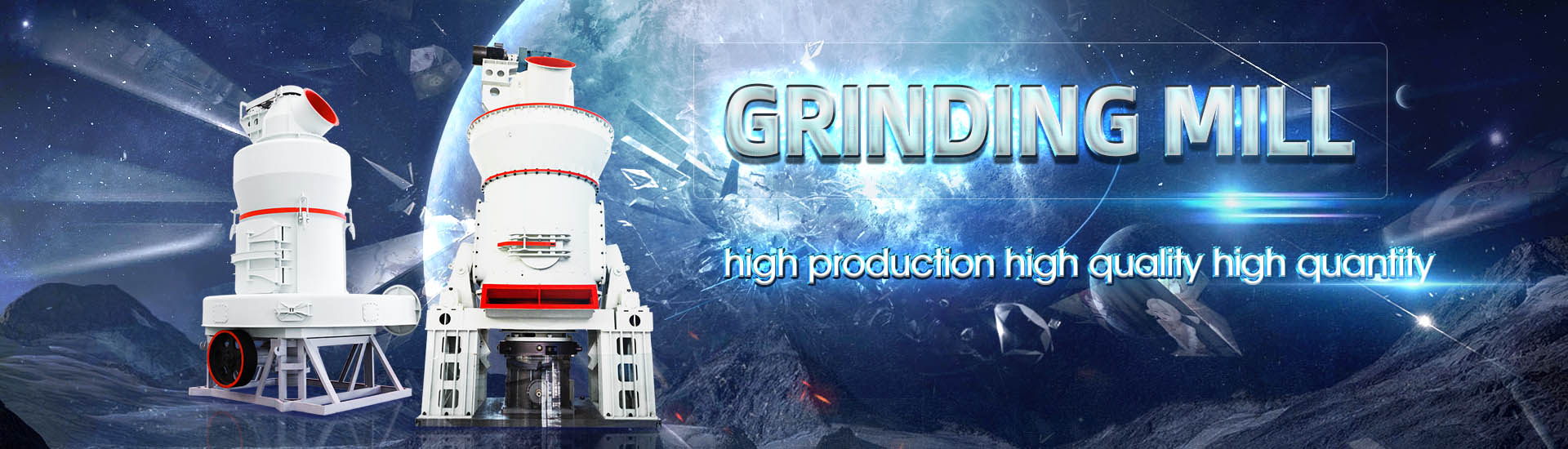
Cobalt ore ultrafine grinding
.jpg)
Flowsheet design and environmental impacts of cobalt coproduct
2023年12月1日 Pressure leaching, roasting, ultrafine grinding, and three crude products examined Results used to inform process selection based on sustainability criteria The 2023年7月20日 Ultrafine grinding process is to produce ultrafine ore particles There is no unified standard for the size of ultrafine particles, but it is generally believed that the ultrafine Ultrafine Grinding Process SpringerLink2023年7月1日 Ultrafine grinding of the ore (d 80: 3 µm) also enhanced the leaching of cobalt whilst increasing the solids ratio led to poor metal extractions The current findings have Extraction of cobalt from a cobaltiferrous pyrite concentrate using 2023年7月20日 According to the particle sizes of grinding products, the grinding process is divided into coarse grinding, medium grinding, fine grinding, microfine grinding, and ultrafine Ore Grinding SpringerLink
.jpg)
Publications Qingqing Huang West Virginia University
Optimization of operating conditions on ultrafine coal grinding through kinetic stirred milling and numerical modeling Powder Technology, 2022 Talan, D, Huang, Q, Liang, L, Song, X 2022年3月1日 A twostep hydrometallurgical method was carried out to prepare ultrafine cobalt powders for the first time The products were characterized by scanning electron microscopy TwoStep Hydrometallurgical Preparation of Ultrafine Cobalt 2015年7月21日 This article discusses the range of application of ultrafine grinding for processing mineral raw materials and presents examples of the successful use of this technology in the Ultrafine Grinding in Contemporary Flow Diagrams for Mineral 2021年1月1日 This paper starts by reviewing the main geometallurgical properties of cobalt ores, with a particular focus on ore mineralogy which exerts a significant control over ore (PDF) Geometallurgy of cobalt ores: A review ResearchGate
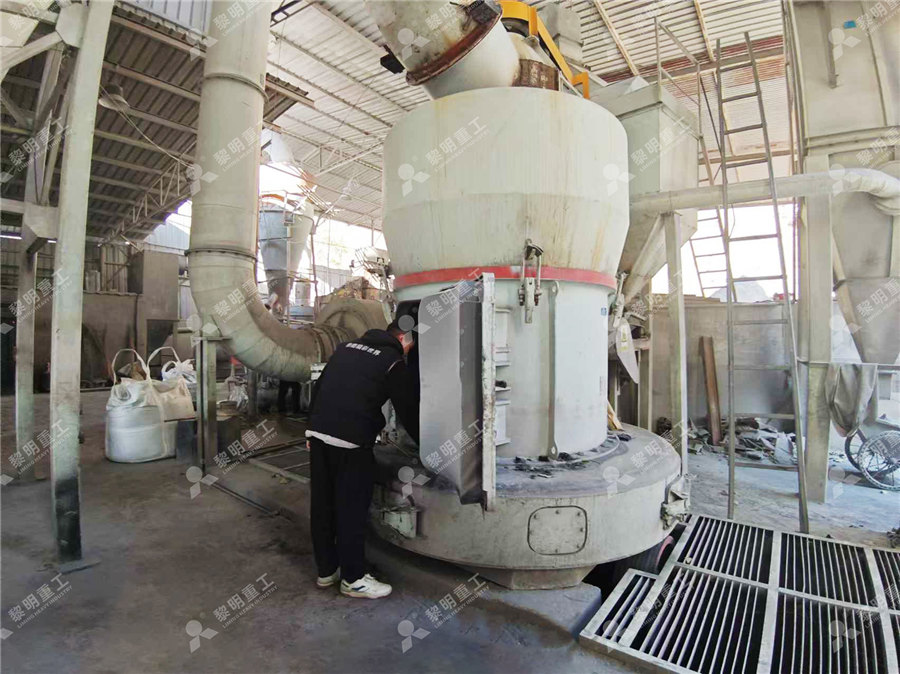
Geometallurgy of cobalt ores: A review ResearchGate
2020年6月25日 This paper starts by reviewing the main geometallurgical properties of cobalt ores, with a particular focus on ore mineralogy which exerts a significant control over ore 2021年9月30日 The mineral composition of copper–cobalt ores is more complex than that of copper sulfides, and it is also difficult to discard tailing efficiently in primary flotation for the finegrained disseminated of ore In this work, a Flotation and Tailing Discarding of Copper Cobalt 2011年12月31日 The extraction of Ni from sulfide ores is much simpler relative to laterites and is dominated by pyrometallurgical processing This typically involves comminution and flotation to produce a nickel Extraction of Nickel and Cobalt from Sulfide Ores2023年7月10日 The present literature review explores the energyefficient ultrafine grinding of particles using stirred mills The review provides an overview of the different techniques for size reduction and the impact of energy EnergyEfficient Advanced Ultrafine Grinding of
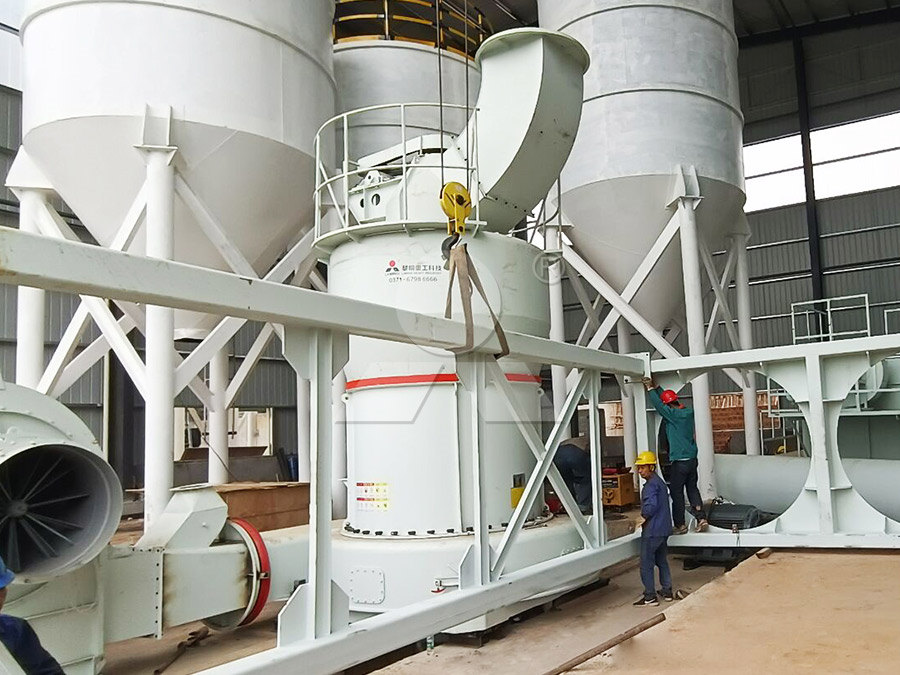
[PDF] Ultra Fine GrindingA Practical Alternative to Oxidative
This paper details the operation of the ultra fine grinding process at KCGM as a non oxidative treatment for the extraction of gold from a refractory ores Since early 2001, Kalgoorlie Consolidated Gold Mines (KCGM) has successfully operated an ultra fine grinding (UFG) circuit to supplement its roaster capacity for the treatment of the refractory gold flotation concentrate2021年9月30日 The mineral composition of copper–cobalt ores is more complex than that of copper sulfides, and it is also difficult to discard tailing efficiently in primary flotation for the finegrained (PDF) Flotation and Tailing Discarding of Copper Cobalt Sulfide Ores 2016年4月1日 In all of these industries, gypsum is needed in ultrafine ground form [2] Grinding has been utilized in manufacturing fine and ultrafine powders for the development of new materials and for improving product quality For a long time, grinding processes, especially in ball mills, have been subjected to statistical and kinetic analysis [3], [4]An experimental study on the ultrafine grinding of gypsum ore 2013年12月18日 Fine grinding, to P80 sizes as low as 7 μm, is becoming increasingly important as mines treat ores with smaller liberation sizes This grinding is typically done using stirred mills such as the Isamill or Stirred Media Detritor While fine grinding consumes less energy than primary grinding, it can still account for a substantial part of a mill’s energy budget Overall Energy Use of Fine Grinding in Mineral Processing
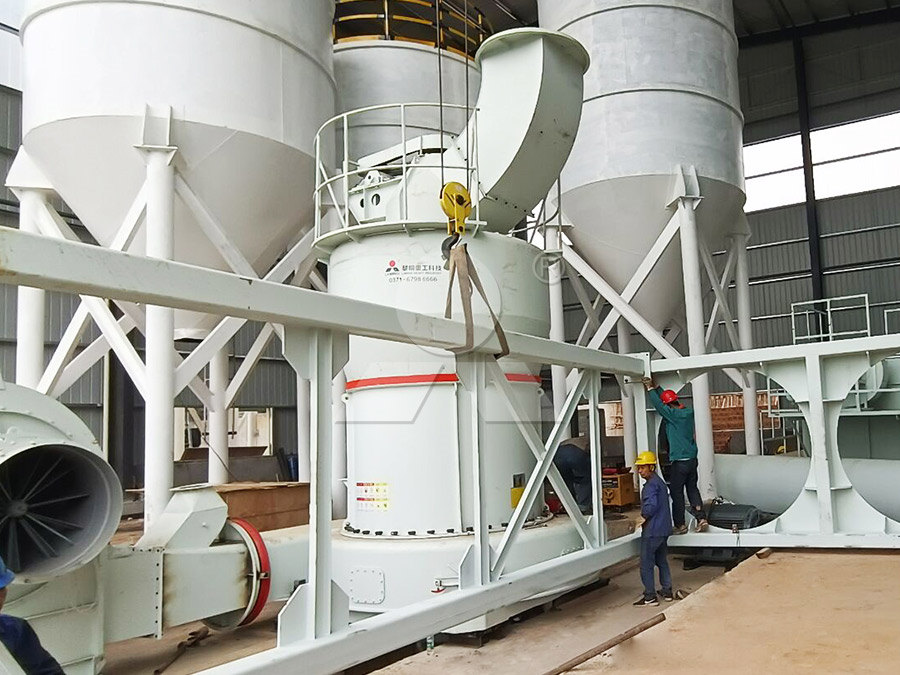
Fine grinding: How mill type affects particle shape characteristics
2017年9月1日 With the continual depletion of high grade simple ore bodies, more complex, finely disseminated ore bodies are being processed, which has led to an increase in the prevalence of fine grinding (Sinnott et al, 2006)This has been evident in the platinum group element (PGE) industry in South Africa, where the Bushveld Complex hosts 70% of global (solvent extraction) The leaching kinetics of oxidised coppercobalt ores strongly depends on the feed particle size distribution [4] Leaching processes of oxidised coppercobalt ores are highly favoured by a fine grinding, usually 65 70 % less than 75 microns For a high talcDetermination and scaleup of the milling parameters of a high IsaMill – The IsaMill is a horizontal disc mill, developed by Mount Isa Mines Ltd and Netzsch and commercialised for ultrafine grinding of ore in 1999 [26] It consists of a horizontal cylindrical chamber, Flowsheet for grinding and leaching of the weathered cobalt–copper oreSemi Autogenous Grinding Mill ScienceDirect TopicsCLUM series of ultrafine gypsum powder vertical grinding mills are a new type of ultrafine industrial ore grinding equipment that integrates grinding, grading, powder collection and conveying +17 [ protected] CLUM Ultrafine Vertical Grinding Mill
.jpg)
(PDF) Geometallurgy of cobalt ores: A review
2021年1月1日 Variability of cobalt ores makes it challenging to develop a single extraction or treatment process that will be able to accommodate all geometallurgical variation Overall, 2018年12月31日 21 ELIDAssisted Conditioning of CoarseGrained Grinding Wheels Dressing of grinding wheels based on the oxidation of the metal bond was initially developed by Ohmori and Nakagawa []Here, the ELID technique was used for the metal bond diamond truer in order to avoid the loading, leading to a continuous and stable conditioning processUltraprecision Machining of Hard and Brittle Materials with DOI: 101016/S10036326(13)628824 Corpus ID: ; Ultra fine grinding of silver plant tailings of refractory ore using vertical stirred media mill @article{Celep2013UltraFG, title={Ultra fine grinding of silver plant tailings of refractory ore using vertical stirred media mill}, author={Oktay Celep and Ersin Yener Yazici}, journal={Transactions of Nonferrous Metals Ultra fine grinding of silver plant tailings of refractory ore using 2024年3月1日 The main influencing factors for grinding damage include abrasive grit size, grinding depth, workpiece feed speed, and wheel speed According to the research of Sabia et al [13], the grinding subsurface damage depth (SSD) of glass ceramics is proportional to 5 times the average abrasive grit sizeMa et al [14] found that the SSD of fused silica is 4–6 times the Optimization of grinding process for hard and brittle materials
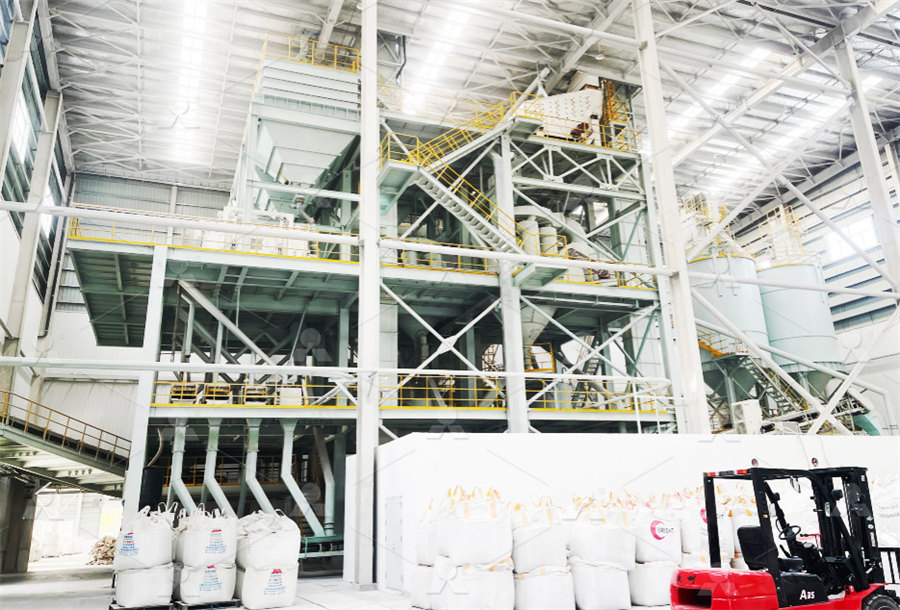
Improvement of Silver Extraction by Ultrafine Grinding Prior to
2014年12月10日 Ultrafine grinding (UFG) was proposed as a pretreatment method prior to cyanide leaching of old plant tailings of a refractory silver ore Direct cyanidation of the asreceived tailings (d80 2015年12月1日 Öksüzoglu and Uçurum [27] studied the ultrafine grinding of gypsum ore in a dry ball mill In their grinding tests, the mill speed was varied from 50 to 90% of the critical speed for gypsum oreAn experimental study on the ultrafine grinding of gypsum ore 2010年12月21日 In the present work, the effects of some key grinding parameters such as ball size (20–40 mm), grinding time (10–30 min), solids content (65–80%), and also ore work index (12–154 kWh/t Optimization of some parameters of stirred mill for ultrafine grinding 2019年12月15日 429 VertiMills Vertical mills were first designed in the 1950s for applications in fine and ultrafine grinding in Japan Lately, the vertical mill is making progress toward primary grind application and shown promise in energy reduction relative to ball mills, typical to what is normally seen in regrinding applications (Mazzinghy et al 2014)Beneficiation of Gold and Silver Ores SpringerLink
.jpg)
Improvement of Cyanidation of Antimonial
PDF On Jan 1, 2010, Celep O and others published Improvement of Cyanidation of Antimonial Refractory Gold/Silver Ores by Ultrafine Grinding in a Stirred Mill Find, read and cite all the Since early2001, Kalgoorlie Consolidated Gold Mines (KCGM) has successfully operated an ultra fine grinding (UFG) circuit to supplement its roaster capacity for the treatment of the refractory gold flotation concentrate A second UFG mill was installed in 2002 taking the total UFG capacity to over 20 tph while grinding to 11 to 12 microns and achieving over 90 per cent gold recoveryUltra Fine Grinding A Practical Alternative to Oxidative2020年11月6日 Simultaneous ultrafine grinding and classification is the widest application of this unit Jet mills may be used to advantage to reduce particle size of solids suspended in liquids, for coating one material with another, and effecting chemical reactions and changes in physical characteristics other than a reduction in sizeUltraFine Grinding and Classification 911MetallurgistMetalmarket analysts project a global nickel supply gap which will be filled by further highpressure acid leach treatment of laterite ores and the commercialization of hydrometallurgical refineries to recover nickel from sulfide ores The Activox® process is one such hydrometallurgical technology developed to recover a range of base and precious metals from sulfide ores and The activox® process: Growing significance in the nickel industry
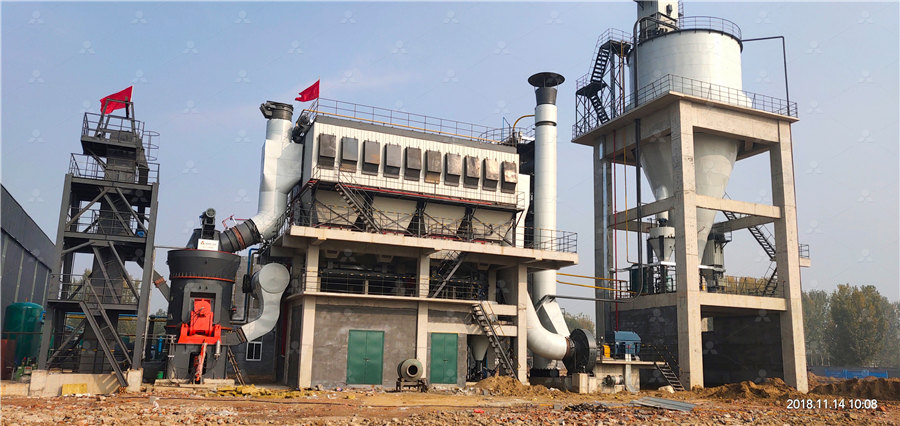
Cobalt Ore an overview ScienceDirect Topics
Nickel and Cobalt Production Michael S Moats, William G Davenport, in Treatise on Process Metallurgy: Industrial Processes, 2014 226 Cobalt from Central African Copper–Cobalt Ores While most cobalt (~ 50%) is produced as a coproduct from the processing of nickel/ cobalt ores, a significant amount of cobalt (~ 35%) is produced from Central African copper–cobalt ores2015年7月21日 This article discusses the range of application of ultrafine grinding for processing mineral raw materials and presents examples of the successful use of this technology in the concentration of polymetallic ores and the hydrometallurgy of gold A description is given of the principle of operation of bead mills and their main technological parameters (the size of the Ultrafine Grinding in Contemporary Flow Diagrams for Mineral (eg magnetic, flotation), iron ore tertiary grinding, precious metal ores, and fine grinding for hydrometallurgical processes Both ceramic and steel beads can be used Ceramic media is typically used for sulphide concentrate regrinding to prevent iron contamination on the sulphide mineral poorer flotation recovery and gradeOutotec HIGmills; A Fine Grinding TechnologyApplication of Knelson Concentrator for Beneficiation of Copper–Cobalt Ore Tailings staged flotation for effectively increasing the recovery of ultrafine copper oxide ore with a new type of collector (ZH1, C35 carbon chain xanthate) A crushing–grinding–flotation system is used to produce a 7–8% cobalt and 25–30% copper bulk Application of Knelson Concentrator for Beneficiation of Copper
.jpg)
SBM Ore Ultrafine Grinding Mill
HGM ultrafine grinding mill can process nonmetallic ores with Mohs hardness less than 7 The equipment has stable operation, simple operation, long service life, low carbon and environmental protection There are 5 models of HGM ultrafine grinding mill, 2023年4月23日 Cobalt (Co) is a chemical element with the atomic number 27 and an atomic mass of 5893 g/mol It is a hard, brittle, and silvergray metal that belongs to the transition metals group in the periodic table Cobalt has a high Cobalt (Co) Ore Properties, Minerals, Occurrence, Ultra Fine Grinding A Practical Alternative to Oxidative Treatment of Refractory Gold Ores S Ellis Kalgoorlie Consolidated Gold Mines Kalgoorlie, WA Abstract Since early 2001, Kalgoorlie Consolidated Gold Mines (KCGM) has successfully operated an ultra fine grinding (UFG) circuit to supplement its roaster capacity for theUltra Fine Grinding A Practical Alternative to Oxidative 2013年11月1日 Ultrafine grinding of the plant tailings of a refractory silver ore was studied using a laboratory type vertical stirred media mill Preliminary tests have confirmed that ultrafine grinding Ultrafine Grinding of Silver Plant Tailings of a Refractory Ore
.jpg)
(PDF) EFFECT OF ULTRAFINE GRINDING ON EXTRACTION OF
2019年4月16日 Ultrafine grinding (UFG) was proposed as a pretreatment method prior to cyanide leaching of old plant tailings of a refractory silver ore Direct cyanidation of the asreceived tailings (d80 2022年12月28日 The crushing and grinding process of cobalt ore can refer to the crushing and grinding process of lithium ore Coarse crushing equipment — jaw crusher After the raw cobalt ore is mined, the volume is large, and it must be roughed with a jaw crusher to crush the large chunk of ore to medium size at one time, and the discharge size of the jaw break is generally 1030 cmNew energy cobalt extraction frontend crushing grinding processDOI: 101016/JPOWTEC201512027 Corpus ID: ; An experimental study on the ultrafine grinding of gypsum ore in a dry ball mill @article{kszolu2016AnES, title={An experimental study on the ultrafine grinding of gypsum ore in a dry ball mill}, author={Bilge {\"O}ks{\"u}zoğlu and Metin Uçurum}, journal={Powder Technology}, year={2016}, An experimental study on the ultrafine grinding of gypsum ore This procedure does not continuously provide protruding abrasive grains, and is considered unsuitable for ultrafine grinding of materials, developed by Mount Isa Mines Ltd and Netzsch and commercialised for ultrafine grinding of ore in 1999 [26] It Ultrafine Grinding an overview ScienceDirect Topics
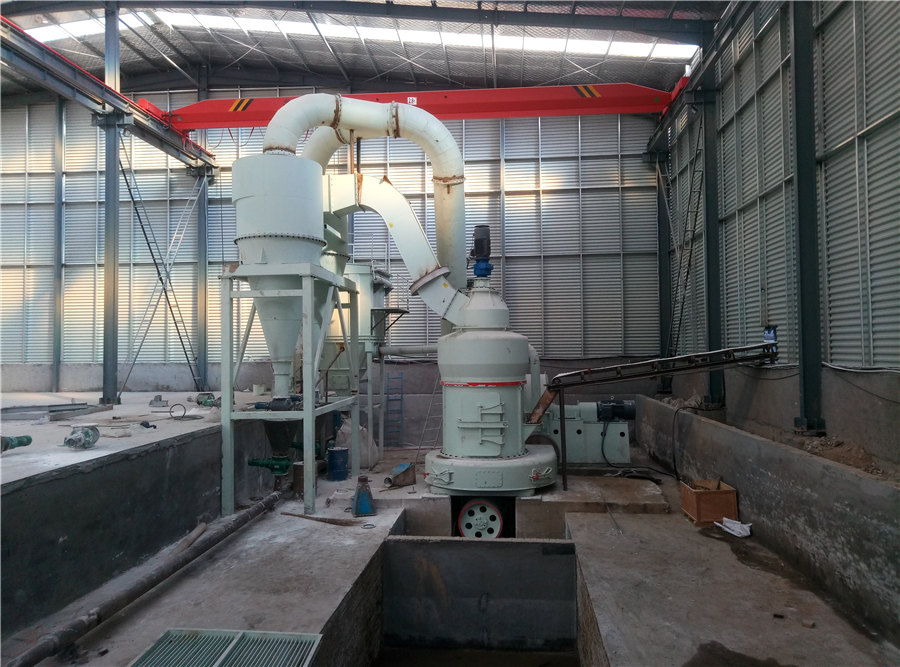
Fine Grinding as Enabling Technology – The IsaMill
Figure 3 : Impact of intense grinding on surface appearance of Chalcopyrite, the stressed and fractured surfaces on the right leach faster and with lower activation energy, even at the same size particles (from Balaz, 2000) Chalcopyrite Concentrate prior to Grinding Chalcopyrite Concentrate Following Ultrafine Grinding 30 Microns 30 MicronsTable 1 The Effect of Ultrafine Grinding on Gold Recovery from Pyritic Ore Figure 4 Gold Recovery versus Particle Size for a Refractory Gold Ore Ultrafine grinding resulted in a significant improvement in the gold recovery through cyanidation Typical gold recoveries for the ore sample, when ground to 80 % passing 75IsaMill Ultrafine Grinding for a Sulphide Leach Process2006年11月1日 Recently, in various industrial processes, the need for fine particles, especially submicronsized particles, has increased in the field of preparing raw powders such as fine ceramics and high value added products Therefore, the research in fine grinding has gained more importance, especially, in submicron grinding In the previous paper, a series of wet Ultrafine grinding mechanism of inorganic powders in a stirred