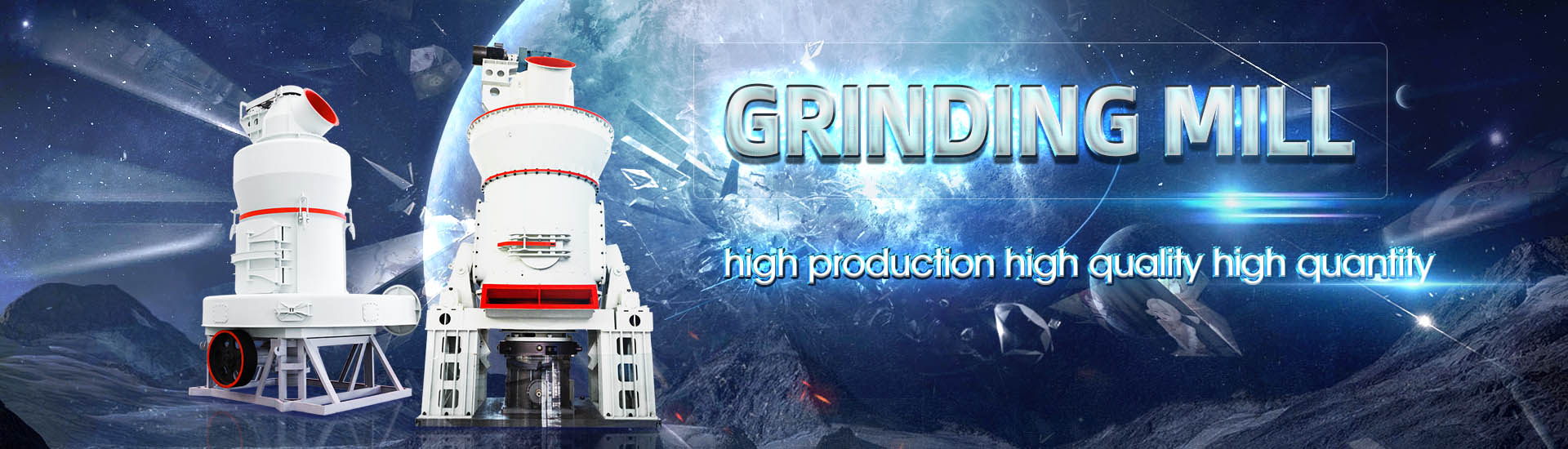
Where can I find powder metallurgy injection molding processing in Wuhan
.jpg)
Process Parameters Used in Macro/Micro Powder Injection
2020年6月3日 Micropowder injection molding (µPIM) for the production of microparts is a modification of the PIM process, and it can be categorized as micrometal injection molding 2013年1月1日 This chapter provides a detailed overview of MIM and includes descriptions of the principles of the process such as powders, binders, mixing and feedstock analysis, injection Developments in metal injection moulding (MIM) ScienceDirect2012年7月20日 The powder injection molding (PIM) process offers a fabrication technology for making parts by metal powder injection molding (MIM) and/or ceramic powder injection Powder Injection Molding Piotter Wiley Online LibraryPowder injection molding (abbreviated PIM) is a variant of plastic injection molding used to produce parts made of metal (MIM = metal injection molding) or made of ceramics (CIM = Metal and ceramic powder injection molding WITTMANN Group
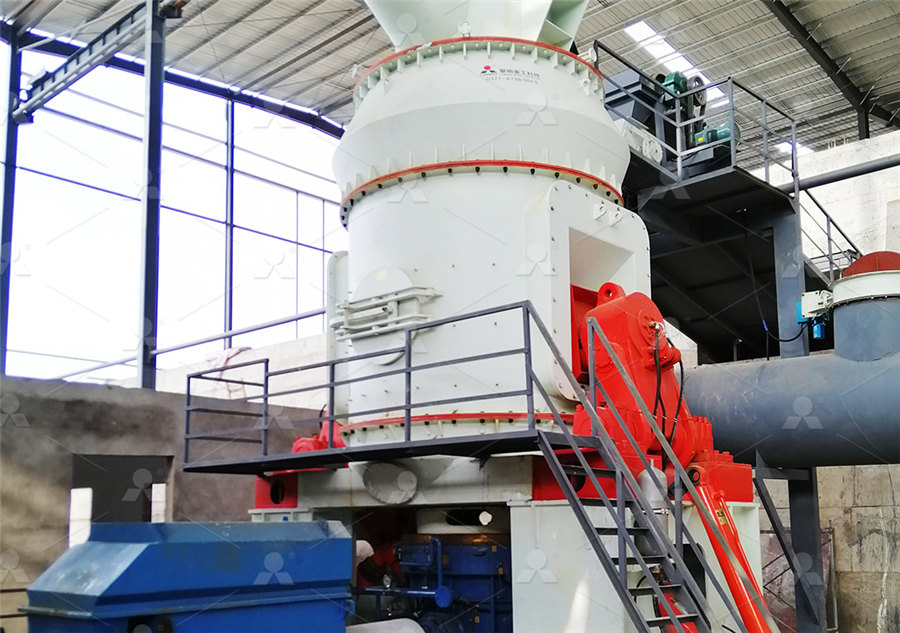
Metal Injection Moulding (MIM) EPMA Association
Metal injection moulding (MIM) is a development of the traditional powder metallurgy (PM) process and is rightly regarded as a branch of that technology The standard PM process that 2024年1月19日 Powder injection molding is a powder metallurgy near net shape forming technology developed by combining modern polymer injection molding and powder metallurgy Powder Injection Molding SpringerLink2015年1月1日 Powder Injection Moulding (shortly PIM) enables a highvolume production of completely metal or ceramic complex geometry parts starting from noncompletely metallic and ceramic materials Powder injection moulding technology: Properties, Powder injection molding (PIM) is a technology for manufacturing complex, precision, netshape components from either metal or ceramic powder The potential of PIM lies in its ability to Powder Injection Molding of Metal and Ceramic Parts IntechOpen
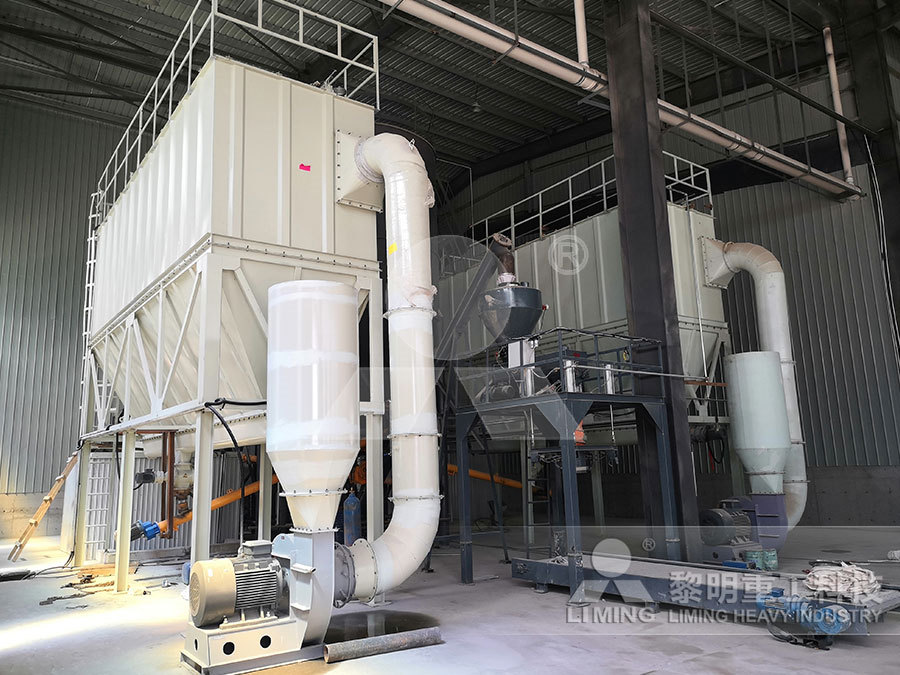
Introduction to Metal Powder Injection Molding Powder Metallurgy
Manufacturing defects, Molds and molding equipment, Reciprocatingscrew injection molding machine, Mechanical and machine components, Powder metal alloys, Heattreating furnaces, Liquidphase sintering, Solidstate sintering, Metal injection molding, Full density consolidation, Sintering, Processing, treatment, and fabricationThis is required to pack the plastic melt The injection molding process normally operates at pressures up to 200 MPa The “high pressure” injection molding machines, operating at 500 MPa, are currently under investigation Injection Injection Molding: Definition, Types Processing JN Sinter Metals Co, Ltd, (Hangzhou Eastern Magnetic Industry Co, Ltd ) is a professional China Injection Molding Powder Metallurgy CopperBased Parts Suppliers and Injection Molding Powder Metallurgy CopperBased Parts Injection Molding Powder Metallurgy Copper An obvious strength of SDS is its similarity to powder injection molding (PIM), either metal (powder) injection molding (MIM) or ceramic (powder) injection molding (CIM) PIM has been in use since the 1970s to produce complex geometries by the appropriate combination of polymer injection molding and of powder metallurgyPolymer Injection Molding an overview ScienceDirect Topics
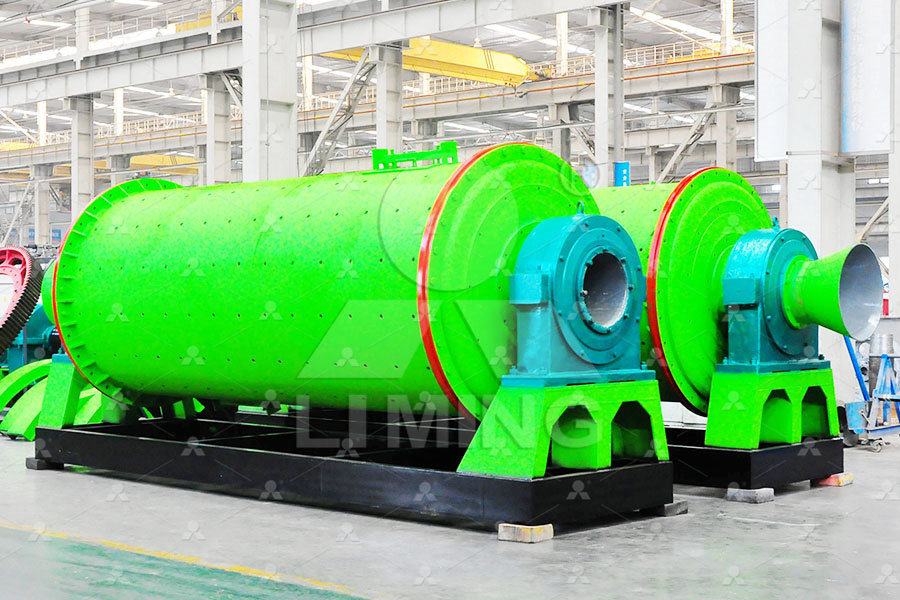
Powder Injection Molding China Metal Injection Molding
2017年9月8日 Powder Injection Molding (PIM), including Metal Injection Molding (MIM) and Ceramic Injection Molding (CIM), is an advanced forming technique for producing shaped components from powders, in high volume This process uses injection molding technology to produce small, high volume and complex parts to tight tolerances The best applications are 2013年8月1日 Powder metallurgy (PM) is a popular metal forming technology used to produce dense and precision components Different powder and component forming routes can be used to create an end product with Advances in powder metallurgy: Properties, processing and applications Get a detailed comparison of powder metallurgy vs metal injection molding, exploring their key differences and benefits 2037437502 World Class Manufacturer of Small Intricate Powdered Metal All parts undergo processing in a climatecontrolled environment and are subjected to a rigorous quality assurance system to ensure the Powder Metallurgy vs Metal Injection Molding2022年11月25日 Powder Injection Moulding In Powder injection moulding, the manufacturer blends fine powder particles with polymer or waxbased binder before injecting the mix into a mould to create a green part This then goes through the sintering process This mixture is then injected into a mould at an elevated temperature Powder injection moulding (PIM What is Powder metallurgy Powder metallurgy types
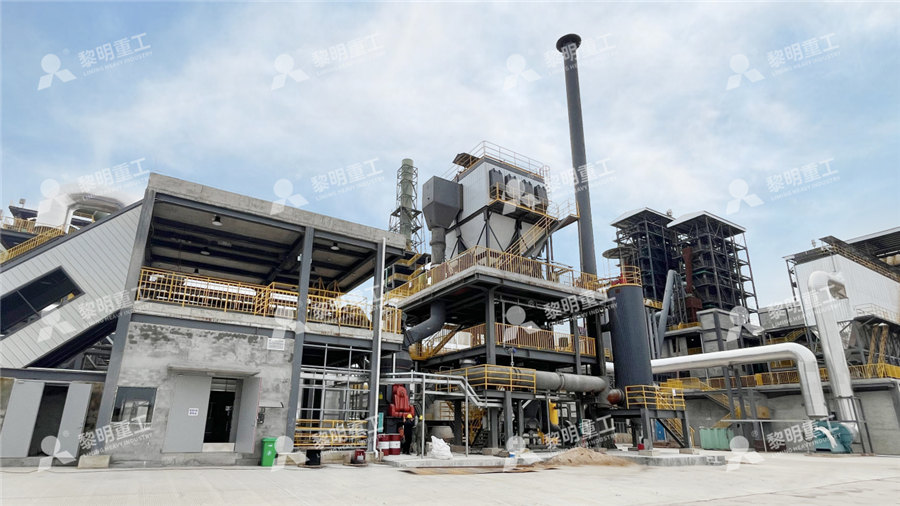
Powder Injection Molding Piotter Wiley Online Library
2012年7月20日 The powder injection molding (PIM) process offers a fabrication technology for making parts by metal powder injection molding (MIM) and/or ceramic powder injection molding (CIM) It consists of four main steps: mixing of feedstock, shaping by Metal Injection Molding (MIM) and Powder Metallurgy (PM) have gained significant importance in modern manufacturing, particularly for components requiring high precision and complex geometries MIM combines the benefits of powder metallurgy and plastic injection molding, while PM relies on compaction and sintering processesMetal Injection Molding vs Powder Metallurgy Becu2024年11月9日 The control of oxygen is paramount in achieving highperformance titanium (Ti) parts by powder metallurgy such as metal injection molding (MIM) In this study, we purposely selected the Ti and Ti–6Al–4V powders as the reference materials since these two are the most representative Ti materials in the industry Herein, hydride–dehydride (HDH) Ti powders were Oxygen variation in titanium powder and metal injection moldingPowder metallurgy – science of producing metal powders and making finished /semifinished objects from mixed or alloyed powders with or without the addition of nonmetallic constituents Steps in powder metallurgy:Powder production, Compaction, Sintering, Secondary operations Powder production: Raw materials => Powder; Powders can be pure Powder metallurgy – basics applications IIT Guwahati
.jpg)
Powder Metallurgy vs Metal Injection Molding (MIM)
2024年7月17日 Powder Metallurgy (PM) and Metal Injection Molding (MIM) are both effective methods for manufacturing metal parts, each with its unique advantages PM is suitable for producing small to mediumsized parts with good mechanical properties and lower tooling costs It is commonly used in automotive, aerospace, and consumer products2023年12月3日 Metal injection molding (MIM) offers numerous advantages in the manufacturing industry, providing complex shapes and high production rates When combined with powder metallurgy, MIM becomes even more efficient and effective In this article, we will explore seven essential tips for achieving successful metal injection molding with powder metallurgy7 Tips for Metal Injection Molding With Powder Metallurgy2006年5月1日 Request PDF Development of niobium powder injection molding: Part I Feedstock and injection molding It has been only during the past four decades that niobium has been consumed on an Development of niobium powder injection molding: Part I2023年12月3日 The design flexibility of powder metallurgy in metal injection molding allows for the creation of intricate and complex metal parts with a high degree of precision and efficiency This flexibility is achieved through the powderbased nature of the process, which enables the production of intricate shapes and designs that would be difficult to achieve using traditional Why Use Powder for Metal Injection Molding? Redstone
.jpg)
This is Powder metallurgy Osweypm
2023年7月2日 Powder metallurgy products can be used in automobiles, motorbikes, textile machinery, medical equipment, aerospace, power tools, hardware tools, smart homes, construction machinery, various metal powder (iron, copper, stainless steelbased) components; the application of powder metallurgy technology seems to have no boundaries, and is suitable 2021年5月21日 The powder metallurgy process has two major molding technologies, one is MM injection molding, and the other is PM compression molding Both molding technologies are onetime molding, nearnet molding technology, suitable for small precision parts manufacturing, Bearing antifriction parts series mass production is more conducive to cost savings And Which is better, powder metallurgy MIM injection molding and 2023年7月26日 However, there are a few key differences when it comes to powder metallurgy and metal injection molding In this blog, we’ll compare powder metallurgy sintering vs metal injection molding sintering What is Sintering? Sintering involves heating the powder near its melting point so the particles can create a permanent bond between themPowder Metallurgy Sintering vs Metal Injection Molding 2013年12月28日 Complexshaped components can be obtained by net or nearnet shaping through the powder metallurgy processing route such as metal injection molding (MIM) process MIM is an advanced powder processing technique for the mass production of Metal Injection Molding (MIM) Processing SpringerLink
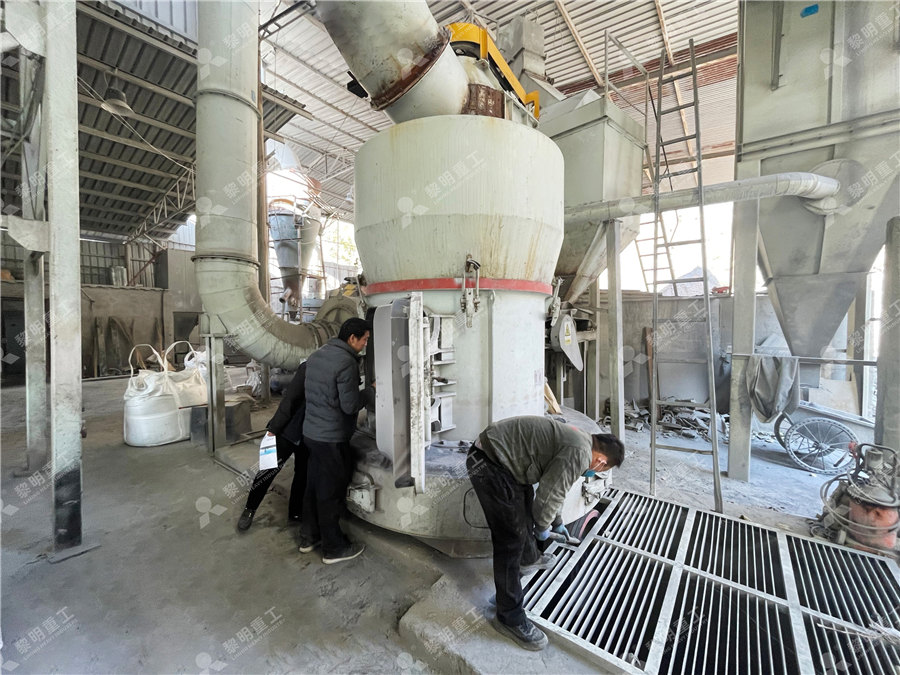
The Powder Injection Moulding Process AZoM
2001年11月29日 Powder injection moulding (PIM) and powder coinjection moulding (PCM) are similar to polymer injection moulding They are used to produce shaped components from powders and are suited to ceramic, metallic 2012年12月31日 Metal powder injection molding (MIM) has been in production since the 1970s During that time the market has expanded enormously to include a broad array of applications; the initial successes Metal powder injection molding (MIM): Key trends and marketsPowder injection molding (PIM) and metal injection molding (MIM) are powder metallurgy processes in which fine metal or ceramic powders are mixed with a binder material to create a feedstock The feedstock is then injection molded to form a ‘green part’ After molding, Powder Injection Molding Material Characterization Solutions2024年1月1日 Powder injection molding is a powder metallurgy near net shape forming parts made powder injection molding can reach up to 95% and the linear shrinkage can reach 15–25% According to the needs, the sintered products are subjected to posttreatment processes such as fine pressing, small amount processing, and surface Powder Injection Molding SpringerLink
.jpg)
Metal Injection Molding vs Traditional Powder Metallurgy
2022年5月9日 Both metal injection molding and traditional powder metallurgy have their strengths and weaknesses Learn about both processes and their Modeled after plastic injection molding techniques and powder metallurgy, MIM provides considerable freedom and flexibility in your choice of materials and enables a high degree of design 2012年3月23日 Powder injection molding (PIM) is a technology for manufacturing complex, precision, netshape components from either metal or ceramic powder The potential of PIM lies in its ability to combine the design flexibility of plastic injection molding and the nearly unlimited choice of material offered by powder metallurgy, making it possible to combine multiple parts Powder Injection Molding of Metal and Ceramic PartsPowder injection moulding, a relatively new technique for manufacturing articles of complex shape from metal or ceramic powders, is considered Production operations are described in detail: powder mixing with a binder to form a slip, injection of the slip into a mold, binder removal, sintering of the billets obtained Fields of application for articles prepared by injection moulding Injection Moulding (Review) Powder Metallurgy and Metal PDF On Mar 4, 2012, Joamin GonzalezGutierrez and others published Powder Injection Molding of Metal and Ceramic Parts Find, read and cite all the research you need on ResearchGatePowder Injection Molding of Metal and Ceramic Parts
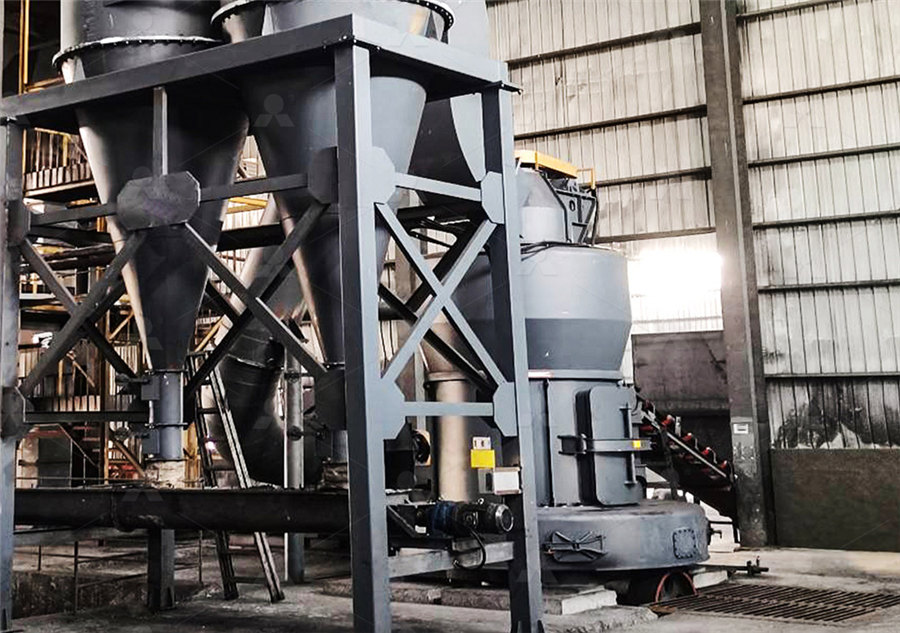
Progress in Titanium Metal Powder Injection Molding
2013年8月20日 Metal powder injection molding is a shaping technology that has achieved solid scientific underpinnings It is from this science base that recent progress has occurred in titanium powder injection The approaches to production of titanium powder injection molded parts are reviewed Historically, oxygen levels have been too high for structural use (particularly with the Ti6Al4V alloy) However, recent advances in starting powders, binders and sintering facilities now allow oxygen levels in the Ti6Al4V alloy to be controlled to about 02 wt% oxygen This should result in Advances in titanium metal injection molding Powder Metallurgy Overview of Powder Injection Molding PJ VERVOORT*, R VETTERt AND J DUSZCZYK* Laboratory of Materials Science, Delft University of Technology, Rotterdamseweg 137, 2628AL Delft, The Netherlands Abstract Powder injection molding is a near netshape technique suitable for the production of moderate toOverview of Powder Injection Molding2009年7月1日 The present work aims to explore the ability to simulate flow patterns and the velocity field in the powder injection molding (PIM) process using the smoothed particle hydrodynamics (SPH) methodEffect of powders and binders on material properties
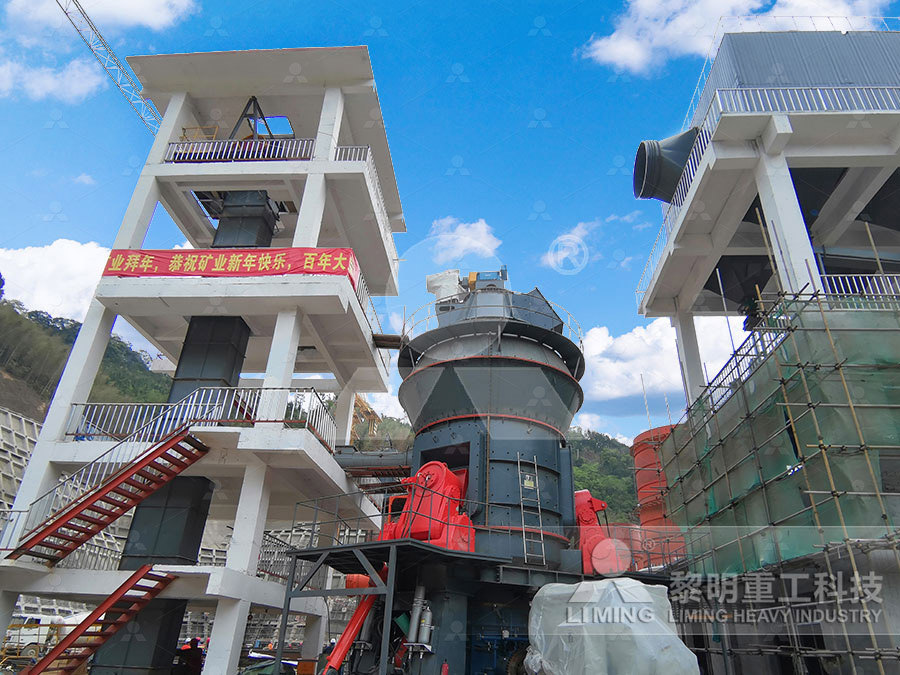
Sintering in the Powder Metallurgy Process
Powder Metallurgy shines in the MPIF’s 2024 Design Excellence Awards competition; PowderMet2024: Postprocessing; Consulting toll sintering; View online: Sign up to our Newsletter Join thousands of other PM 2021年7月12日 It is a new metal injection molding technology developed by combining powder metallurgy and polymer injection molding It is especially suitable for mass production of small, complex and large amount of metal products, especially for precision metal parts with complex structure, small volume and special requirements, which are difficult to be processed by What Are Causes Solutions Of Common Defects In Metal Powder Injection 2023年5月1日 NdFeB magnets can be either bonded or sintered Bonded magnets are composed of a magnetic powder combined with a polymeric component and can be molded using conventional polymer processing techniques such as injection molding [7], compression molding [8], extrusion [9], and material extrusion additive manufacturing [10, 11]In contrast, sintered Current challenges in NdFeB permanent magnets manufacturing by Powder 2022年2月3日 Metal injection molding (MIM) is a complementary process that also uses metal particles—just much finer— to produce highdensity components with threedimensional design flexibility Learn more about the MIM manufacturing process here >>>Metal Manufacturing Feedstock Powder Metallurgy Optimim
.jpg)
Powder Injection Molding Process in Industrial Fields
2018年9月15日 Powder injection molding is a combined technique of traditional powder metallurgy and plastic injection molding Since injection molding step in the process enables to produce complex shapes If you’ve paid attention to “Part of the Year” awards in powder metallurgy, you’ve noticed metal injection molding (MIM) is popular with critics While MIM is great for niche uses, conventional PM still offers many benefits Here's more about metal injection molding vs powder metallurgyMetal Injection Molding Vs Powder Metallurgy the 'Old'2022年11月18日 Metal Injection Molding and Powder Metallurgy Metal injection molding (MIM) is a metal processing process, which combines powdered metal particles with adhesive materials to form a mesh of metal parts and components In addition, unlike other technologies, MIM can produce small and complex parts at a lower costMetal Injection Molding vs Powder MetallurgyRequest PDF On Jan 1, 1991, RM German and others published Key Issues in Powder InjectionMolding Find, read and cite all the research you need on ResearchGateKey Issues in Powder InjectionMolding Request PDF