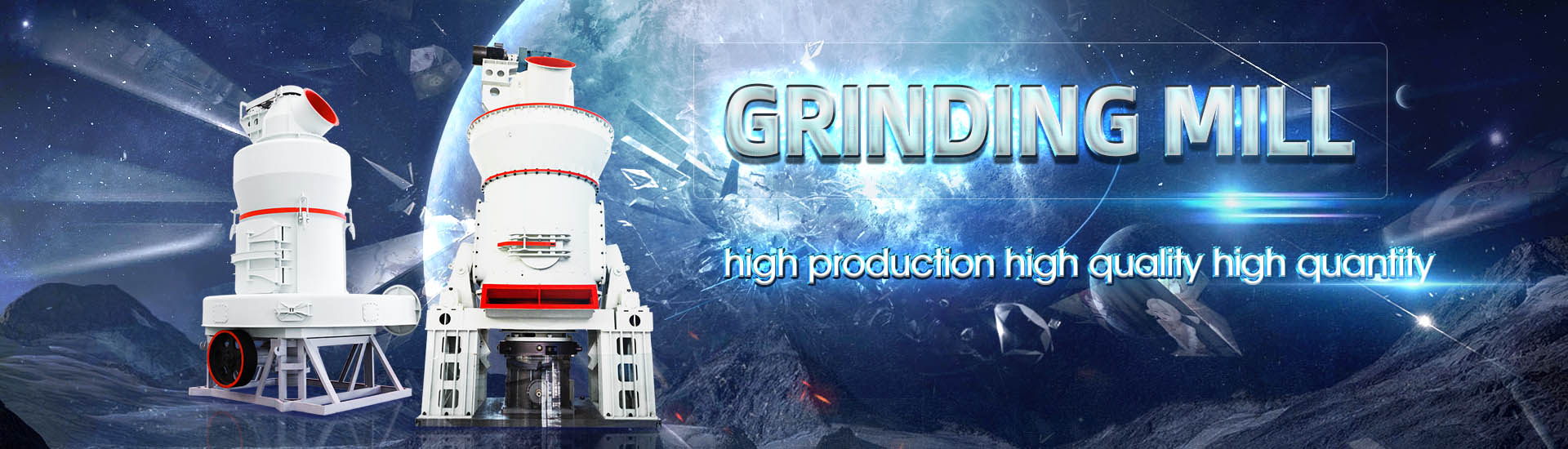
Coal mill blockage phenomenon
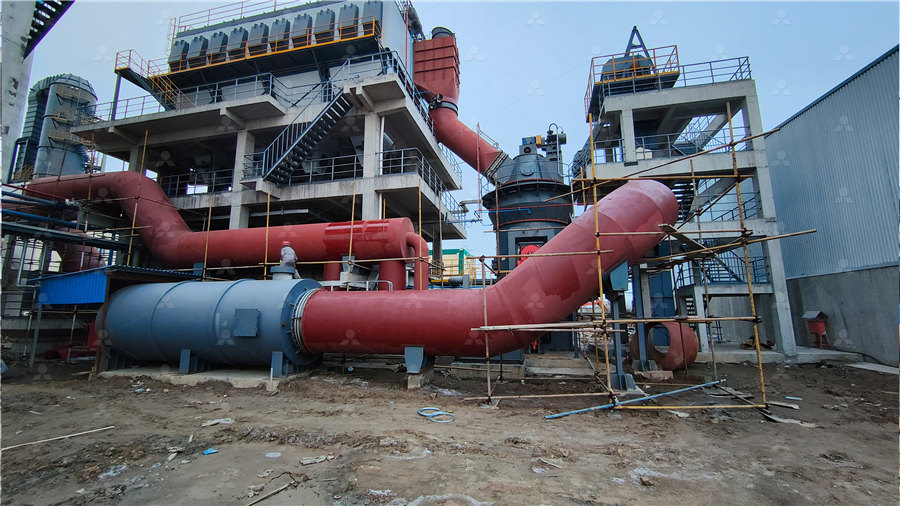
CNA Mediumspeed coal mill operation safety online
The common operational safety risks of the mediumspeed coal mill mainly include abnormal vibration of the coal mill, blockage of the coal mill, deflagration of a coal mill powderThe experimental results show that it can effectively detect the coal blocking and coal breaking faults of the coal feeder and the coal mill, effectively reduce the system false alarm rate, Research and Application of Coal Blockage Early Warning 2020年1月1日 Coal blockage is one of the main reasons for coal mill malfunction It is highly essential to accurately detect the critical blockage in coal mills to ensure a safe and stableEarly Warning of Critical Blockage in Coal Mills Based 2020年9月25日 Abstract: Coal mills have a significant influence on the reliability, efficiency, and safe operation of a coalfired power plant Coal blockage is one of the main reasons for coal Early Warning of Critical Blockage in Coal Mills Based on Stacked
.jpg)
Health indicator construction and application of coal
2023年5月23日 Combined with the common faults of the coal mill, the faults related to the model inputs are summarized into: insufficient coal feed induced by low coal feed; coal blockage induced by excessive coal feed; fault induced by The results demonstrated that the proposed method can effectively detect critical blockage in a coal mill and issue a timely warning, which allows operators to detect potential faults Coal Early Warning of Critical Blockage in Coal Mills Based on Stacked 2020年6月15日 Such a phenomenon indicates that the air to coal ratio of mill A is too low to provide a sufficient air mass flow rate to suspend the PF particles However, although the air Investigations into the blockage of pulverized fuel pipes on coal 2024年9月4日 Based on a realworld coal mills fault case, this paper discusses the effects of different feature selection methods, including expert experience, correlation and causality, on A Fault Early Warning Method for Coal Mills Based on Causality
CFB石灰石脱硫剂制备——磨机公众号12.8 推送案例(8)53.jpg)
Research on fault diagnosis of coal mill system based on the
2020年9月1日 Coal interruption of the coal mill system is usually caused by the blockage of coal dropping pipe or the fault of coal feeder, which directly lead to the reduction or even The invention discloses a method and a system for preventing the coal blockage of a raw and the wallsticking phenomenon of the pulverized coal blocks is piece drenches, bring following difficulty again: 1, increased feeder operation burden; 2, receive the restriction of coal mill temperature out, reduced exerting oneself Method and system for preventing coal blockage of raw coal 2024年9月4日 Li et al proposed a deep learning network based on stacked denoising autoencoder (SDAE) for realizing early blockage warnings for coal mills in coalfired power plants A case study shows that the method is effective in extracting robust features from corrupted data and warns 180 s before the actual coal mill blockage occursA Fault Early Warning Method for Coal Mills Based on Causality This paper introduces the mechanismbased fault diagnosis model of the main equipment of the milling system, and adopts the trend state detection and failure mode recognition methods according to the detection data for comprehensive diagnosis The experimental results show that it can effectively detect the coal blocking and coal breaking faults of the coal feeder and the Research and Application of Coal Blockage Early Warning
.jpg)
Simulation of coal blockage Download Scientific Diagram
Download scientific diagram Simulation of coal blockage from publication: Modeling of Coal Mill System Used for Fault Simulation Monitoring and diagnosis of coal mill systems are critical to 2023年5月23日 Goossens et al 1 combined the values of 60 sensors to construct a global damage index for the structure and implemented the security alert by setting the damage monitoring threshold Lei et al 2 reviewed the four processes of remaining useful life (RUL) prediction for mechanical devices: data acquisition, HI construction, health stage division, and Health indicator construction and application of coal mill based 2020年4月7日 Then, according to the mechanism of various faults, three types of faults (ie coal interruption, coal blockage and coal selfignition) are simulated through the modification of model parametersModeling of Coal Mill System Used for Fault Simulation2018年5月2日 Coal mill malfunctions are some of the most common causes of failing to keep the power plant crucial operating parameters or even unplanned power plant shutdowns Therefore, an algorithm has been developed that enable online detection of abnormal conditions and malfunctions of an operating mill Based on calculated diagnostic signals and defined Detection of Malfunctions and Abnormal Working Conditions of a Coal Mill
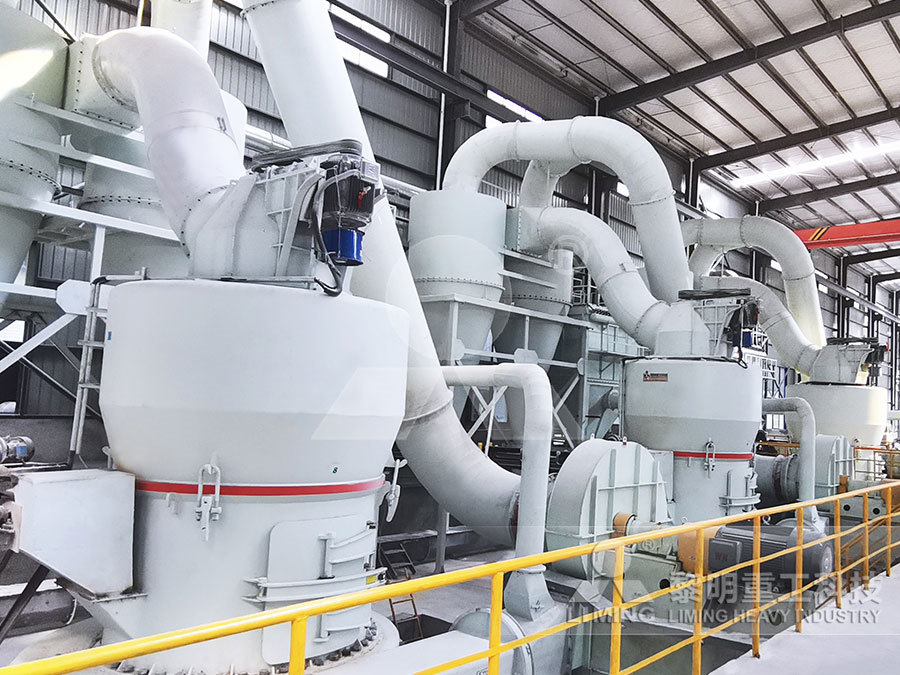
Early Warning of Critical Blockage in Coal Mills Based on Stacked
2020年9月25日 Coal mills have a significant influence on the reliability, efficiency, and safe operation of a coalfired power plant Coal blockage is one of the main reasons for coal mill malfunction It is highly essential to accurately detect the critical blockage in coal mills to ensure a safe and stable operation of the unit Taking advantage of unsupervised learning methods and the coal pulveriz ing system, the coal feeder and the coal mill run at a continuous high load for a long time will lead to various failures in the coal pulverizing system, and a large number ofResearch and Application of Coal Blockage Early Warning the gaps between the balls are filled with coal, the grinding mill has been in its most efficient The output power is the coal storage put into ball mill in unit time With the increase of coal storage, the energy of pulverizing balls have boosted gradually Since the ball mill reaches the maximum output, balls have obtained the maximumCorrelation Analysis of Boiler Operation Parameters Based on Mill The results demonstrated that the proposed method can effectively detect critical blockage in a coal mill and issue a timely warning, which allows operators to detect potential faults Coal mills have a significant influence on the reliability, efficiency, and safe operation of a coalfired power plant Coal blockage is one of the main reasons for coal mill malfunctionEarly Warning of Critical Blockage in Coal Mills Based on Stacked
.jpg)
Early Warning of Critical Blockage in Coal Mills Based on Stacked
2020年9月25日 Coal mills have a significant influence on the reliability, efficiency, and safe operation of a coalfired power plant Coal blockage is one of the main reasons for coal mill malfunction It is highly essential to accurately detect the critical blockage in coal mills to ensure a safe and stable operation of the unit Taking advantage of unsupervised learning methods and 2003年1月1日 Pulverized coal injection has assisted the steel industry to lower operating costs, extend coke oven life and lower greenhouse emissions As the understanding of the impact of quality of the Impact of PCI Coal Quality on Blast Furnace HP coal mill is mainly composed of motor, lubricating oil station, planetary gearbox, side body and its liner plate device, (1)Insufficient primary mixed air volume(2)Phenomenon of coal blockage in coal mill(3)Dynamic separator speed too high(5)Improper adjustment of air throttle ring(6)Coal has high water content, SHPHGLXPVSHHGFRDOPLOO IOPscienceCause analysis:(1)Insufficient primary mixed air volume(2)Phenomenon of coal blockage in coal mill(3)Dynamic separator speed too high(5)Improper adjustment of air throttle ring SHPHGLXP VSHHGFRDOPLOO ResearchGate
.jpg)
Detection of Malfunctions and Abnormal Working Conditions of a Coal Mill
PDF On May 2, 2018, Teresa Kurek and others published Detection of Malfunctions and Abnormal Working Conditions of a Coal Mill mill, such as feeder blockage, lack of coal and mill overloadAs you see in the diagram feeder lies between the bunker and the crusher or coal mill The coal is usually stored in the bunker before feeding, In case the bunker Blockage switch acts the solenoid valve gets direct command through the sensor to open the valve to Blast the air inside the bunker to clear the chokeCoal Feeder Instrumentation basicsAdditionally, large quantity of coal supply required for the same load, which is easy to cause coal mill blockage and other faults When the coal mill is operating under normal conditions, the The monitoring indicator of coal mill under normal conditionCoal mills have a significant influence on the reliability, efficiency, and safe operation of a coalfired power plant Coal blockage is one of the main reasons for coal mill malfunctionThe framework of early warning for coal mill
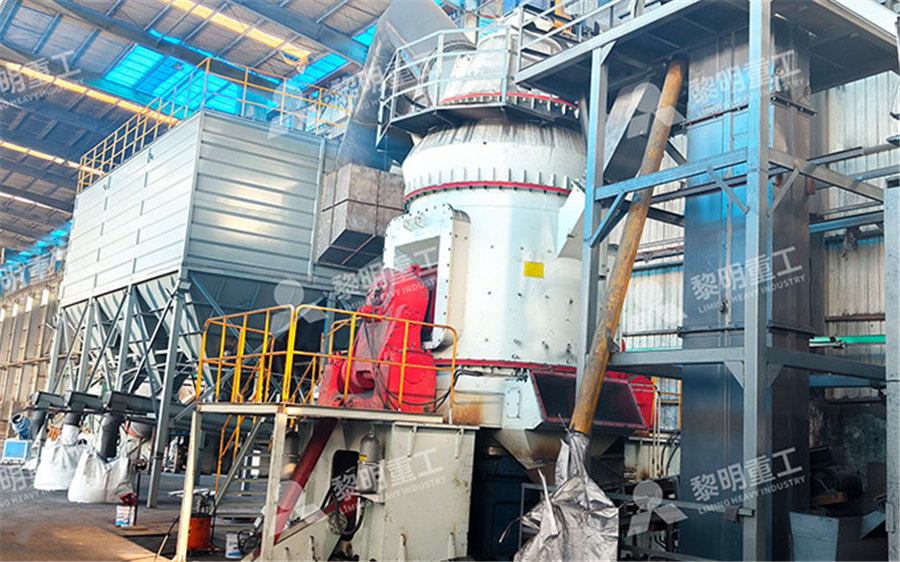
Schematic of medium speed coal mill [5] ResearchGate
Coal mills have a significant influence on the reliability, efficiency, and safe operation of a coalfired power plant Coal blockage is one of the main reasons for coal mill malfunction2020年4月7日 Monitoring and diagnosis of coal mill systems are critical to the security operation of power plants The traditional datadriven fault diagnosis methods often result in low fault recognition rate or even misjudgment due to Modeling of Coal Mill System Used for Fault 1999年7月1日 As Cl result, accidents such as millblockage, overtemperature and emission of pulverized coal often occur, which may cause serious equipment and human damage and environmental pollution and coalpulverizing systems are operated in uneconomic')1 status such that much useful power has been wastedIntelligent Control of CoalPulverizing Systems With BallTube Mill Coal feeder blockage Free download as Word Doc (doc / docx), PDF File (pdf), Text File (txt) or read online for free The coal feeder is blocked, indicated by alarms, dropping load/steam levels and rising coal mill temperatures To Coal Feeder Blockage PDF Valve Scribd
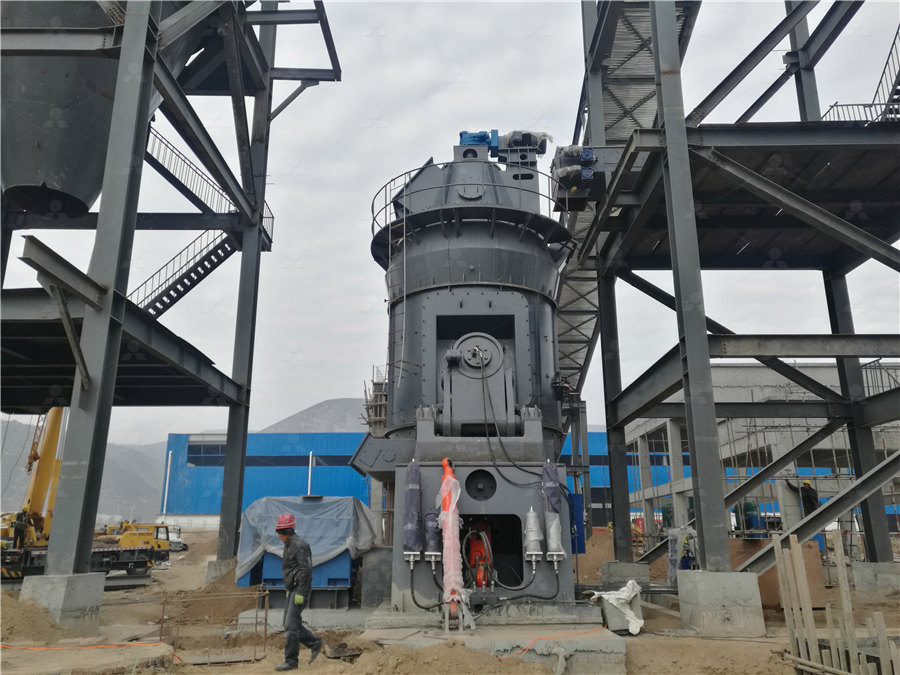
CNA Device for solving coal clogging problem of coal
Feeder is the advanced metering coal supply equipment matching with coal mill in coalfired boiler in thermal power plant pulverized coal preparation system, can viscosity be when large, flowing power is poorer, and frequent blockage phenomenon affects safety, the economical operation of feeder and followup equipmentThere is many 2022年10月1日 Based on the above results, for coalbed gas wells with low gas production or stopped gas production due to pulverized coal blockage, a certain proportion of highpressure nitrogen and clean water mixture can be injected into the coal reservoir from the wellbore in the future, then the powder spitting operation of the coal reservoir can be carried out by controlling Experimental study on coal blockage removal based on pulverized coal DOI: 101016/jmeasurement2020 Corpus ID: ; Research on fault diagnosis of coal mill system based on the simulated typical fault samples @article{Hu2020ResearchOF, title={Research on fault diagnosis of coal mill system based on the simulated typical fault samples}, author={Yong Hu and Boyu Ping and Deliang Zeng and Yuguang Niu and Yaokui Research on fault diagnosis of coal mill system based on the 2014年1月1日 Slagging phenomenon is a common problem for a significant number of coalfired boilers Coal ash deposits typically form on the waterwall tubes, plug the lower regions of the finishing superheater and superheater areas and lay down on the slope of the nose region of the boiler (Fig 1)The slope and superheater areas sometimes covered with heavy ash deposits, Slagging in PC boilers and developing mitigation strategies
.jpg)
Technological advancements in evaluating the performance of
REVIEW Technological advancements in evaluating the performance of the pulverized coal injection through tuyeres in blast furnace Ashish Agrawal1,*,a, Rohit Kumar Tiwari2,b, Sanjiv Kumar1,c coal mill Pulverizing System Wenlan Wang1*, Xionghuai Bai2 and Wanku Liang3 1College of Electricity, Inner Mongolia University of Technology, common and the phenomenon of grinding blockage occurs from time to timeThe unreasonable fineness of pulverized coal results in excessive coarseness of pulverized coal when treated, VWHP IOPscience2020年9月1日 For modelbased fault diagnosis method, it first needs to establish a mathematical model of the coal mill Odgaard et al [2] used a simplified energy balance equation to monitor and diagnose abnormal energy flow in the coal mill Andersen et al [3] designed a Kalman filter to estimate the moisture entering and leaving the coal mill, thereby identifying whether the Research on fault diagnosis of coal mill system based on the 2015年5月7日 Coal blockage is one of the main reasons for coal mill malfunction It is highly essential to accurately detect the critical blockage in coal mills to ensure a safe and stable operation of the unitReview of Control and Fault Diagnosis Methods Applied to Coal
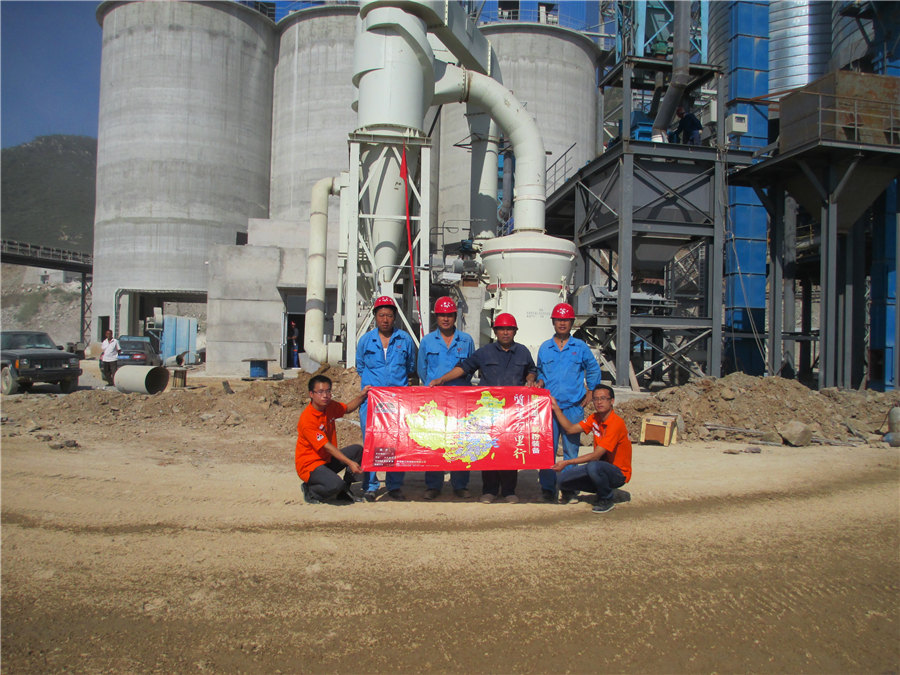
Coal bunker blocking prevention device Google Patents
Being stored in the fire coal in the boiler stokehold coal bunker of coalburning power plant or garbage power plant, is the universal phenomenon that prior art exists owing to reasons such as its water ratio, wet weather, coal bunker design be unreasonable cause boiler stokehold coal bunker chute blockageChute blockage in the coal bunker, major cause are that coal due to " The coal mill under study is a vertical roller type, such as the one available at the PLTU (coalfired steam power plant) Rembang unit, which has two boilers with a steam generator capacity of 513 t/h The schematic of a coal pulverizer mill is provided in Fig 1 Details of these coal mill parameters are presented in Table 1 Coal mill modelingDecision Support System for Coal Mill Fault Diagnosis in Coal Cylindrical Antiblockage raw coal cabin of the present invention solves run coal bin chute blockage phenomenon, and uses the discharge method of single blade impeller feeder, it is possible to achieve run coal bin bottom size strengthens, and diameter adds to 95m, thus realizes meeting volume 650m 3 Cylindrical run coal bin, bunker bay height CNA Antiblocking cylindrical raw coal bunker 2022年10月4日 The reliability of a coal mill's operation is strongly connected with optimizing the combustion process Monitoring the temperature of a dust–air mixture significantly increases the coal mill's operational efficiency and safety Reliable and accurate information about disturbances can help with optimization actions The article describes the application of an additive The Disturbance Detection in the Outlet Temperature of a Coal
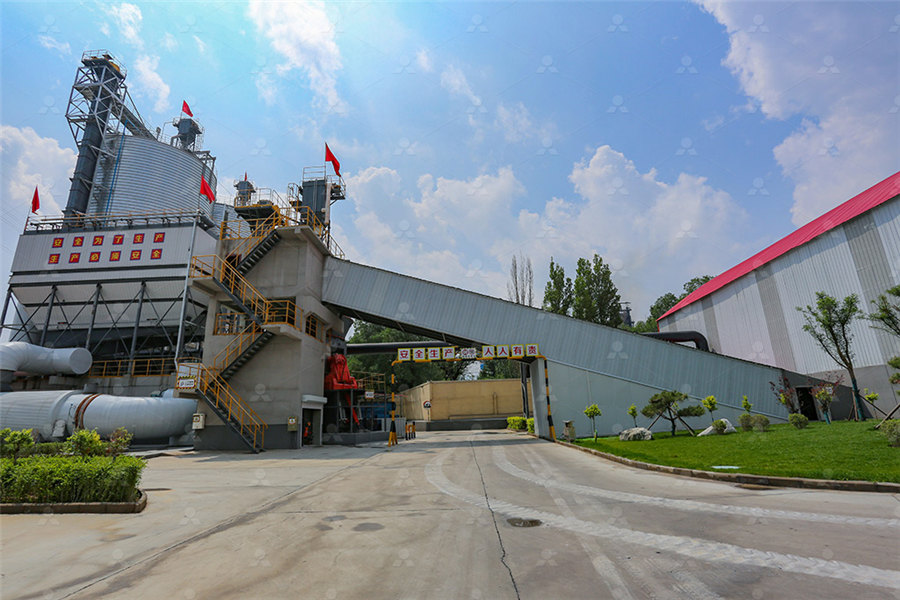
Modeling of complex equipment coal mill in power plant ICJE
steam flow rate, coal feeder nominal speed, inlet coal grindability coefficient, MB coal mill blockage (0100), coal mill outlet pulverized coal temperature, outlet air flow moisture Content, coal storage capacity of the coal mill, average metal temperature of the coal mill machine, and motor power of the coal mill It can be observed that this 2015年10月13日 Coal fired boiler includes the combustion system, steamwater system, attemperation system, air and flue gas system, pulverizing system and the soot blower system []Ball mill is an important part of the combustion system, and the coal pulverizing and treating process is shown in Fig 1The coal falling into coal feeder from coal bunker is grinded up in Correlation Analysis of Boiler Operation Parameters Based on Mill 2019年1月1日 The work in this part is based on a ZGM113N medium speed coal mill equipped in a subcritical 600MW unit Combined with existing research [1, 53] and relevant theoretical knowledge [54], 15 Abnormal Condition Monitoring and Diagnosis for Coal Mills 2020年9月11日 phenomenon of the BF, ensure that the PCI grinding mill is highly available to monitor the coal blockage in tuyeres as shown in Figure 12 [159]Technological advancements in evaluating the performance of
.jpg)
Investigations into the blockage of pulverized fuel pipes on coal
2020年6月15日 The blockage of pulverized fuel (PF) conveying pipes on a coalfired power plant is a hazard accident An indepth understanding of the factors that cause PF pipe blockage provides operators with prior knowledge to avoid such accidents Two representative primary air pipe blockage events are observed on two commercial boilers, respectively