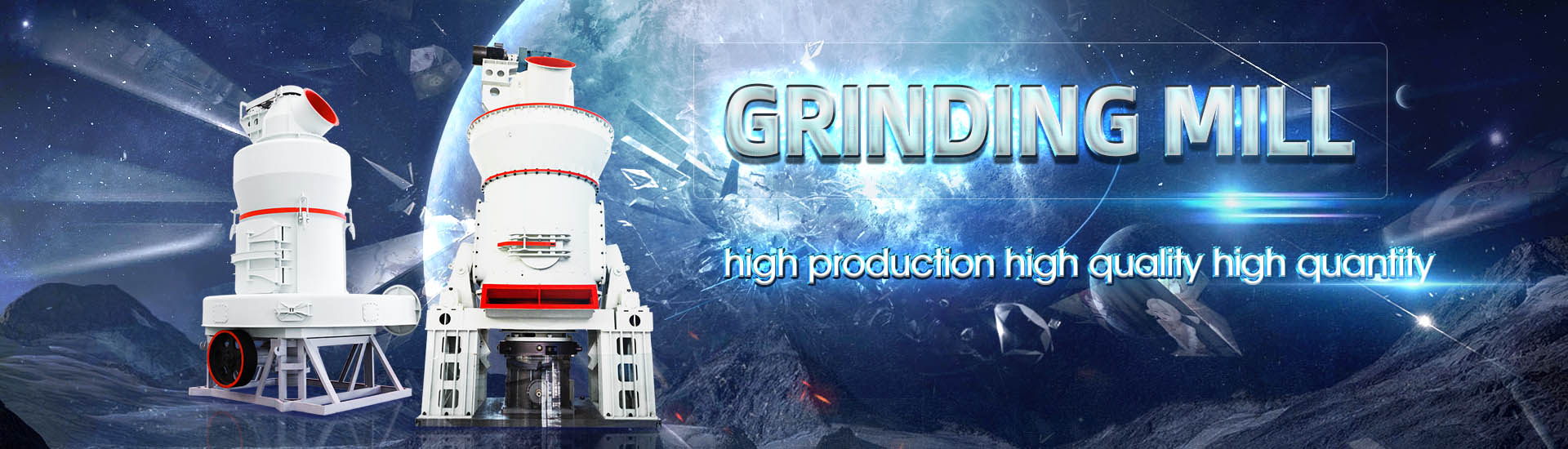
Cement process flow burning
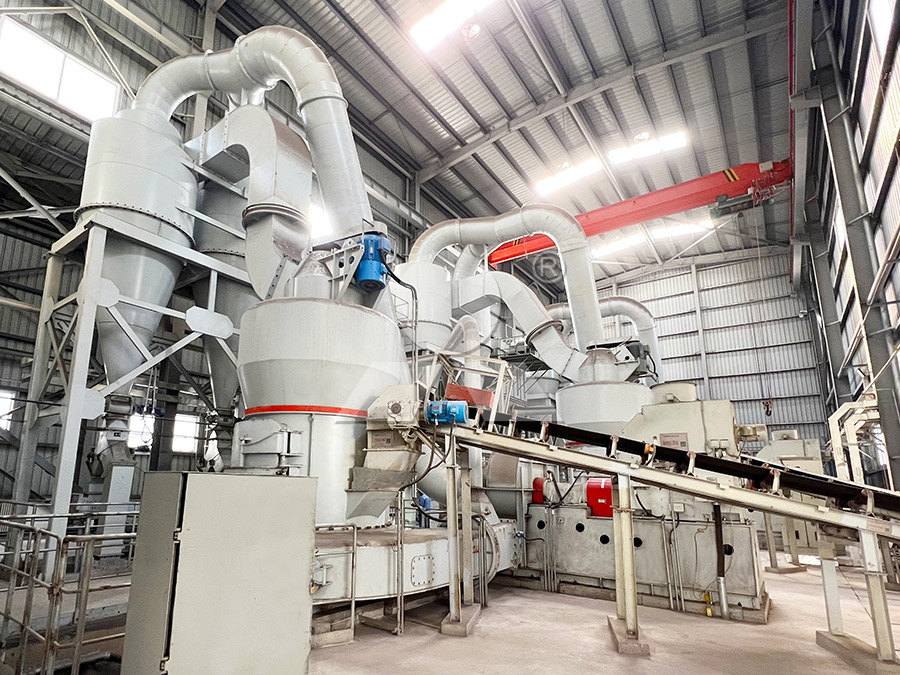
Manufacture of Cement Materials and Manufacturing
The burning process is carried out in the rotary kiln while the raw materials are rotated at 12rpm at its longitudinal axis The rotary kiln is made up of steel tubes having the diameter of 2530 meter and the length differs from 90120meter The Cement Plant Operations Handbook is a concise, practical guide to cement manufacturing and is the standard reference used by plant operations personnel worldwide Providing a The Cement Plant Operations Handbook International Cement The clinker comes out of the kiln redhot with a consistency like a lava flow It is quickly cooled down to a handling temperature in a clinker cooler where heated air from the coolers is recovered and returned to the kilns This process saves How Cement is Made Portland Cement Association1971年8月17日 Five different processes are used in the portland cement industry to accomplish the pyroprocessing step: the wet process, the dry process (long dry process), the semidry 116 Portland Cement Manufacturing US EPA
.jpg)
Manufacturing of Portland Cement – Process and
5 天之前 The manufacture of Portland cement is a complex process and done in the following steps: grinding the raw materials, mixing them in certain proportions depending upon their purity and composition, and burning them to sintering in The burning of the raw meal at approx 1,450°C is carried out in Lepol or preheater kilns that work by varying methods, the main difference being in the preparation and preheating of the kiln feed By chemical conversion, a How cement is made Heidelberg MaterialsThe lower end is fitted with a concentric burner producing a strong flame, by controlled burning of powdered coal, oil, alternative fuels, or gas under forced draft As the material moves through Chapter 4 Cement Manufacturing and Process ControlFive different processes are used in the portland cement industry to accomplish the pyroprocessing step: the wet process, the dry process (long dry process), the semidry 116 Portland Cement Manufacturing US Environmental
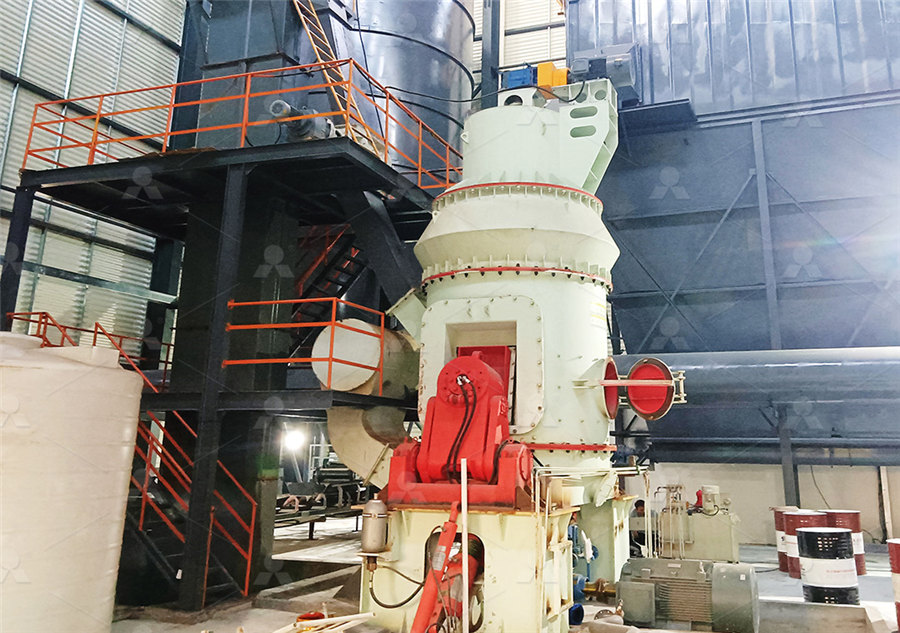
Process flow diagram for the cement manufacturing
According to [39], Figure 4 provides a process flow diagram of the general cement production process and the associated inputs, during various steps of the production process consumptionIn this process, the steps of raw material processing, fuel preparation, clinker burning and cement grinding constitute major emission sources for particulate components While particulate emissions of up to 3,000 mg/m 3 were Cement kiln Wikipediapassivation – 13 Cement quality – 14 Setting time – 15 ASTM cement types and specifications – 16 European EN 197 cement specification – 17 Composite cements (intergrinds and blends) – 18 Supersulphated cement – 19 Calcium aluminate cement (CAC) – 20 Shrinkagecompensating cements (SCC) – 21 ISO 9001:2000 Quality 8The Cement Plant Operations Handbook International Cement 1971年8月17日 116 Portland Cement Manufacturing 1161 Process Description17 Portland cement is a fine powder, gray or white in color, that consists of a mixture of hydraulic cement materials comprising primarily calcium silicates, aluminates and aluminoferrites More than 30 raw materials are known to be used in the manufacture of portland cement, and these116 Portland Cement Manufacturing US EPA
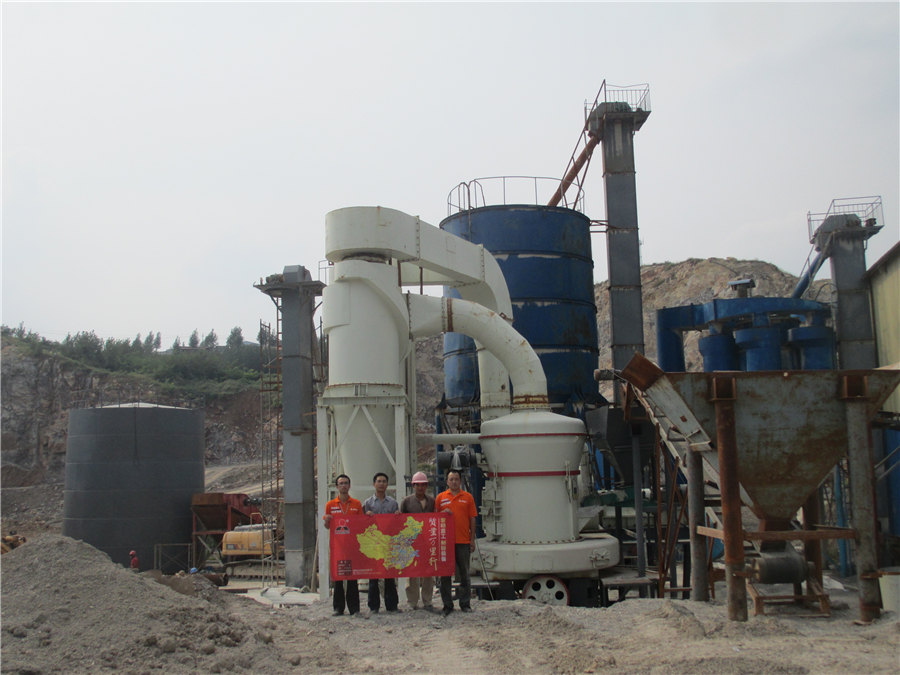
Cement Manufacturing and Process Control SpringerLink
2019年8月27日 The major raw materials used as a source of CaO for cement manufacturing are limestone, chalk, marl, etc These raw materials by virtue of their natural occurrence contains other mineral impurities eg, MgO, SiO 2, Al 2 O 3, Fe 2 O 3, alkali compounds, and sulfidesThese impurities play an important role to influence the cement manufacturing 2024年5月14日 Cement manufacturing process is a reliable bonding material It is obtained by burning calcareous material (lime) and argillaceous material (clay) and then grinding, types of cement The cement manufacturing process was first produced by Joseph Aspidin, a mason from England As its color resembled a variety of sandstone found in Portland, he named it Portland CEMENT MANUFACTURING PROCESS ! TYPES OF CEMENT, FLOW Manufacturing of Cement The manufacturing process of cement consists of, Raw materials grinding Mixing this material in certain proportions depending upon their purity and, Preparing Composition Burning this composition in a kiln at a temperature of about 1300 to 1500°C,Wet Process Of Cement Manufacturing With Flow ChartWet process kilns The original rotary cement kilns were called 'wet process' kilns In their basic form they were relatively simple compared with modern developments The raw meal was supplied at ambient temperature in the form of a slurry A wet process kiln may be up to 200m long and 6m in diameterManufacturing the cement kiln Understanding Cement
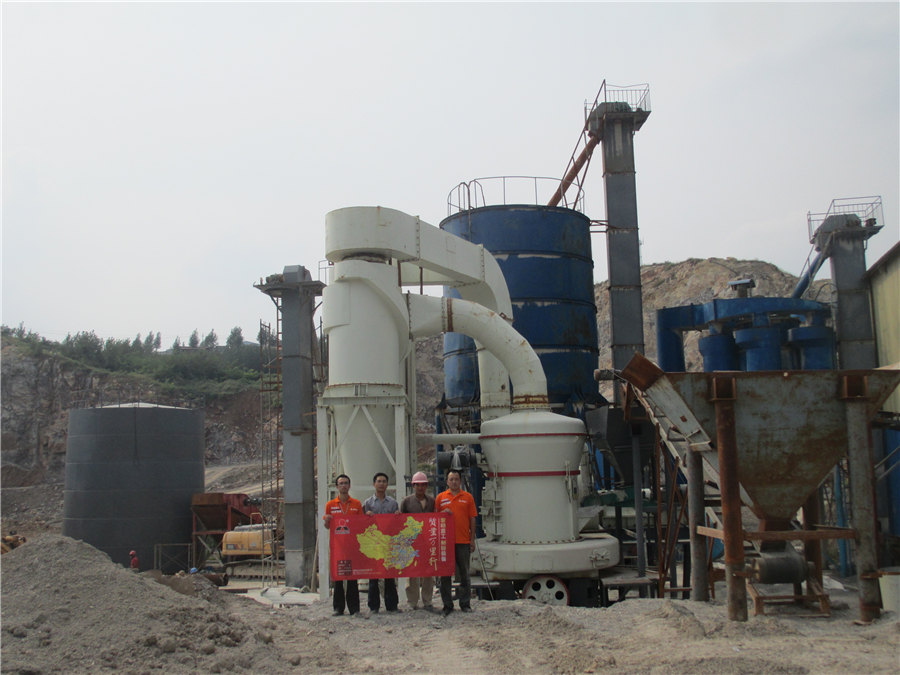
The Cement Manufacturing Process
2017年8月15日 The materials reach temperatures of 2500°F to well above 3000°F in the kiln Rotary kilns are divided into two groups, dryprocess and wetprocess, depending on how the raw materials are prepared In wetprocess kilns, raw materials are fed into the kiln as a slurry with a moisture content of 30 to 40 percent2020年8月25日 A full cement production process includes the cement crushing process, raw mill process, clinker process, and cement grinding process, cement packing process, and related this process is generally known as wet grinding dry burning It has advantages of easy to homogenize raw meal, uniform composition, high and stable quality of Cement Production Process Cement Manufacturing Process AGICO CEMENTThe cement manufacturing process starts from the mining of raw materials that are used in cement manufacturing, mainly limestone and clays A limestone quarry is inside the plant area and a clays quarry is as far from the plant area as 25 kmManufacturing process Lafarge2002年1月1日 Download Citation Mathematical models for the cement clinker burning process: The plantspecific flow conditions, such as the countercurrent flow of the gas and solid phases, Mathematical models for the cement clinker burning process:
.jpg)
Manufacturing of Cement By Dry and Wet Process
Burning: In this operation, the slurry is directly fed into a long inclined steel cylinder called a Rotary kilnIn this kiln there are 3 different zones shown in fig below Cement Manufacturing Process Flow Chart (i) Drying Zones: In the wet Process flow diagram for portland cement manufacturing 1164 EMISSION FACTORS 11/21 Table 1161 Source Classification Code (SCC) Reaction, of the oxides in the burning zone of the rotary kiln, to form cement clinker at temperatures of approximately 1510°C (2750°F)116 Portland Cement Manufacturing US Environmental 2017年12月5日 Methods of Manufacturing Process of Cement At present Portland Cement is manufactured by two processes, Dry Process, and Wet Process The main difference between these two methods of manufacturing of cement is that in the dry process, calcareous and argillaceous raw materials are fed into the burning kilns in a perfectly dry stateCement Manufacturing Process: What is Cement made ofThe high level of CO 2 emission happens when burning fossil fuels to generate heat to initiate the cement manufacturing process and thermal decomposition of calcium carbonate in the progression of manufacturing cement clinker During this process, 30–40% is derived from burning fuels and 60–70% result from decarbonation [4–7] Although Cement Production an overview ScienceDirect Topics
.jpg)
Process flow diagram for the cement manufacturing process,
Download scientific diagram Process flow diagram for the cement manufacturing process, showing electricity and heat consumption or inputs [39] from publication: Energy Savings Associated with 2024年9月10日 Learn about the Cement Manufacturing Process including dry and wet processes and know the major differences between them, advantages, It then enters the precalciner, where a partial calcination process takes place Burning and Clinkerization: The preheated and precalcined slurry is introduced into a rotary kiln, Cement Manufacturing Process: Know Extraction, Processing Everything you need to know about Kiln Burning Systems On the gas flow side, Combustion and the Cement Process Pyroprocessing is the heart of the cementmaking process It is usually the major cost element and kiln performance dictates the efficiency, plant output, Everything you need to know about Kiln Burning SystemsBurning The burning of the raw meal at approx 1,450°C is carried out in Lepol or preheater kilns that work by varying methods, the main difference being in the preparation and preheating of the kiln feed By chemical conversion, a process known as sintering, a new product is formed: clinkerHow cement is made Heidelberg Materials
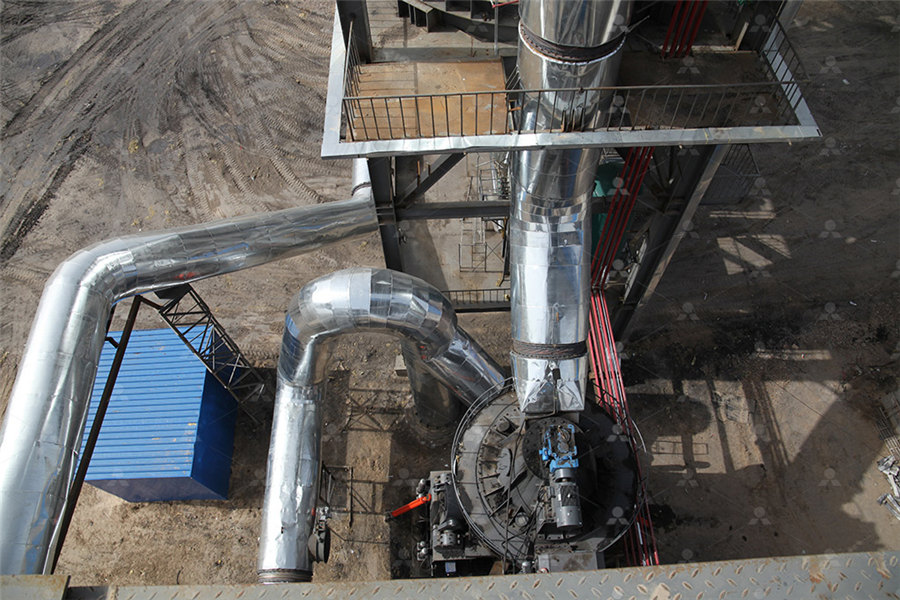
Flow chart of cement clinker burning system ResearchGate
As the most mature denitration technology in the cement clinker burning process, selective noncatalytic reduction (SNCR) has been unable to meet the requirements of ultralow nitrogen oxide (NOX cement notation • is a short hand way to give the phase composition of a cement • is based on model compounds actual cement phases are more or less closeCement Manufacturing2002年1月1日 Download Citation Mathematical models for the cement clinker burning process Part 3: Rotary kiln The mathematical model described in this part of the publication can be used to calculate heat Mathematical models for the cement clinker burning process Part 2021年3月9日 In this study the process flow diagram for the cement production was simulated using Aspen HYSYS 88 software to achieve high energy optimization and optimum cement flow rate by varying the flow rate of calcium Simulation and Optimization of an Integrated Process
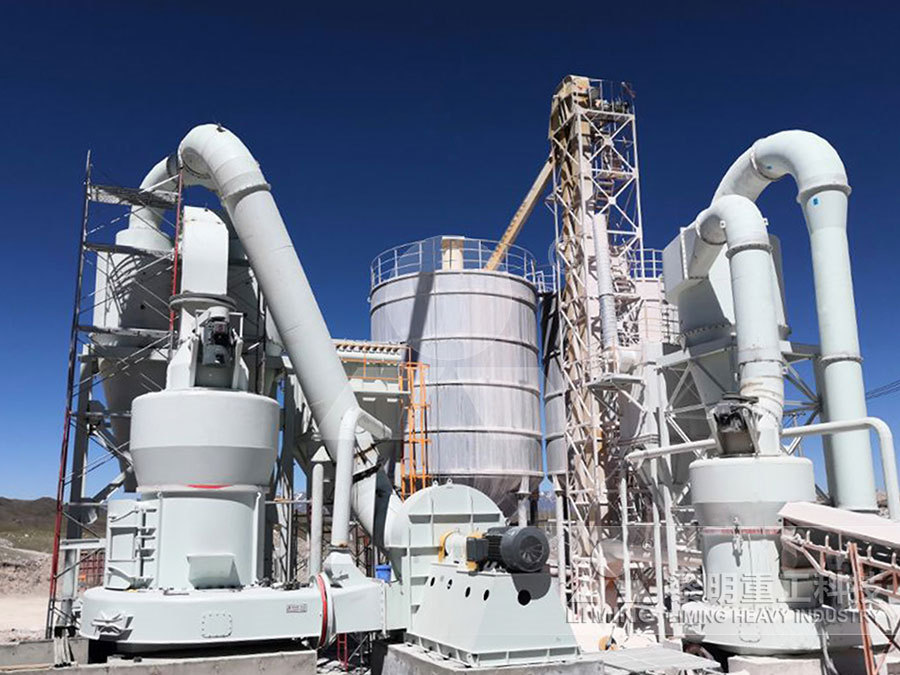
(PDF) THE CEMENT MANUFACTURING PROCESS Academia
Clinker is ground with gypsum (36%) to adjust setting time Packing marketting Wet process Dry process Dry process with preheating tower THE CEMENT MANUFACTURING PROCESS • • • • • • • Quarry Grinding Burning Grinding, Storage, Packing, Dispatch THE CEMENT MANUFACTURING PROCESS quarry dumper loader Quarry face 1controlled burning of powdered coal, oil, alternative fuels, or gas under forced draft Fig 41 Flow sheet of cement manufacturing process 4 Cement Manufacturing andfiProcess Control 63 43 Fuel Different fuels like coal, oil, petcoke, gas, etc are used as the source of heat energyChapter 4 Cement Manufacturing and Process ControlAll the cement plants set up after 1980 use the dry process for the manufacture of cement In this process, the calcareous materials such as limestone are crushed and stored in silos or storage tanks The argillaceous material such as clay is thoroughly mixed with water in a container known as the wash mill This washed clay is stored in basinsCement Manufacturing Process: How the Cement is Made?Calcining and burning or clinkering — the conversion process that takes place within the cement kiln and associated equipment Finish milling — the grinding of clinker to produce cement Raw Materials The main raw material for the manufacture of clinker is a limebearing materialThe Cement Production Process
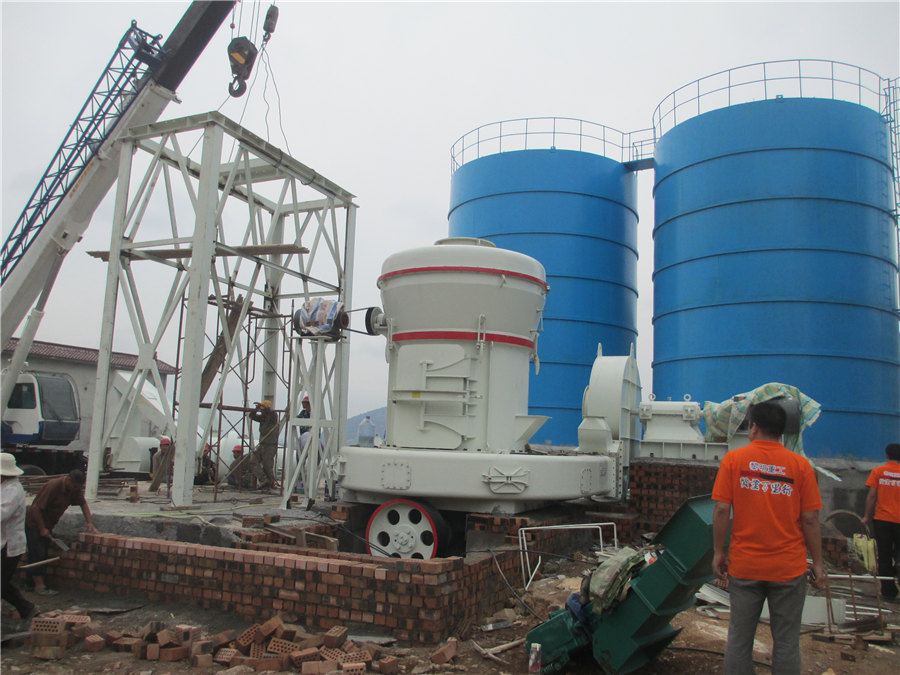
Analysis of material flow and consumption in cement production process
2016年1月20日 The purpose of this study is to examine the material flow in a typical cement production process, to quantify and understand the material flows in each stage, The hot air from the recuperation zone is used mainly as burning air (second dry air) and precalciner fuel (tertiary air) (Fig 3)The use of fossil fuels such as coal, natural gas, and oil is common in cement production, both as a fuel for the kiln and as a source of heat for other parts of the process which leads to CO2 emitted by combustionHowever chemical reactions happening in the kiln (calcination) are also responsible for up to 60% of the total of emissions of the cement production process [PCA]Cement Production Demystified: StepbyStep Process and This mill at this time produces two types of cement namely Ordinary Portland Cement (OPC) and Pozzolana Portland Cement (PPC) OPC comprises 90%clinker, 5%additive (limestone) and 5 %( gypsum) PPC comprises 70% of clinker, 2529%% pozzolana and 5%gypsum The design capacity of the mill is 120t/h for OPC cement But currentlyManufacturing process flow 1 Quarrying and Crushing Messebo Cement2018年2月27日 2 Contents • Introduction • Classification of cements • Portland Cement • Raw materials of Portland cement • Cement Manufacturing Process • Flow chart of Portland Cement manufacturing process • Cement Manufacture of cement Classification and hydration
.jpg)
PPT Engineering Materials Cement PowerPoint
2019年10月23日 Engineering Materials Cement Contents • Introduction • Classification of cements • Portland Cement • Raw materials of Portland cement • Cement Manufacturing Process • Flow chart of Portland Cement The main impact on the energy consumption of cement production is the burning process of cement clinker in a rotary kiln, and the energy costs associated with burning cement clinker constitute 50 Stages in cement production flow chart [43] ResearchGateKnowing density of cement, the weight of the cement required to make a cement bed of 0475 porosity can be calculated Pass the air slowly through the cement bed at a constant velocity Adjust the air flow such that the difference in h 1 of manometer and h 2 of flow meter maintains the constant value of h 1 /h 2 381 Manufacturing Process of Cement Indus University2018年8月28日 After explaining the complete process of cement making, flow chart would be like that flow chart present the summary of whole process as shown below Cement making process flow chart More from my site What You Need To Know About Concrete; Types and Applications of Fly Ash in Construction;Cement Manufacturing Process The Engineering Community
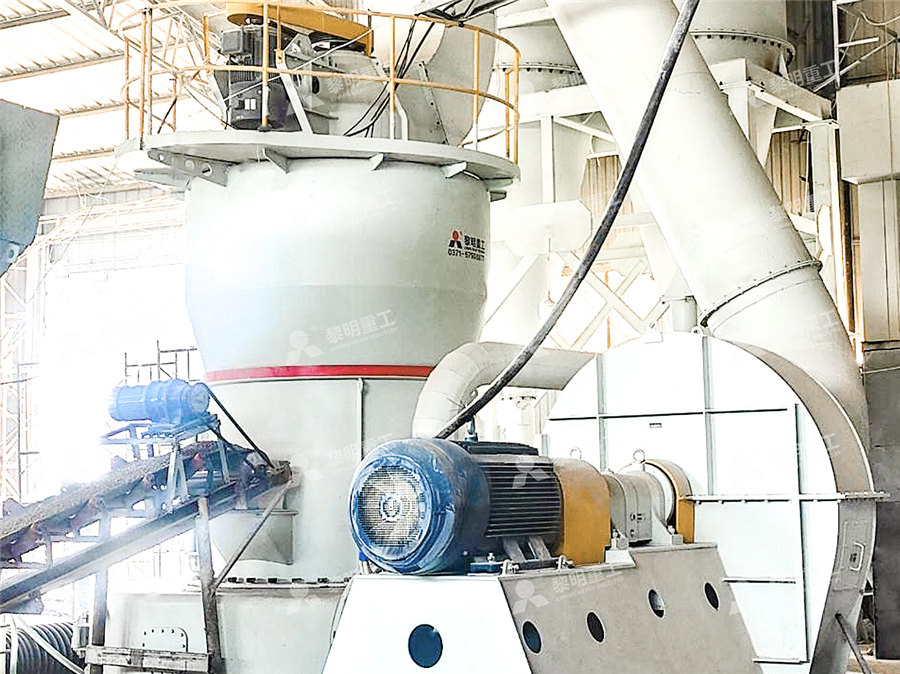
Design and Simulation of a Waste Heat Recovery System for a Cement
Recovery System for a Cement Manufacturing Process Tharun Sivakumar Dept of Electronics Communication Engineering, RV College of Engineering Bengaluru, India chemical process flow software known as DWSIM An analysis of this heat recovery model shows an increase of 1966% in the energy efficiency of the manufacturing processDownload scientific diagram Process flow and energy used during cement manufacturing from publication: Global Carbon Recoverability Experiences from the Cement Industry Achieving netzero Process flow and energy used during cement manufacturingDownload scientific diagram Typical cement manufacturing process flow diagram [4] from publication: Model Development for CO2 Capture in the Cement Industry Climate change has become a Typical cement manufacturing process flow diagram [4]Process Flow; We, as a manufacturer, adopt the dry process for manufacturing of cement Our semiautomated plant operates at global standards and processes to match the quality aspired by our esteemed customers Palletizing Burning Cement Manufacturing Process dry process for manufacturing
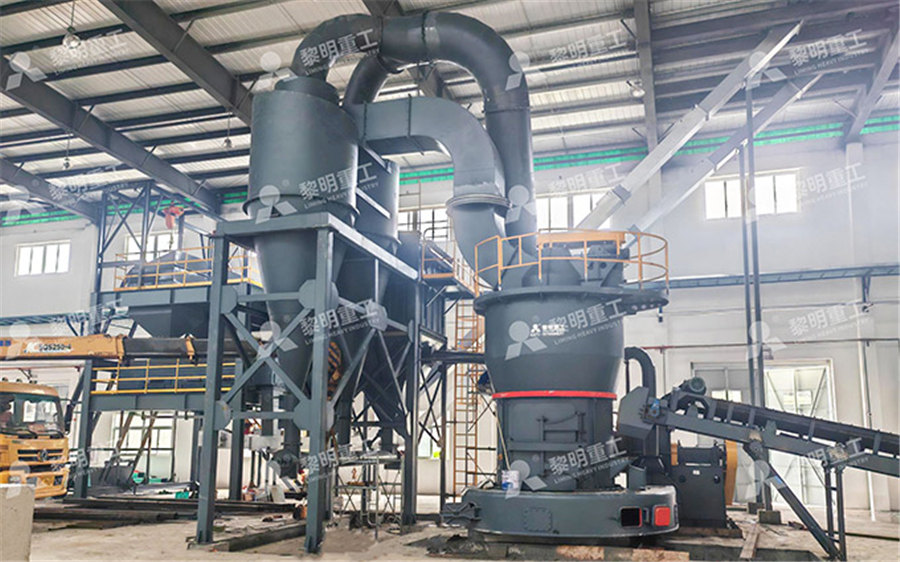
A comprehensive review on Advanced Process Control of cement
2023年1月1日 The heating process in the cement kiln requires intense energy to heat the clinker and compensate for the heating loss Studies illustrate a significant loss of energy (> 50 %) in cement kilns, as shown in Fig 2 [4]Thus, there is a need for optimal design and efficient operation of the cement kiln to minimise this energy loss