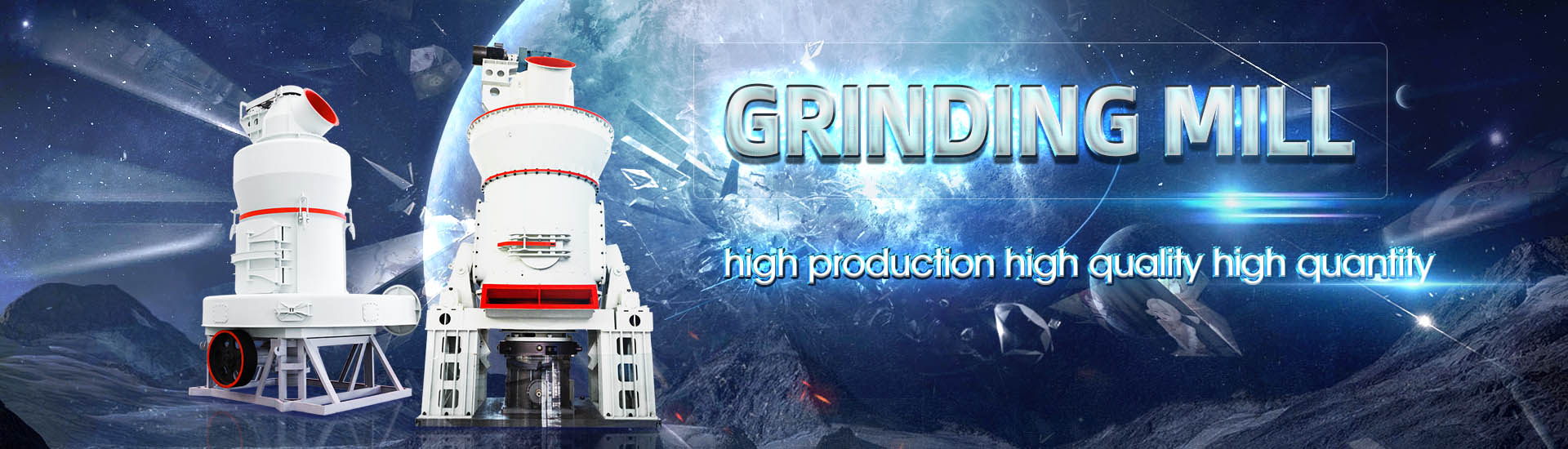
Cement industry grinding system calculation example
.jpg)
OPTIMIZATION OF CEMENT GRINDING OPERATION IN BALL MILLS
An evaluation of the grinding system and operation includes meaningful and critical inspection of all equipment, components and the process parameters by experts PEC Consulting can help carry out detailed evaluation of existing grinding systems and their operation and recommend efficient grinding systems available for the cement and mineral industry, including vertical roller mills (VRM), highpressure grinding units (HPGR) or simple roller presses, as well as the most BALL MILLS Ball mill optimisation Holzinger ConsultingCement grinding In Table 1, three common cement grinding systems are compared on their electrical consumption for a typical 3500 Blaine ordinary portland cement (OPC) Roller press Thomas Holzinger, Holzinger Consulting, grinding system Optimization of a ball charge for cement and raw mills with objective of optimizing the grinding efficiency Best Practice: The ball charge in first and particularly in the second compartment, Ball charge optimization INFINITY FOR CEMENT EQUIPMENT

(PDF) Cement grinding optimisation Alex Jankovic Academia
In this chapter an introduction of widely applied energyefficient grinding technologies in cement grinding and description of the operating principles of the related equip‐ ments and Cement ball mills typically have two grinding chambers The first chamber is filled with larger diameter grinding media and lined with lifting liners The first chamber coarsegrinds the feed material and prepares it for the second chamber The Optimization of Cement Grinding Operation in Ball HOLTEC has undertaken Performance Optimisation of the cement grinding circuits by doing process diagnostic studies in many cement plants The paper describes the approach for the PROCESS DIAGNOSTIC STUDIES FOR CEMENT MILL 2004年11月1日 green house gas emissions, reinforces the need for grinding optimisation This paper describes the tools available for the analysis and optimisation of cement grinding circuits The(PDF) Cement grinding optimisation ResearchGate
.jpg)
EnergyEfficient Technologies in Cement Grinding
2016年10月5日 In this chapter an introduction of widely applied energyefficient grinding technologies in cement grinding and description of the operating principles of the related equipments and comparisons over each other in 2004年11月1日 To optimise cement grinding, standard Bond grinding calculations can be used as well as modelling and simulation techniques based on population balance model (PBM) Cement grinding optimisation ScienceDirectComminution in the cement industry Forces applied in comminution Classification and designation of the stages of Example of calculation Cyclones sizing Calculator Exercise 21 Static Separators Introduction Advantages Pregrinding system Automated control Predictive maintenance Grinding aids 35 Grinding Software presentation Training Courses based on the Grinding SoftwareCement FingerPrint facilitates customers to collaborate with ABB experts to achieve optimal process performance and improve cost effectiveness Cement FingerPrint ensures tuning of plant control system efficiently, benchmarked to Industry Cement plant performance optimization Benchmarking, correction
.jpg)
BALL MILLS Ball mill optimisation Holzinger Consulting
emission benefits to the cement producer n by Thomas Holzinger, Holzinger Consulting, Switzerland BALL MILLS 1 FEBRUARY 2021 INTERNATIONAL CEMENT REVIEW T here are currently several energyefficient grinding systems available for the cement and mineral industry, including vertical roller mills (VRM), highpressure2011年10月21日 3 The necessary inert gas capacity is calculated according to geometrical volumes of all components to be inerted Calculation is based on the total geometrical volume of the coal grinding system (75% of silo net volume in case of two or more silos) Highpressure CO 2 inerting systemsEmergency inerting systems for coalgrinding applications Global Cement2022年10月13日 This reduces grinding energy and results in increasing product throughput These grinding aids are added to the cement prior to the final grinding circuit For controlling the grinding aid to the circuit, the customer was using individual diaphragm pumps and was not satisfied due to inconsistent dosage control and pump unreliabilityControlling grinding aid in cement industry Valmetused in the cement industry These methods are widely used in the cement industry for several reasons: the sizing of new plants and improving existing grinding plants in cement plants Keywords: cement factory, grinding systems, ball mill, grinding ability, fineness of the material, residue, specific energy, energy efficiency 1 IntroductionGRINDING ABILITY OF UNPROCESSED AND PROCESSED CLINKER FROM CEMENT INDUSTRY
.jpg)
Cement Production Seminar: Grinding
Understand the fundamentals and gain insights on how to improve the performance and productivity, efficiency, and product quality of your grinding systems This 3day seminar covers ball and vertical mills with a focus oncomminution theory, design basis, operational principles, control and regulation, process troubleshooting, calculation methods, and optimizationThe Indian cement industry today stands at 260 MTPA capacity, with greater growth prospects and promising future ahead Cement industry has been an excellent example of a fast growing sector showing consistent and steady reduction in its energy consumption This has largely been possible by steady and continuous improvement2010, Confederation of Indian Industry Green Business Centre1 OVERVIEW GRINDING SYSTEMS The common cement grinding systems are summarized in Figure 1 and can be divided into three main groups: Tube Mill Only All grinding work is done in the tube mill and the setup is: ¨ Tube mill in open circuit ¨ Tube mill in closed circuit with; Mechanical air separator; Rotor type separatorCEMENT GRINDING SYSTEMS INFINITY FOR CEMENT EQUIPMENTspreadsheet, and to provide calculation and reporting instructions In order to make the protocol comprehensible to stakeholders from outside the cement sector, some background information on the cement production process has been included in Appendix 3 Please note that in this protocol, metric tonnes are used, where 1 tonne = 1000 kgCO Accounting and Reporting Standard for the Cement Industry
.jpg)
Overview of cement grinding: fundamentals,
2017年5月19日 Cement industry is characterized by sizeable energy demand which accounts for about 110kWh (375 thm) per ton of cement in modern plants Industry impacts heavily also on CO2 emissionsBy taking optimization measures such as reducing the initial roll gap of the roller press, strictly controlling the moisture content of raw materials, controlling equipment air leakage, adjusting the internal structure and grading of the grinding material, the system crust was improved, the system resistance was reduced, and the production capacity of the grinding system increased from Cement Technology2012年2月9日 The design and application of raw material grinding and waste gas treatment systems for dry process cement plants The design and application of raw material grinding and waste gas treatment systems 12 March, 2025 Treating Waste Gases World CementAll formulas are presented in both English and metric systems of units Examples are given to familiarize the reader with the usefulness of Grinding fineness of cement 6 Tests of cement as an example last book we sent to all buyers was refractories for cement industry which cost 97 EUR so buying the book package consider MOST IMPORTANT BOOKS IN CEMENT INDUSTRY !! Essential
.jpg)
Coarse Return Prediction in a Cement Industry’s Closed Grinding
2021年2月3日 Coarse Return Prediction in a Cement Industry’s Closed Grinding Circuit System through a Fully Connected Deep Neural Network (FCDNN) Model February 2021 Applied Sciences 11(4):1361The Vseparator is generally used with a pregrinding system (Roller Press) Applications mainly for raw meals, clinker and slag The main objective of this separator is to remove a maximum of fines particles from the Roller Press feed in orderSeparators in the cement industryExpected production: 130 t/h Cement: 3000 Blaine Specific air load in the fines: 0,75 kg/m3 is chosen Calculated air flow: divided by 0,75 = m3/hSeparators in the cement industryIn cement manufacturing industries, largesized cyclone separators are used as main process equipments in significant numbers for handling high volumetric flow rates of dustladen gases The cyclone is a simple mechanical device commonly used in the grinding circuits to remove relatively large particles from gas streamsSeparators in the cement industry
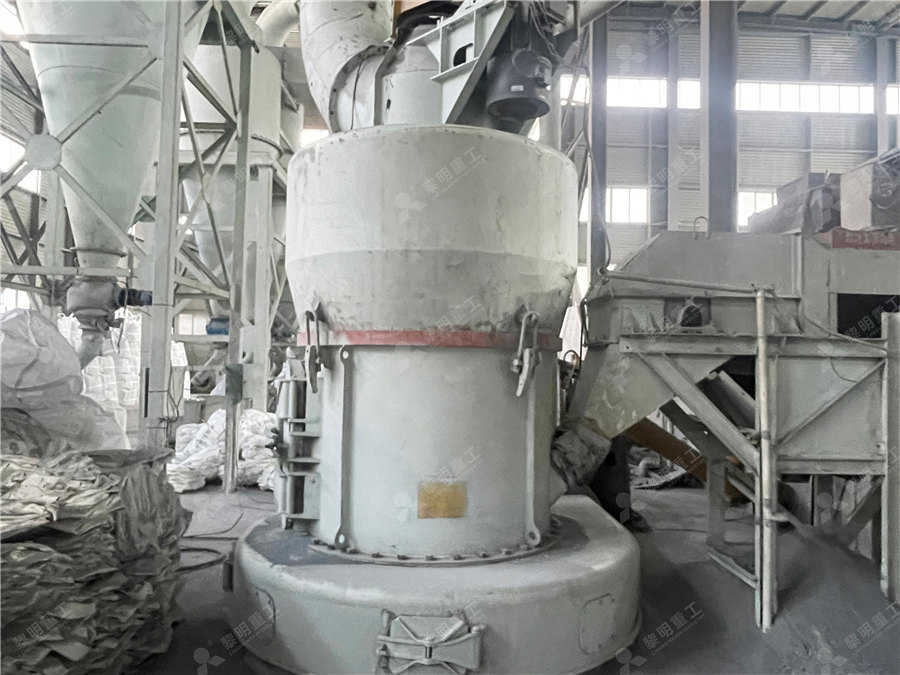
A calculator for valorizing bauxite residue in the cement industry
2021年12月1日 Acronyms in bogue calculation section follow cement chemist notation (C3S = tricalcium silicate, C2S = dicalcium silicate, C3A = tricalcium aluminate, C4AF = tetracalcium aluminoferrite) Figures 2024年1月9日 Cement production contributes significantly to anthropogenic greenhouse gas emissions (GHG), a major contributor to global carbon emissions The environmental impacts of cement production have grown in recent years and it is urgent to reduce its carbon footprint Systems dynamics (SD) is a simulation method used to understand the nonlinear behavior of Carbon emissions mitigation methods for cement industry using a systems PyroProcessing in cement Industry IF YOU WORK IN A CEMENT PLANT AND YOU NEED COURSES AND MANUALS LIKE THIS MANUAL AND BOOKS AND EXCEL SHEETS AND NOTES I SPENT 23 YEARS COLLECTING THEM PyroProcessing in cement Industry2024年2月17日 CEMENT GRINDING COURSE; CEMENT KILN TECHNOLOGY COURSE; A 2week modular course is designed to give the course attendee a solid understanding of KPIs for the cement industry Key Performance Calculation of production costs and operating profit Calculation of production costs exercise – Inventory and spare parts management CEMENT KEY PERFORMANCE INDICATORS (KPI’s The Cement
.jpg)
Air Pollution Control in Cement: Solutions Impact Techflow
2023年9月22日 Bag filters play a vital role in multiple stages of cement production, including grinding, calcining, and clinker grinding They help to improve the quality of the cement by removing impurities, and they also help to reduce emissions of dust and other pollutants into the environment 3 Dense Phase Pneumatic Conveying System for Cement IndustryVIETNAM'S CEMENT INDUSTRY Reduce power consumption in cement grinding system 2) Use additives (Produce blended cements) Clinker content in blended cement in some countries Calculation Target according to Decision 1266, kg CO 2 /t on cement650 550 Notes:(*) Data of VNCA in 2023VIETNAM'S CEMENT INDUSTRY – CURRENT STATUS AND 2019年1月3日 Clinker grinding technology is the most energyintensive process in cement manufacturing Traditionally, it was treated as "low on technology" and "high on energy" as grinding circuits use more than 60 per cent of total energy consumed and account for most of the manufacturing cost Since the increasing energy cost started burning the benefits significantly, Clinker grinding technology in cement manufacturingCement Separator Ball Mill Optimization Update May/2021 , when you buy the package from here , you will get books + complete Courses + Manuals and Notes from very Reputable companies + confedential Guides and Drawings for Cement industry owned Cement Separator Ball Mill Optimization
.jpg)
Most Important Cement books and Manuals and Excel Calculation
This book has a very well gained reputation and frequently is known just as “Labahn” Is a very thorough handbook covering all the cement plant areas from quarry to packing plant, it explains subjects that sometimes are overlooked for example: silos, maintenance, lubrication, automation, storage, handling and feeding systems2015年1月31日 From hubandspoke model to split grinding; from singlegrinding solution to a combination of system solutions; and from energyintensive traditional ball mill to upgraded versions and use of pregrinders, the cement industry is shifting towards more energyefficient grinding solutions ICR trains its spotlight on the current technology trendsGrinding Solutions Indian Cement Review2023年8月21日 ICR looks at the inner workings of grinding mills in the cement industry to understand the technological advancements that are reshaping the landscape against the foreground of sustainability Innovations to enhance the grinding processes are aimed at minimising their environmental footprint while increasing efficiency and performance In CuttingEdge Grinding Solutions Indian Cement Review42 Grinding Systems The selection of the grinding system should be specific to particular situations, to achieve optimum system performance The factors that influence the grinding system performance are: Material characteristics; Moisture in feed materials; Energy costs; Maintenance; Investment; Grinding is a highly energy intensive process Modern Processing Techniques to minimize cost in Cement Industry
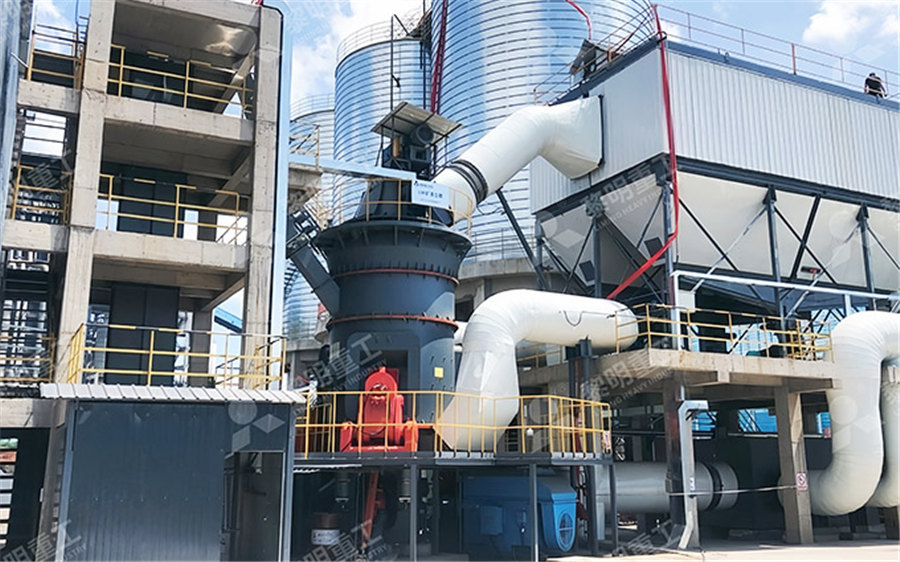
The essentials of electrical systems in cement plants
2020年9月14日 For example if similar plants are consuming 95100 kWh/ton of cement, it may be assumed that the new plant will also consume the same amount and total power to be drawn calculated as shown in subsequent 2021年2月28日 Estimating cement process emissions through an industry’s dataset has more often if not always been majorly based on strong assumptions India being the second largest producer of cement across Deterministic Approach for Calculation of Carbon Vertical roller mills and ball mills represent two clearly distinct technologies However, with proper adjustments to the operational parameters of the vertical roller mill almost identical cement properties can be achieved by the two mills that satisfy the cement user’s demandsNevertheless, the two types of mills have their distinctive meritsCement grinding Vertical roller mills VS ball millsCement Industry is an energy intensive industry and the energy consumption accounts for 4050% of the total manufacturing cost Hence there is a great need to evolve ways and Methods for conserving energy in this industry In cement Industry, conservation of energy can be done by two principal methods, (ie) byOptimizing Electrical Energy Consumption In Cement Process
.jpg)
Cement Manufacturing Process INFINITY FOR CEMENT EQUIPMENT
Grinding: the material is ground between rollers and grinding table while passing from the center of the table to the nozzle ring The commnation method belongs to the most efficient grinding processes applied in the cement manufacturing Separation: the ground and dried material is lifted up with the drying gases2014年3月1日 In the cement industry, the calculation of the parameters per grinding systems of cement 12th Intern ational Conference on Optimization of Electrical andOptimizing the control system of cement milling: Process Previous Post Next Post Contents1 Coarse size reduction of raw materials in Cement Industry11 Size reduction machinery and methods111 A Machinery for size reduction in the coarse range (crushers) by application of compression:112 B Crushers for size reduction by impact:113 C For comminution in the fines range (grinding mills) by application of impact:114 D Mills where Complete Lecture about Crushers in Cement IndustryWe have been in the cement industry for a long time Since 1856, in fact This experience has translated into developments that have improved the efficiency of the cementmaking process For example, back in the 1980s, we introduced the most energyefficient grinding system to the industry: the roller pressGrinding KHD Humboldt Wedag
.jpg)
Grinding trends in the cement industry Cement Lime Gypsum
Summary: The main trends concerning grinding processes in the cement industry are still higher efficiency, reduction of the power consumption and system simplicity In the case of new orders, vertical mills have increased their share to over 60 % and ball mills have fallen to less than 30 % It is somewhat surprising that the number of different grinding processes and mill types used