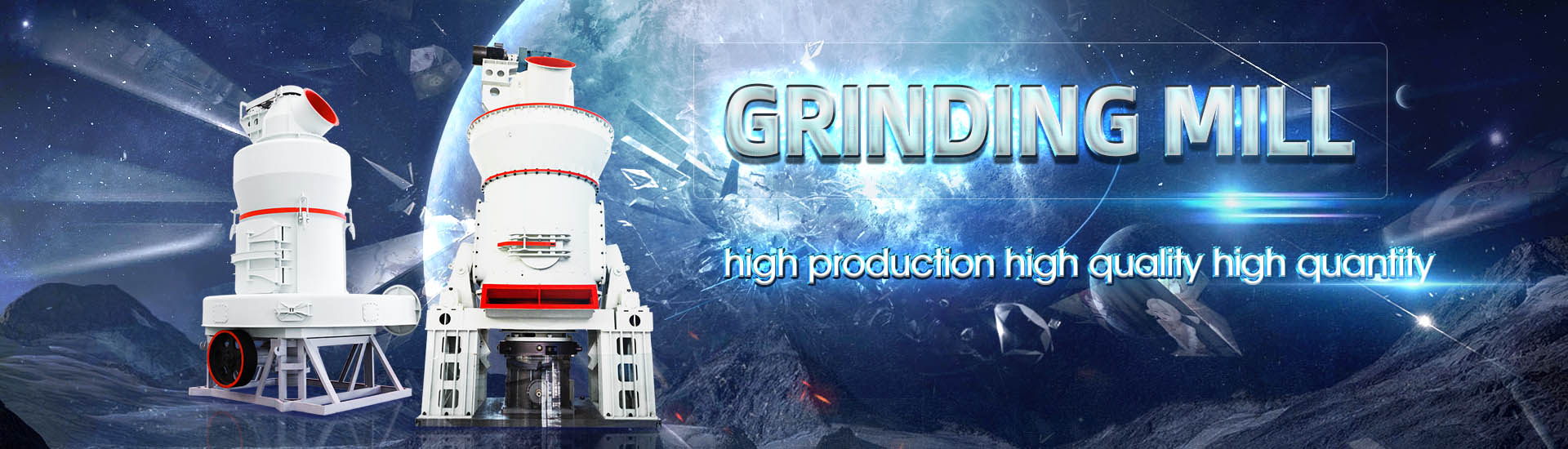
Oxygen Iron to steel ratio
.jpg)
233: Metallurgy of Iron and Steel Chemistry LibreTexts
Steel is made from iron by removing impurities and adding substances such as manganese, chromium, nickel, tungsten, molybdenum, and vanadium to produce alloys with properties that make the material suitable for specific uses Most 2020年2月28日 Mass balances provide a fundamental approach for analysing the oxygen steelmaking process Steelmaking plants commonly have inhouse mass balance models for controlling process parametersGeneral mass balance for oxygen steelmaking2020年12月6日 The study highlights the importance of scrap to hot metal ratio on optimizing the oxygen steelmaking process in terms of global warming potential or CO2 generated, O2 supply, mass of flux,Application of mass and energy balance in oxygen 2022年5月31日 The steelmaking process is an energyintensive multistage process, and the step involving the conversion of molten iron to steel, commonly performed in a basic oxygen Metals Special Issue : Oxygen Steelmaking Process MDPI
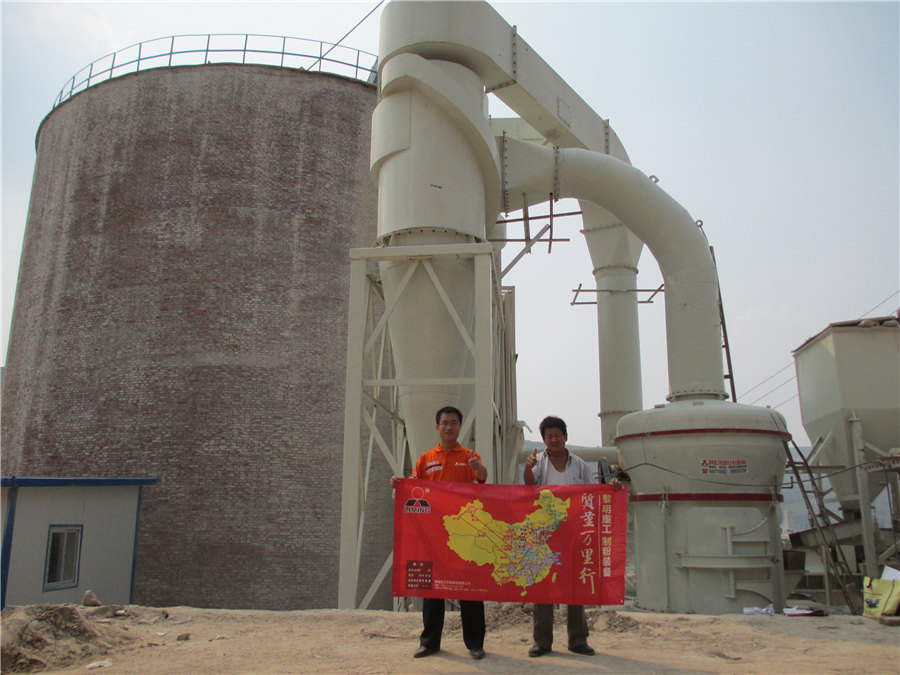
General heat balance for oxygen steelmaking Journal of Iron and
2020年10月12日 To produce steel, carbon and other impurities are released from liquid iron at high temperatures via oxygen blowing or by electric arc technique In oxygen steelmaking, the 2019年7月19日 The basic process of converter is to reduce the carbon content of iron produced in the blast furnace in order to obtain lowcarbon steel This operation is universally known as Basic Oxygen Furnace: Most Efficient Technologies for Greenhouse In this paper, a model based on static mass and energy balance is used to analyze the excess heat generated during the steelmaking process The overall balance is conducted by Analysis of Heat Loss in Oxygen Steelmaking2021年4月21日 Blast furnacebasic oxygen furnace (BFBOF): This is the dominant steel production route in the iron and steel industry, involving the reduction of iron ore to pig iron in Lowcarbon production of iron and steel: Technology options,
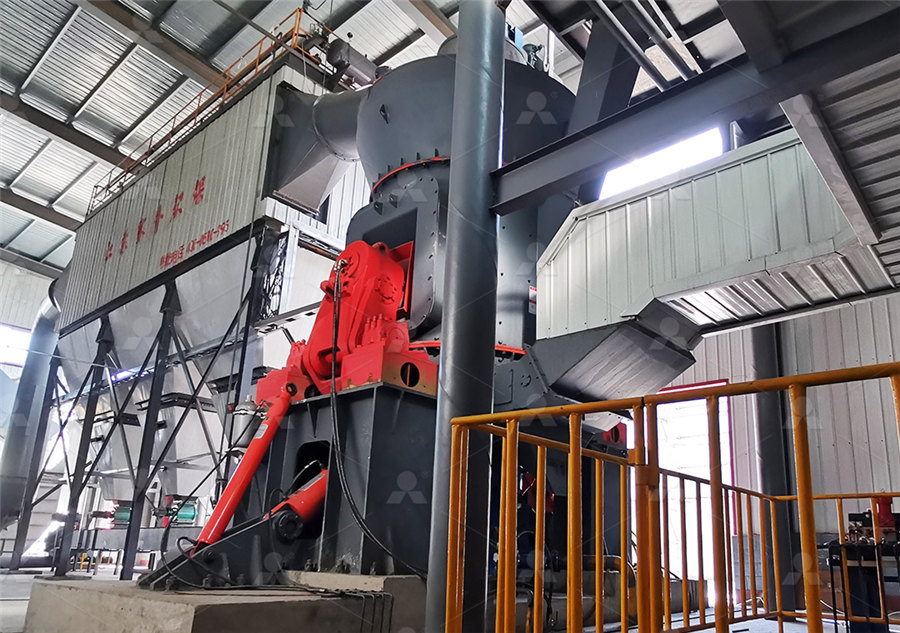
Oxygen and Steels IspatGuru
2015年1月13日 There is a very strong relationship between oxygen and steel Oxygen is first used in the steel making process which is a controlled is based on the principle that the iron pipe burns at approximately 1200 deg C to 2700 2021年1月27日 Im not really sure where to look for these numbers but it seems like iron smelting uses 1 iron ore to produce 1 iron plate steel smelting uses 5 iron plate to produce 1 steel plate Sooo if I want balanced steel smelting I basically need a 5:1 ratio of iron smelting to support it? Have I got this right? Here's a shot of my current setup (Im definitely a factorio Optimal ratio of iron to steel smelters? Steam Community2020年10月12日 To produce steel, carbon and other impurities are released from liquid iron at high temperatures via oxygen blowing or by electric arc technique In oxygen steelmaking, the energy from the reactions is utilized for heating pig iron at 1350 °C to liquid steel at 1600 to 1700 °C, flux dissolution and scrap meltingGeneral heat balance for oxygen steelmaking Journal of Iron and Steel 2024年8月5日 For instance, you must put in 12 iron and 4 coal to make 16 steel You cannot put in 12 iron and 7 coal 327% Oxygen, and 637% Volatiles, and the Volatile to Oxygen ratio will be 195:1 instead of 2:1, but it will burn adequately well The gas should be pumped into the furnace and ignited; Furnace Unofficial Stationeers Wiki
.jpg)
Altered chemistry of oxygen and iron under deep Earth
2019年1月11日 Oxygen and iron are Earth’s most abundant elements by number of atoms and by mass, respectively They form compounds dictating major chemistry of our planet 1It is conventionally accepted that According to Qi et al, the reduction ratios of iron and chromium in the stainless steel slag (SSS) improved on increasing the carbon equivalent added, reduction temperature, and basicity The highest reduction ratio of Fe and Cr achieved was 9392% and 7276%, respectively, under the condition of carbon equivalent 2, reduction temperature 1600 ºC, and binary basicity 12Basic Oxygen Steelmaking Slag: Formation, Reaction, and Energy 2018年6月21日 After the pig iron has been tapped, it must be desulfurized and oxidized with oxygen (refining) to obtain crude steel Introduction Due to its high carbon content and relatively high concentrations of phosphorus and sulphur, pig iron is generally very brittle and is not suitable for forging or weldingFrom pig iron to crude steel tecscienceSteel mill with two arc furnaces Steelmaking is the process of producing steel from iron ore and/or scrapIn steelmaking, impurities such as nitrogen, silicon, phosphorus, sulfur, and excess carbon (the most important impurity) are removed from the sourced iron, and alloying elements such as manganese, nickel, chromium, carbon, and vanadium are added to produce different Steelmaking Wikipedia
.jpg)
Metals Special Issue : Oxygen Steelmaking Process MDPI
2022年5月31日 In this work, multiple interconnected equilibrium/adiabatic stoichiometricreactorbased approaches are used to describe the overall basic oxygen steelmaking process The macroprogramming facility of FactSage™ software was used to understand the thermodynamics and kinetics of basic oxygen steelmaking processes2022年2月2日 The steelmaking process is an energyintensive multistage process, and the step involving the conversion of molten iron to steel, commonly performed in a basic oxygen furnace (BOF), makes an important contribution to greenhouse gas generation The effective utilization of energy is one of the major challenges in the process, as minor variations of operational Contribution of CO 2 Emissions from Basic Oxygen Steelmaking 2015年3月2日 The BOF process is autogenous, or self sufficient in energy, converts liquid iron (hot metal) into steel using gaseous oxygen (O2) to oxidize the unwanted impurities in hot metal (HM) The O2 used must be of high Understanding Steel Making Operations in Basic 2024年3月20日 The steel making process involves several key stages: preparation of raw materials such as iron ore, coke, and limestone; smelting and reduction to produce molten iron; primary steelmaking which converts molten Understanding the Steel Making Process: A Flow
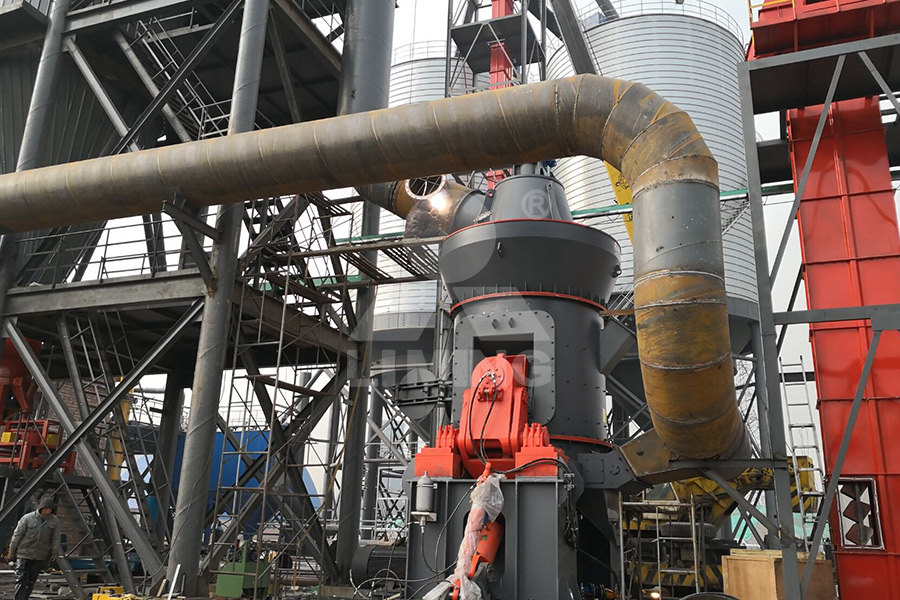
Application of mass and energy balance in oxygen
2020年12月6日 The steelmaking process is an energyintensive multistage process, and the step involving the conversion of molten iron to steel, commonly performed in a basic oxygen furnace (BOF), makes an 2023年5月1日 Energy saving and emissions reduction in the iron and steel industry is a significant challenge to achieve carbon neutrality and sustainable development Many studies focus on the optimization of materials, energy and carbon emissions but lack of optimization strategies in the iron and steel industry A comprehensive and effective system model is still LowCarbon Manufacturing and Optimization Strategies of Iron and Steel 2020年2月28日 The calculations are carried out until the iteration loop is converged to balance the mass input (hot metal, scrap, flux + coolant, oxygen, refractory) to the mass of the product (liquid steel General mass balance for oxygen steelmaking ResearchGate2017年3月22日 Lower oxygen activities in the steel enhance steel desulphurisation After deoxidation (with Al) the oxygen activity is around 2–4 ppm, which is comparable to that of HM The steel temperature (∼1600°C) is higher than that of HM (∼1300°C) This means that magnesium is no longer an option as a reagent due to its high vapour pressureSulphur removal in ironmaking and oxygen steelmaking
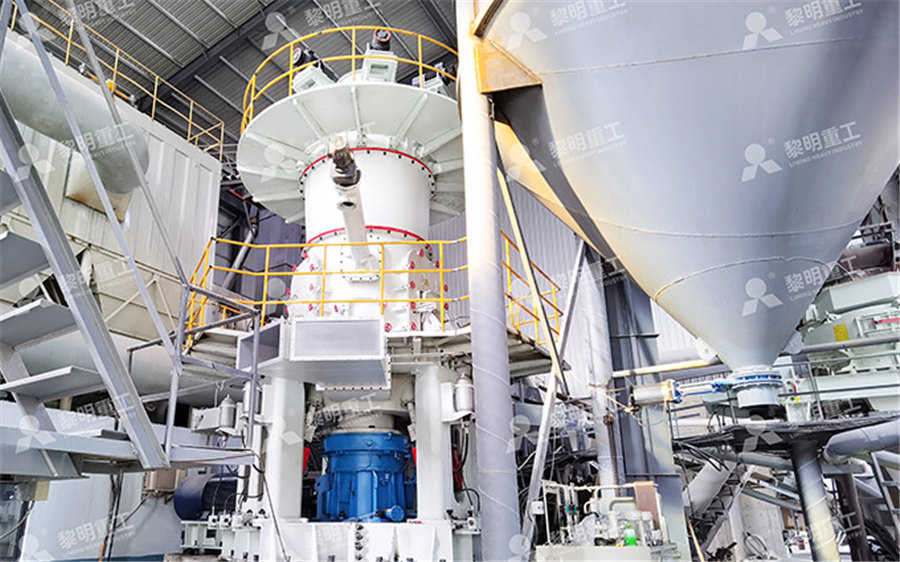
Basic Oxygen Steelmaking Slag: Formation, Reaction, and Energy
2021年8月10日 According to Qi et al, the reduction ratios of iron and chromium in the stainless steel slag (SSS) improved on increasing the carbon equivalent added, reduction temperature, and basicity The highest reduction ratio of Fe and Cr achieved was 9392% and 7276%, respectively, under the condition of carbon equivalent 2, reduction temperature 1600 ºC, and binary basicity This initially will produce 97 kg of liquid iron and 3 kg of SiO2 To balance the V ratio* at 20 requires the addition of 6 kg of CaO and 2 kg of MgO to protect dissolved oxygen in the steel, and FeO in the slag This balance is driven by thermodynamics and the stirring conditions in the furnace (kinetics), as shown in Figure 1, which was Maximizing Iron Unit Yield from Ore to Liquid Steel (Part 3 2024年10月1日 Currently, the iron and steel industry is responsible for 7% of global CO2 emissions In this review, we summarize the operational principles of current emissionsintensive steelmaking Chemical and electrochemical pathways to lowcarbon iron and steel 2022年3月8日 China's crude steel output has grown rapidly since 1990, accounting for more than half of worldwide production in 2019 Iron and steel industry (ISI) in China's energy consumption and carbon emissions accounted for a higher proportion In the context of China's "carbon peak, carbon neutrality", the ISI attaches great importance to energy conservation and Analysis of iron and steel production paths on the energy
.jpg)
IRON AND STEEL chemguide
Types of iron and steel Cast iron has already been mentioned above This section deals with the types of iron and steel which are produced as a result of the steelmaking process Wrought iron If all the carbon is removed from the the iron loss The iron in the blow 1 slag is discharged outside unless it can be recovered by magnetic separation Figure 10 shows the relationship between the amount of iron ore charged in the blow 1 and the total iron (TFe) content of the turndown slag As the amount of the iron ore charged in the blow 1Development to Minimize Iron Loss at Oita Works Nippon Steel 2024年10月3日 The rusting of iron, a process where iron reacts with water and oxygen to form iron oxide, weakens the metal over time, causing it to deteriorate The most familiar form of rust is the reddish coating that forms flakes on iron and steel (Fe 2 O 3), but rusting also happens in other colors including yellow, brown, orange, The Chemical Reaction That Causes Rust ThoughtCoSteelmaking slag, or steel slag, is a byproduct from the production of steel during the conversion of hot metal to crude steel in a basic oxygen furnace, or during the melting of scrap in an EAFThe slag is generated as a melt and is a complex solution of silicates and oxides that solidify upon cooling 11 Depending on the specific steel production process, three different types of steel Steelmaking Slag an overview ScienceDirect Topics
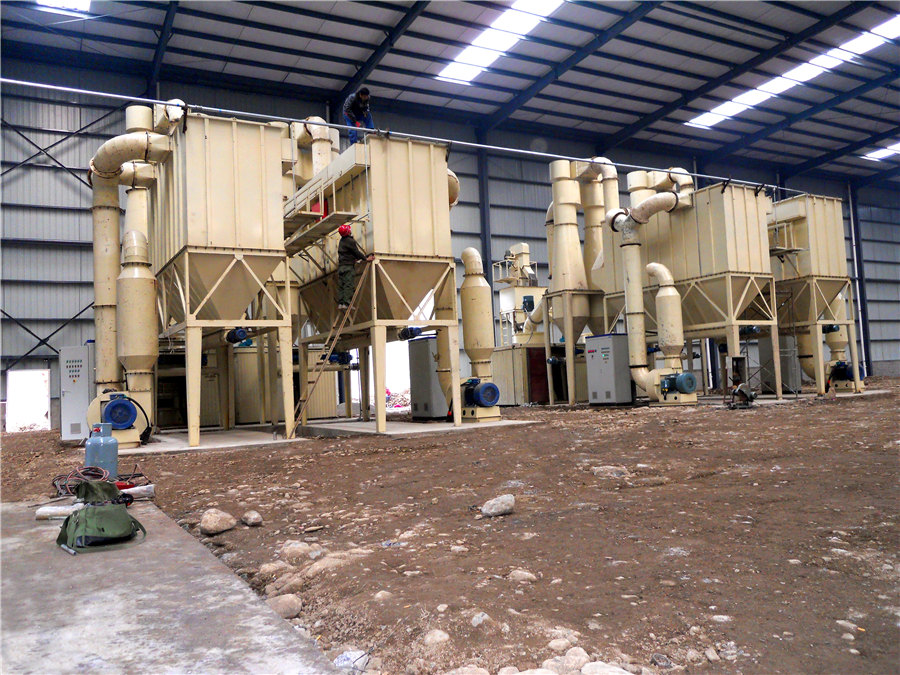
ACP Towards a sectorspecific CO∕CO2 emission ratio: satellite
Abstract Global crude steel production is expected to continue to increase in the coming decades to meet the demands of the growing world population Currently, the dominant steelmaking technology worldwide is the conventional highly CO2intensive blast furnace–basic oxygen furnace production route (also known as the Linz–Donawitz process), which uses iron ore as 2024年11月19日 Steel Basic Oxygen, Refining, Alloying: More than half the world’s steel is produced in the basic oxygen process (BOP), which uses pure oxygen to convert a charge of liquid blastfurnace iron and scrap into steel The basic oxygen furnace (BOF) is a refractorylined, tiltable converter into which a vertically movable, watercooled lance is inserted to blow oxygen Steel Basic Oxygen, Refining, Alloying BritannicaIf you're going to make steel, you need iron and coal in a 3:1 ratio (Iron:Coal) So, 150 iron and 50 coal will net you 200 steel So you put the ore in and the door will open back up when it's done processing the item you put in there If you hold your cursor over the window on the front, it will give you some nice infoA beginners guide to making Steel :: Stationeers General Discussions2008年12月12日 Flame cutting employs a central jet of oxygen surrounded by a ring of oxygen/fuel gas jets which provide the flame The flame preheats the mild steel to a temperature (approximately 1200 K[3, 4 (PDF) Laseroxygen cutting of mild steel: The ResearchGate
.jpg)
Iron Oxygen Not Included Wiki
Usage [] Iron is a main material in Steel production in Metal Refinery 70 kg Iron + 20 kg Refined Carbon + 10 kg Lime = 100 kg Steel It requires Duplicants operation As a Refined Metal, Iron can be used to build advanced Power systems, buildings, and Automation systems Exosuit Forge can produce Atmo Suit with Iron 300 kg Aluminum or Copper or Iron + 2 unit Reed Rust is an iron oxide, a usually reddishbrown oxide formed by the reaction of iron and oxygen in the catalytic presence of water or air moistureRust consists of hydrous iron(III) oxides (Fe 2 O 3 nH 2 O) and iron(III) oxidehydroxide Rust Wikipedia40 knowledge speci”c for steel manufacturing, from bigpicture concepts to speci”c processes 42 Digital Transformations APR 2022 cycle, more than 100 m I IRON STEEL TECHNOLOGY ratio in the input feed These are I Analysis of Heat Loss in Oxygen Steelmaking Steelmaking is an energyintensive process and about 20–40% of theAnalysis of Heat Loss in Oxygen Steelmaking2024年1月12日 A slightly oxidizing flame is used in torch brazing of steel and cast iron A stronger oxidizing flame is used in the welding of brass or bronze shown in figure 113 The flame remains neutral up to about 25:1 oxygentofuel ratio Increasing the oxygen flame produces a lighter blue flame, a longer inner cone, and a louder Welding Flames: Neutral, Carburizing Oxidizing Weld Guru
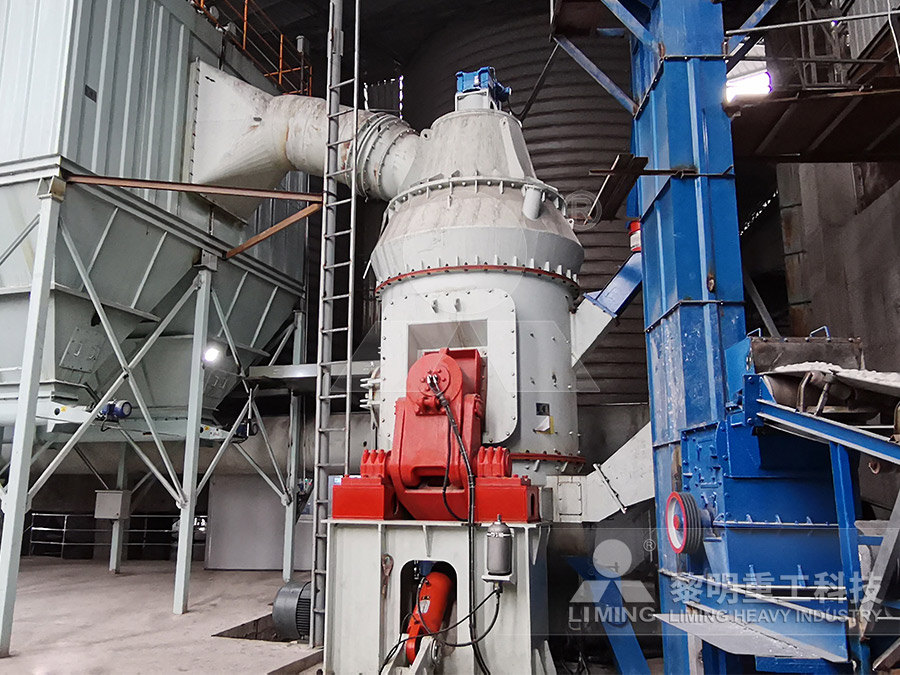
The Basic Oxygen Furnace to Obtain Steel SpringerLink
2021年3月25日 It is used as raw material in the Basic Oxygen Furnace (BOF) to produce steel and in the cupola furnace to produce cast irons This chapter is dedicated to the production of steel in the Basic Oxygen Furnace The technological development is presented as well as the main reactions involved in the treatment of the pig iron in the converterBasic Oxygen Steelmaking Slag: Formation, Reaction, and Energy and Material Recovery Zushu Li,* Juncheng Li, Stephen Spooner, and Sridhar Seetharaman 1 Introduction The basic oxygen steelmaking (BOS) process produced over 70% of the global crude steel in 2018,[1] generating 100 to 150kg of slag (“BOS slag”) for every tonne of crude steel Basic Oxygen Steelmaking Slag: Formation, Reaction, and 2014年1月1日 The oxidation zones in topblown oxygen converter can be divided in three main regions: (1) “hot spot” where oxygen jet impinges on the iron melt surface, (2) slag and emulsion/foam in which liquid iron droplets ejected from the iron melt surface are recycled, and (3) zones inside the iron melt, where the flow of iron melt from the hot spot area with high oxygen Converter Steelmaking ScienceDirect2020年3月3日 Height (H) to diameter (D) ratio varies from 106 to 185; 15 is most preferred ratio The process was developed by the Maximillianshutte Iron and steel Company, Carbon in the metal is oxidized by dissolved oxygen or iron oxides in the slag depending upon the dissolved oxygen contentOxygen Steelmaking Processes SpringerLink
.jpg)
A Visual Guide: Steel Making Process Chart Cabaro Group
2024年3月17日 Basic Oxygen Furnace (BOF) Converting: This critical step involves blowing oxygen into molten iron to reduce carbon content and remove impurities, transitioning from iron to steel Ladle Metallurgy : This is an intermediary stage where the composition of the molten steel is adjusted and finetuned to specific customer requirements2023年6月21日 To avoid the volume expansion of basic oxygen furnace (BOF) slag for use in building materials, a hot slag modification process was proposed to reduce free CaO (fCaO) in the molten slag A transient 3D numerical model of BOF molten slag modification by SiO2 particles was established The flow and heat transfer of molten slag, movement and Numerical investigation of basic oxygen furnace slag Springer