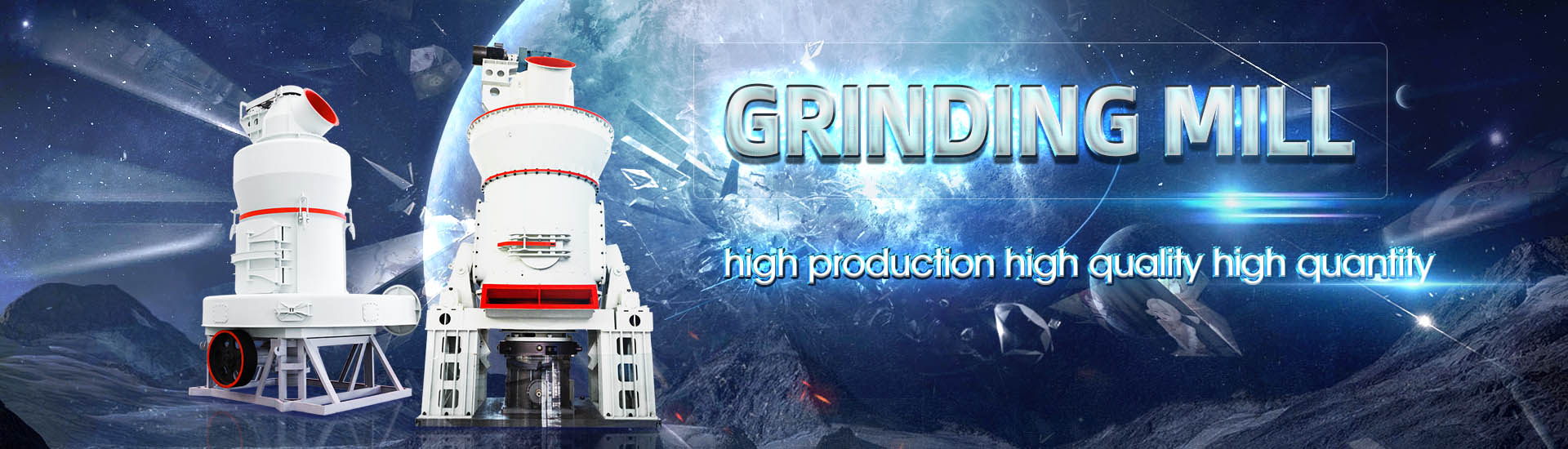
Main process parameters of EDM processing
.jpg)
Principles and Characteristics of Different EDM
The EDM process parameters which drive this process are divided into two types, namely, electrical and nonelectrical parameters The major electrical 2009年12月1日 In this work, response surface modelling (RSM) is utilized for determining the relations between the various EDM process parameters with the various machining criteria Study of the parameters in electrical discharge machining through Electro Discharge Machining (EDM) is an electrothermal nontraditional machining process Electrical energy is used to generate an electrical spark, and material removal mainly occurs ELECTRO DISCHARGE MACHINING IIT Delhi2023年10月12日 In this study, the process parameters of diesinking EDM using copper electrodes and American Iron and Steel Institute (AISI) P20 tool steel workpieces are optimized for various output responses The study surveys Optimization design for diesinking EDM process
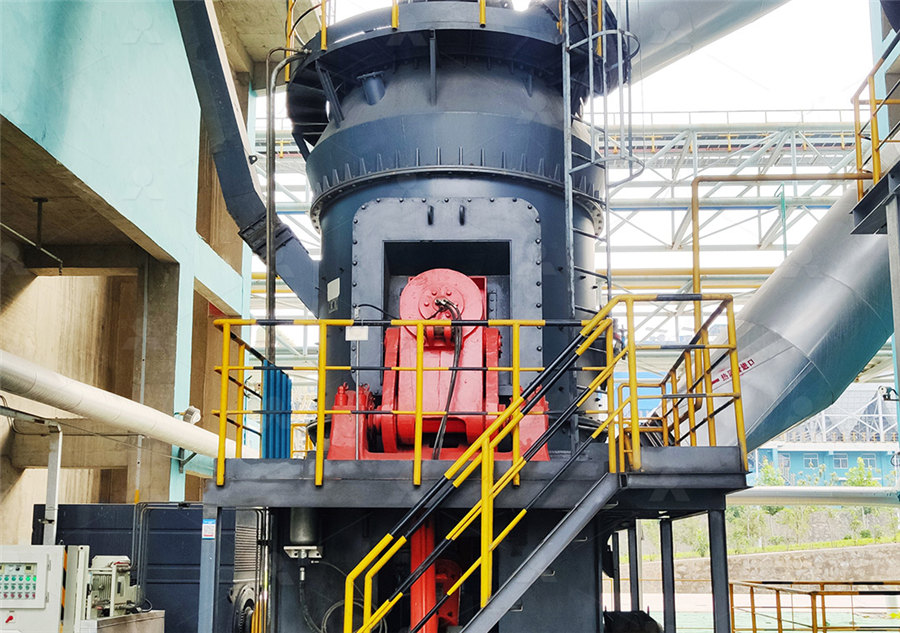
Parameters Optimization of Electrical Discharge
2023年4月24日 In this paper, the existing literature is comprehensively reviewed, and the application of the SI technique in the optimization of EDM process parameters is summarized SinkerEDM (SEDM), wireEDM (WEDM), 2015年1月1日 The present study discusses about having an overview of the EDM process, modeling of process parameters, and influence of process parameters such as input electrical A review on influence of electrical process parameters in EDM 2022年8月31日 To balance the cost and accuracy in the optimization of EDM process parameters, the variablefidelity surrogate model (VFM) was introduced in this paper to Optimization of EDM process parameters based on variable 2023年11月20日 Electrical discharge machining (EDM) is a highly precise technology that not only facilitates the machining of components into desired shapes but also enables the alteration of the physical and chemical properties Recent Trends and Developments in the Electrical
.jpg)
Process parameters and performance measures of
Electrical discharge machining (EDM) is one of the earliest nontraditional machining processes EDM process is based on thermoelectric energy between the workpiece and an electrode2022年6月30日 Alavi F, Jahan MP (2017) Optimization of process parameters in microEDM of Ti6Al4V based on full factorial design Int J Adv Manuf Technol 92:167–187 Article Google Scholar Rajmohan K, Kumar AS (2016) Experimental investigation and prediction of optimum process parameters of microwirecut EDM of 2205 DSSEffects of processing parameters on electrode loss of microEDM 2023年10月28日 Numerous process parameters influence the WEDM process Thus, to achieve affordable and highquality machining, the right set of process parameters must be provided Finding the wire cut EDM optimized settings for Optimization of Wire EDM Process Parameters for Different experimental parameters, which affect surface roughness, were used in EDM process The full factorial response, adopting a facecentered central composite design (FCCD), was performed Process parameters and performance measures of
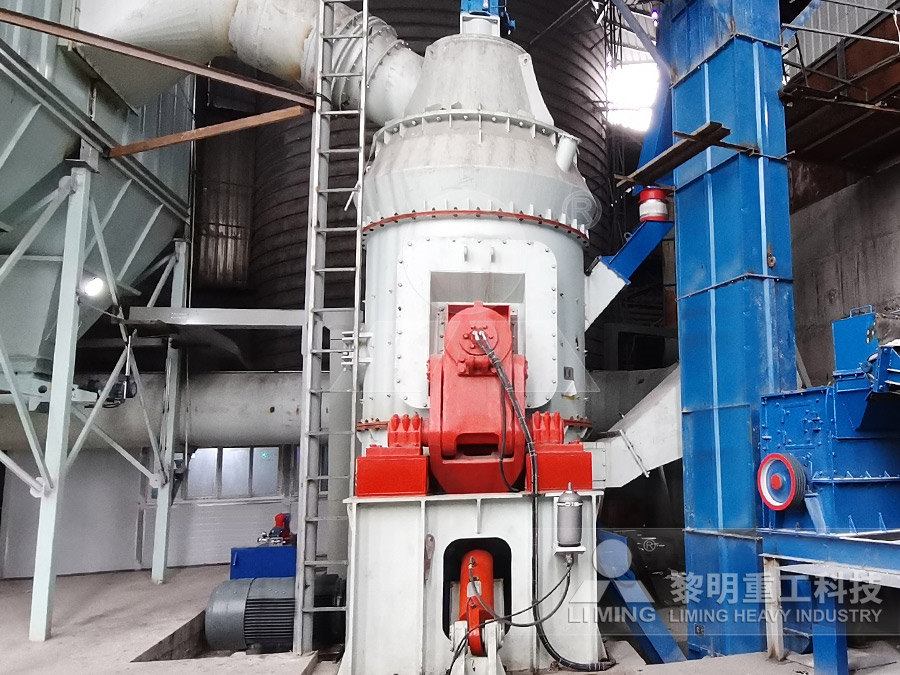
Tool Rotary Assisted EDM Processing of SKD61 Steel: Influence
2022年5月1日 Tool Rotary Assisted EDM Processing of SKD61 Steel: Influence and Optimizing of Main Process Parameters and Surface Roughness May 2022 DOI: 101007/978303099666648Zou et al [118] used EDM to treat alloys to study the effect of EDM parameters on the degree of amorphous of the alloys surface The results showed that both the pulse width and the pulse interval affected the surface amorphous significantly The optimal process parameters were the pulse width of 64 μ s, the pulse interval of 4 μ sElectrical Discharge Machining an overview ScienceDirect TopicsThus, the manufacturing process will be carried out efficiently and quickly when the processing parameters are optimized In research into this area, discharge current (Ip), pulse on time (Ton Process parameters and performance measures of EDM2022年9月30日 In this book chapter a review and critical analysis on current research trends in wire electrical discharge machining (WEDM) and relation between different process parameters including pulse on time, pulse off time, servo voltage, peak current, dielectric flow rate, wire speed, wire tension on different process responses include material removal rate (MRR), Analysis and Optimization of Process Parameters in Wire
.jpg)
Effects of processing parameters on processing performances
2020年11月16日 To improve the processing efficiency and precision of microholes with a large depthtodiameter ratio on titanium alloy, ultrasonic vibrationassisted microelectrical discharge machining (microEDM) is adopted It could improve the effective discharge ratio in the machining process and promote the removal of erosion products Compared with the nonultrasonic 2022年1月12日 In particular, the multiobjective problem consists of two single objectives including the surface roughness (SR) and the electrode wear rate (EWR) In addition, four main parameters of EDM process including the pulse time, the pulse off time, the current, and the servo voltage were selected for this studyEffects of EDM Parameters on Surface Roughness and Electrode 2009年12月1日 In this work, response surface modelling (RSM) is utilized for determining the relations between the various EDM process parameters with the various machining criteria and exploring the effect of these process parameters on the responses, ie the material removal rate, electrode wear ratio, gap size and the surface finishStudy of the parameters in electrical discharge machining through 2022年9月30日 The Taguchi optimization technique proposes the quality engineering method, it provides the novel approaches for testing [], and this method is used to design parameter performs to reduce the different causes of variation on the main quality of features of the product []The S/N ratio has been derived using the Taguchi method, and in this S/N ratio, signal Optimization of Process Parameters in WEDM with HCHCR by
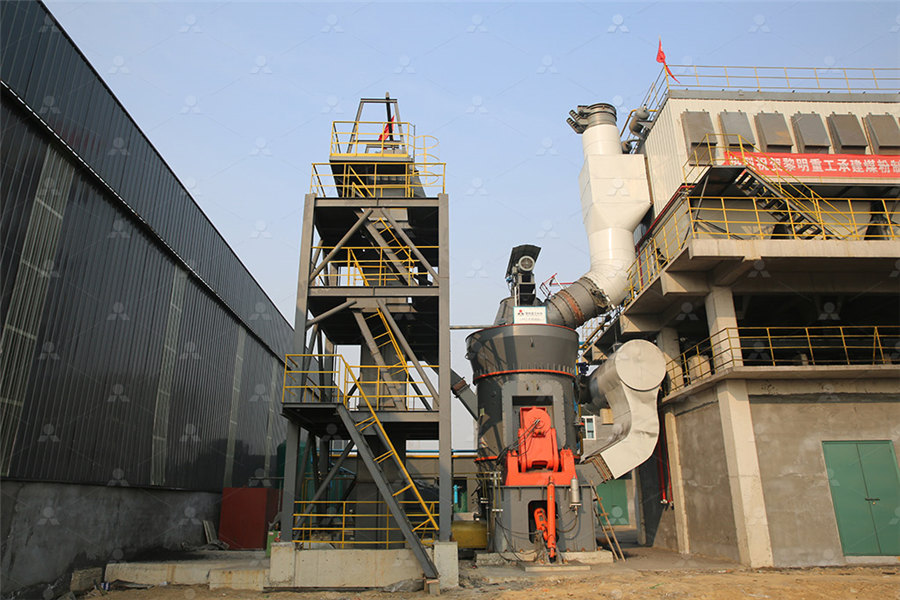
Optimization design for diesinking EDM process
2023年10月12日 In EDM, selecting processing parameters is critical for producing parts with good surface quality while saving processing time and costs (Jeevamalar Ramabalan, Citation 2015; Kumar et al, Citation 2021; This study explores how machining parameters affect Surface Roughness (SR), Tool Wear Rate (TWR), and Material Removal Rate (MRR) during Electrical Discharge Machining (EDM) of a hybrid aluminum metal matrix composite Process parameters optimization of EDM for hybrid 2021年1月14日 Kumar A, Soota T, Kumar J (2018) Optimisation of wirecut EDM process parameter by greybased response surface methodology J Ind Eng Int 14(4):821–829 Article Google Scholar Bhatt D, Goyal A (2019) ScienceDirect Multiobjective optimization of machining parameters in wire EDM for AISI304 Mater Today Proc 18:4227–4242Optimization of EDM Process Parameters: A Review of Technique, Process 2023年4月24日 Electrical discharge machining (EDM) can use soft tool electrodes to process hard workpieces to achieve “soft against hard”, because it directly uses electrical energy and thermal energy to remove metal materials Then, it can generate complex features on harder materials and meet the requirements of excellent surface quality Since EDM involves many Parameters Optimization of Electrical Discharge Machining Process
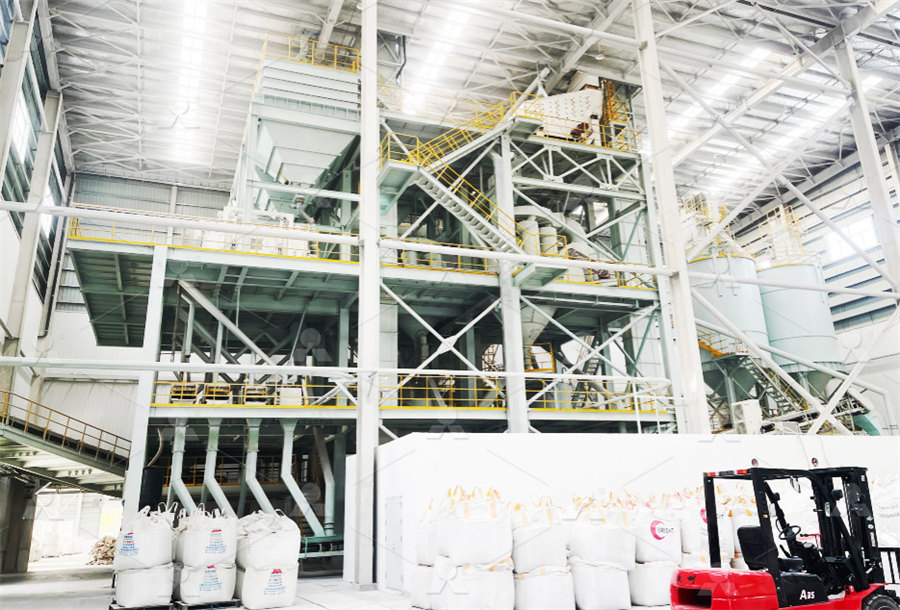
(PDF) Influence of process parameters of wire EDM on
2021年5月1日 The optimum Wire EDM process parameters for machining of Ti6Al4V was concluded as low feed rate, high voltage and high wire speed within the limits of parameters considered for the studyWire electrical discharge machining has become an important nontraditional machining process, as it provides an effective solution for producing components made of difficulttomachine materials like tungsten carbide, titanium, zirconium etc, and intricate shapes, which are not possible by conventional machining methods This research paper deals with Response [PDF] OPTIMIZATION OF PROCESS PARAMETERS IN WIREEDM 2020年3月6日 In the present research, different electrical discharge machining (EDM) process parameters are investigated on alloyed tool steel Several experiments are conducted to investigate the effect of four process parameters, ie, peak current (I p), pulse ontime (T on), polarity, and electrode material, on the machining processThe machining process is evaluated Effects of Process Parameters on the Machining Process in Die To improve the processing efficiency and precision of microholes with a large depthtodiameter ratio on titanium alloy, ultrasonic vibrationassisted microelectrical discharge machining (microEDM) is adopted It could improve the effective discharge ratio in the machining process and promote the removal of erosion products Compared with the nonultrasonic vibrationassisted Effects of processing parameters on processing performances of
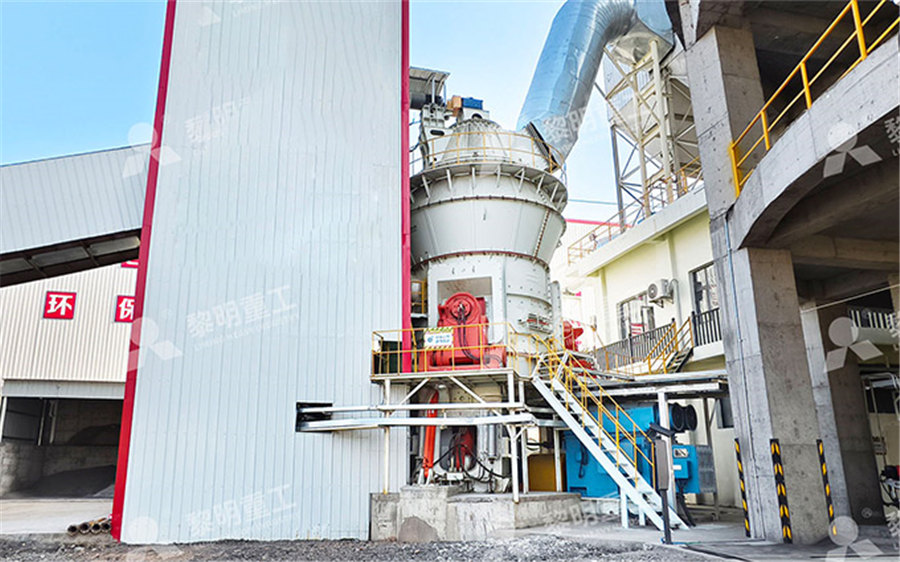
(PDF) Optimization Design for Diesinking EDM Process Parameters
2024年10月7日 Electrical discharge machining (EDM) is a highly regarded method for producing ultraprecise mechanical parts In this study, the process parameters of diesinking EDM using copper electrodes and 2022年8月8日 Imagine pressing a metallic object into clay The clay assumes the negative shape of the metallic object The die sinking EDM process works the same way When people talk about electrical discharge machining, this is the Electrical Discharge Machining EDM Process 2024年9月5日 Materials After conducting a comprehensive review of the existing literature on the parametric optimization of Electrical Discharge Machining (EDM) parameters for various materials and alloys Multiobjective optimization of an EDM process for Monel K500 2004年5月15日 Journal of Materials Processing Technology Volume 148, Issue These properties vary with different levels of the main process parameters The aim of this paper is to present experimental work that has been done in order to quantify the effect of some of the main EDM parameters on the surface texture 3D surface measurements Effect of EDM process parameters on 3D surface topography
.jpg)
Optimization of EDM Process Parameters through Teaching Learning
process has been observed to be difficult to establish [1, 2] The favourable EDM process parameters selection is required for obtaining the best machining performance by increasing the production rate at the same time reducing the machining time The process parameters are generally determined based on experience or on handbook valuesInfluence of EDM process parameters in deep hole drilling of Inconel 718 Thermal modeling of the material removal rate and surface roughness for diesinking EDM Effect of ultrasonicassisted EDM on the surface integrity of cemented tungsten carbide (WCCo) AISI H13 tool steel AISI P20 Tool Steel Tungsten Carbide Cobalt Composites (WC/Co) Al 2 O 3DIE SINKING EDM PROCESS PARAMETERS: A REVIEW IJMERRMuthuramalingam and Mohan [4], discussed having an overview of the EDM process, modeling of process parameters, and influence of process parameters such as input electrical variables, pulse shape, and discharge energy on performance measures such as material removal rate, surface roughness, and electrode wear rateOptimization of EDM Process Parameters: A Review2024年1月30日 What Are the Technological Parameters in EDM? Electrical Discharge Machining (EDM), a marvel of modern manufacturing, operates on a symphony of technological parameters Each parameter plays a pivotal role in ensuring the EDM process is both effective and efficient Understanding these parameters is key to mastering EDM’s potentialWhat is Electrical Discharge Machining: EDM Definition, History,
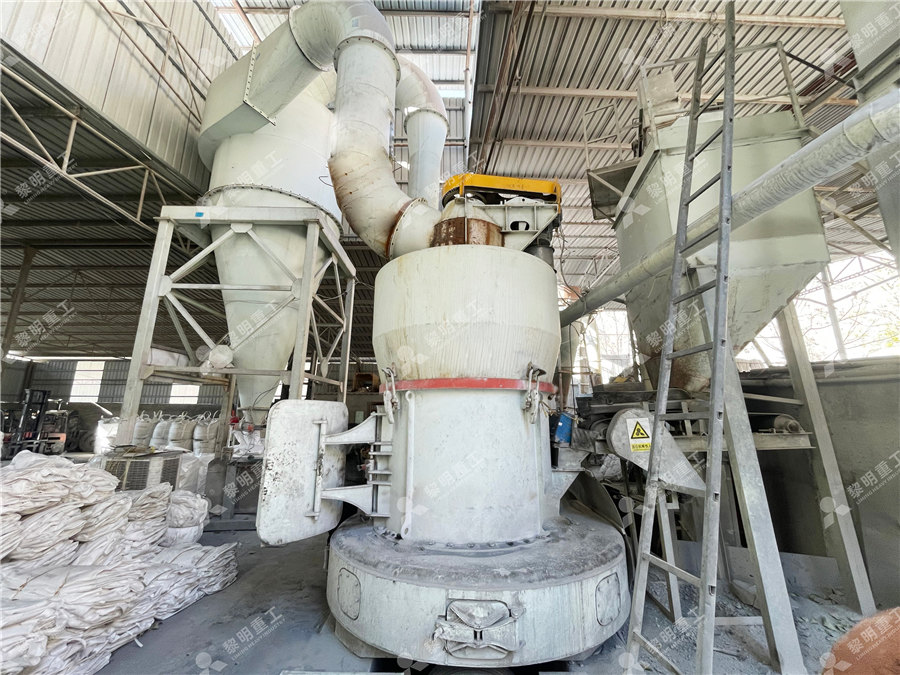
Effect of process parameter on wire cut EDM using RSM method
2023年6月23日 The article aims to estimate the importance of machining parameters for the performance measure material removal rate (MRR) in the Wire Electrical Discharge Machining (WEDM) processing of MONEL 400 K Wire feed, Time On and Time Off (downtime) have been discovered to be more impactful in deciding the MRR criterion substantially The significant 2013年9月1日 Request PDF Role of multiwall carbon nanotubes on the main parameters of the electrical discharge machining (EDM) process Electrical discharge machining is a very accurate nontraditional Role of multiwall carbon nanotubes on the main parameters of 2015年1月1日 Jahan et al conducted a detailed experimental investigation to find out the influence of major operating parameters on surface quality of tungsten carbide with both transistor and RCtype generators in EDM process [5]It has been proved that RC pulse generator has produced a smoother surface finish than the transistor pulse generator due to its lower A review on influence of electrical process parameters in EDM process 2022年1月1日 The main focus of the researcher is obtaining maximum metal removal rate and minimizing the tool wear with better surface quality This paper identifies major academic study done on improvising process performance, optimizing process parameters, and the growth of Analysis of Output Parameters of EDM: A Review SpringerLink
.jpg)
Enhanced machining features and multiobjective optimization of
2022年4月6日 There is a high roughness and tool wear rate (TER), and a minimal material erosion rate (MER) when 316L steel is machined through conventional or conductive powder mixed electrodischarge (EDM) processes Since the required machining outputs are primarily dependent on process parameters due to their fluctuating nature during the operation, a 2021年2月25日 Not everything can be done with wire EDM processing Analyze and review the processing drawings According to the existing processing equipment, consider the feasibility of this process method Processing cannot 6 Steps Of Wire EDM Processing SANS2012年8月1日 In this work the effect of process parameters has been studied on EDM process using ultrasonic assisted cryogenically cooled electrode (UACEDM) during machining of M2 grade high speed steel Electrode wear ratio (EWR), material removal rate (MRR) and surface roughness (SR) were considered as the process responsesEffect of process parameters on the performance of EDM process 2024年1月3日 The need to optimize the process parameters in Electrical Discharge Machining (EDM) for aged AA7075 Metal Matrix Composites (AAMMCs) is evident as it impacts various aspects such as mechanical Optimization on the electrical discharge machining (EDM) process
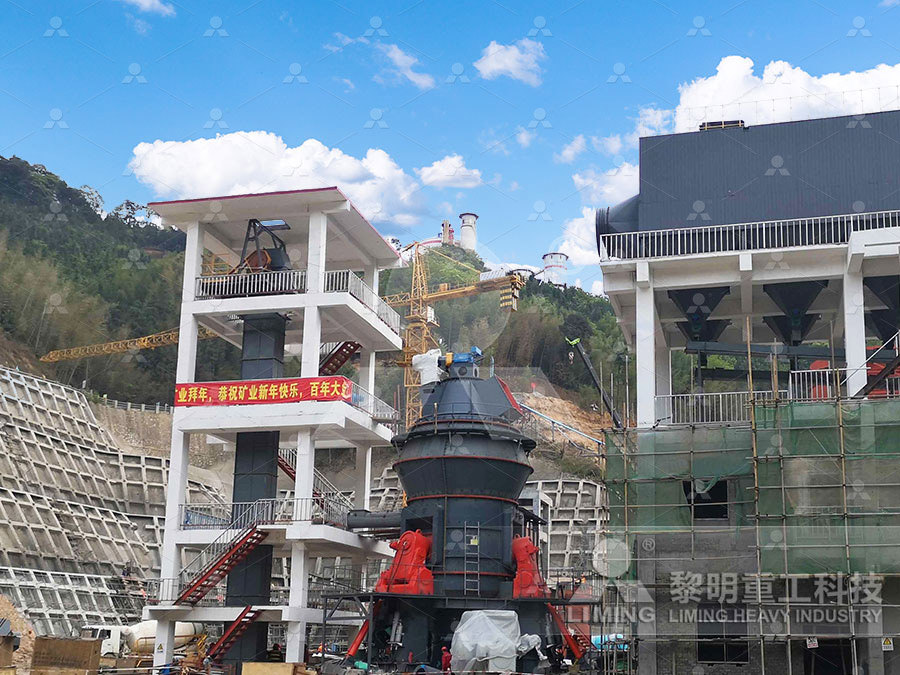
Influence of input parameters on characteristics of EDM process
electrodes in EDM process Due to this wear, tool loses its dimensions resulting in inaccuracy of the cavities formed on the workpiece Consequently, during the EDM process, the main machining output parameters are the material removal rate (MRR), tool wear ratio (TWR) and surface roughness (R a) of the workpieceWire EDM is a precise and efficient manufacturing route in many applications In the present research, TAGUCHI METHOD was used for analysis of effect of wire EDM process parameters on material Optimization of process parameters in wirecut EDM of Inconel 2015年1月1日 Since the thermal energy produced in electrical discharge machining process is due to the applied electrical energy, it is very important to enhance the electrical process parameters to improve the process efficiency The present study discusses about having an overview of the EDM process, modeling of process parameters, and influence of process A review on influence of electrical process parameters in EDM process 2019年11月22日 In this research paper, the effect of process parameters on electrical discharge machining (EDM) of Ti6Al4V has been investigated The process parameters were discharge current, pulse on time Optimization of process parameters on EDM of titanium alloy
.jpg)
Optimization of Process Parameters During EDM on Inconel
2020年8月20日 31 Effect of EDM Parameter on MRR Figure 4 shows the main effect plots of MRR With an increase of current, voltage and Ton time, the MRR is increased As current and voltage increased, the power and number of sparks produced were increased this