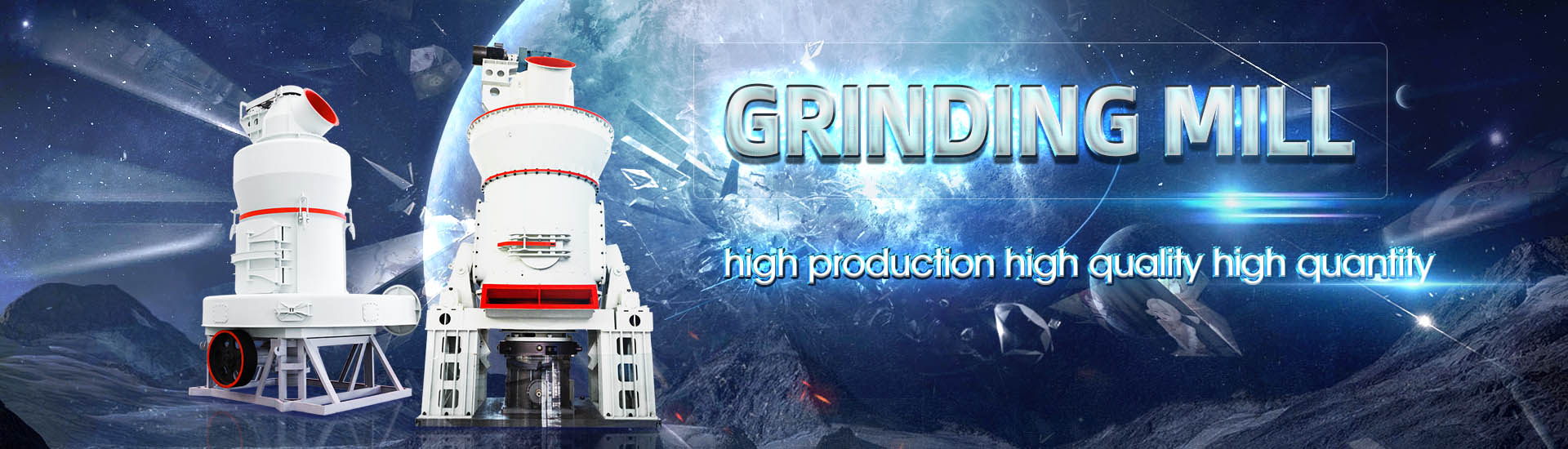
The working pressure of the ore grinding mill is approximately
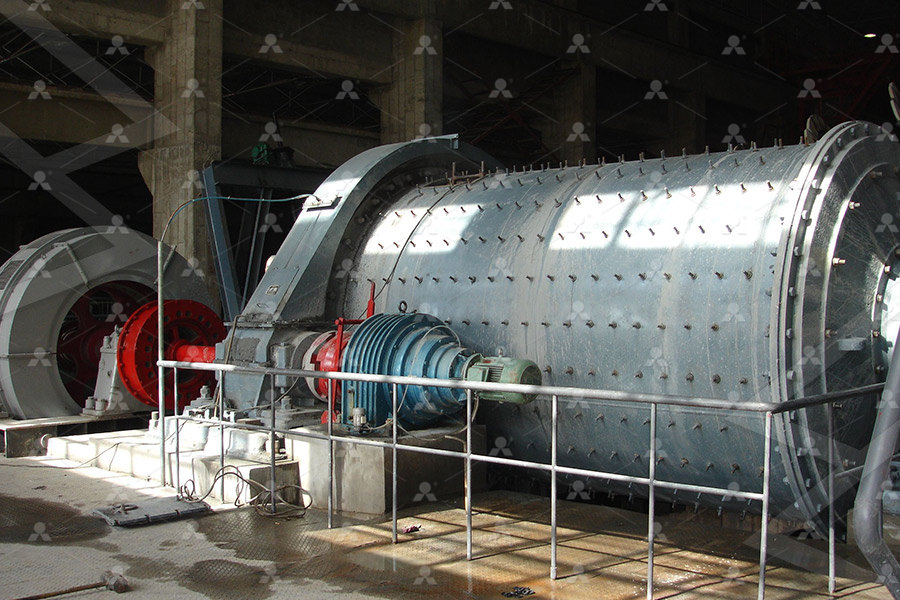
ReviewStirred media mills in the mining industry: Material
2020年6月1日 Stirred media mills are used by the mining industry for ultrafine grinding to enhance liberation, and to decrease particle sizes of industrial minerals to tailor functional properties2017年4月1日 Working pressure is normalized with classifier rotor speed Vertical roller mills (VRM) have found applications mostly in cement grinding operations where they were used in Operational parameters affecting the vertical roller mill 2023年7月20日 Moist grinding, a special grinding method, is used to prepare pellets for smelting According to the grinding medium features, ore grinding is mainly classified into ball grinding Ore Grinding SpringerLinkGrinding can be achieved by several mechanisms, including: impact or compression due to sudden forces applied almost normally to the particle surface; chipping or attrition due to Grinding Mill an overview ScienceDirect Topics
.jpg)
Energy Use of Fine Grinding in Mineral Processing
2013年12月18日 Fine grinding, to P80 sizes as low as 7 μ m, is becoming increasingly important as mines treat ores with smaller liberation sizes This grinding is typically done using stirred mills such as the Isamill or Stirred The comminution process of High Pressure Grinding Rolls (HPGR) was discovered in the 1980s by the research work of the German Professor Schönert Its main advantage is the high Quantification of HPGR energy efficiency effects on downstream Nowadays, conducting grindability tests requiring only a few kilos of material on several samples, is a more typical approach to grinding mill design This paper summarises the requirements SAG Mill Testing Test Procedures to Characterize Ore GrindabilityConventional primary grinding technology uses a semi or fully autogenous mill and the accepted small scale test to determine the specific energy requirement is the SAG Power Index, SPI Work Index Determination for High Pressure Grinding Rolls SGS
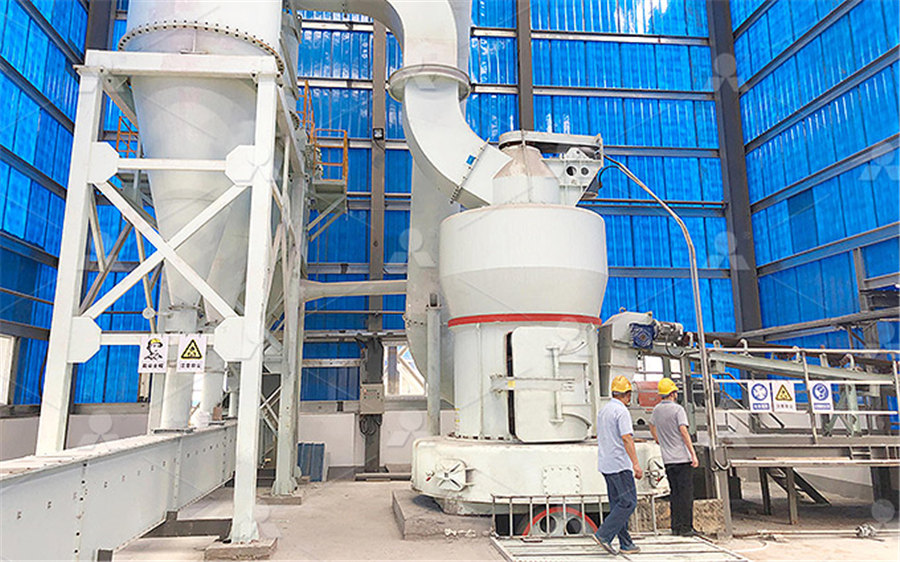
Ore Grindability SpringerLink
2023年7月19日 Ore grindability is mainly used to calculate and select the specifications, models, processing capacity, and number of grinding mills, and to determine whether the grinding mills Estimating the power required by a grinding mill is then particularly interesting for industrial looking to invest in a new grinding process in order to define the CAPEX and OPEX costs The Grinding power : step by step calculation PowderProcess2015年3月15日 For the grinding tests, a Loesche mill LM45 (table diameter 045 m) is used (Fig 2a) This pilot scale mill is a special development for ore grinding, which is reflected by several features The mill has four rollers, which are able to stress the particle bed with grinding pressures of up to 5000 kN/m 2Research of iron ore grinding in a verticalrollermill2022年3月16日 21 Experimental Design The experimental planning with selected key factor like operating gap (X 1), applied load (X 2) and roll speed (X 3) was designed by CCD method to obtain the optimum conditions for grinding the BHQ iron ore in HPGRA full secondorder polynomial model was obtained by regression analysis for three factors by using the Design Potential of HighPressure Grinding Roll (HPGR) for Size
.jpg)
Grinding in an air classifier mill Part I: Characterisation of the
2011年7月1日 Request PDF Grinding in an air classifier mill Part I: Characterisation of the onephase flow In this and the related second paper [1], we present an indepth study of the twophase flow and 2020年10月18日 Concentrates with different morphologies were prepared using highpressure grinding rolls (HPGR) and ball mill (BM) grinding techniques Then pelletizing and induration process is done in the The effects of iron ore concentrate grinding methods (HPGR and 2020年1月16日 This could be achieved through closer monitoring of the primary crusher performance and proper control of the ratios for the SAG mill feeders drawing the ore from the stockpile The ball mill (PDF) Optimization and performance of grinding circuits: the Grinding in an air classifier mill — Part I: Characterisation of the onephase flow For the studies in the mill a thin sheet of light, approximately 05–1 mm thick, has been produced with a dualNd: The pressure loss in the mill is mostly caused by the rotation of the impeller wheel classifier(PDF) Grinding in an air classifier mill Academia
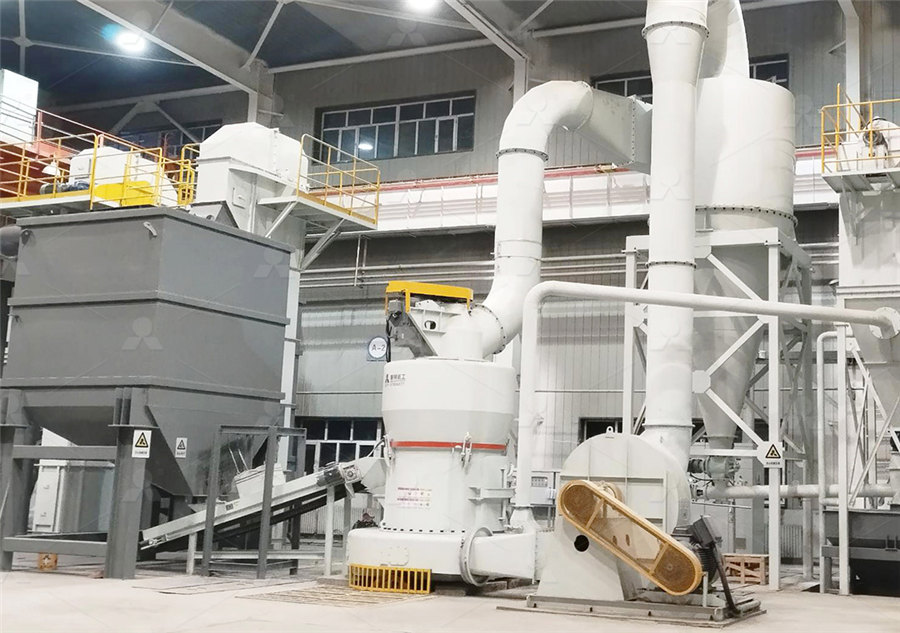
Grinding Mills — Types, Working Principle Applications
2018年8月17日 Rod mills can accept feed up to approximately 50 mm mill load, grinding media, ore types, Trommels — Working Principle, Components, 2015年3月15日 The grinding parts of a Loesche mill (Fig 1) are a rotating table (1) with a horizontal grinding track and rollers (2), which are pressed onto the table by lever arms and a hydro pneumatic spring systemBetween the working surfaces of track and rollers, particle bed comminution takes place A dynamic air separator (3) is located above the grinding chamber, Research of iron ore grinding in a verticalrollermillRequest PDF On Mar 15, 2015, Mathis Reichert and others published Research of iron ore grinding in a verticalrollermill Find, read and cite all the research you need on ResearchGateResearch of iron ore grinding in a verticalrollermillThe results of the analyses clearly shows that using a sieve of +180µm and its bottom 180µm, the best time for grinding 05kg of Itakpe iron ore with 3kg of grinding media and a mill speed of 92 rpm is 8 minutes, yielding 1710% fines and 8290% coarse, 08 mill critical speed measured 1520% fines and 8480% coarse(PDF) Study of Iron Ore Mixtures Behavior in the Grinding
.jpg)
Predicting the overall specific energy requirement
2009年5月1日 High Pressure Grinding Rolls (HPGR) circuits have the potential to reduce these emissions by up to 328 Megatonnes/year, or 443% when compared to the Semiautogenous/ball mill circuit alternativesOne reason is the dry inbed grinding principle Results of extensive test works with two types of magnetite iron ores in a Loesche VRM are presented here Within these test works, mill parameters like grinding pressure, separator speed and dam ring height were varied, following a factorial design of the experimentsResearch of iron ore grinding in a verticalrollermill2020年8月12日 efficiency of vertical roller coal mill currently working in coal feed, grinding pressure, Jorgensen 2005;Wang et al 2009, Ghalandari et al 2021), coal (Tontu 2020), iron ore An investigation of performance characteristics and 2024年4月26日 These mills utilize the ore itself as the grinding media, reducing the need for additional grinding media AG/SAG mills are typically used for coarse grinding, where large pieces of ore are efficiently broken down The grinding process reduces the ore size, which enhances the efficiency of subsequent beneficiation processes by increasing the Iron Ore Processing: From Extraction to Manufacturing

Tower Mill Operating Work Index 911Metallurgist
2016年6月3日 The principal method of grinding in a Tower mill is attrition (scrubbing of particles off material being ground), with the possibility of some shearing and 911 Metallurgist is a trusted resource for practical insights, solutions, and support in mineral processing engineering, helping industry professionals succeed with proven expertise Tower Mill Operating Work Index2023年1月1日 This paper presents the commercial implementation of a novel comminution circuit with high pressure grinding rolls (HPGR) followed by tower mill in a copper–lead–zinc ore dressing plant With a throughput of 650 t/d, the comminution circuit comprises three stages of crushing by a jaw crusher, cone crusher, and HPGR as primary, secondary, and tertiary Evaluating the performance of an industrialscale high pressure The rod mill is a kind of equipment for grinding ore the rod mill is especially suitable The rod mill is a kind of equipment for grinding ore According to different working conditions, the rod mill performs different grinding tasks Highpressure Ball Press Machine; Industries Mining Minerals; Cement;The Working Principle and Advantages of the Rod Mill2009年1月1日 Also, equipment like ball mill is used at the final stages of grinding Among the comminution and grinding equipment, HPGR is increasingly utilized as tertiary crusher or primary mill because of Processing of Magnetite Iron Ores–Comparing Grinding Options
.jpg)
Regrind of metallic ores with vertical mills: An overview of the
2014年10月20日 The results indicated that coarse compact itabirite ore (pebbles) can be used as grinding media Grinding tests have shown that replacing 25% of the steel balls with pebbles offered promising results2018年8月8日 To enable milling, working chamber is filled with grinding media in approximately 20% of its volume Physical parameters of the grinding media depend on the mill diameter and the feed particle size distribution The most common size is 1–3 mm diameter and 10–15 mm lengthGrinding Kinetics Adjustment of Copper Ore Grinding in an1 Grindability: The grindability of the ore affects the efficiency of the grinding mill Harder ores require more energy and longer grinding times, which can impact the mill's performance and operational costs 2 Media andliner Wear: The condition of the grinding media and liners affects the mill's efficiencyUnderstanding the operation of grinding mills in the mining and The suspending gas which may be compressed air or superheated steam, admitted through nozzles at a pressure of 7 atm In the mill the grinding chamber is an oval loop of pipe 25 to 200 mm in diameter and 12 to 24 m high Feed Size Reduction1: Grinding – Unit Operations in Food

(PDF) LEARNING FROM OTHER INDUSTRIES; WHY THE
2019年4月16日 Conference: Applying a Successful Technology from the Cement Industry: Advantages of Grinding Ore in a VerticalRollerMill; At: Antalya, Türkey2016年1月1日 The highpressure grinding roll (HPGR) is a type of roller mill that continuously produces particlebed comminution Since the capacity of the HPGR is determined by not only operating conditions Influence of type of lining in highpressure grinding rolls on Find your highpressure mill easily amongst the 16 products from the leading brands High Pressure Grinding Mill, also called High coal grinding highpressure Contact roller mill YGM Output: 400 kg/h 22,000 kg/h Detailed:The Highpressure Suspension Mill has the same working principle as Raymond Mill, but its grinding fitting Highpressure mill, Highpressure grinding mill All industrial 2014年1月20日 High pressure grinding rolls in AG/SAG mill circuits the next step in the evolution of grinding plants for the new millennium SAG 2001, Conference, Vancouver, BC 2001 Vol(PDF) Effects of High Pressure ORE Grinding on the Efficiency of
.jpg)
The working principle of ultrafine Raymond mill
2022年6月15日 The ore raw materials with suitable particle size are fed into the HCQ ultrafine Raymond mill main machine through the feeding mechanism (vibration/belt/screw feeder or air lock feeder, etc); the highspeed rotating grinding rollers are tightly rolled under the action of centrifugal force2018年3月29日 Comparison of dry and wet grinding process in an electromagnetic mill is presented in this paper The research was conducted in a batch copper ore grinding Batch mode allows for precise parametrization and constant repetitive conditions of the experiments The following key aspects were tested: processing time, feed size, size of the grinding media, Comparison of Wet and Dry Grinding in Electromagnetic Mill MDPI2017年2月20日 All Grinding Mill Ball Mill Manufacturers understand the object of the grinding process is a mechanical reduction in size of crushable When choosing primary autogenous grinding, run of mine ore up to 200300 mm in size is fed to the mill Maximum mill efficiency is reached at a charge volume of approximately 55%, Grinding Mill Design Ball Mill Manufacturer 911MetallurgistWhen the machine is working, the grinding roller of the highpressure roller mill rotates around the main shaft, and rolls close to the grinding ring under the action of the highpressure spring and centrifugal force, and its rolling pressure is 12 times higher than that of the Raymond pulverizer under the same power conditions, so The output of the high pressure pulverizer is greatly YGM High Pressure Grinding Mill
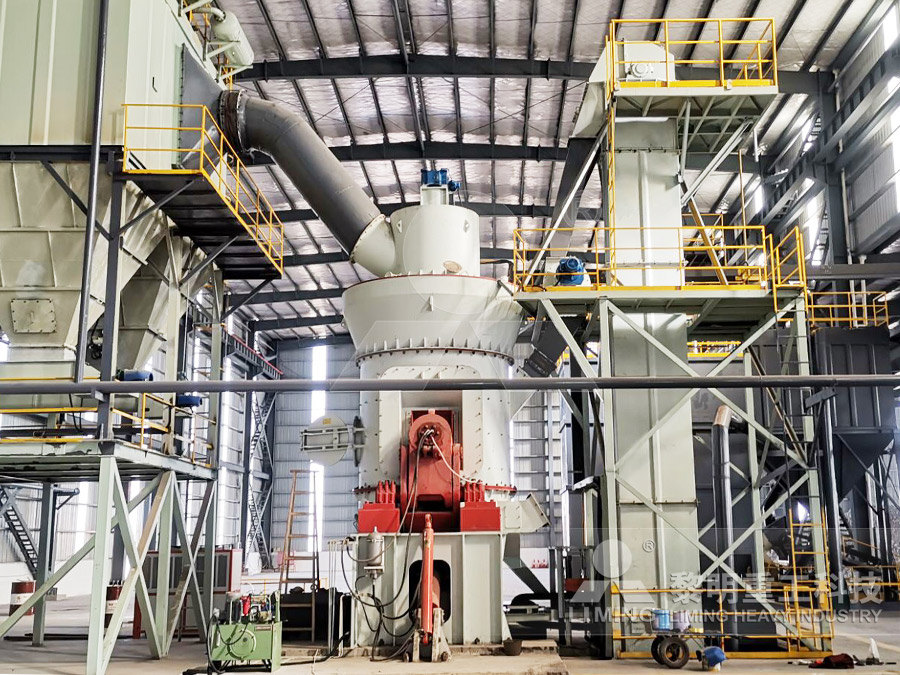
Grinding Mill an overview ScienceDirect Topics
An hydrocyclone is to be installed in a closed circuit grinding circuit with a mill discharge containing 30% solids by volume The solid density is 2800 kg/m 3 and the density of water is 1000 kg/m 3 Given that the maximum pressure deferential between the inlet and overflow was 50 kPa and the throughput from the mill was 800 t/h, estimate:11998年1月1日 The high pressure roll mill, HPRM, a newly invented size reduction equipment, has been recently added to the list of comminution machines and is classified as a highly efficient equipment(PDF) THE PERFORMANCE OF THE HIGH PRESSURE The working principle of a ball mill is based on the impact and attrition between the balls and the grinding media As the mill rotates, the grinding media (usually steel or ceramic balls) are lifted to a certain height and then allowed to fall Ball Mill Grinding Machines: Working Principle, Types, 2015年10月23日 In this chapter an introduction of widely applied energyefficient grinding technologies in cement grinding and description of the operating principles of the related equipments and comparisons over each other in terms of grinding efficiency, specific energy consumption, production capacity and cement quality are given A case study performed on a EnergyEfficient Technologies in Cement Grinding IntechOpen
.jpg)
Modeling and application of stirred mill for the coarse grinding
2022年5月23日 Grinding experiments were conducted in a laboratoryscale stirred mill on a lowgrade PGE bearing chromite ore HighPressure Grinding Rolls (HPGR) product of −1 mm was used as feed material to 2010年1月1日 Three major PGM ore types from the Bushveld Complex of South Africa: Merensky, UG2 and Platreef were comminuted with the use of the high pressure grinding rolls (HPGR)Effects of high pressure grinding rolls on platinumbearing ores The paper presents the advanced control systems installed by the authors in two gold ore grinding circuits in South Africa, Fig 1 illustrates the obvious reduction in the average % +150 lm in the mill product from approximately 11% >150 lm Cyclone pressure Mill power Mill mass based on bearing pressures Product particle size on Advanced control of gold ore grinding plants in South Africa2003年8月1日 Highpressure roller presses are highly effective machines for comminution In 20 years, their application has spread worldwide for grinding cement clinker, ore and a range of mineralsForce distribution in the working gap of highpressure roller
.jpg)
Understanding the SAG Mill in Copper Ore Mining Process
The Autogenous Mill, also known as AG Mill, is a type of grinding mill used in the mining industry This machine uses ore and rock itself as grinding media to perform its job Unlike other types of mills that use steel balls or rods for grinding materials, the Autogenous Mill relies on the material being ground to break itself into smaller pieces2015年7月29日 As you increase the volume of the through put, the time that the ore has to react to the grinding media is lessened As you add ore to the mill you are also adding WATER and changing density which affects the slurry rheology and workings of the grinding action inside that mill This water is one of the main controls that you have over your grindEffect of Water Density on Grinding Mill 911Metallurgist