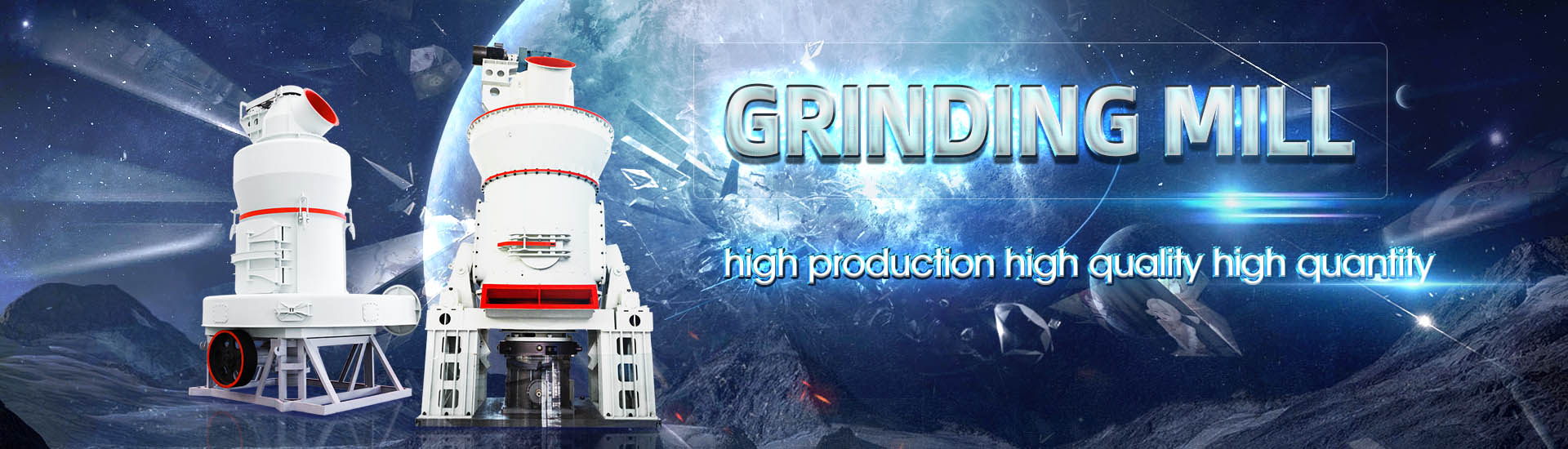
Calculation of cement ball consumption per ton
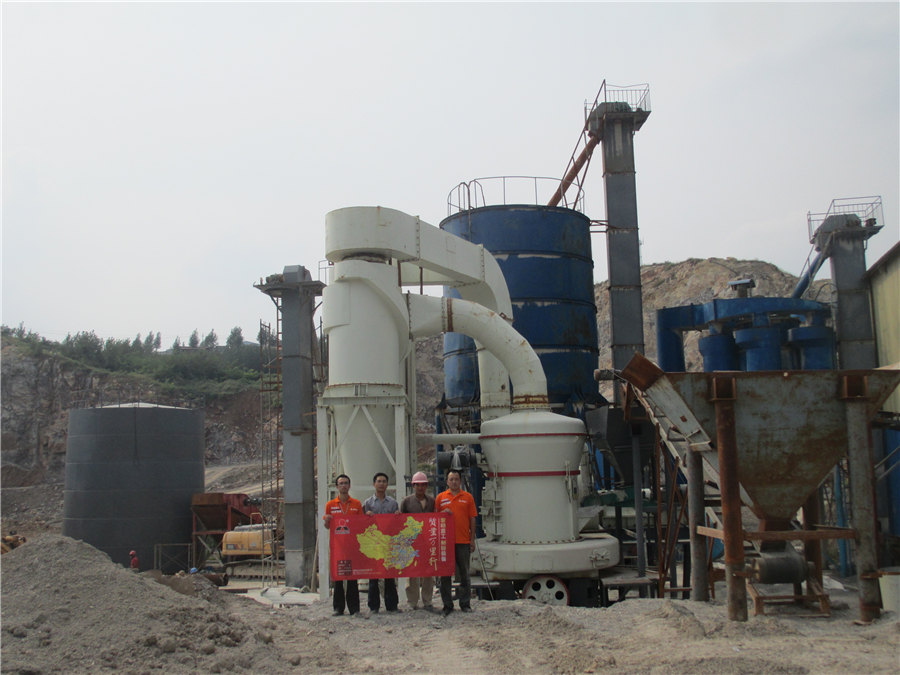
Original Research PaperEnergy and exergy analyses for a cement
2020年5月1日 Cement industry consumes a huge amount of electrical energy that is about 100 kWh/t (kWh per ton (10 3 kg) of cement) [16] In a cement plant, about twothirds of the total electrical energy is used for particle size reduction of raw materials and clinker [17]43 In built Normalization in EPI Calculation 3 431 Product Mix 3 432 Energy Mix 4 433 InputOutput for a typical Cement plant 4 434 Normalisation Factor considered 5 4341 Equivalent Cement Sector Bureau of Energy EfficiencyCement industry is one of the major energy consuming industries and the optimum use of energy is at present important for our national economy The energy cost is the highest component of Optimizing Electrical Energy Consumption In Cement Process Optimization of the Cement Ball Mill Operation Optimization addresses the grinding process, maintenance and product quality The objective is to achieve a more efficient operation and OPTIMIZATION OF CEMENT GRINDING OPERATION IN BALL MILLS
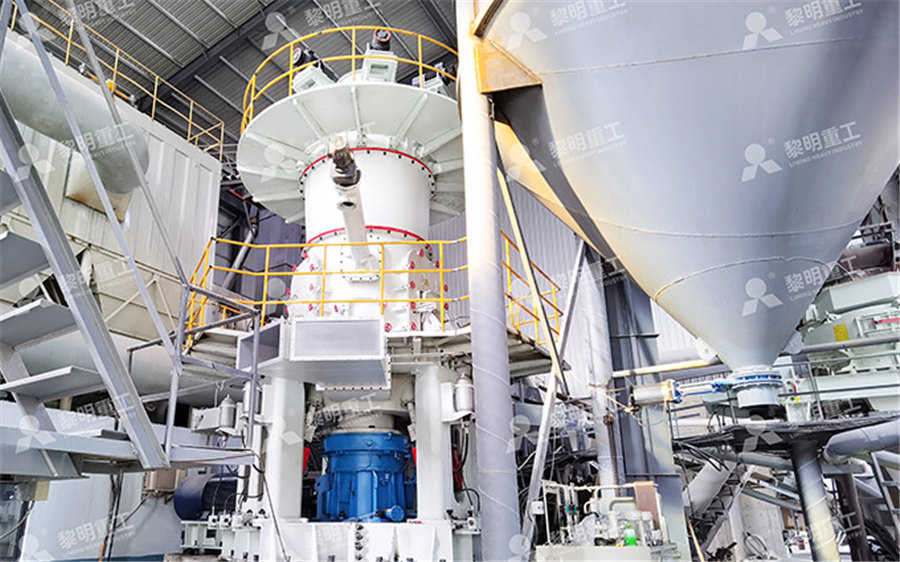
Specific fuel and electricity consumption per ton of
In 2010, the average fuel use was 33 MBtu/ton cement (38 GJ/tonne cement), very slightly higher from that in 2009 (32 MBtu/ton or 38 GJ/tonne)2020年3月1日 General data including annual production capacity, age of the plant, the current electrical and thermal specific energy consumption (ESEC and TSEC), CO2 emission per ton A decision support tool for cement industry to selectThe “Cement Formula Handbook (version 30)” adds to wide array of publications it has made available to important stakeholders in the cement industry Many of these stakeholders CEMENT FORMULAE HANDBOOK Green Business Centre10 Indian cement plants have electrical specific energy consumption less than 70 kWh/MT cement and thermal specific energy consumption less than 690 kCal/kg clinker The best achieved ENERGY BENCHMARKING Green Business Centre
.jpg)
Benchmarking of Energy Consumption and CO2 Emissions in
Key energy and emissions parameters, including thermal and electrical energy intensity, recovered energy and CO2 intensity, are computed per tonne of cement produced along with 2011年5月1日 The typical electrical energy consumption of a modern cement plant is about 110–120 kWh per tonne of cement [19] The main thermal energy is used during the burning A critical review on energy use and savings in the cement industries2024年7月30日 The weight of cement is also automatically calculated using a cement density of 1440 kg/m³ (90 lb/ft³) but you can change this value by entering a new one in the Cement density field of our cement calculator Since you can Cement Calculator2020年7月24日 Determination of granulometrical composition of the clinker by grinding in a ball mill to determine the specific consumption of additional energyDetermination of granulometrical composition of
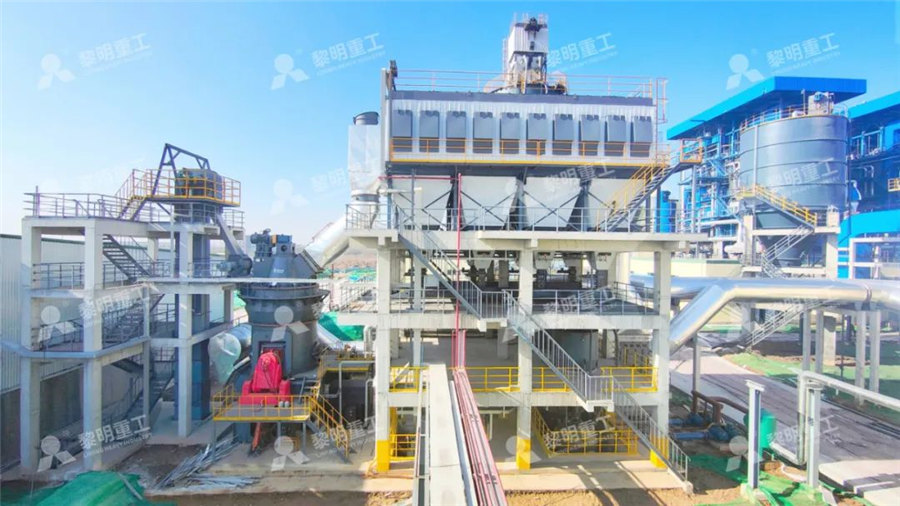
How to calculate no of bricks, cement and sand for
Calculate number of bricks for 1m3 To figure out number of bricks required for 1 cubic meter brickwork, you will need to divide total volume of brickwork by volume of one brick with mortar such as 1m3 ÷ (020 × 010 × 010) m3, 1m3 ÷ than 60 per cent of electrical energy consumption is used for grinding In optimising the process, the grinding tools will have a significant impact on lower production costs as well as maintenance costs Ball mills and grinding tools Cement ball mills BALL MILLS Ball mill optimisation Holzinger Consulting2020年2月26日 Calculation method and its application for energy consumption of ball mills in ceramic industry based on power feature deploymentCalculation method and its application for energy consumption of ball Then, if you need to calculate the cost of sand and cement, check the box "Calculate cost" and enter the prices per unit of the goods in the fields: The price of 1 bag of cement; The price of sand per 1 ton Click the "CALCULATE" button to get the final calculation This way, you can accurately find out how much material you need and their costCement Mortar Calculator Online Calculation of Cement and
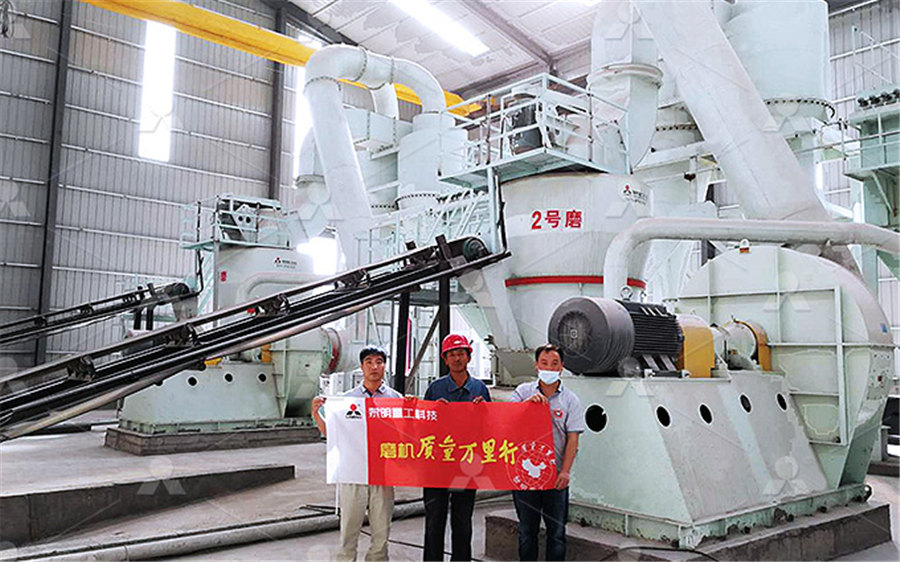
A preliminary calculation of cement carbon dioxide in China
2019年2月21日 The changes in the energy consumption in China’s cement production are also inseparable from the development history of cement kiln Figure 2 shows the energy consumption of different types of kilns Since the 1950s, given the global energy shortage, the NSP kiln can rapidly occupy a place owing to its low energy consumption and high productivity compared 2016年4月25日 In cement industry about 110 kWh of electrical energy is consumed to produce one ton of cement and about 26% of the total electrical power is used during farine productionDetermination of correlation between specific energy consumption consumption and low production The consumption of energy by the cement grinding operation amounts to one third of the total electrical energy used for the production of cement The optimization of this process would yield substantial benefits in terms of energy savings and capacity increase Optimization of the Cement Ball Mill OperationOPTIMIZATION OF CEMENT GRINDING OPERATION IN BALL MILLS2023年4月23日 the grinding media reduces energy and material consumption in a ball mill Different performances are achieved when different sizes and shapes of grinding media are used [ 12 ](PDF) Grinding Media in Ball MillsA Review ResearchGate
.jpg)
Binding wire required for 1 ton Steel as per IS code
Binding wire consumption per ton as per IS code As per IS code, 9 to 13 kg of binding wire are required per ton (1000 kg) of steel Typically, 1 ton of 8mm steel bar requires 12kg binding wire, 1 ton of 816mm steel bar requires 1213kg, 1 ton of 1632mm steel bar requires 79kg and 1 ton of 28mm steel bar or 32mm steel bar requires 7kg2014年5月1日 of 27178 MJ per ton of clinker production It is recognized that the anzast layer has an important role for durability of the refractory bricks and heat transfer out of the kilnAnalysis of the parameters affecting energy As per IS456:2000, M10 Grade concrete proportion is = 1 : 3 : 6 Remember, here (1:3:6) indicates: 1 for cement 3 for sand 6 for aggregate Total volume (cement + sand + aggregate) = 1 + 3 + 6= 10 Calculation of Volume of Calculation of Cement, Sand and Aggregate for M Plastering work can be one way to enhance the splendour of your housePlastering done over interior as well as exterior makes it even and smooth which can add strength to the walls and ceiling along with increasing the attractiveness of the homeThese can be used for both constructions of new buildings and restoration of age old buildingsThis old buildings can Plastering Plaster Volume Calculator Calculation of Materials
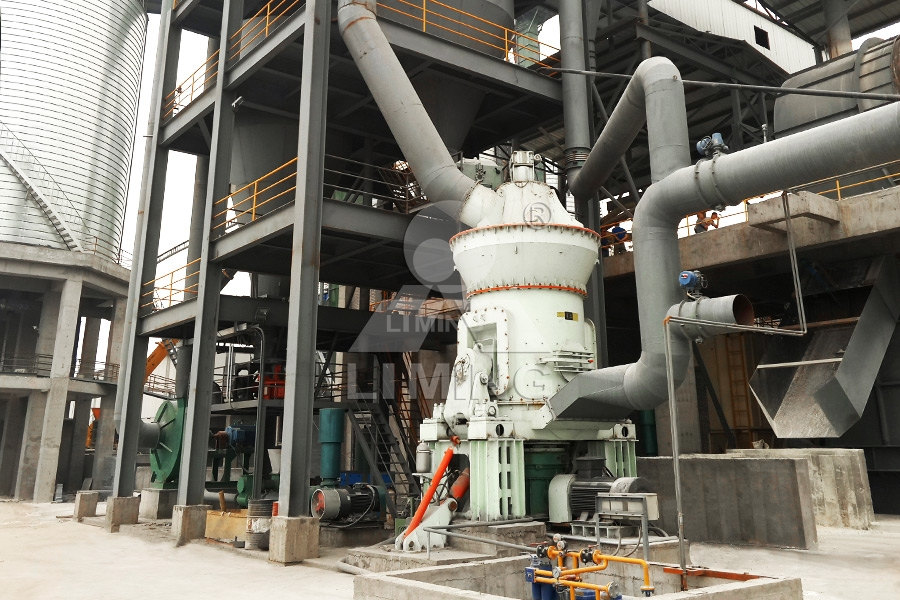
Deterministic Approach for Calculation of Carbon Footprint for Cement
2021年2月28日 08195 ton of CO 2 is emitted per ton of cement production Limitations The import and export of clinker and other r aw materials have not been considered2020年9月14日 Power consumption per ton of clinker with a conversion ratio for consumption 155 : 1 = 174 x 155 = 27 kWh/ton; Using 4% gypsum – 1 ton clinker = 104 tons of cement; Therefore power consumption per ton of cement = ~260 kWh; In this manner list all sections of the plant See Table 4 Table 4 – Power consumption for whole plantThe essentials of electrical systems in cement plants EEP1970 and 2010, primary physical energy intensity for cement production dropped 12% per year from 73 MBtu/short ton to 45 MBtu/short ton Carbon dioxide intensity due to fuel consumption and raw material calcination dropped 24%, from 610 lb C/ton of cement (031 tC/tonne) to 469 lb C/ton cement (023 tC/tonne)Energy Efficiency Improvement and Cost Saving Opportunities for Cement Assuming bulk densities of materials per cubic meter, cubic feet and cubic yards as follows: Cement = 1500 kg/m3 = 93642 lb/ft3 = 2528332 lb/cubic yards Sand = 1700 kg/m3 = 105 lb/ft3 = 2865443 lb/cubic yards Coarse aggregates = 1650 kg/m3 = 103 lb/ft3 = 2781166 lb/cubic yards Specific gravities of concrete materials are as follows: Cement = 315 Sand = 26 Coarse Calculate Quantities of Materials for Concrete Cement, Sand
.jpg)
A comparison of wear rates of ball mill grinding media
2016年1月1日 The wear of balls used during a grinding process is considered one of the losses that cause an increase in the operating cost allocated to the ball mill [21]2019年11月18日 Globally, approximately 44 billion metric tons of ordinary Portland cement (OPC) are produced annually, emitting 085092 tons of carbon dioxide per ton of OPC manufactured (Argalis et al, 2022 Study of Energy Use and CO2 Emissions in the ResearchGateThe Power Consumption Calculation of a Ball Drum Mill Vasily Stepanovich Bogdanov, Sergey Igorevich Antsiferov and Nikita Eduardovich Bogdanov Belgorod State Technological University named after VG Shukhov, 46 Kostukova str Belgorod Russia Abstract: Ball drum mills area commonplace in grinding offerrous and nonferrous metals, and a cementThe Power Consumption Calculation of a Ball Drum MillStrength of PCC is defined as compressive strength after 28 days, expressed as M15, M20, where M stands for Mix and 15 stands for 15 N/mm 2 (n/mm 2 must be read as 'Newton’s per millimeter Cubic') compressive strength at 28 days Cement Concrete Calculator PCC Calculator RCC
.jpg)
Common Basic Formulas for Mineral Processing
2016年3月21日 Reagent Consumption Calculations LiquidSolid Relationships Specific Gravity Volume Original feed may be applied at the ball mill or the primary classifier T—Tons of original feed Formulas for calculating reagent 10 Indian cement plants have electrical specific energy consumption less than 70 kWh/MT cement and thermal specific energy consumption less than 690 kCal/kg clinker The best achieved energy consumption by an Indian cement plant is 561 kWh/MT ENERGY BENCHMARKING Green Business Centre4341 Equivalent major grade of cement production 5 4342 Calculation for Gate to Gate Specific Energy Consumption (SEC) 6 44 Methodology (Summary) 7 5 Target Setting in Cement Plants 7 51 Grouping of Cement plants 7 52 Energy Consumption Range 8 53 Example: Normalised Baseline parameters and Target for PPC 8Cement Sector Bureau of Energy EfficiencyConcrete Calculator Our online tools will provide quick answers to your calculation and conversion needs On this page, you can calculate material consumption viz, cement, sand, stone gravel for the following concrete mix ratios 1:15:3, 1:2:4, 1:3:6, 1:4:8, 1:5:10Concrete Calculator Estimate Cement, Sand, Gravel Quantity
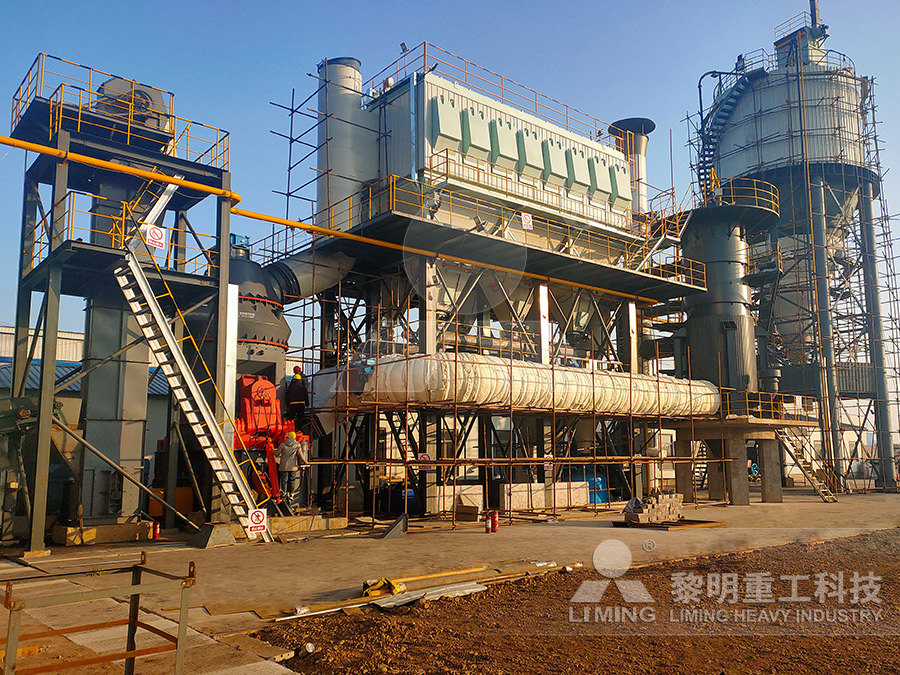
Thermal energy consumption and its conservation for a cement
2020年6月24日 The manufacturing process of cement is very complex consisting of the raw materials of varying properties, several methods for the pyroprocessing and different variety of resources Approximately, the process needs 32–63 GJ amount of energy and near about 17 tons of raw materials (mainly limestone) per ton of the clinker generated CEMENT PLANT FORMULAE NORMS CAPTIVE POWER PLANT REFERENCE DATA Chapter No Title Page No 1 Quality Control Formulae 2 2 Formulae used in Combustion Calculations 6 3 Flame Momentum Calculation 8 4 Kiln Performance Efficiency 11 5 Heat Transfer 13 6 Economic Insulation Thickness 14 7 Physical Chemistry 17CEMENT FORMULAE HANDBOOK Green Business Centre2 per ton of cement in 1949, and declined to 73701 kg CO 2 per ton of cement in 2015 Furthermore, it is likely that China’s cement output is about 161750 Mt in 2050 Meanwhile, China’s CCEF is about 57602 kg CO 2 per ton of cement which based on likely realistic scenario (LRS), and CO 2 emissions are about 93171 Mt inA preliminary calculation of cement carbon dioxide in ChinaStrength of RCC is defined as compressive strength after 28 days, expressed as M15, M20, where M stands for Mix and 15 stands for 15 N/mm 2 (n/mm 2 must be read as 'Newton’s per millimeter Cubed) compressive strength at 28 days The proportions of materials (cement, sand, coarse aggregate) for nominal mix/design mix concrete that are normally used are 1:3:6 or 1:4:8Cement Concrete Calculator PCC Calculator RCC Calculator
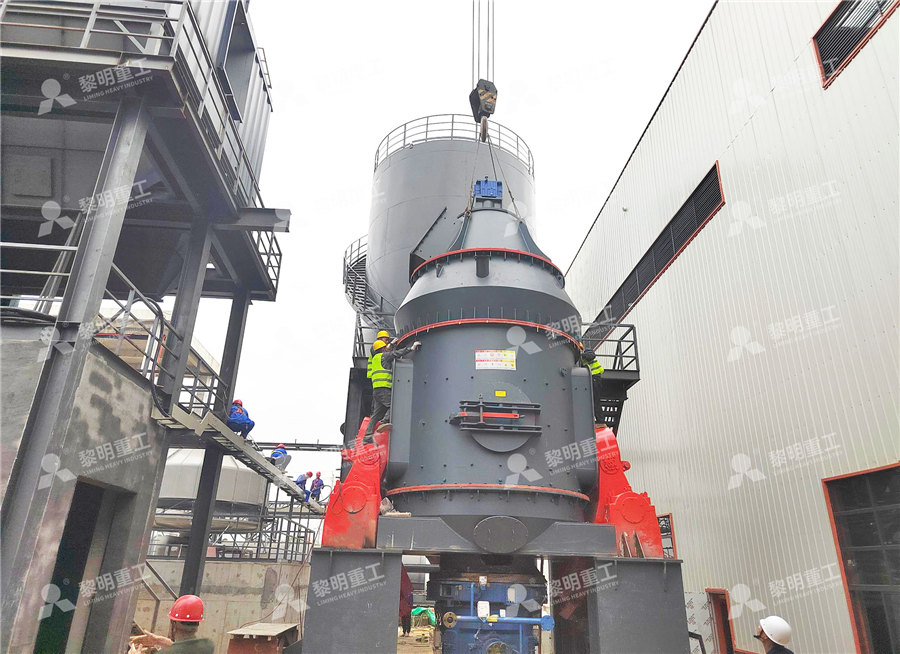
12 MM CEMENT PLASTER CALCULATOR Civil
2023年8月12日 12 MM CEMENT PLASTER CALCULATOR Plaster Area Calculation PlasterArea = Length × Width Plaster Area = 10×10 Plaster Area = 10000 m2 Material Calculation Volume of Mortar = Area of Plaster x Calculation Of Materials For Different Mix Ratio Quantity estimation of building materials is essentially required in any construction work and the quantity of materials depends on the mix proportions of the concrete In our previous How To Calculate Quantities Of Materials For 2022年5月9日 Modeling of energy consumption factors for an industrial cement vertical roller mill by SHAPXGBoost: a "conscious lab" approachModeling of energy consumption factors for an industrial cement 2019年3月8日 use and now account for over 90 percent of cement consumption worldwide reduced the energy consumption by 036 kWh per ton of on the age and performance of the existing ball millIMPROVING THERMAL AND ELECTRIC ENERGY EFFICIENCY AT CEMENT
.jpg)
Rate Analysis of Reinforcement Cement Concrete (RCC): Detailed
2024年7月24日 Unless otherwise stated, all work shall be measured net in the decimal system as fixed in its place as given in below point no 1 to below point no 3Any work is done extra over the specified dimensions shall be ignored Dimensions shall be measured to the nearest 001 m except for the thickness of slab which shall be measured to nearest 0005 m,The online floor screed calculator will help calculate the cement, sand, readymix for 1 m2, Sand price per ton B4 Invalid input Price per m³ of mortar M3 Invalid input To calculate the screed consumption per m2, use our screed calculation calculator The usual (standard) composition of the screed is a cementsand mixture, in other Floor Screed Calculator Online Consumption Calculation per 1m2Higher SO3 in clinker results in a reduction in grindability and increases specific power consumption per ton Also, increasing SO3 (above Composite cement equivalent OPC fineness calculation: When composite cements are ground the fineness according to Blaine is not anymore as reliable as with OPC Ball charge calculation: Everything you need to know about clinker/cement Grindingonline live calculators for grinding calculations, Ball mill, tube mill, critical speed, Degree of filling balls, Arm of gravity, mill net and gross power Optimization Online Trainingball mill calculations, grinding media filling degree, ball size, mill
.jpg)
Cement Plant Grinding Mills Power Consumption
2020年3月14日 The first step in this procedure is to calculate from the following formula the work index, which is the kwhr required to grind one short ton of material from a theoretically infinite size to 80 pct passing 100 microns: where Wi = the work index Gbp = Bond ball mill grindability Pi = micron size of the mesh of grind For 200 mesh, Pi = 74 2021年5月3日 Cement clinkerisation is the major energyconsuming process in cement manufacturing due to the hightemperature requirement In this paper, energy data including specific energy consumption, forms, and types of energy used at different units of cement manufacturing processes were analyzed and compared for effectiveness, availability, cost, Energy and Economic Comparison of Different Fuels in Cement