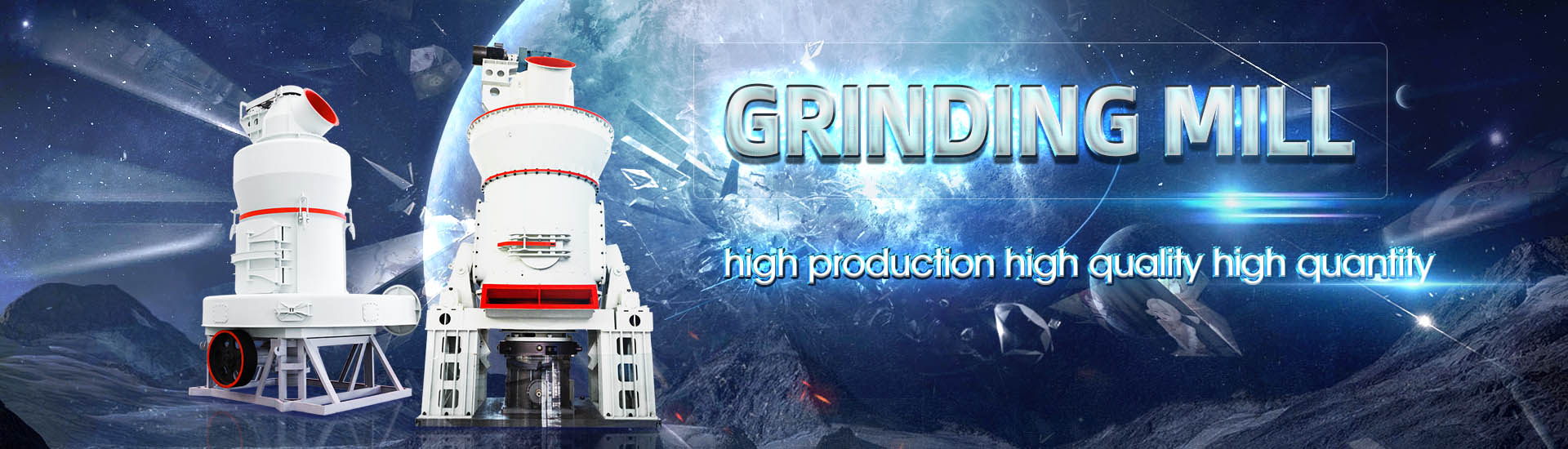
Grate ball mill steel ball wear calculation
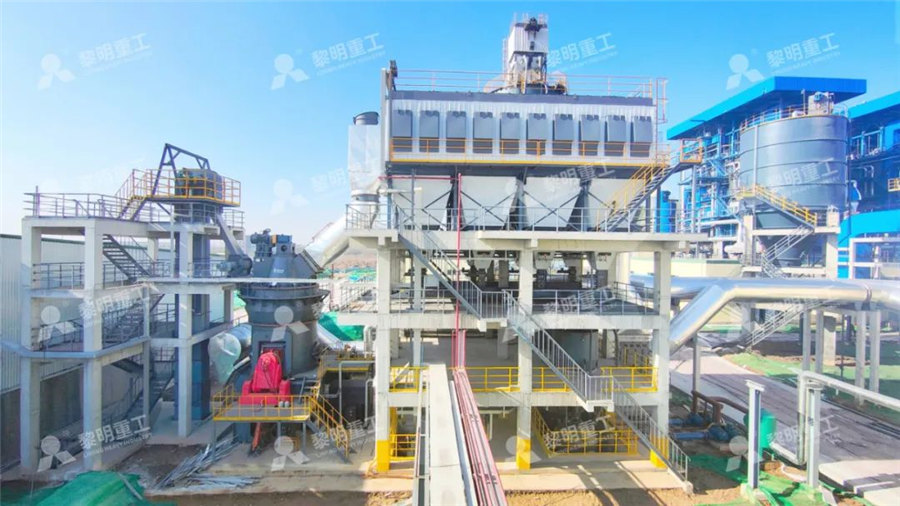
Grinding Media Wear Rate Calculation in Ball Mill
2017年4月29日 First determine the ball wear for the previous 24 hr This may be done by obtaining a rough calibration of the power meter in the motor circuit so that any definite decrease in power indicates a given decrease in the weight of the charge This is, then, the ball wear in 1993年1月1日 Ball mill wear occurs as a result of the violent interactions within the ball charge In the present article, a mathematical description of wear has been added to a ball charge motion model Wear is associated with the Modelling and simulation of ball mill wear1986年3月1日 Using a population balance approach, a general mathematical model is developed for the ball wear in rotary grinding mills The firstorder partial differential equation Mathematical model of ball wear in grinding mills I Zeroorder 2001年3月1日 From the ratio of total weight of balls in the mill to the daily addition weight of balls, the ratio of the grate openings size of the mill to the original ball size, and the rotationA simple calculation for residency time of grinding
.jpg)
(PDF) Prediction method of the law of steel ball wear in ball mill
2014年6月1日 The variation of steel ball diameters can be simulated and predicted effectively, and the prediction model can be also used as a calculation basis in adding steel balls 2016年1月1日 In this paper the BMA test methodology was applied to investigate the wear rates of four grades of grinding media using two small laboratory ball mills The rankings obtained from the testsA comparison of wear rates of ball mill grinding media2001年3月1日 From the ratio of total weight of balls in the mill to the daily addition weight of balls, the ratio of the grate openings size of the mill to the original ball size, and the rotation A simple calculation for residency time of grinding balls inside 1987年10月1日 The effect of wear rate law, design factors and operating conditions on the size distribution of balls and steel consumption were studied via simulation techniques and a Mathematical model of ball wear in grinding mills II General
.jpg)
Wear ofgrinding media in the mineral processing industry: An
SAG mills and calculated the wear rate exponent to be 28 This implies that SAG balls wear fastest at their full size and wear progressively slower as their mass is decreased2016年11月12日 The influence of the ratio of mill size on the rate of wear ∅4(d/D) can more conveniently be written in the form ∅4(D/d), and in Fig 87 are plotted the data of Coghill and Devaney and Gross, relating to the wear of Grinding Media Lining Media Liner Wear Rate – gives us unparalleled insight into the causes of wear and how to combat it Simply put: we know what we’re talking about And that means we’re your reliable partner for mill wear optimisation Add into the mix our advanced 3D scanning, liner profiling, and wear prediction technologies and you have a winning packageFLS Advanced mill liner wear measurement and prediction servicesonline live calculators for grinding calculations, Ball mill, tube mill, critical speed, Degree of filling balls, Arm of gravity, mill net and gross powerball mill calculations, grinding media filling degree, ball size, mill
.jpg)
Converting a ball mill from overflow to grate
2020年6月23日 In some operations, grate discharge mills can lead to unscheduled downtime due to grate failure, blockage of grates due to sticky ores or poor design, and increased ball consumption due to high wear rates of 2016年1月5日 The grates and wear plates are normally made from alloy wear resistant cast steel or rubber They are ribbed to prevent racing and excessive wear In grate ball mill work there are no discharge head liners The discharge grates and grate assembly replace these partsBall Mill Liner Design 911MetallurgistFrom this fixed point, mill speed and After adjusting the model to the ball mill data, the charge volume were varied in order to determine their effects of ball mill rotation speed (Fig 13) and bail effect on ball mill wear, The specifications of the ball mill filling (Fig 14) on the respective energy rate mill are found in Table 4 and Fig Modelling and simulation of ball mill wear Academia2013年9月8日 Ball load is also a factor, as you can operate with a higher ball load of smaller media without risking high ball wear and/or liner damage So going to a larger 5″ ball is a good idea for primary crushed feed with a relatively large grate opening if there is evidence the 4″ ball is not enough to break the coarse particlesSAG Mill Ball Size Evaluator Evaluation Factors Calculate
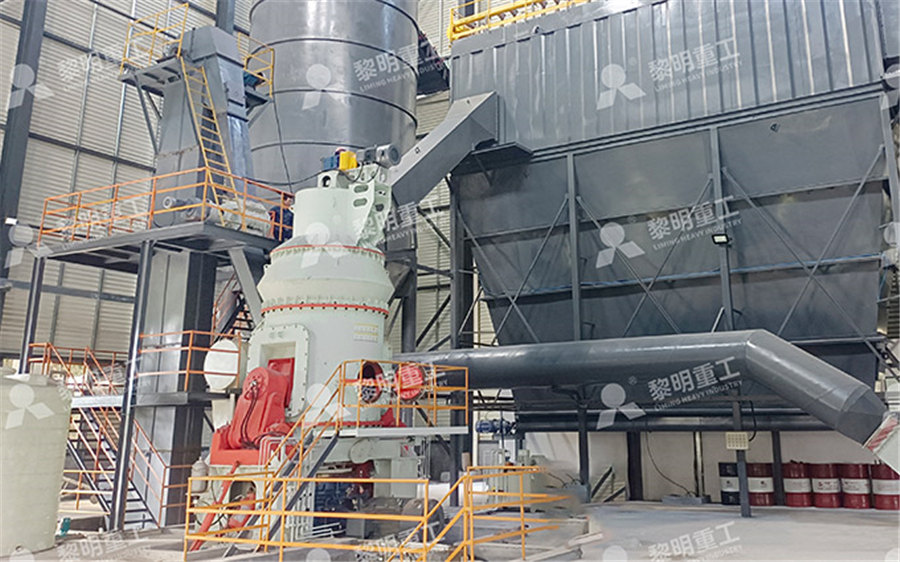
Calculate and Select Ball Mill Ball Size for Optimum Grinding
2013年8月3日 In Grinding, selecting (calculate) the correct or optimum ball size that allows for the best and optimum/ideal or target grind size to be achieved by your ball mill is an important thing for a Mineral Processing Engineer AKA Metallurgist to do Often, the ball used in ball mills is oversize “just in case” Well, this safety factor can cost you much in recovery and/or mill liner 2024年2月19日 The ratio of steel balls in the ball mill depends on the effective length of your mill, whether it has a roller press, the size of the feed particles, the lining and structure used, the expected sieve residue fineness and ratio, how many chromium balls to operate, and the rotation speed How much and other factors make a comprehensive judgmentBall Mill Steel Balls: Quality And Gradation JXSC Mineral2023年10月27日 The ball mill is a rotating cylindrical vessel with grinding media inside, which is responsible for breaking the ore particles Grinding media play an important role in the comminution of mineral ores in these mills This work reviews the application of balls in mineral processing as a function of the materials used to manufacture them and the mass loss, as A Review of the Grinding Media in Ball Mills for Mineral 2023年4月23日 One of the most used tumbling mills is the ball mill already been conducted so far on steel balls has sh own a linear behaviour in the wear rate of steel balls [77] When balls (PDF) Grinding Media in Ball MillsA Review ResearchGate
.jpg)
Ball Mill Success: A StepbyStep Guide to Choosing
2024年8月8日 Steel Balls: Predominantly made from carbon steel, stainless steel, or alloy steel, steel balls are renowned for their high density and impact strength This makes them especially suitable for heavyduty milling tasks in 2016年6月6日 Mill Internals As with rod and ball mills liner designs for autogenous and semiautogenous mills have been in a state of flux for a number of years Operators continually search for optimum designs Each mill SAG Mill Liner Design 911Metallurgist2024年9月12日 Friction and wear test equipment, scanning electron microscope, abrasion balls made of CGr15 high carbon chromium bearing steel, and liners made of NM500 steel were used for wear simulation and friction–wear experiments The variation trends of friction coefficient, wear amount, and subsurface characteristics under dry friction and slurry conditions were studied Friction and wear characteristics and simulation study of NM500 2015年6月20日 A Ball Mill Critical Speed (actually ball, rod, AG or SAG) is the speed at which the centrifugal forces equal gravitational forces at the mill shell’s inside surface and no balls will fall from its position onto the shell The imagery below helps explain what goes on inside a mill as speed varies Use our online formula The mill speed is typically defined as the percent of the Ball Mill Critical Speed 911Metallurgist
.jpg)
Calculate Ball Mill Grinding Capacity 911Metallurgist
2015年10月15日 Learn how to calculate the grinding capacity of your ball mill with 911 Metallurgist This guide provides essential formulas, insights, As defined, this value should never exceed 100%, but in some cases – particularly in Grate Discharge Mills – Grate liners and ball mill liner The type of ball mill liner known as a grate liner is designed for discharge efficiency It allows the discharge of ground materials via slots With the Magotteaux range of alloys and their experience a longer lifetime and optimal grinding can be achievedBall mill liner Magotteaux> 600 – 700 BHN Cr iron rod mills and ball mills > Excellent abrasion resistance Provide the best combination of toughness and abrasion resistance among white cast irons The tradeoff is between wear resistance and toughness > Two types: the hard, discontinuous, X7C3 eutectic carbides present in the microstructureThe Selection Design and Application of Mill Liners for Large Wet Compared with overflow ball mill, grate ball mill is a type of ball mill grinder that can realize forced ore discharging by grid lining plate and fanshaped chamber Besides, it has a larger capacity, less overgrinding phenomenon, low operation noise, and high working efficiencyGRATE DISCHARGE BALL MILL
.jpg)
Horizontal Grinding Mill Overflow Type, Gratedischarge Type,
The gratedischarge type of Ball Mill has a grate at the outlet of the shell and causes less excessive grinding, compared to the overflow type Therefore, generally, it is best suited to grind materials up to the particle sizes ranging from 60 to 100 meshThe ball mill discharge configurations and shell lifter bars have undergone significant modifications and changes to improve mill performance The ball mill was initially fitted with 100% rubber liners and discharge grate The mill had a total number of twenty installed 15 mm × 30 mm opening discharge grates TheConverting of Lubambe Copper Mine Ball Mill from Grate From the principle of crushing machanics, a theoretical formula for calculating ballsizes for ball mills has been derived Empirical parameters are obtained from experimentaland practical data, and a semitheoretical formula for calculating precise ball diametersis establishedTHEORETICAL CALCULATION OF MILL STEEL BALL SIZESciEngineThis paper covers theoretical and experimental explorations for the sake of determining the optimal ball charge in mills Tube mills use steel balls as grinding media Due to wear in the abrasive Vibor razmera šarov dlja THE OPTIMAL BALL DIAMETER IN A MILL
.jpg)
The Ultimate Guide to Ball Mills Miningpedia
2019年8月14日 The Grinding Media Of Ball Mill – Steel Balls back to top The steel balls in ball mill are consumable, which need to be supplied from now and on 1 The filling rate of steel balls Steel balls undertake the main job in grinding, therefore, the number of steel balls in ball mill is highly relative with the grinding strength2024年9月30日 The liner is a wearprone component in ball mills, subject to continuous impacts, squeezing, and abrasion from the grinding media during operation Its service performance directly affects the working efficiency of the ball mill The service life of mining ball mill liners is about 8 months, and frequent downtimes occur due to liner wear and loss of effectiveness, Effect of Grinding Media Grading on Liner Wear and Load Ball mill In properly designed and operated overflow ball mills, the shell is protected by the ore and media charge; there should not be any direct mediatoliner impact The hardest, most wearresistant alloys can be used Some ball mills are equipped with grate discharge systems They require softer alloys, as it is difficult to ensureThree factors that determine the wear life and performance of mill 2016年10月20日 Mill SHELL Liner HEAD Liners Grate discharge heads for ball mills are completely assembled in the shop, with grates, clamp bars, pan liners, and center discharge liners in place Depending upon available handling facilities, the head or shell can be lined separately in a repair bay, or after assembly of the mill proper in the trunnion bearingsBall Mill Maintenance Installation Procedure 911Metallurgist
.jpg)
(PDF) Design of Threechamber Ball Mill ResearchGate
2021年1月1日 Comchambered with the design of Φ 35 × 13m threechamber ball mill, the design process of ball mill is described in detail General arrangement of the mill Filling rate of grinding body in each 2024年1月1日 According to the discharge methods of the ball mill, it can be divided into overflow ball mill, and discharge is through the hollow shaft Grate ball mill (Fig 3), the discharge end of the mill is set with a gratePeripheral discharge ball mill, and the products are discharged through the discharge port around the cylinderBall Mill SpringerLinkInvestigations were carried out in a laboratory ball mill having the size of DxL = 160x200 mm with a ribbed inside surface of the drum The mill ball loading was 40% by volume, the rotation rate was equal to 85% of the critical speed Balls were made from steel: S4146, extra high quality, having hardness 62 ± 2 HRC according to RockwellTHE OPTIMAL BALL DIAMETER IN A MILL 911 Metallurgist2014年6月1日 High wear rates were observed when using forged highcarbon steel ballsA pilotplant ball mill, with a 001m3 chamber, was used to perform wear tests, comparing the original ball material and (PDF) Prediction method of the law of steel ball wear in ball mill
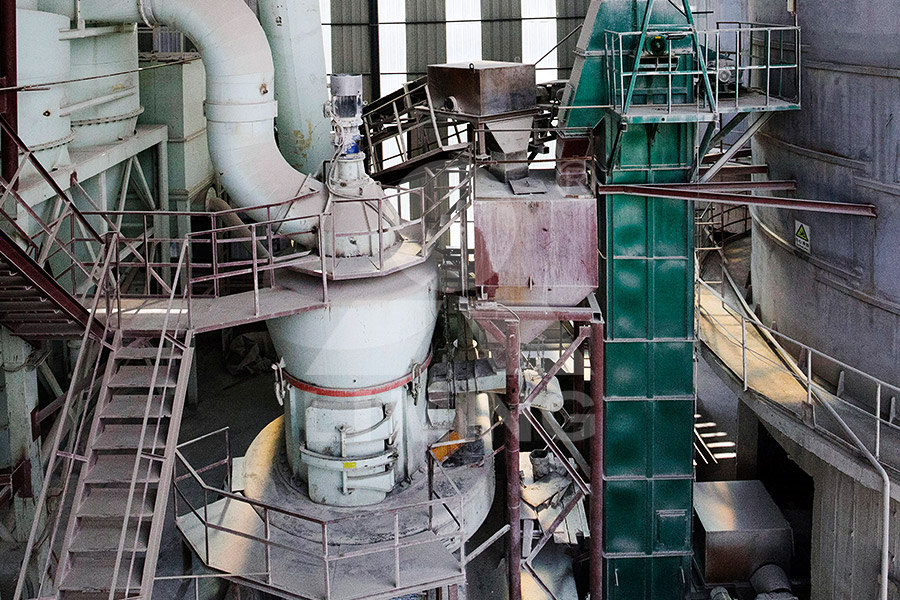
Research on NonUniform Wear of Liner in SAG Mill
largescale SAG mills, especially with the wide application of the SABC (Semiautogenous ball mill crusher) process, concentrators across the country have begun to use largescale SAG mills [2,3]balls inside grinding mills 2 Wear calculation method From the theory of grinding ball wear processes, the weight loss rate of a grinding ball in a grinding mill is expressed as [4–6], dW dt A simple calculation for residency time of grinding balls inside 2001年3月1日 The wear generated in grinding balls having a ball size distribution in a tumbling mill was investigated using a laboratoryscale mill for both dry and wet grindingA simple calculation for residency time of grinding The Ball Mill Abrasion (BMA) test was developed by the University of Queensland Materials Performance group to simulate the high stress abrasion conditions experienced in production ball mills It gives accurate predictions of the service life of wear resistant alloys in mill liner and grinding media applications In this paper the BMA test methodology was applied to A comparison of wear rates of ball mill grinding media
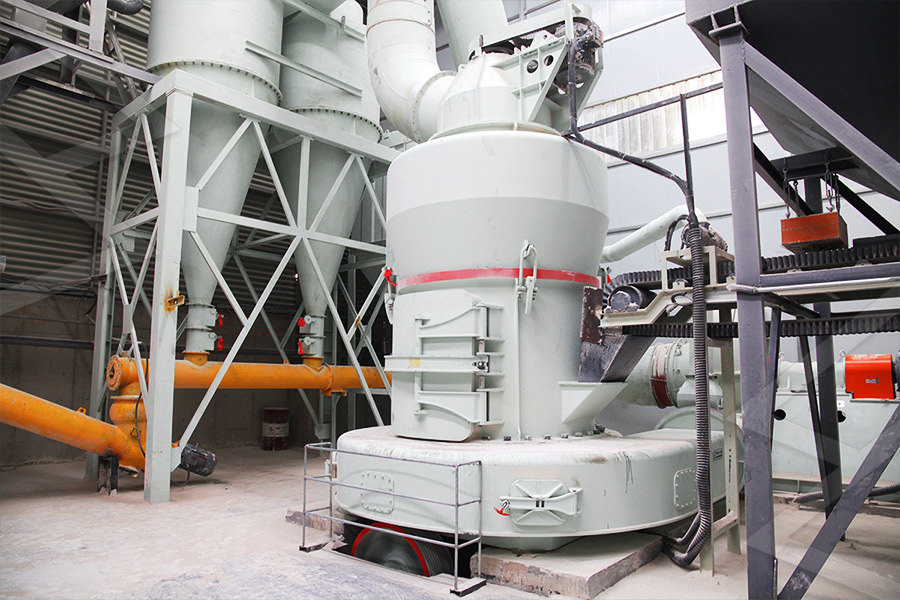
A population balance model of ball wear in grinding mills: An
2018年11月1日 Ball wear kinetics equations for three different sized balls in a grinding mill were found • Calculations of ball flux for the mill recharging were performed • Alumina ball consumption was calculated by a realistic and general model • The wear kinetics was found to be of zero order in accordance with previous reports2018年4月11日 Marked ball wear testing described in a 1948 paper by Norman is an invaluable test method to measure relative and/or absolute wear rates of balls under identical mill operating conditions Preparation of balls at Armco consists of drilling a 64 mm diameter hole in each ball with an electrical discharge machine (EDM), cleaning, weighing, placing a coded identifying Marked Ball Wear Test 911Metallurgist2016年3月14日 It embodies the peripheral discharge with grates, large forgedsteel balls, and the principal features of the modern ball mill The results approach presentday practice, the chief differences being that the mechanical construction has been improved in the modern typesPeripheral Discharge Ball Mills Theory and PracticeIf a ball mill uses little or no water during grinding, it is a ‘dry’ mill If a ball mill uses water during grinding, it is a ‘wet’ mill A typical ball mill will have a drum length that is 1 or 15 times the drum diameter Ball mills with a drum length to diameter ratio greater than Ball Mill (Ball Mills Explained) saVRee saVRee
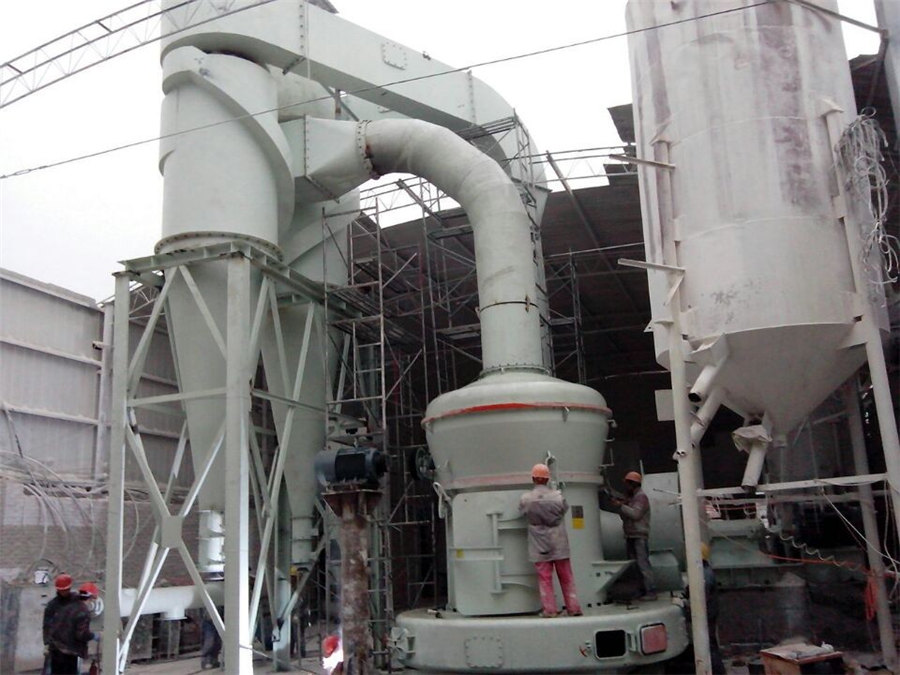
Grinding Mill Liners 911Metallurgist
2015年8月6日 The wrong liner design will increase power and steel consumption, as well as reduce the grind and throughput of the mill Liners not only come in different designs, they are available constructed from different materials Liners may he built from MANGANESE STEEL for rod mills and ball mills that use bigger than two inch ballsThis design uses heavy duty support rollers to drive the rotation of the mill shell directly Depending on the, the drive and support rollers can be polyurethane lined rollers or a series of rubber tyres Bulk Handling Techonolgies can design and supply roller mounted ball mills with capacities ranging from 500 kg/hr up to 25 TPH in a single millBall Mills and Ball Charging Bulk Handling Technologies