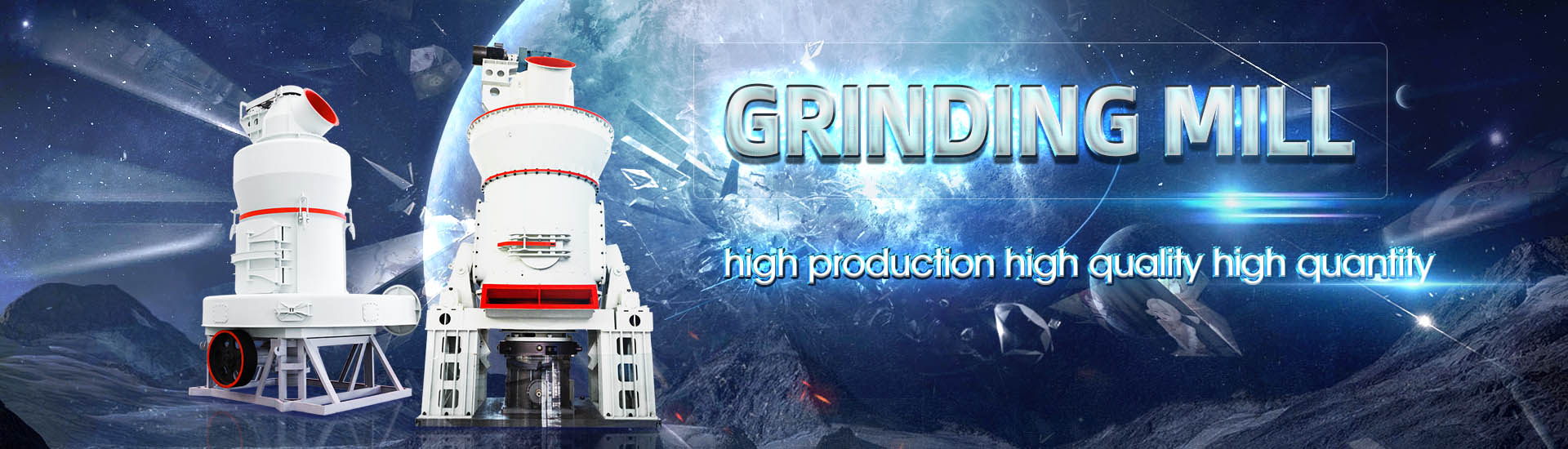
kaolin system operating procedures Changtong vertical mill
[GYQ0R)ZQ]ESS4NJ.jpg)
Kaolin Processing Plant MachinerySBM Industrial Technology Group
2023年1月3日 LM vertical roller mill is simple in process, integrating crushing, drying, grinding, powder selection and transportation into one set, compact in layout, small in floor area, and The HLMX vertical superfine kaolin roller mill is a special mill for the production of superfine kaolin powder It is designed to reduce lumps to a mesh size of 325 to 2500 The maximum capacity Kaolin Clay Processing Vertical MillThe kaolin grinding production line is a comprehensive system designed to process raw kaolin into a fine powder that meets the specific requirements of different industrial applications This Advanced kaolin grinding production line equipment: Elevating 2022年8月10日 Choose the main machine according to the output and powder fineness requirements: below 325 mesh, you can choose a Raymond mill; 1502500 mesh can choose Kaolin grinding production line and equipment selection
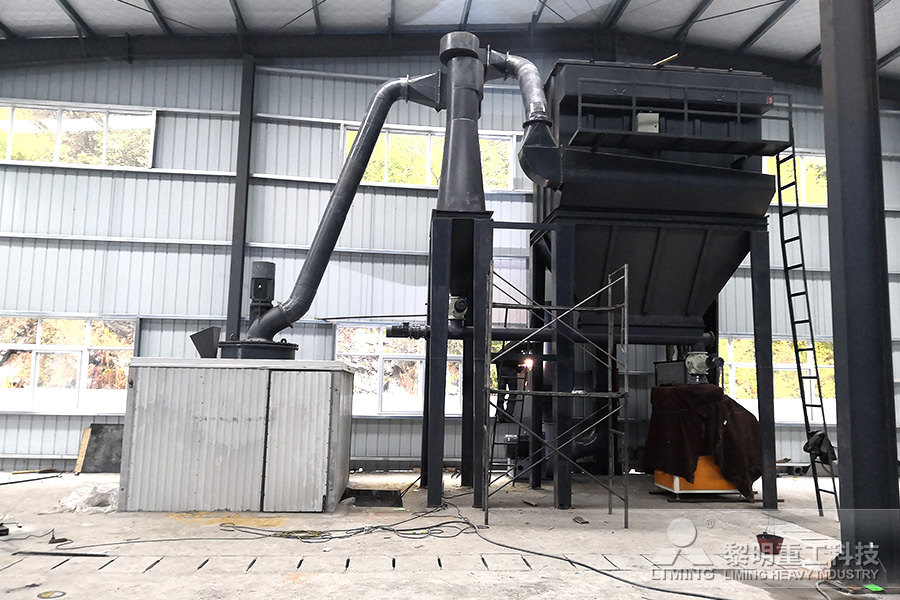
Kaolin Vertical Grinding Mill Production Line
2024年2月2日 In order to adapt to the grinding of highsilicaaluminum materials such as kaolin, pyrophyllite, and white foam stone, the stable material layer, efficient grinding, and fine powder 2023年6月1日 In this paper, a numerical calculation method for internal particle–fluid coupling system of large vertical mills based on CFDDPM theory and a multiobjective optimization Operation parameters multiobjective optimization method of What are the special characteristics, applications, and grinding processes of kaolin? All applications of kaolin must be processed into a fine powder before it can be added to other Kaolin Clay: Understanding Its Processing and Grinding WorkflowLUM Ultrafine Vertical Grinding Mill In the deep processing industry of kaolin, dry process and wet process are generally adopted, both of which require crushing and grinding of raw ore Let's Brief introduction of kaolin deep processing equipment and
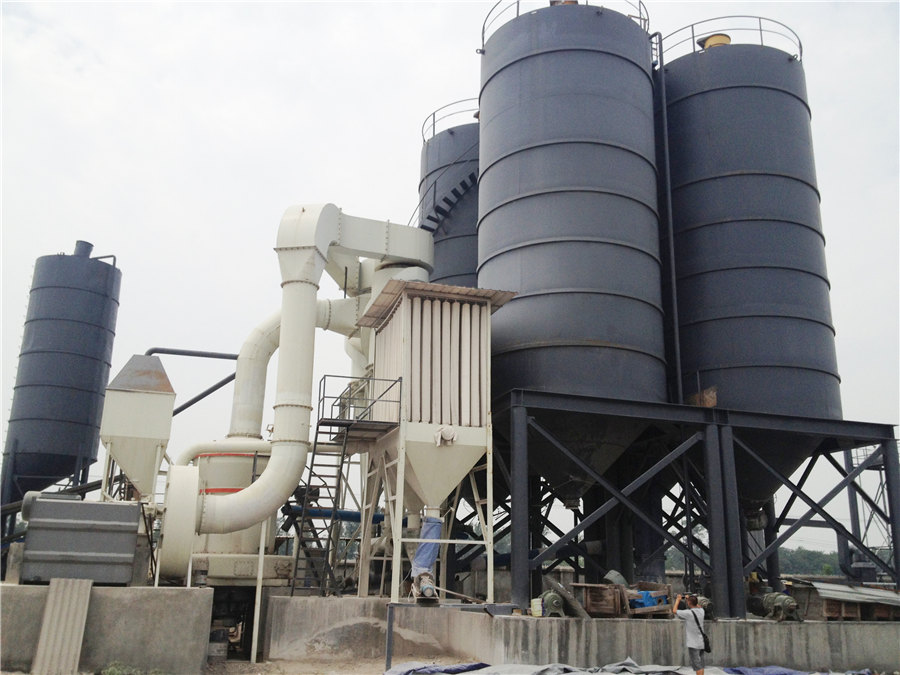
Research and Design of Suspension Calcining Technology and
The vertical roller mill (VRM) is used for the raw material grinding The kaolin with water content less than 14% is fed into the mill by a bucket elevator The material is grinded, dried and 1991年9月1日 Kaolins are white raw materials, their essential constituent being fine grained white clay, which are amenable for beneficiation that make them ideal for an assortment of Kaolin: processing, properties and applications ScienceDirectStandard Operating Procedure (SOP) Vertical Bandsaw • Ensure the guard doors are closed and Rail Drill 18 Hydraulic System Requirements 1920 OUR MISSION STANLEY is committed to the socalled “blank”, which is Standard Operating Procedure (SOP) Vertical The document provides standard operating procedures for a ball mill It lists 18 steps for operating the ball mill, including connecting power, loading materials and grinding media, starting and stopping the mill, and unloading processed Ball Mill: Standard Operating Procedure PDF Scribd
.jpg)
Ultra fine Vertical Roller Mill CEMENTL
Highquality ultra fine powder vertical roller mill manufacturer Tongli Ultrafine Powder Vertical Mill is particularly suitable for ultrafine grinding of nonmetallic minerals, including ultrafine calcium carbonate powder (fineness can reach 25 microns), limestone, barite, calcite, kaolin, gypsum, bauxite and graphite Its production capacity can reach 1030 tons per hour to meet the 2015年3月15日 Vertical stirred mills have become increasingly popular in size reduction operations in the fine and ultrafine range, being normally used in industry in continuous operationVertical Agitated Media Mill scaleup and simulationLimestone Powder Ultrafine Vertical Roller Mill Modle : CLUM Series Finished Size: 4003000 mesh Processing Ability: 3 – 45t/h Max Feeding Size: 10 mm M 1 Set Price: $ Range Of Application: Limestone, Calcium Carbonate, Talc, Limestone Powder Ultrafine Vertical Roller Mill2016年9月1日 Diversified operating conditions, inputoutput constraints, and parametric variations in the Vertical Roller Mill (VRM) make it to have complicated dynamics and closedloop instabilityOperational parameters affecting the vertical roller mill
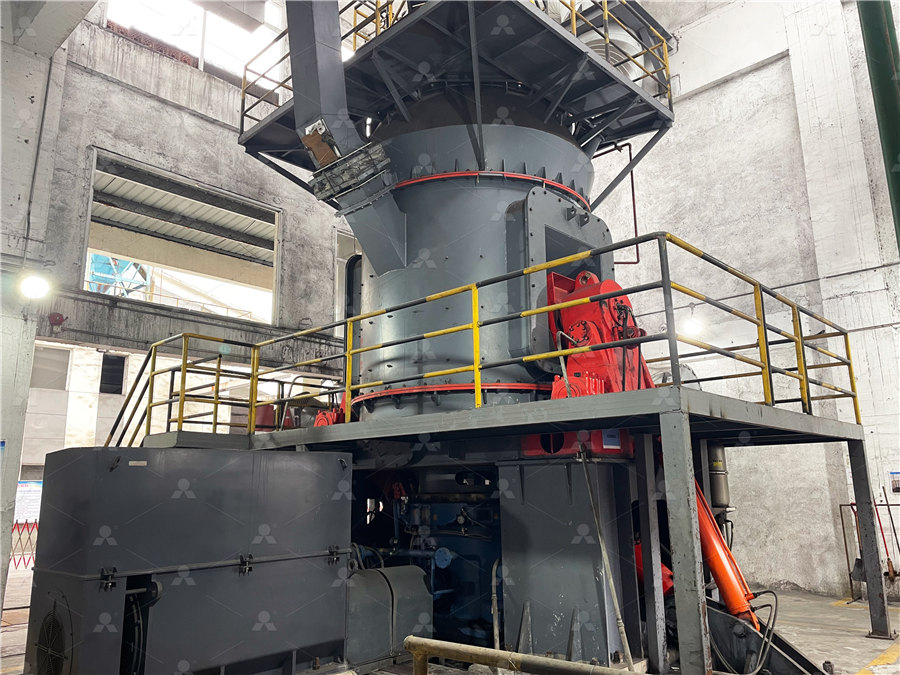
Operation parameters multiobjective optimization method of
2023年6月1日 This study aims to improve the output and production efficiency of a large vertical mill by optimizing its operational parameters This paper takes a large vertical mill in LGM as the object, a numerical calculation method of particle–fluid coupling system in large vertical mill based on CFDDPM theory, and a multiobjective optimization method of operating parameters of Working principle and characteristics of vertical mill Working principle The working principle of a vertical mill involves the rotation of a grinding table with rollers attached to it Raw materials are fed into the table and ground between the rollers and table The ground materials are then blown by hot air through an outlet in the mill's Working principle and characteristics of vertical mill2017年9月11日 Due to the compact design and material transportation system of vertical roller mills (VRM), some important streams (total mill feed and discharge, dynamic separator feed and reject) remain in the (PDF) Performance Evaluation of Vertical Roller Mill inPDF On Jan 1, 2017, J Harder published Drives for large vertical roller mills Find, read and cite all the research you need on ResearchGate(PDF) Drives for large vertical roller mills ResearchGate
.jpg)
Safe Operating Procedures SOP 20 Feed Mill / Roller Mill
Safe Operating Procedures This SOP should be used in conjunction with relevant machinery manuals and manufacturer recommendations Procedure Reference Version Effective Date Review Date Page Number Date Printed WHS SOP 20 10 28/03/2018 28/03/2021 1 24/04/2018 SOP 20 – Feed Mill / Roller Mill Operation Servicing2021年8月3日 SBM recommends 2 selfdeveloped industrial milling machines for you It can meet the grinding requirements of 2003000 mesh of kaolin They are HGM ultrafine grinding mill and CLUM vertical roller mill In addition to Kaolin Ultrafine Grinding Mill SBM Ultrafine Powder First MVR mill for cement grinding 1994 More power for MPS mills by introducing the Bseries 2007 First vertical mill with MultiDrive® 2016 Biggest cement mill in the world in operation 2017 ready2grind – World’s fi rst modular system with a vertical cement millPASSION FOR GRINDINGthe need to monitor and maintain appropriate mill operating procedures with inerting systems As part of the continuing effort to maintain proper mill system design and operation in coalfired power plants, Riley Power Inc, a Babcock Power Inc company has been actively developing technology to validate steam inerting system performanceMill Steam Inerting System Review and Performance Validation
.jpg)
LM series vertical mill
PRODUCT OVERVIEW LM series vertical mill is a new type of milling equipment with advanced technology, excellent performance and drying functionIt integrates the functions of drying, grinding and powder classifying,used in construction,coal,power plant,steel plant,construction,cement,ceramic and easy maintenance, power saving, fast investment FIGURE 4 Particle size distributions of collected samples (Survey 2) Bond work indices and breakage characteristics under compression were determinedPerformance Evaluation of Vertical Roller Mill in Cement Phrase one: raw material crushing Kaolin blocks will be crushed to 15mm50mm fineness by crusher Phrase two: grinding Crushed Kaolin material will be sent to the storage hopper by the elevator and then the feeder will send the material to the main mill for grinding Phrase three: powder classifying Ground material will be classified, coarse powder will fall back to the main Kaolin Grinding Mill Powder Making MachineCLUM series calcium carbonate ultrafine vertical mill, a new type of ultrafine grinding equipment integrating powder grinding, grading, conveying, secondary powder selection, and finished product packaging, focusing on the largescale production field of nonmetallic mineral ultrafine powder processingCalcium Carbonate Ultrafine Vertical Mill SBM Ultrafine

Vertical Milling Machines vs Horizontal: Differences Explained
2023年12月19日 But this limited cutting potential results in a lower removal rate for the vertical mill 7 Overarm and Arbor Support The horizontal milling machine has two elements not present in a vertical mill: an overarm and an arbor support The overarm is a HLMX ultrafine vertical kaolin mill The HLMX vertical superfine kaolin roller mill is a special mill for the production of superfine kaolin powder It is designed to reduce lumps to a mesh size of 325 to 2500 The maximum capacity of this system is up to 40 tons per hour The high airflow and effective air circulation allow for a very fine grindKaolin Clay Processing Vertical MillThe basic structure of the roller mill includes the grinding roller, the grinding body, the force generation and transmission mechanism, airflow, and the device for easy replacement It can be divided into vertical roller mill, horizontal cylinderrollermill,highpressurerollermill,Raymond mill, and column mill Vertical Roller MillRoller Mill Springer2023年12月4日 Operating Principles and Safety Basic Operation Steps and Procedures Like a wellexecuted battle plan, operating a vertical boring mill is about strategy and precision From setup to execution, every move matters: Vertical Boring Mills: A Comprehensive Guide
.jpg)
Increase productivity of vertical roller mill using seven
2021年1月29日 control system for Vertical Roller Mill", The 2nd international conference on Intelligent control and information processing [5] RVirendra, Dr BSudheer, P rem Kumar, JSuresh Babu and DRajani 2020年3月1日 Finally, the health management system, including the functions of condition monitoring, fault diagnosis, and trend prediction for large vertical mill is implemented using Microsoft Visual Studio C A health management system for large vertical mill ResearchGateLUM Series Ultrafine Vertical Roller Mill talc, dolomite, barite, kaolin, wollastonite, gypsum, feldspar, pyrophylite and other nonmetallic mineral ores Online Chat Inquiry Video of LUM Ultrafine Vertical Roller Mill The LUM adopted PLC/DCS automatic control system, which can control grinding pressure accuratelyLUM Series Ultrafine Vertical Roller Mill2012年3月1日 Vertical roller mills are the mills traditionally used for processing granulated blastfurnace slag and for grinding composite cements From the energy aspect they are superior to grinding plant Operating experience with a vertical roller mill for grinding
.jpg)
Atox Vertical Roller Mill, Maintenance and Repair
The document discusses maintenance and repair of an ATOX Vertical Mill It describes systematic and conditionbased maintenance approaches Systematic maintenance consists of regular cleaning, lubrication and visual inspections Conditionbased maintenance monitors factors like vibration levels and temperatures during operation and performs more thorough inspections 2022年1月23日 This work concentrates on the energy consumption and grinding energy efficiency of a laboratory vertical roller mill (VRM) under various operating parametersAnalysis and Optimization of Grinding Performance of Vertical Find your kaolin mill easily amongst the 20 products from the leading brands on DirectIndustry, closed system, no dust, low operating cost, grinding particle size range D50: 0510μm The revolution of dry milling technology, Kaolin mill All industrial manufacturersPROCESS TRAINING for operators of Vertical RAW Mills Heating of mill and grinding plant In fact there are three processes going on in the MPS mill namely grinding, drying and clas sifying, and only when all three processes are working well the operation is smoothPROCESS TRAINING for operators of Vertical RAW Mills
.jpg)
An investigation of performance characteristics and
2020年8月12日 This study shows the performance of a currently running vertical roller coal mill (VRM) in an existing coalfired power plant In a power plant, the coal mill is the critical equipment, whose 2014年7月25日 In this paper, vibration characteristics of a Vertical Roller Mill (VRM) are studied by using physical parameters of an operating VRM The mathematical model is derived and simulated for a set of Vibration Analysis of a Vertical Roller Mill: Modeling and ValidationIntegrated cooling A cooling system is integrated in the milling cup, WTM intelligent vertical mill is dedicated to the highefficiency dissociation of minerals, • High energy utilization rate, low operating cost, grinding particle size range D50: 0510μmVertical mill, Vertical grinding mill All industrial manufacturers2020年7月10日 What’s a Standard Operating Procedure (SOP)? A standard operating procedure, or SOP, is a set of detailed stepbystep instructions that describe how to carry out any given process Most companies that are serious about process management use SOPs to manage their daytoday activities Why? Well, Standard Operating Procedures allow you to:Standard Operating Procedure (SOP) Guide Examples
.jpg)
Grinding process optimization — Featuring case studies and operating
PDF On May 1, 2017, Caroline Woywadt published Grinding process optimization — Featuring case studies and operating results of the modular vertical roller mill Find, read and cite all the Fig 1 Flowsheet of modular vertical roller mill 5000 R4 The required throughput rates were achieved in short time All fineness figures met the target values as well without anyGrinding Process Optimization Featuring Case Studies and Operating Productivity Inc Haas CNC Mill Operator Manual Page 5 Introduction to Basic Vertical Mill Operation Welcome to Productivity, Inc, your local Haas Factory Outlet (HFO) for the Haas Mill Operator Class This class is intended to give a basic understanding of the setup and operation of a Haas Machining CenterNew Mill Operator New 0412docxOperational parameters affecting the vertical roller mill performance × industry In literature, there are many studies performed in cement plants on comparison of conventional grinding systems and vertical roller mills in terms of energy consumption Table 2 presents the operating conditions of the mill at steady state conditions 3(PDF) Operational parameters affecting the vertical roller mill
.jpg)
Vertical roller mill for raw Application p rocess materials
Mill Fig1 Flow of Conventional Vertical Mill Grinding System Mill Kiln IDF (Kiln gas exhaust fan) Fig2 Flow of direct dust collection system Results Power consumption of fan(s) reduces about 3 to4 kWh/t Cost estimation When a mill with a production capacity of 420 t/h was newly constructed, the total cost was about 25 million US$ [1US$=¥ • Mill motor speed • Mill air flow/mill differential pressure • Temperature after the mill • Pressure before the mill • Grinding stock feed • Classifier speed • Mill fan speed • Water spraying • Hot gas • Fresh air Manipulated variables Disturbance variable Process measured value RelauchLMmaster 6 250814 11:47PROCESS OPTIMISATION FOR LOESCHE GRINDING PLANTS