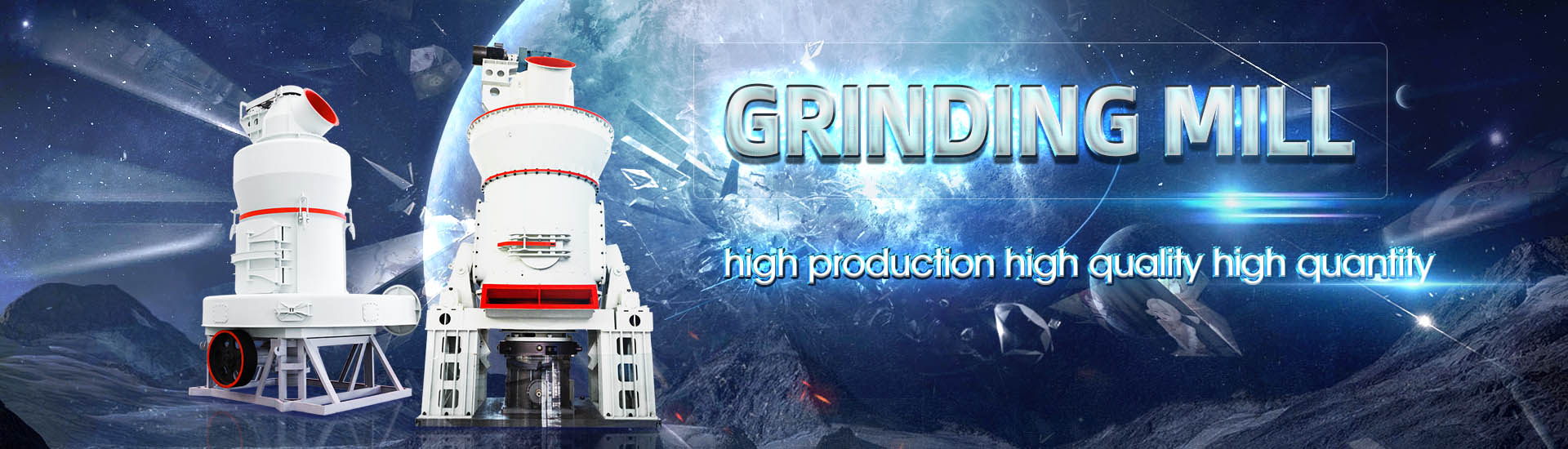
Cement plant raw material grinding process flow chart
.jpg)
Cement manufacturing process PPT Free Download
2014年6月10日 This document discusses Portland cement and the cement manufacturing process It begins with an overview of what cement is and how it is used to make concrete It then describes the industrial process for The whole process of cement manufacturing in Messebo Cement plant which consists of two separate Cement Production lines can be summarized into the following processes ;as can be CEMENT PRODUCTION AND QUALITY CONTROL A Cement Process flow diagram for the cement manufacturing process, showing electricity and heat consumption or inputs [39] The paper presented herein investigates the effects ofProcess flow diagram for the cement manufacturing Vertical roller mills are adopted in 20 cement plants (44 mills) in Japan In the vertical roller mill which is widely used in the raw material grinding process, raw materials input grinding table Vertical roller mill for raw Application p rocess materials
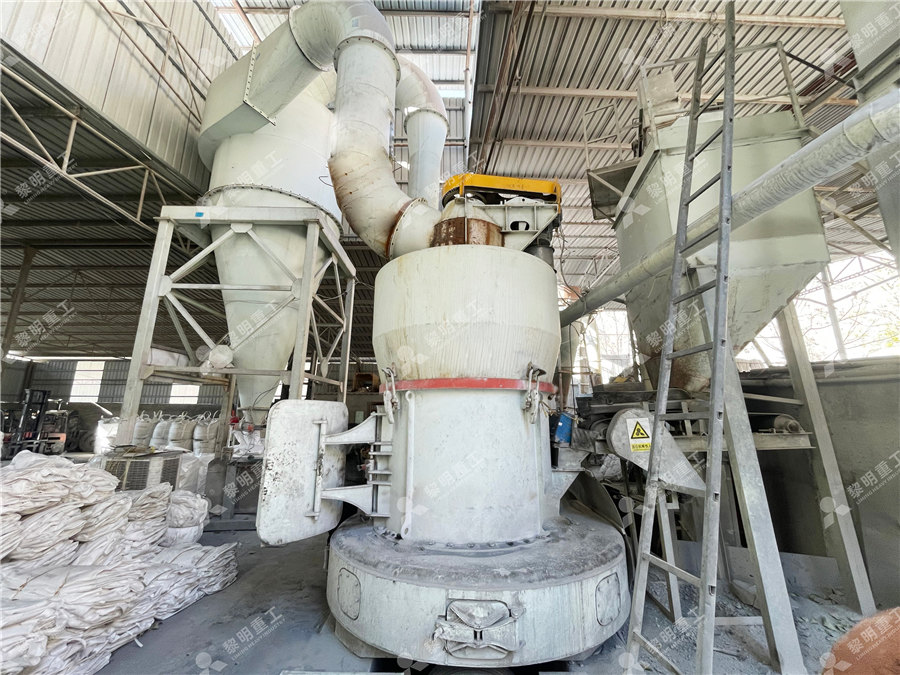
Cement Manufacturing Process Engineering Intro
2012年8月30日 Cement Manufacturing Process Phase II: Proportioning, Blending Grinding The raw materials from quarry are now routed in plant laboratory where, they are analyzed and proper proportioning of limestone raw materials, burning, grinding and quality control are supported by a range of chapters addressing critial topics such as maintenance and plant reporting, alongside a detailed The Cement Plant Operations Handbook International Cement The initial production step in portland cement manufacturing is raw materials acquisition Calcium, the element of highest concentration in portland cement, is obtained from a variety of 116 Portland Cement Manufacturing US Environmental together in a raw mill to a particle size of 90 micrometres, producing “kiln feed” Cement Plant: The Manufacturing Process worldcementassociation 1 Limestone (CaCO3) is taken from a Cement Plant: The Manufacturing Process 4 5 World Cement
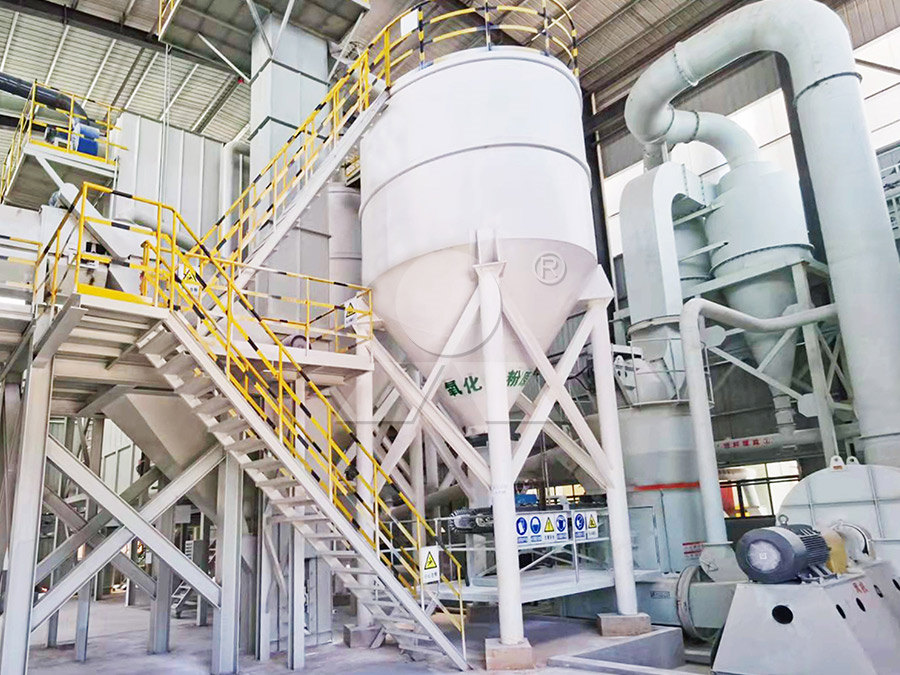
The Cement Manufacturing Process Thermo Fisher
2023年12月20日 Cement manufacturing is a complex process that begins with mining and then grinding raw materials that include limestone and clay, to a fine powder, called raw meal, which is then heated to a sintering temperature as 2019年11月30日 Flow chart for manufacturing of cement In dry process The raw materials are first reduced in size of about 25mm in crushers and Crushed material is ground to get fine particles into ball mill or tube mill Significant Manufacture Of Portland Cement Process Flow Download scientific diagram Process flow diagram for the cement manufacturing process, showing electricity and heat consumption or inputs [39] from publication: Energy Savings Associated with Process flow diagram for the cement Wet Process Of Cement Manufacturing With Flow Chart The raw materials are calcareous materials, like limestone or chalk, and argillaceous material such as shale or clay Skip to content CiviconceptsWet Process Of Cement Manufacturing With Flow
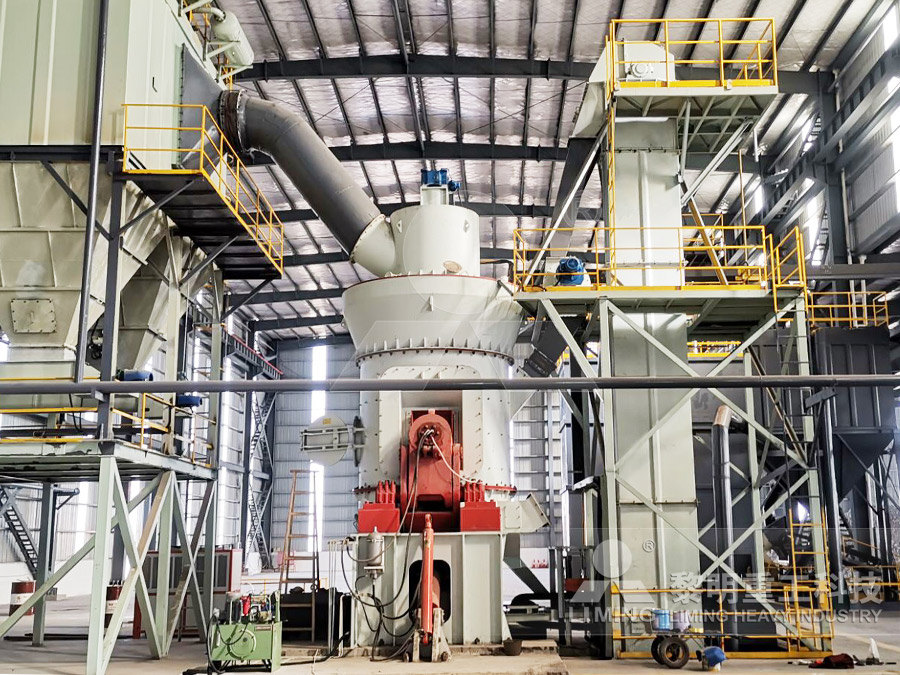
How Cement is Made Cement Manufacturing Process
Stage 2: Grinding, Proportioning, and Blending The crushed raw ingredients are made ready for the cementmaking process in the kiln by combining them with additives and grinding them to ensure a fine homogenous mixture The composition of cement is proportioned here depending on the desired properties of the cement Generally, limestone is 80%, and the remaining 20% 2015年8月1日 The results show that approximately 248t, 469t, and 341t of materials are required to produce a ton of the product in raw material preparation, clinker production, and cement grinding stages Analysis of material flow and consumption in cement production process2015年9月17日 6 00 Limestone Quarry and Crushing plant The major raw material for cement production is limestone The limestone most suitable for cement production must have some ingredients in specified quantities ie, calcium carbonates, silica, alumina, iron,etc Belt Conveyors The quarried raw material is transported to the cement plant, using mechanical conveying Cement Production Process PPT SlideShareWhile each cement plant may differ in layout, equipment, and appearance, the general process of manufacturing portland cement is the same: crushed limestone and sand are mixed with ground clay, shale, iron ore, fly ash and alternative raw materials Some manufacturers grind the raw materials dry, while others use a wetgrinding process How Cement is Made Portland Cement Association
.jpg)
Analysis of material flow and consumption in cement production process
2016年1月20日 In the surveyed cement plant, three balances are established between input and output material in the raw mill, clinker production, and cement grinding system 248 t, 469 t, and 341 t of materials are required to produce a ton of the product in raw material preparation, clinker production, and cement grinding stages; waste gases account for the largest proportion of the 2017年8月15日 The materials reach temperatures of 2500°F to well above 3000°F in the kiln Rotary kilns are divided into two groups, dryprocess and wetprocess, depending on how the raw materials are prepared In wetprocess kilns, raw materials are fed into the kiln as a slurry with a moisture content of 30 to 40 percentThe Cement Manufacturing ProcessCement grinding process mainly includes the mixed materials crushing, material batching, pregrinding, fine grinding, powder classification, dust collecting, automatic control, and other technologies, making cement production high yield and high quality, in line with the requirements of energysaving and emission reductionCement Grinding Unit Clinker Grinder AGICO CementManufacturing of cement involves various raw materials and processes The powdered limestone and water washed clay are sent to flow in the channels and transfer to grinding mills where they are completely mixed and the paste is Manufacture of Cement Materials and Manufacturing
.jpg)
Manufacturing of Cement By Dry and Wet Process
Burning: In this operation, the slurry is directly fed into a long inclined steel cylinder called a Rotary kilnIn this kiln there are 3 different zones shown in fig below Cement Manufacturing Process Flow Chart (i) Drying Zones: In the wet Download scientific diagram Stages in cement production flow chart [43] from publication: A review on kiln system modeling The purpose of this study is to evaluate performance cement of Stages in cement production flow chart [43] ResearchGatekiln feed preparation, pyroprocessing, and finished cement grinding Each of these process components is described briefly below The primary focus of this discussion is on pyroprocessing operations, which constitute the core of a portland cement plant The initial production step in portland cement manufacturing is raw materials acquisition116 Portland Cement Manufacturing US Environmental 2023年12月20日 Cement manufacturing is a complex process that begins with mining and then grinding raw materials that include limestone and clay, to a fine powder, called raw meal, which is then heated to a sintering temperature as high as 1450 °C in a cement kiln In this process, the chemical bonds of the raw materials are broken down and then they are The Cement Manufacturing Process Thermo Fisher Scientific
.jpg)
Manufacturing of Portland Cement – Process and Materials
5 天之前 The manufacture of Portland cement is a complex process and done in the following steps: grinding the raw materials, mixing them in certain proportions depending upon their purity and composition, and burning them to sintering in a kiln at a temperature of about 1350 to 1500 ⁰C During this process, these materials partially fuse to form nodular shaped clinker by ;as can be seen in the process and Quality flow diagram below; 1 Quarrying and Crushing 2 Raw material Storage and Transportation 3 Proportioning 4 Raw material Grinding and Transportation 5 Raw meal storage, homogenization and Kiln feeding 6 Pyroprocessing (Raw meal preheating, calcination Clinkerization, clinker cooling,CEMENT PRODUCTION AND QUALITY CONTROL A Cement manufacturing ProcessAGICO Cement is a cement equipment manufacturer supplies EPC projects for cement grinding station with a simple process, easy operation it will be sent to the stable flow weighing bin of the cement mill by the following seven methods can effectively reduce the energy consumption of cement grinding plant 1 Improve raw materials and Cement Grinding Unit Cement Grinding Plant Cement Grinding 1971年8月17日 116 Portland Cement Manufacturing 1161 Process Description17 Portland cement is a fine powder, gray or white in color, that consists of a mixture of hydraulic cement materials comprising primarily calcium silicates, aluminates and aluminoferrites More than 30 raw materials are known to be used in the manufacture of portland cement, and these116 Portland Cement Manufacturing US EPA
.jpg)
PROCESS OPTIMISATION FOR LOESCHE GRINDING PLANTS
vertical roller grinding mills for grinding: • Coal • Cement raw material • Clinker / granulated slag • Industrial minerals, and • Ores The core elements of these plants are the Loesche vertical mills for drygrinding the abovementioned grinding stock Loesche has In raw grinding, a ball mill with a high efficiency separator is used to achieve uniform particle size in raw mix for the next stages of the manufacturing process At the Cement Grinding Stage, 90 – 95% of the clinker is mixed with gypsum Cement Grinding Unit Process High Quality Download scientific diagram Flow chart of the grinding and blending process from publication: Modeling of Raw Material Mixing Process in Raw Meal Grinding Installations The objective of the Flow chart of the grinding and blending processCement making process – Raw materials, clinker, TYPICAL COMPOSITION OF RAW MATERIALS Kiln Process Thermochemical Reactions Process Reactions Temperature ºC free water evaporates 20 100 Drying/ Preheat crystallization water driven out Cement Manufacturing
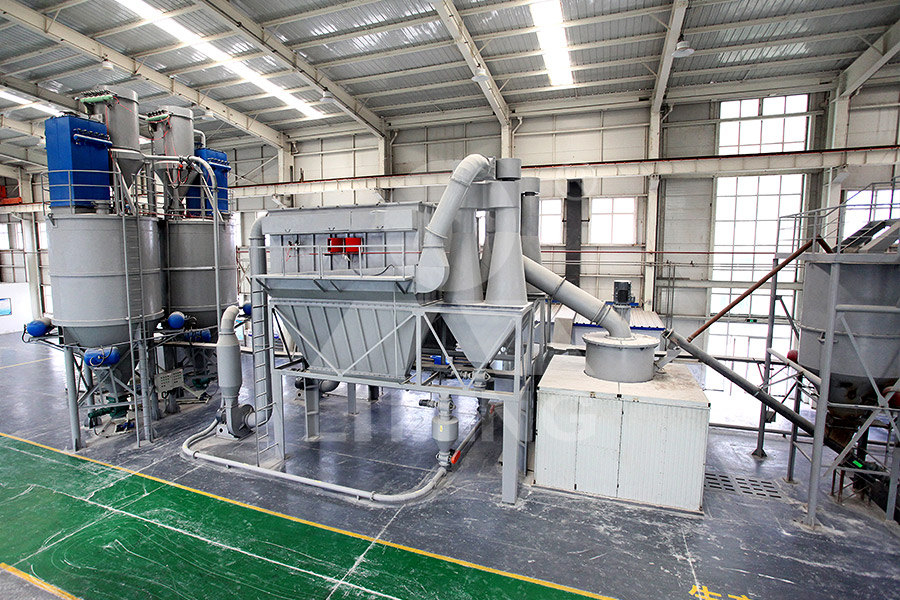
Simulation and Optimization of an Integrated Process Flow Sheet
2021年3月9日 In this study the process flow diagram for the cement production was simulated using Aspen HYSYS 88 software to achieve high energy optimization and optimum cement flow rate by varying the flow rate of calcium oxide and silica in the clinker feed Central composite Design (CCD) of Response Surface Methodology was used to design the ten experiments for 2023年7月10日 The cement manufacturing process involves the extraction and processing of raw materials, such as limestone, clay, and shale, which are then heated in a kiln at high temperatures to form clinkerCement Manufacturing Process and Its Environmental Impact2016年10月5日 In this chapter an introduction of widely applied energyefficient grinding technologies in cement grinding and description of the operating principles of the related equipments and comparisons over each other in terms of grinding efficiency, specific energy consumption, production capacity and cement quality are given A case study performed on a EnergyEfficient Technologies in Cement Grinding IntechOpenCement Plant: The Manufacturing Process worldcementassociation 1 Limestone (CaCO3) is taken from a quarry 2 4 3 The limestone is fed into a crusher and then stored Raw material silos Limestone storage and preblending unit Rotary Kiln Cement Plant: The Manufacturing Process 4 5 World Cement
R)8OC`6F[ZIB.jpg)
Manufacturing process Lafarge
The raw mix is fed into a circular storage unit called a raw mix storage Then, the mix is extracted transversely from the stockpile by reclaimers and conveyed to a raw mill bin called the raw mix bin for grinding The other raw materials that are used in cement manufacturing, called additives, are high purity limestone, sand and iron ore2018年1月15日 We can modify the project capacity and project cost as per your requirement If you need any customized project report and BANKABLE project reports as per your requirement, Click here to CONTACT US Or Call us at +91, +91, +91 011 , , for quick response All reports are prepared by highly CEMENT PLANT Project Report Manufacturing Process2024年9月10日 Steps of Cement Manufacturing The steps involved in cement manufacturing are as follows: Quarrying: Raw materials such as limestone and clay are extracted from quarries or mines; Crushing and Grinding: The extracted raw materials are crushed and ground into a fine powder; Blending: The crushed and ground raw materials are blended in specific proportions Cement Manufacturing Process: Know Extraction, Processing 2020年8月25日 Cement raw material preparation: Limestone is main raw materials for cement manufacturing, and most cement plants are located next to the quarry to reduce the transportation cost; Using explosion or getter loader Cement Production Process Cement Manufacturing
.jpg)
Flow chart of the grinding and blending process
Download scientific diagram Flow chart of the grinding and blending process from publication: Effective Optimization of the Control System for the Cement Raw Meal Mixing Process: I PID Tuning 2021年3月9日 In this study the process flow diagram for the cement production was simulated using Aspen HYSYS 88 software to achieve high energy optimization and optimum cement flow rate by varying the flow Simulation and Optimization of an Integrated Process Flow Sheet 2024年9月5日 2 Raw material grinding After crushing, the raw materials are carried to a grinding mill and made into a fine powder This is done using equipment such as ball mills or vertical roller mills The grinding process ensures the correct particle size of raw material and its homogeneous constitution, which is so critical for product quality 3 A Comprehensive Guide to the Cement Manufacturing ProcessThomas Holzinger, Holzinger Consulting, discusses cement grinding system optimisation Introduction The cement industry uses a wide range of different systems in raw material, coal, and cement grinding While new plants mainly focus on highly energy‑efficient systems, using roller comminution systems like vertical roller mills (VRMs) and highThomas Holzinger, Holzinger Consulting, grinding system
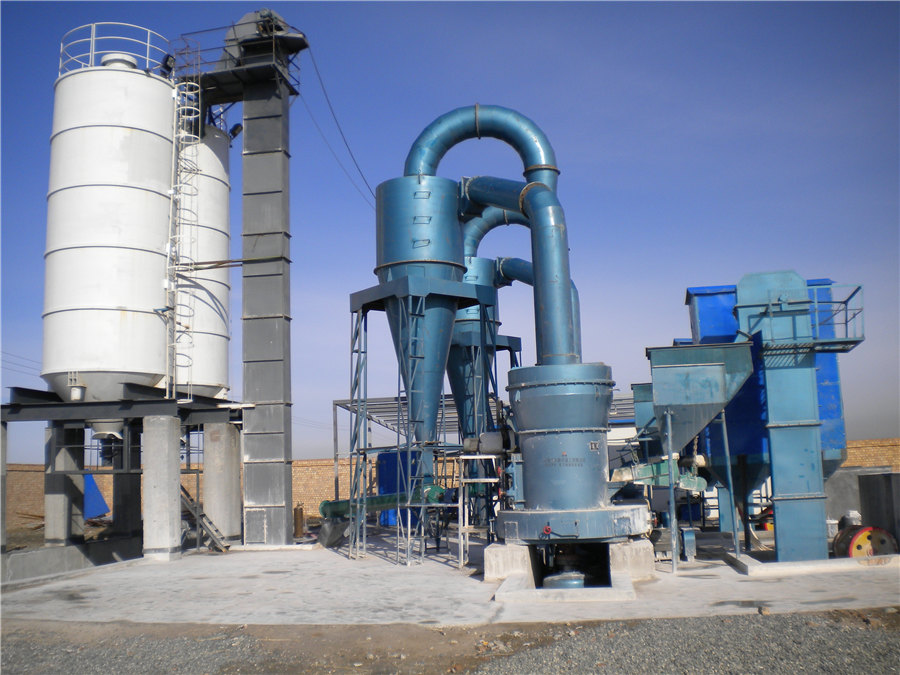
White Cement Manufacturing Process: 6 Steps White Cement Plant
White cement manufacturing process White cement is a type of special cement, belongs to decoration cementIn general, Portland cement is greyishgreen, as the name suggested, white cement is white In the cement manufacturing process, in order to avoid the mixing of colored impurities, calcination of white cement plant mostly use natural gas or heavy oil as fuel A dryinggrinding process often encountered in America, is raw material drying in the mechanical air separator The flow chart of this arrangement is shown in Fig 410 Such a plant dries raw material with a moisture content of 68 % Higher tempera tures generated in a gas or oil fired heater are usually employedDrying of raw materials INFINITY FOR CEMENT EQUIPMENTRaw material process Background Grinding raw materials needs lots of energy Tube mills had been used for grinding, but the energy efficiency level was lower Therefore, the introduction of highly efficient grinding equipment was anticipated Descriptions The vertical roller mill has high energy efficiency and the installation space is smallerVertical roller mill for raw Application p rocess materialsThe vertical roller mill (VRM) is a type of grinding machine for raw material processing and cement grinding in the cement manufacturing processIn recent years, the VRM cement mill has been equipped in more and more cement plants around the world because of its features like high energy efficiency, low pollutant generation, small floor area, etc The VRM cement mill has a Vertical Roller Mill Operation in Cement Plant
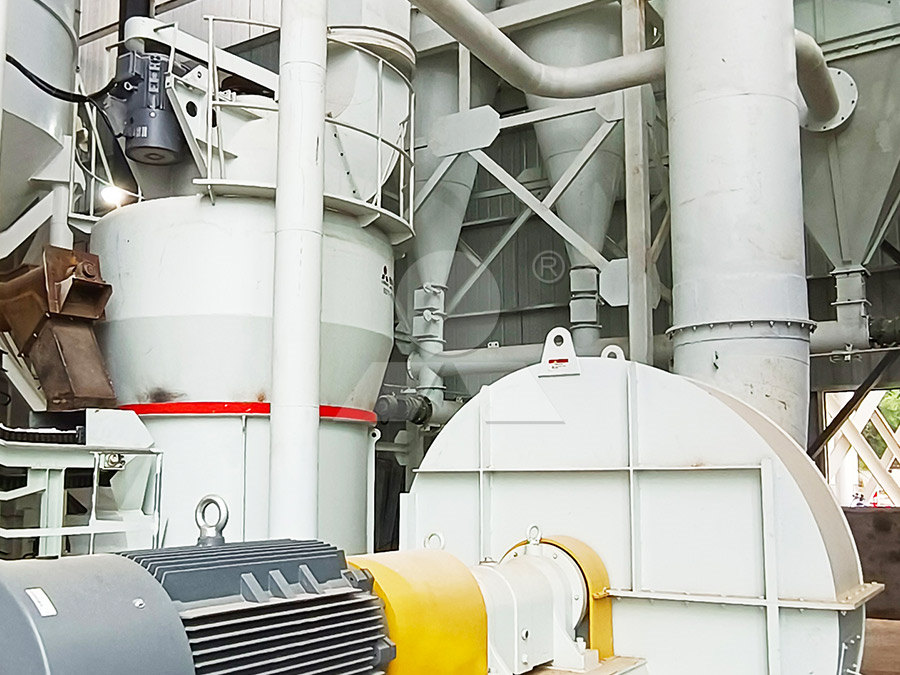
Supply Cement Production Line Process Flow Chart and Machine
1the introduction of the cement plant equipment We Henan Zhengzhou Mining Machinery Co,ltd,can provide complete set technology solutions and supporting production equipments of cement production line 1)Design capacity:1506000TPD 2)According to client's special requirements to design