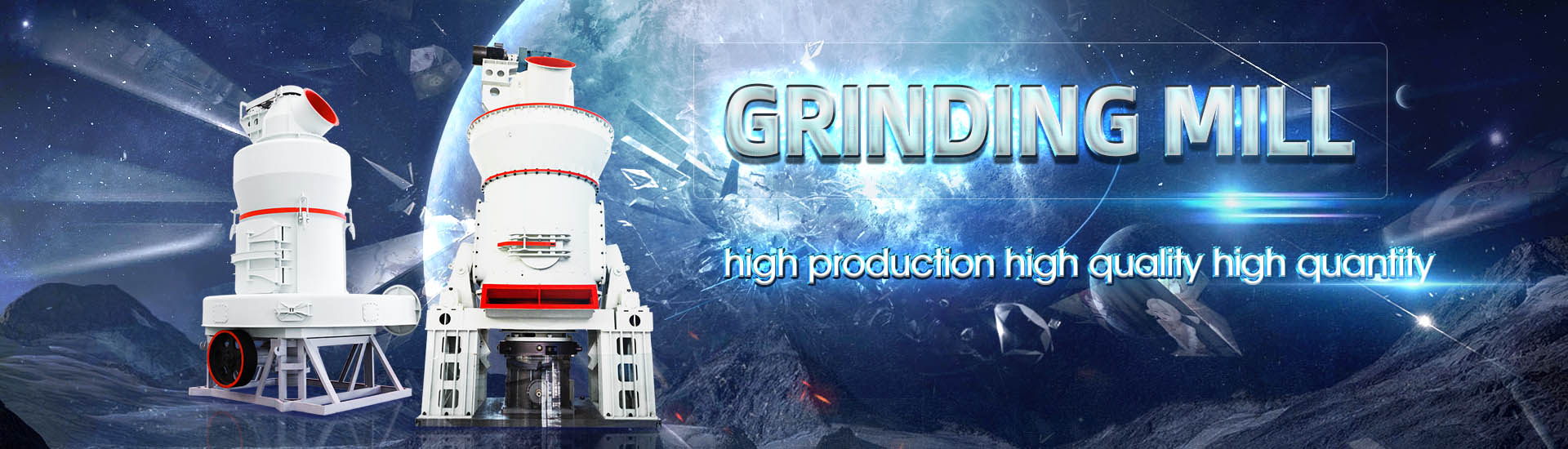
A steel plant uses 60 ore
.jpg)
From Ore to Iron with Smelting and Direct Iron
2017年10月17日 Ironmaking is a critical step in producing high performance steel because highquality raw materials reduce the time and energy to purify al available in the country with an average capacity utilization of 60% The coalbased DRI kilns in India sufer from lowenerg eficiency (about 37%) due to highenergy losses through ofgases ENERGYEFFICIENT TECHNOLOGY OPTIONS FOR DIRECT Most emissions come from the 30 or so integrated steel plants that produce almost twothirds of Europe's steel The majority of European steel (60%) is made via the primary route It involves The future of steelmaking Roland BergerRecycling steel scrap has the potential to reduce the use of iron ore In the US over 60 percent of steel comes from melting scrap metal reducing capital costs for building blast furnacesA Study of Energy Efficiency in the Indian Iron and Steel Industry
.jpg)
FACT SHEET Steel and raw materials
ed iron ore is used to make steel Iron is one of t e most abundant metallic elements Its oxides, or ores, make p about 5% of the earth’s crust Average iron content for highgrade ores is 2021年3月17日 The blast furnacebasic oxygen furnace process route, which uses iron ore and coke to produce steel, represents 90% of primary production The direct reduced ironelectric arc furnace uses highquality iron pellets and Driving Energy Efficiency in Heavy Industries – Analysis2023年6月4日 Steel production, a vital industry, needs transition to lower its carbon footprint Globally, almost 90% of CO 2 emissions of ‘primary steelmaking’ come from use of coal/coke The Blast Furnace: A Vital Tool in Climate Neutral OreBased 2023年5月4日 In this study, we provide a baseline assessment of the global potential of renewablespowered steel production using green H 2 DRIEAF technology, where the entire Global green hydrogenbased steel opportunities surrounding

Iron Ore in India , Types, Uses, Distribution, World Map
2024年9月27日 Haematite (FE2O3): This reddish ore has 6070% iron Limonite: This yellowish ore contains 4060% iron Siderite: Energy Production: Iron ore is used in the production of iron and steel, which is used in power 2012年4月1日 Request PDF Recycling of steel plant mill scale via iron ore sintering plant During the processing of steel in steel mills, iron oxides will form on the surface of the metal These oxides Recycling of steel plant mill scale via iron ore sintering plantThe plant trials were performed at Tata Steel’s iron ore mines at Noamundi The slime sample was withdrawn periodically from the hydrocyclone overflow, that is, the tailings of the beneficiation plant as schematically shown in Figure 3 The fresh slimes sample was stored in a tank for a set of continuous scale testsIron Ore Tailing Beneficiation a Potential Resource for Future2020年8月3日 There is healthy intraregional trade of steel products in the EAC already (see Appendix A) EAC PS banned most scrap metal exports back in 2010 to ensure regional firms retained access to raw The Prospects of Uganda’s Iron Ore Deposits in Developing the Iron
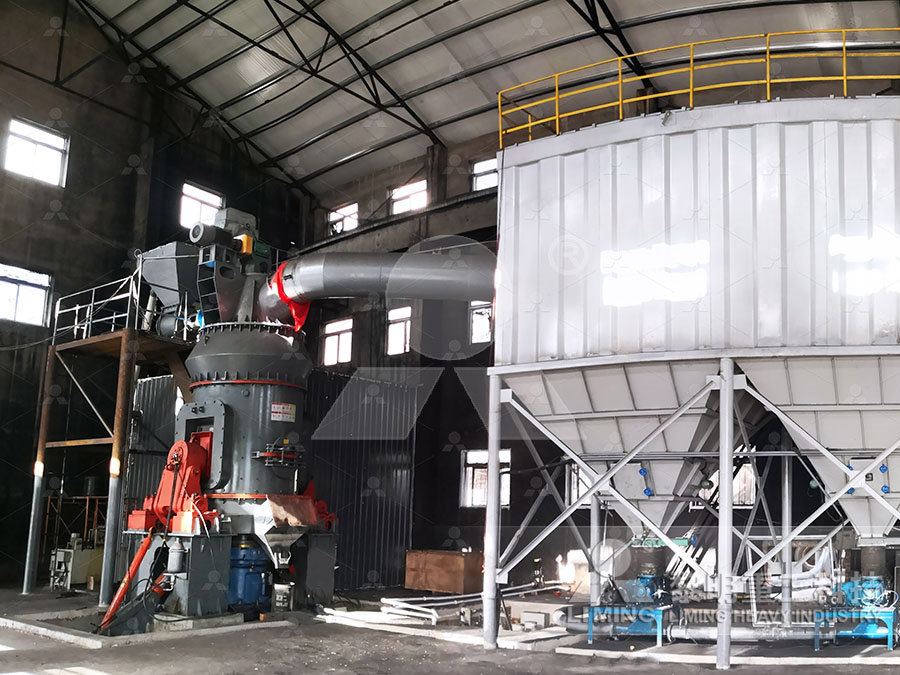
The Blast Furnace: A Vital Tool in Climate Neutral OreBased
2023年6月4日 At least three steel plants Footnote 2 (in India) have applied this concept—of having DRI plants within the steel plant, and directing COG and other steel plant gasses to make DRI The roadmap for lowering footprint of BF in Japan considers use of COG to either make hydrogen input to the BF directly or find ways to make hydrogenbased DRI—and charge to Typically, the integrated steel plants use medium/high grade iron ore, whereas the sponge iron plants require only high grade iron ore, preferably, with + 67% Fe [20] Iron ore production in 2009 was reported as 2,230 million metric tons (Mt), with a metal content of 1,090 million metric tonsIron Ore an overview ScienceDirect TopicsSteel is the world's most important engineering and construction material It is used in every aspect of our lives; in cars and construction products, refrigerators and washing machines, cargo ships and surgical scalpels It can be recycled over and over again without loss of propertyWhat is steel? worldsteel2023年9月20日 A CO2 emissions inventory of 4,883 individual iron and steel plants along with their charcoalbased iron and steel plants can reduce CO 2 emissions by 60% Use of LowGrade Ore as a Global iron and steel plant CO2 emissions and carbonneutrality
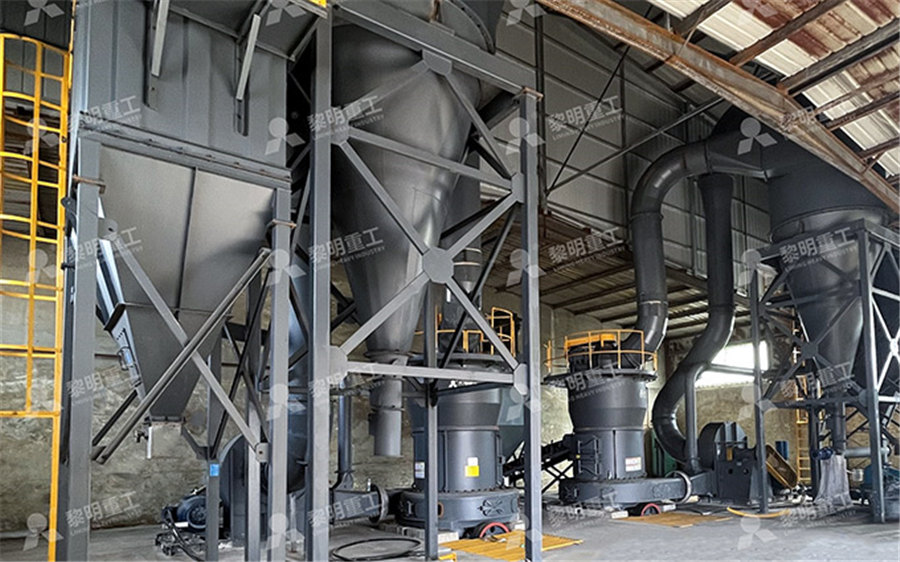
Steel Ingot Official Satisfactory Wiki
Steel Ingots are smelted from Iron Ore and Coal in Foundries They are mainly used to produce Steel Pipes and Steel Beams The following shows different ways to produce 1 Steel Ingot / second, or 60 / min: Weighted Point is the weighted consumption rate which is calculated by: (resource consumption rate / maximum extraction rate) * 10,000 The lower the better Energy 2013年5月8日 Hydrated lime (either dry or as a slurry) has a number of miscellaneous applications in the steel plant and further processing of the steel products It is normally used in wire drawing, acting as a lubricant as the steel rods or wires are drawn through dies, and in pig casting in which a lime whitewash coating on the moulds prevents stickingLimestone and Dolomite and their Use in Iron and Steel Plant2019年7月15日 more ores are used as fe ed material to targ et the required Mn/ dominated by Ch inese and India n steel produc tion plants (2860 MW active power and 052A Review of Ore Smelting in High Carbon hydrogen per hour A plant with a capacity of 100 MW is to be built in the Port of Hamburg5 Steel companies are currently looking at hydrogen use in a number of ways The first approach is to develop and deploy breakthrough hydrogen reduction technology, virtually eliminating direct GHG emissions from the ironmaking process A number ofHydrogen (H2)based ironmaking Steel
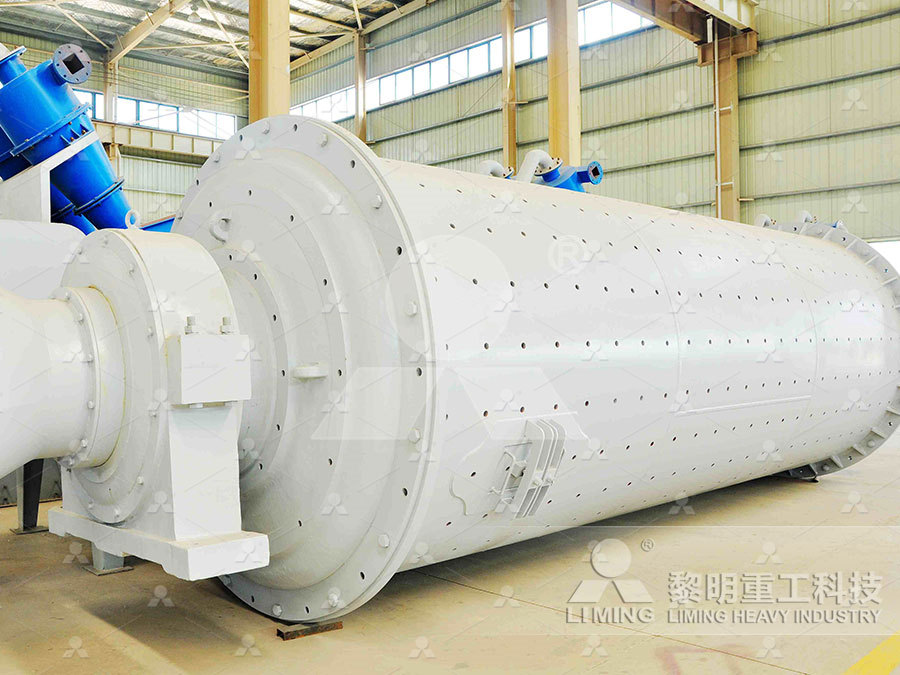
Iron Ore Processing: From Extraction to Manufacturing
2024年4月26日 Iron ore processing is a crucial step in the production of steel, one of the most essential materials in modern society Iron ore, a naturally occurring mineral composed primarily of iron oxides, is mined and processed the needs of our growing population , steel use is projected to increase by 15 times that of present level by 2050 Keywords: Steel Plant; Energy Conservation Cite This Article: Arijit Mukherjee, Soumendra Nath Basu, and Sayan Paul (2018) “A REVIEW ON ENERGY EFFICIENCY OF STEEL PLANTS IN INDIA” International Journal ofA REVIEW ON ENERGY EFFICIENCY OF STEEL PLANTS IN INDIA2009年8月1日 Request PDF Recycling of steel plant mill scale via iron ore pelletisation process Total generation of mill scale at JSWSL is around 150 t/day and contains 60–70%FeO and 30–35%Fe2O3Recycling of steel plant mill scale via iron ore ResearchGateDuring mechanized mining, 60 to 70 per cent output is generated as fines below 10 x103 m size This paper highlights the overview of iron ore fines and steel plant wastes utilizationAn Overview: Utilization of Iron Ore Fines and Steel Plant Wastes
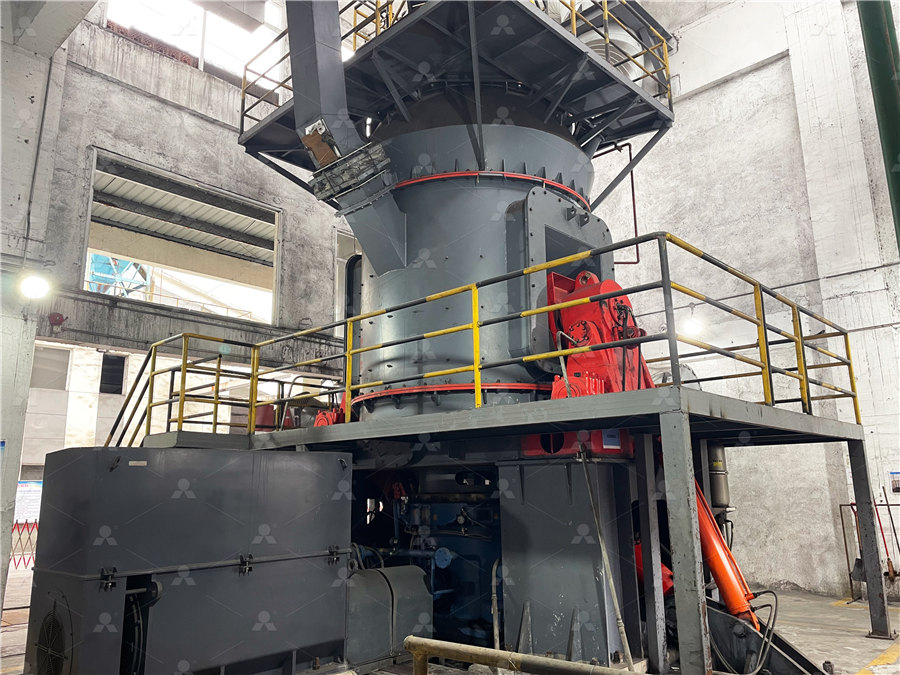
Iron ore quality a potential headwind to green steelmaking
2022年6月28日 Options to address the issue include increased focus on the development of mines that can produce highquality iron ores, further processing of existing ores to improve the grade (beneficiation) and technology solutions that enable the use of lower grade iron ore in DRI processes Steel Sector Decarbonisation Focused on Green Hydrogen2024年3月16日 The sintering process is an intricate system with a protracted process flow The steps in the manufacturing line are primarily composed of the ingredients and mixing process, the sintering operation process, and the treatment of the sintered ore [39, 40]22 Important parameters and characteristics of sintering process As shown in Fig 2, all variables affecting Application of deep learning in iron ore sintering process: a reviewMaking steel Steel is made from iron ore, a compound of iron, oxygen and other minerals that occurs in nature The raw materials for steelmaking are mined and then transformed into steel using two different processes: the blast furnace/basic oxygen furnace route, and Making steel ArcelorMittalŒÎèÑUº E}ÔˆàÏšåB 5vwÍái¤6½\›qD Íž¶— Õ œÎ£þ®ê ¾ ˜ØM:ÁªA” ¤Ë Ÿ™ Š—ræ1ä£ N€o ø iHížë3q ät[0ÓÅ}s¯ Í ]w‡á 9 u BmfF Òº\¶Ÿ Þ[TLÐ s7ÔJ‘„ ÊI¥= ê Š½Úò†ò@T¢ ² »dÜ WËfS‡~£¤*º30£ï{L–flÊ*ÈSX{ ¬òeEð+Î(â¡• c 7âÌQ w b)7i„ Ã"ºy¬Ì 8Ru¿}a,î¼Wô¹O'ÎeJ øô#ì%C$Âö¬ #VXWÏ Glossary American Iron and Steel Institute

COMPARISON OF SINTER AND PELLET USAGE IN
2020年5月13日 Integrated steel plants need to make convenient use of the available iron ore resources to optimize operation slagcoke rates, and the steel plant energy 560 ± 089 and 600 ± 1 2019年9月18日 How steel is made First, the raw materials, either iron ore or scrap iron (depending on the process), are converted into molten steel The orebased process uses a blast furnace or smelter and the scrapbased process Steel production: from iron ore to functional 2012年4月1日 During the processing of steel in steel mills, iron oxides will form on the surface of the metal These oxides, known as mill scale, occur during continuous casting, reheating and hot rolling operations Mill scale is a valuable metallurgical raw material since it contains 65–70% iron JSW Steel Ltd is a 7 Mtpa integrated steel plant and generates 270 t of mill scale per day Recycling of steel plant mill scale via iron ore sintering plantDynamic Tailored Design and Integration Theory of Steel Plants Ruiyu Yin, in Theory and Methods of Metallurgical Process Integration, 2016 53 Design Theory and Methodology for Steel Plants Steel plant design is one of the typical engineering designs As a theoretical concept of engineering design, the steel plant design cannot be limited to the representation of process Steel Plant an overview ScienceDirect Topics
.jpg)
Sintering: A Step Between Mining Iron Ore and Steelmaking
2019年6月11日 The remaining 2% of domestic iron ore was produced for nonsteel end uses Seven openpit iron ore mines (each with associated concentration and pelletizing plants), and three iron metallic plants—one directreduced iron (DRI) plant and two hotbriquetted iron (HBI) plants— operated during the year to supply steelmaking raw materials2017年10月17日 MIDREX claims their technology is used in about 60% of the direct iron reduction plants The overall reduction reactions in a DRI shaft furnace are: Fe 2 O 3 (s) + 3H 2 (g The next step on the road from iron ore mineral to finished steel products is the refining and alloying of hot metal or reduced iron to produce steel alloys From Ore to Iron with Smelting and Direct Iron Reduction2021年12月20日 The project is currently installing a largescale 6 MW PEM electrolysis system at the Voestalpine Linz steel plant (H2FUTURE, 2021) Download Primetals Technologies developed an H 2based DR process to reduce iron ore fines The H 2 used in the process could be green 60–78: 078–168: Coal gasification: 50–70: 056 Hydrogen direct reduction (HDR) in steel industry—An Recycling of steel plant mill scale via iron ore pelletisation process T Umadevi*, M G Sampath Kumar, P C Mahapatra, T Mohan Babu and Madhu Ranjan Mill scale is an iron oxide waste generated during steelmaking, casting and rolling Total generation of mill scale at JSWSL is around 150 t/day and contains 60–70%FeO and 30– 35%Fe2O3Recycling of steel plant mill scale via iron ore sintering plant
.jpg)
(PDF) Technoeconomic Evaluation of Iron Ore Pellet
2012年10月19日 Broadly iron ores may be grouped as: direct shipping ore generally better than 60 per cent iron (Fe), which is mined and used in blast furnaces requiring only simple preparation and beneficiable come from the 30 or so integrated steel plants that produce almost twothirds of Europe's steel THE STATUS QUO The majority of European steel (60%) is made via the primary route It involves processing iron ore to produce iron sinter or pellets, and then melting these in a blast furnace (BF) with coke to make pig iron This is processedThe future of steelmaking Roland Berger2024年3月6日 The actual proportioning of a steel plant indicates that the IMOBWO algorithm applied to the ore proportioning process has good convergence and obtains the uniformly distributed Pareto front Meanwhile, compared with the actual proportioning scheme, the proportioning cost is reduced by 43361 ¥/t, and the TFe content in the mixture is increased by Optimal proportioning of iron ore in sintering process based on 2013年10月22日 To tackle the shortage of iron ore, JSW Steel plans to use lowgrade iron ore dumps, with 46 % Fe content, at its Bellary steel plant This would be the first time an Indian steel company would use such a lowgrade Iron ore pellets as a solution to steel—making raw
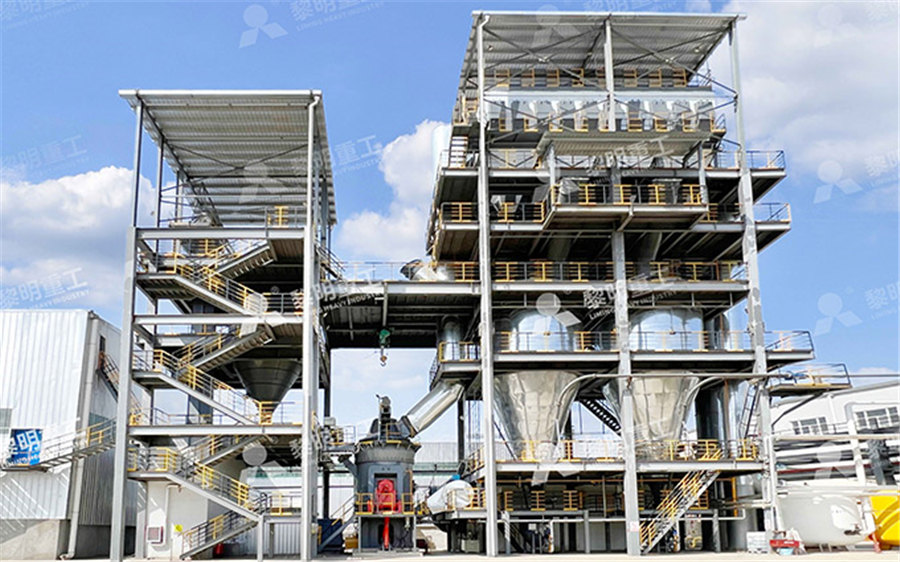
FACT SHEET Steel and raw materials
including iron ore, coal, limestone and recycled steel On average, this route uses 1,400 kg of iron ore, 800 kg of coal, 300 kg of limestone, and 120 kg of recycled steel to produce 1,000 kg of crude steel2 • The electric arc furnace (EAF) route uses primarily recycled steels and direct reduced iron (DRI) or hot metal and electricity On Total Finished Steel 10129 10262 9620 11360 12320 7778 Source: Joint Plant Committee; *Provisional Performance of Steel sector during AprilOctober, FY ’24 has been best ever in AprilOctober of any fiscal year Cumulative production and consumption of steel during AprilOctober of last five financialAN OVERVIEW OF STEEL SECTOR50 RECENT IRON ORE PIPELINES – ONESTEEL WHYALLA OneSteel Limited operate a steel making plant at Whyalla, South Australia The plant has operated for many years using hematite ore from nearby deposits The startup of mining of an associated magnetite deposit can supply the steel plant for another 25 yearsIRON ORE SLURRY PIPELINES – PAST, PRESENT AND FUTURE2017年2月16日 PDF Sintering is a thermal agglomeration process that is applied to a mixture of iron ore fines, recycled ironmaking products, fluxes, slagforming Find, read and cite all the research you (PDF) Iron Ore Sintering: Process ResearchGate
.jpg)
Water usage in steel making: Findings from a worldsteel Water
2010年11月10日 Two of the most critical industries, which use water in vast amounts, are iron ore concentration plants and steel industries Their effluents abound with ferrous compounds and most of the water is 2020年2月24日 The steel industry being highly energy intensive in nature is one the major consumers of energy The iron and steel industry is the largest energy consuming manufacturing sector in the worldA REVIEW ON ENERGY EFFICIENCY OF STEEL PLANTS IN INDIA2024年3月16日 Iron ore is essential in steel making; however, highgrade ores have diminished, making lowgrade ores inevitable These lowgrade iron ores need further beneficiation to upgrade the iron content Currently, traditional physical and chemical methods are utilized and are not environmentally friendly Biobeneficiation techniques have emerged as a sustainable Towards a Sustainable and Enhanced Iron Ore Recovery: Biofrom iron ore12 Recycling to reduce energy use The steel industry uses a high percentage of recycled raw material and most steel production uses recycled scrap steel All the scrap steel that is collected globally is recycled, with a recycling rate of approximately 85% In plants that use electric arc furnaces, up to 100% of the raw materialsWHITE PAPER Energy efficiency