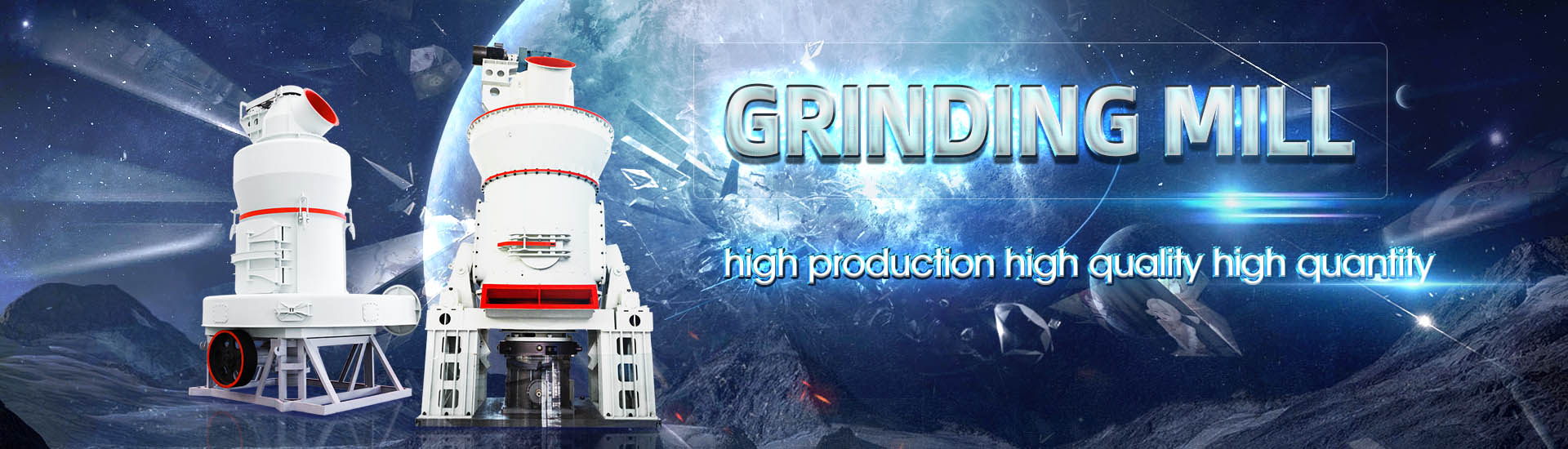
When will the cement mill with a diameter of 3 meters be eliminated
.jpg)
Article 7: Kiln mill under 3 meters will withdraw from the h Jiangsu
Speeding up the elimination of backward production capacity is an important measure to change the mode of economic development, adjust economic structure, improve the quality and efficiency of economic growth It is also an urgent need to speed up energy saving and emission Cement grinding equipment with a diameter of less than 3 meters (excluding the production of special cement) Recently, the Jiangxi Provincial Office of Industry and Information Jiangxi will eliminate mechanical shaft kilns and cement grinding Several energy efficient options for cement grinding are available today such as vertical roller mills, roller presses (typically in combination with a ball mill), and clinker pregrinders with ball millsOptimization of Cement Grinding Operation in Ball 2 BALL MILLS INTERNATIONAL CEMENT REVIEW FEBRUARY 2021 aim of delivering a target mill discharge size at the end of the chamber, with a maximum residue of five per cent >2mm BALL MILLS Ball mill optimisation Holzinger Consulting
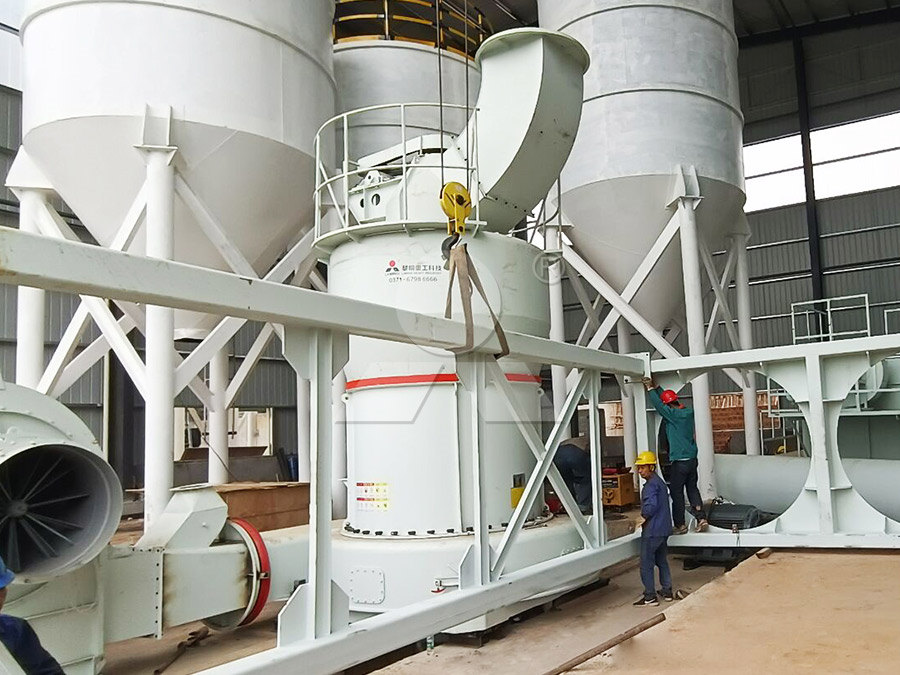
OPTIMIZATION OF CEMENT GRINDING OPERATION IN BALL MILLS
optimization of cement grinding operation in ball mills Several energy efficient options for cement grinding are available today such as vertical roller mills, roller presses (typically in combination From the early 1990s till today, the OK mill has since been successfully developed and manufactured by FLSmidth By combining product leadership with customer intimacy, we OK Mill: The 3: Mechanical optimized and 31: Grinding concept 2017年10月26日 As well, mills with different length to diameter ratios for a given power rating will yield different material retention times, the longer units being utilized for high reduction ratios, and the shorter ones where overgrinding is of Factors Affecting Ball Mill Grinding EfficiencyWhen transferring to closed circuit а mill size 26×13 m at a constant quality cement (3000 cm2pg) capacity grinding unit was increased from 25 to 38 tph while reducing the specific Analysis of the efficiency of the process in closed circuit ball mills
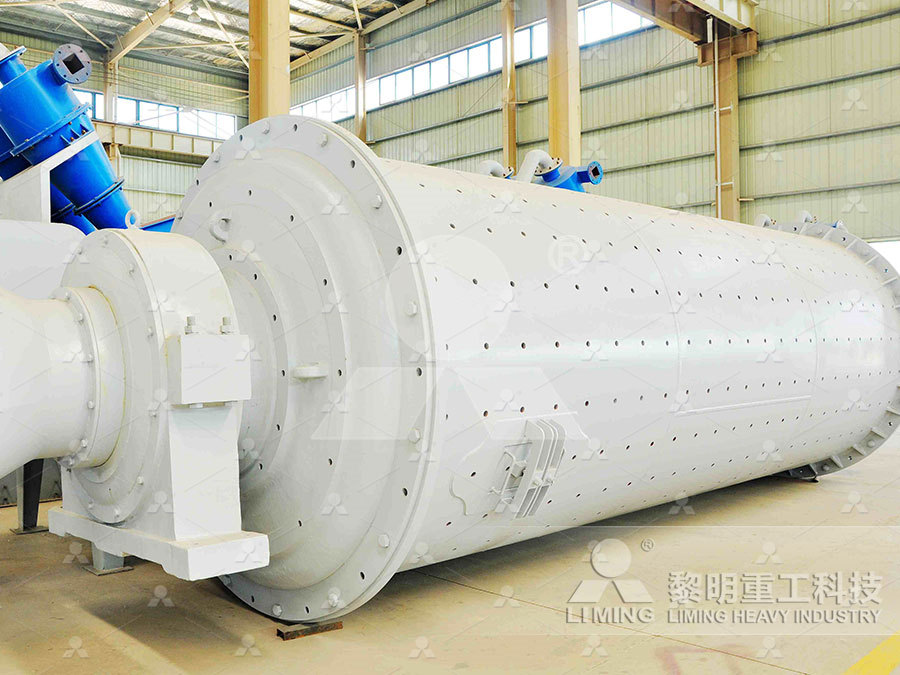
Review on vertical roller mill in cement industry its performance
2021年1月1日 Vertical roller mill has proved to be a popular choice for finished cement grinding over all other machineries due to advantages like low power consumption, higher capacity, The Cement Plant Operations Handbook is a concise, practical guide to cement manufacturing and is the standard reference used by plant operations personnel worldwide Providing a The Cement Plant Operations Handbook International Cement and cement Roller presses are used mainly in combination with a ball mill for cement grinding applications and as finished product grinding units, as well as raw ingredient grinding equipment in mineral applications This paper will focus on the ball mill grinding process, its tools and optimisation possibilities (see Figure 1) The ball millBALL MILLS Ball mill optimisation Holzinger ConsultingCement mill A cement mill (or finish mill in North American usage[1]) is the equipment used to grind the hard, nodular clinker from the cement kiln into My Ball mills are normally operated at around 75% of critical speed, so a mill with diameter 5 metres will turn at around 14 rpmCement mill
.jpg)
Ball charge optimization INFINITY FOR CEMENT EQUIPMENT
Previous Post Next Post Contents1 Ball charge optimization2 1 How to use the BP21 2 Description of the main indicators used in this BP2101 The residue on 2mm/4mm before partition wall2102 Material filling level and ball charge expansion211 Cement mill specific power 1st compartment 212 Raw mill specific power 1st compartment Ball charge clinker are processed in the mill, divided into two stages: the grinding stage in chamber I and the milling stage in chamber II In the final stage, the cement is transferred to the separation stage, where the raw material is returned to the mill while the fine cement is stored in the storage silo [38, 40] 23 Cement Packaging and DispatchImpacts of Cement Production on the Environment with Practical It was found that the monthly average recorded at the level of dust concentrations was about 6764 mg/Nm 3 , together at the two sampling points, for 2019 and 798 mg/Nm 3 for 2020, with a weight The flowchart of cement grinding, A, Bsampling points 2014年4月1日 Two mill systems are employed for most coal grinding applications in the cement industry These are, on the one hand, vertical roller mills (VRM) that have achieved a share of almost 90% and, on (PDF) The latest innovative technology for vertical roller mills
.jpg)
Cement Plant: The Manufacturing Process 4 5 World Cement
ground in a cement mill, which creates cement The cement is then packed and distributed to consumers The kiln feed is blasted in a cement kiln at a temperature of 1450oC, causing clinkering to occur (small balls of up to 25mm diameter) 6 5 Raw mill Preheated tower Cement storage silos Packing warehouse Raw material silos Limestone storage and between 50 meters and 300 meters depending on the thickness of the formation, however the limiting factor in the height of the bench is usually that of safety or hole diameter Safety can be the inherent stability of the formation, the greater the stability the higher the bench and hence the longer the drill holeQuarrying In the cement industry INFINITY FOR CEMENT EQUIPMENTVertical Roller Mill Vertical roller mills (VRM) are a type of mainstream clinker grinding equipment in the cement manufacturing process Vertical roller mills are still newish cement mills since their history in cement production is no more than 20 years, but they have already become the standard cement equipment in many regions and are getting more and more popular among Cement Mill for Sale Buy Cement Ball Mill Vertical Roller Mill Ball weight = [diameter (mm)] 3 / 250 For a cement mill: intermediate or outlet diaphragm For the case of; cement mills with a drying chamber see raw mills Mill working conditions: ventilation air speed through the mill Bigger or smaller than 12 [m/s] Material abrasivityEverything you need to know about clinker/cement Grinding
.jpg)
Analysis of the efficiency of the grinding process in closed circuit
ball mill open and closed circuits [12] with the installation in all cases the dynamic separator When transferring to closedcircuit а mill size 26×13 m at a constant quality cement (3000 cm2pg) capacity grinding unit was increased from 25 to 38 tph while reducing the specific consumption of electricity from 416 to 293 kWhpt The parameterThe performance of the cement ball mill in cement grinding system directly affects the output capacity and cement quality of the cement plant which can reduce the diameter of the clinker particles to 5 ~ 8mm 2) The pregrinding adds a How to Improve Cement Ball Mill PerformanceThe installation of liners Length Diameter Ratio The lengthdiameter ratio of the cement ball mill is relatively large For mills of opencircuit grinding system, the lengthdiameter ratio is usually between 35 and 6 to ensure that the product Cement Ball Mill Cost Effective Cement Grinding Mill Problems of the cement mill can disturb the performance of the separator Uncommon circuit thecementgrindingoffice 710 Special designs for Diameter of the cage: 1,66 multiplied by 1,5 = 2,49m or 2,50m Speed through the cage: Separators in the cement industry
.jpg)
Trials on high quality cement with a Loesche vertical roller mill
2011年3月1日 These mills, which have grinding table diameters of 53 m and three support rollers in addition to the three grinding rollers, have outputs of 145 t/h with a specific power consumption of the mill 2004年12月1日 During the last decade, semifinishgrinding plants have been used more and more for the energy efficient grinding of highquality cement In 1999, it was found that by decreasing the ball charge Optimization of continuous ball mills used for finishgrinding of 3 Two chamber cement ball mill The outer mill shell diameter is 405 m long and the mill can have feed added at the feed end of the first chamber and it then discharges as ground product from the discharge end of the second chamber 31 First chamber The internal shell diameter of the first chamber is 385 m and it is 43 longBall motion, axial segregation and power consumption in a full 2017年8月15日 Cement is used in mortar (to bind together bricks or stones) and concrete (bulk rocklike building material made from cement, aggregate, sand, and water) By modifying the raw material mix and the temperatures utilized in manufacturing, compositional variations can be achieved to produce cements with different propertiesThe Cement Manufacturing Process Process Systems Design
.jpg)
(PDF) Cement mill optimization: Design parameters
1995年10月29日 The control system, based on a 2S4265 CNC unit, allows the milling machine to be operated in universal mode (with manual control), automatic mode (to a set program), copying mode, gauging mode 2020年11月5日 We compare 3 cement milling and cement mill processes, including cement ball mill, vertical roller mill, and rod mill Find your answer here! Skip to content +86 info@ reach 5% or roller diameter, the feeding size of a largesized vertical cement mill can be 150200mm; Strong applicability for grinding materials 3 Necessary Cement Milling Comparison Ball Mill, Vertical Roller Milland not directly related to the mill proper Versatility: Rapid change between feed compositions 3: Mechanical 31: Grinding concept The grinding portion in the OK Mill is significantly different from other cement grinding mills on the market Figure 2: Grinding portion of the OK mill As shown in Figure 2, it consists of aOK Mill: The 3: Mechanical optimized and 31: Grinding concept 2024年1月26日 Cement ball mill is a well known machine to grind raw material (hard clinker) into grey powder: D = mill diameter inside liner (meter) K = proportionality constant = 335 for steel balls L = useful mill length (meters) For R = 21 m Computation of charging media for a double compartment cement ball mill
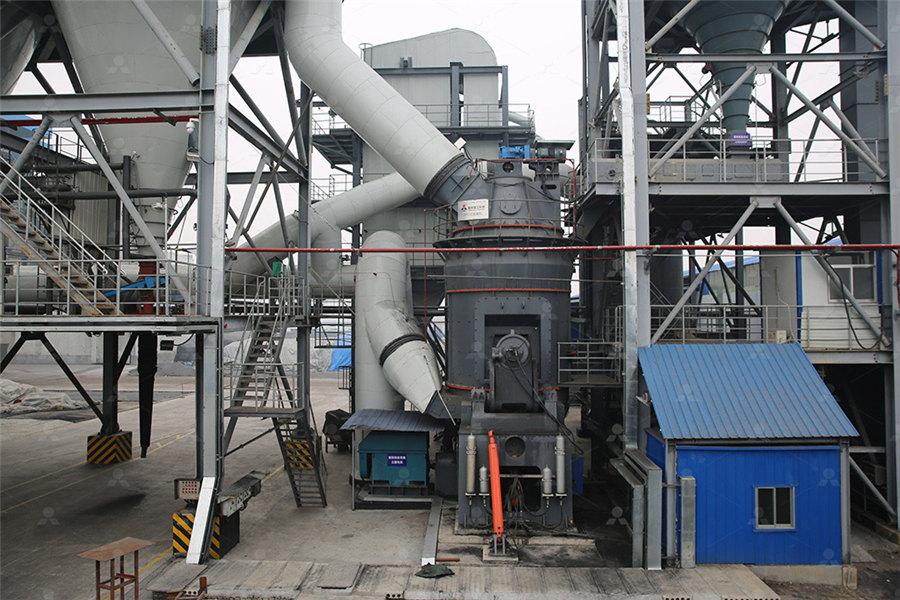
(PDF) Effects of Ball Size Distribution and Mill Speed and Their
2020年7月2日 After determining the model parameters, the mill was simulated in mill fillings of 15, 20, 25, 30, 35 and 40% with ball media of 2 and 25 cm in diameter For every mill filling, the numbers of The principal raw materials for cement manufacturing are: Limestone; Silica and alumina from basalt , shale or sand; Iron from iron ore or steel mill scale Sand stone; Pumice (volcanic ash for Portland Pozzolana cement ) Gypsum General Properties of Raw Material Sources Limestone; The basic raw material of the cement production is limestoneCement Manufacturing Process INFINITY FOR CEMENT EQUIPMENT2015年2月14日 However, the measurement of material flow rates was not easier Costea et al [13] developeda fuzzy logicbased control architecture in which the ball mill grinding process was considered as a Control System Architecture for a Cement Mill Based on Fuzzy The company’s cement ball mill has 31 specifications and models with a cylinder diameter ranging from 22m to 42m, and the supporting motor is 380KW to 3530KW A single cement ball mill can meet the grinding of 1187t cement products per hour, such as with a roller press Combined use, the production capacity will be greatly improvedBall Mill In Cement Plant Selling Various Types Of Cement Mill
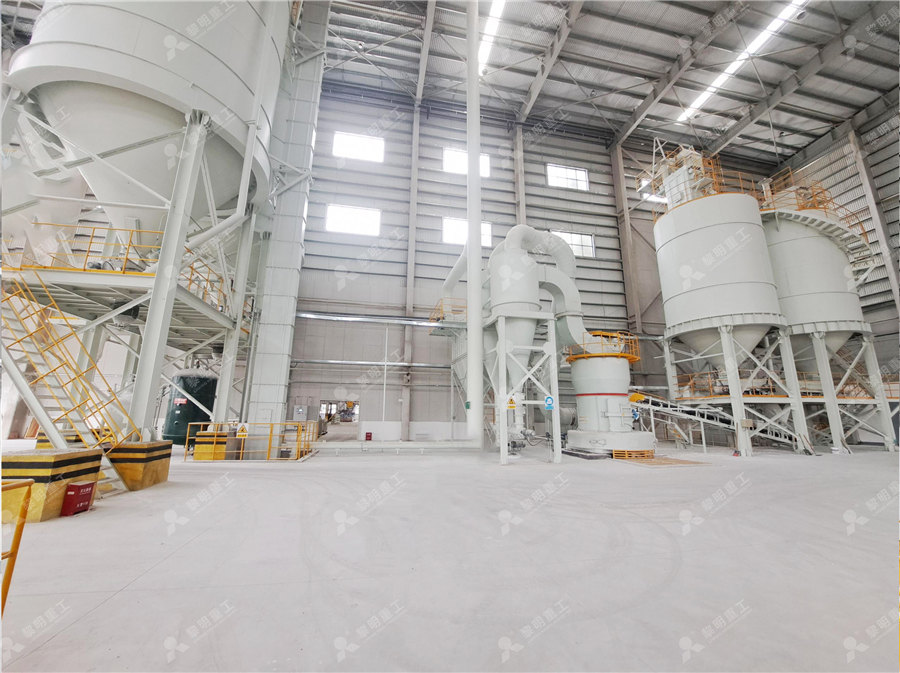
Wet Process Of Cement Manufacturing With Flow Chart
3 Slurry composition in the tank is tested to give the required chemical composition and corrected periodically in the tube mill 4 After that, the slurry is stored in the final storage tanks, and to keep the slurry inhomogeneous condition continuous the agitation is done in the tank The following is a cement manufacturing process flow chart,Cement Grinding Optimization Free download as Word Doc (doc / docx), PDF File (pdf), Text File (txt) or read online for free 1 The document discusses optimizing cement grinding circuits It presents tools like the Bond method and population balance models that can be used to analyze and optimize cement grinding 2 It provides details on the typical cement production process Cement Grinding Optimization PDF Mill (Grinding) CementThe motor was manufactured by Brown, Boveri and Comp, Baden, Switzerland The 5 m diameter mill was supplied by the WEDAG Co, now KHD Humboldt Wedag AG Koln, W Germany The tube mill has a diameter of 5000 mm; a bore of 8000 mm was selected for the motor, which resulted in an outer diameter of about 10,000 mm The active core length is 950 Mill drives INFINITY FOR CEMENT EQUIPMENT2004 The 50th Loesche mill with 2+2 technology for grinding cement and granulated blast furnace slag was sold worldwide 2005 The first mill with 3+3 technology, an LM 563+3, was commissioned in the Rajgangpur works of OCL Ltd in India 2006 The 100th Loesche mill for grinding cement and granulated blast furnace slag was sold worldwide2 µm 5 µm Loesche

Vertical raw mill Cement Plant
Vertical raw mill is one kind of raw mill, generally used to grind bulk, granular, and powder raw materials into required cement raw meal in the cement manufacturing plantVertical raw mill is an ideal grinding mill that crushing, drying, grinding, 2023年7月10日 Cement is the primary material for building and civil engineering constructions Therefore, the cement manufacturing sector plays a vital role in the nation's economic developmentCement Manufacturing Process and Its Environmental Cement manufacturing brief description of a cement mill Cement clinker is usually ground using a ball mill This is essentially a large rotating drum containing grinding media normally steel balls As the drum rotates, the The cement millThe cement mill is more than 3,200 mm in diameter with a doublespoon feeder and a single spoon feeder when the diameter is less than 3,200 mm Cement mill Characteristics of the cement mill 1All parts of the cement ball mill is manufactured by good materials, Cement Mill Manufacturer In China FTM Machinery
.jpg)
A study on the specific rate of breakage of cement materials in a
2003年3月1日 Among these, ball size which is a critical parameter that affects the performance of a mill, has been the subject of many studies Deniz (2003 Deniz ( , 2012a investigated the grinding kinetics of Figure 333 A typical view of kiln burning zone showing flame and material load The location selected to monitor in the kiln will influence the temperature readings If different locations are selected, different temperature readings will usually resultEverything you need to know about Kiln System Operations in Cement 2019年10月18日 One of the advantages of cement and the cement concrete industry in sustainability is the ability to utilize large amounts of industrial solid wastes such as fly ash and ground granulated blast Utilization of tailings in cement and concrete: A reviewPrevious Post Next Post Contents1 Coarse size reduction of raw materials in Cement Industry11 Size reduction machinery and methods111 A Machinery for size reduction in the coarse range (crushers) by application of compression:112 B Crushers for size reduction by impact:113 C For comminution in the fines range (grinding mills) by application of impact:114 D Mills where Complete Lecture about Crushers in Cement Industry
.jpg)
Open and closed circuit dry grinding of cement mill rejects in a
stirred mill grinding rather than ball mill grinding [5] The separator reject sample was brought to the ‘‘Yakup KESKI˙N’’ Mineral Processing Laboratories of the ZEDEMAmong these is Shah Cement, which has ordered the world’s largest OK mill The OK 816 mill features six rollers and an 81metre diameter grinding table, boasting an installed power of 11,600 KW The trend towards larger OK mills in Bangladesh is helping cement producers keep up with the boom in infrastructure developmentMaking gains with the OK™ mill