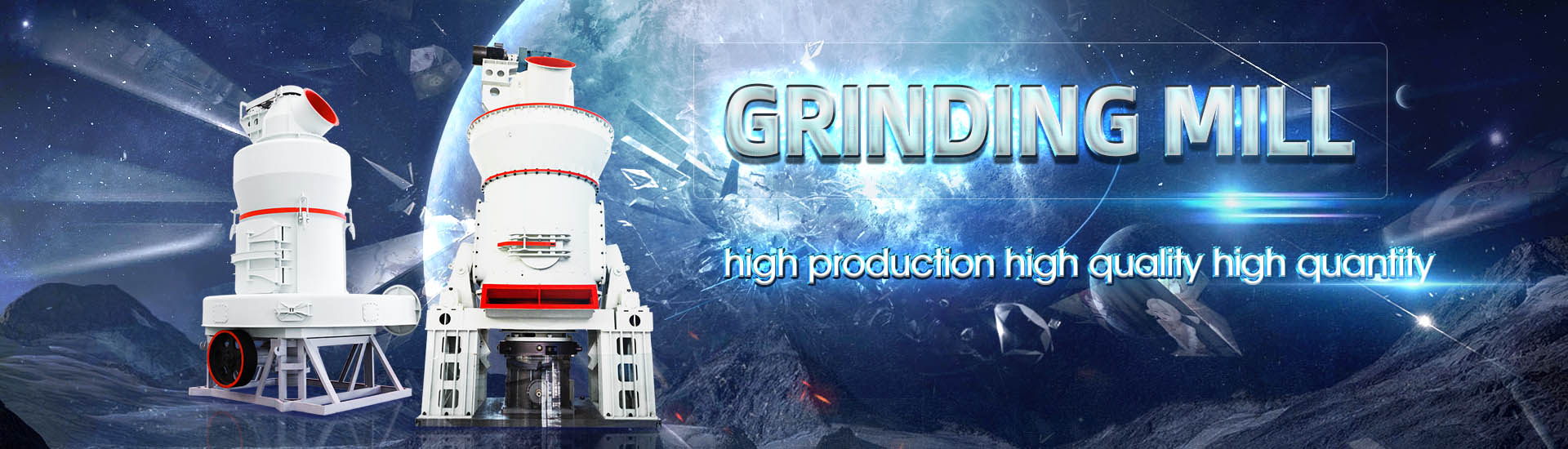
Sintered porous brick weight
.jpg)
Preparation and mechanism of the sintered bricks produced from
2012年2月15日 The weight loss on ignition of sintered bricks was principally caused by the removal of absorbed water and crystal water The sintering shrinkage of sintered bricks mainly 2022年2月7日 The moisture contents in dried bricks can be a maximum of 3% by weight for best quality bricks and a sintering temperature of 850–1000 °C is recommended depending on lime Sustainable insulating porous building materials for energysaving 2022年10月10日 It can be seen from Figure 20 that when heated from room temperature to 200 °C, the sintered brick produces an obvious weight loss, which is caused by the evaporation of free water and bound water; at 400–700 °C, Study on Preparation and Properties of Sintered Brick 2018年11月10日 Tea waste, sawdust and wheat straw were mixed with clay and fired to obtain fired clay bricks at sintering temperatures of 500 °C and 980 °C Physical characterization of Effect of sintering temperature on mechanical and thermophysical
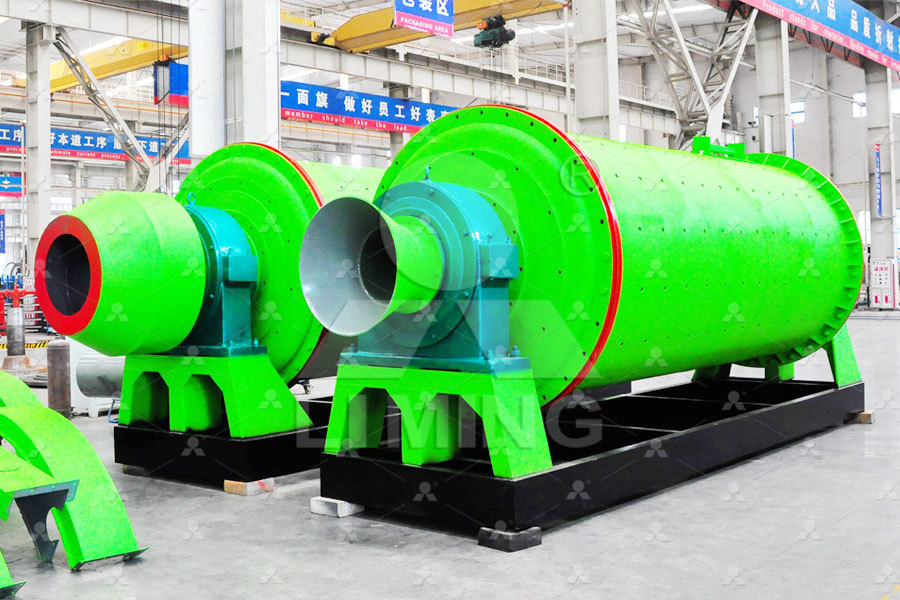
Development of porous lightweight clay bricks using a replication
Over the last decade, many studies have focused on reducing the brick weight and improving the thermal insulation properties of clay bricks To obtain adequate porosity, lightweight clay 2023年2月22日 以黏土、页岩、煤矸石、粉煤灰等为主要原料,经成型、干燥和焙烧而成,孔洞率大于或等于28%的砖。 主要用于建筑物承重部位。烧结多孔砖 《中国大百科全书》第三版网络版2 天之前 Preparation and properties of alkaliactivated fly ashwaste brick porous at 0, 2, 4, 6, and 8% by weight of clay and fired at 950, 1050, and 1100 and enabled sintering at reduced Preparation and properties of alkaliactivated fly ashwaste brick 2021年8月29日 The experimental results show that, the optimal formula of sintered brick is 50% aluminum dross, 3750% engineering soil and 1250% coal gangue The optimum process parameters are molding pressure 10 MPa, Preparation of Sintered Brick with Aluminum Dross and
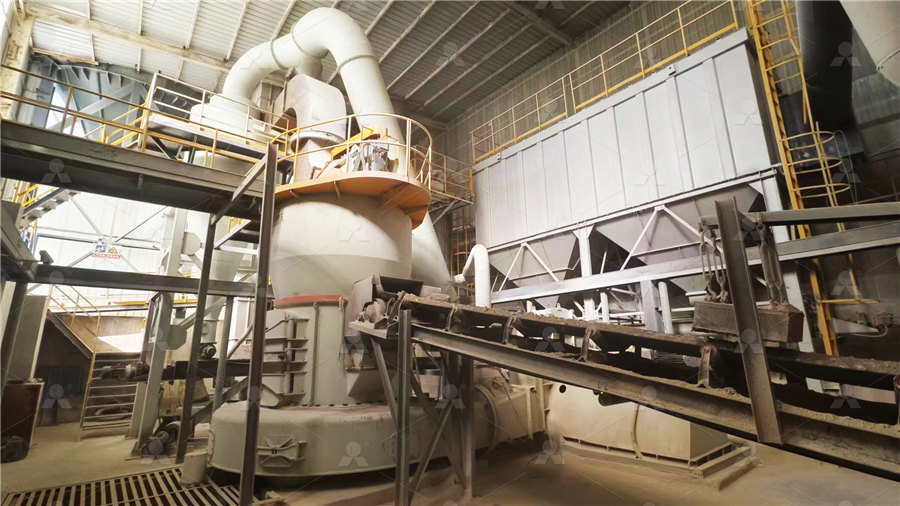
Research Progress on Thermal Properties of Aerated
2022年12月31日 To improve the thermal performance of wall thermal insulation, the thermal performance of sintered shale brick and aerated concrete are introduced in this paperThe invention discloses a sintered coal gangue slag concrete porous brick Components (in terms of weight proportion) of the concrete porous brick are as follows: 1317 percent of cement, 6872 percent of sintered coal gangue slag, 812 percent of river sand and 46 percent fly ash, wherein, sum of percentages of the components is 100 percentSintered coal gangue slag concrete porous brick Google Patentspromotion of the urban sludge sintered shale brick 2 TEST OVERVIEW 21 Brick types in the test The urban sludge sintered solid shale brick and the porous brick masonry used in the test are selected from Gulinger Brick Factory in Liuzhou City The porous brick is a standard KP1 type with the size of 240mm × 115mm × 90mm, hole ratio of 28%, andStraight Joint Shear Performance Test of Urban Sludge Sintered Shale BricksSintered porous plastic materials are manufactured by Porex using a proprietary process that enables the creation of both 2D and 3D porous polymer components that offer superior strength, It is a lowweight, highly pure thermoplastic that Sintered Porous Plastic Innovative Materials for Your
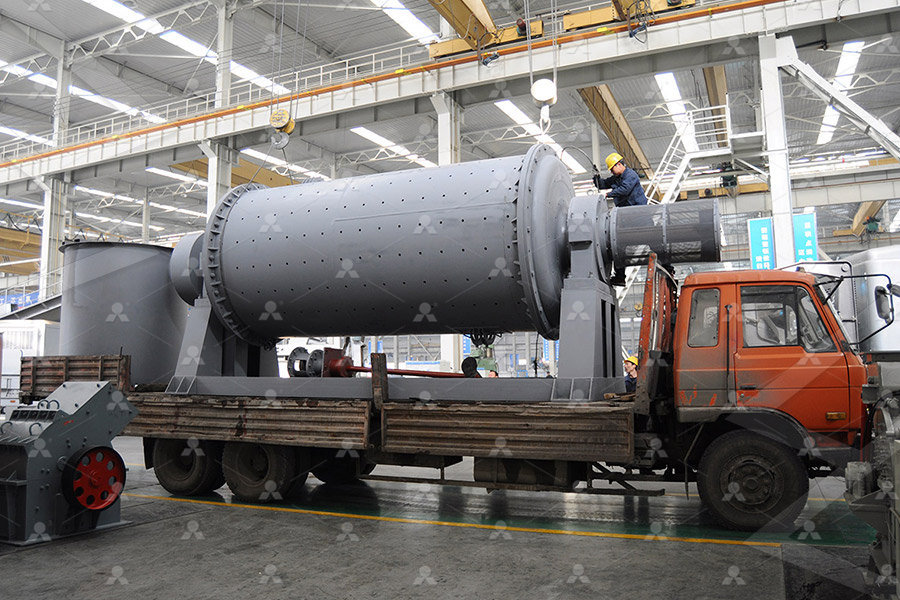
The production of porous brick material from diatomaceous earth and
2015年11月15日 Porous brick as a technological important material has a wide range of applications, such as separation materials, catalyst supports, etc [8–13] Different methods such as freecasting method and sacrificial template method were used to produce porous bricks samples, and some of these have achieved superior performances [14–17]2019年12月31日 Depending on the mineralogy of silicon and other valuable elements in it, coal gangue can be transformed into porous materials categorized as cementbased porous materials 24,41 , porous bricks 42 Preparation, characteristics and mechanisms of the composite sintered At present, sintered porous bricks are divided into two types of P bricks and M bricks As compared with ordinary clay bricks, sintered porous bricks have higher compressive strength, corrosion resistance and durability, as well as light weight What's the difference between fired clay bricks and sintered porous 2015年1月1日 Measured values of shear strength of porous brick in the urban sludge sintered shale brick Figures available via license: Creative Commons Attribution 40 International Content may be subject to Straight Joint Shear Performance Test of Urban Sludge Sintered Shale Bricks
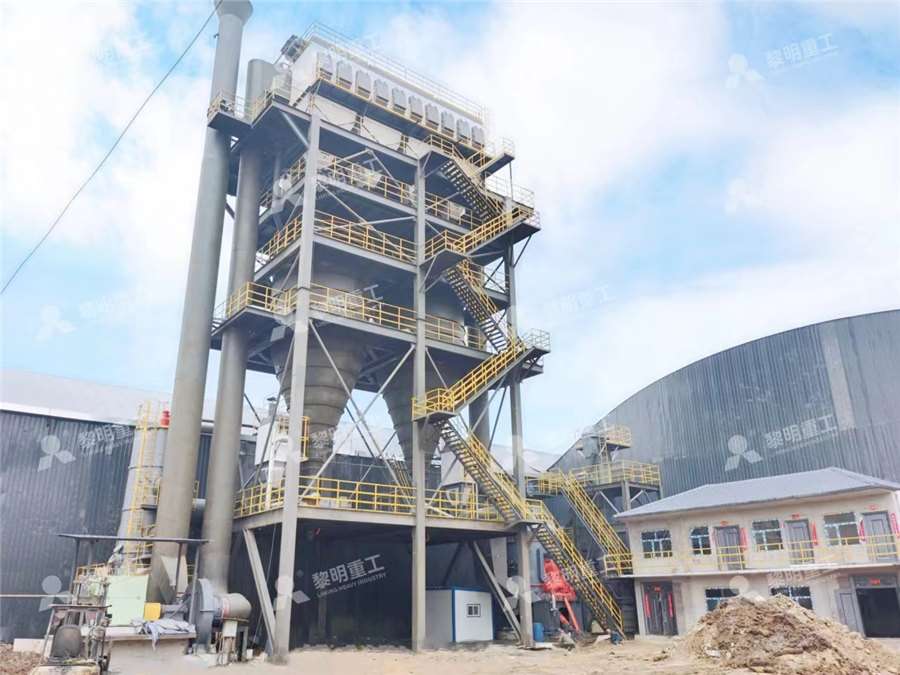
Preparation, pore structure and properties of uniformly porous
2024年10月9日 Compared to single foaming agents, mixed foaming agents improve the pore uniformity and reduce foaming temperature Granite waste was mixed with Na 2 CO 3, boric acid and TiO 2 and melted to produce glass powder The powder mixture was sintered with a mixed foaming agent (SiC + MnO 2) for the foam glassceramics [15]As an oxygen supplier, MnO 2 Through the threedimensional heat transfers numerical simulation of eight kinds with the different number of holes, void ratio and arrangement of sintered shale porous brick (size: 240mm×190mm×90mm), which simulate the sintered porous brick under two different laying way that is 240mm wall and 190mm wall of equivalent thermal conductivityAnalysis of the Sintered Porous Brick Wall Insulation Performance 2020年2月1日 Water absorption into four kinds of brick samples were investigated by NR These samples were not investigated previously These samples are cement light weight brick, cement light weight brick, clay brick and sandlime light weight brick – simply these samples are denoted brick #1, brick #2, brick #3 and brick #4, respectively – Table 1Determination of moisture distributions in porous building bricks 2024年9月1日 In the study of Gencel et al [21], the microstructural, thermal, durability and mechanical properties of clayfree bricks prepared from marble, glass and water treatment sludge wastes were investigated thoroughly, and the results showed that the resulting clayfree bricks all met the requirements of international building codes (such as the minimal density limit (18 Raw material design, sintering temperature optimization and
.jpg)
The production of porous brick material from diatomaceous earth
Addition of 10 wt% ash produces lightweight bricks with 85 MPa at 850 C Porous brick obtained at 850 C and 10 wt% ash had thermal conductivity of 020 W/m K article info Article history: Received 31 January 2015 Received in revised form 14 July 2015 Accepted 4 August 2015 Available online 24 August 2015 Keywords: Diatomaceous earth Brazil 2011年12月8日 Weight loss mechanism analysis: (a) weight loss on ignition of bricks sintered at 1050 • C for 2 h; (b) the theoretical water content of dried specimens(PDF) Preparation and mechanism of the sintered 2015年11月15日 Semantic Scholar extracted view of "The production of porous brick material from diatomaceous earth and Brazil nut shell ash" by E Escalera et al Sintered porous clay for possible as a water filter was fabricated from clay and zeolite mixtures (50:50 ratio weight by weight) with adding of rice husk charcoal as porous template The production of porous brick material from diatomaceous earth 2018年11月10日 This study investigated the thermophysical and mechanical properties of biowasteadded fired clay bricks, which were sintered at two different temperatures in the framework of energy conservation Tea waste, sawdust and wheat straw were mixed with clay and fired to obtain fired clay bricks at sintering temperatures of 500 °C and 980 °C Physical Effect of sintering temperature on mechanical and thermophysical
.jpg)
Component optimization of porous permeable brick in “sponge
the road free of water, etc Permeable brick is mainly divided into three types: cementbased permeable brick, sintered permeable brick and resinbased permeable brick Their main materials are aggregate and binder However, the first two kinds of permeable bricks have some defects, such as: the production and maintenance cycle of cement2012年2月15日 The weight loss on ignition of sintered bricks was principally caused by the removal of absorbed water and crystal water (082 W/m K) due to the formation of highly porous structures, as indicated in the water absorption and SEM resultsPreparation and mechanism of the sintered bricks produced from 2011年8月1日 When the glass powder content of the sintered brick is 10 wt%, with molding moisture of 20 wt%, molding pressure of 25 MPa, heating mode to directly raise the temperature to the target temperature Effect of the sintering technology on the properties of fired brick 2022年12月15日 Sintered brick is a conventional construction and building material produced [10] evaluated the effect of wheat straw and sunflower seeds husks as poreforming agents on the characteristics of porous clay bricks Demir et al 300 °C–400 °C was the most serious interval for weight loss due to the removal of organic Effects of distiller's grains and seawater on properties of sintered

The production of porous brick material from diatomaceous earth
Porous brick obtained at 850 °C and 10 wt% ash had thermal conductivity of 020 W/m K a r t i c l e i n f diatomaceous earth is light in weight due to high porous inner structure with pore size about 100 The sintered porous compacts were used to evaluate bulk density and open porosity by Archimedes’ immersion technique 2020年1月30日 Preparation, characteristics and mechanisms of the composite sintered bricks produced from shale, sewage sludge, coal gangue powder and iron ore tailings Author links open overlay panel Liqun Luo a, The certain amount of iron ore tailings, coal gangue powder, sewage sludge and shale were mixed at different weight ratiosPreparation, characteristics and mechanisms of the composite sintered 2014年10月1日 Porous bricks are usually prepared using the following process (Fig 1) The raw materials (clay, poreforming agents) are first chosen and characterized, then mixed together with addition of water The resulting mixtures are then molded manually or by extrusion Finally, the drying and firing steps lead to the desired bricksDevelopment of ecofriendly porous fired clay bricks using pore 2024年9月1日 Preparation and characterization of highstrength insulating porous bricks by reusing coal mine Model Labsus, Setaram, Caluire, France) under air up to 1000 °C In order to determine the physical properties of sintered bricks, such as bulk density (BD) and RM weight ratio of fired brick on Apparent Porosity Download Preparation and characterization of highstrength insulating porous
7TOCS.jpg)
A stateoftheart review mechanical properties of light weight
2023年6月17日 Sintered fly ash aggregate concrete has compressive strength between 22 and 43 MPa and densities between 1600 and 2000 kg/m 3 Concrete made using fly ash aggregate appears to function well in structural applications Concrete using sintered fly ash aggregate has been considered as a possible structural concrete material2020年5月22日 The present study aims to prepare resinbased permeable bricks with micronsized pores using fine aggregate with a particle diameter of 008–06 mm and bisphenolA epoxy resin, a polymer binder The properties of the binder, the characteristic parameters of the aggregate, and the micro pore structure of the brick were studied in order to break through the Preparation and Component Optimization of ResinBased Permeable Brick使用Reverso Context: ,在英语中文情境中翻译"sintered porous brick" 翻译 拼写检查 Context 词典 词汇 词汇 Documents 同义词 动词变位 协作词典 语法 Expressio Reverso Corporatesintered porous brick翻译为中文例句英语 Reverso Context2012年11月1日 The results indicated that linear shrinkage and weight loss increased while bulk density additive in the manufacture of porous clay bricks The bricks were sintered at 1050°C with Valorization of biodiesel production residues in making porous clay brick
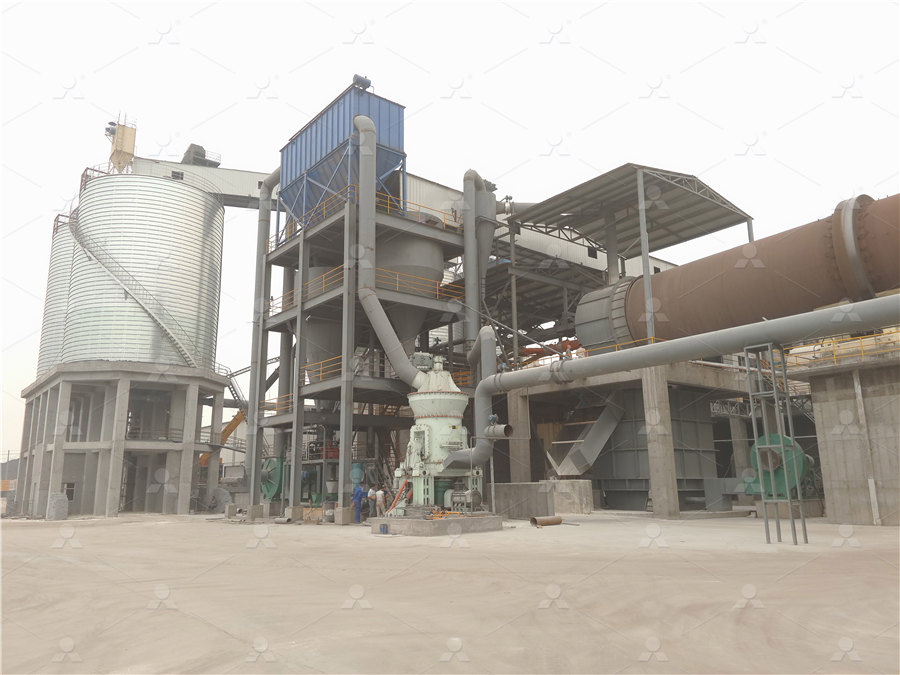
Sintering Wikipedia
Sintered ultra high molecular weight polyethylene materials are used as ski and snowboard base materials The porous texture allows wax to be retained within the structure of the base material, thus providing a more durable wax coating Liquid phase sintering For 2021年2月8日 The sintered bricks were sintered at 800 °C and maintained 1 h, and Fig 4 shows the influence of waste glass as an amorphous binder on the physicalmechanical performance of sintered bricks As the percentage of waste glass was increased from 0 to 30%, the weight loss on ignition decreased from 1452 to 816% and bulk density increased from 1785 to 1924 g Using waterbased drilling cuttings from shale gas development to 2024年5月15日 22 Specimen Preparation Figure 2 shows the process flow and sintering scheme of sintered bricks from lead–zinc tailings Before preparation began, all raw materials were dried to remove moisture and impurities As can be seen in Figure 2 a, the dried tailings, clay, and fly ash were first screened through a 65mesh sieve, and then evenly mixed based Fabrication of Lead–Zinc Tailings Sintered Brick and Its Effect promotion of the urban sludge sintered shale brick 2 TEST OVERVIEW 21 Brick types in the test The urban sludge sintered solid shale brick and the porous brick masonry used in the test are selected from Gulinger Brick Factory in Liuzhou City The porous brick is a standard KP1 type with the size of 240mm × 115mm × 90mm, hole ratio of 28%, andStraight Joint Shear Performance Test of Urban Sludge Sintered Shale Bricks
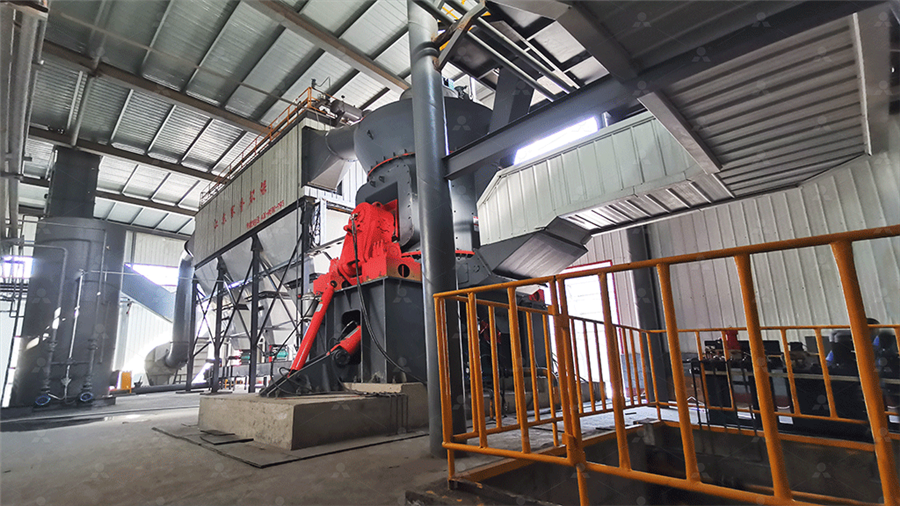
(PDF) Thermal properties of fired clay bricks from
2019年10月10日 addition up to 35% by weight, sintered at 950 and 1050°C porous brick with reduced thermal conductivity Ceram Int 2009;35:262531 20 Folaranmi J Effect of additives on theTechnical properties of 1150 oC fired porous clay brick Expander Additive Ratio(%) Compressive Strength (MPa) Unit Weight (kg/m3) Specific Strength (Strength/UW) FreezeThaw Compressive Strength / Unit Weight Water Absorption Ratio(%) Porosity Ratio(%) Thermal conductivity coefficient ( λ=W/mK) Ref0 2658 1720 1545 3 9093 3 712 878 8109 6 Determination of Physical and Mechanical Properties of Porous Sintered Brick Chenxi Yang1,2,3,4*, Lei Ge1,2,3,4 1Institute of Land Engineering and Technology, Shaanxi Provincial Land Engineering Construction Group Co, Ltd, Xi’an Shaanxi cusses the performance of bricks with different wastes Keywords Waste, Brick, EnvironmentalResearch Progress of Solid Waste Sintered Brick hanspub2017年12月15日 Products of porous bricks from low grade diatomite and sugar filter mud (SFM) in different proportion between 0 and 30 wt% were fabricated at sintering temperatures ranging from 700 to 900 °CPreparation of porous brick from diatomite and sugar filter
.jpg)
Characteristics of Bricks made from waste Steel Slag
2004年2月1日 High quality commercial ceramic bricks typically exhibit WA below 16%, LFS values below 8%, WL values between 5 and 15% and D in the range 2215 g/cm 3 , depending on the type of brick (wall 2022年4月19日 Abstract: Porous refractory ceramics combine the high thermomechanical and chemical resistances of oxidebased compounds with the low thermal conductivity and specific heat of porous materials This twopart study is devoted to understanding and critically reviewing their outstanding behavior as thermal insulators for hightemperature industrial processes (200 Porous Refractory Ceramics for HighTemperature Thermal The sintered porous brick provided by the invention takes magnesium slag and sludge as main raw materials, placing the green bricks in a hightemperature environment of 105+/5 ℃ to dry the green bricks to constant weight; and then, the dried green bricks are sent into a hightemperature kiln for firing, and the firing is divided into Sintered porous brick based on magnesium slag and sludge and