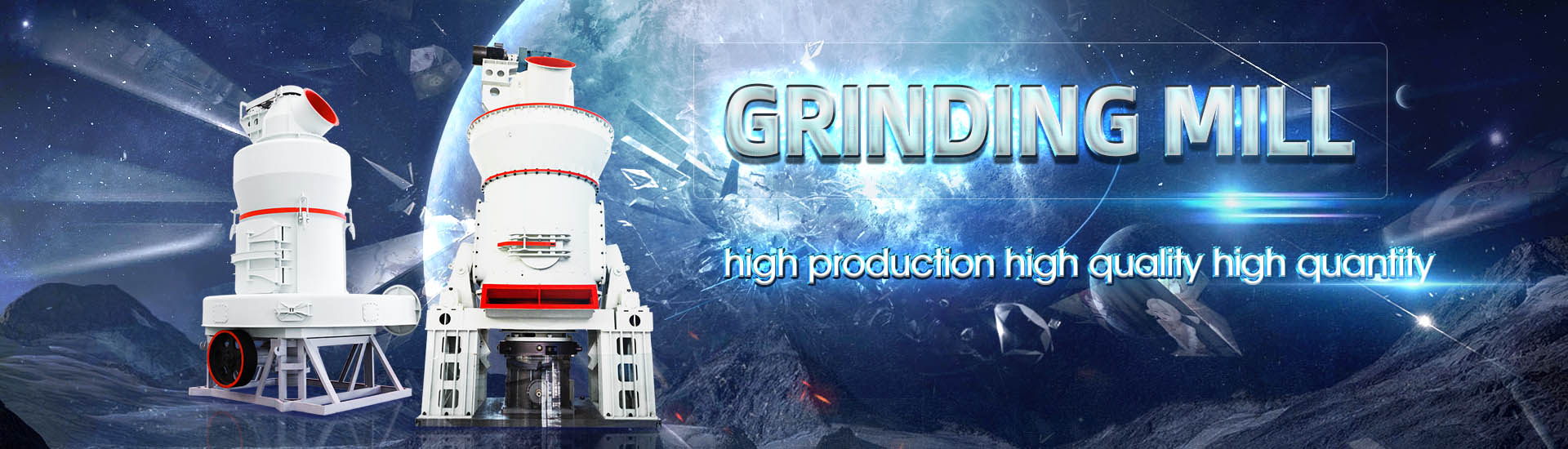
Policy for recycling slag from smelting of limestone crusher
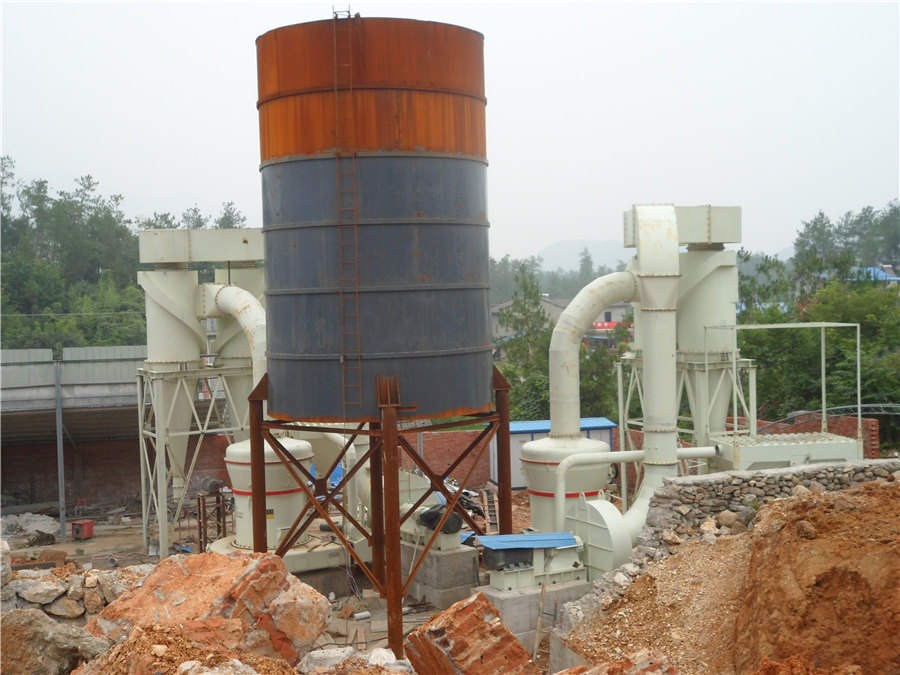
The recycling and reuse of steelmaking slags — A review
2019年7月1日 In order to lower the environmental impact of the steel industry and ensure its economic sustainability, there have been significant studies finding the ways to recycle by 2011年7月1日 The results of this study show that the optimized internal recycling process of BOF slag can improve the environmental performance of crude steel It is important to assess Life Cycle Assessment of Internal Recycling Options of Steel Slag in Slags are the important wastes and byproducts of metallurgical industry, which have been treated, recycled and used worldwide The present paper summarizes the current status of Recycling and environmental issues of metallurgical slags and salt 2021年7月7日 The accumulated experience of world practice in solving the problem of steelmaking slag recycling is described in detail Particular attention is paid to converter slag Solutions to the Converter Slag Recycling Problem in Metallurgical
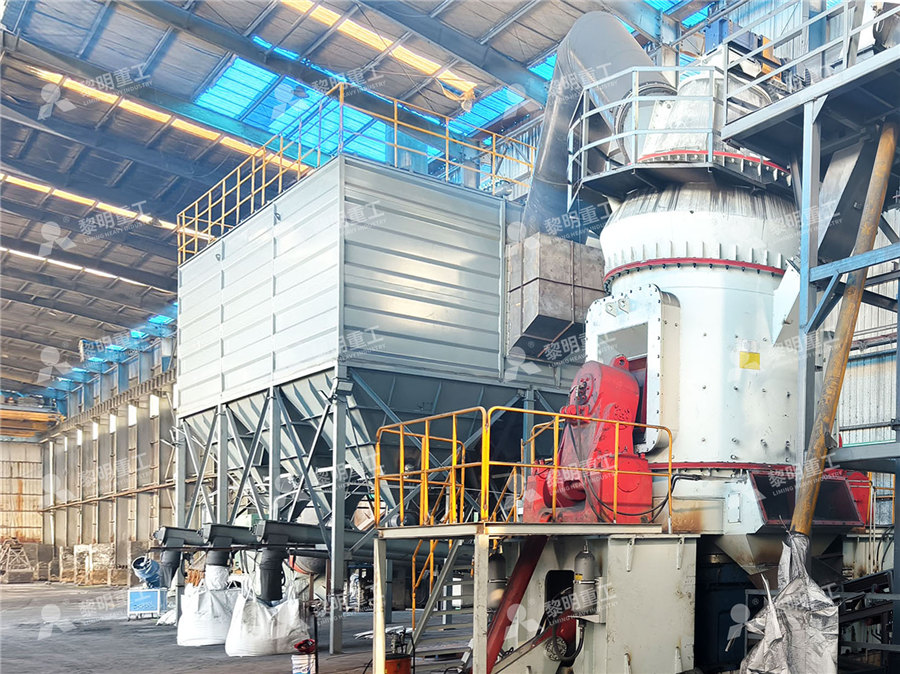
Slag Metallurgy and Metallurgical Waste Recycling JOM
2016年7月29日 One of the most important goals of copper slag metallurgy is to minimize copper losses to slag from entrained Cu droplets during the smelting of copper concentrate, 3 often Given the importance of lead battery recycling to the US lead supply this paper presents a review of lead slag chemistry and behavior, past experimental methods to study lead slags, and A REVIEW OF SLAG CHEMISTRY IN LEAD RECYCLING2016年5月16日 Reduce, reuse, and recycle are important techniques for waste management These become significant for improving environmental and economic condition of industries Sustainable Approaches for LD Slag Waste Management in Steel2023年3月6日 Recycled smelter slags can be used in both in situ and ex situ treatment However, their application has some limitations One of the challenges is how to handle spent Recycled Smelter Slags for In Situ and Ex Situ Water and MDPI
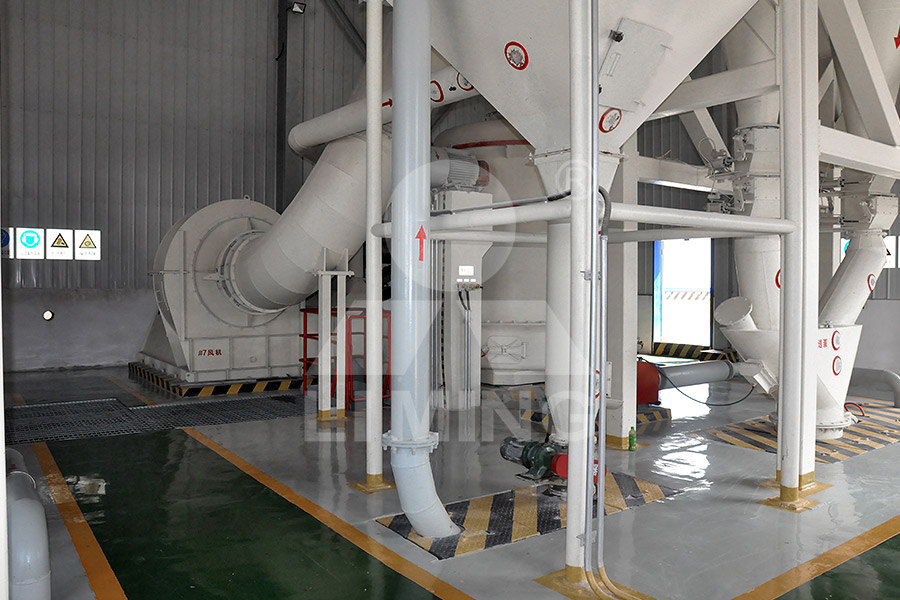
(PDF) Recycling and environmental issues of metallurgical slags
2004年1月1日 It investigated the necessary improved approach through the 5Rs (ie, reduce, reuse, recycle, remove, and recover) using smelter slags as reactive materials in ex situ and in Currently, there is a limited amount of research on the smelting slag in general Zhang S et al has successfully developed highporosity ceramics and glass ceramics using smelting slag from the waste automobile catalyst [31]In addition, the Chinese invention patent also mentioned a method for recovering rare metals lanthanum, cerium, and zirconium from smelting prehensive recycling of slag from the smelting of spent 2007年3月1日 Smelting reduction technique was applied for the recovery of valuable metals such as vanadium and chromium from LD slag using a Tamman furnace The degree of metalization of slag was 98% at 1600 °C at 30 min of time (Park et al, 1994) The slag is also reduced in an electric furnace to separate the slag and metalAn overview of utilization of slag and sludge from steel industries2024年7月16日 The electric arc furnace steelmaking route is essential for sustainable steelmaking through hydrogenbased direct reduced iron About 30% of the global steel production currently follows the scrap/direct reduced iron–electric arc furnace (DRIEAF) route, which is bound to increase given decarburization efforts by the steel industry We investigated Enhancing Recycling Potential: Exploring Reduction and Metal
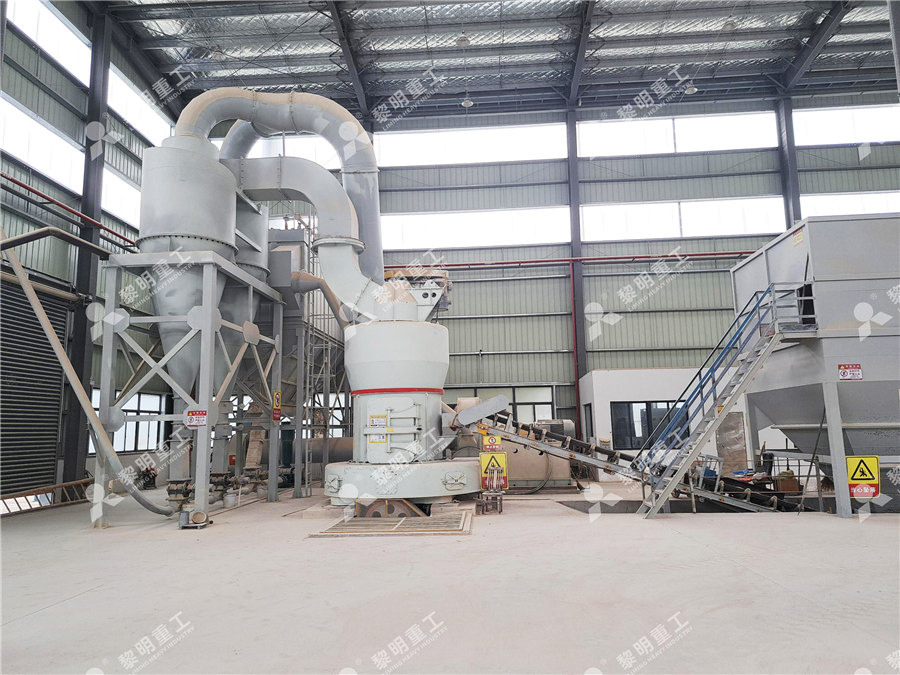
Recovery of CuFe Alloy from Copper Smelting Slag MDPI
2023年1月29日 Copper smelting slag usually contains 1–6 wt% copper, which can be recovered by pyrometallurgical and flotation processes However, the tailing slags still consist of 03–07 wt% Cu and 35–45 wt% Fe equivalents to those in the copper and iron ores, respectively Most of the research was focused on the recovery of iron from the tailing slags Copper can increase the 2024年10月9日 Slag, a byproduct of metal smelting processes, is produced in large quantities by steel mills, foundries, and other metalworking industries While once considered waste, slag is now recognized as a valuable resource due to its potential applications in construction, road building, and other industries Stationary recycling crusher plants for slag play a crucial role in Stationary Recycling Crusher Plants for Slag2017年2月8日 Materials The smelting slag used in this study was obtained from a copper plant in China Mineralogical analysis, performed using scanning electron microscope (SEM) and energy dispersive Xray spectroscope (EDS), polarizing microscope and Xray diffraction (XRD), indicated that fayalite (Fe 2 SiO 4) and magnetite (Fe 3 O 4) phases were major components The Recovery of Copper from Smelting Slag by Flotation Process2020年6月3日 Introduction Smelting slag is a typical hazardous waste generated in the smelting and metallurgy industry 1, 2Slag contains high concentrations of heavy metals, such as Cu, Zn, Cr and Ni, which are harmful if released into the environment 3In China, smelting slag is disposed of as an environmental priority pollutant, wherein the slag is generally stabilized with cement Highpurity recycling of hematite and Zn/Cu mixture from waste smelting
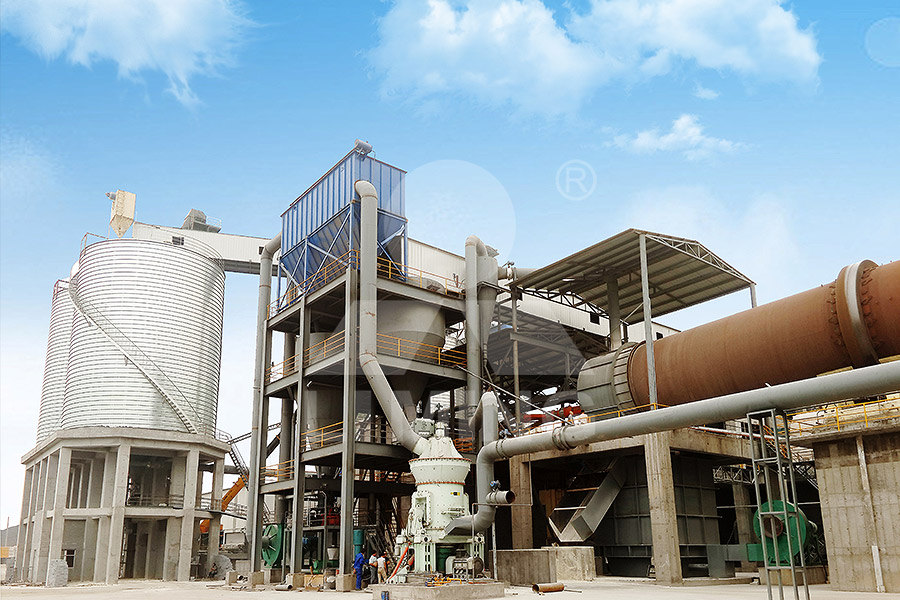
Types of Crushers: Choosing the Right One for Each Stage
2024年7月17日 A crusher, also known as a stone crusher, is a machine that uses mechanical action to break large rocks, ores, or other raw materials into gravel or rock powder Crushers are widely used in ore crushing, aggregate production, 2019年3月13日 Copper smelting production is characterized by formation of a large amount of waste, the majority of which is slags During the production of 1 ton of copper there is 2–4 tons of smelting, converter, and refining conversions slags []Flotation treatment of slags with extraction into concentrate of part of the copper in PO Balkhashtsvetmet started in 1992 [2, 5]Development of Technology for Recycling Copper Smelting 2021年4月30日 Magnesium slag that is piled in the open air is basically in the form of fine powder after the magnesium slag decomposes naturally The particle size of the slag is measured with a laser particle size tester (Microtrac X100), and the particle size distribution diagram is shown in Fig 32Table 32 shows the corresponding composition of the slagMagnesium Slag Generated by Reduction Smelting Using Pidgeon Process2016年1月1日 The principal slag constituents are silica, ferrous oxide, ferric oxide, limestone, and alumina The slag also contains high concentrations of valuable metals and metalloids such as copper, cobalt Recovery of copper from smelting slag by sulphation
.jpg)
A new ecofriendly approach for recovery of iron from copper smelting
DOI: 101016/jpsep202407026 Corpus ID: ; A new ecofriendly approach for recovery of iron from copper smelting slag: Using CO2 and Cl2 recycling strategies @article{Qin2024ANE, title={A new ecofriendly approach for recovery of iron from copper smelting slag: Using CO2 and Cl2 recycling strategies}, author={Zhengliang Qin and Junhui 2021年9月24日 During steel production, the impurities in the hot metal react with the fluxes forming the steel slag Chemical constituents of this steel slag (SS) are relevant to iron/steelmaking or blended cement manufacture Harmful impurities present in it, however, limit its recycling to these applications Japan, Europe, and the US consume a significant amount of BOF Steel Slag: Critical Assessment and Integrated Approach for reductions smelting of high lead slag Herein, toxicity leaching experiment of sulfuric acid and nitric acid method was used to evaluate the safety of the cosmelting slag to provide a basis for the cosmelting of high lead slag with gypsum sludge 2 Experimental 21 Materials and reagents In this study, high lead slag as the experimentalUtilization and detoxification of gypsum sludge by replacing limestone 2021年3月26日 The slag generated by the steel plant has been utilized to produce submerged arc welding flux The flux produced by recycling steel slag has been applied in the submerged arc welding process The effects of recycled slag on the chemical composition, microhardness, and microstructure of weld metal have been evaluated For chemical composition, weld pads were Recycling of steel slag as a flux for submerged arc welding and its
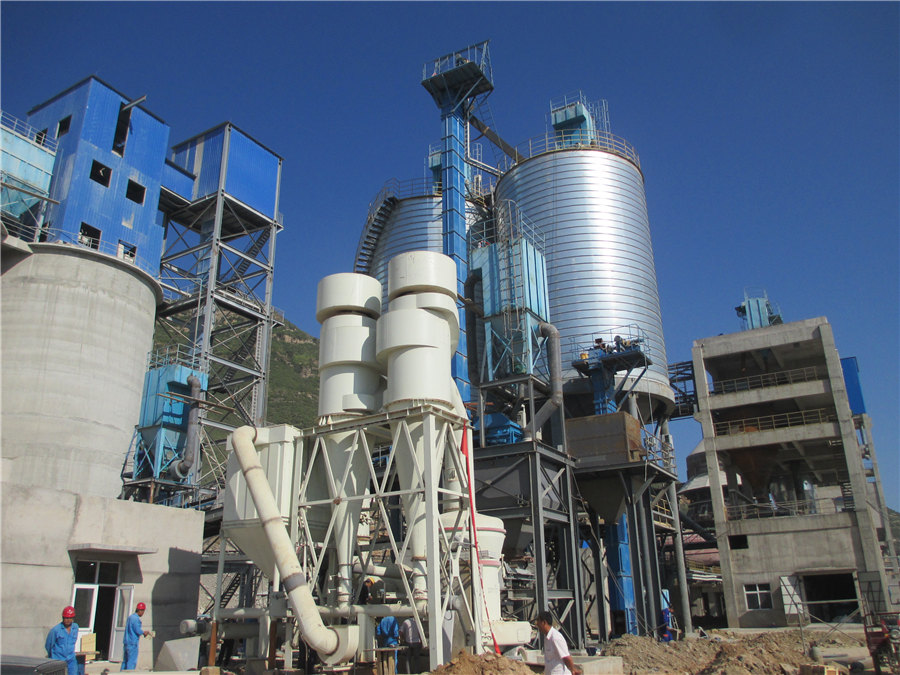
Recovery of Copper from Copper Smelting Slag Using a Green
2020年1月24日 Materials The sample was obtained from slag that was generated during the oxygen enrichment copper smelting process The chemical composition shown in Table 1 indicates that the Cu content was 1782% and the Fe 3 O 4 content was 129% Due to the fact that the copper slag was produced by the oxygen enrichment process, the copper and Fe 3 O Herein we characterize the mineralogy, chemical composition, and environmental geochemistry of slag formed by historic (1880s to circa 1910) smelting of the copperrich lodes of Butte, Montana The aircooled slag exists as monolithic “walls” that border Silver Bow Creek, the headwaters of the upper Clark Fork River Superfund siteMineralogy and environmental geochemistry of copper slag from 2017年10月15日 1 Introduction Based on the research conducted on the possible application and utilization for the copper slag incurred worldwide, the settingup of Database of Mansfelds copper slag was initiated and featured its diverse profile (Zobel, 2016)The interesting investigation of the using of copper slag (144%) together with WIPfly ash from waste New residuefree processing of copper slag from smelterDespite this, many smelting enterprises possess limited recycling and treatment capabilities For instance, a domestic copper refining enterprise generates hundreds of tons of copper slag annually, yet only a minimal amount can be sold to cement plants at a low price of 30 yuan per ton, exacerbated by the high treatment costs, so smelting enterprises mostly choose to pile up Resource utilization strategy of Febearing smelting slag in China:
.jpg)
Steel Slag Recycling: The Definitive Processing Solution
2024年3月12日 Unlock the potential of steel slag with efficient recycling and processing methods, After the initial crushing by a jaw crusher, the steel slag is reduced to a size smaller than 60 mm replacing traditional limestone to improve smelting efficiency and recover a large amount of metal iron and other useful elements2024年2月7日 Reduction The reduction process for copper slag is typically followed by magnetic separation []Depending on the temperature and intensity of reduction, it can be classified as direct reduction, deep reduction, and smelting reduction []Commonly used reducing agents include coke, biomass carbon, and natural gas [31, 32]The reduction process converts Resource Utilization of Copper Slag with a Focus on Springer2019年4月9日 crusher, then the iron nugget and alumina slag were magnetically separated by the high strength roller dry magnetic separator (LONGi, Zhengzhou, China) with a magnet ic intensity of 4000 GsSemiSmelting Reduction and Magnetic Separation 2024年10月1日 The efficient and selective recovery of Li from lithiumcontaining smelting slag is crucial for the shortprocess recycling of SLIBs [30]Dang [31] achieved outstanding selectivity for lithium with a recovery rate of 9387 % by employing a mixture of K 2 CO 3 and Na 2 CO 3 for roasting with lithiumcontaining simulated slag (CaOAl 2 O 3SiO 2) Selective extraction of Li and Mn from spent lithiumion battery
.jpg)
Extraction and separation of copper and iron from copper smelting slag
2022年9月25日 It is generally considered that the smelting slag with an iron content of about 30%–45% and copper content of less additive limestone 10%, soda ash 15% and binder 5%), and iron concentrate with an iron content of 926% and Cleaner recycling of iron from waste copper slag by using walnut shell char as green 2024年8月15日 Copper smelting slag (CSS) is commonly generated during the smelting process of the copper concentrate, it comprises a range of valuable metals, especially the valuable copper (Cu), possessing the greatest recovery value Currently, direct flotation is commonly used to recover Cu from CSS, but the Cu recovery rate is usually below 90%Efficient recovery of copper from copper smelting slag by gravity Limestone is a sedimentary rock composed primarily of calcium carbonate (CaCO3) and is widely used in various industries, such as mining industry, metallurgy industry, and construction industryMore and more customers are paying attention to this industry and invest into limestone crushers and have made great achievementsLimestone Crusher Machine: Boost Quarrying Mining Operations2020年11月1日 Controlling the slag basicity in smelting with nickel laterite using an ACarc furnace in RKEF also can reduce energy consumption by promoting the formation of low melting point phases, such as Control of slag formation in the electric furnace smelting of
.jpg)
Smelting Reduction: Most Efficient Technologies for Greenhouse
2019年7月19日 Here, the smelting offgases are employed for the prereduction stage Those processes without a prereduction step such as HIsmelt ® Smelting acts in a single operation in a reactor where iron ores and coal are mixed In both the solution, large attention is avoided to the control of the offgas which results richer of CO 2 with respect to 2020年11月16日 Metals smeltingcollection method for recycling of platinum group metals from waste catalysts: A mini review November 2020 Waste Management Research 39(1):XMetals smeltingcollection method for recycling of platinum Didn’t find what you are looking for? Feel free to get in touch with us Just call +903123979133 and we will help you in any way we can You can also send an email to [ protected], or fill in the inquiry form if you would like to pass us a detailed inquiry or project informationUse the Call Back option if you would like to be contacted by our sales teamSlag Recycling and Metal Recovery MEKA2020年7月10日 On the basis of the above laboratorial experiments of reduction smelting and vacuum metallurgy, scaleup experiments were carried out 45 kg Kaldo smelting slag of copper anode slime was first treated by reduction smelting to form Pb–Bi–Ag alloy for 40min under 1350 °C with the addition of 10 wt% coke, 20 wt% limestone and 26 wt%iron powder, and then the A novel process for silver enrichment from Kaldo smelting slag
2FD{P}PC]854]XQ.jpg)
Slag Wikipedia
Molten slag is carried outside and poured into a dump The general term slag may be a byproduct or coproduct of smelting (pyrometallurgical) ores and recycled metals depending on the type of material being produced [1] Slag is mainly a 2011年7月1日 Table 1 Results of allocation factor Process Coproduct Allocation factor Coking Coke 0 78 Coke oven gas 0 22 Chemicals 0001 BF smelting Liquid iron 0 98 BF gas 0 02 BOF smelting Idquid steel 0 99 ROF gas 0 01 Steel slag recycling Waste iron 0 52 Steel slag after recycling iron 0 48 * 36 * Journal of Iron and Steel Research, International Vol 18 I I Life Cycle Assessment of Internal Recycling Options of Steel Slag 2019年4月9日 This work presents a semismelting reduction and magnetic separation process for the recovery of iron and alumina slag from iron rich bauxite ore The effect of the process parameters on the recovery rate of iron, maximum particle size of the iron nugget, and the Al2O3 content of the alumina slag was investigated and optimized The results show that the iron SemiSmelting Reduction and Magnetic Separation for the 2024年6月12日 1 INTRODUCTION Blast furnace slag (BFS) and steel slag (SS), as industrial solid wastes produced in the process of steelmaking, account for 80%–90% of the total smelting slag [] BFS accounts for about 30% of pig iron output, [] while SS accounts for 10%–15% of the crude steel output [] SS comprises various slags, including basic oxygen furnace slag (BOFS) Recycling of iron and steel slag for carbon reduction and low
.jpg)
The Recovery of Copper from Smelting Slag by Flotation Process
Taking into account that the slag contained more copper than ore, a series of flotation tests was conducted on copper smelting slag produced in an electric furnace of a copper plant in China Based on the mineralogical analyses of slag, the tested copper smelting slag was composed of fine particles with complex associaDownload: Download highres image (555KB) Download: Download fullsize image Fig 1 China's ISW annual growth, publication, hazards of CSS, and the value and stockpile of CSS (a) Annual growth of ISW in China; (b) publication of all kinds of ISW, “FA” means that the fly ash, “CG” means that the coal gangue, “FS” means that the furnace slag, “RM” means that the red mud, Practical experience to theoretical innovation: A model for 2021年3月1日 In our previous study, smelting slag contained appropriate 20–30 wt% liquid compositions at 800–1000°C and 70–80 wt% at 1200°C (Ding et al, 2020) The formation of liquid slag can significantly facilitate the sintering of green body, further improving the mechanical properties of productsHighly porous ceramics production using slags from smelting 2018年1月11日 The submerged electric arc furnace (SAF) has proven a versatile unit in numerous metallurgical applications for more than a century Countless innovations have made this furnace type become the most commonly used furnace for increased metal recoveries and slagcleaning operations In many applications, SAFs are also employed as primary melting The Submerged Arc Furnace (SAF): StateoftheArt Metal
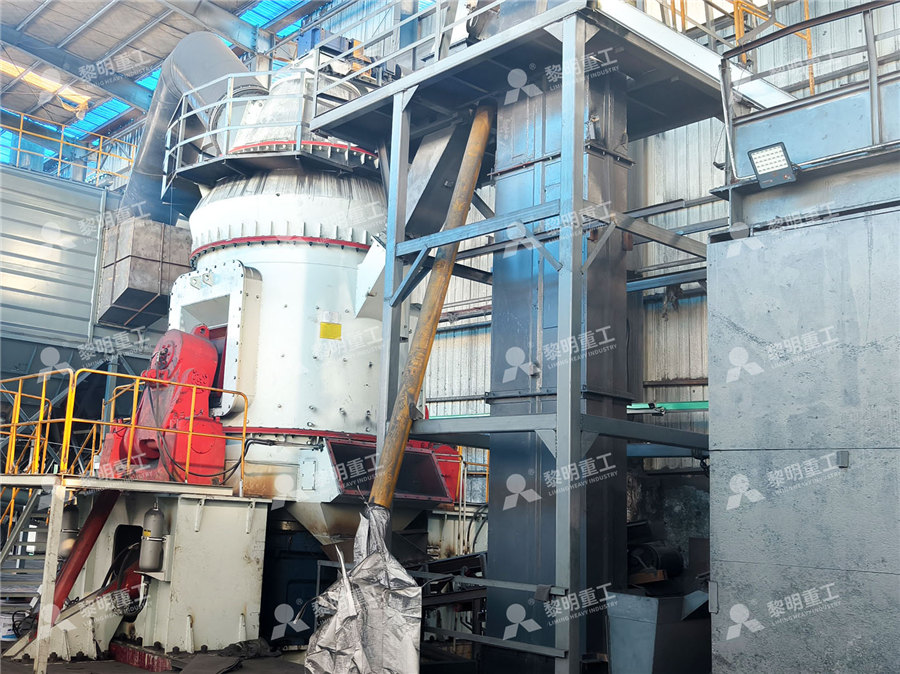
A Study on Reduction of Copper Smelting Slag by Carbon for Recycling
2020年1月17日 Copper smelting slag is a solution of molten oxides created during the copper smelting and refining process, and about 15 million tons of copper slag are generated annually in Korea The oxides in copper smelting slag include ferrous (FeO), ferric oxide (Fe2O3), silica (SiO2 from flux), alumina (AI2O3), calcia (CaO) and magnesia (MgO) The main oxides in copper