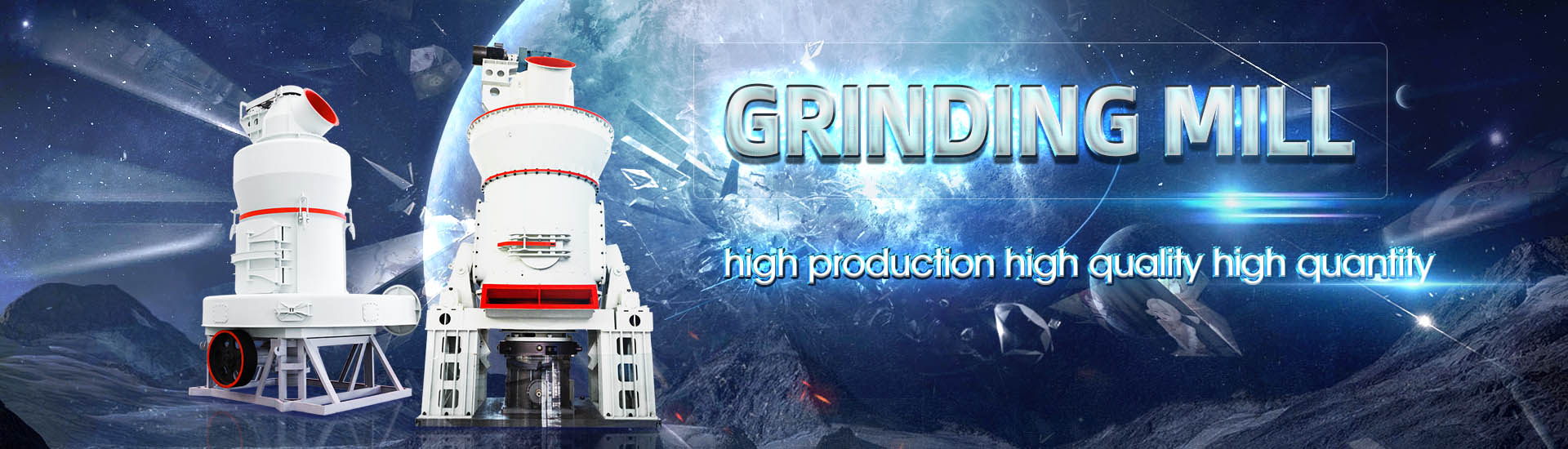
Ball mill feed particle size Ball mill feed particle size Ball mill feed particle size
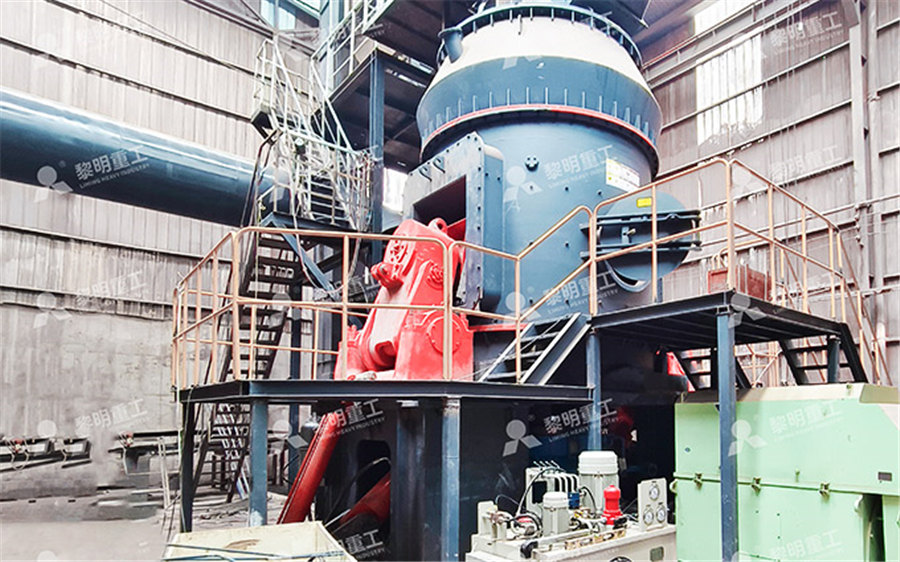
Effect of ball and feed particle size distribution on the milling
In this article, alternative forms of optimizing the milling efficiency of a laboratory scale ball mill by varying the grinding media size distribution and the feed material particle size distribution were2022年11月1日 Various efforts have been exerted to investigate the influence of ball size on the particle size distribution (PSD) in laboratory ball mills, but most studies (eg, Katubilwa et al, Impact of ball size distribution, compartment configuration, and 2019年9月1日 Experiments were undertaken on a laboratory scale to demonstrate how ball milling can be optimised from a feed size distribution point of view and the procedure is Tailoring ball mill feed size distribution for the production of a size Number, size and mass of each ball size depends on mill load and whether or not the media is being added as the initial charge For the initial chargin of a mill, Coghill and DeVaney (1937) defined the ball size as a function of the top size AMIT 135: Lesson 7 Ball Mills Circuits – Mining
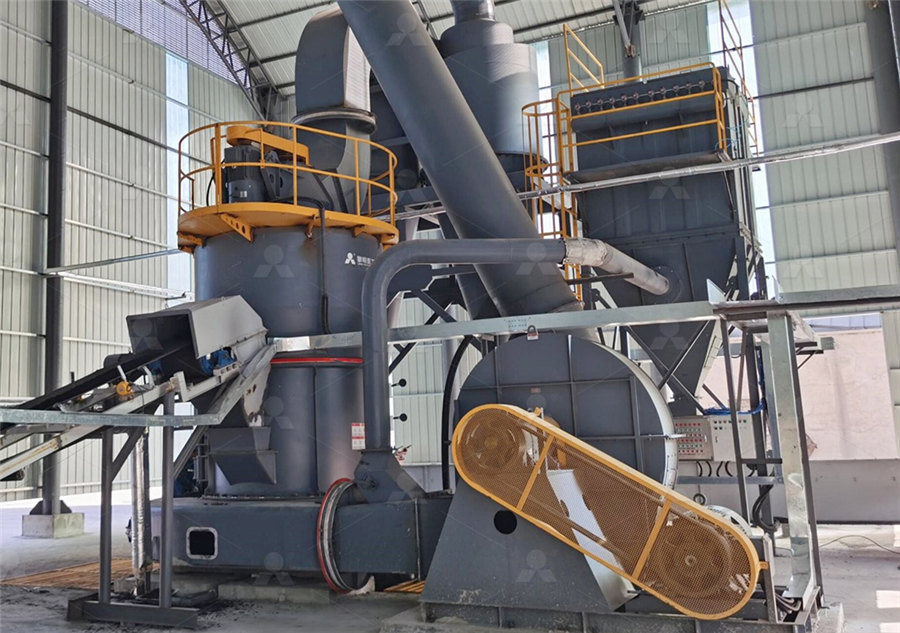
Ball Mill Design/Power Calculation 911Metallurgist
2015年6月19日 The basic parameters used in ball mill design (power calculations), rod mill or any tumbling mill sizing are; material to be ground, characteristics, Bond Work Index, bulk density, specific density, desired mill The feed to ball mills (dry basis) is typically 75 vol% ore and 25% steel The ball mill is operated in closed circuit with a particlesize measurement device and sizecontrol cyclones The cyclones send correctsize material on to flotation and direct oversize material back to the ball mill for further grindingBall Mill an overview ScienceDirect TopicsInvestigation on the particle size and shape of iron ore pellet feed using ball mill and HPGR 909 areas of 500–1600 cm2 g1The concentrate must therefore be reground in order toInvestigation on the particle size and shape of iron ore pellet feed 2023年9月22日 These developments relate to experimental technique and design of experiments, nature of grinding kinetics, estimation of the model parameters, energy–size reduction relationship, and mill scaleup design The new insight obtained into the ball mill grinding operation can help develop improved approaches to the design and scaleup of ball Selected Advances in Modelling of Size Reduction in Ball Mills
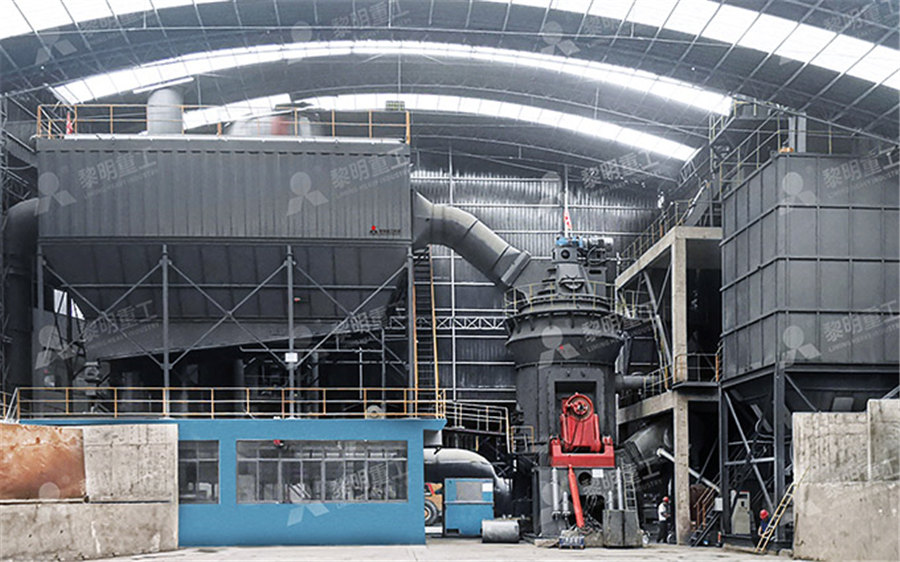
How Ball Mill Ore Feed Size Affects Tonnage Capacity
2017年7月26日 Generally, up until the early 1960’s the classical flow sheet for a beneficiation plant was primary crushing followed by two stages of cone crushing in closed or open circuit, making feed for rod mills, followed by ball mills The rod mill was needed to reduce feed size to the ball mill because crushing plant output was normally coarser than DOI: 101016/JSAJCE201802001 Corpus ID: ; Effect of ball and feed particle size distribution on the milling efficiency of a ball mill: An attainable region approachEffect of ball and feed particle size distribution on the milling The percentage passing 425 microns has decreased from 8133 % in the PSD of the mill feed to 5397 % in the tailings indicating that the ball mill sufficiently liberated the copper minerals to Particle size distribution (PSD) of the mill feed2019年9月1日 Having acknowledged that little is still known about the effects of the feed size distributions on the production of a given target size class, this work thus intends to shed light on this grey area in the research by combining PBM and AR to investigate how ball milling can be optimised from a feed size distribution perspective to produce the maximum amount of the Tailoring ball mill feed size distribution for the production of a size
.jpg)
(PDF) Effects of Ball Size Distribution and Mill Speed and Their
2020年7月2日 The effect of ball size distribution increased with increasing mill filling and for the mill filling of 35%, the ball size distribution had the maximum effect on the power drawand with the decreased grain size, the necessary ball size also decreases (Olejnik, 2010; 2011) For each grain size there is an optimal ball size (Trumic et al, 2007) The bigger ball in relation to the optimal one will have an excess energy, and consequently, the smaller ball mill has less energy necessary for grinding In bothTHE OPTIMAL BALL DIAMETER IN A MILL 911 Metallurgist2022年11月1日 In the opencircuit continuous operation of a ball mill (Fig 1), raw materials are continuously fed to the mill and continuously discharged from the mill (King, 2001)Feed particles become progressively finer along the axial direction due to Impact of ball size distribution, compartment configuration, and 2019年8月15日 Effect of interstitial filling, ball and feed size on particle breakage in a laboratory ball mill: An Attainable Region technique August 2019 Procedia Engineering 35(2019):80 84(PDF) Effect of interstitial filling, ball and feed size on
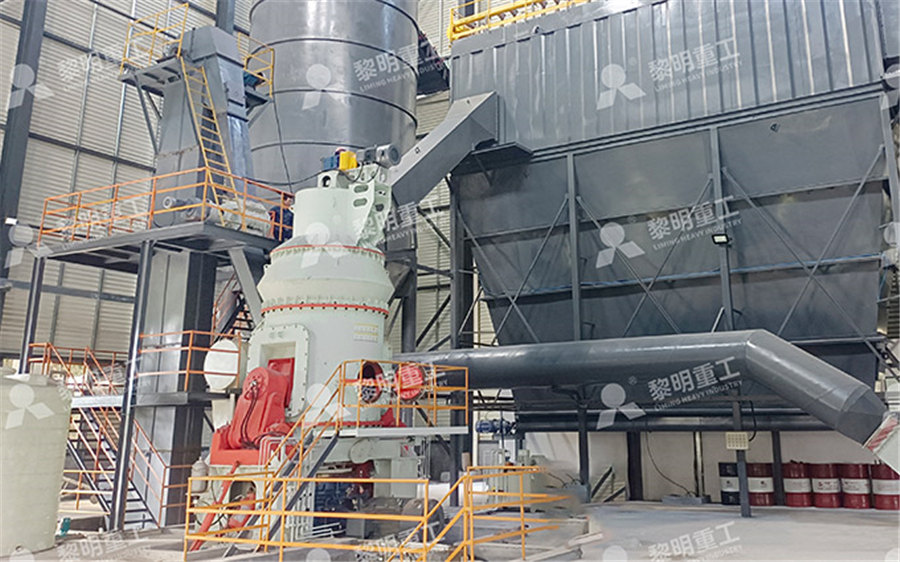
The Effect of Ball Size Diameter on Milling Performance
had decreased for the 2 mm +14 mm monosize feed compared to the bigger 4 mm +28 mm monosize feed This therefore shows that should the material feed size continue to decrease, the smaller balls will perform better than the larger balls during milling, as was mentioned by Katubilwa et al Effect of ball diameter size on mill power draw2023年3月16日 Feed size was divided into two fractions of (+238 −4) and (+2 −238) millimeters, from which different feeds with different weight and size percent values were fed to mill at three feeds of Fractal approach of particle size distribution description of ball 2017年2月13日 The apparent difference in capacities between grinding mills (listed as being the same size) is due to the fact that there is no uniform method of designating the size of a mill, for example: a 5′ x 5′ Ball Mill has a working diameter of 5′ inside the liners and has 20 per cent more capacity than all other ball mills designated as 5′ x 5′ where the shell is 5′ inside diameter and Ball Mills 911Metallurgist2022年3月9日 In this article we focused on the ways how to optimize the particle size in the grinding process of the feed mill However, there is still much to learn in order to understand the animal biology and the effect of particle size on its nutrition to be able to define what the most optimal particle size About Arthur vom HofeImportance and optimization of particle size in animal feed
.jpg)
Secrets of the Bond Ball mill grindability test
feed size distribution is different to a standard Bond ball mill work index test A series of 10 samples for an Andean copper project were treated to both the SAGDesign (and Sdbwi) test and the standard Bond ball mill work index test with 180 µm closing screens The SAGDesign results (with the nonstandard ball mill feed) are given in Table 12020年1月1日 The particle size measurement for the feed sample was conducted using a mechanical vibratory sieve shaker and the resultant PSD is presented in percentage of the recirculating load to the ball mill and passing particle size fraction at P 80 is given in Table 3 Download: Download highres image (70KB) Download: Download full A comparative study on a newly designed ball mill and the 2023年9月23日 Controlling the Ground Particle Size and Ball Mill Load Based on Acoustic Signal, Quantum Computation Basis, and Least Squares Regression, Case Study: Lakan LeadZinc Processing Plant September Controlling the Ground Particle Size and Ball Mill Load Based on 2017年3月20日 Ball mill process parameters for five ground samples with ball load J = 050, particle filling U = 053, mill speed N c = 71% and mill factor F c = 069 Shape and size factors equation and Physicochemical Problems of Mineral Processing
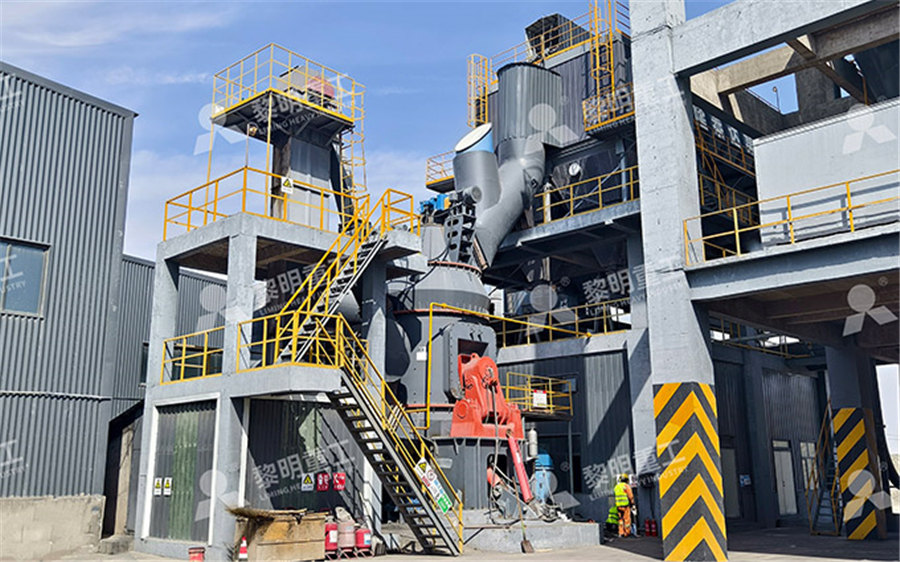
An Energy T 75 Size Reduction Model for Ball Mills Springer
2022年12月22日 The ball mill is also suitable for the JK model, where tests on monosized feed samples are conducted to investigate the effect of feed particle size on ore breakage results Shi et al performed ball mill breakage characterization and developed a ball mill breakage model using new ore [ 9 ]particle size as the target grind size for the ball mill circuit; for example, it is convenient to select the desired 80% passing size as the target grind size The feed to the ball mill circuit contained 3038% fines and the circuit product contained 7760% finesMODULE #5: FUNCTIONAL PERFOMANCE OF BALL MILLINGA section cutthrough of ball mills A ball mill is a type of grinder filled with grinding balls, used to grind or blend materials for use in mineral dressing processes, paints, pyrotechnics, ceramics, and selective laser sinteringIt works on the principle of impact and attrition: size reduction is done by impact as the balls drop from near the top of the shellBall mill Wikipedia2019年9月1日 Having acknowledged that little is still known about the effects of the feed size distributions on the production of a given target size class, this work thus intends to shed light on this grey area in the research by combining PBM and AR to investigate how ball milling can be optimised from a feed size distribution perspective to produce the maximum amount of the Tailoring ball mill feed size distribution for the production of a size
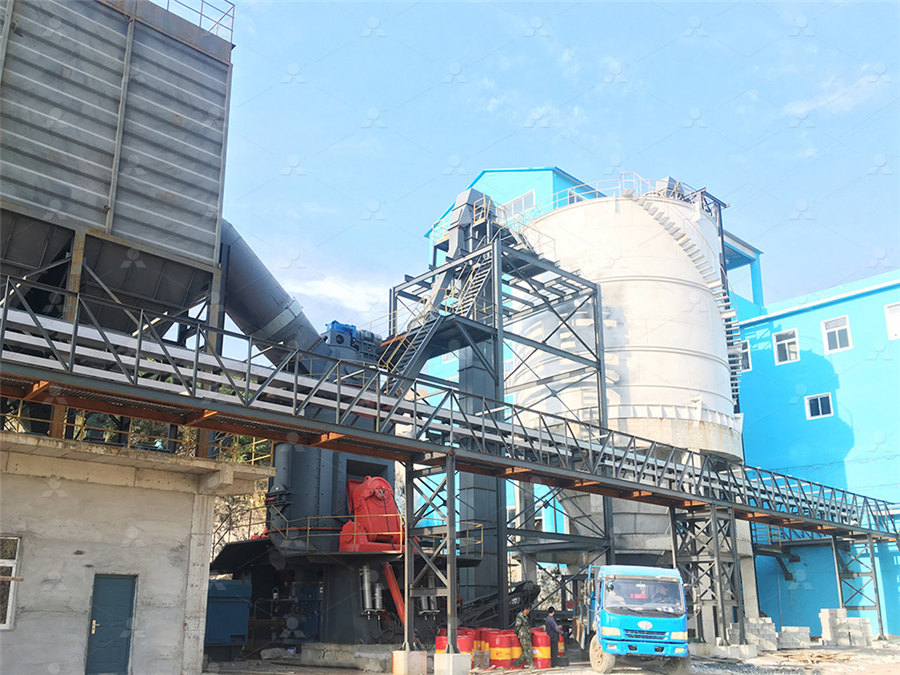
Optimization of Particle Size and Specific Surface Area of Pellet Feed
2016年11月25日 Objective: The dimensional properties of iron ore pellet feed including specific surface area and particle size distribution in the ball mill was studied using response surface area method2019年8月1日 Dry or wet grinding, steel ball size or shape, feed particle size, grinding concentration, grinding time, filling ratio, rotational rate and other operating conditions will also significantly Tailoring ball mill feed size distribution for the production of a size 2022年10月1日 This paper describes a methodology for providing an estimation of the Bond ball mill work index for a sample of nonstandard size (F 100 ≠ −335 mm) when all the parameters from Bond's ball mill equation using that nonstandard feed are knownA new methodology to obtain a corrected Bond ball mill work Ball mill optimisation • Check maximum feed size of fresh feed: if >50mm, adjust the crushing unit If, for all different particle sizes, a continuous evolution is seen, as well as steadily increasing Blaine values, the ball charge is working properly and no actionBALL MILLS Ball mill optimisation Holzinger Consulting
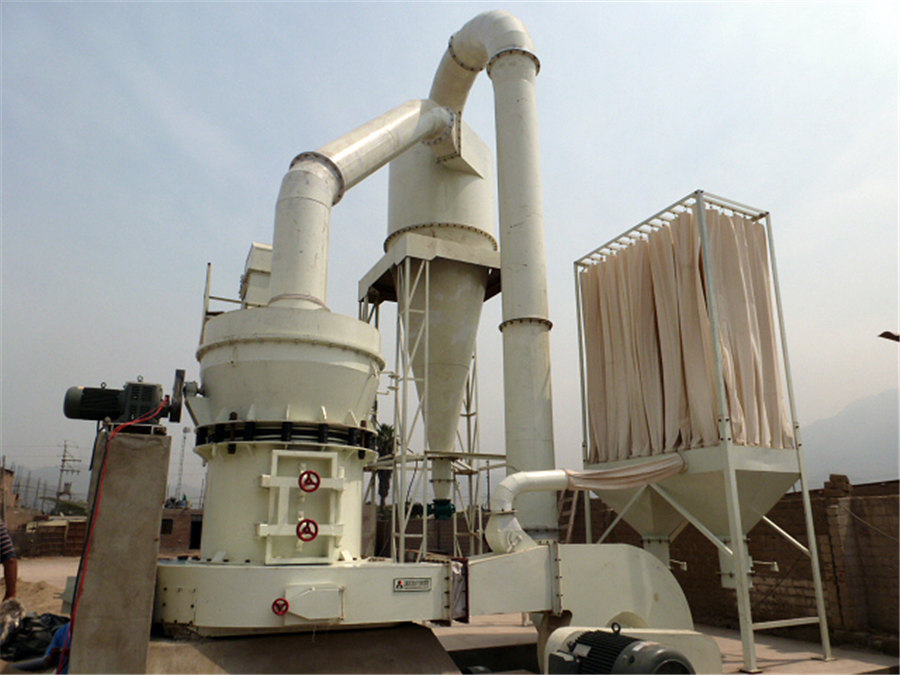
Importance of feed structure (particle size) and feed form
2017年11月1日 Besides feed composition, as the most important factor that determines the efficiency of feed utilization by pigs, feed structure (particle size) and feed form (mash, pellets) are also important for the optimal nutrient utilization (Wondra et al, 1995a, Choct et al, 2004, Thorsten, 2011, Ball et al, 2015)2012年6月1日 Besides particle size reduction, ball mills are also widely used for mixing, blending and dispersing, The process input variables in the figure are: u 1 − mill feed water flow rate,Grinding in Ball Mills: Modeling and Process Control20 mm top ball size (Fine feed) Fig 1 Obtained particle size distributions of mill content versus grinding time using coarse and fine size feed material under ball load in which 20 mm top size ball diameter B Breakage rate of material in the test of ball The effect of feed particle size on breakage rate parameter in a Ball Mill Introduction There are three main stages to mineral processing in the mining industryThese are: Comminution (crushing and grinding); Beneficiation (separation and concentration); Smelting and refining; Ball mills are Ball Mill (Ball Mills Explained) saVRee saVRee
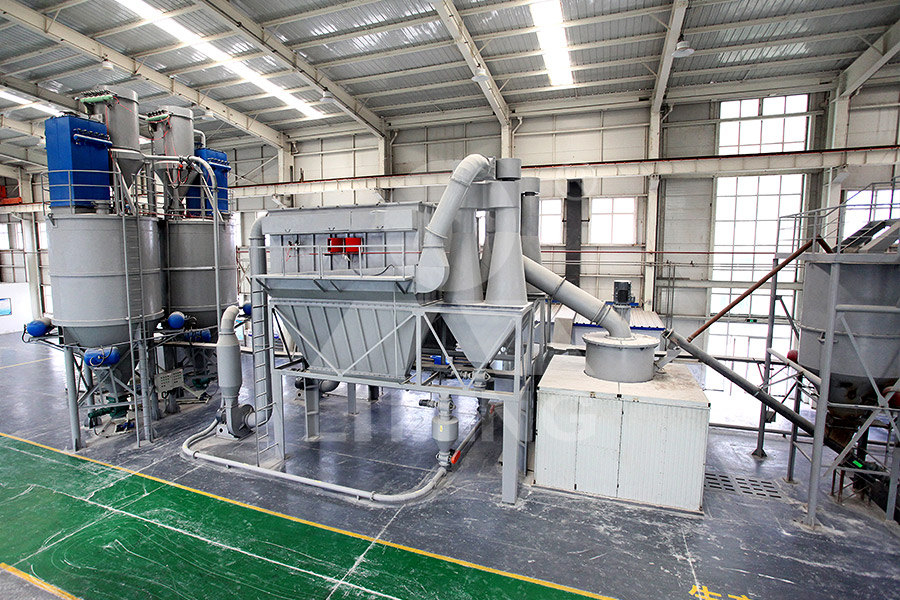
Controlling the Ground Particle Size and Ball Mill Load Based on
know the parameters of the ball mill Here, the aim is to use such techniques in industrial applications [9] In this paper, a new approach was implemented to control the ground particle size and feed rate (load of a ball mill) in the Lakan leadzinc processing plant Lakan leadzinc processing plant is 年1月1日 One of these being the relationship between the ball and feed particle size On the other hand, the powder filling will affect the product fineness when changed in relation to ball and feed particle size Figure 1(b) shows Policy I, where a larger ball size added to a relatively large size ~> 1 mm has an optimal U =1Effect of interstitial filling, ball and feed size on particle 2019年11月1日 In conclusion, the determination, expression and prediction of particle size can be a new direction for controlling the grinding process in the feed mill to better explain its relationship with Size reduction in feed technology and methods for determining Investigation on the particle size and shape of iron ore pellet feed using ball mill and HPGR grinding methods Armin Abazarpoor, Mohammad Halali Materials Science Engineering Department, Sharif University of Technology, Azadi Street, PO box 1136511155, Tehran, Iran, Corresponding author: f (Armin Abazarpoor)Investigation on the particle size and shape of iron ore pellet feed
.jpg)
Intro to Size Reduction Schutte Hammermill
finished particle size is the screen Any material that enters the grinding chamber must be reduced to a size small enough to pass through the screen that covers the mill's discharge opening Because of this the screen size generally provides 70% or more of the control over the finished particle sizeHe concluded that the size distribution from a laboratory rod mill gave a similarshaped size distribution to that of a closed circuit laboratory ball mill He also demonstrated how a laboratory rod mill gave a similar shape of size distribution to a 36 inch (08 m) Hardinge ball mill in closed circuit with a rake classifi er treating the same oreParticle Size Distribution Effects that Should be Considered when 2024年7月31日 The production of cement, an essential material in civil engineering, requires a substantial energy input, with a significant portion of this energy consumed during the grinding stage This study addresses the gap in the literature concerning the collective impact of key parameters, including ball size, feed rate, and mill speed, on grinding efficiency Nine spherical Effect of Grinding Conditions on Clinker Grinding Efficiency: Ball Size