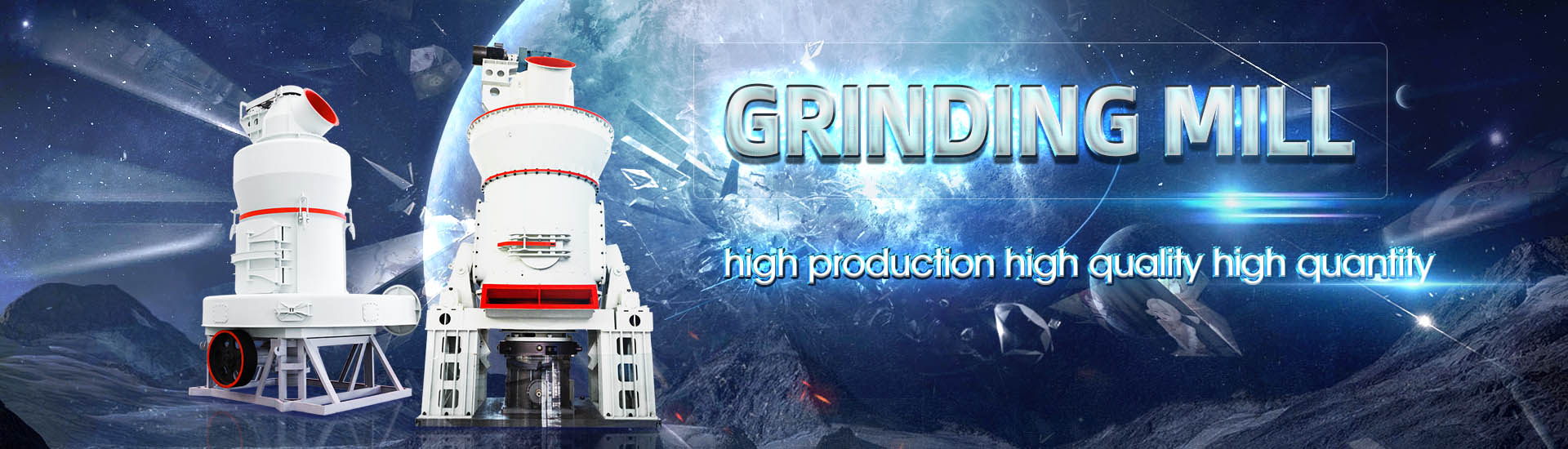
Fly ash aerated block powder making process and cost
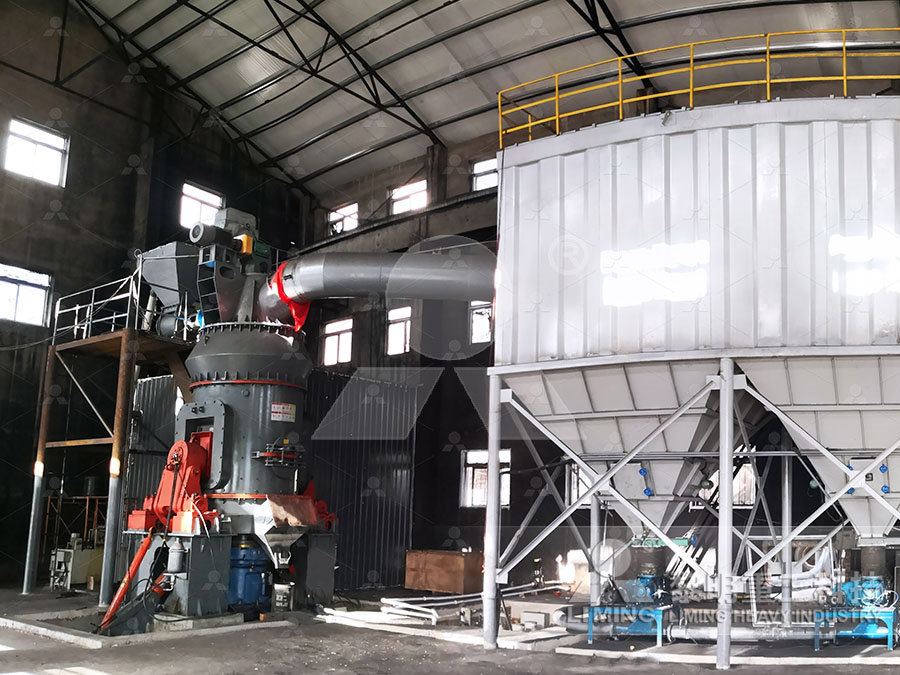
Life cycle assessment of autoclaved aerated fly ash and concrete
In this study, ReCiPe midpoint (H) model is used to examine the environmental impact of AAFACB production Characterization (midpoint results) refers to analyze 展开2017年9月17日 AAC blocks are light weight Aerated Autoclave Concrete Block It is manufactured through a reaction of aluminium powder and a proportionate blend of lime, cement, and fly ash or sandMANUFACTURING PROCESS OF AAC BLOCKAutoclave curing is a critical process for enhancing the mechanical strength of the AAC, and tobermorite is the major hydration product The fly ash (FA) generated from a municipal solid Production of autoclaved aerated concrete by using municipal 2020年7月15日 The Autoclaved aerated concrete (AAC) is a product of fly ash which is mixed with lime, cement, and water and an aerating agent The AAC is mainly produced as cuboid blocks and(PDF) Analysis of Autoclaved Aerated Concrete (AAC)
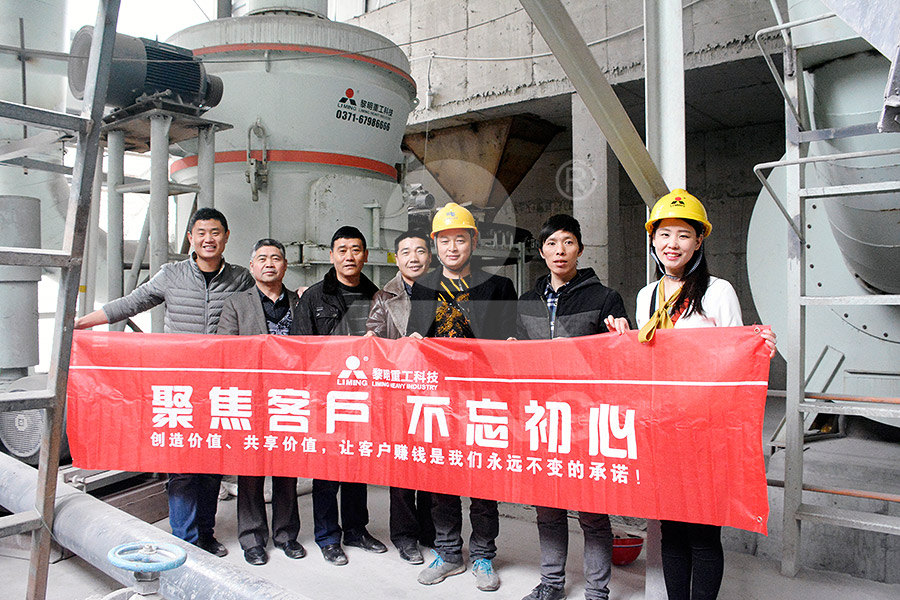
(PDF) Comparison of Fly Ash Based (AAC) Block and Clay Bricks for
2021年8月1日 This paper presents comparative analysis of clay bricks and fly ash based autoclaved aerated concrete (AAC) block properties, methodology, process and material 2024年10月22日 This study explores the utilization of these waste streams in developing sustainable construction materials, focusing on fly ashbased geopolymers and incorporating Mechanical, microstructural, durability, and energy analysis of fly Autoclaved Aerated Concrete (AAC) is versatile light weight concrete and they are generally used as blocks The study of AAC replacing natural sand by fly ash is investigated Design AAC mix Study and Experimentation of Autoclaved Aerated Concrete by 2022年11月17日 The primary goal of this study is to develop lowcost sustainable aerated concrete utilizing silica fume and fly ash and investigate their effect on strength characteristics Combined effect of silica fume and fly ash as cementitious
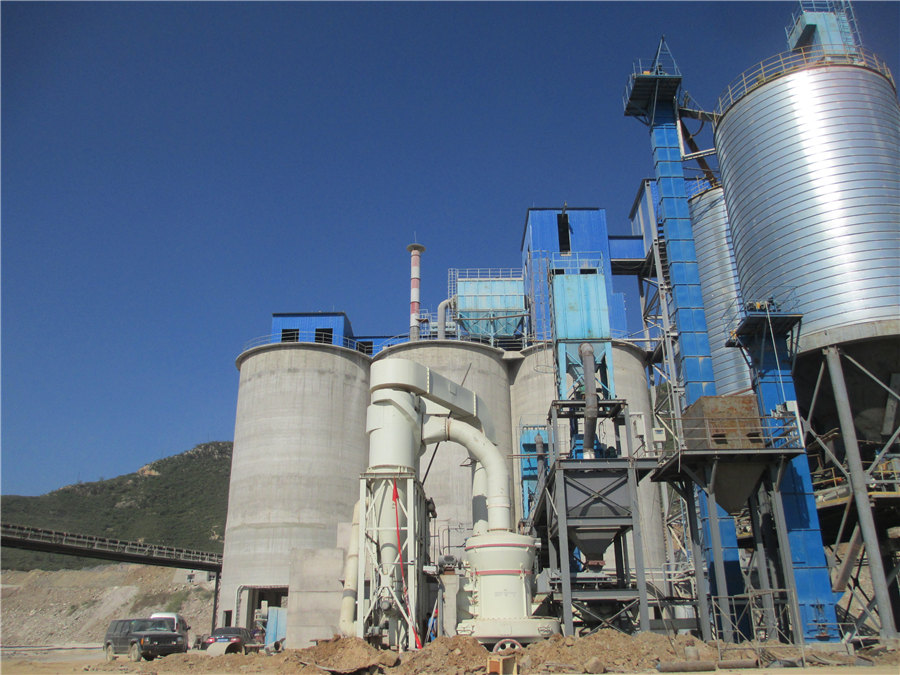
Fly ash for sustainable construction: A review of fly ash concrete
2022年12月1日 Fly ash makes concrete workable; increasing its levels may reduce water demand and superplasticizer needs Fly ash can improve mechanical and durability 3 天之前 The most commonly used onepart AAC are GBFS and fly ash (FA) GBFS is the most commonly used raw material for AAC production AAC derived from GBFS possess a dense Fly ash sinking beads and slag based onepart alkaliactivated FLY ASH BRICKS: AAC BLOCKS: Major component: Fly ash bricks use the fly ash as major raw material In Acc blocks , aluminum acts as major component factor Percentage composition: Fly ash – 50%80% Sand – 20%40% Fly ash bricks vs AAC blocks – Features, Preparation, 2023年8月4日 AAC blocks are ecofriendly because fly ash recycles waste and reduces carbon footprint Faster Construction Process: AAC blocks‘ huge size and ease of installation make building projects faster and cheaper Cost Aerated Concrete Blocks: Building with Innovation
.jpg)
Autoclaved Aerated Concrete: Difference Between
2022年8月15日 Conclusion Autoclaved sand aerated concrete has certain advantages compared with autoclaved ash aerated concrete After all, sand aerated block is an updated alternative to traditional fly ash aerated block, and A Fly Ash or Sand Key ingredient for manufacturing AAC blocks is silica rich material like fly ash or sand Most of the AAC companies in India use fly ash to manufacture AAC blocks Fly ash is mixed with water to form fly ash slurry Slurry thus formed is Study and Experimentation of Autoclaved Aerated Concrete by using Fly Ashaluminium powder and a proportionate blend of lime, cement, and fly ash or sand Autoclaved aerated concrete (AAC) is a lightweight cellular concrete that has been used for more than 80 yearsMANUFACTURING PROCESS OF AAC BLOCK ResearchGateThis paper presents comparative analysis of clay bricks and fly ash based autoclaved aerated concrete (AAC) block properties, methodology, process and material required for preparing fly ash based Cost Comparative Analysis for AAC Blocks and Clay Brick
.jpg)
Understanding the Differences: AAC Blocks vs Fly Ash Bricks
2024年6月16日 AAC Blocks: Autoclaved Aerated Concrete (AAC) blocks are made from a mixture of cement, lime, sand, water, and an expansion agent such as aluminum powder This mixture is then cured in an autoclave, a highpressure steam chamber, which gives AAC blocks their lightweight and porous structurealuminium powder and a proportionate blend of lime, cement, and fly ash or sand Autoclaved aerated concrete (AAC) is a lightweight cellular concrete that has been used for more than 80 yearsMANUFACTURING PROCESS OF AAC BLOCK ResearchGate2023年7月7日 Lime Powder: Lime powder serves as a crucial binding agent, constituting approximately 14% of the Autoclaved Aerated Blocks composition Prior to usage during production, lime powder undergoes rigorous testing to assess its properties, including the temperature and calcium oxide concentrationAutoclaved Aerated Blocks – IJERT2023年10月1日 Concrete hollow blocks (CHB) have been used worldwide, especially in the Philippines, due to their costsaving and lightweight features Moreover, the energyefficient CHB promotes faster Comparison of Autoclaved Aerated Concrete (AAC) Blocks and
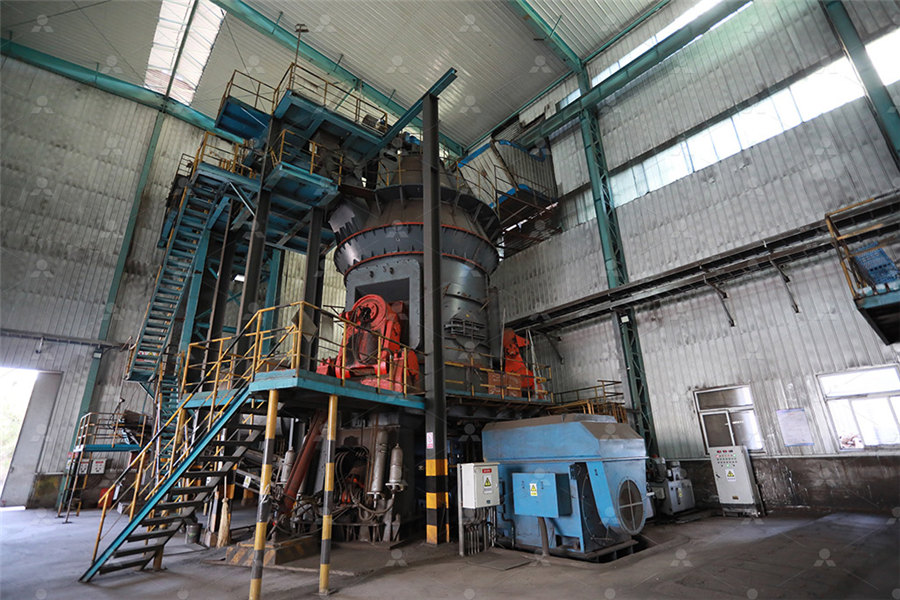
Life cycle assessment of autoclaved aerated fly ash and concrete block
2019年6月23日 Choosing 1 m3 of autoclaved aerated fly ash and concrete block product as functional unit and “cradle to gate” as system boundary, aluminum powder, phosphogypsum, and fly ash is 100 km, 17 km, 17 km, and 26 km, The AAFACB production process cost mainly derive from four stages, namely, lime grinding, Fly Ash Bricks advantages and excellent manufacturing process In India Fly ash bricks are lighter than Red clay bricks Best Quality fly ash bricks manufacturing process advantages and cost Main ingredients include fly ash, water, quicklime or Fly Ash Bricks, Advantages, Cost, Excellent Manufacturing Process2022年11月17日 The mix containing 15% silica fume and 30% fly ash as cement replacement produced 234568 KgCO 2 /m 3, a great reduction of 4263% of embodied CO 2 emission as compared to control mix at 40888 KgCO 2 /m 3 5 With the substitution of cement with silica fume and coal fly ash, cost of AAC greatly bined effect of silica fume and fly ash as cementitious Non autoclave aerated concrete blocks consists of fly ash, cement, lime, gypsum and aluminium powder as an expansion agent Compressive strength test is carried on 706 mm × 706 mm ×706 mm cubes of nonautoclave concreteAnalysis and Design of Light Weight Aerated Concrete using Fly Ash
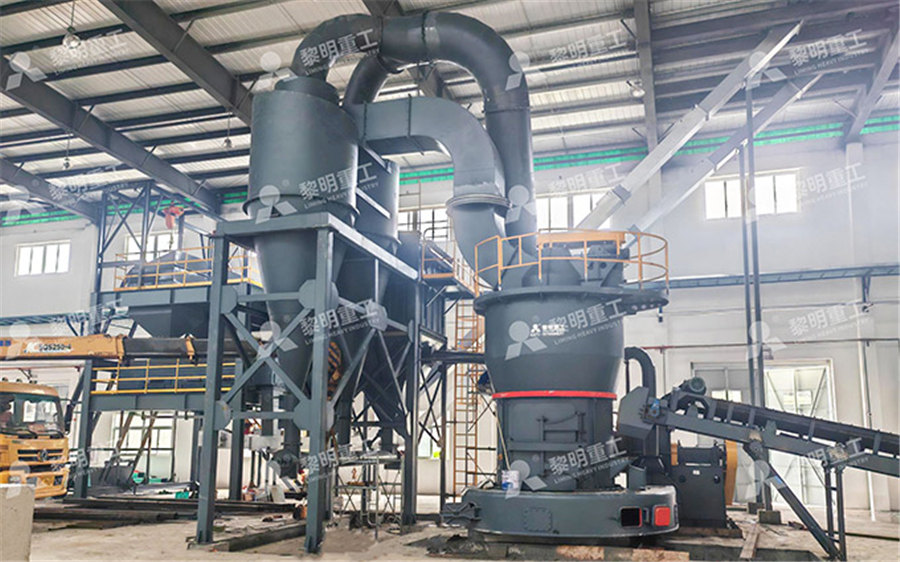
Preparation of Autoclaved Foamed Concrete Block from Fly Ash
2018年1月1日 To achieve the comprehensive utilization of solid waste and reduce costs, fly ash, carbide slag, and lowclinker cement were used to produce lightweight foamed concrete block2023年12月6日 The process of creating AAC blocks sets it apart from other materials It involves the combination of sand, cement, lime, and aluminum powder Highpressure steam cures the mixture in autoclaves, making blocks that are both light and strong that are changing the story of building 1 Cost Efficiency: AAC Blocks: Economical production processAAC Blocks vs Traditional Materials: A CostEfficient and Superior Manufacturing Process of AAC Block First a fall, autoclaved aerated concrete is produced by mixing silica or sand or fly ash with cement, lime, water, and expansion agents such as aluminum powder Advantage of AAC Block Due to lightweight, it Save cost and energy in transportation;AAC Blocks Specifications (Autoclaved Aerated Concrete), 2024年4月26日 The research concludes that foamed concrete with 65% fly ash and 25% marble sludge powder exhibits high 28day compressive strength, making it suitable for building partition walls Lastly, an exploration into environmentally friendly concrete incorporates natural fibers like jute, coconut, sugar cane, sisal, and basalt, maintaining reasonable compressive strength A comprehensive study of building materials and bricks for
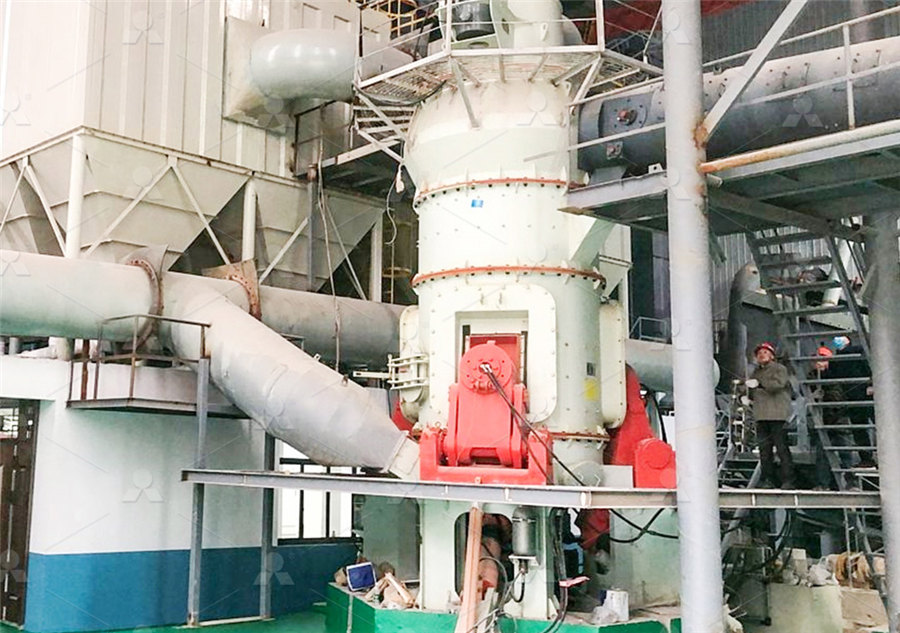
Autoclaved Aerated Concrete AAC Block Making Machine
Autoclaved Aerated Concrete AAC Block Making Machine, Fly ash style aerated block raw material: Sand style aerated block raw material: Parameter Name: Fly ash: 6570%: Sand: 5565%: cement: 615%: cement: 1020%: Lime: 1825%: Lime: 2030%: Gypsum: 35%: Gypsum: 23%: Aluminum powder paste: 8: Aluminum powder paste: 8: Water material 2021年5月11日 20244 Bricks Manufacturing The synthetic pozzolanic character of FA is because of the constituents accomplishing amorphous silicate minerals Usually pozzolanic ash does react with slaked lime and water to form the complex, ie, CaO–Al 2 O 3 –SiO 2 –H 2 O (Çiçek and Çinçin 2015)The fired clay type bricks have been used on masonry constructed Prospective Utilization of Coal Fly Ash for Making Advanced Materials2021年9月1日 Adsorption has been a simple and efficient technique among many removal methods for the uptake of heavy metal ions by using fly ash as a low cost as well as effective adsorbent The first reported employment of fly ash for the removal of heavy metals from industrial wastewater was interpreted at 1975 by Gangoli et al (Wang, 2006)Fly ash properties, characterization, and applications: A review2024年5月24日 The blocks’ advantages are enhanced by using fly ash, a waste byproduct Using these blocks in a building’s construction makes them an environmentally responsible option Properties of AAC Blocks The properties Guide to Autoclaved Aerated Concrete Blocks (AAC
.jpg)
Technological Properties of Fly AshBased Lightweight Springer
2021年2月23日 According to the previous report by Ling and Teo [], Siram [] and Xu et al [], there are still uses an OPC cement and clay as a source material in making lightweight bricksEven in the production of commercial lightweight masonry units, which are cellular lightweight (CLC) blocks and autoclaved aerated concrete (AAC) had utilized OPC cement The manufacturing process and equipment of aerated block production line have been exported to Uzbekista HOME; ABOUT ABOUT US; HISTORICAL cement, gypsum, aluminum powder, fly ash lime and cement as a cement, gypsum as a hardener stable quality, effectively reduce the cost of finished products 04 Cutting system cutting machine is FLY ASH AAC BLOCK PLANTAAC BLOCK 2022年10月13日 For the AAC blocks manufacturing process, raw material preparation is crucial The raw material for AAC blocks is fly ash or pond ash The mixture of fly ash and water forms a slurry, which is mixed with other ingredients such as lime powder, cement, gypsum and aluminium powder in quantities consistent with the recipe Dosing and MixingManufacturing Process of AAC Blocks A Quick Guideessential for the production of AAC blocks is fly ash, which plays an essential role in the manufacturing process Fly ash is combined with water to create a fly ash slurry, which serves as the foundation for the subsequent steps This slurry is then blended with precise quantities of lime powder, cement, gypsum,Autoclaved Aerated Blocks International Journal of Engineering
.jpg)
Analysis of Aerated Concrete (AAC) Block and it's Masonry
Autoclaved aerated concrete (AAC) blocks are the lightweight and green concrete blocks that are composed of cement, fly ash, lime, gypsum and aluminium powder Depending on its density AAC 2023年9月1日 This study presents a comprehensive analysis of the development of aerated concrete (AC) blocks with a focus on the effect of various binders and additives on their mechanical and durability properties The binders are flyash (FA), glass powder (GLP), and ground granulated blast furnace slag (GGBS) Further, cement, lime, gypsum powder, FA, Study on Mechanical and Durability Properties of Aerated Concrete Block 2020年2月2日 To achieve the comprehensive utilization of solid waste and reduce costs, fly ash, carbide slag, and lowclinker cement were used to produce lightweight foamed concrete blockPreparation of Autoclaved Aerated Concrete (AAC) Block by using 2023年10月9日 of fly ash in aerated concrete [71] the cost of this type of catalyst makes it a valid option only for specific cases with doses of 10 to 33% fly ash The processUse and effect of fly ash in concrete: A literature review
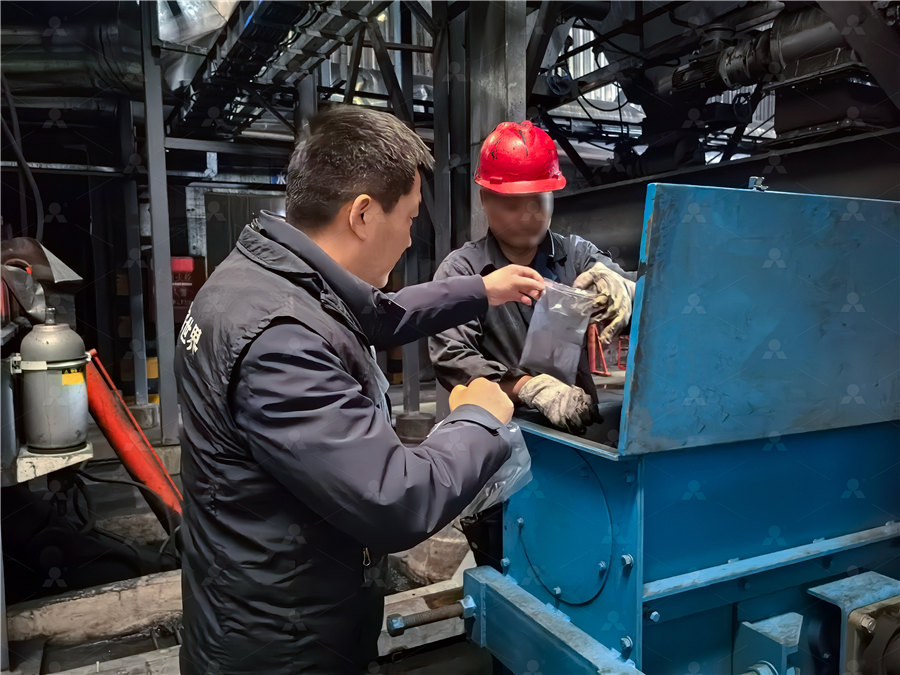
Fly Ash SpringerLink
Figure 1 shows fly ash produced in a typical pulverizedcoalfired utility boiler and collected by an electrostatic precipitator There are two commonly used methods for removing the fine powdery fly ash from the fly ash hopper of the precipitator – a wet method or a dry method [12–15]In the wet method, water is used to flush the fly ash out of the hoppers and the ash slurry is pumped 2022年11月28日 Aerated concrete is a type of lightweight concrete in which air bubbles are incorporated into concrete using aluminium powder to make it light in weight The manufacture of aerated concrete blocks without affecting the quality using waste rubber powder is an efficient waste management method and a vital step towards minimizing environmental pollution An optimized mix for the manufacture of sustainable aerated Dosing Mixing: A dosing and mixing unit is used to form the correct mix to produce Autoclaved Aerated Concrete (AAC) blocksFly ash/sand slurry is pumped into a separate container Once the desired weight is poured in, An Overview on AAC Block Manufacturing Process2018年10月12日 (3) Fly ash During the production of CAC blocks, the cement is partially replaced with fly ash to save cost and fill up the gaps [5], making the products denser Here, the Grade II fly ash produced from Quzhou Juhua Thermal Power Plant is adopted for our research The chemical composition of the fly ash is shown in Table 3 below (4) Foaming agentEffects of Replacing Fly Ash with Cutting Mud on the IIETA
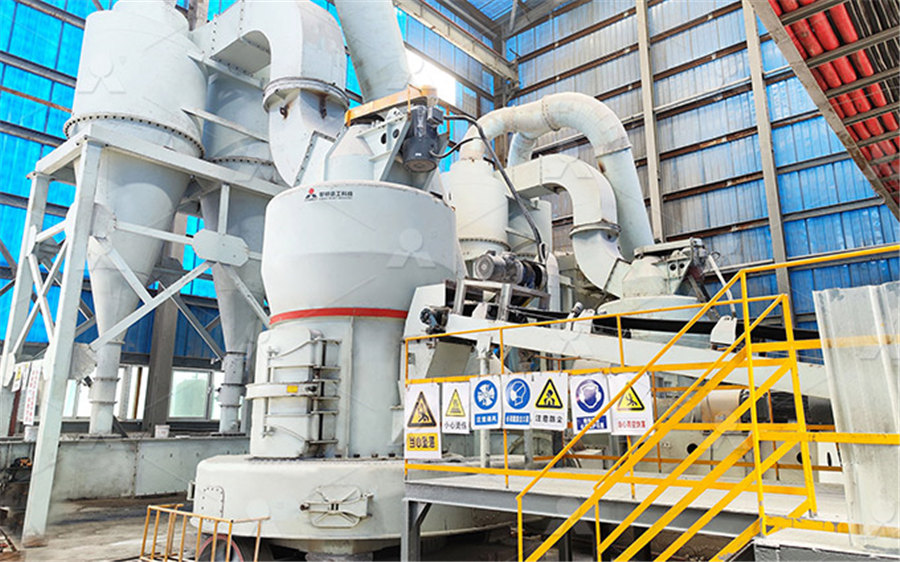
Experimental Analysis of Aerated Concrete Block
form bottom ash and fly ash Fly ash is the material that is carried off with the flue gases, where it is collected and can be stored in silos for testing and beneficial use Fly ash can be classified into classes Class F fly ash normally produced by burning anthracite or bituminous coal Usually it has less than 5% of CaOFly ash bricks making process; Fly ash bricks; Advantages and disadvantages of fly ash bricks; Fly ash brick strength test; Fly ash brick; Grey acc solid ash bricks; Rectangular autoclaved aerated concrete blocks; Fly ash bricks 230x110x70, 9 in x 4 in x 3 in; A garde rectangular lightweight bricks blocks, size: 24; What is Fly Ash Brick Fly Ash Bricks Fly Ash Blocks Latest Price, ManufacturersProject cost: Pervious concrete can lower overall project costs on a firstcost basis and promote more efficient use of the land by eliminating the need for retention ponds, swales, and other stormwater devices Operational costs: Can reduce operational costs and allow developers to increase use of available propertyApplications of Cement Portland Cement AssociationThere is ample scope for fly ash brick and block units In Chennai alone 1 crore bricks are required for constructional MANUFACTURING PROCESS: Fly ash (70%)Lime (10%) Gypsum (5%) and sand(15%) The technology adopted for making fly ash bricks is ecofriendlyPROJECT PROFILE ON FLY ASH BRICKS
.jpg)
Process Flow MEPCO
A dosing and mixing unit is used to form the correct mix to produce Autoclaved Aerated Concrete (AAC) blocks Fly ash/sand slurry is pumped into a separate container Once the desired weight is poured in, pumping is stopped Similarly lime powder, cement and gypsum are poured into individual containers using screw conveyors2021年8月26日 Fly Ash Block Size The larger version of the fly ash brick is the fly ash stone It is made of the same substance and is prepared using the same process Fly ash bricks are 24in x 8in x 4in dimension These blocks are mostly used in the partition and sidewall walls In India, a single piece of fly ash block costs around 50 rupeesWhat Is Flyash Brick? Fly Ash Bricks Cost Civil Scoops