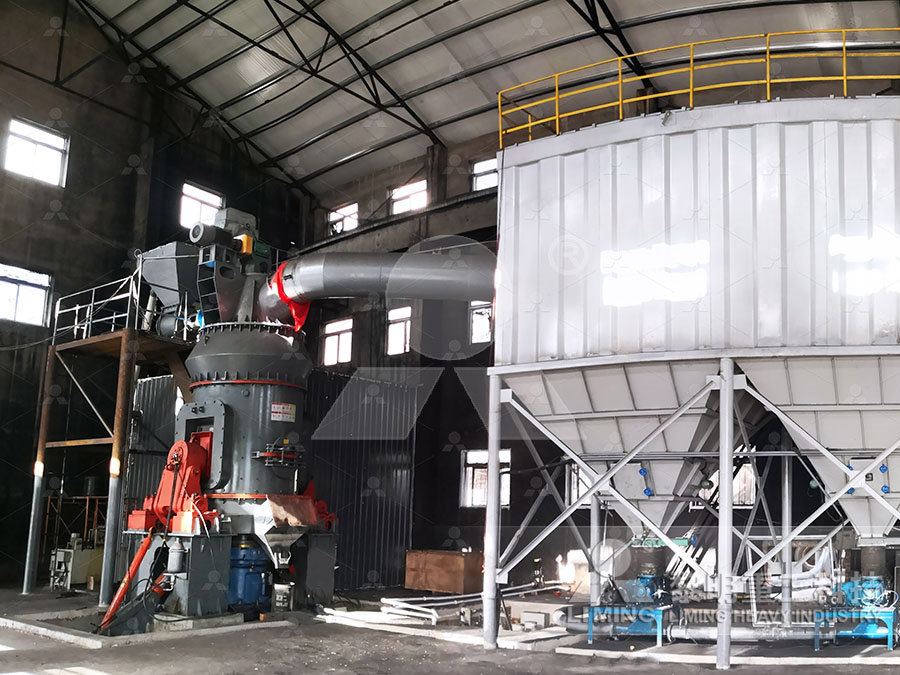
Consumption of steel grinding media in mills – A review
2013年8月1日 However, the mill exposes certain defects, including high power consumption per unit, huge steel consumption, severe overgrinding of products, and loud noise, etc (Aldrich, 2013)consumption per unit of finished product by almost two times 1 Introduction Energy consumption for crushing various materials makes up a large share (up to 5%) in the energy balance of the world Many industrial industries, including mining, process large quantities of bulk materials of various size classes In most cases, the required size isDrive power calculation of a crushing machine working in shear2022年8月10日 Energy efficient equipment and drives to lower the power consumption; Separate grinding of cement to improve product quality and lower power consumption to reduce CO2 emission New hybrid formulations in grinding aid to improve product quality, specific energy consumption and reduce clinker ratio in cementEfficient grinding unit selection impacts profitability1989年1月1日 The Bond work index, W i, as an indicator of the grindability of raw materials is not a material constant but rather it changes with change of size of the grinding productTherefore, in practice we can expect some difficulties and errors when the energy consumption is determined according to this formula in the case when, for a given size of grinding product, the value of Calculation of energy required for grinding in a ball mill
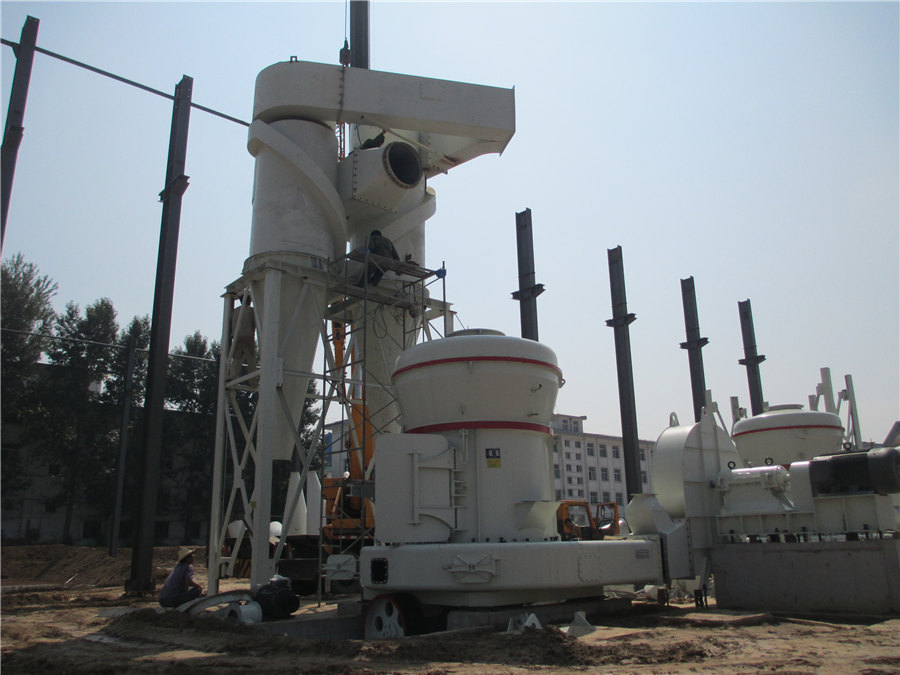
BALL MILLS Ball mill optimisation Holzinger Consulting
than 60 per cent of electrical energy consumption is used for grinding In optimising the process, the grinding tools will have a significant impact on lower production costs as well as maintenance costs Ball mills and grinding tools Cement ball mills 2018年3月12日 SEC correction SEC was affected by the material feed rate; a high feed rate will use less energy per unit mass than a low feeding rate The minimum SEC was achieved when the equipment was operated at a feeding rate that matches its rated power [], defined as the highest power input allowed to flow through the particular equipmentIn a commercial grinding system, Energy consumption of twostage fine grinding of Douglasfir