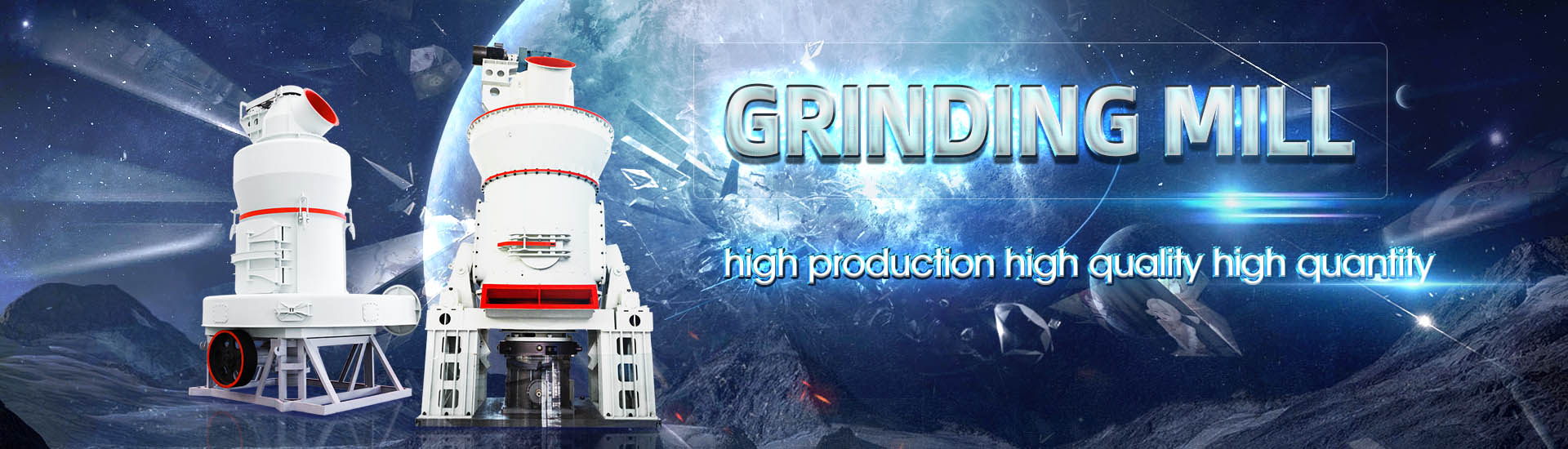
Process flow of iron slag micro powder

Preparation of ultrafine iron phosphate micropowder from
Abstract: In this experiment, ultrafine iron phosphate micropowder was prepared by hydrothermal method which used phosphate slag as an iron source The effects of reaction temperature, surfactants type and amount on its particle size were explored The samples were 2020年11月1日 Optimal solution for slag powder production process is determined by proposed CTNSGAII algorithm Slag powder is a process with characters of multivariables, strongly Analysis and multiobjective optimization of slag powder process2023年5月15日 On this basis, steel slag and slag composite micro powder (SSCM) technology was proposed, which realized the high added value and utilization rate of steel slag in Comprehensive utilization of steel slag: A review ScienceDirect3 Steelmaking Slag Processing Technology The iron/steel slag processing flow is schematically shown in Fig 2 Steelmaking slag is subjected to the following four processes: ① solidify and Processing and Reusing Technologies for Steelmaking Slag
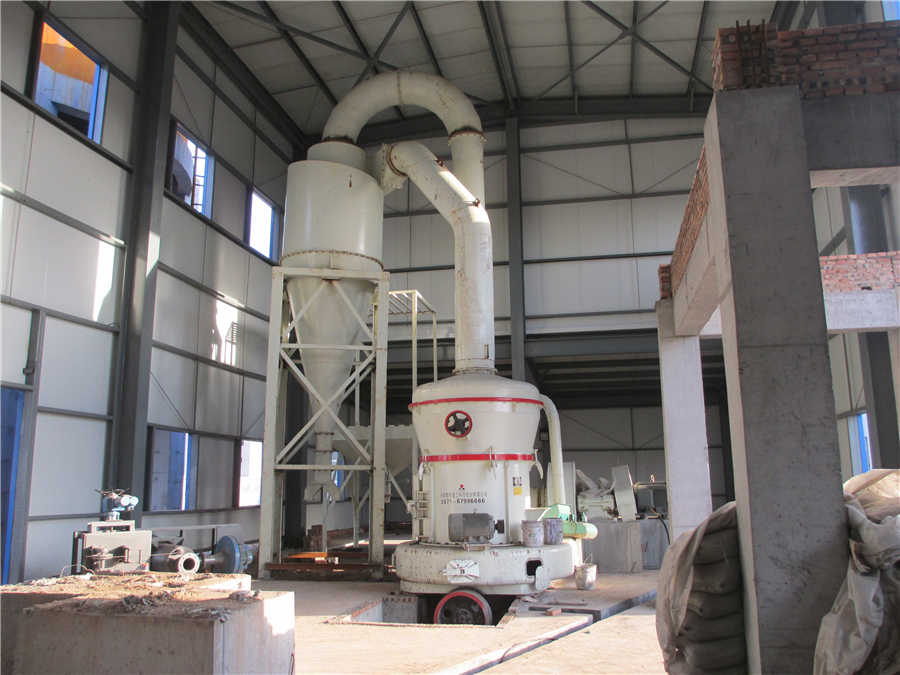
Analysis and multiobjective optimization of slag
2020年7月1日 Slag powder is a process with characters of multivariables, strongly coupling and nonlinearity The material layer thickness plays an important role in the process It can reflect the2018年1月1日 In this experiment, ultrafine iron phosphate micropowder was prepared by hydrothermal method which used phosphate slag as an iron source The effects of reaction temperature, surfactantsPreparation of ultrafine iron phosphate micropowder 2023年3月1日 In this study, chemical analysis, Xray diffraction, and scanning electron microscopy were used to analyze the changes in phase composition and morphology during Efficient separation of iron elements from steel slag based on The ironmaking process generates approximately 290 kg/tsteel of blast furnace slag, which is effectively utilized as a raw material for cement, while the steelmaking process generates Development of Iron Recovery Technique from Steelmaking Slag
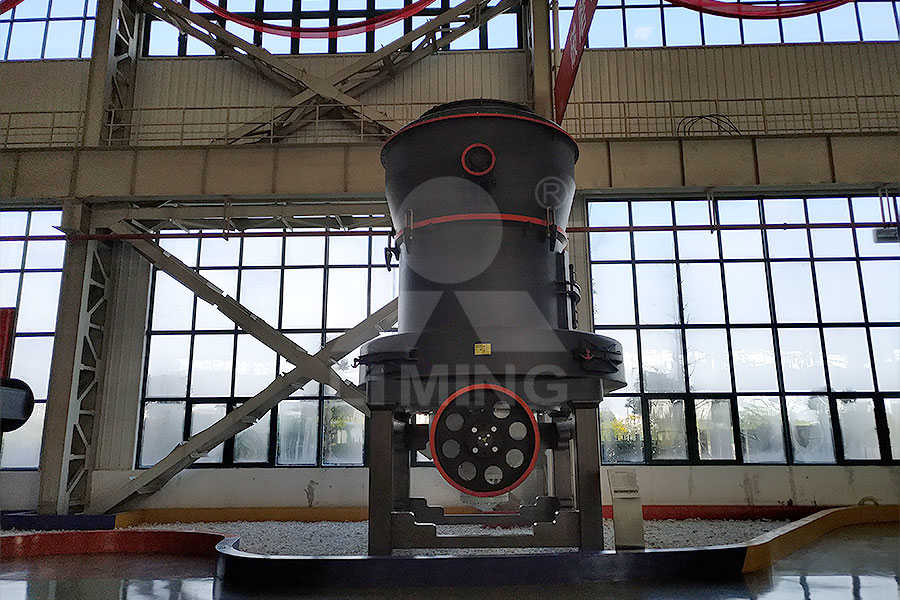
Production process of steel slag micropowder Semantic Scholar
2011年3月17日 The invention relates to a production process of steel slag micropowder, which comprises the following steps: enabling wet steel slag powder with water content of 5% and 2017年3月5日 The physicochemical properties of four different types of iron and steel slags, including blast furnace slag, basic oxygen furnace slag, electric arc furnace slag, and ladle furnace(PDF) Iron and Steel Slags ResearchGate2021年7月1日 The addition of tailings powder improves the working performance of concrete and slightly improves the strength Due to the large amount of cement used in ultrahighperformance concrete, physical (PDF) Effect of Iron Tailings and Slag Powders on Download scientific diagram Flowchart of iron and steelmaking processes [8] from publication: Characteristics and Utilization of Steel Slag in Road Construction Presently, the rate of Flowchart of iron and steelmaking processes [8] ResearchGate
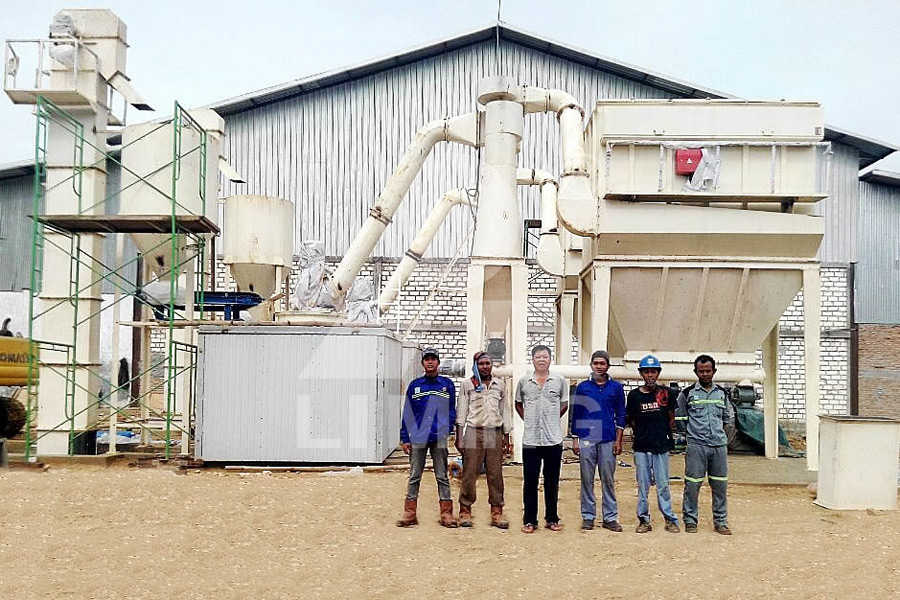
Slag Formation during Reduction of Iron Oxide Using Hydrogen
Iron ore powder with two different grain size distributions, 63–74 and 44–53 μm, was used to carry out the experiments The iron ore powder was fed continuously to a water‐cooled2017年2月16日 Sintering is a thermal agglomeration process that is applied to a mixture of iron ore fines, recycled ironmaking products, fluxes, slagforming agents and solid fuel (coke)(PDF) Iron Ore Sintering: Process ResearchGate2013年8月2日 Furthermore, Xray powder diffraction was used to confirm the mineralogical composition The archaeometallurgical studies suggest that Ban Khao Din Tai slag evidence is entirely consistent with the expect waste product of the bloomery ironmaking process or direct smelting processArchaeometallurgical Studies of Ancient Iron Smelting Slags 2014年2月19日 Drumgranulation process is a new process for molten steel slag granulation It is an improved version of the HK process, which was originally used for BF slag granulation []A kind of heat resistant alloy steel was used as material of the drum, and the cooling ability for the drum was enhanced in order to fit the high temperature of molten BOF slagCurrent Development of Slag Valorisation in China
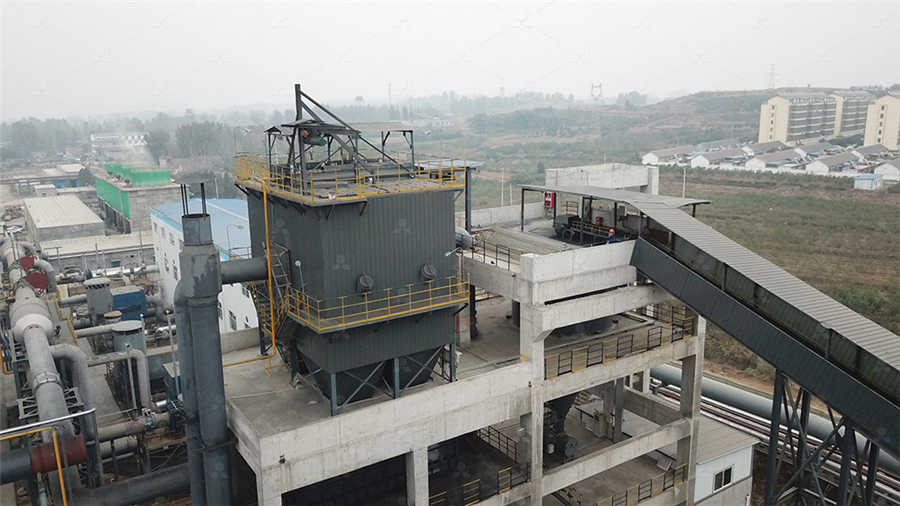
A literature review of titanium slag metallurgical processes
2012年1月1日 Basic procedure of ilmenite smelting and rational Ti slag grade in pyrometallurgical process have been summarized and analyzed The rational Ti slag grade is related to reduction degree, FeO Download scientific diagram The technical flow process of recycling ironrich phases in steel slag from publication: Comparison of Grinding Characteristics of Converter Steel Slag with and The technical flow process of recycling ironrich phases in steel slag Iron powder via atomization process (gas and water) floats on top of the iron Slag and iron are tapped at regular intervals through flow of hydrogen gas in a temperature range 400 to 800 °C and deagglomerated to make iron metal containing micronsize alloyed powdersIron Manufacturing process related to the specified manufacture2005年2月1日 The importance of understanding slags, their reusability, their specific roles and improvements in functions to lead a significant reduction in slag volumes in iron and steel industry is discussed(PDF) Industrial uses of slag The use and reuse of iron and
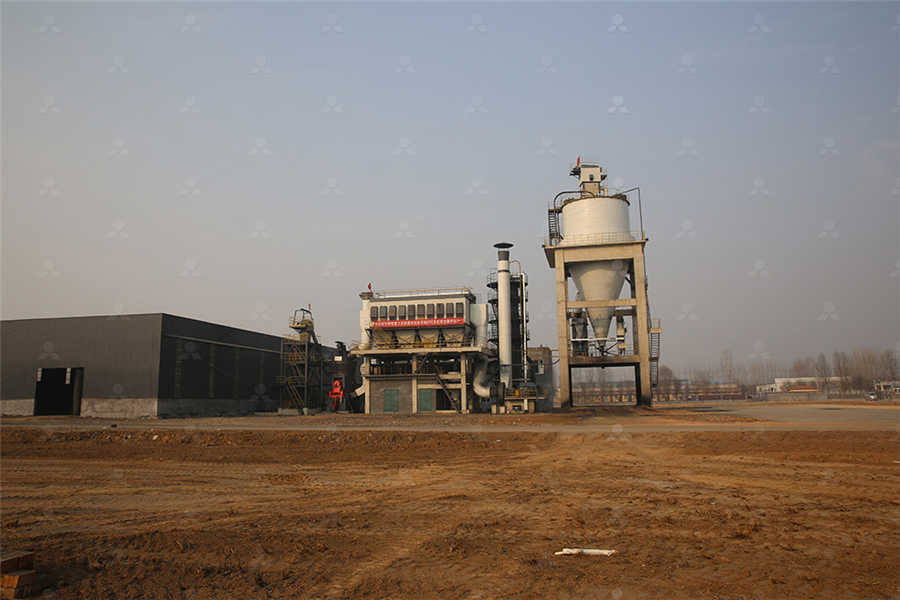
Preparation of ultrafine iron phosphate micropowder from phosphate slag
of phosphate slag and the synthetic process of recycling and reuse It has a deep understanding of it and has mastered the technology of phosphate slag to purify iron phosphate[5,8,2526] I have adopted a new method to purify and prepare iron phosphate micropowder with smaller particle size The purified and modified iron phosphate2016年2月29日 Slag appearance is a good indicator of the process Although iron minerals have influence on color slag, it is possible to draw some conclusions according to the color For example, a blue color is symptom of copper Gold Smelting Refining Process 911Metallurgist2006年3月1日 Hydration heat evolution, nonevaporative water, setting time and SEM tests were performed to investigate the effect of fine steel slag powder on the hydration process of Portland cement and its Effect of fine steel slag powder on the early hydration process of 2013年10月30日 The drainage of molten iron and slag is of considerable significance for the ironmaking blast furnace (BF) The draining process is in principle driven by the infurnace overpressure that balances Flow Patterns of Iron and Slag in the Blast Furnace Taphole
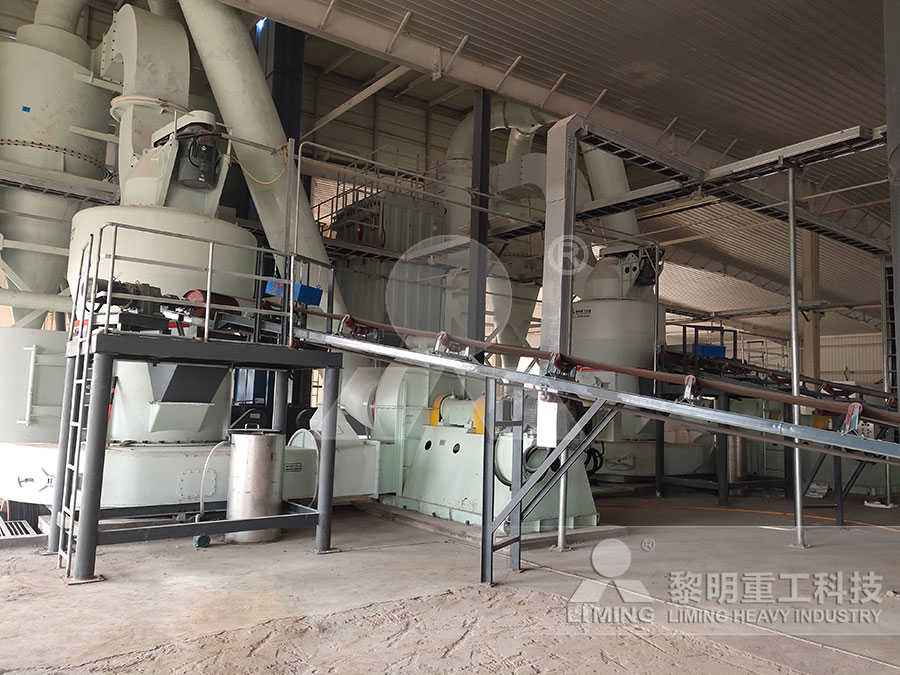
Micromorphology and phase composition of lithium slag from
2019年4月10日 Lithium slag is industrial byproduct of the extraction of lithium carbonate industry, which is produced by high temperature roasting of spodumene and sulfuric acid [1], [2], [3]For each tonne of lithium carbonate, 8 to 10 tonnes of lithium slag will be discharged [4], [5]Xinjiang and Sichuan in China are the most major lithium salt production bases and 2013年4月1日 A considerable amount of waste slag from the pyrite roasting process is produced every year Recovery of iron from the waste slag is of great interest for maximum use of mineral resource (PDF) Recovery of iron from waste slag of pyrite processing using DOI: 101155/2017/ Corpus ID: ; Numerical Analysis on Flow Behavior of Molten Iron and Slag in Main Trough of Blast Furnace during Tapping Process @article{Wang2017NumericalAO, title={Numerical Analysis on Flow Behavior of Molten Iron and Slag in Main Trough of Blast Furnace during Tapping Process}, author={Li Wang and Chien Numerical Analysis on Flow Behavior of Molten Iron and Slag in 2024年1月1日 In 2022, global crude steel production reached 1,885,738 million tons, marking increase of 02 % compared to 2020 [1]Basicity oxygen furnace (BOF) slag and blast furnace slag (BFS), as prominent solid wastes in the steel industry, have seen rising emissions, which negatively affects the development of the steel industry [2]Notably, the application of steel Synergistic treatment of blast furnace slag and basic oxygen
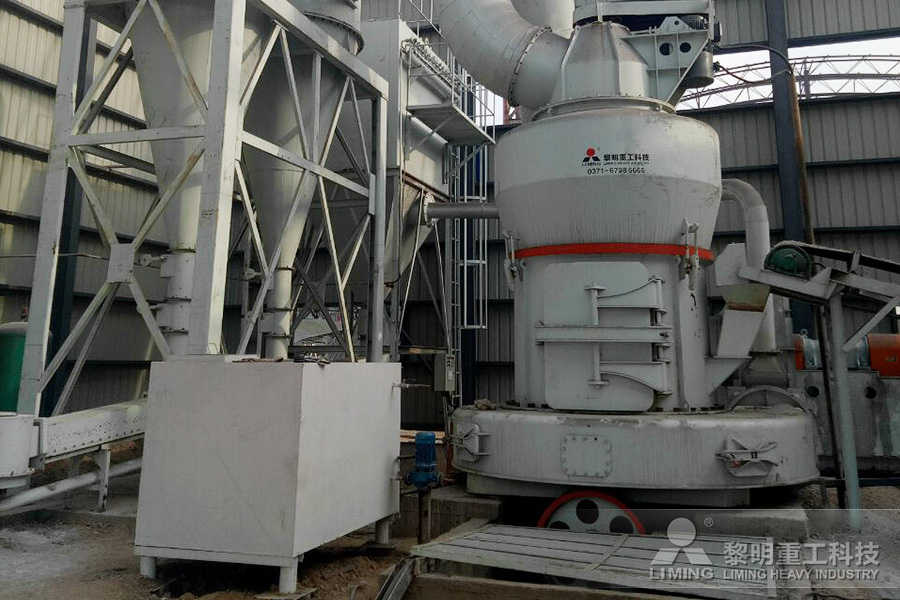
(PDF) Slag Formation During Reduction of Iron Oxide Using
2020年1月28日 Process flow sheet of laboratory equipment: (A) process flow diagram and (B) reactor layout, reproduced from ref [13] with permission A DC electrical power supply with the maximum power of 12 kW process,1–3) with the aim of recycling and utilizing its Fe and CaO content, but in recycling to the ironmaking process, the phosphorus in the slag is transferred to the hot metal in the blast furnace under a reducing condition and may have an Development of Iron Recovery Technique from Steelmaking Slag by Reduction at High TemperatureDevelopment of Iron Recovery Technique from Steelmaking Slag Steelmaking slag, or steel slag, is a byproduct from the production of steel during the conversion of hot metal to crude steel in a basic oxygen furnace, or during the melting of scrap in an EAFThe slag is generated as a melt and is a complex solution of silicates and oxides that solidify upon cooling 11 Depending on the specific steel production process, three different types of steel Steelmaking Slag an overview ScienceDirect Topics2020年4月14日 In this study, highpurity iron with purity of 99987 wt% was prepared employing a process of direct reduction–melting separation–slag refiningThe Preparation of HighPurity Iron (99987%)
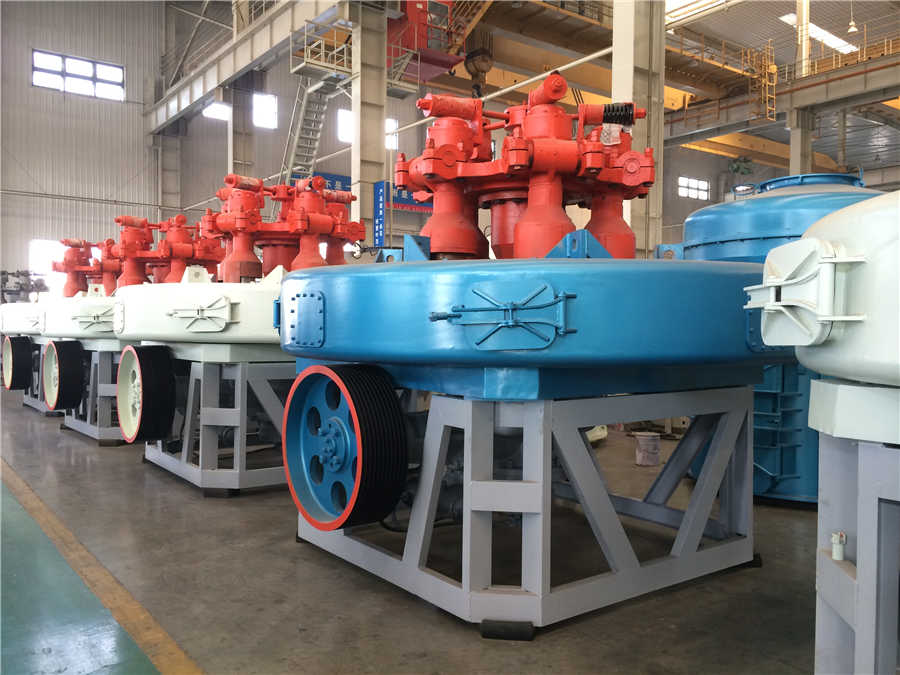
Recent research progress on recycling metallurgical waste slag
2024年11月1日 The utilization rate of SS exceeds that of LFS due to its lower basicity, although it remains considerably lower than the rates observed in developed countries in Europe and the United States, standing at approximately 30 % [4]Currently, the internal recycling of SS predominantly takes place within the smelting production process, serving purposes such as Iron powder is normally manufactured from acicular particles of goethite (αFeOOH) by dehydration and subsequent gasphase reduction with hydrogen without extensive change of the original shape 73,74 In order to prevent the sintering of the iron powder during the thermal treatments, the starting material, αFeOOH, is pretreated with silicone oil, silver or cobalt Iron Powder an overview ScienceDirect Topics2020年10月31日 The Fe3O4 and Fe2SiO4 in copper slag were successfully reduced to metallic iron by coalbased direct reduction Under the best reduction conditions of 1300 °C reduction temperature, 30 min reduction time, 35 wt% coal dosage, and 20 wt% CaO dosage (075 binary basicity), the Fe grade of obtained iron concentration achieved 9155%, and the Fe recovery Recovery of Iron from Copper Slag Using CoalBased Direct2022年12月13日 The cement was replaced with iron slag (IS) at the substitution levels of 75%, with slag Microstructural studies have reported the concrete by using iron slag as a powder in concrete(PDF) Impact of Waste Iron Slag on Mechanical and
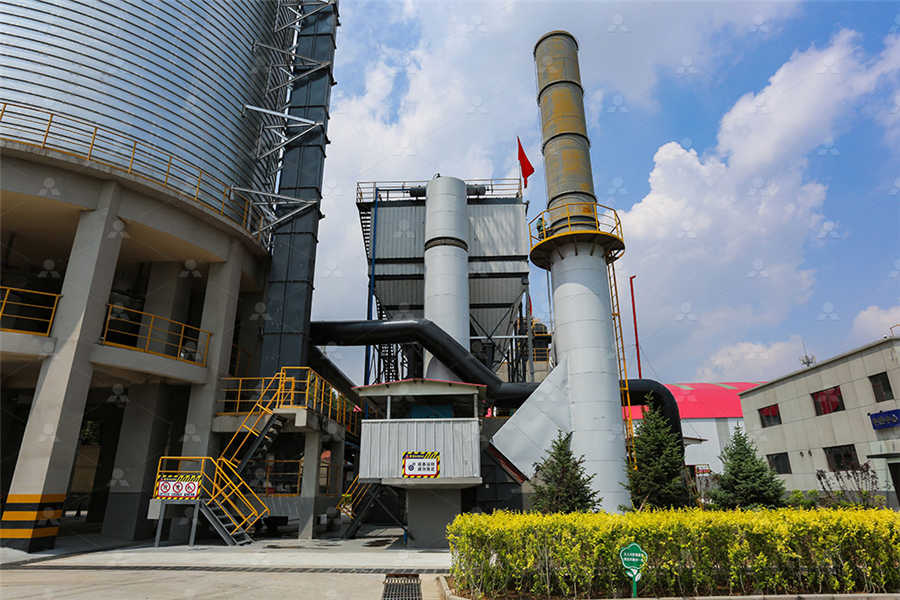
Carbon mineralization of steel and ironmaking slag: Paving the
2024年4月1日 Carbon mineralization technology has emerged as a promising method for permanently sequestering CO 2 by transforming it into a thermodynamically stable solid carbonate material Recently, alkaline industrial waste, particularly from steel and ironmaking processes, has been identified as a proper feedstock due to its high potential for CO 2 storage and the 2020年4月14日 In this study, highpurity iron with purity of 99987 wt% was prepared employing a process of direct reduction–melting separation–slag refining The iron ore after pelletizing and roasting was reduced by hydrogen to obtain direct reduced iron (DRI) Carbon and sulfur were removed in this step and other impurities such as silicon, manganese, titanium and aluminum The Preparation of HighPurity Iron (99987%) Employing a Process 2020年10月31日 The Fe3O4 and Fe2SiO4 in copper slag were successfully reduced to metallic iron by coalbased direct reduction Under the best reduction conditions of 1300 °C reduction temperature, 30 min (PDF) Recovery of Iron from Copper Slag Using CoalBased Direct 2015年7月30日 Lots of iron molten slag from blast furnace can be produced during iron making process It is generally cooled by water quenching method which causes many problems, such as water consumption Modeling on Dry Centrifugal Granulation Process of
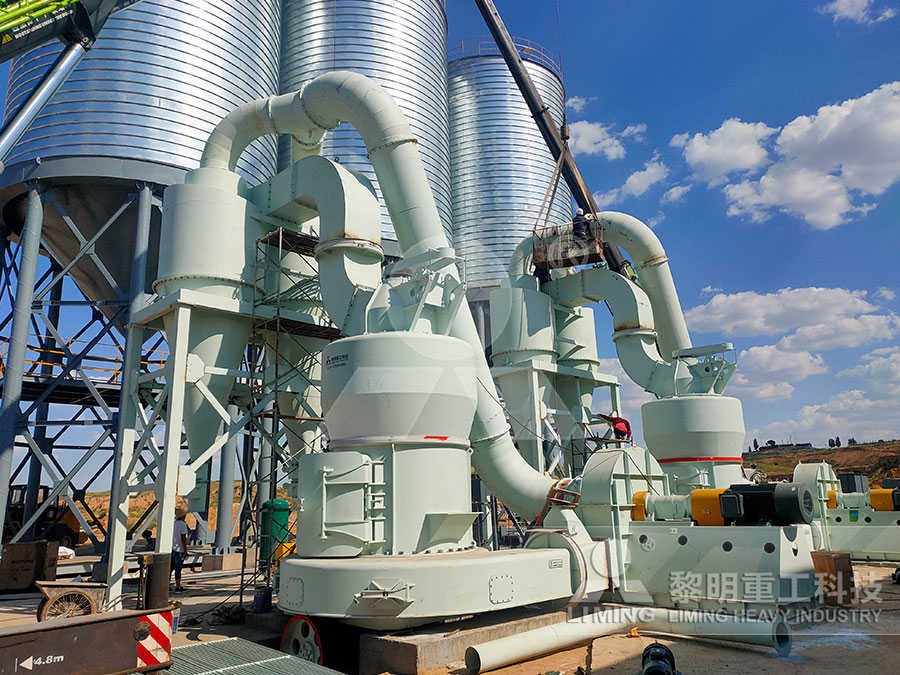
Enhancing Recycling Potential: Exploring Reduction and Metal
2024年7月16日 The electric arc furnace steelmaking route is essential for sustainable steelmaking through hydrogenbased direct reduced iron About 30% of the global steel production currently follows the scrap/direct reduced iron–electric arc furnace (DRIEAF) route, which is bound to increase given decarburization efforts by the steel industry We investigated 2024年11月1日 The concrete prepared by replacing cement with mechanically activated iron tailings powder and slag powder had higher strength than ordinary Portland cement concrete (Han et al, 2019), with a substitution rate reaching 50 %, consistent with the findings of reference (Puertas et al, 2003)Dynamic mechanical properties and microstructure of ultrafine slag 2023年11月20日 Mineral process wastes, such as metallurgical slags nowadays, are of significant metals and materials resources in the circular economy The usability of ironmaking slag is well established; however, steel A Review on Environmental Concerns and Molten pig iron is transported from the blast furnace to the steel making plant by torpedoes Treatment of the pig iron to reduce sulphur levels to be as low as 001% is a prerequisite for the production of low sulphur steel grades [1] Upon arrival in the steelmaking plant, pig iron undergoes the desulphurization processProcess Design for the Magnetic Recovery of Iron from
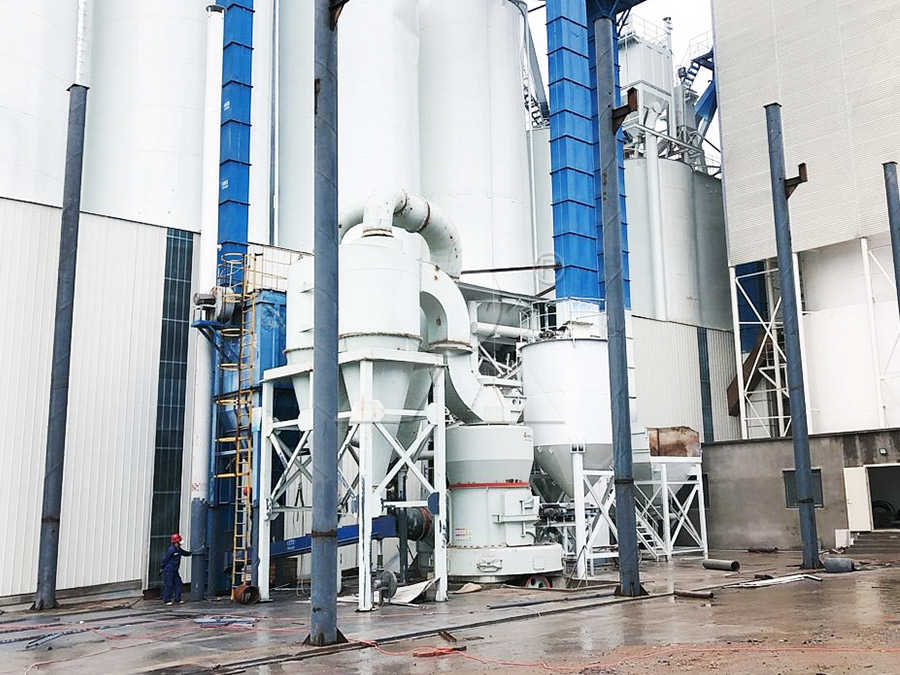
Research progress of hydrogen production and CO
2024年4月22日 Abstract Steel slag is a waste discharged from the iron and steel smelting process, which has the characteristics of large output, used steel slag to fix carbon, fully mixed steel slag powder with water at a mass ratio of 215 g of carbon is fixed per kg of steel slag: Temperature, Slurry flow rate: 30°C–60°C Optimum Steel slag, desulphurised ash, desulphurised gypsum and ultrafine iron tailing sand are common industrial solid wastes with low utilisation rates Herein, industrial solid wastes (steel slag, desulphurised gypsum and desulphurised ash) were used as the main raw materials to prepare a gelling material and ultrafine tailing was used as an aggregate to prepare a new type of The Preparation Process and Hydration Mechanism of Steel Slag 2022年2月26日 Blast furnace slag powder of 0325 mesh generally adopts European plate mill The 1000 mesh blast furnace slag powder is suitable for three ring medium speed micro powder mill Three ring medium speed micro grinding is a kind of ultrafine grinding equipmentWhat is Blast Furnace Slag and How to Process It?2021年4月14日 Similar compounds were found in cement and copper slag, such as Ca, Si, Al, Na, Fe, Mg, etc The high peaks from the XRD image of copper slag indicate the presence of iron silicate fines and Characterization of copper slag for beneficiation of iron and copper
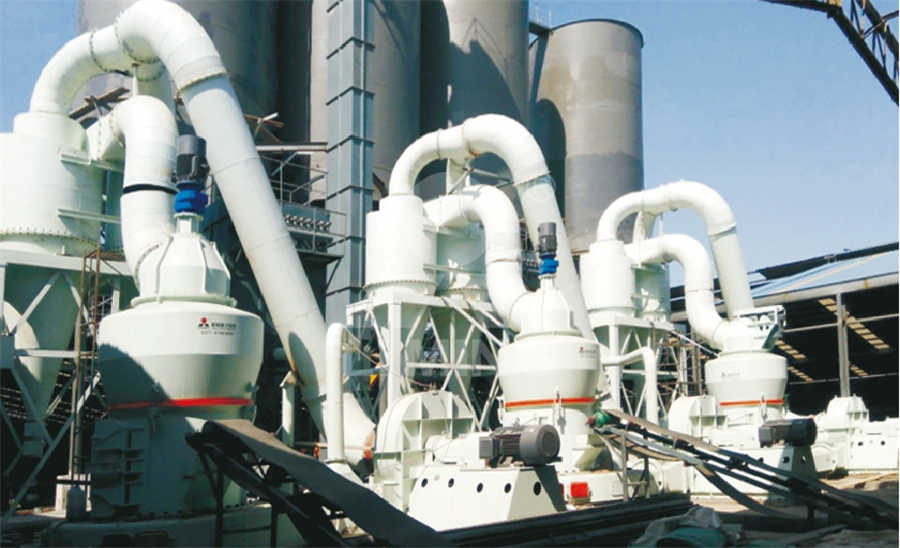
Simplified process flow sheet of the alkaline roasting of titanium slag
Download scientific diagram Simplified process flow sheet of the alkaline roasting of titanium slag (ARTS) process from publication: Life cycle assessment comparison of emerging and traditional 2024年3月28日 To promote the resource utilization of steel slag and improve the production process of steel slag in steelmaking plants, this research studied the characteristics of three different processed steel slags from four steelmaking plants The physical and mechanical characteristics and volume stability of steel slags were analyzed through density, water Research on the Properties of Steel Slag with Different MDPI