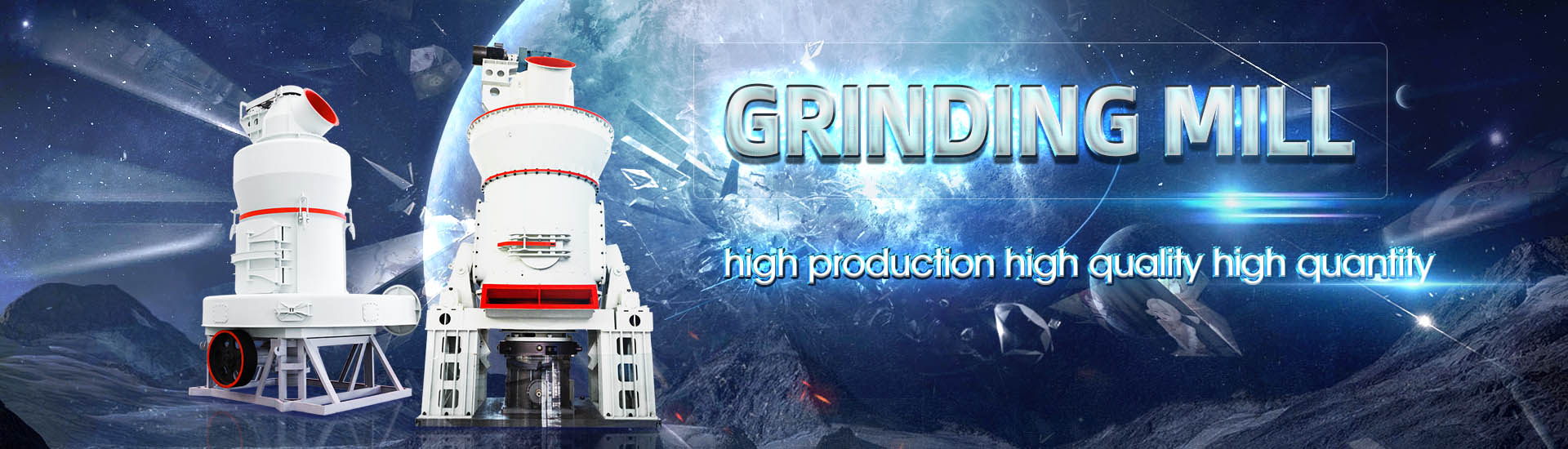
HOME→How much sponge iron is produced from 1 ton of iron oxide How much sponge iron is produced from 1 ton of iron oxide How much sponge iron is produced from 1 ton of iron oxide
How much sponge iron is produced from 1 ton of iron oxide How much sponge iron is produced from 1 ton of iron oxide How much sponge iron is produced from 1 ton of iron oxide
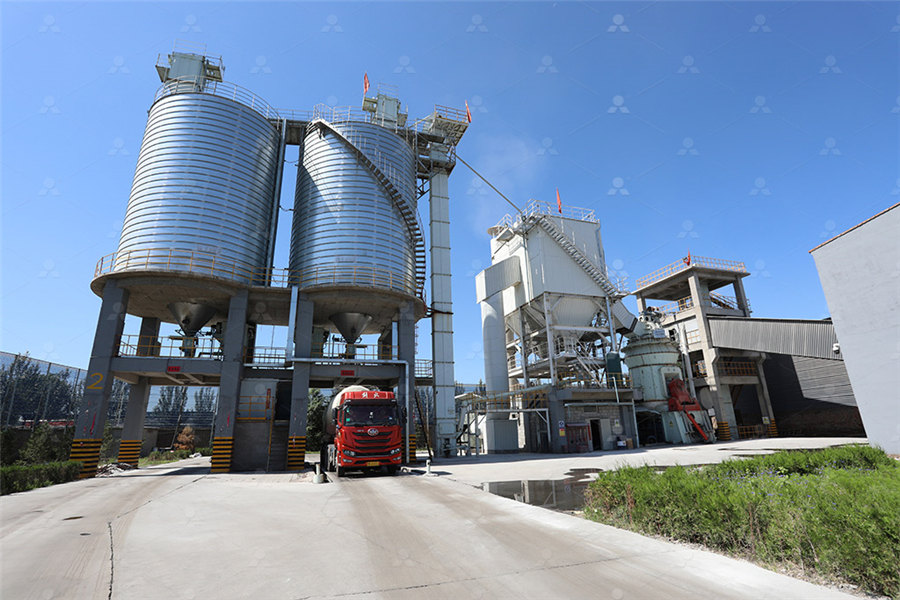
Direct reduced iron Wikipedia
Direct reduction refers to solidstate processes which reduce iron oxides to metallic iron at temperatures below the melting point of iron Reduced iron derives its name from these processes, one example being heating iron ore in a furnace at a high temperature of 800 to 1,200 °C (1,470 to 2,190 °F) in the presence of 展开2017年10月17日 Direct iron reduction processes produce a form of sponge iron called direct reduced iron (DRI) Smelting reduction and direct iron reduction From Ore to Iron with Smelting and Direct Iron India is the largest producer of direct reduction of iron (DRI), popularly known as sponge iron and accounted for about 393% of the global production in 2020 India’s growing economy will ENERGYEFFICIENT TECHNOLOGY OPTIONS FOR DIRECT 2016年3月30日 During the last four decades, a new route of ironmaking has rapidly developed for direct reduction (DR) of iron ore to metallic iron by using noncoking coal/natural gas This (PDF) i) Direct Reduced Iron: Production ResearchGate
.jpg)
Sponge Iron Production By Direct Reduction Of Iron Oxide
This book provides a fascinating study of the very important emerging field of direct reduction in which iron ore is ‘directly reduced’ in the solidstate, using either natural gas or noncokingDRI, also known as sponge iron, is the product of reducing iron oxide in the form of iron ore and steel plant wastes into metallic iron, below the melting point of iron and typically in the range of Sponge Iron an overview ScienceDirect Topics2020年3月3日 Forms of sponge iron, characteristics of sponge iron and reoxidation of sponge iron are described Uses of sponge iron are also discussed Processes that produce iron by Sponge Iron SpringerLink2023年10月17日 Sponge iron adopts direct reduction ironmaking method to obtain iron with spongelike pores inside Sponge iron is produced by lowtemperature reduction of iron ore in Sponge Iron SpringerLink
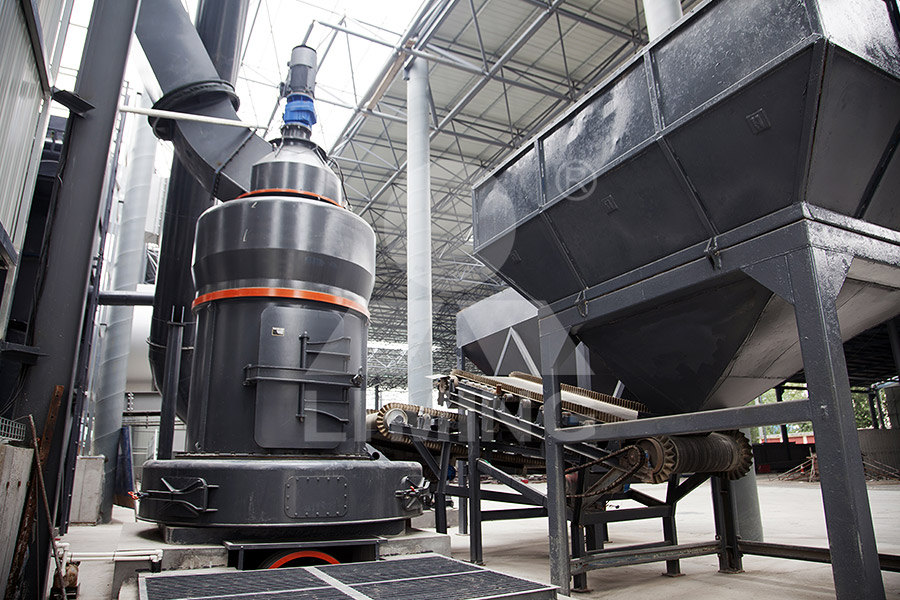
Direct Reduction of Ferrous Oxides to form an IronRich
Abstract: In this study, production of sponge iron by direct reduction of oxides and the effect of reductant on metallization were investigated In the first stage of the study, scale formed 2018年6月21日 The reduction gases only dissolve oxygen from the iron ores This causes the iron ores to crack on the surface The appearance resembles a porous sponge, which is why the deoxidized and thus strongly ferrous iron ore Direct reduced iron process tecscience2020年3月3日 1 Less capital cost: The capital cost per tonne of installed capacity, in case of coalbased plants, is 18–2 times as high as in the gasbased plants 2 High productivity: The throughput rates for gasbased sponge iron plants are much higher than in coalbased plantsThe productivity for gasbased plants can be as high as 11 t/m 3 /day as against merely 05 to 09 Sponge Iron SpringerLink2012年11月1日 For production of 100 ton sponge iron, there are 154 ton of iron ore and 120 ton of (BGrade) coal required The solid waste generated during this process is around 45 ton and out of which 25 ton Characterization of dolochar waste generated by sponge iron
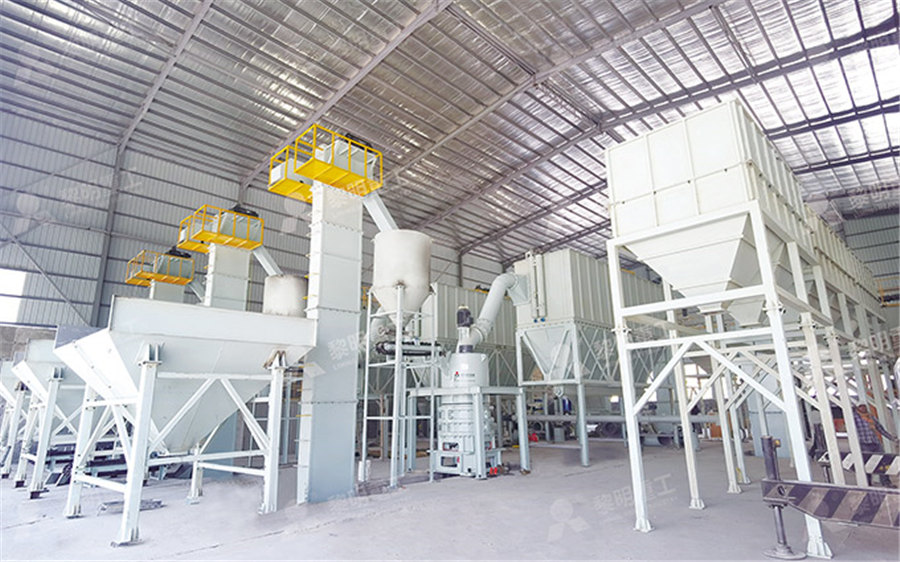
Direct reduced iron Wikipedia
Hotbriquetted iron Direct reduced iron (DRI), also called sponge iron, [1] is produced from the direct reduction of iron ore (in the form of lumps, pellets, or fines) into iron by a reducing gas which contains elemental carbon (produced from natural gas or coal) and/or hydrogenWhen hydrogen is used as the reducing gas no carbon dioxide is producedIron ores consist predominantly of the iron oxide minerals hematite (Fe 2 O 3) and magnetite (Fe 3 O 4)The primary intermixed noniron oxides are SiO 2, Al 2 O 3, MnO, and MgO, and are referred to as gangueBoth pellets and sinter can be produced from a mixture of hematite and magnetite; essentially all the input magnetite is oxidized to hematite when pellets are Overview of the Steel Production Process Springer2016年3月30日 In book: Encyclopedia of Iron, Steel, and Their Alloys (pppp 10821108) Chapter: i) Direct Reduced Iron: Production; Publisher: CRC Press, Taylor and Francis Group, New York(PDF) i) Direct Reduced Iron: Production ResearchGate2019年7月19日 The employed fuels are natural gas and/or coal The energy consumption is in the order of 104 GJ/tDRI that is equivalent to 300 m 3 of natural gas per ton of reduced iron The CO 2 emissions are quantified in the range 077–092 t of CO 2 per ton of steel As a function of the employed reducing reactors, the systems are of four main types:Direct Reduced Iron: Most Efficient Technologies for Greenhouse
.jpg)
Hydrogen Ironmaking: How It Works MDPI
2020年6月3日 A new route for making steel from iron ore based on the use of hydrogen to reduce iron oxides is presented, detailed and analyzed The main advantage of this steelmaking route is the dramatic reduction (90% off) in CO2 emissions compared to those of the current standard blastfurnace route The first process of the route is the production of hydrogen by PIG Iron It is a semifinished metal produced from iron ore in a blast furnace It has 92%iron in it with high amounts of carbon (typically up to 35%), and the balance includes mostly manganese and silicone with small amounts of phosphorus, sulfur, and some other impuritiesRaw Material for Steel, PIG Iron, Sponge Iron, Steel Scrap, 2023年10月2日 Hydrogenbased reduction of iron ores is the key technology for future sustainable ironmaking, to mitigate the CO2 burden from the steel industry, accounting for ~7–8% of all global emissionsHow much hydrogen is in green steel? npj Materials Özge Özgün1,XuLu2, Yan Ma 1 and Dierk Raabe 1 Hydrogenbased reduction of iron ores is the key technology for future sustainable ironmaking, to mitigate the CO 2 burden fromHow much hydrogen is in green steel? Nature
.jpg)
A review of ironmaking by direct reduction processes: Quality
2019年1月1日 ScienceDirect Available online at sciencedirect Procedia Manufacturing 35 (2019) 242–245 23519789 © 2019 The Authors Published by Elsevier BV Peerreview under responsibility of the organizing committee of SMPM 2019 101016/jpromfg201905034 101016/jpromfg201905034 23519789 © 2019 The Authors2023年10月10日 Sponge Iron – Where Is It Used? Sponge Iron plant manufacturers in India use sponge iron as a substitute for scrap in induction and electrical furnaces The reason for this is that melting scrap is expensive and also in short supply, so sponge iron is the perfect alternative when it comes to using it in the production of highquality steelAll About The Production Of Sponge Iron Sree Metaliks2017年10月10日 Fe 3 O 4 decomposes when heated to ferrous oxide (FeO) and ferric oxide (Fe 2 O 3) via Fe 3 O 4 → FeO + Fe 2 O 3 A specialized type of coal, called hard coal, is used to make coke, a porous form of carbon Coke is a reductant or a chemical that can reduce iron oxide to iron metal – especially when combined with heat and oxygenIronmaking 101 – From Ore to Iron with Blast Furnaces2015年9月1日 Considerable amount of heat is lost in the waste gas which is about 435% of the heat generated in the kiln Sponge iron containing 925% total iron could be produced with FC/Fe(T) ratio of 0381 It is the fact that the coal consumption per ton sponge iron produced increases when the retention time decreases, since the loss of waste gas increasesEnergy survey of the coal based sponge iron industry
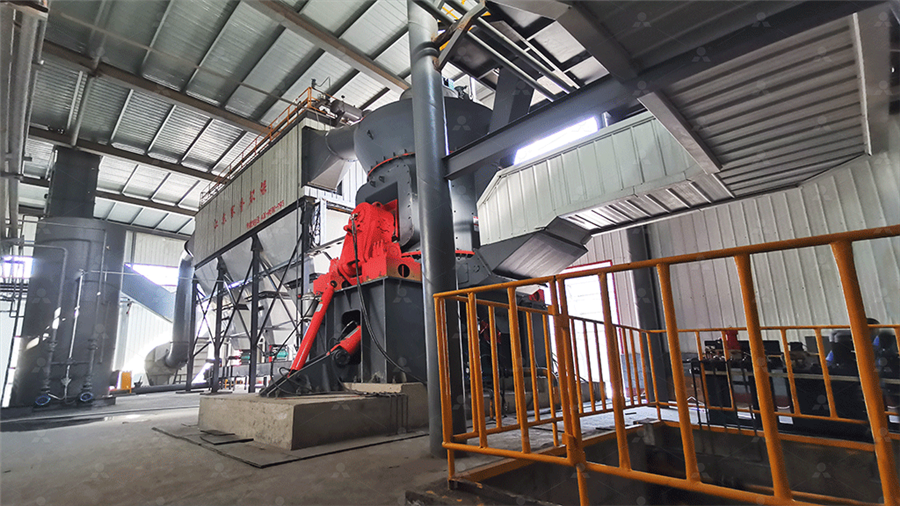
(PDF) Operation of CoalBased Sponge Iron Rotary Kiln to Reduce
2019年6月4日 Data1 includes temperatures profiles and air inlet at positions, AT1 to AT3 and MF1 and MF2, inside the kiln whereas, flow rates of iron ore, feed coal, slinger coal and sponge iron is Sponge Iron Ferro Alloys 2 CONTENTS SlNo Chapter Name Page No 1 Review of sponge iron making process 313 2 Thermodynamics of Sponge Iron making 1418 3 Parameters of Sponge Iron making 1925 4 Plant operating parameter 2630 5 Environmental management in DRI 3133LECTURE NOTES ON Sponge Iron Ferro Alloys KIIT PolytechnicThis book provides a fascinating study of the very important emerging field of direct reduction in which iron ore is ‘directly reduced’ in the solidstate, using either natural gas or noncoking coal, to produce a highly metallised material, referred to as sponge iron (or direct reduced iron) This intermediate product is subsequently melted in electric arc furnaces or induction furnaces Sponge Iron Production By Direct Reduction Of Iron OxideDaily Metal Price: Iron Ore Price Chart (USD / Metric Ton) for the Last Year Chart daily metal price movements in multiple units Daily Metal Prices Toggle navigation All Metals Aluminum; Cobalt; Copper; Gallium; Gold; $14138 lb: 11/29 Nov 29, 2024: More Metal Prices Free Metal Price Charts Widgets for Your Website;Daily Metal Price: Iron Ore Price Chart (USD / Metric Ton) for the
.jpg)
Sponge Iron Production Process Arij Trading
Sponge iron production process The sponge iron production process discussed herein is selected from known methods, the references of which are available and referable We look at the four different methods of producing sponge iron: Midrex process; HYL process (4th generation) or Energiron; SL / RN process; Tunnel furnace process 1) Midrex process2015年12月1日 The direct reduction process has commonly been used by many companies to obtain metallic iron powder by the reaction of iron oxide (magnetite, hematite ore or mill scale) and reducing gases (CO/H 2) at high temperatures Direct Reduction of Ferrous Oxides to form an Iron 2021年4月7日 Today, it is estimated that the global steel industry used about 2 billion tonnes of iron ore, 1 billion tonnes How much iron ore is needed for 1 tonne of steel rebar? Steel is around 95% Iron Steel is around 95% iron The amount of iron ore it takes to produce 1 ton of steel is dependent on the iron content of your iron oreHow much steel is produced from a ton of iron ore?the fourth consecutive record year for annual growth in DRI production (see Figure 1) 1 DIRECT REDUCTION OF IRON ORE 0 400 800 1200 1600 2000 2010 2019 Iron Production (Mt) Pig iron Direct reduced iron Figure 1: Iron production, 2000, 2010, 2019 Source: (WSA, 2020) India is the country with the largest DRI production, reaching 34 Mt in 2019 GREEN STEEL THROUGH HYDROGEN DIRECT REDUCTION
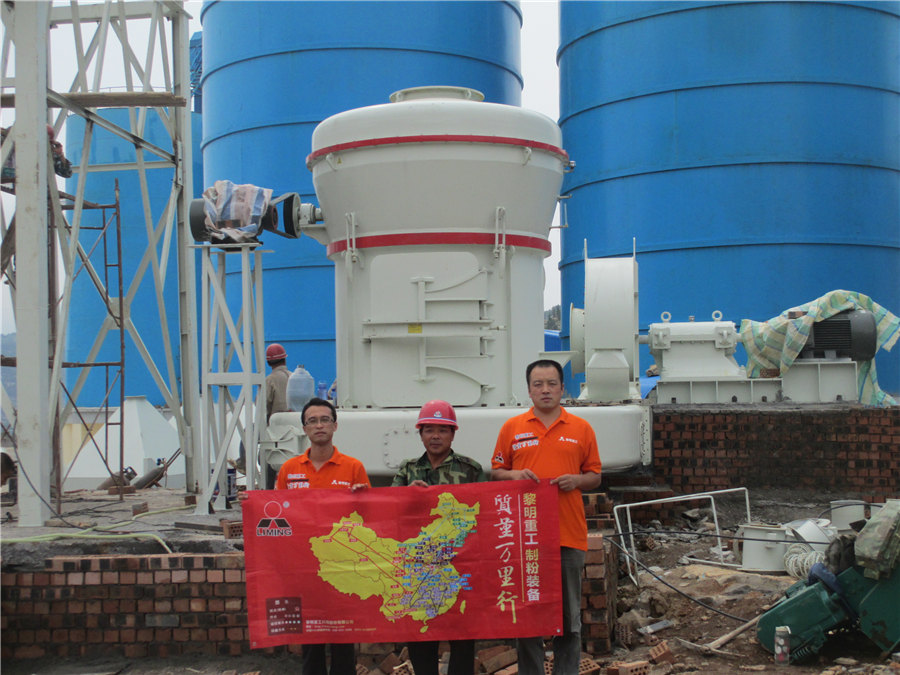
Iron Ore Pellet an overview ScienceDirect Topics
31 Iron tailings311 Iron tailings composition and status Iron tailings are wastes produced in the process of beneficiation of iron ore concentrates (Tang et al, 2019b) It is estimated that 400 kg tailings per ton selected iron ore will be produced (Dauce et al, 2019)2023年10月17日 Sponge iron is produced by lowtemperature reduction of iron ore in a rotary furnace, shaft the smelting cycle is short, and the output is high However, when the sponge iron is used excessively, more slag and iron oxide need to be reduced, which will increase energy consumption Further Reading Wang XL (2013) Ferrous Sponge Iron SpringerLinkSponge Iron Manufacturers Association The Sponge Iron Manufacturers Association (SIMA) established in 1992 is an all India apex body of Indian sponge iron industry It is the voice of the indian iron ore based sponge iron steel industry, at both domestic and global forumsSponge Iron Manufacturer India2023年10月9日 Midrex process has high efficiency in heat transfer and mass transfer, low energy consumption (105 GJ per ton of sponge iron), high yield, high synthetic natural gas, and coal made gas were used as reducing gas for reduction of iron oxide In 2017, the output of direct reduction iron produced from HYL process accounted for Direct Reduction Ironmaking SpringerLink
.jpg)
Fact sheet Hydrogen (H2)based ironmaking
Carbon combines with the oxygen in the iron ore, producing metallic iron and a carbonrich process gas, according to the following simplified chemical reaction: 2Fe 2 O 3 + 3C > 4Fe + 3CO 2 It is also possible to reduce iron ore using hydrogen instead of carbon; in this case the waste gas produced is water, as per the following reactions:2019年12月12日 How much iron ore is needed for 1 tonne of steel rebar? Steel is around 95% Iron Steel is around 95% iron The amount of iron ore it takes to produce 1 ton of steel is dependent on the iron content of your iron ore The most heavily referenced iron ore indices (TSI, Platts) take to a 62/63% iron ore standard How is iron ore converted to steel HM?How much iron ore does it take to make a ton of steel?u While the produced DRI is mainly used as the raw material of electric steelmaking, Gulf sponge iron (UAE) ・Suez Steel (Egypt) ・Nucor (USA) ・JSPL (India), etc (When 100 kg of DRI is used for the production of 1 ton of molten iron, CO 2 emission (including that from the DRI production plant) will be reduced by 50 100 kg)Direct Reduced Iron (DRI) Production Plant2024年7月29日 What is sponge iron Sponge iron, also known as DRI (direct reduced iron or direct reduction iron), bulk density 1619g/cm3, apparent density 3436g/cm3, typical size 420mm, is a kind of material produced by the DRI briquetting, sponge iron briquette making – why
.jpg)
HighQuality Sponge Iron Manufacturing by Lloyds
Sponge Iron We are the leading manufacturer of Directreduced iron (DRI), also called sponge iron, which is produced from the direct reduction of iron ore (in the form of lumps, pellets, or fines) by a reducing gas produced from natural gas 2023年7月15日 An integrated steel plant plays an important role in India’s economic growth with a positive impact on country’s GDP The contribution of iron and steel sector towards India’s GDP is around 2% which is quite high []India is the second largest producer of crude steel after China with a market share of almost 6% []India has produced around 1112 million tons in 2019 [] to Utilization of Some of Major Steel Plant Wastes to Produce Metallic IronDiscover the benefits of sponge iron (DRI), its high iron grade, About 663% of the world’s crude steel is produced by the blast furnace method, standards, requires at least 15 tons of iron ore and 450 kg of metallurgical coke, sometimes increasing to 3 tons of iron ore and 1 Brief introduction of Sponge Iron Arij Trading2023年4月5日 This implies the rate of reaction will be faster in the iron oxide/methane reduction reaction as the burning of methane gas in the absence of air produces a chemical loop of CO and H 2 which makes the reduction reaction of iron oxide to iron proceed much faster into completion compared to when using the individual reducing gas (ie CO and H 2)Recent Trends in the Technologies of the Direct Reduction and
.jpg)
Scrap use in the steel industry
production avoids the emission of 15 tonnes of CO 2 and the consumption of 14 tonnes of iron ore, 740kg of coal and 120 kg of limestone3 How much scrap is used? All the scrap that is available to the steel industry is used repeatedly to create new steel Recycled steel maintains the inherent properties of the original steel and the quality canthree decades India, entered the sponge iron industry only in 1980, when the coal based DRI plant of Sponge Iron India Limited (SIIL) was commissioned at Kothagudem, in Andhra Pradesh 2 The reasons for the tremendous growth of the sponge iron industry world over could be attributed to the advantages of using sponge ironEXECUTIVE SUMMARY DSIRDirect reduction of iron is the removal of oxygen from iron ore or other iron bearing materials in the solid state, ie without melting, (total 1081 million tonnes); gasbased fluidized bed processes (the Finmet / Finored process being the only commercial scale one in operation) accounting for 02% of 2019 DRI production;DRI production International Iron Metallics AssociationTo produce 1 ton of DRI, we use 135 tons of iron ore raw materials, 400 m3 of natural gas and spend extra US$5070 To produce 1 ton of pig iron, we use 15 tons of iron ore raw materials, 05 tons of coke and and spend extra US$5070 Let us compare the theoretical costs of DRI and pig iron production as well as market prices of pig iron and Directreduced iron URMCompany
.jpg)
Lowcarbon production of iron and steel: Technology options,
2021年4月21日 We recognize that EAF can take feedstock from DRI sponge iron (eg, India Iran), BF pig iron (eg, China), and steel scraps (most Organization for Economic Cooperation and Development [OECD] countries) and process them together 10 Similarly, the DRI carbon footprint will vary if syngas is produced from a coalbased process or gasbased process 15